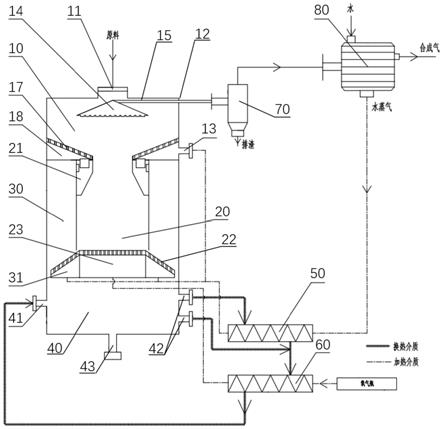
1.本发明属于固体燃料利用技术领域,更具体地,涉及一种适合于宽筛分原料的气化反应器。
背景技术:
2.气化作为一种非常重要的能源转化方式,在煤、生物质和垃圾等固体燃料利用领域有着举足轻重的地位。气化的主要产物是以氢气、一氧化碳为主的合成气,合成气可以直接燃烧进行发电和供热,还可以通过化学合成生产液体燃料和化学品。
3.目前,气化装置类型主要有固定床和流化床。常压固定床技术以混合发生炉、ugi水煤气炉(常压固定床煤气化设备)、水煤气炉、两段混合发生炉、两段水煤气炉为主,其特点是操作简单、投资少,但是固定床必须选用固定种类、形状和尺寸尽可能一致的原料。流化床的技术特点是增强气固传热传质过程,便于气化剂的利用和高效气化,但是只适用于较小颗粒原料。而实际固体燃料来源广泛、性质各异,很难将其破碎成满足现有气化装置粒径要求的原料,往往导致气化效果不佳等问题。
技术实现要素:
4.针对现有技术的缺陷,本发明的目的在于提供一种适合于宽筛分原料的气化反应器,通过设置多级反应室,为不同粒径范围的原料提供相适应的气化氛围,旨在解决现有气化装置对进料粒径要求高导致宽筛分固体燃料气化效果不佳的问题。
5.为实现上述目的,本发明提供了一种适合于宽筛分原料的气化反应器,其包括反应器本体,所述反应器本体包括相互连通的第一反应室、第二反应室和第三反应室;所述第一反应室顶部设置有进料口和出气口;
6.所述第二反应室和所述第三反应室均位于所述第一反应室下方,所述第三反应室套设在所述第二反应室外围;所述第一反应室侧壁设置有第一通气口,所述第一通气口用于通入气化剂使得第一反应室中的小颗粒原料流化并发生气化反应;所述第二反应室底部设置有第二通气口,所述第二通气口用于通入氧化剂使得第二反应室中堆积的颗粒床层发生氧化反应;所述第三反应室底部设置有第三通气口,所述第三通气口用于通入气化剂使得第三反应室中的颗粒流化并发生气化反应。
7.优选地,所述第一反应室内设置有集气装置,所述集气装置包括底部开口的集气罩和导气管,所述集气罩靠近所述第一反应室的顶部,所述集气罩的顶部与所述导气管连通,所述导气管远离所述集气罩的一端与所述出气口连通。
8.优选地,所述集气罩呈锥形且位于所述进料口正下方。
9.优选地,所述集气罩底部开口处设置有多个角度可调节的百叶窗片。
10.优选地,所述第一反应室内靠近其底部设置有倾斜的环形布风板,所述环形布风板将所述第一反应室的内部分隔出第一环形气室,使得从所述第一通气口通入的气化剂进入所述第一环形气室后,通过所述环形布风板上的布风孔均匀布入所述第一反应室中。
11.优选地,所述第二反应室内靠近其顶部沿周向设置有至少一个第一气固分离器,所述第二反应室内壁上开设有与所述第一气固分离器数量相同的通孔,所述第一气固分离器的进口通过所述通孔与所述第三反应室连通,所述第一气固分离器的气体出口与所述环形布风板上的布风孔连通。
12.优选地,所述第一气固分离器的横截面为正方形且其内部具有圆筒状腔室,所述第一气固分离器的内壁采用刚玉莫来石材料。
13.优选地,所述反应器本体还包括横跨所述第二反应室和第三反应室的布风板,所述布风板将所述第二反应室的内部分隔出氧化剂气室,使得从所述第二通气口通入的氧化剂进入所述氧化剂气室后,通过所述布风板上的布风孔均匀布入所述第二反应室中;所述布风板将所述第三反应室的内部分隔出第二环形气室,使得从所述第三通气口通入的气化剂进入所述第二环形气室后,通过所述布风板上的布风孔均匀布入所述第三反应室中。
14.优选地,连接第一通气口、第二通气口和第三通气口的管道上均设置有流量控制阀。
15.优选地,本发明气化反应器还包括换热装置,所述反应器本体还包括冷渣室,所述冷渣室位于所述第三反应室的下方且与所述第三反应室连通,所述冷渣室的侧壁上设置有换热介质进口和至少一个换热介质出口,所述换热介质进口连接所述换热装置的出口,所述换热介质出口连接所述换热装置的进口。
16.优选地,所述换热装置包括高温换热器和低温换热器,所述冷渣室的侧壁上沿竖直方向设置有两个换热介质出口,位于上方的换热介质出口与所述高温换热器的热流进口连通,位于下方的换热介质出口与所述低温换热器的热流进口连通,所述低温换热器的热流进口还与所述高温换热器的冷流出口连通,所述高温换热器的热流出口与所述第三通气口连通,所述低温换热器的热流出口与所述第二通气口连通,所述低温换热器的冷流出口与所述换热介质进口连通。
17.优选地,本发明气化反应器还包括第二气固分离器和余热回收装置,所述第二气固分离器的进口与所述出气口连通,所述第二气固分离器的气体出口与所述余热回收装置的进口连通。
18.优选地,所述余热回收装置为蒸汽发生器,所述蒸汽发生器的水蒸气出口与所述高温换热器的冷流进口连通。
19.总体而言,通过本发明所构思的以上技术方案与现有技术相比,具有以下有益效果:
20.(1)本发明气化反应器通过设置三个相互连通的反应室,并分别通入不同的气化剂,以实现固体燃料颗粒的筛分,为不同粒径范围的原料提供相适应的气化氛围,使气化反应更高效;该反应器结构紧凑,占地小,利用该反应器气化固体燃料,无需在气化反应前对原料进行复杂的粉碎筛分处理,具有原料适应性广、处理过程简单、转化率高、成本低等优点。
21.(2)本发明通过在进料口正下方设置锥形集气罩,既实现进料颗粒的均匀分布,又可以实现集气功能,一举多得;同时,设置在集气罩罩口的百叶窗片还起到了扰流和延长颗粒停留时间的作用,有利于气化反应更完全。
22.(3)本发明通过布风板将各反应室隔出相应气室,布风板对通入的气流产生一定
的阻力,使得在布风板上具有均匀的气流速度分布,为各反应室提供良好的流化工况;利用高流速的气化剂使细颗粒原料处于悬浮流化状态,并维持流化床层的稳定,实现原料颗粒的筛分,有利于不同粒径原料气化反应的进行。
23.(4)本发明通过在第二反应室内设置气固分离器,对第三反应室中的产物进一步筛分,使得气化反应更彻底;该分离器采用外方内圆的异形结构,有利于颗粒在内壁的摩擦破碎,并且增大内部腔室体积,延长颗粒的破碎时间;同时该气固分离器内壁使用耐磨的刚玉莫来石材料,一方面提高分离效率,另一方面增大颗粒与内壁之间的摩擦,有利于颗粒粒径的减小和进一步的反应。
24.(5)本发明利用余热回收装置和多级换热装置,对高温气体和炉渣的物理显热进行回收,对气化剂水蒸气和氧气进行加热,实现换热介质的循环利用,减少能源损失;无需额外设置加热装置,能耗低。
附图说明
25.图1为本发明实施例提供的气化反应器的结构示意图;
26.图2为本发明实施例提供的集气装置的结构示意图;
27.在所有附图中,相同的附图标记用来表示相同的元件或结构,其中:
28.10
‑
第一反应室,11
‑
进料口,12
‑
出气口,13
‑
第一通气口,14
‑
集气罩,15
‑
导气管,16
‑
百叶窗片,17
‑
环形布风板,18
‑
第一环形气室;20
‑
第二反应室,21
‑
第一气固分离器,22
‑
布风板,23
‑
氧化剂气室;30
‑
第三反应室,31
‑
第二环形气室;40
‑
冷渣室,41
‑
换热介质进口,42
‑
换热介质出口,43
‑
排渣口;50
‑
高温换热器;60
‑
低温换热器;70
‑
第二气固分离器;80
‑
余热回收装置。
具体实施方式
29.为了使本发明的目的、技术方案及优点更加清楚明白,以下结合附图及实施例,对本发明进行进一步详细说明。应当理解,此处所描述的具体实施例仅仅用以解释本发明,并不用于限定本发明。
30.如图1所示,本发明提供的一种适合于宽筛分原料的气化反应器,其包括反应器本体,该反应器本体包括相互连通的第一反应室10、第二反应室20和第三反应室30,第二反应室20和第三反应室30均位于第一反应室10下方,第三反应室30呈环形且套设在第二反应室20外围,具体地,第一反应室10底部与第二反应室20顶部连通,第二反应室20底部与第三反应室底部30连通,第三反应室30顶部与第一反应室10底部连通。
31.第一反应室10顶部设置有进料口11和出气口12,宽筛分原料从进料口11落下,在第一反应室10中气化的产物从出气口12排出。第一反应室10侧壁设置有第一通气口13,第一通气口13用于通入气化剂,使得初始落入第一反应室10中的一部分细小颗粒原料流化并发生气化反应,产生的气体从出气口12排出。第二反应室20底部设置有第二通气口,第二通气口用于通入氧化剂,第一反应室10中一部分未发生气化反应或未反应完全的粗大颗粒落入第二反应室20中并堆积形成颗粒床层,颗粒床层在此发生氧化反应,释放出热量,产生的气体上升进入第一反应室10。第二反应室20中的颗粒床层会逐渐向下移动,底部的颗粒进入第三反应室30,第三反应室30底部设置有第三通气口,第三通气口用于通入气化剂,使得
落入第三反应室30中未反应完全的小颗粒进一步气化,产生的气体上升进入第一反应室10。
32.本发明气化反应器通过设置多级反应室,为不同粒径范围的原料提供相适应的气化氛围,实现对宽筛分原料的分步气化,使得气化反应更完全,提高了反应的转化率,气化效果更好。
33.本发明的气化反应器适用于固体燃料的气化,生成可燃性气体(煤气),煤气主要成分是一氧化碳和氢气。固体燃料可以为各种煤、焦炭、生物质、有机固废中的任意一种,或者多种不同性质原料组成的混合物。气化剂有空气、富氧空气、氧气和水蒸气、二氧化碳等,本发明所提到的气化剂主要成分是水蒸气和二氧化碳,固体燃料中的碳和气化剂发生化学反应使得固体燃料气化,在第一反应室10和第三反应室30中可能会发生的化学反应如下方程式(1)、(2)、(3)和(4)所示;本发明提到的氧化剂实质也是一种气化剂,主要成分是氧气,和固体燃料中的碳发生氧化还原反应生成气体,在第二反应室20中可能会发生的化学反应如下方程式(4)、(5)和(6)所示。
[0034][0035][0036][0037][0038]
2c+o2=2co
ꢀꢀ
(5)
[0039]
c+o2=co2ꢀꢀ
(6)
[0040]
以下结合具体实施例,对上述技术方案详细说明。
[0041]
参见图1,第一反应室10位于第二反应室20和第三反应室30的上方,第一反应室10内设置有集气装置,集气装置包括集气罩14和导气管15,集气罩14用于收集第一反应室10内的气体,并由导气管15通过出气口12排出到反应器本体外。具体地,集气罩14靠近第一反应室10的顶部,集气罩14底部开口,集气罩14的顶部与导气管15连通,导气管15远离集气罩14的一端与出气口12连通。第一反应室10内靠近其底部设置有倾斜的环形布风板17,环形布风板17将第一反应室10的内部分隔出第一环形气室18,使得从第一通气口13通入的气化剂进入第一环形气室18后,通过环形布风板17上的布风孔均匀布入第一反应室10中。具体地,环形布风板17的倾斜角度为30
°‑
60
°
。
[0042]
作为优选实施例,集气罩14呈锥形且位于进料口11正下方,使得从进料口11落下的原料经过集气罩14的阻挡而向四周均匀分散,随后落入第一反应室10中的反应区。
[0043]
进一步优选地,参见图2,集气罩14底部开口处设置有多个角度可调节的百叶窗片16,用于拦截上升气流中较大的颗粒,从而延长其在反应区的停留时间,有利于其充分气化。百叶窗片16的倾斜角度可调节,通过设置不同数量的百叶窗片16,使得相邻两个百叶窗片16的间距也是可适应性调节的,并且百叶窗片16可以设置一层或者多层,这些可针对不同粒径范围的固体燃料进行相应设计,在此不赘述。同时,百叶窗片16可以固定设置也可以可拆卸设置在集气罩14的底部,可拆卸设置便于百叶窗片16的清洗更换,防止百叶窗片16间发生颗粒堵塞而影响气化效果。
[0044]
反应器本体还包括横跨第二反应室20和第三反应室30的布风板22,第二反应室20其位于布风板22以上的侧壁与布风板22之间设有缝隙,用于连通第二反应室20和第三反应室30的底部,使得未反应完全的原料颗粒进入第三反应室30中进行进一步气化反应,同时反应完全的剩余固体颗粒(固体燃料中不仅只有碳,有些杂质成分无法气化)由于温度较高会粘结成尺寸较大的渣块,随着颗粒床层的向下移动,渣块也会进入第三反应室30中。具体地,布风板22包括中间部分和围绕在中间部分外围一圈的环形部分,布风板22的中间部分位于第二反应室20内、并将第二反应室20的内部分隔出氧化剂气室23,使得从第二通气口通入的氧化剂进入氧化剂气室23后,通过布风板22中间部分的布风孔均匀布入第二反应室20中;布风板22的环形部分位于第三反应室30内、并将第三反应室30的内部分隔出第二环形气室31,使得从第三通气口通入的气化剂进入第二环形气室31后,通过布风板22环形部分的布风孔均匀布入第三反应室30中。优选地,布风板22的环形部分是向下倾斜的,且其与第三反应室30侧壁之间形成环形缝隙,便于第二反应室20底部的颗粒物料落入第三反应室30中,并且反应后剩余的渣块通过环形缝隙排出。布风板22环形部分的倾斜角度优选为30
°‑
60
°
。
[0045]
第二反应室20内靠近其顶部沿周向还设置有至少一个第一气固分离器21,该第一气固分离器21可以为旋风筒分离器,也可以为方形分离器。第二反应室20内壁上开设有与第一气固分离器21数量相同的通孔,第一气固分离器21的进口通过第二反应室20内壁上的通孔与第三反应室30连通,第一气固分离器21的气体出口与环形布风板17上的布风孔连通。具体地,各第一气固分离器21固定安装在第二反应室20的内壁上,并且其进口与第二反应室20内壁上的通孔相对应;第一环形气室18底部开设有与第一气固分离器21数量相同的通孔,第一气固分离器21的气体出口通过第一环形气室18底部的通孔与第一环形气室18连通。第三反应室30顶部的气固混合物料从第一气固分离器21的进口吸入,经过气固分离后,气体从其气体出口进入第一环形气室18,与通入的气化剂混合后通过环形布风板17上的布风孔均匀布入第一反应室10中,共同气化燃料颗粒;而固体从第一气固分离器21的固体出口排出并再次落入第二反应室20中循环反应。作为另一个实施例,环形布风板17向反应器本体中心轴线延伸出第一环形气室18外,第一气固分离器21的顶面、第二反应室20的内壁与环形布风板17靠近反应器本体中心轴线的下端面之间形成一个腔室,第一气固分离器21的气体出口位于该腔室内,经过分离后的气体通过环形布风板17上的布风孔布入第一反应室10后再与通入的气化剂混合共同参与气化反应。
[0046]
作为优选实施例,第一气固分离器21的横截面为正方形且其内部具有圆筒状腔室,这种结构有利于离心过程中颗粒在内壁的摩擦破碎,并有利于增大内部腔室体积,延长颗粒的停留破碎时间,同时外部具有一定棱角的方形结构有利于拦截第二反应室20中的颗粒。其内壁材料采用耐磨的刚玉莫来石,一方面提高该分离器的分离效率,另一方面增大分离器中颗粒与筒壁的摩擦,有利于颗粒粒径的减小和进一步的气化反应。
[0047]
作为优选实施例,连接第一通气口13、第二通气口和第三通气口的管道上均设置有流量控制阀,用于控制气化剂和氧化剂的流速,有助于实现不同粒径大小颗粒的筛分。
[0048]
继续参见图1,本实施例气化反应器还包括换热装置,反应器本体还包括冷渣室40,冷渣室40位于第三反应室30的下方且与第三反应室30连通,反应后剩余的渣块通过布风板22与第三反应室30侧壁之间的环形缝隙落入冷渣室40中。冷渣室40的侧壁上设置有换
热介质进口41和至少一个换热介质出口42,换热介质进口41连接换热装置的出口,换热介质出口42连接换热装置的进口;冷渣室40的底部设置有排渣口43,用于排出换热后的渣块。
[0049]
具体地,换热装置包括高温换热器50和低温换热器60,冷渣室40的侧壁上沿竖直方向设置有两个换热介质出口42,位于上方的换热介质出口42与高温换热器50的热流进口连通,位于下方的换热介质出口42与低温换热器60的热流进口连通,低温换热器60的热流进口还与高温换热器50的冷流出口连通,高温换热器50的热流出口与第三通气口连通,低温换热器60的热流出口与第二通气口连通,低温换热器60的冷流出口与换热介质进口41连通。高温换热器50的冷流进口通入水蒸气,经过换热后形成高温的水蒸气,用作反应器中的气化剂;低温换热器60的冷流进口通入氧气,经过换热后形成高温的氧气,用作反应器中的氧化剂。
[0050]
本实施例气化反应器还包括第二气固分离器70和余热回收装置80,第二气固分离器70的进口与出气口12连通,第二气固分离器70的气体出口与余热回收装置80的进口连通。具体地,余热回收装置80可以为蒸汽发生器,通过吸收反应器排出气体的热量,将蒸汽发生器中的水加热成水蒸气,余热回收装置80的水蒸气出口可以连通高温换热器50的冷流进口,经过高温加热后作为气化剂而得到有效利用。
[0051]
下面对本发明气化反应器的工作过程进行说明,该气化反应器具体工作过程如下:
[0052]
宽筛分原料从进料口11落下,由于集气罩14的阻挡而向四周均匀分散,随后落入到第一反应室10中,其中的细小颗粒会被来自环形布风板17上的布风孔布入的气化剂气流以及来自第二反应室20的上升气流携带,发生气化反应并流向集气罩14;同时,集气罩14底部的百叶窗片16会将其中一部分较大的颗粒拦截下来,继续进行进一步气化;
[0053]
无法被气流携带的粗大颗粒会沿着倾斜的环形布风板17滑入第二反应室20中,并随着颗粒床层向下移动,在此过程中,与通入的氧化剂接触发生氧化反应,释放出热量,产生的气体上升进入第一反应室10,最终被集气罩14捕集;同时,反应完全的颗粒由于温度较高会粘结成尺寸较大的渣块;
[0054]
在布风板22的导流作用下,第二反应室20底部的物料进入到第三反应室30中,其中反应完全的渣块通过环形缝隙继续落入冷渣室40中,未反应完全的颗粒被通入的气化剂流化,并继续发生气化反应;第三反应室30中携带颗粒的气流进入到第一气固分离器21,利用离心作用进行气固分离,其中的气体在第一环形气室18中与通入的气化剂混合后通过环形布风板17进入到第一反应室10中,并最终被集气罩14捕集,其中的固体颗粒则会因与第一气固分离器21粗糙内壁的接触摩擦而粒径变小,分离下来的颗粒再次落入第二反应室20;如此经过多次气化、氧化反应,直到反应完全;
[0055]
集气罩14捕集的气化气先经过第二气固分离器70除尘,再经过蒸汽发生器进行余热回收,产生气化所需的水蒸气,并得到合成气产品;
[0056]
在反应器底部的冷渣室40中,换热介质吸收渣块的显热而被加热,加热后的换热介质中位于冷渣室40内上方的温度较高并形成高温换热介质,加热后的换热介质中位于冷渣室40内下方的温度较低并形成相对的低温换热介质,其中高温换热介质用于高温换热器50对来自蒸汽发生器的水蒸气进行再热,降温后的高温换热介质与低温换热介质一起用于低温换热器60对氧气进行预热,冷却后的渣块从排渣口43排出,低温换热器60中出来的换
热介质再通入冷渣室40中,实现换热介质的循环利用。
[0057]
本领域的技术人员容易理解,以上所述仅为本发明的较佳实施例而已,并不用以限制本发明,凡在本发明的精神和原则之内所作的任何修改、等同替换和改进等,均应包含在本发明的保护范围之内。