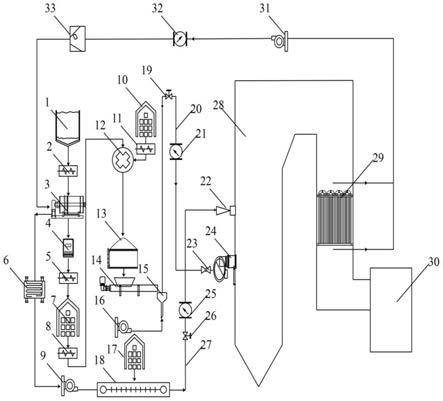
1.本发明涉及污泥干化焚烧处理技术及控制重金属排放技术领域,尤其是一种燃煤电厂利用烟气再循环掺烧污泥系统及方法。
背景技术:
2.污泥的法热处理法不仅能够杀死污泥中的病菌有害物质,并且能够有效地利用污泥中可燃成分的热能,在兼顾减容污泥体积、处理效率的同时极大程度上保护了环境,是目前主要的处理与处置污泥的手段和方式之一。然而污泥单独焚烧时存在热值低、工艺复杂、运行费用高、设备投资大、效果不稳定等问题。因此使用燃煤电厂中煤掺烧污泥的方式存在明显优势,基于电厂中已有的煤粉炉、尾气处理等设备减少了投资运行成本,煤与污泥的掺烧也提升了燃烧的稳定性,在保证燃烧效率的同时也处理了大量污泥。
3.在目前燃煤电厂掺烧处置污泥的系统中还存在着以下几点问题:(1)湿污泥的含水率高达80%以上,在进入电厂燃烧系统前必须先进过干化、破碎等预处理以符合电厂燃煤锅炉的运行参数和保证燃烧效率,是掺烧系统的关键环节之一。若将湿污泥单独干化处理会提高运行成本,运行维护成本等,系统的集成性减弱,运行效率降低;若使用锅炉排出烟气进行直接干化处理,会造成污泥中的有机物挥发产生恶臭气体,恶臭气体会进入烟气引起环境的污染。(2)污泥中的重金属会转移到烟气和燃烧灰之中,它们性质较为稳定难以去除,若直接跟随烟气排入环境中会造成严重的重金属污染。(3)系统运行灵活性不高,污泥含水率和污泥掺烧量是燃煤电厂掺烧系统的关键参数之一,需要对污泥干化效果以及掺烧情况作有效地反馈,根据电厂实际运行情况对系统进行适当调控。
技术实现要素:
4.针对现有技术的不足,本发明提供一种燃煤电厂利用烟气再循环掺烧污泥系统及方法,以提高掺烧系统效率、降低系统能耗和环境污染。
5.本发明采用的技术方案如下:
6.一种燃煤电厂利用烟气再循环掺烧污泥系统,包括:
7.污泥颗粒制备系统,其利用来自污泥干化系统的热源制备干污泥并将其与煤粉混合、破碎后制成颗粒状混合燃料;
8.燃煤颗粒输运系统,其用于将所述混合燃料输送至安装在燃煤锅炉炉膛上的燃烧器;
9.污泥干化系统,其包括燃煤锅炉的省煤器,省煤器的进口、出口的部分烟气被引出并混合后送入所述污泥颗粒制备系统的干燥器内,用作污泥干燥的热源;
10.吸附剂输运系统,其包括蒸汽换热器和吸附剂输运机构,所述蒸汽换热器被加热介质进口与所述干燥器的烟气出口连接,所述蒸汽换热器被加热介质出口与所述吸附剂输运机构连接,所述吸附剂输运机构通过管路与安装在燃煤锅炉炉膛上的喷射器与连接。
11.其进一步技术方案为:
12.蒸汽换热器和吸附剂输运机构之间通过第一风机相连,吸附剂输运机构与高岭土仓出口连接,吸附剂输运机构与喷射器连接的管路上设置有流量控制仪一和开关阀一。
13.所述污泥颗粒制备系统的结构还包括湿污泥池、湿污泥输送机、干污泥仓和煤粉仓和粉料仓,所述湿污泥池出口与所述干燥器入口通过湿污泥输送机相连,所述干燥器出口和所述干污泥仓入口通过含水率检测仪及干污泥输送机一相连;干污泥仓和煤粉仓出口通过各自的输送机构与破碎机入口相连,破碎机出口与所述粉料仓入口连接。
14.所述燃料颗粒输运系统的结构包括输粉机、漏斗和第二风机,所述输粉机入口与粉料仓出口连接,所述输粉机出口与所述漏斗对接,所述漏斗通过连接管路与所述燃烧器连接,并在连接管路上设有开关阀二、流量控制仪二和气动球阀;用于将漏斗中的混合燃料通过所述第二风机作用由连接管路经燃烧器喷至炉膛内。
15.所述省煤器的进、出口分别通过支管将烟气引出并汇入一根总管,混合后烟气经总管送入所述干燥器的烟气进口,所述总管上连接有第三风机、流量控制仪三和温度调节器。
16.燃煤锅炉产生的烟气经省煤器进口、出口抽取部分后,剩余部分通过烟气净化系统处理后排出。
17.一种燃煤电厂利用烟气再循环掺烧污泥系统的掺烧方法,包括以下流程:
18.将省煤器进口及出口的、温度在400
‑
450℃的部分烟气抽取并混合后,输入干燥器,用以将干燥器内80%含水率以上的湿污泥干燥至10%含水率以下;湿污泥经过干燥器干化后经过含水率检测仪检测合格后,输送至干污泥仓储存备用;
19.干污泥由干污泥仓通过输送机构送入破碎机,在破碎机内与从煤粉仓输送来的煤一同破碎,制成污泥与煤的颗粒状混合燃料,然后储存在粉料仓;粉料仓中的燃料颗粒被输送至燃烧器,然后喷入燃煤锅炉;同时,干燥器出口的烟气经蒸汽换热器加热至180℃以上,然后携带高岭土吹入喷射器后喷入燃煤锅炉与混合燃料发生固
‑
固燃烧反应。
20.其进一步技术方案为:
21.干燥器和煤粉仓分别通过输送机构与破碎机连接,通过输送机构调整的污泥及煤量,使得混合燃料中污泥的质量占比不高于15%。
22.所述蒸汽换热器中的蒸汽来自于燃煤电厂汽轮机中压缸与低压缸之间的抽汽,蒸汽放热后进入蒸汽再热系统循环利用。
23.本发明的有益效果如下:
24.本发明利用省煤器进、出口的高温烟气循环干化湿污泥,并且将干燥器出口烟气携带矿物质吸附剂喷入燃煤锅炉。相较于单独干化污泥系统,本系统灵活性强,效率高,利用已有的设备进行改进节约了成本。
25.本发明还具有如下优点:
26.(1)本发明采用烟气再循环结构,从省煤器出口及入口段抽取400℃
‑
450℃左右的烟气通过旁路通入干燥器中干化湿污泥,而后将干污泥与煤粉按照一定的掺混比送入破碎机研磨成颗粒状后送入燃煤锅炉进行掺烧,这使得污泥干化系统与原有燃煤发电系统相结合,有效地利用了烟气余热与污泥中可燃物质的热量,提升了系统效率的同时也通过烟气再循环技术降低了所生成氮氧化物的含量。
27.(2)本发明抽取的烟气温度为400℃
‑
450℃之间,相较于尾部烟气干燥,对于湿污
泥有着良好的干燥效果且减少了所用的烟气量,风机功率低,投资成本少;同时改变抽取省煤器出、入口烟气量有利于干燥器入口烟温的调节,增强系统的灵活性。
28.(3)相较于将干化污泥后的烟气直接通入燃煤锅炉,本发明充分利用换热后干燥器出口的烟气,利用其携带矿物质吸附剂进入喷射器后喷入炉内进行燃烧,既利用烟气循环降低了燃煤电厂燃烧所产生的氮氧化物又携带吸附剂进行掺烧,吸附剂与重金属在炉膛内发生化学吸附反应,提高掺烧过程中部分重金属的固留率。在一定程度上控制污泥中重金属进入烟气中。干燥后的烟气通入炉内也防止了恶臭气体的泄露,同时抑制了燃烧污泥和煤混合物时有害重金属的挥发,保护了生态环境。
29.(4)本发明系统灵活性强,设置了风机以保证干燥器的负压状态,防止恶臭气体的泄露;在循环烟气输送过程中设有温度调节器、流量控制仪、开关阀等,可以根据实际燃烧工况进行调节循环烟气温度及流量;在污泥干化后设有含水率检测仪可在线检验干化效果、以及烟气流量计用于反馈掺烧系统的关键参数;同时干污泥进入破碎机所采用的输送机可以有效地控制煤与污泥的掺烧比,调节燃烧过程的关键参数。
附图说明
30.图1为本发明系统的具体实施例的结构示意图。
31.图中:1、湿污泥池;2、湿污泥输送机;3、干燥器;4、含水率检测仪;5、干污泥输送机一;6、蒸汽换热器;7、干污泥仓;8、干污泥输送机二;9、第一风机;10、煤粉仓;11、煤粉输送机;12、破碎机;13、粉料仓;14、输粉机;15、漏斗;16、第二风机;17、高岭土仓;18、吸附剂输运机构;19、开关阀二;20、混合燃料输送管;21、流量控制仪二;22、喷射器;23、气动球阀;24、燃烧器;25、流量控制仪一;26、开关阀一;27、吸附剂输送管;28、燃煤锅炉;29、省煤器;30、烟气净化系统;31、第三风机;32、流量控制仪三;33、温度调节器。
具体实施方式
32.以下结合附图说明本发明的具体实施方式。
33.如图1所示,本实施例的燃煤电厂利用烟气再循环掺烧污泥系统,包括:
34.污泥颗粒制备系统,其利用来自污泥干化系统的热源制备干污泥并将其与煤粉混合、破碎后制成颗粒状混合燃料;
35.燃煤颗粒输运系统,其用于将混合燃料输送至安装在燃煤锅炉28炉膛上的燃烧器24;
36.污泥干化系统,其包括燃煤锅炉28的省煤器29,省煤器29上设置旁路烟气:省煤器29的进口、出口部分烟气被引出并混合送入干燥器3内,用作干燥污泥的热源;
37.吸附剂输运系统,其包括蒸汽换热器6和吸附剂输运机构18,蒸汽换热器6被加热介质进口与干燥器3的烟气出口连接,蒸汽换热器6被加热介质出口与吸附剂输运机构18连接,吸附剂输运机构18通过管路与安装在燃煤锅炉28炉膛上的喷射器22与连接。
38.上述实施例中,蒸汽换热器6和吸附剂输运机构18之间通过第一风机9相连,吸附剂输运机构18与高岭土仓17出口连接,吸附剂输运机构18与喷射器22连接的管路上设置有流量控制仪一25和开关阀一26。
39.具体地,吸附剂输运机构18采用刮板式输运机。
40.上述实施例中,污泥颗粒制备系统的结构还包括湿污泥池1、湿污泥输送机2、干污泥仓7和煤粉仓10和粉料仓13,湿污泥池1出口与干燥器3入口通过湿污泥输送机2相连,干燥器3出口和干污泥仓7入口通过含水率检测仪4及干污泥输送机一5相连;干污泥仓7和煤粉仓10出口通过各自的输送机构与破碎机12入口相连,破碎机12出口与粉料仓13入口连接。
41.具体地,经干燥器3间接干燥脱水的污泥在由干污泥输送机一5进入干污泥仓7之前由含水率检测仪4进行评估,实时监控污泥干化效果,也有助于接受系统反馈,对不同的燃烧工况进行调整。
42.具体地,干污泥仓7出口与干污泥输送机二8入口连接,干污泥输送机二8出口与破碎机12的一个入口连接;煤粉仓10与煤粉输送机二11入口连接,煤粉输送机二11出口与破碎机12的另一个入口连接。通过干污泥输送机二8、煤粉输送机二11控制进入破碎机12的干污泥和燃煤的量,从而调节破碎后混合燃料颗粒中污泥的含量,以保证燃煤锅炉28的燃烧效率和最终的发电效率。
43.此外,采用中间储仓式结构将经破碎后的混合燃料储存在粉料仓13中,能够保证颗粒制备系统能长时间的处于额定条件下工作,提升了燃烧过程中燃料供给的可靠性,同时也有利于工况调节。
44.上述实施例中,燃料颗粒输运系统的结构包括输粉机14、漏斗15和第二风机16,输粉机14入口与粉料仓13出口连接,输粉机14出口与漏斗15对接,漏斗15通过连接管路与燃烧器24连接,并在连接管路上设有开关阀二19、流量控制仪二21和气动球阀23;用于将漏斗15中的混合燃料通过第二风机16作用下,由连接管路经燃烧器24喷至炉膛内。
45.具体地,漏斗15通过混合燃料输送管20与燃烧器24连接在系统发生紧急状况时可使用开关阀二19对给料过程进行急停,混合燃料输送管20上的流量控制仪二21可以控制一次风量的同时,也可以实时监控风粉混合物的速度,防止出现堵塞的情况,气动球阀23可以控制流量并且有着节流的作用,在发生危险情况时气动球阀23可以在控制室里直接进行切断,提升了燃煤电厂的安全性。
46.上述实施例中,省煤器29的进、出口分别通过支管将烟气引出并汇入一根总管,混合后烟气经总管送入干燥器3的烟气进口,总管上连接有第三风机31、流量控制仪三32和温度调节器33。
47.具体地,抽取省煤器29进口和出口烟气有着更高的烟温与干燥效率,通过调整省煤器29进口和出口抽气量之比,配合温度调节器33和流量控制仪三32,可以更好的根据湿污泥含水量变化调整抽取烟气的参数,使进入干燥器3进行间接干燥的旁路烟气符合干化要求的同时又可以进行良性的烟气再循环,降低掺烧过程中n0x的排放含量。
48.上述实施例中,燃煤锅炉28产生的烟气经省煤器29进口、出口抽取部分后,剩余部分通过烟气净化系统30处理后排出。
49.本实施例的一种燃煤电厂利用烟气再循环掺烧污泥系统的掺烧方法,包括以下流程:
50.将省煤器29进口及出口的、温度在400
‑
450℃的部分烟气抽取并混合后输入干燥器3,用以将干燥器3内80%含水率以上的湿污泥干燥至10%含水率以下;湿污泥经过干燥器3干化后经过含水率检测仪4检测合格后,输送至干污泥仓7储存备用;
51.干污泥由干污泥仓7通过输送机构送入破碎机12,在破碎机12内与从煤粉仓10输送来的煤一同破碎,制成污泥与煤的颗粒状混合燃料,然后储存在粉料仓13;
52.粉料仓13中的燃料颗粒被输送至燃烧器24,然后喷入燃煤锅炉28;同时,干燥器3出口的烟气经蒸汽换热器6加热至180℃以上,然后携带高岭土吹入喷射器22后喷入燃煤锅炉28与混合燃料发生固
‑
固燃烧反应。
53.上述实施例中,干燥器3和煤粉仓10分别通过输送机构(干污泥输送机二8、煤粉输送机二11)与破碎机12连接,通过输送机构调整的污泥及煤量,使得混合燃料中污泥的质量占比不高于15%,以保证燃煤锅炉28的燃烧效率和电厂发电效率。
54.上述实施例中,湿污泥水分高达80%以上,直接参与掺烧会大大降低燃烧效率,必须在进入燃煤锅炉28前进行干化处理。通过湿污泥输送机2送入干燥器3将污泥水分降至10%以下以便进一步地破碎与掺烧,干燥器3热源来自于省煤器29入口与出口的400℃
‑
450℃的烟气,具有较强的干化效率。
55.上述实施例中,在第一风机9作用下,将干燥器3出口烟气经蒸汽换热器6升温后携带高岭土经吸附剂输送管27进入喷射器22,喷射器22将高岭土喷入燃煤锅炉28与燃料颗粒混燃。其中,高岭土是一种硅铝基吸附剂,价格低廉并且有着良好的吸附效果,在炉内与物料的掺烧过程有助于控制部分有害重金属元素向大气环境进行排放。吸附剂与煤污泥混合物的燃烧属于固
‑
固反应,对于吸附效果要考虑吸附反应温度范围约为800℃
‑
1000℃。
56.本实施例旁路烟气换热后,经过蒸汽换热器6后再循环,循环烟气携带矿物质吸附剂(高岭土)由喷射器22进入燃煤锅炉28方式既有效降低了系统能耗又完成了烟气再循环过程,矿物质吸附剂的加入有效抑制了掺烧过程中重金属挥发等问题,吸附剂输运系统中设备的负压状态也可以有效地防止干化污泥后的臭气泄露,保护了环境。在干燥器3中换热后的烟气经过蒸汽换热器6再次加热,使烟气温度达到180℃以上,满足固固反应的温度要求。蒸汽换热器6的蒸汽可采用来自于燃煤电厂汽轮机中压缸与低压缸之间的抽汽,蒸汽在蒸汽换热器6中放热后,进入蒸汽再热系统循环利用。