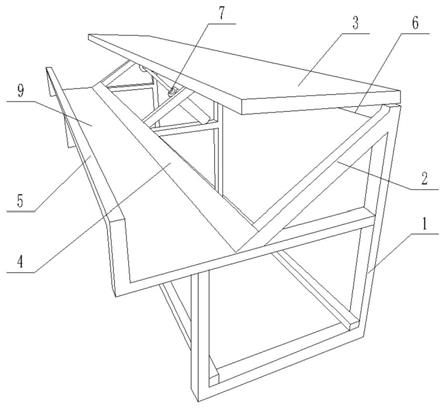
1.本实用新型涉及绿色节能建材技术领域,特别涉及一种木方自动翻料装置。
背景技术:
2.在木方加工中,加工完成的成品木方由出料口排出,目前是通过人工逐根接出转移,耗费人工,有时人工操作出现误差,会造成积料、落料损坏。
技术实现要素:
3.为了解决上述技术问题,本实用新型公开了一种木方自动翻料装置。
4.具体技术方案如下:
5.一种木方自动翻料装置,安装在木方加工出料口之后,包括底部框架,框架中部设置水平储料台,框架顶部横梁通过折页与托板铰接,框架和托板分别与气缸的固定端和伸缩端铰接;所述托板安装重量传感器,气缸的伸缩由计算机控制,重量传感器向计算机反馈信号;所述托板在气缸带动下的下行极限位置与导料板起始端衔接。
6.所述储料台的外沿竖直向上设置护板。
7.所述框架的竖直部分与储料台之间通过斜梁加固。
8.所述斜梁上安装内凹弧形的导料板,用来舒缓衔接木方下落至储料台的路径。
9.与现有技术相比,本实用新型具有如下有益技术效果:
10.本实用新型可实现自动化接料由托板的重量感应器检测,达到一定数量时,由气缸带动托板下翻,完成一次翻料。翻下的木方成品经由导料板滑至储料台储存,托板归位准备下一次翻料,全程可连续自动化作业,可完全脱离人工监管,节约人工。
附图说明
11.图1为本实用新型翻料装置立体结构示意图;
12.图2为本实用新型翻料装置平面结构示意图;
13.图3为本实用新型翻料装置工作示意图;
14.图中,1、框架;2、斜梁;3、托板;4、导料板;5、护板;6、横梁;7、气缸;8、折页;9、储料台;10、木方。
具体实施方式
15.下面结合附图对本实用新型进行进一步说明,但本实用新型的保护范围不仅限于附图。
16.图1为本实用新型翻料装置立体结构示意图,图2为本实用新型翻料装置平面结构示意图,如图所示:
17.本实用新型木方自动翻料装置,安装在木方加工出料口之后,包括底部框架1,框架1中部设置水平储料台9,框架1顶部横梁6通过折页8与托板3铰接,框架1和托板3分别与
气缸7的固定端和伸缩端铰接;所述托板3安装重量传感器,气缸的伸缩由计算机控制,重量传感器向计算机反馈信号;所述托板3在气缸7带动下的下行极限位置与导料板4起始端衔接。
18.所述储料台9的外沿竖直向上设置护板5。所述框架1的竖直部分与储料台9之间通过斜梁2加固。所述斜梁2上安装内凹弧形的导料板4,用来舒缓衔接木方10下落至储料台9的路径。
19.图3为本实用新型翻料装置工作示意图,如图所示,工作时,自动翻料装置安装与木方加工出料口之后,初始的状态托板3处于水平,且低于出料口,用来承接出料口排出的成品木方。加工完成的成品木方推至托板3上摆放,待积累到一定重量,触发重量传感器,重量传感器向计算机反馈信号,计算机控制气缸的伸缩端缩回,从而向下拉动托板,托板3上的木方失去平衡下落,通过导料板4滑至储料台9储存,此时重量传感器再次触发,向计算机反馈信号,计算机控制气缸的伸缩端伸出,从而推动托板3恢复至初始的水平位置,归位准备下一次翻料。
技术特征:
1.一种木方自动翻料装置,其特征在于:安装在木方加工出料口之后,包括底部框架(1),框架(1)中部设置水平储料台(9),框架(1)顶部横梁(6)通过折页(8)与托板(3)铰接,框架(1)和托板(3)分别与气缸(7)的固定端和伸缩端铰接;所述托板(3)安装重量传感器,气缸(7)的伸缩由计算机控制,重量传感器向计算机反馈信号;所述托板(3)在气缸(7)带动下的下行极限位置与导料板(4)起始端衔接。2.根据权利要求1所述的木方自动翻料装置,其特征在于:所述储料台(9)的外沿竖直向上设置护板(5)。3.根据权利要求1所述的木方自动翻料装置,其特征在于:所述框架(1)的竖直部分与储料台(9)之间通过斜梁(2)加固。4.根据权利要求3所述的木方自动翻料装置,其特征在于:所述斜梁(2)上安装内凹弧形的导料板(4),用来舒缓衔接木方下落至储料台(9)的路径。
技术总结
本实用新型涉及绿色节能建材技术领域,特别涉及一种木方自动翻料装置。框架中部设置水平储料台,框架顶部横梁通过折页与托板铰接,框架和托板分别与气缸的固定端和伸缩端铰接;托板安装重量传感器,气缸的伸缩由计算机控制,重量传感器向计算机反馈信号;托板在气缸带动下的下行极限位置与导料板起始端衔接。本实用新型可实现自动化接料由托板的重量感应器检测,达到一定数量时,由气缸带动托板下翻,完成一次翻料。翻下的木方成品经由导料板滑至储料台储存,托板归位准备下一次翻料,全程可连续自动化作业,可完全脱离人工监管,节约人工。工。工。
技术研发人员:李广达 沈恩辉 朱振春
受保护的技术使用者:辽宁中建绿建环保科技有限公司
技术研发日:2021.09.02
技术公布日:2022/2/18