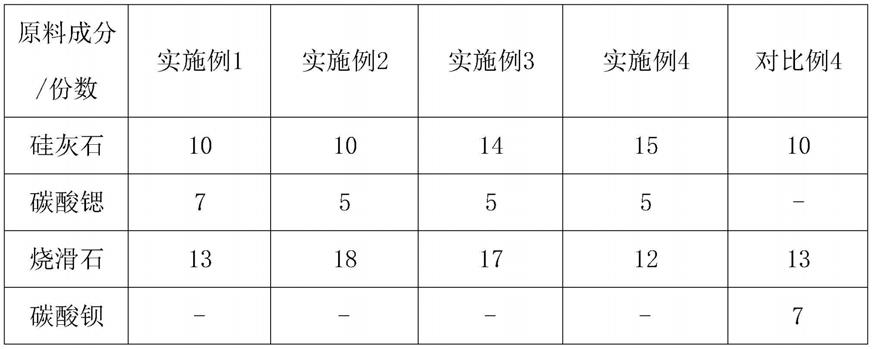
1.本发明涉及一种陶瓷生产技术,尤其涉及一种金丝绒质感陶瓷岩板的制备工艺及陶瓷岩板。
背景技术:
2.随着经济的发展和人民生活水平的提高,建筑地面装饰业越来越受到重视,在家居装修中占据主要部分。陶瓷岩板作为一种新型装饰材料,广泛的应用于家居装饰领域,可用于背景墙、橱柜、衣柜、茶具、浴室柜、洗手台、门和厨房灶台面板等。当前,随着陶瓷岩板产品的应用市场越来越广阔,同时对陶瓷装饰技术有着愈加苛刻的要求。借助其他材料的融合丰富陶瓷装饰,使陶瓷装饰效果更加丰富多样,是现代陶瓷釉面装饰的重要风向标之一;例如,陶瓷岩板应用在上述衣柜、茶具、浴室柜、洗手台等装饰中,由于消费者可经常近距离观察及触摸到,因此更好地控制陶瓷岩板砖面的平整度、细腻度及光泽度满足细腻质感要求,打造开发出性能更优异的陶瓷岩板也是全行业追求的共同目标。
3.目前,传统陶瓷的生产工艺流程为制坯体、施底釉、喷墨印花、喷保护釉、烧成、磨边、检测入库。施釉工艺主要包括喷釉、印釉和淋釉等方式。现有的喷釉方式是用喷枪通过高压将釉浆喷散成雾状,施加到坯体表面,但容易产生施釉不均,不平,缺釉现象,为常用的施釉方式。现有的淋釉方式是将釉浆抽入高位罐,通过管道和阀门的控制作用,使釉浆通过光滑的半弧形淋釉器如瀑布一样覆盖在坯体表面;但是该方法的施釉量由于半弧形瀑布状釉料呈曲面泄落,容易产生施釉分布不够均匀,容易产生断釉,开叉,釉料泄落一致性差等问题,导致釉面平整度、光泽度、细腻度不够;而陶瓷岩板因为规格大,其平整度、光泽度、细腻度的控制难度大大提高,用于生产一般规格的陶瓷(小于1m2)所采用的半弧形淋釉设备不能满足陶瓷岩板的生产需要,额外研发适配陶瓷岩板生产的设备成本居高。虽然现有技术有采用数码打印机控制施釉的陶瓷生产技术,但数码打印机采购成本极高。因此,在现有的生产设备前提下生产陶瓷岩板,上述技术问题仍是一个亟待攻克的技术难点。
4.因此,有必要研发一种砖面光泽度、平整度更优,细腻度更好、手感更好、成本更可控的陶瓷岩板制备工艺及其产品。
技术实现要素:
5.为了克服现有技术的不足,本发明的目的之一在于提供一种金丝绒质感陶瓷岩板的制备工艺。本陶瓷岩板制备工艺制得的陶瓷岩板其砖面光泽度、平整度更优,细腻度更好、手感更好、成本更可控。
6.本发明的目的之二在于提供一种由本发明目的一所述的金丝绒质感陶瓷岩板的制备工艺制备而成的金丝绒质感陶瓷岩板。该陶瓷岩板其砖面光泽度、平整度优,细腻度好、手感好。
7.本发明的目的之一采用如下技术方案实现:一种金丝绒质感陶瓷岩板的制备工艺,包括如下步骤:
8.(1)坯体成型
9.将陶瓷岩板粉料压制成型为陶瓷岩板坯体;将成型后的坯体运送至干燥窑中干燥;坯体经过干燥窑后,喷水,保持表面湿度;
10.(2)施底釉
11.将底釉喷洒到坯体表面,形成底釉层;所述底釉的比重1.85-1.92,流速为32-36s,施釉量85-95g;
12.(3)喷墨印花
13.在底釉层上,根据设计的图案,再进行喷墨印花处理;
14.(4)施金丝绒基釉
15.将金丝绒基釉按每100g添加100g辊筒印油的比例调至比重为1.1-1.3的浆釉,搅拌均匀,采用辊筒印刷方式施第一道金丝绒釉;将制备好的金丝绒基釉加添加剂调至比重为1.88-1.95的浆釉,施釉量为85-90g,流速为30-33s,采用线性淋釉管施第二道金丝绒釉;
16.按质量百分比计,所述金丝绒基釉的化学组成包括:sio
2 50-55%、al2o
3 15-17%、k2o 3-4%、na2o 3-4%、cao 4-8%、mgo 3-7%、sro 3-5%、zno 4-6%,所述金丝绒基釉的烧失量为1-10%;
17.(5)烧成、磨边、检测入库
18.施釉后的坯体送入窑炉中,高温烧成,出窑,冷却,磨边、检测入库,得陶瓷成品。
19.进一步地,所述坯体由如下重量份的组分制备而成:钾钠石16-18份、钾长石3-5份、超白石粒12-14份、强塑砂1-3份、精选砂20-24份、煅烧高岭土15-18份、高铝粉2-4份、高粘土3-5份、福白砂6-8份、高白煅烧高岭土11-13份、坯黑色料4-5份、水玻璃0.5-0.8份、三聚磷酸钠0.1-0.3份、解胶剂0.1-0.2份。
20.进一步地,所述底釉由如下重量份的组分制备而成:钾长石32-38份、钠长石18-22份、石英6-9份、烧土20-25份、煅烧氧化铝10-14份、煅烧氧化锌1-3份。
21.进一步地,按质量百分比计,所述底釉的化学组成包括:sio
2 55-60%、cao 0.2-0.4%、al2o
3 30-35%、na2o 2-5%、k2o 2-5%、mgo 0.1-0.5%、zno 2-3%,所述底釉的烧失量为0.01-5%。
22.进一步地,所述金丝绒基釉由如下重量份组分制备而成:硅灰石5-15份、碳酸锶5-10份、烧滑石10-18份、钾长石30-40份、霞石10-20份、煅烧高岭土5-12份、石英1-10份、白刚玉1-5份、煅烧氧化锌3-8份。
23.进一步地,所述金丝绒基釉由如下重量份组分制备而成:硅灰石10份、碳酸锶7份、烧滑石13份、钾长石35份、霞石15份、煅烧高岭土8份、石英4份、白刚玉3份、煅烧氧化锌5份。
24.进一步地,所述金丝绒基釉的制备工艺如下:按照配方量的金丝绒基釉;加入羧甲基纤维素和三聚磷酸钠添加剂;以料:水:羧甲基纤维素:三聚磷酸钠=100:36:(0.1-0.2):(0.3-0.35)进行配料,球磨,球磨时间为8-9h,以使出球釉浆性能为325目,筛余0.4-0.6%,比重1.88-1.95,出球流速为60-80s。
25.进一步地,在步骤(2)施底釉之前以及之后均需要干燥的步骤;在步骤(2)施底釉之前,对喷水的坯体进行干燥,干燥温度为150-180℃,时间为2-5min;在步骤(2)施底釉之后,对底釉层表面进行干燥,干燥温度为150-180℃,时间为2-5min;
26.在步骤(4)施金丝绒基釉之前需要对喷墨印花后的图案层表面进行干燥,出窑产
品表面温度控制在80℃以下。
27.进一步地,所述步骤(5)的烧成温度为1160℃-1180℃,时间为70-90min。
28.本发明的目的之二采用如下技术方案实现:一种金丝绒质感陶瓷岩板,由如上所述的金丝绒质感陶瓷岩板的制备工艺制备而成。
29.相比现有技术,本发明的有益效果在于:
30.在本发明中,解决淋釉工艺中“分叉”导致陶瓷岩板因为规格大,其平整度、光泽度、细腻度难以控制的技术问题,其关键在于通过控制两道金丝釉料的施布、金丝绒基釉比重的控制、光滑的线性施釉管的设计等因素共同作用;
31.本工艺设计两道金丝釉料施布,第一道金丝绒基釉的作用有两方面,一方面在于对喷墨图案起到保护作用,另一方面在于提高与第二道金丝绒基釉的结合度与适配度,起到承上启下的作用。另外,第一道金丝绒基釉要求很薄,印釉方式更平整,更薄,淋釉无法实现生产。印釉的比重不易过高,粘度不易过大,否则容易粘辊,无法实现生产。第二道金丝绒基釉的作用一方面增加釉层厚度,另一方面通过调整第二道金丝绒基釉配方的高温粘度、高温流动性以及比重大小,以提高釉面平整度、光泽度、细腻度,减少水波纹。本发明实施例1为最佳的实施例,其制得的金丝绒质感陶瓷岩板的平整度、光泽度、细腻度优异。
32.相比现有的半弧形施釉设备,本发明采用光滑的线性施釉管直接安装在原来的施釉设备上,使同一施釉面上的釉料分布更为均匀,不开叉,提高釉面平整度、光泽度、细腻度;且线性施釉管代替半弧形施釉器,仅仅改进施釉器该部件,设备改装成本低。
附图说明
33.图1为由本发明实施例1制备而得的陶瓷岩板的图片。图2为本发明实施例1的金丝绒质感陶瓷岩板的灯照试验下的砖面效果。
34.图3为现有市面常见的柔光砖的灯照试验下的砖面效果。
35.图4为现有市面常见的亮面砖的灯照试验下的砖面效果。
具体实施方式
36.下面,结合附图以及具体实施方式,对本发明做进一步描述,需要说明的是,在不相冲突的前提下,以下描述的各实施例之间或各技术特征之间可以任意组合形成新的实施例。
37.在本发明中,若非特指,所有的份、百分比均为重量单位,所采用的设备和原料等均可从市场购得或是本领域常用的。下述实施例中的方法,如无特别说明,均为本领域的常规方法。
38.一种金丝绒质感陶瓷岩板的制备工艺,包括如下步骤:
39.(1)坯体成型
40.将陶瓷岩板粉料压制成型为陶瓷岩板坯体;将成型后的坯体运送至干燥窑中干燥;坯体经过干燥窑后,喷水,保持表面湿度;
41.本步骤中,坯体配方的优选方案如下:所述坯体由如下重量份的组分制备而成:钾钠石16-18份、钾长石3-5份、超白石粒12-14份、强塑砂1-3份、精选砂20-24份、煅烧高岭土15-18份、高铝粉2-4份、高粘土3-5份、福白砂6-8份、高白煅烧高岭土11-13份、坯黑色料4-5
份、水玻璃0.5-0.8份、三聚磷酸钠0.1-0.3份、解胶剂0.1-0.2份。
42.作为最优方案,所述坯体由如下重量份的组分制备而成:钾钠石17份、钾长石4份、超白石粒13份、强塑砂2份、精选砂22份、煅烧高岭土16份、高铝粉3份、高粘土4份、福白砂7份、高白煅烧高岭土12份、坯黑色料4.5份、水玻璃0.6份、三聚磷酸钠0.2份、解胶剂0.1份。
43.(2)施底釉
44.在步骤(2)施底釉之前,对喷水的坯体进行干燥,干燥温度为150-180℃,时间为2-5min;将底釉喷洒到坯体表面,形成底釉层;所述底釉的比重1.85-1.92,流速为32-36s,施釉量85-95g;在步骤(2)施底釉之后,对底釉层表面进行干燥,干燥温度为150-180℃,时间为2-5min;
45.在步骤(2)施底釉之前,对喷水的坯体进行干燥,防止坯体表面水分过多,产生裂坯。在步骤(2)施底釉之后,对底釉层表面进行干燥,烘干防止水油互相排斥,即水性的底釉与待喷墨的油性墨水之间相互排斥。
46.此外,本底釉为高粘高钾系配方,硅含量和烧土主要是调整高温粘度(硅含量50%以上),高温粘度大可以压制气泡,减少痱子;钾含量影响烧成范围,射程范围比较宽,提高膨胀系数,调整发色。
47.本步骤中,底釉配方的优选方案如下:所述底釉由如下重量份的组分制备而成:钾长石32-38份、钠长石18-22份、石英6-9份、烧土20-25份、煅烧氧化铝10-14份、煅烧氧化锌1-3份。按质量百分比计,所述底釉的化学组成包括:sio
2 55-60%、cao 0.2-0.4%、al2o
3 30-35%、na2o 2-5%、k2o 2-5%、mgo 0.1-0.5%、zno 2-3%,所述底釉的烧失量为0.01-5%。
48.作为最优方案,所述底釉由如下重量份的组分制备而成:钾长石35份、钠长石21份、石英8份、烧土22份、煅烧氧化铝12份、煅烧氧化锌2份。按质量百分比计,该底釉的化学组成包括:sio
2 58.64%、cao 0.36%、al2o
3 31.76%、na2o 3.15%、k2o 3.36%、mgo 0.2%、zno 2.0%,所述底釉的烧失量为0.53%。
49.(3)喷墨印花
50.在底釉层上,根据设计的图案,再进行喷墨印花处理;
51.(4)施金丝绒基釉
52.在步骤(4)施金丝绒基釉之前需要对喷墨印花后的图案层表面进行干燥,出窑产品表面温度控制在80℃以下,以进一步对喷墨图案起到定型、保护作用。然后,将金丝绒基釉按每100g添加100g辊筒印油的比例调至比重为1.1-1.3的浆釉,搅拌均匀,采用辊筒印刷方式施第一道金丝绒釉;将制备好的金丝绒基釉加添加剂调至比重为1.88-1.95的浆釉,施釉量为85-90g,流速为30-33s,采用线性淋釉管施第二道金丝绒釉;
53.本步骤中,金丝绒基釉配方的优选方案如下:所述金丝绒基釉由如下重量份组分制备而成:硅灰石5-15份、碳酸锶5-10份、烧滑石10-18份、钾长石30-40份、霞石10-20份、煅烧高岭土5-12份、石英1-10份、白刚玉1-5份、煅烧氧化锌3-8份。按质量百分比计,所述金丝绒基釉的化学组成包括:sio
2 50-55%、al2o
3 15-17%、k2o 3-4%、na2o 3-4%、cao 4-8%、mgo 3-7%、sro 3-5%、zno 4-6%,所述金丝绒基釉的烧失量为1-10%。
54.作为最优方案,所述金丝绒基釉由如下重量份组分制备而成:硅灰石10份、碳酸锶7份、烧滑石13份、钾长石35份、霞石15份、煅烧高岭土8份、石英4份、白刚玉3份、煅烧氧化锌
5份。按质量百分比计,所述金丝绒基釉的化学组成包括:sio
2 53.3%、al2o
3 16.37%、k2o 3.9%、na2o 3.15%、cao 4.95%、mgo 4.29%、sro 4.9%、zno 5%,所述金丝绒基釉的烧失量为3.14%。
55.本发明金丝绒基釉的高温粘度低、高温流动性好,具体通过提高配方中硅含量以提高釉料的高温粘度,再通过调整钙镁钡锶含量,降低高温粘度,提高釉料的高温流动性,具体通过调整钾钠含量,调整釉料的膨胀系数,调节釉料膨胀系数,使得砖型达到要求。
56.所述金丝绒基釉的制备工艺如下:按照配方量的金丝绒基釉;加入羧甲基纤维素和三聚磷酸钠添加剂;以料:水:羧甲基纤维素:三聚磷酸钠=100:36:(0.1-0.2):(0.3-0.35)进行配料,球磨,球磨时间为8-9h,以使出球釉浆性能为325目,筛余0.4-0.6%,比重1.88-1.95,出球流速为60-80s。
57.本发明通过加入三聚磷酸钠添加剂提高金丝绒基釉的物理流动性,通过加入羧甲基纤维素提高金丝绒基釉的物理粘度,保持一定粘度、且高流动的金丝绒基釉有利于解决淋釉工艺中“分叉”问题,保持淋釉的釉料泄面一致性。
58.(5)烧成、磨边、检测入库
59.施釉后的坯体送入窑炉中,高温烧成,出窑,冷却,磨边、检测入库,得陶瓷成品。其中,所述步骤(5)的烧成温度为1160℃-1180℃,时间为70-90min。
60.本发明还提供一种金丝绒质感陶瓷岩板,由如上所述的金丝绒质感陶瓷岩板的制备工艺制备而成。
61.实施例1
62.一种金丝绒质感陶瓷岩板的制备工艺,包括如下步骤:
63.(1)坯体成型
64.将陶瓷岩板粉料压制成型为陶瓷岩板坯体;将成型后的坯体运送至干燥窑中干燥;坯体经过干燥窑后,喷水,保持表面湿度;
65.所述坯体的配方为最优选配方,具体由如下重量份的组分制备而成:钾钠石17份、钾长石4份、超白石粒13份、强塑砂2份、精选砂22份、煅烧高岭土16份、高铝粉3份、高粘土4份、福白砂7份、高白煅烧高岭土12份、坯黑色料4.5份、水玻璃0.6份、三聚磷酸钠0.2份、解胶剂0.1份。
66.(2)施底釉
67.在步骤(2)施底釉之前,对喷水的坯体进行干燥,干燥温度为150-180℃,时间为2-5min;将底釉喷洒到坯体表面,形成底釉层;所述底釉的比重1.85-1.92,流速为32-36s,施釉量85-95g;在步骤(2)施底釉之后,对底釉层表面进行干燥,干燥温度为150-180℃,时间为2-5min;
68.本实施例底釉采用最优配方,具体由如下重量份的组分制备而成:钾长石35份、钠长石21份、石英8份、烧土22份、煅烧氧化铝12份、煅烧氧化锌2份。按质量百分比计,该底釉的化学组成包括:sio
2 58.64%、cao 0.36%、al2o
3 31.76%、na2o 3.15%、k2o 3.36%、mgo 0.2%、zno 2.0%,所述底釉的烧失量为0.53%。
69.(3)喷墨印花
70.在底釉层上,根据设计的图案,再进行喷墨印花处理;
71.(4)施金丝绒基釉
72.在步骤(4)施金丝绒基釉之前需要对喷墨印花后的图案层表面进行干燥,出窑产品表面温度控制在80℃以下。然后,将金丝绒基釉按每100g添加100g辊筒印油的比例调至比重为1.2的浆釉,搅拌均匀,通过采用辊筒印刷方式施第一道金丝绒釉;将制备好的金丝绒基釉加水调至比重为1.9的浆釉,施釉量为88g,流速为32s,采用线性淋釉管施第二道金丝绒釉;
73.本实施例所述金丝绒基釉为最优配方,具体由如下重量份组分制备而成:硅灰石10份、碳酸锶7份、烧滑石13份、钾长石35份、霞石15份、煅烧高岭土8份、石英4份、白刚玉3份、煅烧氧化锌5份。
74.按质量百分比计,所述金丝绒基釉的化学组成包括:sio
2 53.3%、al2o
3 16.37%、k2o 3.9%、na2o 3.15%、cao 4.95%、mgo 4.29%、sro 4.9%、zno 5%,所述金丝绒基釉的烧失量为3.14%。
75.所述金丝绒基釉的制备工艺如下:按照配方量的金丝绒基釉;加入羧甲基纤维素和三聚磷酸钠添加剂;以料:水:羧甲基纤维素:三聚磷酸钠=100:36:0.15:0.3进行配料,球磨,球磨时间为8-9h,以使出球釉浆性能为325目筛余0.4-0.6%,比重1.9,出球流速为60-80s。
76.(5)烧成、磨边、检测入库
77.施釉后的坯体送入窑炉中,高温烧成,出窑,冷却,磨边、检测入库,得陶瓷成品。其中,所述步骤(5)的烧成温度为1160℃-1180℃,时间为70-90min。
78.对比例1-3(工艺比较)
79.对比例1
80.与实施例1相比,对比例1的区别在于步骤(4)施金丝绒基釉方式采用现有喷釉方式,将金丝绒基釉喷洒到图案层表面,形成单一一层金丝绒釉层;所述金丝绒釉加水调整至比重1.9,流速为32,施釉量88g。
81.对比例2
82.与实施例1相比,对比例2的区别在于第二道金丝绒釉的淋釉方式采用现有技术中的半弧形淋釉器。
83.对比例3
84.与实施例1相比,对比例3的区别在于将实施案例1的第一道金丝绒釉改为常规花釉(常规保护釉),防止油水互相排斥,直接用印油添加剂。
85.实施例2-4及对比例4(金丝绒基釉的配方比较)
86.与实施例1相比,实施例2-4及对比例4中所采用坯体的配方相同,底釉的配方相同,工艺参数相同,区别在于金丝绒基釉的配方不同,具体参见表1。
87.表1:实施例1-4及对比例4金丝绒效果釉原料成分表
[0088][0089][0090]
其中,上述金丝绒效果釉原料中的化学成分组成具体详见表2:
[0091]
表2:实施例1-4及对比例4金丝绒效果釉化学成分表
[0092][0093]
效果评价及性能检测
[0094]
1.陶瓷岩板性能测试
[0095]
评分标准:10分为满分,分值越高表示效果越理想。
[0096]
发色以图案显色情况为评判标准,不偏色为效果最佳,
[0097]
砖型达到企业标准为最佳,
[0098]
表面细腻度以手的触感为准,柔、细、滑为最佳;光泽度哑光为最佳,
[0099]
防污性能以油性笔印迹擦拭结果为评判标准,擦拭得越干净得分越高。
[0100]
表3:实施例1-4及对比例4的陶瓷岩板性能测试表
[0101][0102]
在本发明中,解决淋釉工艺中“分叉”导致陶瓷岩板因为规格大,其平整度、光泽度、细腻度难以控制的技术问题,其关键在于通过控制两道金丝釉料的施布、金丝绒基釉比
重的控制、光滑的线性施釉管的设计等因素共同作用;
[0103]
本工艺设计两道金丝釉料施布,第一道金丝绒基釉的作用有两方面,一方面在于对喷墨图案起到保护作用,另一方面在于提高与第二道金丝绒基釉的结合度与适配度,起到承上启下的作用。第二道金丝绒基釉的作用一方面增加釉层厚度,另一方面通过调整第二道金丝绒基釉配方的高温粘度、高温流动性以及比重大小,以提高釉面平整度、光泽度、细腻度,减少水波纹。本发明实施例1为最佳的实施例,其制得的金丝绒质感陶瓷岩板的平整度、光泽度、细腻度优异,如图1所示。
[0104]
从对比例1可知,底釉和金丝绒基釉均采用现有的喷涂方式喷涂,其砖面的平整度、光泽度、细腻度仍然不能达到最优的效果。
[0105]
从对比例2可知,相比现有的半弧形施釉设备,本发明采用光滑的线性施釉管直接安装在原来的施釉设备上,使同一施釉面上的釉料分布更为均匀,不开叉,提高釉面平整度、光泽度、细腻度;且线性施釉管代替半弧形施釉器,仅仅改进施釉器该部件,设备改装成本低。
[0106]
从对比例3可知,第一道金丝绒釉改为常规花釉(常规保护釉),防止油水互相排斥,直接用印油添加剂,容易造成釉面缩釉和剥离。
[0107]
从实施例2-4以及对比例4可知,本发明金丝绒基釉配方中锶比钡更细腻更哑光,排气效果越好,底层气泡少;钙容易析晶,影响发色,图案容易偏青,偏黄;镁易发红、发蒙,釉层透感不佳,通过调整锶、钙、镁的比例寻求最佳的搭配比例,从而同时满足发色和釉面效果的要求。霞石的主要作用是调整和控制坯釉膨胀系数,调整砖型,其效果比钠长石更佳。所以得出实施案例1的综合效果最佳。而对比例4在于突出实施案例中金丝绒效果釉选用碳酸锶和霞石,而不选用硅灰石和钠长石。对比例4中,选用硅灰石和钠长石其表面细腻度没有实施案例好,釉面效果更粗糙,且砖形偏拱,其原因在于硅灰石的主要成分是cao 48.25%,sio
2 51.75%的始熔温度比碳酸锶高,高温流动性没有碳酸锶好,所以对比案例4的效果没有实施案例1好。
[0108]
2.灯照试验
[0109]
将本发明实施例1的金丝绒质感陶瓷岩板、现有市面常见的柔光砖、亮面砖在相同室内环境下的灯照试验,观察其砖面效果。
[0110]
如图2-4所示,试验结果显示,本发明的金丝绒质感陶瓷岩板其砖面平整度、光泽度、细腻度相对于现有常见的柔光砖、亮面砖优异。
[0111]
上述实施方式仅为本发明的优选实施方式,不能以此来限定本发明保护的范围,本领域的技术人员在本发明的基础上所做的任何非实质性的变化及替换均属于本发明所要求保护的范围。