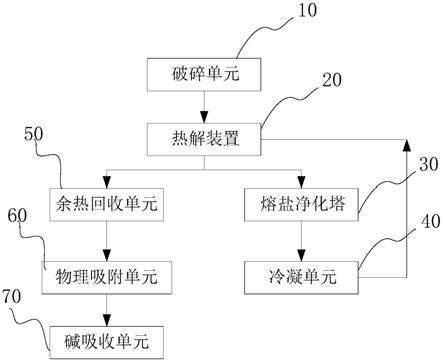
1.本实用新型涉及废线路板资源化处理技术领域,具体而言,涉及一种废线路板热解脱溴净化装置。
背景技术:
2.中国现已成为世界第二大线路板生产国,废旧线路板的增长率超过任何其他类型的废弃物。废线路板中有丰富的金属、塑料、玻璃纤维等可回收资源,金属含量高达40%以上,金属品位是普通矿物中金属品位的几十倍至上百倍,具有很高回收价值。同时废线路板中的重金属和溴化阻燃剂等有害物质也会导致废线路板回收方面的困难,如果处理不当,会造成环境污染,严重浪费资源。
3.废线路板传统处理方法主要有机械物理法、湿法浸出和火法冶炼等,其均主要针对废线路板中有价金属,对于非金属部分没有进行充分利用,造成资源浪费的同时产生大量二次污染。近年来,低温热解技术已广泛应用于废线路板的处理,其能够将金属、有机物和玻璃纤维进行有效分离,但是,废线路板中具有含卤素的阻燃剂,导致热解产物中含有大量的含溴物质,严重阻碍了热解产物的进一步应用。
4.最常用的脱溴方法为添加剂与废线路板共热解,比如分别添加naoh、na2co3、cao、zno、5a分子筛和13x分子筛与废线路板共热解,添加剂大部分为碱性物质,结果表明强碱性无机物能显著改变溴代酚和溴化苯乙烯的产量,但给热解渣资源回收再利用带来极大的困难。cn103846272a提供一种加入naoh等碱性物质实现热解油净化,但热解后脱溴往往忽略了不凝热解气的资源再利用。专利cn 109539266 a将热解油气进行高温燃烧后骤冷避免二噁英生成,需补充额外燃料补热,能耗高,后续烟气处理成本高,设备腐蚀严重。
5.基于以上原因,有必要提供一种脱溴更有效、无需在热解阶段加入添加剂的废线路板热解脱溴净化工艺。
技术实现要素:
6.本实用新型的主要目的在于提供一种废线路板热解脱溴净化装置,以解决现有技术中热解处理废线路板时,脱溴效果欠佳、或者引入添加剂容易导致热解残渣资源化处理难度增加的问题。
7.为了实现上述目的,根据本实用新型的一个方面,提供了一种废线路板热解脱溴净化装置,其包括:破碎单元,用于破碎废线路板形成破碎料;热解装置,具有破碎料入口、热解油气出口和热解残渣出口,破碎料入口与破碎单元相连通,热解装置用于对破碎料进行热解以生成热解油气和热解残渣;熔盐净化塔,具有脱溴气出口、熔盐入口和热解油气入口,热解油气入口与热解油气出口相连通,熔盐入口用于向熔盐净化塔内部通入氢氧化钠和/或氢氧化钾熔盐,熔盐净化塔用于使热解油气与熔盐接触并进行脱溴处理以得到溴盐和脱溴气;冷凝单元,其具有脱溴气入口、热解油出口和不凝气出口;烧嘴与不凝气出口相连;余热回收单元,与燃烧烟气出口相连。具体地,热解装置包括:热解炉体,具有破碎料入
口、热解油气出口、热解残渣出口和惰性气体入口;可旋转中心轴,位于热解炉体内中心轴处;电机,位于热解炉体外侧并与可旋转中心轴的一端通过联轴器连接,用于驱动可旋转中心轴进行旋转;螺旋叶片,固定设置在可旋转中心轴上;保温夹套,其设置在热解炉体的外部,且保温夹套与热解炉体的外壁之间形成燃烧腔,燃烧腔中设置有烧嘴,燃烧腔还设置有燃烧烟气出口。
8.进一步地,熔盐净化塔包括:塔体,具有脱溴气出口、熔盐入口和热解油气入口;布盐盘,设置在塔体内部,布盐盘开设有多个布盐孔,布盐盘用于承接熔盐入口进入的熔盐;一个或多个塔板,由上至下依次设置在塔体内部的低于布盐盘的位置,塔板开设有多个漏盐孔;其中,脱溴气出口位于布盐盘的上方,热解油气入口位于塔板的下方。
9.进一步地,塔体底部还设置有熔盐出口,熔盐净化塔还包括:输盐管路,其一端与熔盐出口相连,其另一端通过熔盐入口延伸至布盐盘上方;熔盐加热炉,设置在输盐管路,用于加热熔盐;泵体,设置在位于熔盐加热炉下游的输盐管路上。
10.进一步地,熔盐净化塔包括多个塔板,塔板固定设置在塔体内部,其一侧与塔体的内部侧壁之间具有流通通道。
11.进一步地,塔板朝向各自的流通通道倾斜向下设置,且位于流通通道的一侧设置有溢流堰;相邻两个塔板的倾斜方向相反。
12.进一步地,塔板向下倾斜的角度为2~10
°
。
13.进一步地,热解炉体的炉壁上还设置有热电偶。
14.进一步地,废线路板热解脱溴净化装置还包括:物理吸附单元,与余热回收单元的出口相连。
15.进一步地,废线路板热解脱溴净化装置还包括:碱吸收单元,与物理吸附单元的出口相连。
16.利用本实用新型提供的装置进行废线路板热解脱溴净化,是在将废线路板破碎热解后,采用熔盐净化塔进行脱溴处理。具体可将热解油气通入熔盐净化塔内部,通过与氢氧化钠和/或氢氧化钾熔盐进行接触,达到脱溴净化的目的。采用该装置处理废线路板,一方面具有较高的溴脱除率,一方面也无需在热解阶段在废线路板破碎料中加入naoh、na2co3、cao、zno等添加剂,因此不影响后续热解残渣的资源化回收。
附图说明
17.构成本技术的一部分的说明书附图用来提供对本实用新型的进一步理解,本实用新型的示意性实施例及其说明用于解释本实用新型,并不构成对本实用新型的不当限定。在附图中:
18.图1示出了根据本实用新型一种实施例的废线路板热解脱溴净化装置结构框图;
19.图2示出了根据本实用新型一种实施例的废线路板热解脱溴净化装置中熔盐净化塔的结构示意图;以及
20.图3示出了根据本实用新型一种实施例的废线路板热解脱溴净化装置中热解装置的结构示意图。
21.其中,上述附图包括以下附图标记:
22.10、破碎单元;20、热解装置;30、熔盐净化塔;40、冷凝单元;50、余热回收单元;60、
物理吸附单元;70、碱吸收单元;
23.201、破碎料入口;202、热解油气出口;203、热解残渣出口;204、惰性气体入口;205、燃烧烟气出口;206、氮气密封口;301、脱溴气出口;302、熔盐入口;303、热解油气入口;304、熔盐出口;305、排渣口;
24.21、热解炉体;22、可旋转中心轴;23、电机;231、联轴器;24、螺旋叶片;25、保温夹套;26、燃烧腔;261、烧嘴;27、热电偶;31、塔体;32、布盐盘;33、塔板;34、输盐管路;35、熔盐加热炉;36、泵体。
具体实施方式
25.需要说明的是,在不冲突的情况下,本技术中的实施例及实施例中的特征可以相互组合。下面将参考附图并结合实施例来详细说明本实用新型。
26.正如背景技术部分所描述的,现有技术中热解处理废线路板时,存在脱溴效果欠佳、或者引入添加剂容易导致热解残渣资源化处理难度增加的问题。
27.为了解决上述问题,本实用新型提供了一种废线路板热解脱溴净化装置,如图1所示,该装置包括破碎单元10、热解装置20、熔盐净化塔30、冷凝单元40和余热回收单元50。破碎单元10用于破碎废线路板形成破碎料;如图3所示,热解装置20具有破碎料入口201、热解油气出口202和热解残渣出口203,破碎料入口201与破碎单元10相连通,热解装置20用于对破碎料进行热解以生成热解油气和热解残渣;具体地,如图3所示,上述热解装置20包括热解炉体21、可旋转中心轴22、电机23、螺旋叶片24和保温夹套25,热解炉体21具有破碎料入口201、热解油气出口202、热解残渣出口203和惰性气体入口204;可旋转中心轴22位于热解炉体21内中心轴处;电机23位于热解炉体21外侧并与可旋转中心轴22的一端通过联轴器231连接,用于驱动可旋转中心轴22进行旋转;螺旋叶片24固定设置在可旋转中心轴22上;保温夹套25设置在热解炉体21的外部,且保温夹套25与热解炉体21的外壁之间形成燃烧腔26,燃烧腔26中设置有烧嘴261;燃烧腔26还设置有燃烧烟气出口205。如图2所示,熔盐净化塔30具有脱溴气出口301、熔盐入口302和热解油气入口303,热解油气入口303与热解油气出口202相连通,熔盐入口302用于向熔盐净化塔30内部通入氢氧化钠和/或氢氧化钾熔盐,熔盐净化塔30用于使热解油气与熔盐接触并进行脱溴处理以得到溴盐和脱溴气。冷凝单元40具有脱溴气入口、热解油出口和不凝气出口,烧嘴261与不凝气出口相连。余热回收单元50与燃烧烟气出口205相连。
28.利用本实用新型提供的装置进行废线路板热解脱溴净化,是在将废线路板破碎热解后,采用熔盐净化塔进行脱溴处理。具体可将热解油气通入熔盐净化塔内部,通过与氢氧化钠和/或氢氧化钾熔盐进行接触,达到脱溴净化的目的。采用该装置处理废线路板,一方面具有较高的溴脱除率,一方面也无需在热解阶段在废线路板破碎料中加入naoh、na2co3、cao、zno等添加剂,因此不影响后续热解残渣的资源化回收。此外,热解过程中产生的热解残渣可达到冶炼原料标准,无需预处理直接用于冶炼。
29.需说明的是,利用该热解装置20对废线路板破碎料进行热解处理,具有更好的热解效果。具体地,不同于固定床热解炉或回转窑式热解炉,上述热解炉体21内部设置有可旋转中心轴22,其上固定设置有螺旋叶片24。当破碎料从破碎料入口201进入炉体后,能够在旋转的螺旋叶片24的带动作用下完成热解,因螺旋叶片24同时起到了搅拌和带动前行的作
用,使得破碎料得以更充分进行。
30.实际操作过程中,可旋转中心轴22通过联轴器231与电机23连接,实现了可旋转中心轴22的360
°
变速转动;轴上设置有螺旋叶片,使物料向前移动同时起到搅拌作用,使物料充分混合,受热均匀,热解充分。优选地,可旋转中心轴22的两端均设置有氮气密封口206,设置成氮气密封,以便于调整其压力大于炉内压力,防止热解油气从轴两端逸出。
31.利用烧嘴261可以将燃料(包括但不限于燃烧天然气等其他气体燃料)在燃烧腔26中进行燃烧以对热解炉体21进行供热和补热。炉体上设置的惰性气体入口204可向炉体内通入惰性气体(比如氮气),用于清洗炉体保证炉内惰性气氛。优选地,热解残渣出口203和热解油气出口202均设置在热解炉体21的相对于破碎料入口201的另一端,热解油气出口202设置在上方,热解残渣出口203设置在下方。优选地,破碎料入口201和热解残渣出口203均为双闸板氮气密封,防止上下料时空气进入炉内。优选地,燃烧腔26中设置有水平对称的两排烧嘴,用于燃烧返回的不凝气和/或天然气加热炉体。
32.废线路板热解脱溴净化装置还包括冷凝单元40,其具有脱溴气入口、热解油出口和不凝气出口;烧嘴261与不凝气出口相连。这样,可以将脱溴气体冷凝后分离的不凝气返回至热解装置中,利用烧嘴将其燃烧,实现净化后热解气返回热解过程燃烧供热,达成热解自热回用,节约能源。这样,能够进一步降低热解能耗。此处需要说明的是,正是由于本实用新型使用上述熔盐净化塔进行了热解油气的脱溴,具有较高的脱溴率,实现了热解油气充分净化,因此脱溴气中分离得到的不凝气才能够返回至热解过程进行补热。通过该装置,能够实现热解过程自热率高达99%,燃烧尾气无需经过高温燃烧、骤冷等工序进行二噁英脱除,尾气处理系统简单,同时减小腐蚀设备风险。冷凝单元40分离得到的热解油可直接作为燃料或进一步精制提炼。至此,本实用新型实现了废线路板全组分洁净化综合利用。
33.为了进一步处理燃烧腔26中产生的燃烧烟气,燃烧腔26还设置有燃烧烟气出口205,废线路板热解脱溴净化装置还包括余热回收单元50,以便于回收余热。
34.为了进一步提高脱溴效果,在一种优选的实施方式中,如图2所示,熔盐净化塔30包括塔体31、布盐盘32和一个或多个塔板33;塔体31具有脱溴气出口301、熔盐入口302和热解油气入口303;布盐盘32设置在塔体31内部,布盐盘32开设有多个布盐孔,布盐盘32用于承接熔盐入口302进入的熔盐;一个或多个塔板33由上至下依次设置在塔体31内部的低于布盐盘32的位置,塔板33开设有多个漏盐孔;其中脱溴气出口301位于布盐盘32的上方,热解油气入口303位于塔板33的下方。此处“多个”表示两个或两个以上。
35.如此设置,进入塔体31内部的naoh或koh的一种或两种的熔盐被承接在布盐盘32上,并通过多个布盐孔较为均匀地流出并流向向位于下方的塔板33,然后又通过各层塔板33上的漏盐孔继续向下流出,由此在各相邻的塔板33之间形成了液柱或液滴。而从塔体31下部进入的热解油气则能够在向上流动的过程中在每层塔板33之间与这些熔盐液柱或液滴充分接触,通过更为充分的反应实现高效脱溴,之后从顶部的脱溴气出口301排出即可。为了进一步提高热解油气和熔盐的接触面积,优选地,各层塔板33上的漏盐孔开孔率不大于40%,且开孔直径小于10mm。优选地,上述布盐盘32为水平设置,布盐孔的孔径<10mm,布盐盘32一端固定在塔体31内壁,一端设置有溢流堰。
36.在一种优选的实施方式中,塔体31底部还设置有熔盐出口304,熔盐净化塔30还包括输盐管路34、熔盐加热炉35、泵体36;输盐管路34其一端与熔盐出口304相连,其另一端通
过熔盐入口302延伸至布盐盘32上方;熔盐加热炉35设置在输盐管路34,用于加热熔盐;泵体36设置在位于熔盐加热炉35下游的输盐管路34上。这样,塔体31底部未反应完的熔盐可通过输盐管路34上的熔盐加热炉35进一步加热后返回塔体31上部,进行再次脱溴,起到循环利用的目的。当然,此期间也可由输盐管路34补充新鲜的熔盐。优选地,上述塔体31底部设置有熔盐沉淀池,用于承接上方落下的溴盐和未反应的熔盐,上述熔盐出口304设置在熔盐沉淀池靠上的位置,熔盐沉淀池下部与熔盐出口304相对的另一侧还具有排渣口305,用于排出脱溴反应的产物——溴盐沉淀渣。
37.在一种优选的实施方式中,熔盐净化塔30包括多个塔板33,塔板33固定设置在塔体31内部,其一侧与塔体31的内部侧壁之间具有流通通道。如此设置,下方进入的热解油气能够从这些流通通道进入各层塔板33中,与熔盐进行接触反应。为了进一步提高热解油气和熔盐的接触面积,以进一步提高脱溴率,优选地,塔板33朝向各自的流通通道倾斜向下设置,且位于流通通道的一侧设置有溢流堰;相邻两个塔板33的倾斜方向相反。这样一方面热解油气能够呈s型曲线逐渐向上流动,充分与塔板33之间的熔盐接触;另一方面将塔板33朝向各自的流通通道倾斜向下设置,则更有利于控制熔盐通过漏盐孔向下流动的速度,且熔盐能够在各塔板33上充分铺展开来。优选地,溢流堰的高度高于最远端的漏盐孔高度。优选地,塔板33向下倾斜的角度为2~10
°
。
38.在实际应用过程中,通过塔板33的数量及塔体31的高度等控制热解油气在塔体31内部的停留时间,优选停留时间为10~60s。优选上述塔体31由耐火材料及隔热材料组成。
39.上述热解过程中,热源可以为电加热或者燃烧天然气等燃料进行加热。优选地,为了便于监控热解过程中的温度情况,维持热解过程的稳定性,在一种优选的实施方式中,热解炉体21的炉壁上还设置有热电偶27。具体地,可以在热解炉体21的两侧分别设置多个热电偶,以监控不同区域的温度。
40.为了进一步处理燃烧腔26中产生的燃烧烟气,优选地,废线路板热解脱溴净化装置还包括物理吸附单元60和碱吸收单元70;物理吸附单元60与余热回收单元50的出口相连;碱吸收单元70与物理吸附单元60的出口相连。这样,通过将燃烧烟气依次进行余热回收、物理吸附(比如活性炭吸附)、碱吸收,即可完成热能回收和尾气净化达标排放。如前文所述,因热解过程、脱溴过程较为充分,且不凝气自热率较高,使得该燃烧烟气较为清洁,无需经过高温燃烧、骤冷等工序进行二噁英脱除,尾气处理简单,同时腐蚀性低。
41.根据本实用新型的另一方面,还提供了一种废线路板热解脱溴净化方法,其采用上述废线路板热解脱溴净化装置处理废线路板,该方法包括以下步骤:将废线路板热解在破碎单元10中进行破碎,得到破碎料;将破碎料在热解装置20中进行热解,得到热解油气和热解残渣;将热解油气通入熔盐净化塔30中与氢氧化钠和/或氢氧化钾熔盐接触,以进行脱溴处理,得到溴盐和脱溴气。
42.利用本实用新型提供的上述装置进行废线路板热解脱溴净化,是在将废线路板破碎热解后,采用熔盐净化塔进行脱溴处理。具体可将热解油气通入熔盐净化塔内部,通过与氢氧化钠和/或氢氧化钾熔盐进行接触,达到脱溴净化的目的。采用该装置处理废线路板,一方面具有较高的溴脱除率,一方面也无需在热解阶段在废线路板破碎料中加入naoh、na2co3、cao、zno等添加剂,因此不影响后续热解残渣的资源化回收。此外,热解过程中产生的热解残渣可达到冶炼原料标准,无需预处理直接用于冶炼。
43.为了进一步提高热解效果,在一种优选的实施方式中,热解过程中,热解温度为550~700℃,热解时间为60~120min。在该条件下能够使破碎料更充分热解。优选地,破碎料的粒径为1~4cm。更优选其粒径在2cm左右。
44.为使脱溴过程反应更充分,在一种优选的实施方式中,熔盐的温度为500~650℃。更优选地,热解油气在熔盐净化塔30中的停留时间为10~60s。
45.在一种优选的实施方式中,上述热解过程中,采用燃料燃烧的方式作为热源;优选地,在脱溴处理的步骤之后,上述方法还包括:将脱溴气进行冷凝处理,得到热解油和不凝气;将不凝气返回至热解过程,作为部分热源。
46.更优选地,燃料燃烧过程产生燃烧烟气,上述方法还包括:将燃烧烟气依次进行余热回收、物理吸附及碱洗收,得到净化烟气。
47.总之,本实用新型提供一种废线路板热解脱溴方法及装置,热解装置使废线路板充分热解同时实现热解气自热回用,熔盐净化塔使热解油气高效脱溴(脱溴率能够高达95~99%),净化后不凝热解气直接返回热解过程燃烧供热,热解油作为燃料或精制提炼化工产品,从而实现废线路板全组分洁净化综合利用。
48.以下结合具体实施例对本技术作进一步详细描述,这些实施例不能理解为限制本技术所要求保护的范围。
49.实施例1
50.使用图1至3中所述的装置对废线路板进行热解脱溴净化处理,其中布盐盘孔径在7~9mm,塔板漏盐孔开孔率不大于为35~40%,开孔直径在7~9mm,相邻两个塔板的倾斜方向相反,向下倾斜的角度为2~10
°
。具体处理过程如下:
51.破碎废线路板至粒度约2cm左右,在热解炉内惰性气氛氮气保护下加热至600℃,热解时间为60min,所得热解油气进入熔盐净化塔,熔盐采用naoh加热至600℃,热解油气在塔内停留时间为20s,与熔盐充分反应后排出进行冷凝,溴脱除率为97%。冷凝分离的不凝气返回热解过程采用喷嘴燃烧补热,自热率达90%,其余采用天然气燃烧补热。燃烧烟气先后经余热回收、活性碳吸收、碱吸收,达标排放。
52.实施例2
53.采用的装置同实施例1,具体处理过程如下:
54.破碎废线路板至粒度约2cm左右,在热解炉内惰性气氛保护下加热至650℃,热解时间为60min,所得热解油气进入熔盐净化塔,熔盐采用koh加热至600℃,热解油气在塔内停留时间为30s,与熔盐充分反应后排出进行冷凝,溴脱除率为97.5%。冷凝分离的不凝气返回热解过程采用喷嘴燃烧补热,自热率达90%,其余采用天然气燃烧补热。燃烧烟气先后经余热回收、活性碳吸收、碱吸收,达标排放。
55.实施例3
56.采用的装置同实施例1,具体处理过程如下:
57.破碎废线路板至粒度约2cm左右,在热解炉内惰性气氛保护下加热至600℃,热解时间为60min,所得热解油气进入熔盐净化塔,熔盐采用naoh与koh混合,比例为1:1,加热温度至550℃,热解油气在塔内停留时间为40s,与熔盐充分反应后排出进行冷凝,溴脱除率为98%。冷凝分离的不凝气返回热解过程采用喷嘴燃烧补热,自热率达90%,其余采用天然气燃烧补热。燃烧烟气先后经余热回收、活性碳吸收、碱吸收,达标排放。
58.以上所述仅为本实用新型的优选实施例而已,并不用于限制本实用新型,对于本领域的技术人员来说,本实用新型可以有各种更改和变化。凡在本实用新型的精神和原则之内,所作的任何修改、等同替换、改进等,均应包含在本实用新型的保护范围之内。