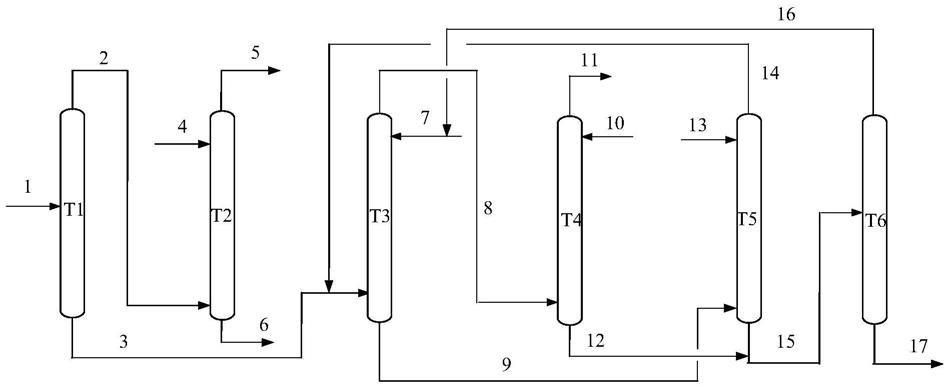
1.本发明属于费托合成油的精制技术领域,涉及一种费托合成油的分离方法,更具体的涉及从费托合成油中脱除醇、醛、酮、酸、酯类含氧化合物的方法。
背景技术:
2.费托合成是以合成气(co和h2)为原料,在催化剂作用下合成液体燃料的技术,是将煤或天然气转化为液体燃料和化学品的有效手段。费托合成油是费托合成的主要产物,具有无硫、无氮、多烯烃的特点,是生产燃料油品和提炼化工产品的重要原料,可进一步加工成汽油、柴油、航空煤油以及提炼出多种高价值化工产品。
3.高温费托合成油中含有一定量的醇、醛、酮、酸、酯等含氧化合物,这些含氧化合物降低了油品品质,对油品深加工造成严重影响,具体表现为:(1)油品中的有机酸会在后续加工中腐蚀设备,影响合成油下游开发进程;(2)和油品中的烃类相比,这些含氧化合物活性高,极性大,能使催化剂中毒,不利于α
‑
烯烃聚合生产pao;(3)氧化物在油品中的存在,增加了油品的极性,不利于从油品中分离提纯烃类组分。因此需要对费托合成油进行脱氧精制以提高油品性质,更好地发挥费托合成油品的优越性。
4.专利文献us4686317公开了一种从烃类(c2‑
c9)组分中脱除氧化物的方法,该方法以碳酸丙烯酯、糠醛、乙醇胺等有机溶剂为萃取剂,通过两级萃取和水洗,能将油品中氧化物降至0.1%以下,受萃取剂沸点的限制,该方法难以将高沸点馏分的氧化物脱除。
5.专利文献wo9958625公开了一种从烃类(c3‑
c
20
)物流中脱除氧化物的方法,该方法含水质量分数为18%的乙腈为萃取剂,该方法能将烃类物流中氧化物脱至较低值,但乙腈萃取剂极易挥发,毒性大。
6.专利文献us2494371公开了一种从费托油品中脱除氧化物的方法,该方法是以甲醇碱溶液为萃取剂,萃取后的萃余油中含有甲醇发生酯化反应的产物,需通过蒸馏法将萃余油中的酯类分离。该方法涉及萃取和蒸馏两个工艺过程,使产品油收率进一步降低,同时产品油中混有的酯类较难完全分离。
7.专利文献us2610977用低碳醇的水溶液分离烃中的醇,该方法为了使醇从烃中有效分离,使用的油剂比高达1:8~9,萃取剂用量大,且烃中氧化物的类型只有醇,原料体系简单。
8.专利文献us2746984为将脂肪族醇从醇烃混合物中分离出来,先用硼酸与醇烃混合物中的醇发生反应生成酯,而后用甲醇、乙醇、水等溶剂进行萃取,再将硼酸酯水解,从而得到脂肪族醇。该方法涉及酯化和水解两步化学反应,工艺复杂,且处理物料体系中只有醇类含氧化合物。
9.专利文献cn108822885a采用有机溶剂、胺类溶剂和烃类有机溶剂复配构成的复合萃取剂,对费托油中的含氧化合物具有优异的萃取脱除效果,含氧化合物脱除率最高可达99%以上,烃损失率最低可小于1%。该方法受萃取剂沸点限制,无法脱除高沸点馏分中的氧化物。
10.上述的公开工艺中,有的仅适合窄馏分的费托合成油脱氧,而针对宽馏分费托合成油脱氧的方法的工艺流程都比较复杂。
11.基于此,本领域技术人员有必要提供一种工艺流程简便、萃取分离效率高、萃取剂易于再生、工艺更加绿色环保的费托合成油的分离方法。
技术实现要素:
12.针对上述现有技术中的不足,本发明提供了一种工艺流程简便、萃取分离效率高、萃取剂易于再生、工艺更加绿色环保、适合工业化生产的费托合成油的分离方法。
13.本发明的目的之一是提供一种费托合成油的分离方法,采用了如下的技术方案:
14.一种费托合成油的分离方法,该方法包括如下步骤:
15.a.将费托合成油物流分成c5~c7馏分物流和c
8+
馏分物流;以第一水物流为溶剂,对c5‑
c7馏分物流进行液液逆流萃取,得到脱氧c5~c7物流和第一含氧化合物水溶液物流;以低碳醇水溶液物流为萃取剂,对c
8+
馏分物流进行液液逆流萃取,得到萃余相物流和萃取相物流;
16.b.以第二水物流对萃余相物流进行逆流水洗,脱除油中夹带的萃取剂后,分别得到脱氧c
8+
物流及第一萃取剂水溶液物流;
17.以第三水物流对萃取相物流进行逆流水洗反萃取,脱除萃取相中夹带的烃组分,分别得到凝析油物流及第二萃取剂水溶液物流;其中,凝析油物流返回至步骤a中与c
8+
馏分物流一同进行液液逆流;
18.c.将步骤b中得到的第二萃取剂水溶液物流以及第一萃取剂水溶液物流进行萃取剂再生,分别得到再生萃取剂物流及第二含氧化合物水溶液物流;其中,再生萃取剂物流返回至步骤a中用于对c
8+
馏分物流进行液液逆流萃取;对第二含氧化合物水溶液物流及步骤a中对c5~c7馏分萃取后得到的第一含氧化合物水溶液物流进行精馏,将含氧化合物与水分离。
19.优选的,所述费托合成油的碳数为c5~c
20
,所述费托合成油中含氧化合物的质量百分含量为1~15wt%,所述的氧化合物包括不同碳数的醇、醛、酮、酸、酯。
20.优选的,步骤a中,所述的费托合成油物流进入油品切割塔对c5~c7馏分和c
8+
馏分进行分离;所述油品切割塔的理论塔板数为10~60块,回流比为1~8,进料位置为上起第3~55块。该工艺参数使得塔顶得到的c5~c7馏分中c
8+
烃的质量含量<0.3wt%,塔釜c
8+
馏分中c7‑
烃的质量含量<0.3wt%。
21.优选的,步骤a中,所述的c5‑
c7馏分物流进入第一萃取塔进行液液逆流萃取。
22.进一步的,所述第一萃取塔的操作温度为5~60℃、压力为0~0.5mpa,理论萃取级数为1~8级,优选2~4级;第一水物流与c5‑
c7馏分物流进入第一萃取塔内的水油体积比为1~8,优选2~4。
23.优选的,步骤a中,所述的c
8+
馏分物流进入第二萃取塔进行液液逆流萃取。
24.进一步的,所述第二萃取塔中采用的萃取剂为低碳醇水溶液,其中,低碳醇为甲醇、乙醇、异丙醇、正丙醇中的一种或几种。低碳醇优选甲醇、乙醇,或二者的混合物。
25.进一步的,所述萃取剂低碳醇水溶液中,低碳醇的体积百分数为30~95%。低碳醇的体积百分数优选为60~85%。
26.进一步的,所述第二萃取塔的操作温度5~50℃、压力为0~0.5mpa,理论萃取级数为1~8级,优选2~4级,萃取剂低碳醇水溶液与c
8+
馏分物流进入第二萃取塔内的剂油体积比为1~8,优选2~4。
27.优选的,步骤b中,萃余相物流进入第一水洗塔下部,与从上部进入的第二水物流逆流接触进行水洗。
28.进一步的,所述第一水洗塔的操作温度5~60℃,压力为0~0.5mpa,理论级数为1级,第二水物流与萃余相物流进入第一水洗塔内的水油体积比为0.2~2,优选0.5~1。
29.优选的,步骤b中,萃取相物流进入第二水洗塔下部,与从上部进入的第三水物流逆流接触进行水洗。
30.进一步的,所述第二水洗塔的操作温度为5~60℃,压力0~0.5mpa,理论级数为1级,第三水物流与萃取相物流进入第二水洗塔内的水油体积比为0.5~4,优选1~2。
31.优选的,步骤c中,步骤b中得到的第二萃取剂水溶液物流以及第一萃取剂水溶液物流进入萃取剂再生塔,进行萃取剂再生。
32.进一步的,所述的萃取剂再生塔为精馏塔,理论塔板数为10~60块,进料位置为上起第3~55块,回流比为0.5~10,操作压力为常压,塔顶温度为50~80℃,塔釜温度为95~110℃。
33.与现有技术相比,本发明能够带来以下有益效果:
34.本发明对费托合成油中的烃类组分进行分级处理,分别以水物流和低碳醇水溶液实现较重烃类(c8以上)和较轻烃类(c5‑
c7)的梯度分离,利用不同浓度的低碳醇水溶液对烃类化合物溶解度不同的原理,将低碳醇水溶液萃取后的萃取相液进行水洗,回收萃取相液中夹带的烃组分,该过程不引入新溶剂进行反萃取,既回收了萃取相中夹带的烃,后续对萃取剂的再生也简单、环保。与现有技术相比,本方法具有萃取剂再生容易、工艺流程简单、符合绿色环保要求的优点。
附图说明
35.图1为本发明费托合成油分离方法的流程示意图。
36.其中标记符号的含义如下:
37.t1
‑
油品切割塔;t2
‑
第一萃取塔;t3
‑
第二萃取塔;t4
‑
第一水洗塔;t5
‑
第二水洗塔;t6
‑
萃取剂再生塔。
[0038]1‑
费托合成油物流;2
‑
c5~c7馏分物流;3
‑
c
8+
馏分物流;4
‑
第一水物流;5
‑
脱氧c5~c7物流;6
‑
第一含氧化物水溶液物流;7
‑
低碳醇水溶液物流;8
‑
萃余相物流;9
‑
萃取相物流;10
‑
第二水物流;11
‑
脱氧c
8+
物流;12
‑
第一萃取剂水溶液物流;13
‑
第三水物流;14
‑
凝析油物流;15
‑
第二萃取剂水溶液物流;16
‑
再生萃取剂物流;17
‑
第二含氧化合物水溶液物流。
具体实施方式
[0039]
下面将结合具体实施例,对本发明中的技术方案进行清楚、完整地描述。以下实施例仅用于更加清楚地说明本发明的技术方案,而不能以此来限制本发明的保护范围。
[0040]
根据本发明提供的一种实施例,一种费托合成油的分离方法,该方法包括如下步骤:
[0041]
a.将费托合成油物流1分成c5~c7馏分物流2和c
8+
馏分物流3;以第一水物流4为溶剂,对c5‑
c7馏分物流2进行液液逆流萃取,分别得到脱氧c5~c7物流5和第一含氧化合物水溶液物流6;以低碳醇水溶液物流7为萃取剂,对c
8+
馏分物流3进行液液逆流萃取,分别得到萃余相物流8和萃取相物流9;
[0042]
b.以第二水物流10对萃余相物流8进行逆流水洗,脱除油中夹带的萃取剂后,分别得到脱氧c
8+
物流11、含少量萃取剂的水物流12(也即第一萃取剂水溶液物流12);
[0043]
以第三水物流13对萃取相物流9进行逆流水洗反萃取,脱除萃取相中夹带的烃组分,分别得到凝析油物流14,以及萃取剂与水的混合物流(也即第二萃取剂水溶液物流15);其中,凝析油物流14返回至步骤a中与c
8+
馏分物流3一同进行液液逆流;
[0044]
c.将步骤b中得到的第二萃取剂水溶液物流15,以及第一萃取剂水溶液物流12一起进行萃取剂再生,分别得到再生萃取剂物流16和第二含氧化合物水溶液17;其中,再生萃取剂物流16返回至步骤a中用于对c
8+
馏分物流3进行液液逆流萃取;第二含氧化合物水溶液17与步骤a中对c5~c7萃取后得到的第一含氧化合物水溶液物流6进行精馏,将含氧化合物与水分离。
[0045]
根据本实施例,对费托合成油中的烃类组分进行分级处理,分别以第一水物流4和低碳醇水溶液实现较重烃类c8以上和较轻烃类c5‑
c7的梯度分离,利用不同浓度的低碳醇水溶液对烃类化合物溶解度不同的原理,将低碳醇水溶液萃取后的萃取相液进行水洗,相当于萃取相中的醇浓度稀释,降低了低碳醇水溶液对烃类化合物的溶解度,达到回收萃取相液中夹带的烃组分也即分离出油的目的,该过程不引入新溶剂进行反萃取,既回收了萃取相中夹带的烃,后续对萃取剂的再生也简单、环保。与现有技术相比,本方法具有萃取剂再生容易、工艺流程简单、符合绿色环保要去的优点。
[0046]
作为优选的实施例,所述费托合成油的碳数为c5~c
20
,所述费托合成油中含氧化合物的质量百分含量为1~15wt%,所述的氧化合物包括不同碳数的醇、醛、酮、酸、酯。
[0047]
为了提高c5~c7馏分和c
8+
馏分的分离效率,本发明针对各步骤中的工艺条件进行了如下的设计:
[0048]
步骤a中:
[0049]
所述的费托合成油物流1进入油品切割塔t1对c5~c7馏分物流2和c
8+
馏分物流3进行分离,所述油品切割塔t1的理论塔板数为10~60块,回流比为1~8,进料位置为上起第3~55块。该工艺参数使得在塔顶得到的c5~c7馏分中,c
8+
烃的质量含量<0.3wt%,塔釜c
8+
馏分中c7‑
烃的质量含量<0.3wt%。
[0050]
对于分离后的c5~c7馏分物流2及c
8+
馏分物流3:
[0051]
所述的c5‑
c7馏分物流2进入第一萃取塔t2进行液液逆流萃取;其中,所述第一萃取塔t2的操作温度为5~60℃、压力为0~0.5mpa,理论萃取级数为1~8级,优选2~4级;第一水物流4与c5‑
c7馏分物流2进入第一萃取塔t2内的水油体积比(以下简称水油比)为1~8,优选2~4。
[0052]
所述的c
8+
馏分物流3进入第二萃取塔t3进行液液逆流萃取;其中,所述第二萃取塔t3的所用的萃取剂为低碳醇水溶液,低碳醇为甲醇、乙醇、异丙醇、正丙醇中的一种或几种,优选甲醇、乙醇,或二者的混合物。更优的,所述的低碳醇水溶液萃取剂中,低碳醇的体积百分数为30~95%,优选60~85%。所述第二萃取塔t3的操作温度5~50℃、压力为0~
0.5mpa,理论萃取级数为1~8级,优选2~4级,萃取剂低碳醇水溶液与c
8+
馏分物流3进入第二萃取塔t3内的剂油体积比为1~8,优选2~4。
[0053]
步骤b中:
[0054]
萃余相物流8进入第一水洗塔t4下部,与从上部进入的第二水物流10逆流接触进行水洗;所述第二水洗塔t4的操作温度5~60℃,压力为0~0.5mpa,理论级数为1级,第二水物流10与萃余相物流8进入第一水洗塔t4内的水油体积比为0.2~2,优选0.5~1。
[0055]
萃取相物流9进入第二水洗塔t5下部,与从上部进入的第三水物流13逆流接触进行水洗;所述第二水洗塔t5的操作温度为5~60℃,压力0~0.5mpa,理论级数为1级,第三水物流13与萃取相物流9进入第二水洗塔t5内的水油体积比为0.5~4,优选1~2。
[0056]
步骤c中:
[0057]
步骤b中得到的第二萃取剂水溶液物流15以及第一萃取剂水溶液物流12一起进入萃取剂再生塔t6,进行萃取剂再生;所述的萃取剂再生塔t6为精馏塔,理论塔板数为10~60块,进料位置为上起第3~55块,回流比为0.5~10,操作压力为常压,塔顶温度为50~80℃,塔釜温度为95~110℃。
[0058]
利用发明的工艺方法进行具体实施的说明:
[0059]
以下具体实施例中涉及的费托合成油为脱除c4‑
和c
20+
馏分后得到的c5~c
20
馏分,油中烃和各含氧化合物的组成见表1。
[0060]
表1费托合成油中烃和氧化物组成
[0061]
组成烃醇酮醛酸氧化物总量含量、重量%86.766.373.451.072.3513.24
[0062]
实施例1
[0063]
按图1所示流程:
[0064]
a.费托合成油物流1进入油品切割塔t1,在理论塔板数为25块、进料位置为上起第12块,回流比为3的条件下,塔顶得到c
8+
烃含量为0.2wt%的c5~c7馏分物流2,塔釜得到c7‑
烃含量小于0.25wt%的c
8+
馏分物流3;
[0065]
c5~c7馏分物流2进入第一萃取塔t2,以第一水物流4对c5~c7馏分物流2进行液液逆流萃取,在操作温度为25℃、压力为0.1mpag、水油体积比为4,萃取级数为4级的条件下,塔顶得到脱氧c5~c7物流5,脱氧c5~c7物流5中醇含量为0、醛含量为0.002wt%、酮含量为0.006wt%、酸含量为0、含氧化合物总量为0.008wt%,c5~c7烃的质量收率为99.48%,塔釜得到第一含氧化合物水溶液物流6;
[0066]
c
8+
馏分物流3进入第二萃取塔t3,以体积分数为80%的甲醇水溶液物流7为萃取剂对c
8+
馏分物流3进行液液逆流萃取,在操作温度为25℃、压力为0.1mpag,剂油体积比为4,理论萃取级数为4的条件下,塔顶得到萃余相物流8,塔釜得到萃取相物流9。
[0067]
b.萃余相物流8进入第一水洗塔t4下部,与从上部进入的第二水物流10逆流接触,在操作温度为25℃、压力0.1mpa、水油体积比为1,水洗级数为1的条件下,脱除油(萃余相)中夹带的萃取剂后,塔顶得到脱氧c
8+
物流11,该物流中醇含量为0、醛含量为0.0015wt%、酮含量为0.0057wt%、酸含量为0,含氧化合物总量为0.0072wt%,c8+烃的质量收率为99.31%,塔釜得到第一萃取剂水溶液物流12;
[0068]
萃取相物流9进入第二水洗塔t5下部,与从上部进入的第三水物流13逆流接触,在
操作温度为25℃、压力为0.1mpag、在水油比为1、水洗级数为1的条件下,脱除萃取相中夹带的烃组分后,塔顶得到凝析油物流14,主要为萃取相中夹带的c8+烃,该物流返回第二萃取塔t3循环,塔釜得到第二萃取剂水溶液物流15。
[0069]
c.第二萃取剂水溶液物流15和第一萃取剂水溶液物流12一起进入萃取剂再生塔t6,在理论塔板数为20块,进料位置为上起第10块,回流比为3的条件下,操作压力为常压,控制塔顶温度为62~66℃,塔釜温度为101℃,塔顶得到再生萃取剂物流16,该物流返回第二萃取塔t3循环对c
8+
馏分物流3进行液液逆流萃取;塔釜得到第二含氧化合物水溶液物流17,该第二含氧化合物水溶液物流17与第一含氧化合物水溶液物流6一起送入费托合成单元的反应水精馏塔,将含氧化合物物与水分离。
[0070]
实施例2
[0071]
本实施例与实施例1基本相同,不同之处仅在于:
[0072]
a.费托合成油物流1进入油品切割塔t1,在理论塔板数为30块、进料位置为上起第15块,回流比为2的条件下,塔顶得到c
8+
烃含量为0.2wt%的c5~c7馏分物流2,塔釜得到c7‑
烃含量为0.2wt%的c
8+
馏分物流3;其中:
[0073]
c5~c7馏分物流2进入第一萃取塔t2,以第一水物流4为溶剂,在操作温度为30℃、压力为0.1mpag、水油体积比为3,萃取级数为5级的条件下,塔顶得到脱氧c5~c7物流5中醇含量为0、醛含量为0.0028wt%、酮含量为0.0068wt%、酸含量为0、含氧化合物总量为0.0096wt%,c5~c7烃的质量收率为99.43%。塔釜得到第一含氧化合物水溶液物流6;
[0074]
c
8+
馏分物流3进入第二萃取塔t3,以体积分数为70wt%的乙醇水溶液物流7为萃取剂,在操作温度为30℃、压力为0mpag,剂油体积比为3,理论萃取级数为2的条件下,塔顶得到萃余相物流8,塔釜得到萃取相物流9;
[0075]
b.萃余相物流8进入第一水洗塔t4,与从上部进入的第二水物流10逆流接触,在操作温度为30℃、压力0.1mpa、水油体积比为1,水洗级数为1的条件下,塔顶得到脱氧c
8+
物流11,该物流中醇含量为0、醛含量为0.0024wt%、酮含量为0.0067wt%、酸含量为0,含氧化合物总量为0.0091wt%,c8烃的质量收率为99.39%;塔釜得到第一萃取剂水溶液物流12;
[0076]
萃取相物流9进入第二水洗塔t5下部,与从上部进入的第三水物流13逆流接触,在操作温度为30℃、压力为0.1mpag、在水油比为1、水洗级数为1的条件下,塔顶得到凝析油物流14,该物流返回萃取塔t3循环,塔釜得到第二萃取剂水溶液物流15;
[0077]
c.第二萃取剂水溶液物流15和第一萃取剂水溶液物流12一起进入萃取剂再生塔t6,在理论塔板数为30块,进料位置为上起第15块,回流比为2的条件下,操作压力为常压,控制塔顶温度为62~66℃,塔釜温度为101℃,塔顶得到再生的萃取剂物流16,该物流返回萃取塔t3循环,塔釜得到第二含氧化物的水溶液物流17,该物流与第一含氧化合物水溶液物流6一起送入费托合成单元的反应水精馏塔,将含氧化合物物与水分离。
[0078]
实施例3
[0079]
本实施例与实施例1的步骤基本相同,不同之处仅在于:
[0080]
步骤a中,将第一萃取塔t2的分离条件改为:理论萃取级数为6级,水油体积比2;将第二萃取塔t3中对c
8+
馏分物流3的萃取剂替换成体积分数为70%的异丙醇水溶液。
[0081]
按照实施例1的方法处理后,得到的脱氧c5~c7物流5中的醇含量为0、醛含量为0.0032wt%、酮含量为0.0065wt%、酸含量为0、含氧化合物总量为0.0097wt%,c5~c7烃质
量收率为99.57%。脱氧c
8+
物流11中的醇含量为0,醛含量为0.0048wt%,酮含量为0.0094wt%,氧化物总含量为0.0142wt%,c5~c7烃质量收率为99.29%。
[0082]
实施例4
[0083]
本实施例与实施例1的步骤基本相同,不同之处仅在于:
[0084]
步骤a中,将第一萃取塔t2的分离条件改为:理论萃取级数为3级,水油体积比5;将第二萃取塔t3中对c
8+
馏分物流3的萃取剂替换成体积分数为70%的正丙醇水溶液。
[0085]
按照实施例1的方法处理后,得到的脱氧c5~c7物流5中的醇含量为0、醛含量为0.0019wt%、酮含量为0.0062wt%、酸含量为0、含氧化合物总量为0.0081wt%,c5~c7烃的质量收率为99.49%。脱氧c
8+
物流11中的醇含量为0,醛含量为0.116wt%,酮含量为0.364wt%,氧化物总含量为0.48wt%,c8+烃质量收率为99.23%。
[0086]
实施例5
[0087]
本实施例与实施例1的步骤基本相同,不同之处仅在于:
[0088]
步骤a中,将第一萃取塔t2的分离条件改为:理论萃取级数为2级,水油体积比6;将第二萃取塔t3对c
8+
馏分物流3的萃取剂替换成体积分数为40%甲醇和40%乙醇的混合物水溶液。
[0089]
按照实施例1的方法处理后,得到的脱氧c5~c7物流5中的醇含量为0、醛含量为0.0031wt%、酮含量为0.0062wt%、酸含量为0、含氧化合物总量为0.0093wt%,c5~c7烃的质量收率为99.59%。脱氧c
8+
物流11中的醇含量为0,醛含量为0.0022wt%,酮含量为0.0065wt%,氧化物总含量为0.0087wt%,c8烃的质量收率为99.35%。
[0090]
实施例6
[0091]
本实施例与实施例1的步骤相同,不同之处仅在于:从第二萃取塔t3塔釜出来的萃取相物流9不经过第二水洗塔t5的水洗处理,不回收萃取液中的夹带的烃组分。
[0092]
按照实施例1的方法处理后,得到的脱氧c5~c7物流5中的氧化物含量与烃收率与实施例1相同。脱氧c8+物流11中醇含量为0、醛含量为0.0014wt%、酮含量为0.0055wt%、酸含量为0,含氧化合物总量为0.0069wt%,c8+烃的质量收率为97.89%,低于经过水反萃取的实施例1的烃收率。
[0093]
应当说明的是,上述实施例均可根据需要自由组合。以上所述仅是本发明的优选实施方式,应当指出,对于本技术领域的普通技术人员来说,在不脱离本发明原理的前提下,还可以做出若干改进和润饰,这些改进和润饰也应视为本发明的保护范围。