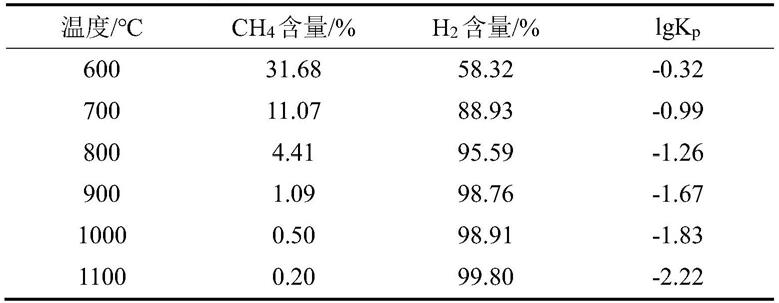
1.本发明属于煤化工技术领域,具体涉及一种煤气化方法、煤气化炉、煤气化系统和煤气化合成氨系统。
背景技术:
2.煤炭作为一种化石燃料,是目前甚至未来很长一段时间内人们生产生活必不可缺的能源之一。如果将煤炭直接燃烧不仅浪费了大量资源,更会排放so2、no
x
、co等有害气体,造成环境污染。因此,推动煤炭的清洁利用已经成为行业发展的必然选择。
3.煤气化是煤炭清洁利用的重要途径之一。现有的煤气化技术是将煤炭加入煤气化炉内,在加压和气化剂存在条件下,使煤炭转化成煤气。煤气中除了有效气(co和h2),还含有较多的ch4。由于煤气中的ch4含量较高,为后续用于合成氨等化学合成具有不利影响。ch4在诸如合成氨等采用煤气作为原料的工艺中为惰性气体,煤气中的ch4含量过高容易导致工艺系统中的压缩机能耗增加,还会导致过多的驰放气排放,因此严重影响合成氨的经济性。因此,开发一种低甲烷煤气化工艺具有重要意义。
技术实现要素:
4.本发明第一方面提供一种煤气化方法,其在煤气化炉中进行,煤气化炉包括气化腔室,气化腔室在高度方向上依次区分为上部区域、中部区域和下部区域,方法包括:将第一气化剂引入气化腔室的下部区域,与经过气化腔室的上部区域和中部区域的气化处理后的煤料进行燃烧反应;将第二气化剂引入气化腔室的中部区域参与气化反应,以产生煤气。
5.本发明第二方面提供一种煤气化炉,包括炉体,炉体设有气化腔室、位于顶部的进煤口、以及位于底部的排渣口,炉体在高度方向上依次区分为上部区域、中部区域和下部区域,其中,在炉体的下部区域设有第一气化剂引入口,在炉体的中部区域设有第二气化剂引入口,第一气化剂入口和第二气化剂入口分别与气化腔室连通。
6.本发明第三方面提供一种煤气化系统,包括:根据本发明的煤气化炉,用于进行煤气化处理;气化剂供应组件,用于通过第一气化剂引入口向煤气化炉的气化腔室供应第一气化剂,以使第一气化剂与经过炉体的上部区域和中部区域的气化处理后的煤料进行燃烧反应,以及通过第二气化剂引入口向煤气化炉的气化腔室供应第二气化剂,以使第二气化剂参与气化反应,以产生煤气。
7.本发明第四方面提供一种煤气化合成氨系统,其包括:造气单元,包括根据本发明的煤气化系统;变换单元,用于接收来自造气单元的合成气,并对合成气进行变换处理,以使co变换为co2,送出变换气体;脱碳单元,用于对来自变换单元的变换气体进行脱碳处理,获得脱碳气体;双甲精制单元,用于对来自脱碳单元的脱碳气体进行双甲精制,获得原料气;合成氨单元,用于接收来自双甲精制单元的原料气,并用原料气合成氨。
8.本发明在现有煤气化炉由下部区域引入气化剂的基础上,还在中部区域引入气化剂参与气化反应,由此能减少煤加氢热解反应生成ch4的量,并且还能促使炉内的ch4进行转
化,从而能降低煤气的ch4含量。低ch4含量的煤气化产品可用作合成氨的原料气,并且有利于降低合成氨系统的驰放气量和能耗。进一步地,采用本发明的方案还可以促进煤气化过程产生的焦油发生裂解,因此能降低煤气的焦油含量,进一步提高有效气(co和h2)占比。
附图说明
9.为了更清楚地说明本发明实施例的技术方案,下面将对本发明实施例中所需要使用的附图作简单地介绍,显而易见地,下面所描述的附图仅仅是本发明的一些实施例,对于本领域普通技术人员来讲,在不付出创造性劳动的前提下,还可以根据附图获得其他的附图。
10.图1是本发明实施例提供的一种煤气化炉的结构示意图。
11.图2是本发明实施例提供的一种煤气化系统的流程图。
12.图3是本发明实施例提供的一种煤气化合成氨系统的流程图。
13.图4是本发明另一实施例提供的一种煤气化合成氨系统的流程图。
14.图5是实施例1的煤气化炉的炉内温度曲线。
15.图6是实施例2的煤气化炉的炉内温度曲线。
具体实施方式
16.为了使本发明的发明目的、技术方案和有益技术效果更加清晰,以下将详细描述本发明的各个方面的特征和示例性实施例。在下面的详细描述中,提出了许多具体细节,以便提供对本发明的全面理解。但是,对于本领域技术人员来说很明显的是,本发明可以在不需要这些具体细节中的一些细节的情况下实施。下面对实施例的描述仅仅是为了通过示出本发明的示例来提供对本发明的更好的理解。在附图和下面的描述中,至少部分的公知结构和技术没有被示出,以便避免对本发明造成不必要的模糊;并且,为了清晰,可能夸大了部分结构的尺寸。此外,下文中所描述的特征、结构或特性可以以任何合适的方式结合在一个或更多实施例中。
17.在本发明的描述中,需要说明的是,除非另有说明,“以上”、“以下”为包含本数;“多个(种)”、“几个(种)”的含义是两个(种)以上;术语“上”、“下”、“左”、“右”、“内”、“外”等指示的方位或位置关系仅是为了便于描述本发明和简化描述,而不是指示或暗示所指的装置或元件必须具有特定的方位、以特定的方位构造和操作,因此不能理解为对本发明的限制。此外,术语“第一”、“第二”等仅用于描述目的,而不能理解为指示或暗示相对重要性。
18.下述描述中出现的方位词均为图中示出的方向,并不是对本发明的实施例的具体结构进行限定。在本发明的描述中,还需要说明的是,除非另有明确的规定和限定,术语“安装”、“连接”应做广义理解,例如,可以是固定连接,也可以是可拆卸连接,或一体地连接;可以是直接相连,也可以间接相连。对于本领域的普通技术人员而言,可视具体情况理解上述术语在本发明中的具体含义。
19.本发明的上述发明内容并不意欲描述本发明中的每个公开的实施方式或每种实现方式。如下描述更具体地举例说明示例性实施方式。在整篇申请中的多处,通过一系列实施例提供了指导,这些实施例可以以各种组合形式使用。在各个实例中,列举仅作为代表性组,不应解释为穷举。
20.作为煤炭清洁利用的重要途径之一,可以使原料煤在煤气化炉内,在加压和气化剂存在条件下,依次经历干燥、干馏、气化、燃烧几个阶段,转化成煤气。原料煤由煤气化炉顶部的进煤口进入气化腔室后,首先经历干燥。在干燥区,原料煤与自下而上的高温煤气逆流接触,对煤气进行降温的同时,其自身温度升高,从而脱除原料煤所携带的水分(如游离水和/或结合水)。煤干燥后,继续向下移动至干馏区,被该区域的高温煤气加热,并发生煤的低温干馏和加氢热解反应,产生焦炭(或半焦)、煤焦油、以及干馏煤气(包括co、h2、co2、ch4及其他烃类等)等。焦炭(或半焦)继续向下移动至气化区进一步升温,并发生一系列氧化还原反应,产生包括co、h2、co2、ch4的粗煤气以及含c固体残余。含c固体残余向下移动至燃烧区,与气化剂接触发生燃烧反应,产生包含co、co2等的气体,同时产生大量的热。气体携带热量向上运动,从而为气化过程提供所需的热量。反应剩余的渣料以固态灰渣或液态熔渣排出气化炉。对于液态熔渣,可以将其进行激冷后破碎成玻璃态渣,以进行资源回收利用。
21.由于现有的煤气化炉是在气化腔室的下部区域引入气化剂,炉内温度由燃烧区域至干燥区域的温度逐步降低,其中干馏区的区间很长,区间温度为250℃~800℃。在此区间会产生大量的ch4,这使得气化炉煤气出口送出的煤气的ch4含量较高。根据原料煤种的不同,煤气的ch4含量在4%~9%。生成ch4的主要反应方程为:
22.煤
→
焦炭+co+h2+ch4+焦油
ꢀꢀꢀ
(1)
[0023][0024]
反应(1)取决于气化煤种中挥发份的含量,挥发份含量越高,反应(1)生成的ch4越高,并且反应(1)生成的ch4是无法通过操作工艺进行抑制的。反应(2)是放热可逆反应,受化学平衡影响严重。反应温度是影响反应(2)平衡常数的主要因素。经实验测得不同温度下平衡时的组分含量和平衡常数lgk
p
见下表:
[0025][0026]
由上表可以看出,由于干馏区的温度<800℃,因此ch4生成量很大。但是当温度为800℃以上时,ch4生成明显受到抑制,并且ch4能进行转化而进一步减少。
[0027]
基于此,本发明对原有煤气化炉和煤气化工艺进行了改进,在已有的由气化腔室下部区域引入气化剂的基础上,还在气化腔室中部区域引入气化剂。由气化腔室中部区域引入的气化剂会与煤气(如co和h2)等反应,并放出大量的热。由此创造的高温(例如≥800℃)环境既能抑制煤加氢热解反应生成的ch4量,还能促使煤干馏产生的ch4发生转化,从而大幅度减少煤气产品的ch4含量。
[0028]
接下来,首先说明本发明提供的一种煤气化方法。本发明的煤气化方法在煤气化
炉中进行,煤气化炉包括气化腔室,气化腔室在高度方向上依次区分为上部区域、中部区域和下部区域,方法包括:将第一气化剂引入气化腔室的下部区域,与经过气化腔室的上部区域和中部区域的气化处理后的煤料进行燃烧反应;将第二气化剂引入气化腔室的中部区域参与气化反应,以产生煤气。
[0029]
煤气化炉可采用固定床气化炉。固定床气化炉通常采用块煤作为原料,在加压下与气化剂反应制取合成气,具有原料适应性广的优点。例如,原料煤可选自无烟煤、烟煤、褐煤等煤种。煤气化炉可以为固态排渣固定床气化炉或液态排渣固定床气化炉。优选地,煤气化炉为液态排渣固定床气化炉。
[0030]
煤气化炉包括炉体,炉体设有气化腔室、位于顶部的进煤口、位于底部的排渣口、以及位于侧壁的煤气出口。并且,在炉体的下部区域设有第一气化剂引入口,在炉体的中部区域设有第二气化剂引入口,第一气化剂入口和第二气化剂入口分别与气化腔室连通。
[0031]
原料煤由进煤口送入气化腔室,并且将第一气化剂由第一气化剂引入口引入气化腔室的下部区域,将第二气化剂由第二气化剂引入口引入气化腔室的中部区域。原料煤经干燥、低温干馏、加氢热解、焦炭(或半焦)的气化反应后剩余的含c固体残余在下部区域与第一气化剂接触发生燃烧反应,以产生炉内一系列反应所需的热量,同时还产生co等还原性气体供反应所需。在气化腔室中部区域,第二气化剂与co和h2等反应,产生的热量创造出抑制ch4生成和促进ch4转化的高温环境,最终产生低ch4含量的煤气。高温环境还可以促进煤气化过程产生的焦油发生裂解,因此能降低煤气的焦油含量,进一步提高有效气(co和h2)占比。
[0032]
在一些实施例中,在第一气化剂的引入位置至第二气化剂的引入位置的区间,气化腔室呈先降低后升高的温度变化,其中该区间的最低温度为850℃~1200℃,优选为850℃~1000℃,更优选为900℃~950℃。在第一气化剂的引入位置至第二气化剂的引入位置的区间的最低温度在适当范围内,有利于使第二气化剂引入位置以下及以上的炉内温度均达到能抑制ch4生成和促进ch4转化的高温,从而降低煤气的ch4含量。此外,炉内温度还能促进煤气中的焦油发生裂解转化,使得煤气的焦油含量减少。因此,所得煤气能获得较高的有效气占比。
[0033]
在一些实施例中,气化腔室对应第二气化剂的引入位置处的温度为1100℃~1300℃,优选为1200℃~1300℃。气化腔室对应第二气化剂的引入位置处的温度较高,有利于提升第二气化剂引入位置以下及以上区域的炉内温度,由此能抑制ch4生成和促进ch4转化,获得低ch4含量的煤气。同时还能促进煤气中的焦油发生裂解转化,降低煤气的焦油含量。气化腔室对应第二气化剂的引入位置处的温度在适当范围内,可以防止该区域的煤料熔融,保证炉内气化过程的稳定进行,获得高有效气占比的煤气。
[0034]
在一些实施例中,煤气化炉的煤气出口位于气化腔室的上部区域,其中气化腔室对应煤气出口处的温度为850℃~950℃,优选为870℃~920℃。气化腔室对应第二气化剂的引入位置以上的温度较高,有利于抑制ch4生成和促进ch4转化,并且有利于焦油裂解转化,从而降低煤气的ch4含量和焦油含量。
[0035]
可以通过调整第二气化剂的引入位置以及第一气化剂和第二气化剂的组成,来控制炉内反应和温度,实现降低煤气的ch4含量和焦油含量。
[0036]
在一些实施例中,由第一气化剂引入气化腔室的氧气与由第二气化剂引入气化腔
室的氧气的体积流量之比为9:1~5:5,优选为7:3~6:4。第一气化剂与第二气化剂的氧气体积流量之比在适当范围内,有利于降低煤气的ch4含量,并且使煤气具有较高的有效气占比。前述体积流量之比可以通过调节第一气化剂的蒸氧比、第一气化剂的流量、第二气化剂的蒸氧比、第二气化剂的流量中的一者以上来进行调控。
[0037]
在一些实施例中,第一气化剂包括氧气和水蒸气。可选地,第一气化剂为氧气和水蒸气的混合气。进一步可选地,水蒸气为过热水蒸气。第一气化剂的水蒸气与氧气的质量体积比可选为0.8kg/nm3~1.2kg/nm3,还可选为0.9kg/nm3~1.1kg/nm3,或0.95kg/nm3~1.05kg/nm3。水蒸气和氧气的质量体积比(可简称为蒸氧比)指的是水蒸气以kg计的质量与氧气以nm3计的体积之比,单位为kg/nm3。nm3是标准立方米,其表示在一个标准大气压(101.325kpa)的压力,0℃的温度,0%的相对湿度下,1立方米的气体量。
[0038]
在一些实施例中,第二气化剂包括氧气和水蒸气。可选地,第二气化剂为氧气和水蒸气的混合气。进一步可选地,水蒸气为过热水蒸气。第二气化剂的蒸氧比为2.0kg/nm3~5.0kg/nm3。第二气化剂的蒸氧比可以在保证第二气化剂引入位置处的煤料不致于烧熔融的前提下,根据原料煤的种类来进行选择和调节。第二气化剂的蒸氧比越小,煤气的ch4含量越低。
[0039]
可选地,灰熔点高的煤可采用较小的二次蒸氧比。作为示例,原料煤的灰熔点>1400℃,第二气化剂中水蒸气与氧气的质量体积比可选为2.5kg/nm3~3.5kg/nm3。
[0040]
可选地,灰熔点较低的煤可采用较大的二次蒸氧比。作为示例,原料煤的灰熔点≤1400℃,第二气化剂的蒸氧比可选为3.0kg/nm3~5.0kg/nm3。
[0041]
煤气化通常在加压的条件下进行。在一些实施例中,气化腔室的压力可选为2.0mpa~6.0mpa,还可选为2.5mpa~5mpa,2.5mpa~4.5mpa,或2.5mpa~4.0mpa。
[0042]
本发明的煤气化炉中,气化腔室的下部区域对应燃烧区。气化腔室的中部区域位于干燥区和燃烧区之间。在一些实施例中,炉体的高度记为h,第二气化剂引入口的设置高度记为h,其中可满足:0.3h≤h≤0.6h。在一些实施例中,0.35h≤h≤0.55h。在一些实施例中,0.4h≤h≤0.5h。在一些实施例中,0.42h≤h≤0.47h。在一些实施例中,0.45h≤h≤0.5h。
[0043]
根据本发明的煤气化方法可以获得低ch4和焦油含量和高有效气含量的煤气。煤气主要成分为co和h2,并且含有co2以及少量的ch4和焦油等气化产物。优选地,煤气中co和h2的含量可以达到80%以上,82%以上,85%以上,甚至88%以上。优选地,煤气中ch4的含量可以低至2%以下,或1.5%以下。优选地,煤气中焦油的含量可以低至1%以下,或0.5%以下。
[0044]
本发明还提供一种煤气化炉。图1是作为一个示例的煤气化炉的结构示意图。参照图1,本发明提供的煤气化炉100包括炉体110,炉体110设有气化腔室、位于顶部的进煤口、以及位于底部的排渣口,炉体在高度方向上依次区分为上部区域、中部区域和下部区域,其中,在炉体110的下部区域设有第一气化剂引入口111,在炉体的中部区域设有第二气化剂引入口112,第一气化剂入口111和第二气化剂入口112分别与气化腔室连通。
[0045]
在一些实施例中,炉体110的高度记为h,第二气化剂引入口112的设置高度记为h,其中可满足:0.3h≤h≤0.6h。在一些实施例中,0.35h≤h≤0.55h。在一些实施例中,0.4h≤h≤0.5h。在一些实施例中,0.42h≤h≤0.47h。在一些实施例中,0.45h≤h≤0.5h。
[0046]
炉体110包括筒体110a以及分设于筒体两端的顶部法兰110b和底部法兰110c。炉体110的高度h是指由顶部法兰110b的顶面至底部法兰110c的底面之间的距离。第二气化剂引入口112的设置高度h是指由第二气化剂引入口112的中心所在水平线至底部法兰110c的底面之间的垂直距离。
[0047]
在一些实施例中,可以在炉体110的中部区域,沿炉体110的周向间隔设置有多个第二气化剂引入口112。例如,第二气化剂引入口112有2、3、4、5或6个等。多个第二气化剂引入口112优选地沿炉体110的周向均匀分布。这样有利于炉内径向温度场和流场的均匀一致性。
[0048]
可以在第二气化剂引入口112设置第二气化剂喷嘴120。通过第二气化剂喷嘴120向气化腔室提供第二气化剂。优选地,第二气化剂喷嘴113由进煤口至排渣口的方向倾斜设置,其中第二气化剂喷嘴120与炉体110的径向之间的夹角为5
°
~22
°
,还可选为8
°
~20
°
,5
°
~15
°
,或5
°
~10
°
。第二气化剂喷嘴120的倾斜角度在适当范围内,有利于气化腔室内形成良好的温度场和流场,进而有助于降低煤气的ch4含量,并且使煤气获得较高的有效气占比。
[0049]
优选地,第二气化剂喷嘴120伸入气化腔室内的深度为300mm~350mm。第二气化剂喷嘴120伸入气化腔室内的深度表示第二气化剂喷嘴120的出口至炉体110内侧壁的垂直距离。第二气化剂喷嘴120伸入气化腔室内的长度在适当范围内,有利于气化腔室内形成良好的温度场和流场,进而有助于降低煤气的ch4含量,并且使煤气获得较高的有效气占比。
[0050]
在一些实施例中,第一气化剂引入口111的设置高度记为g,其中可满足:0.1h≤g≤0.3h。在一些实施例中,0.15h≤g≤0.25h。在一些实施例中,0.1h≤g≤0.2h。在一些实施例中,0.12h≤g≤0.17h。在一些实施例中,0.13h≤g≤0.18h。第一气化剂引入口111的设置高度g是指由第一气化剂引入口111的中心所在水平线至底部法兰的底面110c之间的垂直距离。
[0051]
在一些实施例中,可以在炉体110的下部区域,沿炉体110的周向间隔设置有多个第一气化剂引入口111。例如,第一气化剂引入口111有4、5或6个。多个第一气化剂引入口111优选地沿炉体110的周向均匀分布。
[0052]
可以在第一气化剂引入口111设置第一气化剂喷嘴130。通过第一气化剂喷嘴130向气化腔室提供第一气化剂。优选地,第一气化剂喷嘴130由进煤口至排渣口的方向倾斜设置,其中第一气化剂喷嘴130与炉体110的径向之间的夹角为10
°
~30
°
,进一步优选为15
°
~25
°
,如19℃。
[0053]
优选地,第一气化剂喷嘴130伸入气化腔室内的深度为300mm~350mm。第一气化剂喷嘴130伸入气化腔室内的深度表示第一气化剂喷嘴130的出口至炉体110内侧壁的垂直距离。
[0054]
煤气化炉100的煤气出口113可设置于炉体110的靠近进煤口的位置,以充分利用煤气的显热。在一些实施例中,煤气出口130的设置高度记为t,其中可满足:0.03h≤h
‑
t≤0.2h。在一些实施例中,0.05h≤h
‑
t≤0.1h。在一些实施例中,0.05h≤h
‑
t≤0.15h。煤气出口130的设置高度h是指由煤气出口130的中心所在水平线至底部法兰110c的底面之间的垂直距离。
[0055]
采用本发明的煤气化炉能实施根据本发明的煤气化方法,产生具有低ch4和焦油
含量以及高有效气含量的煤气。
[0056]
本发明还提供一种煤气化系统。该系统能够实施本发明的煤气化方法,产生具有低ch4和焦油含量以及高有效气含量的煤气。图2是作为一个示例的煤气化系统的流程图。参照图2,本发明提供的一种煤气化系统包括煤气化炉100和气化剂供应组件200。
[0057]
煤气化炉100采用根据本发明的煤气化炉100。
[0058]
气化剂供应组件200用于通过第一气化剂引入口111向煤气化炉100的气化腔室供应第一气化剂,以使第一气化剂与经过炉体110的上部区域和中部区域的气化处理后的煤料进行燃烧反应,以及通过第二气化剂引入口向煤气化炉100的气化腔室供应第二气化剂,以使第二气化剂参与气化反应,以产生煤气。气化剂供应组件200可以采用本领域已知的向煤气化炉100供应气化剂的组件。例如,气化剂供应组件200可包括蒸汽管道,氧气管道,与蒸汽管道和氧气管道连接的蒸氧混合器210,以及连接于蒸氧混合器210和煤气化炉100之间的蒸氧管道。
[0059]
在一些实施例中,煤气化系统还包括除尘装置300。除尘装置300的进口与煤气化炉100的煤气出口113连接,用于对煤气化炉100送出的煤气进行除尘。除尘装置300可采用本领域已知的用于煤气除尘的装置,例如文丘里洗涤器。文丘里洗涤器可采用本领域已知的洗涤液,例如水。
[0060]
煤气化炉100送出的煤气温度较高,为了进行余热回收,在一些实施例中,煤气化系统还可以包括余热回收装置400。余热回收装置400可以与除尘装置300的气体出口连接,用于对来自除尘装置300的煤气进行余热回收。余热回收装置400可采用本领域已知的能用于煤气余热回收的装置,例如废热锅炉。
[0061]
在一些实施例中,煤气化系统包括除尘装置300和余热回收装置400,除尘装置300包括文丘里洗涤器。煤气化系统还包括气液分离装置500和废液处理装置600。气液分离装置500与余热回收装置400的气体出口连接,用于对来自余热回收装置400的煤气进行气液分离。废液处理装置600的进口分别与余热回收装置400和气液分离装置500的液体出口连接,废液处理装置600的液体出口与文丘里洗涤器的洗涤液进口连接。废液处理装置600用于对来自余热回收装置400和气液分离装置500的废液进行净化处理,并将净化后的液体送至文丘里洗涤器循环利用。气液分离装置500和废液处理装置600均可以采用本领域已知的装置。例如气液分离装置500可选自采用重力沉降、折流分离、离心力分离、丝网分离、超滤分离、或填料分离等分离结构的气液分离器。废液处理装置600例如可采用固液分离设备,如沉淀槽。
[0062]
尽管图中未示出,本发明的煤气化系统还可选地包括加煤单元、排渣单元、夹套水循环单元(炉体可设置冷却水夹套)等。加煤单元、排渣单元、夹套水循环单元分别可包括本领域已知的相关装置。作为示例,加煤单元可包括煤锁,其连接于进煤口。作为示例,排渣单元可包括连接于排渣口的激冷室与渣锁等。
[0063]
本发明的煤气化方法及系统生产的煤气可作为化工原料气、工业煤气、燃料气等用途。例如,煤气可用作合成氨的原料气。由于煤气中的ch4含量降低,因此有利于降低合成氨系统的驰放气量和能耗。在一些实施例中,煤气化炉送出的煤气经除尘、余热回收和气液分离后,温度可降至180℃~190℃,可直接送至后续工段。
[0064]
接下来本发明提供一种煤气化合成氨系统。图3是作为一个示例的煤气化合成氨
系统的流程图。参照图3,本发明实施例提供的一种煤气化合成氨系统包括造气单元1、变换单元2、脱碳单元3、双甲精制单元4和合成氨单元5。
[0065]
造气单元1包括本发明所述煤气化系统。造气单元1对原料煤进行气化,产出煤气。煤气化系统的煤气可直接送入变换单元2进行变换处理。
[0066]
变换单元2与造气单元1的煤气出口连接,用于接收来自造气单元1的合成气,并对合成气进行变换处理,以使co变换为co2,送出变换气体。由于煤气出口送出的煤气温度较高,经洗涤除尘后的煤气中的水蒸气含量升高(例如40%~45%),大大减少了变换工艺补入的水蒸气量,从而有利于进一步降低整个合成氨系统的能耗。
[0067]
脱碳单元3用于对来自变换单元2的变换气体进行脱碳处理,获得脱碳气体。通过脱碳处理使得脱碳气体中的co2含量明显降低。
[0068]
双甲精制单元4用于对来自脱碳单元3的脱碳气体进行双甲精制,获得原料气。双甲精制是用甲醇化、甲烷化精制精炼脱碳气体中的co、co2,并副产甲基化合物。通过双甲精制处理,使得原料气中的碳氧化物的含量达到合成氨的严格要求。
[0069]
合成氨单元5用于接收来自双甲精制单元4的原料气,并用原料气合成氨。
[0070]
参照图4,在一些实施例中,若来自造气单元1的合成气的硫含量大于0.05ppm,系统还可包括变脱单元6和脱硫单元7。变脱单元6和脱硫单元7依次设置于变换单元2和脱碳单元3之间,用于对合成气进行脱硫。
[0071]
变换单元2、脱碳单元3、双甲精制单元4、合成氨单元5、变脱单元6和脱硫单元7均可采用本领域公知的工艺和装置。
[0072]
在本文中,煤气中的组分含量指的是体积百分含量。
[0073]
实施例
[0074]
实施例1
[0075]
煤气化炉为液态排渣固定床气化炉。在炉体的下部区域沿炉体的周向均匀分布有6个第一气化剂引入口。第一气化剂引入口的设置高度g等于0.12倍的炉体高度h。在第一气化剂引入口设置第一气化剂喷嘴。在炉体的中部区域沿炉体的周向均匀分布有4个第二气化剂引入口。第二气化剂引入口的设置高度h等于0.45倍的炉体高度h。在第二气化剂引入口设置第二气化剂喷嘴。
[0076]
原料煤采用无烟块煤,其灰熔点为1450℃。
[0077]
第一气化剂为氧气和过热水蒸气的混合气体,蒸氧比为0.96kg/nm3。
[0078]
第二气化剂为氧气和过热水蒸气的混合气体,蒸氧比为3.0kg/nm3。
[0079]
原料煤经煤锁从煤气化炉的顶部进煤口加入气化腔室,第一气化剂由第一气化剂喷嘴加入气化腔室,第二气化剂由第二气化剂喷嘴加入气化腔室,并且满足由第一气化剂引入气化腔室的氧气与由第二气化剂引入气化腔室的氧气的体积流量之比为6:4。在2.5mpa气化压力下,原料煤气化生成煤气,由煤气出口送出。炉内温度曲线如图5所示,图中横坐标表示高度(以底部法兰底面为基准),纵坐标表示炉内温度(℃),由左至右的纵虚线依次表示第一气化剂引入口的设置位置、第二气化剂引入口的设置位置、煤气出口的设置位置。煤气出口的煤气的温度约为900℃。煤气组成见表1。
[0080]
表1
[0081]
成分h2coco2ch4焦油
含量37.2%51.91%9.2%1.4%0.29%
[0082]
实施例2
[0083]
与实施例1不同的是,第一气化剂引入口的设置高度g等于0.15倍的炉体高度h;第二气化剂引入口的设置高度h等于0.5倍的炉体高度h;原料煤采用烟煤块煤,其灰熔点为1380℃;第二气化剂的蒸氧比为4.0kg/nm3;气化压力为4.0mpa。炉内温度曲线如图6所示,图中横坐标表示高度(以底部法兰底面为基准),纵坐标表示炉内温度(℃),由左至右的纵虚线依次表示第一气化剂引入口的设置位置、第二气化剂引入口的设置位置、煤气出口的设置位置。煤气出口的煤气的温度约为900℃。煤气组成见表2。
[0084]
表2
[0085]
成分h2coco2ch4焦油含量34.31%48.39%14.9%1.49%0.91%
[0086]
由以上结果可知,采用本发明的煤气化方法及系统,能获得高品质的煤气产品。煤气中的焦油和ch4的含量较低,有效气含量较高。此外,由于煤气的焦油含量降低,还能有效缓解废水处理难题。
[0087]
以上所述,仅为本发明的具体实施方式,但本发明的保护范围并不局限于此,任何熟悉本技术领域的技术人员在本发明揭露的技术范围内,可轻易想到各种等效的修改或替换,这些修改或替换都应涵盖在本发明的保护范围之内。因此,本发明的保护范围应以权利要求的保护范围为准。