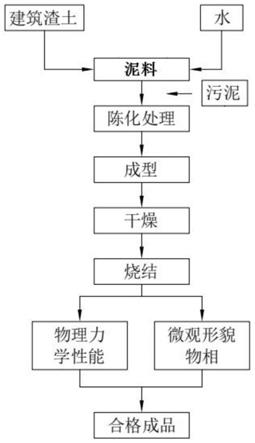
1.本发明属于建筑墙体材料技术领域,尤其涉及一种烧结砖及其制备方法和应用。
背景技术:
2.传统烧结砖的主要原料为粘土,粘土主要靠开挖的土壤得到,因此易对土壤及土壤表面的植被造成破坏,引起水土流失,破坏坏境。
3.近年来,由于城镇化进程的加快,建筑渣土的产生量急剧上升,已成为现代建筑垃圾中占比最多的固体废弃物,达建筑垃圾总量的50~60%。但大多数建筑渣土仅是采取填埋、堆积等简单的方式进行处理,不仅占用土地资源、污染环境,而且可能带来严重的安全隐患。
4.同时,随着城市污水排放量越来越大,污水处理产生的污泥量也逐年增加,污泥含水率高、体积大,给运输和填埋造成困难,并易于产生渗滤液,污染地下水和土壤环境。
5.中国专利cn107032756公开了一种使用建筑垃圾制备烧结砖的工艺,但是其得到的烧结砖的吸水率在9.5%以上,制成建筑墙体后易返潮,强度性能会变差。
技术实现要素:
6.有鉴于此,本发明提供了一种烧结砖及其制备方法和应用,本发明提供的烧结砖具有吸水率小且抗压强度高的特点。
7.为了实现上述发明目的,本发明提供以下技术方案:
8.本发明提供了一种烧结砖,由包括泥料、污泥的原料制备得到:
9.所述泥料和污泥的质量比为(70~75):(15~20);
10.所述泥料包括建筑渣土和水,所述建筑渣土和水的质量比为1:(0.15~0.3);
11.所述建筑渣土包括以下质量百分数的组分:
12.sio250~70%、al2o315~30%、fe2o32~10%、k2o 3~7%、cao 3~5%;
13.所述污泥的含水率≤40%。
14.优选的,所述建筑渣土的粒径≤0.6mm。
15.优选的,所述建筑渣土中还包括mgo,所述mgo的质量百分数为0.01~3%。
16.优选的,所述烧结砖的含水率为25~30%。
17.本发明提供了上述技术方案所述烧结砖的制备方法,包括以下步骤:
18.将泥料和污泥依次进行混合和陈化,得到陈化料;
19.将所述陈化料进行半干压成型,得到砖坯;
20.将所述砖坯进行微波烧结,得到所述烧结砖。
21.优选的,所述微波烧结包括:将所述砖坯依次经过低温干燥区、低温烧结区和高温烧结区进行烧结;
22.所述低温干燥区和低温烧结区的功率独立的为850~1000w,所述高温烧结区的功率为4000~4050w。
23.优选的,所述微波烧结时,所述砖坯在低温干燥区时的升温程序为:由室温按照第一升温速率升温至第一温度,在所述第一温度进行第一保温;所述第一温度为95~105℃,所述第一升温速率为2~6℃/min,所述第一保温的时间为1~2h;
24.所述微波烧结时,所述砖坯在低温烧结区时的升温程序为:由第一温度按照第二升温速率升温至第二温度,在所述第二温度进行第二保温;再由所述第二温度按照第三升温速速率升温至第三温度,在所述第三温度进行第三保温;
25.所述第二温度为150~200℃;所述第三温度为250~350℃;所述第二升温速率和第三升温速率独立的为2~6℃/min;所述第二保温时间和第三保温时间独立地为10~15min;
26.所述微波烧结时,所述砖坯在高温烧结区时的升温程序为:由所述第三温度按照第四升温速率升温至第四温度,在所述第四温度进行第四保温;再由所述第四温度按照第五升温速速率升温至第五温度,在所述第五温度进行第五保温;
27.所述第四温度为450~550℃;所述第五温度为900~1000℃;所述第四升温速率和第五升温速率独立的为8~12℃/min;所述第四保温时间为10~15min;所述第五保温时间为为5~7h。
28.优选的,所述半干压成型的成型压力为0.5~1mpa;所述半干压成型的保压时间为25~40s。
29.优选的,所述陈化为覆膜陈化,所述覆膜陈化的温度为室温,所述覆膜陈化的时间为24~30h。
30.本发明提供了上述技术方案所述烧结砖或上述技术方案所述制备方法制得的烧结砖在建筑墙体中的应用。
31.本发明提供了一种烧结砖,由包括泥料和污泥的原料制备得到:所述泥料和污泥的质量比为(70~75):(15~20);所述泥料包括建筑渣土和水,所述建筑渣土和水的质量比为1:(0.15~0.3);所述建筑渣土包括以下质量百分数的组分:sio250~70%、al2o315~30%、fe2o32~10%、k2o 3~7%、cao 3~5%;所述污泥的含水率≤40%。本发明提供的烧结砖的制备原料包括泥料和污泥,所述泥料包括建筑渣土和水,实现了建筑渣土和污泥废料的回收利用;本发明提供的烧结砖通过控制泥料和污泥的质量配比关系以及建筑渣土的组成,使建筑渣土和污泥在水的辅助作用下充分融合,能够提高所述烧结砖的致密程度,减少烧结砖烧成后孔洞缺陷的产生;从而使本发明提供的烧结砖具有吸水率小且抗压强度高的特点。由实施例的结果表明,本发明提供的烧结砖具有吸水率<0.37%,抗压强度大于19mpa,收缩率小于1.37%,具有吸水率低且抗压强度高的特点。本发明提供的烧结砖不仅节约了紧缺的粘土原料,并且符合国家的节能减排政策,因此具有广泛的应用前景。
32.本发明提供到了上述技术方案所述烧结砖的制备方法,包括以下步骤:将泥料和污泥依次进行混合和陈化,得到陈化料;将所述陈化料进行半干压成型,得到砖坯;将所述砖坯进行微波烧结,得到所述烧结砖。本发明提供的制备方法采用微波烧结,能够使砖坯的内部和表面受热均匀,使砖坯整体加热至烧结温度实现烧结和致密化,并且微波烧结的热惯性小,使砖坯烧结时温度无惰性改变,不产生“余热”现象,进而使高温的砖坯能够迅速降温,实现生产过程中的自动控温和连续化生产。
附图说明
33.图1为本发明实施例提供的烧结砖的制备流程图;
34.图2为本发明实施例使用的隧道式微波烘干机的实物照片。
具体实施方式
35.本发明提供了一种烧结砖,由包括泥料和污泥的原料制备得到:
36.所述泥料和污泥的质量比为(70~75):(15~20);
37.所述泥料包括建筑渣土和水,所述建筑渣土和水的质量比为1:(0.15~0.3);
38.所述建筑渣土包括以下质量百分数的组分:
39.sio250~70%、al2o315~30%、fe2o32~10%、k2o 3~7%、cao 3~5%;
40.所述污泥的含水率≤40%。
41.在本发明中,若无特殊说明,所用原料均为本领域技术人员熟知的市售产品。
42.本发明提供的烧结砖的制备原料包括泥料;在本发明中,所述所述泥料包括建筑渣土和水,所述建筑渣土包括以下质量百分数的组分:sio250~70%、al2o315~30%、fe2o32~10%、k2o 3~7%、cao 3~5%。以质量百分数计,所述建筑渣土包括50~70%份的sio2,优选为55~65%;以质量百分数计,所述建筑渣土包括15~30%的al2o3,优选为16~28%;以质量百分数计,所述建筑渣土包括3~10%的fe2o3,优选为4~8%;以质量百分数计,所述建筑渣土包括3~7%k2o,优选为4~6%;以质量百分数计,所述建筑渣土包括3~5%cao,优选为3.3~4.5%;以质量百分数计,所述建筑渣土优选还包括0.01~3%mgo,优选为0.05~1%。在本发明中,所述所述建筑渣土的粒径优选≤0.6mm;所述建筑渣土的含水率优选≤10%,更优选≤5%。
43.在本发明中,所述建筑渣土和水的质量比为1:(0.15~0.3),优选为1:(0.25~0.3)。
44.本发明提供的烧结砖的制备原料包括污泥;在本发明中,所述污泥的含水率≤40%,优选为≤38%;在本发明的具体实施例中,所述污泥来源于污水处理厂。
45.在本发明中,所述泥料和污泥的质量比为(70~75):(15~20),优选为(72~74):(16~18)。
46.在本法明中,所述烧结砖的含水率优选为25~30%。
47.本发明提供的烧结砖的制备原料包括建筑渣土和污泥,实现了废料的回收利用;本发明提供的烧结砖的制备原料泥料中包括水,水有助于使骨料充分分散于建筑渣土和污泥中且提高建筑渣土和污泥对河沙的粘结性能;同时,本发明提供的烧结砖通过控制各组分的配比关系和建筑渣土的组成,使建筑渣土和污泥在水的辅助作用下充分融合,能够提高所述烧结砖的致密程度,减少烧结砖烧成后孔洞缺陷的产生;从而使本发明提供的烧结砖具有吸水率小且抗压强度高的特点。
48.本发明提供了上述技术方案所述烧结砖的制备方法,包括以下步骤:
49.将泥料和污泥依次进行混合和陈化,得到陈化料;
50.将所述湿土料进行半干压成型,得到砖坯;
51.将所述陈化料进行微波烧结,得到所述烧结砖。
52.本发明将泥料和污泥依次进行混合和陈化,得到陈化料。
53.在本发明中,所述泥料包括建筑渣土和水,本发明优选对所述建筑渣土进行前处理,在本发明中,所述前处理优选包括依次进行:取料、干燥、破碎和过筛;在本发明中,所述取料优选采用五点法取样;在本发明中,所述干燥优选包括依次进行低温干燥和高温干燥,所述低温干燥的温度优选为40~45℃,所述低温干燥的时间优选为24~30h;所述高温干燥的温度优选为100~110℃,所述高温干燥的时间优选为24~30h。本发明对由室温升温至低温干燥温度的升温速率没有特殊要求;本发明对由低温干燥的温度升温至高温干燥的温度的升温速率没有特殊要求;在本发明的具体实施例中,所述低温干燥和高温干燥优选在干燥箱中进行。
54.在本发明中,当所述建筑渣土的质量优选为80~100kg时,所述破碎的时间优选为5~10min,所述破碎的具体方式优选为干法球磨,本发明对所述干法球磨的具体实施过程没有特殊要求;在本发明的具体实施例中,所述破碎优选在球磨机中进行。
55.在本发明中,所述过筛用的筛子的筛孔孔径优选为0.6mm。
56.本发明优选对所述污泥进行前处理,在本发明中,所述前处理优选包括干燥,本发明优选通过干燥得到含水率小于40%的污泥,在本发明中,所述干燥的方式优选为翻晒,本发明对所述翻晒的具体实施过程没有特殊要求。
57.在本发明中,所述混合优选包括以下步骤:
58.将所述建筑渣土和水进行预混合,得到泥料;
59.将所述泥料和污泥进行终混合。
60.本发明将所述建筑渣土和水进行预混合,得到泥料;在本发明中,所述预混合优选在室温条进行,所述预混合的时间优选为2~5min,所述预混合优选在搅拌的条件下进行,本发明对所述搅拌的具体实施过程没有特殊要求;在本发明的具体实施中,所述预混合优选在搅拌锅中进行。
61.得到泥料后,本发明将所述泥料和污泥进行终混合;在本发明中,所述终混合优选在室温条进行,所述终混合的时间优选为2~5min,所述终混合优选在搅拌的条件下进行,本发明对所述搅拌的具体实施过程没有特殊要求;在本发明的具体实施中,所述终混合优选在搅拌锅中进行。
62.在本发明中,所陈化优选为覆膜陈化,在本发明中,所述覆膜陈化的温度优选为室温,所述覆膜陈化的时间优选为24~30h;在本发明的具体实施例中,所述覆膜陈化优选在陈化桶中进行,本发明优选将所述混合料倒入陈化桶中后,人工搅拌均匀后在所述陈化桶口覆盖保鲜膜,并在保鲜膜内喷洒水,以保证所述陈化桶内的相对湿度。
63.本发明通过陈化能够使所述混合料中的固体颗粒表面的水分充分渗入固体颗粒内部,固体颗粒疏解、水分匀化,能够提升所述湿土料的塑性。
64.得到陈化料后,本发明将所述陈化料进行半干压成型,得到砖坯。
65.在本发明中,所述半干压成型的成型压力优选为0.5~1mpa,更优选为0.6~0.8mpa;所述半干压成型的保压时间优选为25~40s,更优选为30~35s;本发明对由常压升压至所述成型压力的升压速率没有特殊要求。在本发明中,所述半干压成型后的初坯优选为矩形坯体,本发明对所述初坯的尺寸没有特殊要求,在本发明的具体实施例中,所述初坯的长优选为240mm,所述初始坯体的款优选为115mm,所述初坯的高优选为53mm。
66.本发明由于提供的烧结砖原料中含有水分,采用半干压成型能够克服干压法密度
过大的缺点,又无湿法成型后样品在烧结中形成的大量气孔使烧成品强度下降的弱点。
67.在本发明中,所述半干压成型后得到湿砖坯,所述半干压成型后,本发明优选还包括将所述湿砖坯自然晾干,得到所述砖坯。在本发明中,所述自然晾干的温度优选为室温,所述自然晾干的时间优选为3~5天。本发明优选通过自然晾干使湿砖坯中自由水缓慢蒸发除去自由水,防止其在微波烧结中快速挥发造成坯体变形或在坯体中形成气泡。
68.得到砖坯后,本发明将所述砖坯进行微波烧结,得到所述烧结砖。
69.在本发明中,所述微波烧结优选包括:将所述砖坯依次经过低温干燥区、低温烧结区和高温烧结区进行烧结。
70.在本发明中,所述低温干燥区的功率优选为850~1000w,所述低温烧结区的功率优选为850~1000w,所述高温烧结的功率优选为4000~4050w。
71.在本发明的具体实施例中,所述微波烧结优选在隧道式微波烘干机中进行,在本发明中,所述砖坯在低温干燥区、低温烧结区和高温烧结区进行烧结时,所述砖坯为静置状态,所述砖坯由低温干燥区输送至低温烧结区的速度优选为5s/m,由低温烧结区输送至中温烧结区的的输送速度为5s/m,由中温烧结区输送至高温烧结区的输送速度优选为5s/m。
72.在本发明中,所述微波烧结时,所述砖坯在低温干燥区时的升温程序优选为:由室温按照第一升温速率升温至第一温度,在所述第一温度进行第一保温;所述第一温度优选为95~105℃,所述第一升温速率优选为2~6℃/min,更优选为2.3~5℃/min。所述第一保温的时间优选为1~2h;本发明通过低温干燥使砖坯中结合水缓慢蒸发,防止其在微波烧结中快速挥发造成坯体变形或在坯体中形成气泡。
73.在本发明中,所述微波烧结时,所述砖坯在过低温烧结区时的升温程序为:由第一温度按照第二升温速率升温至第二温度,在所述第二温度进行第二保温;再由所述第二温度按照第三升温速速率升温至第三温度,在所述第三温度进行第三保温;在本发明中,所述第二温度优选为150~200℃,更优选为180
±
5℃;所述第三温度优选为250~350℃,更优选为300
±
5℃;所述第二升温速率优选为2~6℃/min,更优选为2.3~5℃/min,所述第三升温速率优选为2~6℃/min,更优选为2.3~5℃/min;所述第二保温时间优选为10~15min,所述第三保温时间优选为10~15min。
74.在本发明中,所述微波烧结时,所述砖坯在高温烧结区时的升温程序为:由所述第三温度按照第四升温速率升温至第四温度,在所述第四温度进行第四保温;再由所述第四温度按照第五升温速速率升温至第五温度,在所述第五温度进行第五保温;在本发明中,所述第四温度优选为450~550℃,更优选为500
±
5℃;所述第五温度优选为900~1000℃,更优选为1000
±
5℃;所述第四升温速率优选为8~12℃/min,更优选为10℃/min,所述第五升温速率优选为8~12℃/min,更优选为10℃/min;所述第四保温时间优选为10~15min,所述第五保温时间优选为5~7h。
75.在本发明中,所述微波烧结时,所述砖坯的数量优选为2块。
76.本发明优选对所述微波烧结后的烧成砖坯进行检测,检测合格后得到烧结砖成品,在本发明中,所述检测优选包括物相检测和力学性能检测;在本发明中,所述物相检测优选为检测所述烧成砖坯是否存在微观气孔缺陷、宏观形貌是否规整;所述力学性能检测优选为检测所述烧成砖坯的抗压强度是否合格。在本发明中,当所述烧成砖坯进行物相检测满足微观无气孔且宏观形貌完整,同时,当所述烧成砖坯进行力学性能检测满足抗压强
度≥10mpa时,则检测合格得到烧结砖成品。
77.本发明提供了上述技术方案所述烧结砖或上述技术方案所述制备方法制得的烧结砖在建筑墙体中的应用。
78.在本发明中,所述烧结砖优选用于民用建筑、工业建筑或农业建筑的砖结构墙体中。
79.下面将结合本发明中的实施例,对本发明中的技术方案进行清楚、完整地描述。显然,所描述的实施例仅是本发明一部分实施例,而不是全部的实施例。基于本发明中的实施例,本领域普通技术人员在没有做出创造性劳动前提下所获得的所有其他实施例,都属于本发明保护的范围。
80.实施例1
81.按照五点法取建筑渣土废料(sio269%、al2o318%、fe2o35%、k2o 4%、cao 4%)在100℃干燥24h;然后采用干法球磨破碎5min,过0.6mm筛,得到建筑渣土,粒径≤0.6mm。
82.按照图1所示工艺流程,将处理后的建筑渣土和水(质量比为1:0.15)在搅拌锅中混合5min,得到泥料;
83.将污水厂的污泥经过翻晒,得到含水率为38%污泥;
84.将75kg泥料和15kg污泥在搅拌锅中混合5min,然后倒入陈化桶中,人工搅拌均匀后,用保鲜膜覆盖,并在保鲜膜内喷洒少量水,放置在室温下陈化24h,得到90kg陈化料;
85.将陈化料采用半干压成型压制成湿砖坯,成型压力为0.8mpa,保压时间为30s,得到湿砖坯,尺寸为240mm
×
115mm
×
53mm;
86.将湿砖坯在室温条件下自然晾干3天得到砖坯;
87.将2块砖坯送入隧道式微波烘干机中进行微波烧结,首先将砖坯放置在隧道式微波烘干机烘干带中进行低温干燥,具体升温程序为:按照1000w功率将2块砖坯由室温升温至100
±
5℃(升温速率为2~4℃/min)保温1h后,然后将2块砖坯随输送带送入隧道式微波烘干机烧结带中,按照1000w功率升温至300
±
5℃(升温速率为2~4℃/min)保温12min后,按照4000w功率升温至500
±
5℃(升温速率为8~10℃/min)保温12min后;按照4000w功率升温至1050
±
5℃(升温速率为8~10℃/min)保温6h后,对降温至室温的烧成砖坯进行物相检测和力学性能检测后,得到烧结砖成品。
88.实施例2
89.按照五点法取建筑渣土废料(sio266%、al2o318%、fe2o35%、k2o 4%、cao 4%、mgo 3%)在45℃干燥24h后在100℃干燥24h;然后采用干法球磨破碎5min,过0.6mm筛,得到建筑渣土,粒径≤0.6mm。
90.按照图1所示工艺流程,将处理后的建筑渣土和水(质量比为1:0.17)在搅拌锅中混合5min,得到泥料;
91.将污水厂的污泥经过翻晒,得到含水率为38%污泥;
92.将70kg泥料和18kg污泥在搅拌锅中混合5min,然后倒入陈化桶中,人工搅拌均匀后,用保鲜膜覆盖,并在保鲜膜内喷洒少量水,放置在室温下陈化24h,得到88kg陈化料;
93.将陈化料采用半干压成型压制成湿砖坯,成型压力为0.8mpa,保压时间为30s,得到湿砖坯,尺寸为240mm
×
115mm
×
53mm;
94.将湿砖坯在室温条件下自然晾干3天得到砖坯;
95.将2块砖坯送入隧道式微波烘干机中进行微波烧结,首先将砖坯放置在隧道式微波烘干机烘干带中进行低温干燥,具体升温程序为:按照1000w功率将2块砖坯由室温升温至100
±
5℃(升温速率为2~4℃/min)保温1h后,然后将2块砖坯随输送带送入隧道式微波烘干机烧结带中,按照1000w功率升温至300
±
5℃(升温速率为2~4℃/min)保温12min后,按照4000w功率升温至500
±
5℃(升温速率为8~10℃/min)保温12min后;按照4000w功率升温至1050
±
5℃(升温速率为8~10℃/min)保温6h后,对降温至室温的烧成砖坯进行物相检测和力学性能检测后,得到烧结砖成品。
96.实施例3
97.按照五点法取建筑渣土废料(sio269%、al2o318%、fe2o35%、k2o 4%、cao 4%)在45℃干燥24h后在100℃干燥24h;然后采用干法球磨破碎5min,过0.6mm筛,得到建筑渣土,粒径≤0.6mm。
98.按照图1所示工艺流程,将处理后的建筑渣土和水(质量比为1:0.172)在搅拌锅中混合5min,得到73.66kg泥料;
99.将污水厂的污泥经过翻晒,得到含水率为38%污泥;
100.将73.66kg泥料和16kg污泥在搅拌锅中混合5min,然后倒入陈化桶中,人工搅拌均匀后,用保鲜膜覆盖,并在保鲜膜内喷洒少量水,放置在室温下陈化24h,得到90kg陈化料;
101.将陈化料采用半干压成型压制成湿砖坯,成型压力为0.8mpa,保压时间为30s,得到湿砖坯,尺寸为240mm
×
115mm
×
53mm;
102.将湿砖坯在室温条件下自然晾干3天得到砖坯;
103.按照1000w功率将2块砖坯由室温升温至100
±
5℃(升温速率为2~4℃/min)保温1h后,然后将2块砖坯随输送带送入隧道式微波烘干机烧结带中,按照1000w功率升温至300
±
5℃(升温速率为2~4℃/min)保温12min后,按照4000w功率升温至500
±
5℃(升温速率为8~10℃/min)保温12min后;按照4000w功率升温至1050
±
5℃(升温速率为8~10℃/min)保温6h后,对降温至室温的烧成砖坯进行物相检测和力学性能检测后,得到烧结砖成品。
104.对比例1
105.按照五点法取建筑渣土废料(sio269%、al2o318%、fe2o35%、k2o 4%、cao 4%)在45℃干燥24h后在100℃干燥24h;然后采用干法球磨破碎5min,过0.6mm筛,得到建筑渣土,粒径≤0.6mm。
106.按照图1所示工艺流程,将处理后的建筑渣土在搅拌锅中搅拌5min,得到泥料;
107.将污水厂的污泥经过翻晒,得到含水率为38%污泥;
108.将75kg泥料和15kg污泥在搅拌锅中混合5min,然后倒入陈化桶中,人工搅拌均匀后,用保鲜膜覆盖,并在保鲜膜内喷洒少量水,放置在室温下陈化24h,得到陈化料;
109.将陈化料采用半干压成型压制成湿砖坯,成型压力为0.8mpa,保压时间为30s,得到湿砖坯,尺寸为240mm
×
115mm
×
53mm;
110.将湿砖坯在室温条件下自然晾干3天得到砖坯;
111.按照1000w功率将2块砖坯由室温升温至100
±
5℃(升温速率为2~4℃/min)保温1h后,然后将2块砖坯随输送带送入隧道式微波烘干机烧结带中,按照1000w功率升温至300
±
5℃(升温速率为2~4℃/min)保温12min后,按照4000w功率升温至500
±
5℃(升温速率为8~10℃/min)保温12min后;按照4000w功率升温至1050
±
5℃(升温速率为8~10℃/min)保
温6h后,对降温至室温的烧成砖坯进行物相检测和力学性能检测后,得到烧结砖成品。
112.对比例2
113.按照五点法取建筑渣土废料(sio269%、al2o318%、fe2o35%、k2o 4%、cao 4%)在45℃干燥24h后在100℃干燥24h;然后采用干法球磨破碎5min,过0.6mm筛,得到建筑渣土,粒径≤0.6mm。
114.按照图1所示工艺流程,将处理后的建筑渣土和水(质量比为1:0.2)在搅拌锅中混合5min,得到泥料;
115.将污水厂的污泥经过翻晒,得到含水率为38%污泥;
116.将75kg泥料和15kg污泥在搅拌锅中混合5min,然后倒入陈化桶中,人工搅拌均匀后,用保鲜膜覆盖,并在保鲜膜内喷洒少量水,放置在室温下陈化24h,得到陈化料;
117.将陈化料和10kg骨料(粒径为10mm)在搅拌锅中混合5min,得到100kg湿土料;
118.将湿土料采用半干压成型压制成湿砖坯,成型压力为0.8mpa,保压时间为30s,得到湿砖坯,尺寸为240mm
×
115mm
×
53mm;
119.将湿砖坯在室温条件下自然晾干3天得到砖坯;
120.按照1000w功率将2块砖坯由室温升温至100
±
5℃(升温速率为2~4℃/min)保温1h后,然后将2块砖坯随输送带送入隧道式微波烘干机烧结带中,按照1000w功率升温至300
±
5℃(升温速率为2~4℃/min)保温12min后,按照4000w功率升温至500
±
5℃(升温速率为8~10℃/min)保温12min后;按照4000w功率升温至1050
±
5℃(升温速率为8~10℃/min)保温6h后,对降温至室温的烧成砖坯进行物相检测和力学性能检测后,得到烧结砖成品。
121.对比例3
122.按照五点法取建筑渣土废料(sio269%、al2o318%、fe2o35%、k2o 4%、cao 4%)在100℃干燥24h;然后采用干法球磨破碎5min,过0.6mm筛,得到建筑渣土,粒径≤0.6mm。
123.按照图1所示工艺流程,将处理后的建筑渣土和水(质量比为7.5:1)在搅拌锅中混合5min,得到泥料;
124.将污水厂的污泥经过翻晒,得到含水率为38%污泥;
125.将75泥料和15kg污泥在搅拌锅中混合5min,然后倒入陈化桶中,人工搅拌均匀后,用保鲜膜覆盖,并在保鲜膜内喷洒少量水,放置在室温下陈化24h,得到陈化料;
126.将陈化料采用半干压成型压制成湿砖坯,成型压力为0.8mpa,保压时间为30s,得到湿砖坯,尺寸为240mm
×
115mm
×
53mm;
127.将湿砖坯在室温条件下自然晾干3天得到砖坯;
128.按照4000w功率将2块砖坯由室温升温至100
±
5℃(升温速率为2~4℃/min)保温15h后,砖坯爆裂,无法得到产品。
129.对比例4
130.按照五点法取建筑渣土废料(sio269%、al2o318%、fe2o35%、k2o 4%、cao 4%)在100℃干燥24h;然后采用干法球磨破碎5min,过0.6mm筛,得到建筑渣土,粒径≤0.6mm。
131.按照图1所示工艺流程,将处理后的建筑渣土和水(质量比为1:0.15)在搅拌锅中混合5min,得到泥料;
132.将污水厂的污泥经过翻晒,得到含水率为38%污泥;
133.将75kg泥料和15kg污泥在搅拌锅中混合5min,然后倒入陈化桶中,人工搅拌均匀
后,用保鲜膜覆盖,并在保鲜膜内喷洒少量水,放置在室温下陈化24h,得到90kg陈化料;
134.将陈化料采用半干压成型压制成湿砖坯,成型压力为0.8mpa,保压时间为30s,得到湿砖坯,尺寸为240mm
×
115mm
×
53mm;
135.将湿砖坯在室温条件下自然晾干3天得到砖坯;
136.按照4000w功率将1块砖坯由室温升温至100
±
5℃(升温速率为2~4℃/min)保温1h后,砖坯爆裂,无法得到产品。
137.对比例5
138.按照五点法取建筑渣土废料(sio269%、al2o318%、fe2o35%、k2o 4%、cao 4%)在100℃干燥24h;然后采用干法球磨破碎5min,过0.6mm筛,得到建筑渣土,粒径≤0.6mm。
139.按照图1所示工艺流程,将处理后的建筑渣土和水(质量比为1:0.15)在搅拌锅中混合5min,得到泥料;
140.将污水厂的污泥经过翻晒,得到含水率为38%污泥;
141.将75kg泥料和15kg污泥在搅拌锅中混合5min,然后倒入陈化桶中,人工搅拌均匀后,用保鲜膜覆盖,并在保鲜膜内喷洒少量水,放置在室温下陈化24h,得到90kg陈化料;
142.将陈化料采用半干压成型压制成湿砖坯,成型压力为0.8mpa,保压时间为30s,得到湿砖坯,尺寸为240mm
×
115mm
×
53mm;
143.将湿砖坯在室温条件下自然晾干3天得到砖坯;
144.按照2000w功率将2块砖坯由室温升温至100
±
5℃(升温速率为2~4℃/min)保温1h后,砖坯爆裂,无法得到产品。
145.测试例1
146.对实施例1~3、对比例1和2制备的烧结砖进行吸水率和力学性能测试,其中,吸水率、抗压强度和收缩率的测试标准为gb/t 2542-2012;测试结果如表1所示,由表1可以得出,本发明实施例1~3制备的烧结砖具有吸水率<0.37%,抗压强度大于19mpa,收缩率小于1.37%,具有吸水率低且抗压强度高的特点。本发明提供的烧结砖不仅节约了紧缺的粘土原料,并且符合国家的节能减排政策,因此具有广泛的应用前景。
147.表1实施例1~3、对比例1和2制备的产品的性能测试
148.序号吸水率/%抗压强度/mpa收缩率/%实施例10.3119.321.29实施例20.3319.701.32实施例30.3719.551.37对比例10.4210.313.74对比例20.4011.933.68
149.以上所述仅是本发明的优选实施方式,应当指出,对于本技术领域的普通技术人员来说,在不脱离本发明原理的前提下,还可以做出若干改进和润饰,这些改进和润饰也应视为本发明的保护范围。