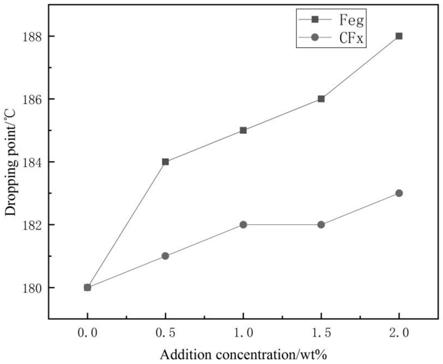
1.本发明涉及润滑脂,属于机械摩擦学技术领域,具体地涉及一种含氟化石墨烯的抗磨减摩锂基润滑脂及其制备方法。
背景技术:
2.石墨烯具有卓越的光学、电学、润滑特性等,近年来人们对石墨烯的研究火热。氟化石墨烯是新型石墨烯衍生物的一种,它是通过一些手段将f原子打入石墨烯中,改变石墨烯本身的结构状态,石墨烯原来的大π键结构被破坏,原子间主要是c
‑
f键的形式,伴随着c
‑
c 键从sp2到sp3的结构转换,也在物化性能上产生新的变化。f原子的引入对石墨烯的耐水性、热稳定性及化学稳定性都有所改善,所以氟化石墨烯广泛应用于电池、医学、光学传感器、表面材料涂层和润滑添加剂等领域。在润滑添加剂领域中,研究者探究了氟化石墨烯在 pao、大豆油、gtl、水等体系中的摩擦学性能,结果表明其可以显著提高液体润滑剂的抗磨减摩性能。
3.锂基润滑脂是至今以来发展最为迅速的润滑脂,其使用范围广泛,性能优良。随着机械设备工作环境的日益严苛,对传统锂基润滑脂的极压抗磨和耐高温性能提出了更高的要求。为了提高润滑脂的抗磨减摩性能,除了采用添加zddp、moddp、氯化石蜡等传统的极压抗磨剂外,也可以通过添加石墨烯、二维二硫化钼、二维二硫化钨等二维层状材料。因此,开展氟化石墨烯作为润滑脂润滑添加剂的研究,有利于拓宽氟化石墨烯应用领域。
4.中国发明专利(申请公布号:cn 109810748 a,申请公布日: 2019
‑
05
‑
28)公开了锂基润滑脂及其制备方法,具体是向锂基润滑脂中加入羟基化合物改性石墨烯,其中,羟基化合物改性石墨烯可以缩短锂基润滑脂的皂化反应时间和降低皂化反应温度,同时可以大幅度提高基础锂基润滑脂的安定性,稳定性和抗摩擦性,这可能是因为其中的季铵盐一方面提供较大的位阻,防止石墨烯材料进行团聚,提高抗磨性能。另一方面,季铵盐可以作为相转移催化剂,季铵盐的正电子不断携带着氢氧根负离子进入有机相,大幅度降低皂化反应的温度和时间,同时季铵盐可以提供碱性,减少游离碱的存在,可以大幅度提高基础锂基润滑脂的安定性,稳定性和抗磨性能。而苯酚可以作为自由基捕获剂,同时季铵盐较大的位阻,可以减缓自由基的下一步转移,降低自由基对润滑脂的氧化作用,大幅度减少酸性物质产生,提高润滑脂的抗氧化作用和存储时间。
5.中国发明专利(申请公布号:cn 108130178 a,申请公布日: 2018
‑
06
‑
08)公开了一种氟化石墨烯增强润滑油及其制备方法,按照重量份数计,其包括以下原料。基础油200~300份、改性氟化石墨烯2~5份、油酸10~15份、胺溶剂10~15份、抗磨磷化液20~25 份、三羟甲基丙烷10~15份、氟硼酸铵2~3份、焦磷酸钠2~3份、增塑剂0.5~1份、乳化剂0.5~1份;其中,所述改性氟化石墨烯按以下步骤制备:将氟化石墨烯分散在改性液中,加热至80~90℃,保温搅拌1~2h,过滤得到改性氟化石墨烯,按照质量百分比,所述改性液包括80~87%木质素溶液、10~15%的聚乙二醇、0.1~0.5%硫醇甲基锡以及2~5%的炭黑,所述木质素溶液的质量分数为5~ 8%。氟化石墨烯能够有效提高润滑油的性能,抗磨性能优异,
延长发动机的使用寿命。并对氟化石墨烯进行改性,通过添加木质素、油酸、炭黑等,能够进一步加强产品的抗磨性能。此外,添加抗磨磷化液,与氟化石墨烯协同促进润滑油的抗磨性能、稳定性能,并能改善润滑油的防锈性能。cn108130178a一种氟化石墨烯增强润滑油及其制备方法:该专利以氟化石墨烯为原料,通过木质素、聚乙二醇、硫醇甲基锡和炭黑组成的改性液进行表面改性,将其作为矿物基础油、合成基础油或植物基础油的润滑剂添加剂。该专利与本发明的区分在于,本发明是将氟化石墨烯作为锂基润滑脂的润滑剂添加剂,润滑油与润滑脂同属润滑剂,但二者在组成、外观、性质和应用条件等方面具有明显不同,润滑油主要应用于发动机、变速箱、传动箱和液压系统等部位,主要起润滑、冷却、防锈、清洁、密封和缓冲等作用,而润滑脂主要应用于汽车、拖拉机、联合收等大型机械的轮毂轴承、各拉杆球头、传动轴万向节等部位。
6.cn109810748a锂基润滑脂及其制备方法:该专利以鳞片石墨粉为原料,采用化学法经氧化酸化插层、水洗、干燥、高温膨胀过程制备膨胀石墨,再采用超声剥离法制备出石墨烯,进一步采用羟基化合物对石墨烯进行表面改性得到羟基化合物改性石墨烯,将其作为锂基润滑脂的润滑剂添加剂提升其抗磨减摩性能。该专利与本发明的区分在于,本发明是将氟化石墨烯作为锂基润滑脂的润滑剂添加剂,作为石墨烯的新型衍生物,氟化石墨烯具有表面能低、疏水性强及带隙宽等优异的物理化学性能,同时还具有耐高温、耐腐蚀性、耐摩擦性、化学性质稳定和优异的润滑性,因此其在润滑剂添加剂领域具有广阔的潜在应用前景。
技术实现要素:
7.为解决上述技术问题,本发明提供了一种含氟化石墨烯的抗磨减摩锂基润滑脂及其制备方法。其中,氟化石墨烯能提高润滑脂的稠度、胶体安定性和高温性。
8.为实现上述目的,本发明公开了一种含氟化石墨烯的抗磨减摩锂基润滑脂,它包括如下质量份数的各原料组分:
9.基础油:100份、稠化剂:1~10份、添加剂:1~10份;
10.其中,所述基础油为mvi500;
11.所述添加剂包括润滑剂;所述润滑剂为氟化石墨烯;且所述润滑剂的添加量为基础油质量的0.5~2.0%。
12.此外,所述添加剂还包括抗氧剂、抗腐剂、防锈剂、金属钝化剂、极压剂、颜色安定剂、增黏剂、染料或结构改善剂中的任意一种或两种及两种以上。
13.进一步地,所述稠化剂的添加量为基础油质量的9.0%,所述稠化剂为12
‑
羟硬脂酸锂皂。
14.为更好的实现本发明技术目的,本发明还公开了一种含氟化石墨烯的抗磨减摩锂基润滑脂的制备方法,它包括如下制备步骤:
15.1)制备锂基脂;
16.2)制备氟化石墨烯锂基脂:向步骤1)制备的锂基脂中加入添加剂,得到不同含量的氟化石墨烯锂基脂。
17.此外,本发明还公开了一种含氟化石墨烯的抗磨减摩锂基润滑脂在降低各装备机械摩擦损耗中的应用。
18.本发明的有益效果主要体现在如下:
19.氟化石墨烯作为锂基润滑脂添加剂对极压、抗磨和减磨等摩擦学性能的影响,结果表明,氟化石墨烯能够对锂基润滑脂的极压性有较大提升,可以作为一种新型的极压抗磨添加剂,并且具有一定的减磨性能。
20.且氟化石墨作为锂基润滑脂添加剂对极压、抗磨和减磨等摩擦学性能的影响,并与氟化石墨烯作为锂基润滑脂添加剂的摩擦学性能进行比较,结果表明,氟化石墨烯作为润滑脂添加剂对抗磨减磨和极压性能的影响比氟化石墨好。本发明侧重对比分析氟化石墨和氟化石墨烯作为锂基润滑脂润滑剂添加剂的摩擦学性能差异,传统锂基润滑脂通过添加一定比例的氟化石墨提高其抗磨减摩性能,将氟化石墨降维为二维氟化石墨烯之后,在相同添加量情况下,含氟化石墨烯锂基润滑脂的摩擦学性能优于含氟化石墨锂基润滑脂,即氟化石墨烯较氟化石墨更有利于满足日益严苛的润滑要求和节能减排需求。与此同时在四球长磨实验条件下磨斑的大小,结合磨斑表面形貌进一步反应氟化石墨烯对润滑脂的抗磨减磨性能有提升。
附图说明
21.图1为锂基脂的实物图片,其中,图1a为mvi500基础油做锂基脂,图1b为600n基础油做锂基脂;
22.图2为氟化石墨烯的扫描电镜图;
23.图3为氟化石墨烯的透射电镜图;
24.图4为不同氟化石墨烯/氟化石墨含量的锂基脂实物图片;
25.图5为氟化石墨和氟化石墨烯不同加入量对润滑脂工作锥入度的影响图示;
26.图6为氟化石墨和氟化石墨烯不同加入量对润滑脂滴点的影响图示;
27.图7为氟化石墨和氟化石墨烯不同加入量对润滑脂钢网分油量的影响图示;
28.图8为氟化石墨和氟化石墨烯不同加入量对pb值及pd值的影响图示;其中,图8a为不同氟化石墨烯和氟化石墨的锂基润滑脂对 pb值的影响,图8b为不同氟化石墨烯和氟化石墨的锂基润滑脂对 pd值的影响;
29.图9为不同载荷下往复式摩擦及氟化石墨烯和氟化石墨不同加入量对平均摩擦系数的影响图示;其中,图9a为200n载荷下氟化石墨烯、氟化石墨添加量对平均摩擦系数的影响,图9b为400n载荷下氟化石墨烯、氟化石墨添加量对平均摩擦系数的影响;
30.图10为不同载荷下往复式摩擦及氟化石墨烯和氟化石墨不同加入量对磨斑直径的影响图示;
31.图11为不同载荷下钢球表面磨斑形貌图,其中,11a为490n载荷下基础脂+0.5%wtfeg、11b为490n载荷下的基础脂、11c为392n 载荷下基础脂+0.5%wtfe、11d为392n载荷下的基础脂;
32.图12为不同润滑介质时磨损表面元素li1s,c1s,fe2p,f1s和o1s 的xps谱图,其中,12b、12d、12f、12h为基础脂,12a、12c、 12e、12g、12i为基础脂+0.5%wtfeg润滑;
33.图13为不同载荷下往复式摩擦及氟化石墨烯和氟化石墨不同加入量对磨斑直径的影响图示。
具体实施方式
34.为了更好地解释本发明,以下结合具体实施例进一步阐明本发明的主要内容,但本发明的内容不仅仅局限于以下实施例。
35.本技术采用的实验试剂与仪器、装置
36.1、试剂和药品
37.表1主要试剂和药品及其生产厂家
[0038][0039]
2、仪器
[0040]
表2主要仪器及其生产厂家
[0041]
[0042][0043]
实施例1
[0044]
本实施例公开了锂基脂的制备工艺:
[0045]
制作100g稠化剂含量为9.0%wt的12
‑
羟锂基润滑脂,用电子天平分别称取购于9.0g的12
‑
羟基硬脂酸锂皂皂粉,加入烧杯1和烧杯2中,再用电子天平分别称取60.67g的mvi500基础油、600n基础油,加入到烧杯1和烧杯2中,为方便区别,烧杯1中加入mvi500 基础油而烧杯2中加入600n基础油。将烧杯放入润滑脂反应釜中,匀速搅拌升温,达到150
‑
170℃时恒温搅拌保持10
‑
12mins;调高电压使温度继续升高至210
‑
220℃成真溶液,保持恒温膨化5min;再向其中加入剩下的30.33g的基础油,使温度降低至150
‑
170℃维持 10
‑
12min;用玻璃棒保持恒定速度搅拌直至润滑脂温度降至 130
‑
140℃,放置冷却至室温,用三辊研磨机均化、脱气,得到制作完成的润滑脂,如图1所示。结合图1a可知,润滑脂呈橙黄色,表面无明显分油,清澈透亮,润滑脂在盛放器皿中倾斜放置不流动。用相关实验方法分别测得该锂基润滑脂的1/4工作锥入度:61(0.1mm),润滑脂滴点:180℃,润滑脂钢网分油量:2.0%wt。
[0046]
结合图1b可知,润滑脂呈乳白色,表面分油明显,润滑脂不透亮,润滑脂在盛放器皿中晃动时流动明显。用相关实验方法分别测得该锂基润滑脂的1/4工作锥入度;329(0.1mm),润滑脂滴点:178℃,润滑脂钢网分油量:4.8%wt。
[0047]
接下来对上述制备的不同锂基脂的理化指标进行测定和分析;
[0048]
其中,检测结果如表3和表4所示;
[0049]
表3 mvi500基础油各项参数
[0050][0051][0052]
表4 600n基础油参数
[0053][0054][0055]
结合表3、表4可知,两种基础油均是矿物基础油,但mvi500 作为中粘度基础油比600n的粘度更低,据说明书附图图1观测外观和实验数据发现,稠化剂量为9.0%时,对mvi500作基础油的润滑脂的稠化效果比600n做基础油的效果好,因为600n作基础油的锂基脂表面有明显分油,且从可流动性与1/4工作锥入度可以反映出 600n作基础油的锂基润滑脂比mvi500作基础油的润滑脂稠度更小;从润滑脂滴点和钢网分油量数据表明,600n作基础油的锂基脂相较于mvi500作基础油的锂基脂更不适合在高温下工作,且不适合在高温下
长时间工作,因为长时间工作会使得600n作基础油的锂基脂大量分油,加快润滑脂的消耗量,加快润滑剂作用消失的速率。
[0056]
综上所述,当12
‑
羟基硬脂酸锂皂作稠化剂的量为9.0%wt时,选用mvi500作基础油做锂基润滑脂效果比600n作基础油做锂基润滑脂的效果更好。
[0057]
实施例2
[0058]
本实施例是关于氟化石墨烯的制备及表征;
[0059]
其中,购自昂星新型碳材料有限公司的氟化石墨烯,是以石墨烯为原材料,采用化学气象沉积法,用氟原子取代原石墨烯上的c原子,从而制备出具备船式结构的氟化石墨烯。具体结构表征如图2、图3所示。
[0060]
结合图2可知,氟化石墨烯为片状结构,且具有一定的褶皱形貌,且尺寸大小相对均匀。
[0061]
结合图3可知,从图中可以看出清晰的层状结构,证明物质具有空间结构,各层间具有一定间隙。
[0062]
实施例3
[0063]
本实施例公开了制备氟化石墨烯锂基脂;
[0064]
首先,将546.00g mvi500基础油和81.00g十二羟硬脂酸锂皂混合加入反应釜加热,达到150
‑
170℃时恒温搅拌并保持12min;再继续升温至210
‑
220℃成真溶液,恒温膨化5min,迅速将溶液平均分装入在210℃下烘干干燥的9个烧杯中;然后将剩余273.00g基础油平均分成9份,即每份33.33g基础油,并向其中8份加入不同质量分数(0.5wt%、1.0wt%、1.5wt%和2.0wt%)的氟化石墨烯/氟化石墨,然后用kq
‑
250b型超声波清洗器,超声振荡15min,以提高氟化石墨烯/氟化石墨在冷却用油中的分散,将冷却油依次加入9个烧杯中,并记录对应烧杯的添加剂种类和添加剂的量,当温度降到150
‑
170℃,恒温搅拌并保持12min,当温度降至130
‑
140℃时,搅拌均匀,待其冷却至室温时,在三辊研磨机上均化脱气,得到不同含量的氟化石墨烯/氟化石墨的锂基润滑脂如图4所示。
[0065]
进一步的对上述制备的氟化石墨烯/氟化石墨的锂基润滑脂进行理化指标测定及分析。
[0066]
(1)润滑脂锥入度
[0067]
根据gb/t 269方法,用bf
‑
38针入度测定器测定润滑脂锥入度,分别对基础脂,基础脂+0.5%wtfeg,基础脂+1.0%wtfeg,基础脂 +1.5%wtfeg,基础脂+2.0%wtfeg,,基础脂+0.5%wtcfx,基础脂 +1.0%wtcfx.基础脂+1.5%wtcfx和基础脂+2.0wt%cfx共9种润滑脂(其中feg为氟化石墨烯,cfx为氟化石墨),测试1/4工作锥入度,具体数据如图5所示。
[0068]
结合图5可知,随着氟化石墨烯和氟化石墨的添加量的增加,润滑脂的锥入度减小,即润滑脂的稠度提高。当添加量大于1%后,润滑脂的锥入度减小,说明氟化石墨烯和氟化石墨对润滑脂都具有增稠作用,但是添加量过高,可能导致润滑脂皂纤维被破坏,从而又使得锥入度降低。氟化石墨烯相较于氟化石墨是一个二维结构物质,有更大的物质内间距,比表面积更大,分散性更好,所以增稠效果比氟化石墨好。
[0069]
(2)润滑脂滴点
[0070]
根据gb/t 3498方法,利用bf
‑
22润滑脂宽温度范围滴点测定器测定润滑脂滴点,对自制含氟化石墨烯、氟化石墨量不同的锂基润滑脂共9种进行测试,实验数据如图6所示。
[0071]
结合图6可知,氟化石墨烯的加入对润滑脂滴点有所提高,原基础脂的滴点为180℃,加入氟化石墨烯后使润滑脂的滴点增大(添加量为0.5%时达到188℃),说明氟化石墨烯的加入使润滑脂的高温性能得到改善、提升,使润滑脂可用最高温度有所提高,且氟化石墨对润滑脂滴点也有提高,但是与氟化石墨烯对比,对润滑脂滴点的影响较小。
[0072]
(3)润滑脂钢网分油量
[0073]
根据sh/t 0324测定润滑脂钢网分油量测试,对自制含氟化石墨烯、氟化石墨量不同的锂基润滑脂共9种进行测试,实验数据如图 7所示。
[0074]
结合图7可知,氟化石墨烯的加入使润滑脂的钢网分油量有明显下降,说明氟化石墨烯的加入使润滑脂在高温环境下胶体安定性得到提高、增强,使润滑脂的结构更为稳定。氟化石墨也可以提升润滑脂胶体安定性,但提升效果较于氟化石墨烯弱。
[0075]
实施例4
[0076]
本实施例公开了上述实施例3制得的氟化石墨烯锂基脂摩擦学性能研究;
[0077]
其可能采用的实验仪器如表5所示;
[0078]
表5主要仪器及其生产厂家
[0079][0080][0081]
一、进行摩擦学性能测定;
[0082]
(1)高温端面摩擦试验机测氟化石墨烯和氟化石墨对锂基润滑脂极压抗磨性的影响;
[0083]
根据gb/t3142
‑
92方法,采用mmu
‑
10g高温端面摩擦试验机测试润滑脂的承载能力,考察氟化石墨烯与氟化石墨对润滑脂最大无卡咬负荷(p
b pd 1450
±
50r/min25℃),试验时间(10s),本实验使用钢球是石油化学科学院制造的 gcr15标准钢球。
[0084]
(2)rtec多功能摩擦磨损试验机测氟化石墨和氟化石墨烯对锂基润滑脂抗磨减磨性的影响;
[0085]
根据sht 0721
‑
2002方法,采用rtec多功能摩擦磨损试验机考察氟化石墨烯和氟化石墨对高频线性振动条件下的摩擦系数(μ),和磨损量(ω)的影响,实验条件如下:往复行程1mm,频率为50hz,时间2h,实验温度80℃。
[0086]
二、进行极压性能检测;
[0087]
最大无卡咬负荷p
b
,是在四球机测定油样极压性能时,设定一定条件钢球不发生卡咬的最高负荷,其值的大小表示油膜强度的高低。测定的条件为:转速1450
±
50rpm,试验温度:室温,时间10s,负荷根据试样的性能而改变。
[0088]
最小烧结负荷p
d
,指在四球机测定油样极压性能时,设定一定条件钢球正好发生烧结的最小符合,其值的大小表示润滑剂的极限工作能力。测定的条件为:转速1450rpm,室温,时间10s,符合根据试样的性能而改变,一般情况下以80n为测定起点,部分加入极压抗磨添加剂的润滑剂无法测得p
d
值,这一情况下以当磨斑直径为 4mm时的最小负荷为p
d
值。
[0089]
本实验使用基础脂,基础脂+0.5%wtfeg,基础脂+1.0%wtfeg,基础脂+1.5%wtfeg,基础脂+2.0%wtfeg,基础脂+0.5%wtcfx,基础脂+1.0%wtcfx.基础脂+1.5%wtcfx和基础脂+2.0wt%cfx共9种润滑脂,根据实验所测得的p
b
值和p
d
值如图8所示。
[0090]
结合图8可知,基础脂的p
b
值为539n,基础脂加入氟化石墨烯后p
b
值提升至1019n;对比基础脂加入不同添加量的氟化石墨烯的 p
b
值发现,氟化石墨烯在加入到0.5%wt时即达到1019n,随着氟化石墨烯添加量的增加,p
b
值不会随之增大。加入不同添加量的氟化石墨的基础脂的p
b
值也有提升,最大提升在添加量为1.0%wt时p
b
值为931n。基础脂的p
d
值为1235n,基础脂加入氟化石墨烯量为0.5%wt 时p
d
值提升至2450n,基础脂加入同等浓度的氟化石石墨后可将p
d
提升至1960n。
[0091]
综上所述,基础脂中加入氟化石墨烯和氟化石墨后,对于润滑脂的极压抗磨性能有较大的提升,以氟化石墨烯锂基脂极压抗磨性比氟化石墨锂基脂的极压抗磨性更好,氟化石墨烯和氟化石墨的添加量均在加入量为0.5%wt时效果达到最好,且极压性能均不会受到添加量多少所影响。
[0092]
三、进行减磨性能;
[0093]
分别对基础脂,基础脂+0.5%wtfeg,基础脂+1.0%wtfeg,基础脂+1.5%wtfeg,基础脂+2.0%wtfeg,,基础脂+0.5%wtcfx,基础脂 +1.0%wtcfx.基础脂+1.5%wtcfx和基础脂+2.0wt%cfx共9种润滑脂在振动频率50hz,冲程1.0mm,试验温度80℃,施加压力分别为200n和400n条件下实验1h,得到各个摩擦系数,如图9所示。
[0094]
结合图9可知,氟化石墨烯作添加剂的润滑脂对摩擦性能有较大提升。加入了氟化石墨烯的锂基脂,在200n载荷下对摩擦性有部分的提升,最大的提升是当添加量为0.5%时,与基础锂基脂相比摩擦系数减小了21.1%,在400n载荷下,摩擦系数的减小量在添加量为 0.5%时更是达到了25.5%,其余不同添加浓度的锂基脂对摩擦系数也有不同程度的减小。加入氟化石墨的锂基脂,200n载荷下,当氟化石墨的添加量为1.0%时,达到了最好效果,与基础锂基脂摩擦系数减小了10.5%,同样,在400n载荷下,也是在氟化石墨添加量为1.0%时减磨性能最好,摩擦系数降低了15.6%。相较于氟化石墨烯,氟化石墨作为润滑脂添加剂在200n负荷下对的减磨性能较弱于氟化石墨烯。且随着氟化石墨烯和氟化石墨添加量的增加,润滑脂的摩擦系数降低量会有所降低,这是因为氟化石墨烯和氟化石墨本质上是颗粒物,添加量在合适量时,他们堆积的颗粒较少,容易进入摩擦副,而当添加量过多时,会导致较多的氟化石墨烯和氟化石墨推挤,无法全部进入摩擦副参与摩擦,堆积的颗粒反而增大了横向摩擦的摩擦力矩,从而变相增大了摩擦系数,从而导致当添加量大于0.5%时,平均摩擦系数的降低量反而减少。
[0095]
综上所述,氟化石墨烯以添加剂的形式加入锂基润滑脂当中,可以对润滑脂的润滑性能有所提高,在400n载荷下氟化石墨烯所提升的润滑性能比在200n载荷下更为明显、突出。并且在设定的添加量梯度中,氟化石墨烯的在锂基润滑脂中的添加量为0.5%时效果最好。氟化石墨烯作为添加剂的减磨效果比氟化石墨的效果好。
[0096]
四、进行抗磨性能检测;
[0097]
(1)球块模型往复式摩擦磨损实验评定抗磨性能
[0098]
据sht 0721
‑
2002方法,对上述测定减磨性能所使用球块模型中的钢球通过带有十字观察镜的显微镜测量磨斑直径,再根据不同氟化石墨烯添加量的润滑脂,不同氟化石墨添加量的润滑脂所摩出的磨斑直径进行比较,由此评定这些不同氟化石墨烯添加量、不同氟化石墨添加量的锂基润滑脂的抗磨性能的好坏。
[0099]
该实验测定条件与往复式摩擦磨损实验测定条件相同:冲程 1.0mm,振动频率50hz,试验温度80℃,选用脂样为基础脂,基础脂+0.5%wtfeg,基础脂+1.0%wtfeg,基础脂+1.5%wtfeg,基础脂 +2.0%wtfeg,,基础脂+0.5%wtcfx,基础脂+1.0%wtcfx.基础脂 +1.5%wtcfx和基础脂+2.0wt%cfx共9种润滑脂,载荷分别为200n 和400n。实验结果如下图10所示。
[0100]
结合图10可知,磨斑直径随着负荷增大而增大,且磨斑直径会因为氟化石墨烯的加入,使磨斑直径减小,但磨斑直径大小不会有随着氟化石墨烯添加量的增多而逐渐变小,但与未添加氟化石墨烯的基础脂相比,其磨斑直径大小呈降低趋势,证明氟化石墨烯作为添加剂能够增强润滑脂的抗磨性。在200n载荷下,当氟化石墨烯添加量达到0.5%时效果最好,磨斑直径减小了15.8%。在400n负荷下,氟化石墨烯展现了更好的抗磨性能,添加量为0.5%时,磨斑直径减小量达到了21.6%。从图线上看,氟化石墨同样拥有提升润滑脂抗磨性的效果,但相较于氟化石墨烯较弱。
[0101]
(2)四球磨损试验机法摩擦磨损实验评价抗磨性能
[0102]
采用mrs
‑
1型四球长时抗磨试验机法,通过评价下球盘三个钢球平均摩擦直径的变化,再次验证氟化石墨烯对润滑脂抗磨性能有提升。
[0103]
该实验测定条件如下:转速1200
±
50rpm,室温,时间1.0h,选用脂样为自制基础脂,基础脂+0.5%wtfeg,基础脂+1.0%wtfeg,基础脂+1.5%wtfeg,基础脂+2.0%wtfeg,,基础脂+0.5%wtcfx,基础脂 +1.0%wtcfx.基础脂+1.5%wtcfx和基础脂+2.0wt%cfx共9种润滑脂,载荷分别为392n和490n,实验结果如下图11所示。
[0104]
结合图13可知,磨斑直径随负荷增大而增大;且氟化石墨烯锂基脂抗磨性能明显增强,但不会随着氟化石墨烯的含量增加而继续提高抗磨性能,且氟化石墨烯的在490n负荷下的抗磨效果更明显。
[0105]
五、对钢球磨斑表面进行分析;
[0106]
为了更直观的分析加入氟化石墨烯前后的润滑脂在摩擦实验后钢球表面磨斑的差异,采用扫描电子显微镜(sem)对样品的磨斑表面形貌进行分析和x射线能谱仪(xps)对磨斑表面参与方反应元素和对应价电子进行表征。为更直观的展现润滑脂添加氟化石墨烯前后对钢球磨斑表面的影响,直接观察在四球摩擦磨损试验机下负荷在 392n和490n实验下抗磨性最优的添加量为0.5%的润滑脂和基础脂实验后的钢球表面磨斑进行观测,如图12所示。
[0107]
结合图11可知,磨斑在放大500倍下观测,可以清楚看到由摩擦而产生的表面犁沟;分别比较同一作用力下氟化石墨烯在润滑脂中含量为0.5%wt和基础脂,可以发现,无论是在392n的载荷下或者是在490n的载荷下,都有效的减少了由于摩擦所产生的犁沟数量,从而证明氟化石墨烯作为锂基润滑脂添加剂,能够有效提升润滑脂抗磨性。
[0108]
为进一步分析磨斑表面润滑油膜的物相组成,对添加了0.5%wt 氟化石墨烯前后的润滑脂在392n载荷下润滑的磨斑表面进行了xps 对比分析,如图12所示。
[0109]
结合图12可知,未加入氟化石墨烯时fe2p1/2和fe2p3/2的谱峰分别为711.3ev和724.0ev,对应于fe2o3这说明在摩擦过程中,钢球表面因为摩擦发生氧化反应,从而产生了摩擦反应膜,同时li1s谱峰为55.4ev,对应于li2o,这说明在摩擦过程中,因为摩擦生热,导致局部高温,硬脂酸锂发生反应形成了li2o摩擦反应膜。
[0110]
加入氟化石墨烯后,f1s的谱峰为685.4ev,证明钢球表面因为氟化石墨烯的加入后f元素也参与如反应膜的生成,从而提高了抗磨性能,fe和li的相对元素含量也分别由1.18%和27.35%提升至1.49%和54.72%,表明了磨斑表面有更多的fe2o3和li2o和部分含氟化合物共同产生了摩擦反应膜,从而降低了摩擦系数,减少了磨损量,对摩擦副表面有更好的保护作用。
[0111]
综上所述,氟化石墨烯作为锂基润滑脂添加剂对极压、抗磨和减磨等摩擦学性能的影响,结果表明,氟化石墨烯能够对锂基润滑脂的极压性有较大提升,可以作为一种新型的极压抗磨添加剂,并且具有一定的减磨性能。
[0112]
且氟化石墨作为锂基润滑脂添加剂对极压、抗磨和减磨等摩擦学性能的影响,并与氟化石墨烯作为锂基润滑脂添加剂的摩擦学性能进行比较,结果表明,氟化石墨烯作为润滑脂添加剂对抗磨减磨和极压性能的影响比氟化石墨好。
[0113]
与此同时在四球长磨实验条件下磨斑的大小,结合磨斑表面形貌进一步反应氟化石墨烯对润滑脂的抗磨减磨性能有提升。
[0114]
以上实施例仅为最佳举例,而并非是对本发明的实施方式的限定。除上述实施例外,本发明还有其他实施方式。凡采用等同替换或等效变换形成的技术方案,均落在本发明要求的保护范围。