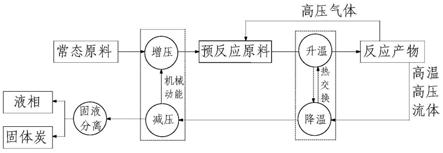
1.本发明涉及水热反应技术领域,尤其涉及一种生物质连续水热转化工艺方法。
背景技术:
2.水热炭化技术是将生物质与水按一定的比例混合放入反应釜中,在一定的反应温度、反应时间和反应压力下进行的温和的水热反应,主要反应机理包括水解、脱水、脱羧、聚合和芳构化,其目标产物是水热炭。水热炭由于表面具有丰富的官能团,以及较大的比表面积和孔隙度等特征,经常用于制备吸附剂、活性剂以及储能储电等领域。
3.在反应过程中,需要对反应釜持续加热,以保证反应所需的高温高压条件。当反应釜内的压力值超过反应所需的最大压力时,需要将反应釜内的高压气体排出,以使反应釜内的压力降低至反应所需压力范围内。向外排出高压气体时,一般直接将高压气体排至大气中,造成了能量的浪费。并且,在向反应釜内添加物料时,还需要利用增压设备克服储料罐与反应釜之间的压差,对增压设备的要求较高。此外,反应完成后,从反应釜排出的反应产物具有较大的压力,直接利用泄压设备进行泄压,也会造成能量的浪费。
4.因此,如何解决现有技术中的水热炭化工艺对加压设备要求高且存在能量浪费的问题,成为本领域技术人员所要解决的重要技术问题。
技术实现要素:
5.针对现有技术存在的问题,本发明实施例提供一种生物质连续水热转化工艺方法。
6.本发明提供一种生物质连续水热转化工艺方法,包括以下步骤:
7.将待反应原料加入反应容器内;
8.对所述待反应原料加热,以使所述待反应原料中分解产生的气体以及所述反应容器中的水汽形成高压环境,并维持反应时间;
9.反应完成后,将部分反应产物从所述反应容器内排出;
10.回收从所述反应容器内排出的所述反应产物的能量;
11.向所述反应容器内补充所述待反应原料;
12.所述待反应原料包括常态原料和位于密闭的预反应器内的预反应原料,在向所述反应容器内补充所述待反应原料之前,利用所述反应容器内的部分高压气体对所述预反应器内的所述预反应原料进行加压处理。
13.根据本发明提供的一种生物质连续水热转化工艺方法,所述加压处理包括:
14.将所述反应容器内的部分所述高压气体通入至所述预反应器内,以提高所述预反应器内的压力,降低所述预反应器与所述反应容器之间的压力差。
15.根据本发明提供的一种生物质连续水热转化工艺方法,所述回收从所述反应容器内排出的所述反应产物的能量包括:
16.回收所述反应产物的压力势能和回收所述反应产物的内能。
17.根据本发明提供的一种生物质连续水热转化工艺方法,所述回收所述反应产物的压力势能包括:
18.利用液压马达将所述反应产物的压力势能转化为机械动能;
19.利用增压泵将所述机械动能转化为所述待反应原料的压力势能,以将所述常态原料输送至所述预反应器内。
20.根据本发明提供的一种生物质连续水热转化工艺方法,在将所述常态原料输送至所述预反应器内之前,还包括:
21.对所述预反应器进行降压处理,以使所述预反应器内的压力小于从所述反应容器内排出的所述反应产物的液体压力。
22.根据本发明提供的一种生物质连续水热转化工艺方法,所述回收所述反应产物的内能包括:
23.利用所述预反应原料与所述反应产物进行热交换,将所述反应产物的热量传递至所述预反应原料。
24.根据本发明提供的一种生物质连续水热转化工艺方法,利用间壁式换热的方法使所述预反应原料与所述反应产物进行直接热交换。
25.根据本发明提供的一种生物质连续水热转化工艺方法,采用列管换热器使所述预反应原料与所述反应产物进行直接热交换。
26.根据本发明提供的一种生物质连续水热转化工艺方法,还包括以下步骤:
27.对所述反应产物进行固液分离,得到液相和固体炭。
28.根据本发明提供的一种生物质连续水热转化工艺方法,利用第一上料位计和第一下料位计将所述反应容器内的物料控制在所述反应容器的容积的75%
‑
85%;
29.利用第二上料位计和第二下料位计将所述预反应器内的所述预反应原料控制在所述预反应器的容积的50%
‑
80%。
30.本发明提供的生物质连续水热转化工艺方法中,在反应完成后,将反应产物从反应容器内排出后,对排出的反应产物的能量进行回收,避免了能量的浪费;在向反应容器内补充待反应原料之前,利用反应容器内的部分高压气体对预反应器内的预反应原料进行加压处理,增加待反应原料的压力,减小了待反应原料与反应容器之间的压力差,从而能够降低对增压设备的要求。解决了现有技术中的水热炭化工艺对加压设备要求高且存在能量浪费的问题。
附图说明
31.为了更清楚地说明本发明或现有技术中的技术方案,下面将对实施例或现有技术描述中所需要使用的附图作一简单地介绍,显而易见地,下面描述中的附图是本发明的一些实施例,对于本领域普通技术人员来讲,在不付出创造性劳动的前提下,还可以根据这些附图获得其他的附图。
32.图1是本发明提供的生物质连续水热转化工艺方法的流程图;
33.图2是本发明提供的用于实施生物质连续水热转化工艺方法的装置示意图。
具体实施方式
34.为使本发明的目的、技术方案和优点更加清楚,下面将结合本发明中的附图,对本发明中的技术方案进行清楚、完整地描述,显然,所描述的实施例是本发明一部分实施例,而不是全部的实施例。基于本发明中的实施例,本领域普通技术人员在没有作出创造性劳动前提下所获得的所有其他实施例,都属于本发明保护的范围。
35.下面结合图1至图2描述本发明实施例的生物质连续水热转化工艺方法。
36.参照图1和图2,本发明实施例提供一种生物质连续水热转化工艺方法,包括以下步骤:
37.将待反应原料加入反应容器内;
38.对所述待反应原料加热,以使所述待反应原料分解产生的气体以及所述反应容器中的水汽形成高压环境,并维持反应时间;
39.反应完成后,将部分反应产物从所述反应容器内排出;
40.回收从所述反应容器内排出的所述反应产物的能量;
41.向所述反应容器内补充所述待反应原料;
42.所述待反应原料包括常态原料和位于密闭的预反应器内的预反应原料,在向所述反应容器内补充所述待反应原料之前,利用所述反应容器内的部分高压气体对所述预反应器内的所述预反应原料进行加压处理。
43.具体来说,先将待反应原料加入至反应容器内,然后通过加热组件对反应容器内的待反应原料加热,使待反应原料分解,同时,待反应原料中的水分受热蒸发,利用分解产生的气体以及反应容器内的水汽在反应容器内形成高压环境,持续加热并维持所需的反应时间,以使待反应原料充分反应。
44.在反应完成后,将部分反应产物从反应容器内排出。从反应容器排出的反应产物为高压流体,将反应产物从反应容器排出后,对反应产物的能量进行回收,避免能量的流失浪费。
45.上述待反应原料包括常态原料和位于密闭的预反应器内的预反应原料。将反应产物排出后,在向反应容器内补充待反应原料之前,利用反应容器内的部分高压气体对位于预反应器内的预反应原料进行加压处理,利用反应容器内的高压气体增加待反应原料的压力,从而减小待反应原料与反应容器之间的压力差,降低对增压设备的要求。
46.向反应容器内补充待反应原料后,循环进行上述步骤。在水热转化过程中,不断有待反应原料输送至反应器内,并且反应产物不断从反应容器内排出,实现连续式转化。
47.如此设置,利用本发明实施例中的生物质连续水热转化工艺方法,能够解决现有技术中的水热炭化工艺对加压设备要求高且存在能量浪费的问题。
48.此外,反应完成后,反应容器内的高压气体还具有较高的温度,将反应容器内的高压气体通入待反应原料后,在增加待反应原料的压力的同时,能够对待反应原料进行预热,实现对热量的回收。
49.本发明实施例中,可以利用导热油与待反应原料进行间壁式换热的方式对反应容器进行加热。例如在反应容器的外侧壁上设置换热夹套,使经加热的高温导热油在换热夹套内流通。
50.本发明实施例中,通过在预反应器和反应容器之间设置增压设备,如螺杆增压泵,
可以将预反应器内的预反应原料输送至反应容器内。在预反应器的上端和反应容器的上端设置回压管路,通过回压管路使反应容器内的部分高压气体通入至预反应器内,使预反应器内的压力增加,从而降低预反应器与反应容器之间的压力差。在回压管路上设置有回压阀,通过回压阀控制回压管路的通断。在反应过程中,需要使回压阀处于关闭状态。
51.本发明实施例中,反应产物为高温高压流体,既具有压力势能,又具有内能,故上述回收从反应容器内排出的反应产物的能量的步骤包括回收反应产物的压力势能和回收反应产物的内能。
52.回收反应产物的压力势能包括以下步骤:
53.利用液压马达将反应产物的压力势能转化为机械动能;
54.利用增压泵将机械动能转化为待反应原料的压力势能,以将常态原料输送至预反应器内。
55.反应容器的出料口处连接有出料管,将液压马达设置在出料管上,高压流体流经液压马达时,依靠高压流体回转产生的动力能够驱使液压马达运转,液压马达的输出轴随之转动,从而将液体压力转化为液压马达的输出轴的机械动能,出料管内的液体压力降低。
56.用于盛放常态原料的容器为储料容器,储料容器与预反应器之间通过进料管连通。在进料管上设置有单向阀,避免预反应器内的预反应原料反流至储料容器内。在储料容器与预反应器之间设置有增压泵,将增压泵设置在进料管上,用于克服预反应器与储料容器之间的压力差,将储料容器内的常态原料输送至预反应器内。将增压泵的输入轴与上述液压马达的输出轴传动连接,液压马达的输出轴转动的同时,带动增压泵的输入轴转动,驱使储料容器内的常态原料逐渐向预反应器内流动,从而将液压马达的输出轴的机械动能转化为待反应原料的压力势能。
57.若预反应器内的压力过大,如预反应器内的压力大于出料管内反应产物的压力,液压马达则难以正常工作,无法驱使增压泵运转。故本发明实施例中,在将常态原料输送至预反应器内之前,需要先对预反应器进行降压处理,降低预反应器内的压力,使预反应器内的压力小于出料管中从反应容器内排出的反应产物的液体压力。具体可在预反应器的上端设置泄压阀,将泄压阀打开,使预反应器内的部分气体排出,即可降低预反应器内的压力。
58.本发明实施例中,利用预反应原料与反应产物进行热交换,将反应产物的热量传递至预反应原料,使反应产物的温度降低,预反应原料的温度升高,从而实现反应产物的内能的回收。利用反应产物对预反应原料预加热后,降低了预反应原料的温度与反应所需温度之间的差值,有利于缩短加热时间,提高效率。
59.本发明实施例中,利用间壁式换热的方法使预反应原料与反应产物进行直接热交换。具体可通过在出料管上套设换热夹套,使预反应原料在换热夹套内流通,从而能够与出料管内的反应产物进行换热。
60.对于预反应原料与反应产物之间的直接热交换可以采用列管换热器实现,列管换热器具有列管和管壳,列管的内部空间和管壳的内部空间相互独立。具体可以使预反应原料在列管内流通,使反应产物在管壳内流通,从而实现高效换热。
61.液压马达的出口连接有暂存罐,完成对反应产物的能量回收之后,可以将反应产物临时储存于暂存罐内。
62.本发明实施例中,完成对反应产物的能量回收之后,还需要对暂存罐内的反应产
物进行固液分离,分别收集液相和固体炭。具体可通过固液分离机实现。
63.本发明实施例中,在反应容器上设置第一上料位计和第一下料位计,将第一上料位计设置在反应容器容积的75%位置处,将第一下料位计设置在反应容器容积的85%位置处,综合利用第一上料位计和第一下料位计将反应容器内的物料控制在反应容器的容积的75%
‑
85%。如此设置,能够减少连续水热过程中反应容器内的压力和温度等参数的波动,保证水热反应过程的稳定以及产物产品的质量。
64.在预反应器上设置第二上料位计和第二下料位计,根据系统经济性,将预反应器的容积设计为反应容器的容积的1/3,同时配合反应容器的物料进出规律,将第二上料位计设置在预反应器容积的80%位置处,将第二下料位计设置在预反应器容积的50%位置处,综合利用第二上料位计和第二下料位计将预反应器内的预反应原料控制在预反应器的容积的50%
‑
80%。
65.在储料容器上也可以设置第三上料位计和第三下料位计,将第三上料位计设置在储料容器容积的80%位置处,将第三下料位计设置在储料容器容积的50%位置处,综合利用第三上料位计和第三下料位计将储料容器内的常态原料控制在储料容器的容积的50%
‑
80%。
66.以下对本发明实施例中的生物质连续水热转化工艺方法进行综合阐述:
67.上述待反应原料可以为玉米秸秆与水的混合物,将玉米秸秆粉碎并与水按一定比例混合可得;
68.在反应之前,将预反应器加料至50%,将反应容器加料至85%,然后使单向阀、泄压阀、回压阀和截止阀均处于关闭状态;
69.利用加热组件对反应容器进行加热至反应容器内的压力和温度均满足反应条件,并维持反应所需的时间;
70.待反应容器内的物料反应结束后,打开截止阀,将反应容器内位于第一下料位计上方的高压高温物料排出;
71.利用液压马达将排出的反应产物的压力势能转化为机械动能,并利用增压泵将机械动能转化为待反应原料的压力势能,从而将储料容器内的常态原料输送至预反应器内;
72.当反应容器内的物料降低至第一下料位计位置时,关闭截止阀,打开回压阀,实现预反应器与反应容器之间的压力连通,利用反应容器内的部分高压气体增加预反应器内的压力;
73.利用增压设备将预反应器内的预反应原料从反应容器的底部输送至反应容器内,当反应容器内的待反应原料增加至第一上料位计位置时,使增压设备停止工作,并关闭回压阀;
74.利用加热组件对反应容器进行加热,待反应结束后,将反应产物排出之前,需要先打开泄压阀使预反应器内的压力降低,至略小于出料管内反应产物的压力,以确保出料管内的高压液体能够驱使液压马达运转,以开始新一轮排出反应产物同时向预反应器内加料的过程。
75.出料管内经液压马达后的反应产物临时储存于暂存罐内,利用固液分离机将液相和固体炭分离即可得到水热炭。
76.最后应说明的是:以上实施例仅用以说明本发明的技术方案,而非对其限制;尽管
参照前述实施例对本发明进行了详细的说明,本领域的普通技术人员应当理解:其依然可以对前述各实施例所记载的技术方案进行修改,或者对其中部分技术特征进行等同替换;而这些修改或者替换,并不使相应技术方案的本质脱离本发明各实施例技术方案的精神和范围。