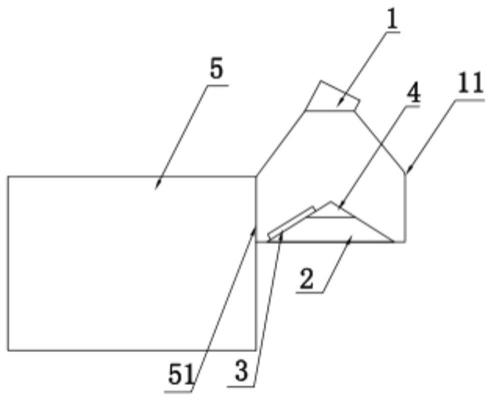
1.本实用新型涉及锅炉给料设备领域,尤其涉及一种锅炉抛料机。
背景技术:
2.我国有大量中小型自备电厂使用热电联产锅炉,这些锅炉炉型大多为层燃炉,层燃炉在给煤过程中因给煤不均匀,导致炉膛燃烧不均匀,炉排上燃烧层穿孔跑风,导致锅炉达不到应有的出力和燃烧效率,造成原料浪费和环境污染。我国还有大量的小型木片燃烧炉在广泛使用,这些锅炉因为出力不大,使用燃料相对便宜而得不到重视,长期处于不受控制的粗放燃烧状态,主要表现在人工进料随意,多进料时堆积起来燃烧,少进料时燃料不足,形成不了正常的燃烧状态。原料不按设计要求进行处理,大片小料、木块树枝混合进料,炉膛内也不可能形成稳定的燃烧工况。同时工人劳动强度大,现场坏境卫生差,不符合现代工业生产的基本要求。还有一些相对大点的木片燃烧锅炉尽管布置了相对完善的木片给料系统,但因为木片抛料机抛料不均匀也同样达不到设计的燃烧效果。
3.现有锅炉的给料系统抛煤机或给料机大都采用直线向前抛料,使用中存在很多问题,主要缺陷首先是抛料不均匀,炉排在直线方向就不能均匀接受原料。其次是覆盖面不宽,炉排横向原料接受也不均匀。第三是没有有效的调节手段,在使用过程中,由于抛料不均匀导致锅炉出力不够时,唯一的办法就是增加给料量,但在这种情况下增加给料量带来的却是更大的浪费和环境污染。第四,长期没有技术改进。对这些锅炉进行给料系统改造,有利于提高劳动生产率,节能降耗减少污染,经济效益和社会效益明显。
技术实现要素:
4.本实用新型所要解决的是现有层燃炉的燃料给料系统抛料不均匀,造成导致锅炉出力不够,燃烧效率低的技术问题。
5.为了解决上述问题,本实用新型提供的技术方案是:一种锅炉抛料机,包括凸锥盘、抛料片底座和抛料片,还包括安装在凸锥盘外围的外罩,外罩侧面开有出料口,出料口与锅炉进料口连接,外罩的顶部开有落料口,落料口与传送带连接,凸锥盘呈中空的顶部开口的凸锥形,电机安装在凸锥盘内,电机转轴伸出到凸锥盘顶部外与轴承连接,轴承安装在抛料片底座内部,抛料片底座也呈凸锥形,抛料片底座与所述凸锥盘外表面的上半部分匹配、贴合安装在凸锥盘表面的上半部位置上,通过电机驱动使得抛料片底座可在凸锥盘上转动,抛料片安装在抛料片底座上,抛料片垂直于抛料片底座。
6.本实用新型的进一步技术方案是:所述抛料片包括抛料片底板和拨料片,抛料片底板贴合固定在抛料片底座上,拨料片垂直于抛料片底板。
7.本实用新型的进一步技术方案是:所述拨料片的上半部分安装到抛料片的下半部分上。
8.本实用新型的进一步技术方案是:抛料片底板设置有安装孔,抛料片底座上设置有2圈或3圈沉头螺孔,抛料片底板上的安装孔与沉头螺孔的大小一致,抛料片底板用沉头
螺丝固定在抛料片底座上。
9.本实用新型的进一步技术方案是:抛料片底座上开有多个横向卡槽,拨料片与抛料片底板部分连接,拨料片与抛料片底板连接的一端大,不与抛料片底板连接的一端小,拨料片与抛料片底板连接后在连接线下方形成开口缝隙,开口缝隙一端的抛料片底板插入卡槽内。
10.本实用新型的进一步技术方案是:抛料片底板为曲面,抛料片底板曲面弧度与凸锥盘锥形面弧度一致。
11.本实用新型的进一步技术方案是:凸锥盘凸锥顶部角度设置为120
°
~150
°
。
12.本实用新型的进一步技术方案是:所述凸锥盘的直径设置在1.2m~1.5m。
13.本实用新型的进一步技术方案是:抛料片底板和拨料片采用一体成型制成。
14.本实用新型的进一步技术方案是:抛料片底板和拨料片分别成型后通过焊接或者铆接方式连接在一起。
15.本实用新型的有益效果是:由于采用上述技术方案,抛料机的抛料片可方便调节,该抛料机的抛物线抛料方式可使整个炉膛内各个方向上的抛料量均匀,抛料的覆盖范围和厚度可通过抛料机的转速和进料量进行调节,让锅炉内燃料更充分的燃烧,有效提高锅炉燃烧效率,有利于提高劳动生产率,节能降耗减少环境污染。
附图说明
16.图1是本实用新型所述锅炉抛料机的整体结构示意图
17.图2是本实用新型所述锅炉抛料机的结构示意图;
18.图3是本实用新型实施例一所述抛料片的结构示意图;
19.图4是本实用新型实施例一所述凸锥盘的俯视示意图;
20.图5是本实用新型实施例二所述抛料片的结构示意图;
21.图6是本实用新型实施例二所述抛料片安装在凸锥盘上的示意图;
22.图7是本实用新型实施例二所述抛料片底座的结构示意图;
23.图中:
24.1-落料口,11-外罩,2-凸锥盘,3-抛料片,31-拨料片,32-抛料片底板,33-安装孔,4-抛料片底座,41-卡槽,5-锅炉,51-锅炉进料口。
具体实施方式
25.下面结合附图和具体实施方式对本实用新型做进一步的说明。
26.实施例一:
27.如图1至4所示的一种锅炉抛料机,包括凸锥盘2、抛料片底座4和抛料片3,还包括安装在凸锥盘外围的外罩11,外罩侧面开有出料口,出料口与锅炉进料口51连接,外罩的顶部开有落料口,落料口1与传送带连接,凸锥盘呈中空的顶部开口的凸锥形,电机安装在凸锥盘内,电机转轴伸出到凸锥盘顶部外与轴承连接,轴承安装在抛料片底座内部,抛料片底座也呈凸锥形,抛料片底座4与所述凸锥盘外表面的上半部分匹配、贴合安装在凸锥盘表面的上半部位置上,通过电机驱动使得抛料片底座可在凸锥盘上转动,抛料片安装在抛料片底座上,抛料片垂直于抛料片底座。经过处理好的原料从送料皮带落料口进入凸锥盘,形成
越靠近凸锥盘边缘越厚越靠近凸锥顶部越薄的原料层,抛料片高速旋转将原料抛送进炉膛,抛送过程由于转速固定,原料进入炉膛后呈抛物线下落,均匀分布在锅炉燃烧层面上,抛料片底座在使用现场可做辅助微调。
28.优选的,所述抛料片包括抛料片底板32和拨料片31,抛料片底板贴合固定在抛料片底座上,拨料片垂直于抛料片底板。
29.优选的,所述拨料片的上半部分安装到抛料片的下半部分上。
30.优选的,抛料片底板设置有安装孔33,抛料片底座上设置有2圈或3圈沉头螺孔,抛料片底板上的安装孔与沉头螺孔的大小一致,抛料片底板用沉头螺丝固定在抛料片底座上。可方便的对抛料片的安装位置进行调节以适应锅炉5的抛料需求。抛料片可根据使用情况在现场增减调整。当使用单个抛料片时,单个抛料料片做圆周运动,确保了料片在炉膛呈扇形状分布,当使用多个抛料片时,多个抛料片配合调整就可以保证纵横和远近方向上的均匀。
31.优选的,抛料片底板为曲面,抛料片底板曲面弧度与凸锥盘锥形面弧度一致。当抛料片辐射状布置时将抛料片底板为曲面,更利于原料的抛送;在实际生产过程,如果调整需要非辐射状布置时可将抛料片底板设置为平面。
32.优选的,凸锥盘凸锥顶部角度设置为120
°
~150
°
。对于小型的锅炉凸锥盘2凸锥顶部角度可设置为120
°
,对于中型的锅炉凸锥盘2凸锥顶部角度可设置为135
°
,对于较大的锅炉,凸锥盘2凸锥顶部角度可设置为150
°
,凸锥角度小,则凸锥盘四周的料层厚度大,抛料片靠外圆的线速度大,炉膛内远处就可以正常接收到原料,反之亦然。
33.优选的,在制作标准产品时,凸锥盘2的直径设置在1.2m~1.5m,例如,在针对较小的锅炉制作标准品时,凸锥盘2的直径可设置为1.2m,在针对中型的锅炉制作标准品时,凸锥盘2的直径可设置为1.3m,在针对大型的锅炉制作标准品时,凸锥盘2的直径可设置为1.5m;此外,在实际应用中,很多锅炉需要按锅炉具体尺寸制作非标产品,凸锥盘2的直径,可根据实际情况进行设置。
34.优选的,抛料片底板和拨料片采用一体成型制成。
35.优选的,抛料片底板和拨料片分别成型后通过焊接或者铆接方式连接在一起。
36.本实用新型针对现有抛煤机和木片给料机的缺陷设计,可以在35吨/小时以下中低压层燃燃煤锅炉和绝大部分木片燃烧炉上使用,木片燃烧炉木片规格最好在10cm以内,原煤颗粒最好在5cm以内。目前使用的小型木片锅炉热效率普片在50%-60%,有些甚至更低。采用本技术方案进行给料系统改造后锅炉热效率可达到70%,可提高锅炉热效率15%以上,大量节省原料,并节省两名以上现场运行员工。燃煤炉和大型木片燃烧炉改造后亦可提高热效率10%左右。
37.实施例二:
38.本实施例技术方案与实施例一基本相同,所不同之处在于:如图5至7所示,抛料片底座4上开有多个横向卡槽41,拨料片与抛料片底板部分连接,拨料片与抛料片底板连接的一端大,不与抛料片底板连接的一端小,拨料片与抛料片底板连接后在连接线下方形成开口缝隙,开口缝隙一端的抛料片底板插入卡槽内,该方式对于抛料片的安装和拆卸十分方便,便于调节以及后期维护。
39.以上所述仅为本实用新型的较佳实施例而已,并不用以限制本实用新型,凡在本
实用新型的精神和原则之内所作的任何修改、等同替换和改进等,均应包含在本实用新型的保护范围之内。