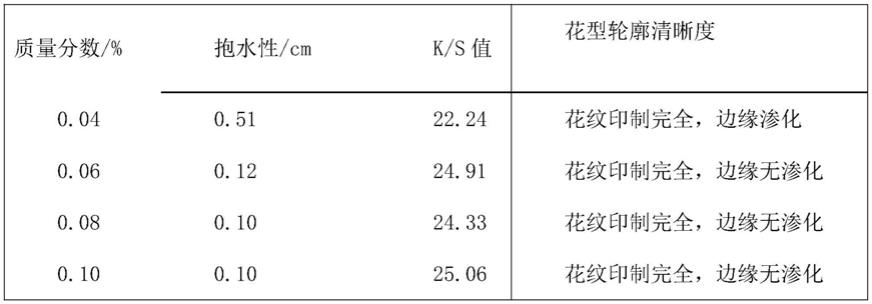
1.本发明涉及技轻化工术领域,具体为一种分散染料免蒸洗印花的方法。
背景技术:
2.涤纶由于具有优良的耐热性、化学稳定性和尺寸稳定性,发展异常迅速,加之分散染料印花后整理技术发展突飞猛进,使得分散染料印花比例上升到整个印花产品的85%。传统涤纶分散染料印花由于染料在织物上固色不完全,在印花过程中需要通过蒸化来发色。在蒸化过程中,织物表面的色浆吸水膨化,染料溶解并向纤维内部扩散、渗透。同时,纤维的大分子结构在这种湿热条件下,内部空隙增大,接纳染料的渗入并与之发生各种化学键结合,从而将染料固定在纤维上。传统分散染料印花工艺生产的产品,染料的固色率较低,一般为50-70%左右,织物上有大量未固着的染料。因此,在蒸化发色后,还需要通过还原清洗、水洗工序将没有进入纤维里的分散染料、糊料和其他助剂洗去。在水洗过程中会造成大量污水排出,污水中有机污染物含量大、色度深,对生态环境破坏严重,是较难处理的工业废水之一。
3.因此,如何解决现有分散染料平网和圆网印花技术中普遍使用蒸、洗工序带来的能耗高、污染大、工艺流程长的问题,从清洁生产角度考虑,简化印花工艺,真正从源头上堵住色水、污水排放,实现节能减排,是众多印染企业亟待攻克的技术难题。
4.目前急切需要寻找一种能实现分散染料免蒸洗印花的方法。
5.为了解决上述问题,本案由此而生。
技术实现要素:
6.(一)解决的技术问题
7.针对现有技术的不足,本发明提供了一种分散染料免蒸洗印花的方法,解决了常规分散染料工艺中普遍使用蒸、洗工序带来的高能耗、高污染问题。
8.(二)技术方案
9.为实现以上目的,本发明通过以下技术方案予以实现:一种分散染料免蒸洗印花的方法,包括在自制印花糊料的基础上,进行涤纶织物免蒸洗印花,印花方法包括如下步骤:
10.(1)免蒸洗印花糊料的制备:将超高分子量丙烯酸增稠剂、防渗化剂、手感调节剂按一定比例复配。
11.(2)免蒸洗印花工艺流程:印花坯布
→
网印
→
烘干
→
定形
→
成品。
12.优选的,步骤一配方中加入量为:0.06%超高分子量丙烯酸酯增稠剂用量、3%防渗化剂fs-30、2%手感调节剂pe乳液。
13.优选的,步骤一中免蒸洗印花分散染料为:分散黑s-2bl。
14.优选的,步骤二中烘干时间为10min,温度为70℃,定形时间为3min,温度为190℃。
15.方案中超高分子量是指:与普通丙烯酸增稠剂相比,采用较低的浓度就能使其水
溶液增加到一定印花粘度要求。
16.本发明的原理:
17.免蒸洗印花糊料需要与分散染料具有较好的相容性,含固量低而增稠效率高,需要解决色浆渗化的技术难题。现有的印花糊料难以满足免蒸洗印花技术的要求。本发明采用自制印花糊料,在分散染料印花中主要起以下作用:(1)使印花色浆具有一定的黏度,部分地抵消面料的毛细管效应而引起的渗化,从而保证花纹的轮廓清晰度。(2)作为染料的传递剂,起到载体的作用。印花时分散染料借助原糊传递到面料上,要与染料具有很好的相容性。(3)具备含固率低、浆膜薄、手感柔软的特点。
18.分散染料会产生不同程度的热迁移现象,升华牢度差会造成高温定形时染料挥发,影响印花产品的色牢度。本发明从固色率和升华牢度方面对分散染料进行合理筛选,解决分散染料在织物上的固色完全性。
19.(三)有益效果
20.采用上述技术方案后,本发明与现有技术相比,具备以下优点:
21.1、本发明一种分散染料免蒸洗印花的方法,自制的免蒸洗糊料具有用量低、浆膜薄、与分散染料相容性好、防渗化性好、发色容易,花型轮廓清晰优点。
22.2、本发明一种分散染料免蒸洗印花的方法,将自制糊料和筛选的分散染料用于涤纶织物印花,承印物得色量高、手感柔软、色牢度优良,印花后只需在织物定形时即可同步发色,省去了传统分散染料印花工艺中蒸化和水洗工序,缩短了工艺流程,节能减排效果显著。
附图说明
23.图1为实施例二中质量分数对黏度的影响。
具体实施方式
24.下面通过附图和实施例对本发明作进一步详细阐述。
25.实施例1自制免蒸洗印花糊料复配体系优化
26.(1)超高分子量丙烯酸增稠剂用量对抱水性和k/s值的影响
27.将3%分散黑s-2bl,3%防渗化剂fs-30、2%手感调节剂pe乳液与不同用量的超高分子量丙烯酸增稠剂进行复配,按免蒸洗印花工艺流程进行印花,测试不同复配体系下色浆的抱水性能和印花制品的表观得色量,结果见表1。
28.表1自制糊料用量对抱水性和k/s值的影响
29.30.从表1可以看出,超高分子量丙烯酸增稠剂用量为0.06%,即可满足免蒸洗印花的要求,抱水性为0.21cm;k/s值为24.91,花型轮廓清晰,不会发生渗化。
31.(2)防渗化剂用量对抱水性和k/s值的影响
32.将3%分散黑s-2bl,0.06%超高分子量丙烯酸增稠剂、2%手感调节剂pe乳液与防渗化剂进行复配,研究不同复配体系下浆料的抱水性能和印花制品的表观得色量,实验结果见表2。
33.表2防渗化剂用量对抱水性和k/s值的影响
[0034][0035]
由表2可知,随着防渗化剂用量的增加,抱水性变好,通常抱水性在0.2cm,就能够满足印花需求。防渗化剂质量分数3%即可满足印花要求。
[0036]
自制免蒸洗印花糊料配方为:0.06%超高分子量丙烯酸增稠剂、3%防渗化剂fs-30、2%手感调节剂pe乳液。
[0037]
实施例2超高分子量丙烯酸增稠剂质量分数对黏度的影响
[0038]
将自制糊料配制成质量分数为0.04%、0.06%、0.08%、0.1%、0.12%的浆料,测定黏度,结果见图1。
[0039]
根据图1可知,随质量分数增加浆料黏度不断增大。当质量分数为0.06%时,原糊的黏度就能达到3676mpa
·
s。印花糊料的黏度应保证能防止因织物的毛细管效应而使染料产生的渗化,同时使色浆在印花时均匀刮浆,保证印花均匀。除此之外,当增稠剂用量过多时会导致印花产品的手感发硬。自制糊料在较低的用量下(质量分数为0.06%)就能满足分散染料印花要求,超低的糊料用量优点是形成的浆膜薄,不影响手感,印花后可以不经水洗就能满足手感要求。
[0040]
实施例3不同种类糊料对比
[0041]
将自制免蒸洗印花糊料(配方:0.06%超高分子量丙烯酸增稠剂、3%防渗化剂fs-30、2%手感调节剂pe乳液)与不同种类印花糊料进行对比,结果见表3。
[0042]
表3糊料种类对抱水性和k/s值的影响
[0043][0044][0045]
由表3可知,自制糊料在用量为0.06%时,抱水性0.14cm;k/s值为24.21,就可以满足免蒸洗印花要求。而其他糊料用量只有在3%及以上时,才能有较好的抱水性和印制性能。
[0046]
实施例4定形温度对印花产品性能的影响
[0047]
定形温度对印花产品k/s值的影响见表4。
[0048]
表4定形温度对印花产品k/s值的影响
[0049][0050]
由表4可知,在一定温度范围内,印花织物k/s值随定形温度的升高而增大。超过190℃,k/s值反而下降,这可能是由于温度过高引起染料升华所致。
[0051]
实施例5印制性能
[0052]
选用常规印花所使用的海藻酸钠糊料(用量5%)与自制糊料(用量0.06%)进行印花对比实验。海藻酸钠糊料采用常规印花工艺(印花坯布
→
网印
→
烘干(80℃,5min)
→
蒸化(180℃,8min)
→
还原清洗(烧碱2g/l,保险粉2g/l,80℃,10min)
→
定形
→
成品),自制糊料采用免蒸洗印花工艺,测试印花制品的k/s值和色牢度等印制性能,实验结果见表5。
[0053]
表5印制性能
[0054][0055]
由表5可以看出,自制糊料印花织物的k/s值高于海藻酸钠糊料,自制糊料印花织物未经水洗,其摩擦牢度和皂洗牢度均可达到4级以上;经过还原清洗后,各项色牢度均能达到5级,色牢度优异。
[0056]
以上所述依据实施例为启示,通过上述的说明内容,相关工作人员完全可以在不
偏离本项发明思想的范围内,进行多样的变更以及修改。本项使用新型的技术性范围并不局限于说明书上的内容,必须要根据权利要求范围来确定其保护的范围。