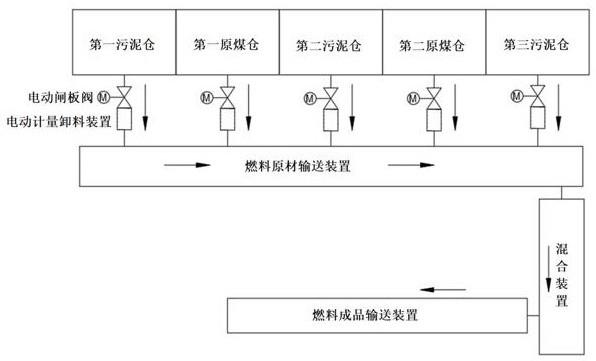
1.本发明涉及一种污泥处理设备,具体而言,涉及一种污泥协同处置自动掺配系统及应用该系统的掺配方法,属于工业、市政污泥处理领域。
背景技术:
2.随着我国城市化进程步伐的加快,针对城市中污水、污泥的处理方式也在不断发生着变化。现阶段,我国对于污泥最为普遍的处理方式当属污泥焚烧,而为了保证焚烧效率,在焚烧前还需要对污泥进行脱水处理。
3.目前,在国内城市污水处理厂的污泥脱水工艺中,设备主要以带式脱水机、离心式脱水机和板框压滤机为主,经带式脱水机、离心式脱水机处理后的污泥含水率约75%~85%左右、经板框压滤机脱水后的污泥含水率约55%~65%左右,这些污泥在进行后续的协同处置时,一般会在处置中心内通过铲车、行车等工具车与原煤进行简单混和,最后被送入锅炉焚烧中。
4.污泥协同处置焚烧时所使用的锅炉一般为流化床锅炉或者鼓泡床锅炉,此类锅炉受燃料热值变化影响较大,燃料混和不均匀会直接导致入炉燃料热值不均匀、造成锅炉燃烧工况不稳定,进而影响整个系统的稳定运行、严重时还会造成锅炉灭火等重大事故。特别是单机炉运行对外供热供汽情况下,负荷不稳定多会造成对外供热不稳定,很容易出现劣质产品、引起客户投诉。
5.为了避免上述现象的发生,提高燃料热值、保证燃料混合均匀也就成为了业内所普遍关注的问题。经过带式脱水机、离心式脱水机及板框压滤机脱水后的污泥含水率相对较高且热值相对较低,并不利于后续协同处置,为此,近年来在污泥初步脱水的基础上,还会对含水率为55%~85%的污泥采取低温干化和圆盘干化工艺,进一步将其含水率降低至30%~45%左右,然后和燃煤按一定比例掺配送至电站锅炉进行统一集中协同处置。虽然上述操作能够降低污泥的含水率,但实际的掺配过程仍然是将污泥与燃煤简单混和,不仅掺配过程中的飞灰和扬尘较大,而且混和不均匀的现象并不能得到显著地改善,还是会影响到锅炉的燃烧工况。
6.综上所述,如何在现有的技术条件下,提出一种系统性的、污泥协同处置自动掺配系统及应用该系统的掺配方法,使燃煤与污泥实现均匀混和,有效解决入炉燃料热值均匀性,也就成为了目前行业内技术人员亟待解决的问题。
技术实现要素:
7.鉴于现有技术存在上述缺陷,本发明的目的是提出一种污泥协同处置自动掺配系统及应用该系统的掺配方法,具体如下。
8.一种污泥协同处置自动掺配系统,由原煤与污泥储存组件、计量组件、燃料输送组件以及混合装置四部分组成;所述原煤与污泥储存组件包括多个用于存储原煤的原煤仓及多个用于存储污泥的污泥仓,多个所述污泥仓内所存储的污泥含水量各异;所述计量组件
包括多个用于控制卸料作业的电动计量卸料装置,所述电动计量卸料装置的数量与所述原煤仓与所述污泥仓二者的总数量相同;所述燃料输送组件包括将原煤与污泥输送至混合装置的燃料原材输送装置及从混合装置内将燃料成品运出的燃料成品输送装置;所述原煤仓与所述污泥仓均借助输送管道连接至所述燃料原材输送装置,每条所述输送管道上均设置有一个所述电动计量卸料装置。
9.优选地,所述原煤与污泥储存组件包括两个原煤仓及三个污泥仓,两个所述原煤仓分别为第一原煤仓及第二原煤仓,三个所述污泥仓分别为第一污泥仓、第二污泥仓以及第三污泥仓;沿所述燃料原材输送装置的输送方向,所述原煤与污泥储存组件内的仓体设置按序依次为第一污泥仓、第一原煤仓、第二污泥仓、第二原煤仓以及第三污泥仓。
10.优选地,所述第一污泥仓内所存储的污泥含水量为60%,所述第二污泥仓内所存储的污泥含水量为80%,所述第三污泥仓内所存储的污泥含水量为40%。
11.优选地,所述燃料原材输送装置内设置有至少两条输送皮带,所述输送皮带间平行设置;在所述输送皮带的运行状态下,所述原煤仓内的原煤落入位于上层的所述输送皮带上并由其输送至所述混合装置,所述污泥仓内的污泥落入位于下层的所述输送皮带上并由其输送至所述混合装置。
12.优选地,所述计量组件还包括多个电动闸板阀,所述电动闸板阀的数量与所述电动计量卸料装置的数量相同;每条所述输送管道的前段均设置有一个电动闸板阀、用于控制该条管道开闭,每条所述输送管道的后段均设置有一个所述电动计量卸料装置。
13.优选地,还包括一台用于实现系统自动化运作的控制终端,所述计量组件、燃料输送组件以及混合装置均与所述控制终端电性连接并由其控制驱动;所述控制终端内设置有联锁保护机构,所述联锁保护机构分别与所述电动计量卸料装置、燃料输送组件以及混合装置相关联、用于在所述燃料输送组件或所述混合装置的停止状态时关闭所述电动计量卸料装置。
14.一种污泥协同处置自动掺配方法,基于如上所述的一种污泥协同处置自动掺配系统,包括如下步骤:
15.s1、确定实际入炉的燃料成品所需要的热值,在控制终端内输入原煤与污泥储存组件内各仓体中燃料原材的热值、设定并匹配各料仓对应的电动计量卸料装置的转速,所述控制终端随即显示最终燃料成品的综合热值;
16.s2、燃料原材输送装置及混合装置启动,待所述混合装置正常运行后、燃料成品输送装置启动;
17.s3、所述控制终端控制与原煤仓相连的输送管道上的电动闸板阀开启、随后启动该管道上的电动计量卸料装置,所述控制终端再控制与污泥仓相连的输送管道上的电动闸板阀开启、随后启动该管道上的所述电动计量卸料装置;
18.s4、所述原煤与污泥储存组件内的污泥与原煤在所述电动计量卸料装置的控制下,沿输送管道落入燃料原材输送装置内、再被送入所述混合装置,经所述混合装置的搅拌混合后、成为燃料成品,最终由所述燃料成品输送装置被送出系统。
19.与现有技术相比,本发明的优点主要体现在以下几个方面:
20.本发明所提供的一种污泥协同处置自动掺配系统,通过设备间的相互配合,既可将污泥独立焚烧过程中含水率不同的污泥进行准确掺配,也可对污泥系统处置过程中的原
煤与污泥进行合理掺配,实现了燃煤与污泥的耦合,有效地提升了入炉燃料的热值均匀性,改善和杜绝了锅炉燃烧负荷恶化和变动大等问题。
21.同时,本发明的系统结构相对简单、可靠,企业可以通过对现有设备的组合、改造而获得本发明的技术方案,硬件制造成本相对较低,且使用效果显著,十分适合生产企业的大规模推广,应用前景广阔。
22.相对应地,本发明的掺配方法基于前述污泥协同处置自动掺配系统,整体过程以自动化地方式进行,不仅掺配过程无需人工干预、节约了人力资源、保证了操作的安全性,而且不同含水率的污泥间、污泥与燃煤间的配比控制精确,显著地提升了掺配结果的准确性。
23.以下便结合实施例附图,对本发明的具体实施方式作进一步的详述,以使本发明技术方案更易于理解、掌握。
附图说明
24.图1为本发明的系统架构示意图。
具体实施方式
25.本发明揭示了一种污泥协同处置自动掺配系统及应用该系统的掺配方法,具体方案如下。
26.如图1所示,一种污泥协同处置自动掺配系统,由原煤与污泥储存组件、计量组件、燃料输送组件以及混合装置四部分组成。
27.所述原煤与污泥储存组件包括多个用于存储原煤的原煤仓及多个用于存储污泥的污泥仓,多个所述污泥仓内所存储的污泥含水量各异。在本实施例中,所述原煤与污泥储存组件包括两个原煤仓及三个污泥仓,两个所述原煤仓分别为第一原煤仓及第二原煤仓,三个所述污泥仓分别为第一污泥仓、第二污泥仓以及第三污泥仓。所述第一污泥仓内所存储的污泥含水量为60%,所述第二污泥仓内所存储的污泥含水量为80%,所述第三污泥仓内所存储的污泥含水量为40%。
28.所述燃料输送组件包括将原煤与污泥输送至混合装置的燃料原材输送装置及从混合装置内将燃料成品运出的燃料成品输送装置。所述燃料原材输送装置内设置有至少两条输送皮带,所述输送皮带间平行设置;在所述输送皮带的运行状态下,所述原煤仓内的原煤落入位于上层的所述输送皮带上并由其输送至所述混合装置,所述污泥仓内的污泥落入位于下层的所述输送皮带上并由其输送至所述混合装置。这样的设置可以保证原煤与污泥在进入所述混合装置后能够被充分搅拌、达到锅炉掺烧要求、实现协同处置的目的。
29.还需要补充的是,沿所述燃料原材输送装置的输送方向,所述原煤与污泥储存组件内的仓体设置按序依次为第一污泥仓、第一原煤仓、第二污泥仓、第二原煤仓以及第三污泥仓。
30.所述计量组件包括多个用于控制卸料作业的电动计量卸料装置,所述电动计量卸料装置的数量与所述原煤仓与所述污泥仓二者的总数量相同;所述原煤仓与所述污泥仓均借助输送管道连接至所述燃料原材输送装置,每条所述输送管道上均设置有一个所述电动计量卸料装置。
31.所述计量组件还包括多个电动闸板阀,所述电动闸板阀的数量与所述电动计量卸料装置的数量相同;每条所述输送管道的前段均设置有一个电动闸板阀、用于控制该条管道开闭,每条所述输送管道的后段均设置有一个所述电动计量卸料装置。
32.除上述装置外,本发明的一种污泥协同处置自动掺配系统,还包括一台用于实现系统自动化运作的控制终端,所述计量组件、燃料输送组件以及混合装置均与所述控制终端电性连接并由其控制驱动;所述控制终端内设置有联锁保护机构,所述联锁保护机构分别与所述电动计量卸料装置、燃料输送组件以及混合装置相关联,所述联锁保护机构用于在所述燃料输送组件或所述混合装置的停止状态时关闭所述电动计量卸料装置、防止所述燃料输送组件的皮带或所述混合装置突然跳闸后所述电动计量卸料装置未及时停止引起堵煤现象。
33.综上所述,本发明所提供的一种污泥协同处置自动掺配系统,通过设备间的相互配合,既可将污泥独立焚烧过程中含水率不同的污泥进行准确掺配,也可对污泥系统处置过程中的原煤与污泥进行合理掺配,实现了燃煤与污泥的耦合,有效地提升了入炉燃料的热值均匀性,改善和杜绝了锅炉燃烧负荷恶化和变动大等问题。
34.同时,本发明的系统结构相对简单、可靠,企业可以通过对现有设备的组合、改造而获得本发明的技术方案,硬件制造成本相对较低,且使用效果显著,十分适合生产企业的大规模推广,应用前景广阔。
35.一种污泥协同处置自动掺配方法,基于如上所述的一种污泥协同处置自动掺配系统,包括如下步骤:
36.s1、确定实际入炉的燃料成品所需要的热值,在控制终端内输入原煤与污泥储存组件内各仓体中燃料原材的热值、设定并匹配各料仓对应的电动计量卸料装置的转速,所述控制终端随即显示最终燃料成品的综合热值,设置完成后,系统依次执行后续步骤;
37.s2、燃料原材输送装置及混合装置启动,待所述混合装置正常运行后、燃料成品输送装置启动;
38.s3、所述控制终端控制与原煤仓相连的输送管道上的电动闸板阀开启、随后启动该管道上的电动计量卸料装置,所述控制终端再控制与污泥仓相连的输送管道上的电动闸板阀开启、随后启动该管道上的所述电动计量卸料装置,需要补充的是,所述污泥协同处置自动掺配系统的停止步骤与上述启动步骤相反;
39.s4、所述原煤与污泥储存组件内的污泥与原煤在所述电动计量卸料装置的控制下,沿输送管道落入燃料原材输送装置内、再被送入所述混合装置,经所述混合装置的搅拌混合后、成为燃料成品,最终由所述燃料成品输送装置被送出系统。
40.需要补充的是,在所述污泥协同处置自动掺配系统前,需要根据生产部门提出的热值需求单、化验室提供的燃煤化验单、公式计算出燃煤及污泥的数量及合理配比,确定称重装置数量。生产过程中,依次启动混合装置、燃料输送组件、计量组件,在通过事先调整好电动计量卸料装置参数的情况下,即可取得锅炉燃烧需要的燃煤与污泥热值最佳配比。
41.具体操作时,可以列出如下表格。
[0042][0043]
其中,a1、a2及b1、b2、b3由化验室提供数据,x1、x2及y1、y2、y3可调整所述电动计量卸料装置的转速取得。以上数据可在所述控制终端的控制面板上输入,正常情况下,每批次入场煤a1、a2及b1、b2、b3数据基本不变,如果有变化也可在输入面板内进行修改。通过调整控制面板上计量装置的转速即可获得x1、x2及y1、y2、y3的数量,通过所述控制终端的后台计算即可混合燃料的热值。且根据化验室提供的化验单,每次入厂煤的热值发生变动时,所述控制终端内的数值均需要重新设置。
[0044]
在实际生产过程中,生产部门可根据各种燃料的库存情况及锅炉燃烧需要在控制面板输入各料仓相对应的所述电动计量卸料装置的转速,就可得到污泥和燃煤的准确配比。
[0045]
在实际的系统设置时,污泥仓和原煤仓可根据实际需求选用。如果后续的焚烧处理系统为独立焚烧系统,可根据实际情况取消原煤仓,此时可取x1、x2为零;若不取消原煤仓,可做污泥储存仓用,计算方法不变。
[0046]
相对应地,本发明的掺配方法基于前述污泥协同处置自动掺配系统,整体过程以自动化地方式进行,不仅掺配过程无需人工干预、节约了人力资源、保证了操作的安全性,而且不同含水率的污泥间、污泥与燃煤间的配比控制精确,显著地提升了掺配结果的准确性。
[0047]
本发明还为同领域内的其他相关问题提供了参考,可以以此为依据进行拓展延伸,运用于领域内其他污泥协同处置设备及方法的相关方案中,具有十分广阔的应用前景。
[0048]
对于本领域技术人员而言,显然本发明不限于上述示范性实施例的细节,而且在不背离本发明的精神和基本特征的情况下,能够以其他的具体形式实现本发明。因此,无论从哪一点来看,均应将实施例看作是示范性的,而且是非限制性的,本发明的范围由所附权利要求而不是上述说明限定,因此旨在将落在权利要求的等同要件的含义和范围内的所有变化囊括在本发明内,不应将权利要求中的任何附图标记视为限制所涉及的权利要求。
[0049]
最后,应当理解,虽然本说明书按照实施方式加以描述,但并非每个实施方式仅包含一个独立的技术方案,说明书的这种叙述方式仅仅是为清楚起见,本领域技术人员应当将说明书作为一个整体,各实施例中的技术方案也可以经适当组合,形成本领域技术人员可以理解的其他实施方式。