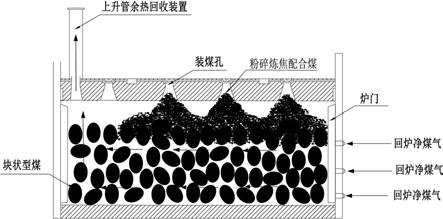
1.本发明属于焦化技术领域,具体涉及一种基于焦炉炭化室内深度脱硫的炼焦方法。
背景技术:
2.当前,钢铁行业成为了大气污染治理的“主战场”,近年来,我国通过采取结构优化、重点地区企业异地搬迁、强化末端污染治理等措施,钢铁行业大气污染物减排工作取得重要进展,但是随着国家环保要求的进一步提高,钢铁行业超低排放改造迫在眉睫。目前的炼铁行业脱硫技术路线主要包括源头控制和燃烧后的末端治理,末端治理需在多点设置脱硫设施,同时,煤气燃烧后的废气量大,处理设施规模变大;采取源头控制,实施煤气精脱硫,减少燃气中的硫分,可大大降低末端治理的压力,省掉末端治理设施,同时随着烟气中硫分减少,酸露点温度也随之降低,排烟温度也可降低,可以提高煤气利用效率。综上可知,当前的治理技术主要聚焦在高炉煤气和焦炉煤气的精脱硫,煤气硫源头主要来自于炼焦过程,因此,要从根本上解决二氧化硫污染排放,必须由末端治理实现真正的源头整治,即深度脱除焦炭与焦炉煤气中的硫,这将大大减少末端脱硫工序的运营压力与经济负担。
3.目前的炼焦现状是:鉴于当前国际形势以及我国炼焦煤资源情况,优质炼焦煤资源供求矛盾长期存在,而且愈演愈烈。为扩大炼焦煤资源、保证生产稳定,以及降低成本,越来越多的焦化企业不得不采用硫含量较高的炼焦配合煤,结果造成焦炭与煤气中硫含量增加。这是因为在现行的炼焦工艺制度下,炼焦配合煤中60%的硫会转入焦炭,且主要以有机硫形态存在,难以脱除,最终进入高炉,转化为高炉煤气中的cos、cs2等,而高炉煤气精脱硫是当前的一个技术难点,高炉煤气燃烧后排放出so2污染物;而约40%的硫以h2s,cos、cs2、噻吩等形态进入荒煤气中形成焦炉煤气,而焦化目前的脱硫工艺主要以脱除无机h2s为主,焦炉煤气中有机硫含量增加,势必也造成焦炉煤气燃烧后烟气中so2超标,增加后续脱硫负荷。因此,开发一种深度脱除焦炭与焦炉煤气中有机硫的源头控制技术显得尤为重要。
4.公开号为cn1247740c的中国发明专利公开了一种炼焦过程焦炭脱硫方法,在结焦期从焦炉炭化室中下部向炭化室鼓入富氢元素气体实现焦炭降硫。公告号为cn1219850c的中国发明专利公开了一种炼焦过程中脱硫方法,该方法是在焦煤中加入固体有机物和可作为缚硫剂的冶金固体废弃物,采用现有的炼焦设备和炼焦工艺进行炼焦。胡德生(宝钢技术,2006年第4期,53
‑
55页)公开了一种煤气返回炼焦过程焦炭脱硫探索试验,对在半工业炭化室内进行炭化并进行的脱硫试验却未能取得成功。因此,在现有的炼焦工艺基础上,不论是顶装炼焦或是捣固炼焦,在煤热解成焦过程中,其孔隙有限,不可能提供顺畅的气流分布,也没有足够的气固反应比表面积,这将大大影响热解成焦脱硫过程,致使脱硫效果较差。
技术实现要素:
5.为克服上述缺陷,本发明的目的在于提供一种基于焦炉炭化室内深度脱硫的炼焦
方法,脱硫效果显著,从源头大大减少因焦炉煤气和高炉煤气燃烧而排放的so2污染物。
6.为实现上述目的,本发明采用如下技术方案:一种基于焦炉炭化室内深度脱硫的炼焦方法,包括以下步骤:(1)型煤制备工艺:将不同种类的单种炼焦煤配合成炼焦配合煤,粉碎,加入粘结剂、供氢剂和瘦化剂,混捏后在对辊成型机中挤压成型,干燥,制得块状型煤;(2)型煤热解脱硫工艺:采用山峰型装煤法将步骤(1)所得块状型煤装入炭化室内,在隔绝空气的炭化室内受两侧加热火道间接加热,进行炭化结焦处理;(3)焦炭脱硫余热回收工艺:在结焦末期,在火落温度之后0.5
‑
1h开始,从上升管对侧炉门上中下三处通入回炉净煤气,焦炭在加氢脱硫的同时得到冷却,出炉煤气进入上升管余热回收装置回收余热。
7.优选地,步骤(1)所述的炼焦配合煤配合方法为:按照重量百分比计,将15%
‑
23%气煤、13%
‑
20%的1/3焦煤、10%
‑
16%肥煤、27%
‑
40%焦煤、15%
‑
25%瘦煤进行配合,得到炼焦配合煤。
8.优选地,步骤(1)所述的粘结剂加入量为炼焦配合煤重量的5
‑
10%,所述的供氢剂加入量为炼焦配合煤重量的3
‑
5%,所述的瘦化剂加入量为炼焦配合煤重量的4
‑
6%。
9.优选地,步骤(1)所述的粘结剂为煤焦油、焦油渣和酸焦油,三者重量比为90:6
‑
8:2
‑
4。
10.优选地,步骤(1)所述的供氢剂为双酚a型环氧树脂与松木屑的混合,两者重量比为6
‑
8:2
‑
4,粒径≤3mm。
11.优选地,步骤(1)所述的瘦化剂为无烟煤,粒径≤1mm。
12.优选地,步骤(1)所述的块状型煤粒度为60
‑
80mm,抗压强度480
‑
500n/球,落下强度≥97%。
13.优选地,步骤(2)所述的山峰型装煤法步骤为:首先将步骤(1)制取的块状型煤从炭化室顶部的装煤孔自由落体装入炭化室,在离炭化室顶部200
‑
300mm时,采用平煤杆将块状型煤推平,而后除上升管附近一个装煤孔外,从其它装煤孔装入步骤(1)粉碎后的炼焦配合煤,直到煤粉满入装煤孔,停止装煤。
14.优选地,步骤(2)所述的炭化室的加热火道温度控制在1150
‑
1250℃。
15.优选地,步骤(3)所述的回炉净煤气是指经过了脱硫、脱氨、脱苯之后的煤气,温度50
‑
80℃,氢气体积浓度为50%
‑
60%,甲烷体积浓度为20%
‑
30%。
16.本发明的积极有益效果:1. 本发明在煤热解缩聚成焦过程中,由于供氢剂起到供氢作用,更有利于煤中硫加氢析出,且在析出后更易与氢自由基反应,从而生成更多的无机h2s,从焦炉煤气排出,有利于后续脱硫工艺的脱除,同时,选择不同热解温度的双酚a型环氧树脂与松木屑作为供氢剂,从而有利于在煤热解缩聚成焦整个过程中都能起到供氢作用,供氢时间长,脱硫显著。在结焦末期,利用回炉净煤气富含的甲烷和氢气,实现在炭化室与高温焦炭发生加氢脱硫反应,焦炭中的硫含量进一步降低,回炉净煤气的有机硫也部分加氢转化为无机h2s,同时回炉净煤气温度50
‑
80℃,使焦炭的温度得到一定程度的降低,有利于降低焦炭的烧损率,减少污染物排放。
17.本发明炼焦方法能从源头降低焦炉煤气中有机硫含量,这样不仅减轻后续焦炉煤
气精脱硫的负荷与难度,而且有利于降低后续煤气化学产品中硫含量,提高煤气化学产品质量;同时本发明获得的焦炭硫含量低,有利于降低高炉煤气中的硫含量,并减轻后续高炉煤气脱硫负荷。综上所述,本发明从源头大大减少因焦炉煤气和高炉煤气燃烧而排放的so2污染物,有利于环境保护。
18.2. 本发明采用块状型煤炼焦,克服了传统炼焦方式在结焦期内,煤焦颗粒之间孔隙少、分布不均等不利因素,整个炼焦过程本发明型煤或者型焦具有分布均匀的孔隙结构,使传统以传导为主的传热方式改变为以对流、传导为主的传热方式,从而有利于煤气与型煤或型焦的传热传质以及供氢脱硫反应,传热速率大大提高,脱硫效果显著,而且有利于降低火道加热温度,本发明的加热火道温度比常规的加热温度低100
‑
200℃,还缩短了结焦时间,大大降低炼焦能耗,有利于碳减排。同时,炼焦配合煤中还配入非炼焦用煤,如无烟煤,大大扩大了炼焦用煤的范围,降低了配煤成本,且提高了焦炭质量。
19.3. 本发明采用山峰型装煤法,改变传统炭化室顶部预留炉顶空间通道以提供煤气流通,除上升管下面外,在块状型煤上面铺盖上一层粉碎后的炼焦配合煤,炼焦配合煤以及成焦后的焦饼具有较好的不透气性,这样,一方面在结焦过程中,使得上升管对侧产生的荒煤气穿透整个炭化室横向,有利于对流换热及加氢脱硫,另一方面在结焦末期,回炉净煤气从上升管对侧炭化室炉门上中下进入,便于回炉净煤气穿透整个炭化室横向型焦之间,避免了回炉净煤气发生短路,使得回炉净煤气与型焦充分接触,保证了焦炭的脱硫效果,最终煤气从上升管下部空间汇聚,并经上升管导出。
20.4. 现有技术在炭化室底部或侧墙砖设置通气孔,回炉净煤气从通气孔进入,在炉子设计、砖型制造、以及砌炉都是非常麻烦的,特别是后期生产过程中,极易造成通气孔堵塞情况,维护检测十分困难。本发明在火落温度之后0.5
‑
1h开始,从上升管对侧炭化室炉门上中下三处通入回炉净煤气,火落温度是焦炭成熟的一个标志,在火落温度之后通入回炉煤气,对成焦过程不会产生影响,不会降低焦炭强度,而且从炉门上设置通气口便于制造,维护与检测。
附图说明
21.图1为本发明所使用的炭化室结构示意图。
具体实施方式
22.下面结合一些具体实施例对本发明进一步说明。
23.实施例1一种基于焦炉炭化室内深度脱硫的炼焦方法,包括以下步骤:(1)型煤制备工艺:将不同种类的单种炼焦煤配合成炼焦配合煤,粉碎,粉碎至粒度小于3mm的炼焦配合煤重量百分比达到80%以上,然后加入炼焦配合煤重量10%的粘结剂、4%的供氢剂和6%的瘦化剂,混捏后在对辊成型机中挤压成型,干燥,制得块状型煤,所得块状型煤粒度为60mm,抗压强度500n/球,落下强度为99%;(2)型煤热解脱硫工艺:参见图1,采用山峰型装煤法将步骤(1)所得块状型煤装入炭化室内,在隔绝空气的炭化室内受两侧加热火道间接加热,进行炭化结焦处理,加热火道温度控制在1250℃,结焦时间为17h,其中闷炉时间为3h;在结焦前期,型煤受热发生分解反
应,供氢剂热解时易产生活泼氢自由基,从而更易脱除煤中的硫,实现加氢脱硫,最终,随着温度的升高,发生以缩聚反应为主的过程,形成焦炭;(3)焦炭脱硫余热回收工艺:在结焦末期,在火落温度之后0.5h开始,从上升管对侧炉门上中下三处通入50℃回炉净煤气,回炉净煤气主要成分为氢气体积浓度为55%,甲烷体积浓度为30%,加氢脱硫2.5h,在焦炭加氢脱硫的同时得到冷却。
24.结焦结束后,将焦炭从炭化室推出,干熄后取所制代表性焦炭,测定其硫含量并计算焦炭中硫转化率,同时测定焦炭反应性与反应后强度;出炉煤气进入上升管余热回收装置回收余热,出炉煤气冷凝后测定h2s的含量,计算出炉煤气h2s中硫的转化率。
25.优选地,步骤(1)所述的炼焦配合煤配合方法为:按照重量百分比计,将15%气煤、20%的1/3焦煤、10%肥煤、37%焦煤、18%瘦煤进行配合,得到炼焦配合煤。
26.优选地,步骤(1)所述的粘结剂为煤焦油、焦油渣和酸焦油,三者重量比为90:6:4。
27.优选地,步骤(1)所述的供氢剂为双酚a型环氧树脂与松木屑的混合,两者重量比为7:3,粒径≤3mm。
28.优选地,步骤(1)所述的瘦化剂为无烟煤,粒径≤1 mm。
29.优选地,步骤(2)所述的山峰型装煤法步骤为:首先将步骤(1)制取的块状型煤从炭化室顶部的装煤孔自由落体装入炭化室,在离炭化室顶部200mm时,采用平煤杆将块状型煤推平,而后除上升管附近一个装煤孔外,从其它装煤孔装入步骤(1)粉碎后且未加各种添加剂的炼焦配合煤,直到煤粉满入装煤孔,停止装煤。
30.实施例2一种基于焦炉炭化室内深度脱硫的炼焦方法,包括以下步骤:(1)型煤制备工艺:将不同种类的单种炼焦煤配合成炼焦配合煤,粉碎,粉碎至粒度小于3mm的炼焦配合煤重量百分比达到80%以上,然后加入炼焦配合煤重量8%的粘结剂、5%的供氢剂和5%的瘦化剂,混捏后在对辊成型机中挤压成型,干燥,制得块状型煤,块状型煤粒度为80mm,抗压强度495n/球,落下强度为98%;(2)型煤热解脱硫工艺:参见图1,采用山峰型装煤法将步骤(1)所得块状型煤装入炭化室内,在隔绝空气的炭化室内受两侧加热火道间接加热,进行结焦处理,加热火道温度控制在1250℃,结焦时间为17h,其中闷炉时间为2.5h;在结焦前期,型煤受热发生分解反应,供氢剂热解时易产生活泼氢自由基,从而更易脱除煤中的硫,实现加氢脱硫,最终,随着温度的升高,发生以缩聚反应为主的过程,形成焦炭;(3)焦炭脱硫余热回收工艺:在结焦末期,在火落温度之后1h开始,从上升管对侧炉门上中下三处通入60℃的回炉净煤气,回炉净煤气主要成分为氢气体积浓度为55%,甲烷体积浓度为30%,加氢脱硫1.5h,结焦结束后,在焦炭加氢脱硫的同时得到冷却。
31.结焦结束后,将焦炭从炭化室推出,干熄后取所制代表性焦炭,测定其硫含量并计算焦炭中硫转化率,同时测定焦炭反应性与反应后强度;出炉煤气进入上升管余热回收装置回收余热,出炉煤气冷凝后测定h2s的含量,计算出炉煤气h2s中硫的转化率。
32.优选地,步骤(1)所述的炼焦配合煤配合方法为:按照重量百分比计,将18%气煤、15%的1/3焦煤、12%肥煤、30%焦煤、25%瘦煤进行配合,得到炼焦配合煤。
33.优选地,步骤(1)所述的粘结剂为煤焦油、焦油渣和酸焦油,三者重量比为90:8:2。
34.优选地,步骤(1)所述的供氢剂为双酚a型环氧树脂与松木屑的混合,两者重量比
为6:4,粒径≤3mm。
35.优选地,步骤(1)所述的瘦化剂为无烟煤,粒径≤1mm。
36.优选地,步骤(2)所述的山峰型装煤法步骤为:首先将步骤(1)制取的块状型煤从炭化室顶部的装煤孔自由落体装入炭化室,在离炭化室顶部300mm时,采用平煤杆将块状型煤推平,而后除上升管附近一个装煤孔外,从其它装煤孔装入步骤(1)粉碎后且未加各种添加剂的炼焦配合煤,直到煤粉满入装煤孔,停止装煤。
37.实施例3一种基于焦炉炭化室内深度脱硫的炼焦方法,包括以下步骤:(1)型煤制备工艺:将不同种类的单种炼焦煤配合成炼焦配合煤,粉碎,粉碎至粒度小于3mm的炼焦配合煤重量百分比达到80%以上,然后加入炼焦配合煤重量6%的粘结剂、5%的供氢剂和5%的瘦化剂,混捏后在对辊成型机中挤压成型,干燥,制得块状型煤,块状型煤粒度为70mm,抗压强度490n/球,落下强度为97%;(2)型煤热解脱硫工艺:参见图1,采用山峰型装煤法将步骤(1)所得块状型煤装入炭化室内,在隔绝空气的炭化室内受两侧加热火道间接加热,进行结焦处理,加热火道温度控制在1250℃,结焦时间为17h,其中闷炉时间为2.5h;在结焦前期,型煤受热发生分解反应,供氢剂热解时易产生活泼氢自由基,从而更易脱除煤中的硫,实现加氢脱硫,最终,随着温度的升高,发生以缩聚反应为主的过程,形成焦炭;(3)焦炭脱硫余热回收工艺:在结焦末期,在火落温度之后0.5h开始,从上升管对侧炉门上中下三处通入70℃的回炉净煤气,煤气主要成分为氢气体积浓度55%,甲烷体积浓度为30%,加氢脱硫2h,在焦炭加氢脱硫的同时得到冷却。
38.结焦结束后,将焦炭从炭化室推出,干熄后取所制代表性焦炭,测定其硫含量并计算焦炭中硫转化率,同时测定焦炭反应性与反应后强度;出炉煤气进入上升管余热回收装置回收余热,出炉煤气冷凝后测定h2s的含量,计算出炉煤气h2s中硫的转化率。
39.优选地,步骤(1)所述的炼焦配合煤配合方法为:按照重量百分比计,将20%气煤、16%的1/3焦煤、12%肥煤、35%焦煤、17%瘦煤进行配合,得到炼焦配合煤。
40.优选地,步骤(1)所述的粘结剂为煤焦油、焦油渣和酸焦油,三者重量比为90:7:3。
41.优选地,步骤(1)所述的供氢剂为双酚a型环氧树脂与松木屑的混合,两者重量比为7:3,粒径≤3mm。
42.优选地,步骤(1)所述的瘦化剂为无烟煤,粒径≤1mm。
43.优选地,步骤(2)所述的山峰型装煤法步骤为:首先将步骤(1)制取的块状型煤从炭化室顶部的装煤孔自由落体装入炭化室,在离炭化室顶部250mm时,采用平煤杆将块状型煤推平,而后除上升管附近一个装煤孔外,从其它装煤孔装入步骤(1)粉碎后且未加各种添加剂的炼焦配合煤,直到煤粉满入装煤孔,停止装煤。
44.实施例4一种基于焦炉炭化室内深度脱硫的炼焦方法,包括以下步骤:(1)型煤制备工艺:将不同种类的单种炼焦煤配合成炼焦配合煤,粉碎,粉碎至粒度小于3mm的炼焦配合煤重量百分比达到80%以上,然后加入炼焦配合煤重量9%的粘结剂、4%的供氢剂和4%的瘦化剂,混捏后在对辊成型机中挤压成型,干燥,制得块状型煤,块状型煤粒度为60mm,抗压强度500n/球,落下强度为99%;
(2)型煤热解脱硫工艺:参见图1,采用山峰型装煤法将步骤(1)所得块状型煤装入炭化室内,在隔绝空气的炭化室内受两侧加热火道间接加热,进行结焦处理,加热火道温度控制在1250℃,结焦时间为17h,其中闷炉时间为2.5h;在结焦前期,型煤受热发生分解反应,供氢剂热解时易产生活泼氢自由基,从而更易脱除煤中的硫,实现加氢脱硫,最终,随着温度的升高,发生以缩聚反应为主的过程,形成焦炭;(3)焦炭脱硫余热回收工艺:在结焦末期,在火落温度之后0.5h开始,从上升管对侧炉门上中下三处通入70℃回炉净煤气,煤气主要成分为氢气体积浓度为60%,甲烷体积浓度25%,加氢脱硫2h,在焦炭加氢脱硫的同时得到冷却。
45.结焦结束后,将焦炭从炭化室推出,干熄后取所制代表性焦炭,测定其硫含量并计算焦炭中硫转化率,同时测定焦炭反应性与反应后强度;出炉煤气进入上升管余热回收装置回收余热,出炉煤气冷凝后测定h2s的含量,计算出炉煤气h2s中硫的转化率。
46.优选地,步骤(1)所述的炼焦配合煤配合方法为:按照重量百分比计,将23%气煤、13%的1/3焦煤、16%肥煤、33%焦煤、15%瘦煤进行配合,得到炼焦配合煤。
47.优选地,步骤(1)所述的粘结剂为煤焦油、焦油渣和酸焦油,三者重量比为90:6:4。
48.优选地,步骤(1)所述的供氢剂为双酚a型环氧树脂与松木屑的混合,两者重量比为8:2,粒径≤3mm。
49.优选地,步骤(1)所述的瘦化剂为无烟煤,粒径≤1mm。
50.优选地,步骤(2)所述的山峰型装煤法步骤为:首先将步骤(1)制取的块状型煤从炭化室顶部的装煤孔自由落体装入炭化室,在离炭化室顶部300mm时,采用平煤杆将块状型煤推平,而后除上升管附近一个装煤孔外,从其它装煤孔装入步骤(1)粉碎后且未加各种添加剂的炼焦配合煤,直到煤粉满入装煤孔,停止装煤。
51.实施例5一种基于焦炉炭化室内深度脱硫的炼焦方法,包括以下步骤:(1)型煤制备工艺:将不同种类的单种炼焦煤配合成炼焦配合煤,粉碎,粉碎至粒度小于3mm的炼焦配合煤重量百分比达到80%以上,然后加入炼焦配合煤重量5%的粘结剂、5%的供氢剂和6%的瘦化剂,混捏后在对辊成型机中挤压成型,干燥,制得块状型煤,块状型煤粒度为80mm,抗压强度480n/球,落下强度为97%;(2)型煤热解脱硫工艺:参见图1,采用山峰型装煤法将步骤(1)所得块状型煤装入炭化室内,在隔绝空气的炭化室内受两侧加热火道间接加热,进行结焦处理,加热火道温度控制在1150℃,结焦时间为18h,其中闷炉时间为3h;在结焦前期,型煤受热发生分解反应,供氢剂热解时易产生活泼氢自由基,从而更易脱除煤中的硫,实现加氢脱硫,最终,随着温度的升高,发生以缩聚反应为主的过程,形成焦炭;(3)焦炭脱硫余热回收工艺:在结焦末期,在火落温度之后1h开始,从上升管对侧炉门上中下三处通入80℃的回炉净煤气,煤气主要成分为氢气体积浓度为50%,甲烷体积浓度为30%,加氢脱硫2h,在焦炭加氢脱硫的同时得到冷却。
52.结焦结束后,将焦炭从炭化室推出,干熄后取所制代表性焦炭,测定其硫含量并计算焦炭中硫转化率,同时测定焦炭反应性与反应后强度;出炉煤气进入上升管余热回收装置回收余热,出炉煤气冷凝后测定h2s的含量,计算出炉煤气h2s中硫的转化率。
53.优选地,步骤(1)所述的炼焦配合煤配合方法为:按照重量百分比计,将16%气煤、
14%的1/3焦煤、15%肥煤、40%焦煤、15%瘦煤进行配合,得到炼焦配合煤。
54.优选地,步骤(1)所述的粘结剂为煤焦油、焦油渣和酸焦油,三者重量比为90:8:2。
55.优选地,步骤(1)所述的供氢剂为双酚a型环氧树脂与松木屑的混合,两者重量比为7:3,粒径≤3mm。
56.优选地,步骤(1)所述的瘦化剂为无烟煤,粒径≤1mm。
57.优选地,步骤(2)所述的山峰型装煤法步骤为:首先将步骤(1)制取的块状型煤从炭化室顶部的装煤孔自由落体装入炭化室,在离炭化室顶部200mm时,采用平煤杆将块状型煤推平,而后除上升管附近一个装煤孔外,从其它装煤孔装入步骤(1)粉碎后且未加各种添加剂的炼焦配合煤,直到煤粉满入装煤孔,停止装煤。
58.实施例6一种基于焦炉炭化室内深度脱硫的炼焦方法,包括以下步骤:(1)型煤制备工艺:将不同种类的单种炼焦煤配合成炼焦配合煤,粉碎,粉碎至粒度小于3mm的炼焦配合煤重量百分比达到80%以上,然后加入炼焦配合煤重量7%的粘结剂、3%的供氢剂和6%的瘦化剂,混捏后在对辊成型机中挤压成型,干燥,制得块状型煤,块状型煤粒度为70mm,抗压强度490n/球,落下强度为97%;(2)型煤热解脱硫工艺:参见图1,采用山峰型装煤法将步骤(1)所得块状型煤装入炭化室内,在隔绝空气的炭化室内受两侧加热火道间接加热,进行结焦处理,加热火道温度控制在1200℃,结焦时间为18h,其中闷炉时间为3h;在结焦前期,型煤受热发生分解反应,供氢剂热解时易产生活泼氢自由基,从而更易脱除煤中的硫,实现加氢脱硫,最终,随着温度的升高,发生以缩聚反应为主的过程,形成焦炭;(3)焦炭脱硫余热回收工艺:在结焦末期,在火落温度之后0.5h开始,从上升管对侧炉门上中下三处通入70℃的回炉净煤气,煤气主要成分为氢气体积浓度为55%,甲烷体积浓度为20%,加氢脱硫2.5 h,在焦炭加氢脱硫的同时得到冷却。
59.结焦结束后,将焦炭从炭化室推出,干熄后取所制代表性焦炭,测定其硫含量并计算焦炭中硫转化率,同时测定焦炭反应性与反应后强度;出炉煤气进入上升管余热回收装置回收余热,出炉煤气冷凝后测定h2s的含量,计算出炉煤气h2s中硫的转化率。
60.优选地,步骤(1)所述的炼焦配合煤配合方法为:按照重量百分比计,将20%气煤、18%的1/3焦煤、15%肥煤、27%焦煤、20%瘦煤进行配合,得到炼焦配合煤。
61.优选地,步骤(1)所述的粘结剂为煤焦油、焦油渣和酸焦油,三者重量比为90:7:3。
62.优选地,步骤(1)所述的供氢剂为双酚a型环氧树脂与松木屑的混合,两者重量比为8:2,粒径≤3mm。
63.优选地,步骤(1)所述的瘦化剂为无烟煤,粒径≤1mm。
64.优选地,步骤(2)所述的山峰型装煤法步骤为:首先将步骤(1)制取的块状型煤从炭化室顶部的装煤孔自由落体装入炭化室,在离炭化室顶部250mm时,采用平煤杆将块状型煤推平,而后除上升管附近一个装煤孔外,从其它装煤孔装入步骤(1)粉碎后且未加各种添加剂的炼焦配合煤,直到煤粉满入装煤孔,停止装煤。
65.对比实施例1一种基于焦炉炭化室内深度脱硫的炼焦方法,包括以下步骤:(1)混合煤制备工艺:将不同种类的单种炼焦煤配合成炼焦配合煤,粉碎,粉碎至
粒度小于3mm的炼焦配合煤重量百分比达到80%以上,然后加入炼焦配合煤重量6%的粘结剂、5%的供氢剂和5%的瘦化剂,充分搅拌混合均匀;(2)热解脱硫工艺:将步骤(1)所得混合煤从炭化室顶部的装煤孔自由落体装入炭化室,在离炭化室顶部250mm时,采用平煤杆将混合煤推平,在隔绝空气的炭化室内受两侧加热火道间接加热,进行炭化结焦处理,加热火道温度控制在1300℃,结焦时间为19h,其中闷炉时间为2.5h;在结焦前期,煤粉受热发生分解反应,供氢剂热解时易产生活泼氢自由基,从而更易脱除煤中的硫,实现加氢脱硫,最终,随着温度的升高,发生以缩聚反应为主的过程,形成焦炭;(3)焦炭脱硫余热回收工艺:在结焦末期,在火落温度之后0.5h开始,从上升管对侧炉门上中下三处通入70℃的煤气,煤气主要成分为氢气体积浓度为55%,甲烷体积浓度为30%,加氢脱硫2h,在焦炭加氢脱硫的同时得到冷却。
66.结焦结束后,将焦炭从炭化室推出,干熄后取所制代表性焦炭,测定其硫含量并计算焦炭中硫转化率,同时测定焦炭反应性与反应后强度;出炉煤气进入上升管余热回收装置回收余热,出炉煤气冷凝后测定h2s的含量,计算出炉煤气h2s中硫的转化率。
67.优选地,步骤(1)所述的炼焦配合煤配合方法为:按照重量百分比计,将20%气煤、16%的1/3焦煤、12%肥煤、35%焦煤、17%瘦煤进行配合,得到炼焦配合煤。
68.优选地,步骤(1)所述的粘结剂为煤焦油、焦油渣和酸焦油,三者重量比为90:7:3。
69.优选地,步骤(1)所述的供氢剂为双酚a型环氧树脂与松木屑的混合,两者重量比为7:3,粒径≤3mm。
70.优选地,步骤(1)所述的瘦化剂为无烟煤,粒径≤1mm。
71.对比实施例2一种基于焦炉炭化室内深度脱硫的炼焦方法,包括以下步骤:(1)配合煤制备工艺:将不同种类的单种炼焦煤配合成炼焦配合煤,粉碎,粉碎至粒度小于3mm的炼焦配合煤重量百分比达到80%以上,然后充分搅拌混合。
72.(2)热解脱硫工艺:将步骤(1)所得炼焦配合煤从炭化室顶部的装煤孔自由落体装入炭化室,在离炭化室顶部250mm时,采用平煤杆将煤粉推平,在隔绝空气的炭化室内受两侧加热火道间接加热,进行炭化结焦处理,加热火道温度控制在1300℃,结焦时间为19h,其中闷炉时间为2.5h;在结焦前期,煤粉受热发生分解反应,最终,随着温度的升高,发生以缩聚反应为主的过程,形成焦炭;(3)焦炭脱硫余热回收工艺:在结焦末期,在火落温度之后0.5h开始,从上升管对侧炉门上中下三处通入70℃的回炉净煤气,回炉净煤气主要成分为氢气体积浓度为55%,甲烷体积浓度为30%,加氢脱硫2h,在焦炭加氢脱硫的同时得到冷却。
73.结焦结束后,将焦炭从炭化室推出,干熄后取所制代表性焦炭,测定其硫含量并计算焦炭中硫转化率,同时测定焦炭反应性与反应后强度;出炉煤气进入上升管余热回收装置回收余热,出炉煤气冷凝后测定h2s的含量,计算出炉煤气h2s中硫的转化率。
74.优选地,步骤(1)所述的炼焦配合煤配合方法为:按照重量百分比计,将20%气煤、16%的1/3焦煤、12%肥煤、35%焦煤、17%瘦煤进行配合,得到炼焦配合煤。
75.对比实施例3一种基于焦炉炭化室内深度脱硫的炼焦方法,包括以下步骤:
(1)配合煤制备工艺:将不同种类的单种炼焦煤配合成炼焦配合煤,粉碎,粉碎至粒度小于3mm的炼焦配合煤重量百分比达到80%以上,然后充分搅拌混合。
76.(2)热解脱硫工艺:将步骤(1)所得炼焦配合煤从炭化室顶部的装煤孔自由落体装入炭化室,在离炭化室顶部250mm时,采用平煤杆将煤粉推平,在隔绝空气的炭化室内受两侧加热火道间接加热,进行炭化结焦处理,加热火道温度控制在1350℃,结焦时间为19h,其中闷炉时间为2.5h;在结焦前期,煤粉受热发生分解反应,随着温度的升高,发生以缩聚反应为主的过程,形成焦炭。
77.结焦结束后,将焦炭从炭化室推出,干熄后取所制代表性焦炭,测定其硫含量并计算焦炭中硫转化率,同时测定焦炭反应性与反应后强度;出炉煤气进入上升管余热回收装置回收余热,出炉煤气冷凝后测定h2s的含量,计算出炉煤气h2s中硫的转化率。
78.优选地,步骤(1)所述的炼焦配合煤配合方法为:按照重量百分比计,将20%气煤、16%的1/3焦煤、12%肥煤、35%焦煤、17%瘦煤进行配合,得到炼焦配合煤。
79.将本发明实施例1
‑
6以及对比实施例1
‑
3检测结果列在下表 1。
80.表1 本发明炼焦检测结果表中:焦炭中硫转化率=(焦炭中s含量/炼焦配合煤中s含量)
×
100%;出炉煤气h2s中硫转化率=出炉煤气h2s中硫含量/炼焦配合煤中s含量
×
100%。
81.由表1可知,对比实施例1炼焦配合煤不挤压成块状型煤,煤颗粒之间孔隙少、分布不均,且采用常规装煤方法,降低了供氢剂的供氢反应以及焦炭的加氢脱硫反应,焦炭中硫平均转化率高,即焦炭中硫重量百分比较高,出炉煤气h2s中硫转化率降低,即出炉煤气中h2s重量百分比降低。对比实施例2炼焦配合煤不挤压成块状型煤,并且不加入粘结剂、加氢剂和瘦化剂,采用常规装煤方法,仅通过焦炭的加氢脱硫的效果不明显,焦炭中硫重量百分比更高,出炉煤气中h2s重量百分比更低。对比实施例3在对比实施例2的基础上,不通入回炉净煤气焦炭脱硫,在现有炼焦工艺条件下仅依靠煤自身热解脱硫,脱硫效果更差。
82.本发明实施例1
‑
6采用块状型煤炼焦,并配合山峰装煤方法以及回炉净煤气焦炭脱硫方法,焦炭脱硫效果大大提高,焦炭中硫转化率低,出炉煤气中h2s中硫转化率高,同时焦炭质量得到改善,加热火道温度降低,结焦时间得以缩短,达到节能降耗,实现了污染物
源头治理,大大减少末端脱硫工序的运营压力与经济负担,有利于钢铁企业超低排放。
83.最后说明的是,以上实施例仅用以说明本发明的技术方案而非限制,本领域普通技术人员对本发明的技术方案所做的其他修改或者等同替换,只要不脱离本发明技术方案的精神和范围,均应涵盖在本发明的权利要求范围当中。