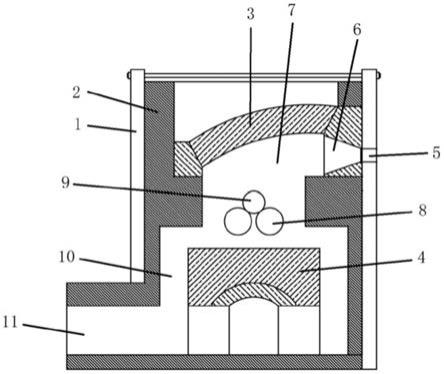
1.本实用新型涉及钢管加工设备技术领域,具体涉及一种柴油喷射炉。
背景技术:
2.双金属机筒的成型过程是采用离心铸造工艺把加热后熔化的合金材料复合在机筒内表面,得到具有合金保护层的机筒工作面。双金属机筒成型工艺过程中需要采用加热设备来加热双金属机筒内部的特种合金材料,通常这些合金材料为铁基硼铸铁,其熔化温度高达1100℃。现有的加热设备通常采用电阻炉来加热双金属机筒以熔化机筒内表面上的合金材料,电阻炉在使用时存在以下缺陷:其加热速度慢、加热时间长,这就为合金材料在相变过程中其内部正在形成或已经形成的各种碳化物硬质相粒子的烧损创造了条件,以致双金属机筒内表面上形成的合金层无法达到所需硬度,降低了合金层的耐磨损性能及耐腐蚀性能。
3.本技术中的柴油喷射炉利用柴油热效率高的优势,具有加热速度快,工件在炉内停留时间短的特点,可有效避免双金属机筒内表面合金层中硬质相碳化物的烧损,减少双金属机筒母材中碳钢熔融原子的转移,可以在最大程度上保障双金属机筒内侧形成的合金层具有较高的硬度及耐磨损性能。
技术实现要素:
4.为了解决上述背景技术中存在的问题,本实用新型提供一种柴油喷射炉,其以最少的燃油消耗得到最大的热值效应,将由进油口喷射出的雾化柴油燃烧,完全充分地转变为热能,并将这些热能以最大的效率来加热机筒,加速机筒内表面上合金材料的熔化,具有加热均匀,加热速度快,工件在炉内停留时间短的特点。
5.为了实现上述目的,本实用新型采用以下技术方案:
6.本实用新型提供一种柴油喷射炉,包括炉体,所述炉体前后两侧分别设有供待加热机筒进出的进料口和出料口,所述炉体顶部安装有倾斜设置的弧形拱顶,所述炉体内下部安装有烟道结构件,所述烟道结构件上方形成燃烧室,所述炉体侧面上开设有多个进油口,所述燃烧室内部形成有分别与所述进油口相连通的锥形喷射通道,所述弧形拱顶下端面的水平高度高于所述锥形喷射通道下端面的水平高度,且低于所述锥形喷射通道上端面的水平高度,所述燃烧室内安装有至少两个旋转辊,所述旋转辊沿所述进料口至所述出料口方向设置,所述旋转辊端部与旋转驱动机构相连接,且所述旋转辊位于所述锥形喷射通道下方;
7.所述烟道结构件外侧面与所述炉体内侧面之间形成排烟通道,所述炉体侧面下部开设有与所述排烟通道相连通的排烟口。
8.进一步地改进在于,多个所述进油口沿所述炉体长度方向等间距设置。
9.进一步地改进在于,所述排烟口通过管路与排烟系统相连通,所述排烟系统中设有过滤装置和换热装置。
10.通过设置,对烟气进行处理后再进行排放,一方面避免对外界环境造成污染,另一方面还可对烟气中热量进行回收再利用。
11.进一步地改进在于,所述炉体内侧壁上安装有耐火砖。
12.通过设置耐火砖,避免炉体内部热量散失,同时也避免内部气流对炉体内侧壁的冲刷磨损,有利于柴油喷射炉的安全、连续、长寿运行。
13.进一步地改进在于,所述进料口和出料口处分别可开合安装有炉门,具体地,炉门通过提升装置安装在进料口和出料口处。
14.通过设置,既不影响筒体进出柴油喷射炉,同时在炉体内部进行加热时,将进料口和出料口进行关闭,确保炉体内达到一定温度。
15.进一步地改进在于,所述进料口和所述出料口处分别安装有支架,所述旋转辊端部分别通过轴承转动安装在所述支架上。
16.与现有技术相比,本实用新型具有如下有益效果:
17.本实用新型中将雾化柴油和高温助燃气体同时由进油口加入,经锥形喷射通道将其引流至燃烧室,在燃烧室内倾斜设置的弧形拱顶的作用下,雾化柴油与其发生碰撞形成细小雾滴,并充满整个燃烧室空间,同时燃油与高温助燃气体充分接触混合,快速充分的燃烧,加热均匀,加热速度快,通过在炉体内形成排烟通道,使得燃烧室内燃油可持续充分的进行燃烧;
18.在旋转辊和旋转驱动机构配合作用下,可带动位于其顶部的待加热机筒转动,保证了机筒在加热过程中受热均匀,提高产品质量;
19.该柴油喷射炉以最少的燃油消耗得到最大的热值效应,将由进油口喷射出的雾化柴油燃烧,完全充分地转变为热能,并将这些热能以最大的效率来加热机筒,加速机筒内表面上合金材料的熔化,具有加热均匀,加热速度快,工件在炉内停留时间短的特点。
附图说明
20.下面结合附图与具体实施例对本实用新型作进一步详细说明。
21.图1为本实用新型中柴油喷射炉的外部结构示意图;
22.图2为图1中沿a-a面的剖视图;
23.其中,具体附图标记为:炉体1,耐火砖2,弧形拱顶3,烟道结构件4,进油口5,锥形喷射通道6,燃烧室7,旋转辊8,机筒9,排烟通道10,排烟口11。
具体实施方式
24.本实用新型的实施例公开了一种柴油喷射炉,如图1和图2所示,包括炉体1,炉体1前后两侧分别设有供待加热机筒9进出的进料口和出料口,炉体1顶部安装有倾斜设置的弧形拱顶3,炉体1内下部安装有烟道结构件4,弧形拱顶3和烟道结构件4均由耐火材料制成,烟道结构件4上方形成燃烧室7,炉体1侧面上开设有多个进油口5,燃烧室7内部形成有分别与进油口5相连通的锥形喷射通道6,弧形拱顶3下端面的水平高度高于锥形喷射通道6下端面的水平高度,且低于锥形喷射通道6上端面的水平高度,燃烧室7内安装有至少两个旋转辊8,待加热机筒9放置于相邻的两个旋转辊8顶部,本实施例中燃烧室7并排安装有两个旋转辊8,旋转辊8沿进料口至出料口方向设置,旋转辊8端部与旋转驱动机构相连接,且旋转
辊8位于锥形喷射通道6下方,旋转驱动机构可采用现有技术中具有旋转驱动功能的组件,具体的可选用齿轮、链条和电机配合使用的结构;
25.烟道结构件4外侧面与炉体1内侧面之间形成排烟通道10,炉体1侧面下部开设有与排烟通道10相连通的排烟口11。
26.工作时,将雾化柴油和高温助燃气体同时由进油口5加入,经锥形喷射通道6将其引流至燃烧室7,在燃烧室7内倾斜设置的弧形拱顶3的作用下,雾化柴油与其发生碰撞形成细小雾滴,并充满整个燃烧室7空间,同时燃油与高温助燃气体充分接触混合,快速充分的燃烧,加热均匀,加热速度快,通过在炉体1内形成排烟通道10,使得燃烧室7内燃油可持续充分的进行燃烧;在旋转辊8和旋转驱动机构配合作用下,可带动位于其顶部的待加热机筒9转动,保证了机筒9在加热过程中受热均匀,提高产品质量。
27.其中,多个进油口5沿炉体1侧面的长度方向等间距设置。
28.其中,排烟口11通过管路与排烟系统相连通,排烟系统中设有过滤装置和换热装置。通过设置,对烟气进行处理后再进行排放,一方面避免对外界环境造成污染,另一方面还可对烟气中热量进行回收再利用。
29.其中,炉体1内侧壁上安装有耐火砖2。通过设置耐火砖2,避免炉体1内部热量散失,同时也避免内部气流对炉体1内侧壁的冲刷磨损,有利于柴油喷射炉的安全、连续、长寿运行。
30.其中,进料口和出料口处分别可开合安装有炉门,具体地,炉门通过提升装置安装在进料口和出料口处。通过设置,既不影响筒体进出柴油喷射炉,同时在炉体1内部进行加热时,将进料口和出料口进行关闭,确保炉体1内达到一定温度。
31.其中,进料口和出料口处分别安装有支架,旋转辊8端部分别通过轴承转动安装在支架上。
32.该柴油喷射炉以最少的燃油消耗得到最大的热值效应,将由进油口5喷射出的雾化柴油燃烧,完全充分地转变为热能,并将这些热能以最大的效率来加热机筒9,加速机筒9内表面上合金材料的熔化,具有加热均匀,加热速度快,工件在炉内停留时间短的特点。
33.以上应用了具体个例对本实用新型进行阐述,只是用于帮助理解本实用新型,并不用以限制本实用新型。对于本实用新型所属技术领域的技术人员,依据本实用新型的思想,还可以做出若干简单推演、变形或替换。