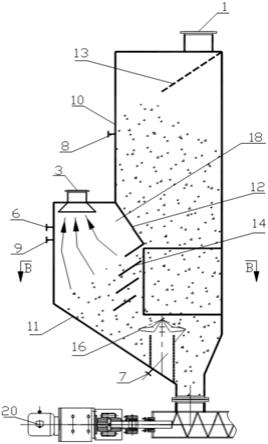
1.本实用新型属于煤化工技术领域,具体涉及一种热解油气除尘装置。
背景技术:
2.煤炭通过燃烧生产电力或热能,是冶金、化学工业的重要原料,用于精炼金属或生产化肥和许多化工产品,是非常重要的能源。随着环保要求日益严格,为了充分利用煤炭资源,采用洁净煤技术生产石油替代化工产品是我国能源政策的重要组成部分,也是保证能源安全的重要措施。
3.迄今为止,许多科研院所和企业都在致力于推进煤热解提质技术的工业化进程,并取得了一定程度的突破性进展,例如部分地区依托丰富的煤炭资源,已规划、建设并运行了粉煤洁净化分级利用项目,以生产高附加值的提质煤、焦油、lng、lpg等产品。但是现有热解油气净化技术仍存在诸多不足:(1)含有大量粉尘,容易沉积并堵塞管道和设备;(2)气体中的烃类物质易于冷凝析出或高温结焦,附着在管壁上也会造成管道和设备堵塞;(3)煤热解气体所产生的煤焦油杂质含量大、品质较低。油气和粉尘的分离技术至今没有得到有效突破,成为制约煤洁净技术推广利用的瓶颈。
4.现有技术中常采用旋风分离器和金属丝网过滤器等对煤热解油气进行除尘过滤。其中,旋风分离器的压降一般较高,而且对于5
‑
10μm以下的尘粒捕效率低,只能达到60
‑
80%左右,故旋风分离器一般只能作为预除尘设备,而且其也不能解决油气容易结焦的问题。对于金属丝网过滤器来说,虽然其具有良好的热抗震性、机械性能以及较高的过滤精度,但该工艺仍然不能有效解决因粉尘沉积及高温结焦而导致金属丝网过滤无法正常运行的问题。
5.因此,为了克服粉煤热解油气的除尘和结焦难题,寻找一种可行的热解油气除尘装置就势在必行。
技术实现要素:
6.因此,本实用新型要解决的技术问题在于克服现有技术中热解油气除尘不彻底,容易结焦等缺陷,从而提供一种热解油气除尘装置。
7.为此,本实用新型提供如下技术方案:
8.本实用新型提供一种热解油气除尘装置,包括:
9.除尘剂进口和除尘剂出口,在所述除尘剂进口和除尘剂出口之间形成除尘剂通道;
10.油气出口和油气进口,在所述油气出口和油气进口之间形成油气通道,所述油气通道和所述除尘剂通道交叉设置;
11.内挡板,设置在靠近所述油气出口的位置,用于在所述油气出口的位置形成气相区;
12.百叶窗挡板,设置在所述油气通道内。
13.可选的,还包括筛网,倾斜设置在所述除尘剂进口的下方;
14.所述筛网的与水平方向的夹角≥37
°
;
15.所述筛网的孔径为5
×
5mm。
16.可选的,所述气相区的空高≥1/4所述除尘剂通道高度。
17.可选的,所述百叶窗挡板之间的间距≥150mm,所述百叶窗挡板与水平方向的夹角≥37
°
。
18.可选的,还包括强制折流板,设置在所述油气进口的上方;
19.还包括进气口保护罩,设置在所述油气进口与所述强制折流板之间。
20.可选的,所述进气口保护罩的外径d、所述进气口保护罩与油气进口之间的距离h之间满足h<1/2d
×
tg37
°
。
21.可选的,还包括集气喇叭口,设置在所述油气通道内油气出口处;
22.所述热解油气除尘装置的底板向除尘剂出口的方向倾斜设置。
23.可选的,还包括导气装置,与所述油气进口连通设置;
24.还包括反应炉进料螺旋,与所述除尘剂出口连通设置。
25.可选的,还包括料位计口。
26.可选的,还包括若干温度计口和压力表。
27.本实用新型技术方案,具有如下优点:
28.1.本实用新型提供的热解油气除尘装置,包括:除尘剂进口和除尘剂出口,在所述除尘剂进口和除尘剂出口之间形成除尘剂通道;油气出口和油气进口,在所述油气出口和油气进口之间形成油气通道,所述油气通道与所述除尘剂通道交叉设置;内挡板,设置在靠近所述油气出口的位置,用于在所述油气出口的位置形成气相区;百叶窗挡板,设置在所述油气通道内。本实用新型首先利用百叶窗挡板使气流急转改变方向的特性,使粉尘在惯性力作用下与气流进行第一次分离脱除,然后利用固体颗粒干燥煤的高比表面积和过滤精度特性,对热解油气中的粉尘进行筛滤、惯性碰撞、截留,从而达到第二次高效除尘的目的,同时对所述热解油气进行进一步除尘净化及热量回收处理,得到无尘煤气。与现有技术相比,本实用新型无需设置陶瓷高温过滤单元,就可截留住热解油气中的胶质、沥青质、重组分及粉尘,从而实现对热解油气的高效除尘。同时,本实用新型还利用除尘剂作为冷媒对热解油气进行换热降温,不仅能够减少重组分因高温结焦而导致管道堵塞的发生,也可降低后续使热解油气冷却所需的能源消耗。解决了现有技术中热解油气除尘装置结构复杂、粉尘分离净化效果差、热量回收利用率低、装置运行成本高等问题。
29.2.本实用新型提供的热解油气除尘装置,还包括筛网,倾斜设置在所述除尘剂进口的下方;所述筛网的与水平方向的夹角≥37
°
;所述筛网的孔径为5
×
5mm。除尘剂从所述除尘剂进口进入,靠重力降落到筛网上进行筛分,筛下物直接落入除尘剂出口中,能够避免除尘剂中的粉尘进入到热解油气中,筛上物沿筛面滑落到除尘剂通道与油气通道的交叉区域,使得热解油气与除尘剂形成的移动床颗粒层的筛滤、惯性碰撞、截留及扩散等方式对所述热解油气进行进一步除尘净化及热量回收处理,得到无尘煤气。所述筛网的与水平方向的夹角≥37
°
,大于除尘剂的安息角,有利于除尘剂沿筛网自然流动和滑落,防止堆积堵塞。所述筛网的孔径为5
×
5mm,其作用是使除尘剂中小于5mm的细颗粒直接进入除尘剂出口,不作为除尘剂参与对热解油气中夹带的粉尘的捕集,防止其中小于5mm的颗粒被热解油气夹
带扬起,降低除尘效果或堵塞后续管道设备。
30.3.本实用新型提供的热解油气除尘装置,所述气相区的空高≥1/4所述除尘剂通道高度,形成足够的气固沉降区间,不仅有利于热解油气与除尘剂之间的气固分离,防止热解油气流速过大导致除尘剂被携带入后续管路和设备中,又可有效降低除尘装置的高度和安装空间要求。
31.4.本实用新型提供的热解油气除尘装置,所述百叶窗挡板之间的间距≥150mm,所述百叶窗挡板与水平方向的夹角≥37
°
。所述百叶窗挡板之间的间距≥150mm,可防止除尘剂在百叶窗挡板间的搭桥堵塞;所述百叶窗挡板与水平方向的夹角≥37
°
,有利于除尘的自然流动和更新,防止堆积堵塞。
32.5.本实用新型提供的热解油气除尘装置,还包括强制折流板,设置在所述油气进口的上方;还包括进气口保护罩,设置在所述油气进口与所述强制折流板之间。除尘剂滑落到强制折流板上,经导向后滑落至除尘剂通道与油气通道的交叉区域,能够保证该区域的除尘剂不断更新和移动,使得热解油气与除尘剂充分接触,有利于热解油气的除尘过滤和热量回收,从而有效提高除尘净化效果和整体压降,同时还能避免除尘剂直接进入尤其进口造成堵塞。所述进气口保护罩的设置,能够使热解油气从所述油气进口和进气口保护罩之间的环形通道进入热解油气除尘装置,能够将其气体的流速,同时还能防止除尘剂落入油气进口内造成堵塞。
33.6.本实用新型提供的热解油气除尘装置,所述进气口保护罩的外径d、所述进气口保护罩与油气进口之间的距离h之间满足h<1/2d
×
tg37
°
。在此高度范围内h优选大值,这样不仅能够增大气体的流通面积,降低气体的流速,又能防止除尘剂落入油气进口管道内。
34.7.本实用新型提供的热解油气除尘装置,还包括集气喇叭口,设置在所述油气通道内油气出口处;所述热解油气除尘装置的底板向除尘剂出口的方向倾斜设置。所述集气喇叭口的设置利于将净化后的热解油气引出除尘装置;所述热解油气除尘装置的底板向除尘剂出口的方向倾斜设置,能够保证除尘剂沿底板流向除尘剂出口附近,从而引出装置。
35.8.本实用新型提供的热解油气除尘装置,还包括料位计口、若干温度计口和压力表。如此便于实时观测除尘装置中的料位高度和各处的温度以及压力。
附图说明
36.为了更清楚地说明本实用新型具体实施方式或现有技术中的技术方案,下面将对具体实施方式或现有技术描述中所需要使用的附图作简单地介绍,显而易见地,下面描述中的附图是本实用新型的一些实施方式,对于本领域普通技术人员来讲,在不付出创造性劳动的前提下,还可以根据这些附图获得其他的附图。
37.图1为本实用新型提供的热解油气除尘装置的主视结构示意图;
38.图2为本实用新型提供的热解油气除尘装置的俯视结构示意图;
39.图3为图1中b
‑
b截面的俯视结构示意图;
40.图4为本实用新型提供的热解油气除尘装置的左视结构示意图。
41.附图标记说明:
[0042]1‑
除尘剂进口,2
‑
除尘剂出口,3
‑
油气出口,4
‑
油气进口,5
‑
料位计口,6
‑
第一温度计口,7
‑
第二温度计口,8
‑
第三温度计口,9
‑
压力表口,10
‑
方筒体,11
‑
异形椎体,12
‑
内挡
板,13
‑
筛网,14
‑
百叶窗挡板,15
‑
集气喇叭口,16
‑
进气口保护罩,17
‑
气相区顶板,18
‑
气相区,19
‑
强制折流板,20
‑
反应炉进料螺旋,21
‑
导气装置。
具体实施方式
[0043]
下面将结合附图对本实用新型的技术方案进行清楚、完整地描述,显然,所描述的实施例是本实用新型一部分实施例,而不是全部的实施例。基于本实用新型中的实施例,本领域普通技术人员在没有做出创造性劳动前提下所获得的所有其他实施例,都属于本实用新型保护的范围。
[0044]
在本实用新型的描述中,需要说明的是,术语“中心”、“上”、“下”、“左”、“右”、“竖直”、“水平”、“内”、“外”等指示的方位或位置关系为基于附图所示的方位或位置关系,仅是为了便于描述本实用新型和简化描述,而不是指示或暗示所指的装置或元件必须具有特定的方位、以特定的方位构造和操作,因此不能理解为对本实用新型的限制。此外,术语“第一”、“第二”、“第三”仅用于描述目的,而不能理解为指示或暗示相对重要性。
[0045]
在本实用新型的描述中,需要说明的是,除非另有明确的规定和限定,术语“安装”、“相连”、“连接”应做广义理解,例如,可以是固定连接,也可以是可拆卸连接,或一体地连接;可以是机械连接,也可以是电连接;可以是直接相连,也可以通过中间媒介间接相连,可以是两个元件内部的连通。对于本领域的普通技术人员而言,可以具体情况理解上述术语在本实用新型中的具体含义。
[0046]
此外,下面所描述的本实用新型不同实施方式中所涉及的技术特征只要彼此之间未构成冲突就可以相互结合。
[0047]
实施例1
[0048]
本实用新型提供一种热解油气除尘装置,如图1
‑
4所示,包括:除尘剂进口1和除尘剂出口2,在所述除尘剂进口1和除尘剂出口2之间形成除尘剂通道;油气出口3和油气进口4,在所述油气出口3和油气进口4之间形成油气通道,所述油气通道与所述除尘剂通道交叉设置;内挡板12,设置在靠近所述油气出口3的位置,用于在所述油气出口3的区域形成气相区;百叶窗挡板14,设置在所述油气通道内。本实用新型首先利用百叶窗挡板14使气流急转改变方向的特性,使粉尘在惯性力作用下与气流进行第一次分离脱除,然后利用固体颗粒干燥煤的高比表面积和过滤精度特性,对热解油气中的粉尘进行筛滤、惯性碰撞、截留,从而达到第二次高效除尘的目的,同时对所述热解油气进行进一步除尘净化及热量回收处理,得到无尘煤气。与现有技术相比,本实用新型无需设置陶瓷高温过滤单元,就可截留住热解油气中的胶质、沥青质、重组分及粉尘,从而实现对热解油气的高效除尘。同时,本实用新型还利用除尘剂作为冷媒对热解油气进行换热降温,不仅能够减少重组分因高温结焦而导致管道堵塞的发生,也可降低后续使热解油气冷却所需的能源消耗。解决了现有技术中热解油气除尘装置结构复杂、粉尘分离净化效果差、热量回收利用率低、装置运行成本高等问题。
[0049]
具体的,所述热解油气除尘装置可以为圆筒体、方筒体或异形筒体,所述热解油气除尘装置可以是等宽(直径)或者不等宽或变径的筒体。在本实施例中,所述热解除尘装置上方为方筒体10,下方为异形椎体11,二者连通设置,下方异形椎体的直径大于方筒体的宽度。在所述方筒体的顶部设置有除尘剂进口1,所述除尘剂出口2和油气进口4设置在异形椎
体的底部;所述油气出口可以设置在所述方筒体的侧壁上,在本实施例中所述油气出口3设置在所述异形椎体11顶部宽于所述方筒体的气相区顶板17上;所述内挡板12设置在所述油气出口3靠近异形椎体中心的一侧,用于在油气出口3的下方区域形成气相区18,百叶窗挡板14设置在所述内挡板12的下方。
[0050]
在一些改进的实施方式中,还包括筛网13,倾斜设置在所述除尘剂进口1的下方;所述筛网13的与水平方向的夹角≥37
°
;所述筛网的孔径为5
×
5mm。除尘剂从所述除尘剂进口1进入,靠重力降落到筛网13上进行筛分,筛下物直接落入除尘剂出口2中,能够避免除尘剂中的粉尘进入到热解油气中,筛上物沿筛面滑落到除尘剂通道与油气通道的交叉区域,使得热解油气与除尘剂形成的移动床颗粒层的筛滤、惯性碰撞、截留及扩散等方式对所述热解油气进行进一步除尘净化及热量回收处理,得到无尘煤气。所述筛网13的与水平方向的夹角≥37
°
,该角度大于除尘剂的安息角,有利于除尘剂沿筛网13自然流动和滑落,防止堆积堵塞。所述筛网13的孔径为5
×
5mm,其作用是使除尘剂中小于5mm的细颗粒直接进入除尘剂出口2,不作为除尘剂参与对热解油气中夹带的粉尘的捕集,防止其中小于5mm的颗粒被热解油气夹带扬起,降低除尘效果或堵塞后续管道设备。
[0051]
在一些改进的实施方式中,所述气相区18的空高≥1/4所述除尘剂通道高度,形成足够的气固沉降区间,不仅有利于热解油气与除尘剂之间的气固分离,防止热解油气流速过大导致除尘剂被携带入后续管路和设备中,又可有效降低除尘装置的高度和安装空间要求。
[0052]
在一些改进的实施方式中,所述百叶窗挡板14之间的间距≥150mm,所述百叶窗挡板14与水平方向的夹角≥37
°
。所述百叶窗挡板14之间的间距≥150mm,可防止除尘剂在百叶窗挡板间的搭桥堵塞;所述百叶窗挡板14与水平方向的夹角≥37
°
,有利于除尘的自然流动和更新,防止堆积堵塞。
[0053]
在一些改进的实施方式中,还包括强制折流板19,设置在所述油气进口4的上方;还包括进气口保护罩16,设置在所述油气进口4与所述强制折流板19之间。除尘剂滑落到强制折流板19上,经导向后滑落至除尘剂通道与油气通道的交叉区域,能够保证该区域的除尘剂不断更新和移动,使得热解油气与除尘剂充分接触,有利于热解油气的除尘过滤和热量回收,从而有效提高除尘净化效果和整体压降,同时还能避免除尘剂直接进入尤其进口造成堵塞。所述进气口保护罩16的设置,能够使热解油气从所述油气进口4和进气口保护罩16之间的环形通道进入热解油气除尘装置,能够将其气体的流速,同时还能防止除尘剂落入油气进口内造成堵塞。
[0054]
在一些改进的实施方式中,所述进气口保护罩的外径d、所述进气口保护罩与油气进口之间的距离h之间满足h<1/2d
×
tg37
°
。在此高度范围内h优选大值,这样不仅能够增大气体的流通面积,降低气体的流速,又能防止除尘剂落入油气进口管道内。
[0055]
在一些改进的实施方式中,还包括集气喇叭口15,设置在所述油气通道内油气出口3处;所述热解油气除尘装置的底板向除尘剂出口的方向倾斜设置。所述集气喇叭口的设置利于将净化后的热解油气引出除尘装置;所述热解油气除尘装置的底板向除尘剂出口的方向倾斜设置,能够保证除尘剂沿底板流向除尘剂出口附近,从而引出装置。
[0056]
此外,为了方便装置运行过程中参数的监控,还包括料位计口5、若干温度计口和压力表。具体的,在方筒体10的顶部设置有料位计口5;在所述油气出口3处设置第一温度计
口6和压力表口9;在所述油气进口4处设置有第二温度计口7,在方筒体10侧壁上设置有第三温度计口8;如此便于实时观测除尘装置中的料位高度和各处的温度以及压力。
[0057]
作为本实用新型的另一个创新点所在,本实用新型选择干燥煤作为除尘剂,所述干燥煤是指温度110
‑
130℃,粒径0.2
‑
30mm,水分含量0.5
‑
1.0%(wt)的煤。
[0058]
本实用新型首次在热解油气的除尘工艺中直接使用干燥煤作为除尘剂以达到除尘降温的目的,与现有技术相比,本实用新型可以不使用特制的固体除尘剂,也无需设置陶瓷高温过滤单元,就可截留住热解油气中的胶质、沥青质、重组分及粉尘,从而实现对热解油气的高效除尘。同时,本实用新型还利用干燥煤作为冷媒对热解油气进行换热降温,不仅能够减少重组分因高温结焦而导致管道堵塞的发生,也可降低后续使热解油气冷却所需的能源消耗。解决了现有技术中热解油气除尘装置结构复杂、粉尘分离净化效果差、热量回收利用率低、装置运行成本高等问题。
[0059]
使用时,热解油气从所述油气进口4和进气口保护罩16之间的环形通道进入热解油气过滤装置,穿过干燥煤颗粒层和百叶窗挡板14,进入内挡板12和气相区顶板17之间形成的气相区18进行沉降分离后,经集气喇叭口15收集气体并从油气出口3排出除尘装置。所述内挡板12底部边缘以上部分的料封高度>1m,如此能够保证干燥气与热解油气互不相窜,有效隔离。
[0060]
干燥煤从所述除尘剂进口1进入,靠重力降落到筛网13上进行筛分,筛下物直接落入干燥煤出口中,筛上物沿筛面滑落到强制折流板19上,经导向后滑落至进气口保护罩16上方,保护罩周围的干燥煤沿着异形椎体11进入除尘剂出口2,经反应炉进料螺旋20输送入回转反应炉。
[0061]
具体的,回转反应炉内煤低温热解产生的400℃热解油气,从所述导气装置21引出经油气进口4和进气口保护罩16之间的通道进入油气过滤器,穿过干燥煤颗粒层和百叶窗挡板14,进入内挡板12和气相区顶板17之间形成的气相区进行沉降分离粉尘后,经集气喇叭口15收集气体并从油气出口3排出除尘装置。
[0062]
温度120℃,粒径0.2
‑
30mm,水分含量1.0%(wt)的干燥煤从所述除尘剂进口1进入,靠重力降落到筛网13上进行筛分,小于5mm的筛下物直接落入除尘剂出口2中,筛上物沿筛面滑落到强制折流板19上,经导向后滑落至进气口保护罩16上方,形成的干燥煤颗粒层对含尘热解油气进行除尘过滤和热量回收,然后保护罩周围的干燥煤沿着异形椎体11的底板进入除尘剂出口2,经反应炉进料螺旋20输送入回转反应炉(图中未示出)进行干馏热解。
[0063]
在一些优选的实施方式中,所述内挡板12和气相区顶板17之间形成的气相区的空高要求为1/4除尘装置总高度,不仅有利于热解油气与干燥煤之间的气固分离,防止热解油气流速过大导致干燥煤被携带入后续管路和设备中,又可有效降低除尘装置的高度和安装空间要求。
[0064]
所述百叶窗挡板14之间的平形间距为150mm,可防止干燥煤在百叶窗挡板间的搭桥堵塞;百叶窗挡板与水平方向的夹角为38
°
,其大于干燥煤的安息角37
°
,有利于干燥煤的自然流动和更新,防止堆积堵塞。
[0065]
所述进气口保护罩16外径d、进气口保护罩16与油气进口4之间的高度h关系为h<1/2d
×
tg37
°
。在此高度范围内h优选大值,这样不仅能够增大气体的流通面积,降低气体的流速,又能防止提质煤落入油气进口管道内。
[0066]
所述内挡板12底部边缘以上部分的料封高度为1.5m,既能保证干燥气与热解油气通过干燥煤颗粒层形成的料封有效隔离,互不相窜,又能提高过滤器的物料缓存时间,减少系统波动,保证装置运行安全。
[0067]
显然,上述实施例仅仅是为清楚地说明所作的举例,而并非对实施方式的限定。对于所属领域的普通技术人员来说,在上述说明的基础上还可以做出其它不同形式的变化或变动。这里无需也无法对所有的实施方式予以穷举。而由此所引申出的显而易见的变化或变动仍处于本实用新型创造的保护范围之中。