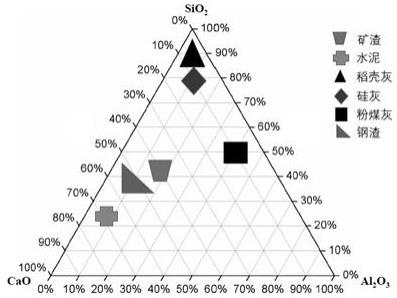
和cao,主要的矿物组成为无定型的玻璃相。国外学者研究了煤气化残渣掺入水泥和石灰后水化产物的结构特征和组成,cgr是具有火山灰活性矿物,可以作为碱激发胶凝材料的前驱体。
6.如何将钢渣、钢铁尘泥、赤泥、煤气化残渣进行有效利用,变废为宝,大大减轻环境污染,同时,还能实现重大的经济效益和社会效益,这一技术难题亟待人们去解决。
技术实现要素:
7.针对相关技术中的上述技术问题,本发明提出一种基于钢铁尘泥和赤泥的改性钢渣及其制备方法和应用,能够克服现有技术的上述不足。
8.为实现上述技术目的,本发明的技术方案是这样实现的:一种基于钢铁尘泥和赤泥的改性钢渣,其特征在于,包括钢渣和复合改性剂,所述复合改性剂包括煤气化残渣、赤泥和钢铁尘泥,所述钢渣和复合改性剂的质量比为65~75:25~35,所述复合改性剂中煤气化残渣、赤泥和钢铁尘泥的质量比为1~2:2~3:3~4。
9.进一步的,所述钢渣中各组分的质量百分比为sio210~20%,al2o
3 1~7%,fe2o
3 2~33%,mgo 3~12%,cao 30~50%,feo 3~15%,na2o 0.01~3%,k2o 0.01~3%,so
3 0.26%, p2o
5 1~6%,所述煤气残渣中各组分的质量百分比为sio
2 30~60%,al2o
3 14~21%,fe2o
3 12~24%,mgo 2~6%,cao 8~20%,k2o 1~3%,na2o 1~3%,so
3 0.1~2%,p2o
5 0.01~1%,tio
2 0.1~2%,烧失量10~40%,所述赤泥中各组分的质量百分比为sio
2 5~30%,al2o
3 15~30%,fe2o
3 10~40%,mgo 0.1~2%,cao 10~20%,k2o 0.01~1%,na2o 1~10%,tio
2 1~8%,烧失量9~15%,所述钢铁尘泥中各组分的质量百分比为 sio
2 1~10%,al2o
3 0.1~12%,fe2o
3 20~50%,feo 10~40%,mgo 0.1~12%,cao 0.1~45%,k2o 0.01~6%,na2o 0.01~3%,zno 0.01~5%,c 0.01~20%,cl 0.01~4.5%,so
3 0.01~2%,烧失量9~20%。
10.一种以上所述的改性钢渣的制备方法,其特征在于,包括以下步骤:s1钢渣预处理:钢渣经颚式破碎机破碎1~3mm颗粒后,将颗粒放入碳化箱中碳化40~56h,所述碳化条件为co2浓度15%,温度20
±
1℃,湿度85%
±
1,碳化后的钢渣在105℃烘干12h,而后放入球磨机中球磨,将钢渣粉磨至比表面积100~200 m2/kg;s2煤气化残渣预处理:煤气化残渣经颚式破碎机破碎1~3mm颗粒,将破碎后的煤气化残渣颗粒烘干,将s1中的100~200 m2/kg钢渣和煤气化残渣按比例混合,放入球磨机中粉磨,粉磨至比表面积250~350 m2/kg;s3赤泥预处理:将赤泥堆放晾干,使其含水量小于10~15%,而后在105℃烘干12h,冷却至常温后,采用行星式球磨机进行分散,使物料的比表面积达到400~550 m2/kg;s4钢铁尘泥预处理:将钢铁尘泥堆放阴凉通风处晾干,使其含水量小于10%,然后在105℃烘干12h,冷却至常温后,采用球磨机进行粉磨加工,使物料的比表面积达到350~500 m2/kg;s5球磨混合:将预处理后的钢渣、煤气残渣、赤泥和钢铁尘泥按比例放入行星磨中混合均匀;s6压制成型:将步骤s5得到的干料混合物加入其质量8~11%的水,然后将混合料放入模具,经液压压力机压制成尺寸为φ30 mm
ꢀ×ꢀ
20 mm的球团;s7烧结改性:将步骤s6压制成型后的球团放入加盖刚玉坩埚,再将坩埚置于马弗
炉中,烧结改性;s8鼓风急冷:将步骤s7烧结改性后的钢渣进行鼓风急冷,得到改性钢渣。
11.进一步的,所述s3中赤泥堆放于阴凉晾干,每天搅拌1次,使其含水量为10~15%,所述行星式球磨机分散时间为15~30min,磨机速率为 200r/min。
12.进一步的,所述s4中钢铁尘泥堆放于阴凉晾干,每天搅拌1次,使其含水量小于10%;所述球磨机粉磨时间为15~30min,球磨速率为 48r/min。
13.进一步的,所述s5将预处理后的钢渣、煤气残渣、赤泥和钢铁尘泥按比例放入行星磨中混合均匀,所述行星磨混匀时间为10~20min,磨机速率为 200r/min。
14.进一步的,所述s6中压制成型的压力为10~20 mpa。
15.进一步的,所述s7中,烧结改性为以10℃/ min升至1100~1350℃,保温0.5-3h。
16.一种以上所述的改性钢渣的应用,其特征在于,将改性钢渣经破碎、粉磨,采用干式强磁选铁,得到的产物海绵铁和改性钢渣粉,将海绵铁应用于炼铁行业,改性钢渣粉应用于水泥混凝土的制备。
17.进一步的,所述破碎、粉磨为将改性钢渣用颚式破碎机破碎至1~3mm颗粒,而后采用球磨机进行粉磨,磨细至比表面积400~600 m2/kg,所述磁选机磁选强度为1-3t,磁选机转速为10~30r/min。
18.本发明的有益效果:本发明的基于钢铁尘泥和赤泥的改性钢渣及其制备方法和应用能够解决钢渣、钢铁尘泥、赤泥、煤气化残渣无法有效利用,污染环境的问题,从而达到有效利用钢渣、煤气化残渣、钢铁尘泥和赤泥的同时提升钢渣的胶凝活性、安定性,同时变废为宝,实现废弃物的规模化利用,产生较高的经济价值,实现固体废弃物的绿色可持续发展,节能环保,资源化利用的目的。
附图说明
19.为了更清楚地说明本发明实施例或现有技术中的技术方案,下面将对实施例中所需要使用的附图作简单地介绍,显而易见地,下面描述中的附图仅仅是本发明的一些实施例,对于本领域普通技术人员来讲,在不付出创造性劳动的前提下,还可以根据这些附图获得其他的附图。
20.图1是根据本发明实施例所述的基于钢铁尘泥和赤泥的改性钢渣及其制备方法和应用的钢渣的化学成分图;图2是根据本发明实施例所述的基于钢铁尘泥和赤泥的改性钢渣及其制备方法和应用的实施例2不同保温时间对铁的各项指标影响图;图3是根据本发明实施例所述的基于钢铁尘泥和赤泥的改性钢渣及其制备方法和应用的实施例2不同改性温度对铁的各项指标影响图;图4是根据本发明实施例所述的基于钢铁尘泥和赤泥的改性钢渣及其制备方法和应用的实施例3所制备改性钢渣的sem-eds图一;图5是根据本发明实施例所述的基于钢铁尘泥和赤泥的改性钢渣及其制备方法和应用的实施例3所制备改性钢渣的sem-eds图二;图6是根据本发明实施例所述的基于钢铁尘泥和赤泥的改性钢渣及其制备方法和应用的实施例3所制备改性钢渣的sem-eds图三;
图7是根据本发明实施例所述的基于钢铁尘泥和赤泥的改性钢渣及其制备方法和应用的实施例3所制备改性钢渣的sem-eds图四;图8是根据本发明实施例所述的基于钢铁尘泥和赤泥的改性钢渣及其制备方法和应用的实施例3磁选后海绵铁的sem-eds图一;图9是根据本发明实施例所述的基于钢铁尘泥和赤泥的改性钢渣及其制备方法和应用的实施例3磁选后海绵铁的sem-eds图二;图10是根据本发明实施例所述的基于钢铁尘泥和赤泥的改性钢渣及其制备方法和应用的实施例1-3的改性钢渣与原钢渣的f-cao和f-mgo含量图;图11是根据本发明实施例所述的基于钢铁尘泥和赤泥的改性钢渣及其制备方法和应用的实施例2不同龄期钢渣粉净浆材料的xrd图。
具体实施方式
21.下面将对本发明实施例中的技术方案进行清楚、完整地描述,显然,所描述的实施例仅仅是本发明一部分实施例,而不是全部的实施例。基于本发明中的实施例,本领域普通技术人员所获得的所有其他实施例,都属于本发明保护的范围。
22.为了方便理解本发明的上述技术方案,以下通过具体使用方式上对本发明的上述技术方案进行详细说明。
23.实施例1本发明利用工业固体废弃物改性钢渣,所述改性钢渣包括钢渣和复合改性剂,所述复合改性剂包括煤气化残渣、赤泥和钢铁尘泥组成,所述钢渣和复合改性剂的质量比为65:35;所述复合改性剂中煤气化残渣、赤泥和钢铁尘泥的质量比为1:2.5:3.5。
24.以上所述钢渣中各组分的质量百分比为sio210~20%,al2o31~7%,fe2o32~33%,mgo3~12%,cao30~50%,feo3~15%,na2o0.01~3%,k2o0.01~3%,so30.26%,p2o51~6%,所述煤气残渣中各组分的质量百分比为sio230~60%,al2o314~21%,fe2o312~24%,mgo2~6%,cao8~20%,k2o1~3%,na2o1~3%,so30.1~2%,p2o50.01~1%,tio20.1~2%,烧失量10~40%,所述赤泥中各组分的质量百分比为sio25~30%,al2o315~30%,fe2o310~40%,mgo0.1~2%,cao10~20%,k2o0.01~1%,na2o1~10%,tio21~8%,烧失量9~15%,所述钢铁尘泥中各组分的质量百分比为sio21~10%,al2o30.1~12%,fe2o320~50%,feo10~40%,mgo0.1~12%,cao0.1~45%,k2o0.01~6%,na2o0.01~3%,zno0.01~5%,c0.01~20%,cl0.01~4.5%,so30.01~2%,烧失量9~20%。
25.上述改性钢渣的制备方法,包括以下步骤:s1、钢渣预处理:钢渣经颚式破碎机破碎1~3mm颗粒后,将颗粒放入碳化箱中碳化48h(碳化条件:co2浓度15%,温度20
±
1℃,湿度85%
±
1),碳化后的钢渣烘干12h(烘干条件105℃),而后放入球磨机中(转速48r/min),将钢渣粉磨至比表面积100m2/kg;s2、煤气化残渣预处理:煤气化残渣经颚式破碎机破碎1~3mm颗粒,将破碎后的煤气化残渣颗粒烘干12h(烘干条件105℃)备用;将s1中的100m2/kg钢渣和煤气化残渣按比例混合,放入球磨机中粉磨,粉磨至比表面积250m2/kg;s3、赤泥预处理:将赤泥堆放晾干,使其含水量为10%,而后进行12h烘干处理(烘干条件105℃),以脱除赤泥中的游离水,取出后在干燥空气中冷却,采用行星式球磨机进行分
散,使物料的比表面积达到400m2/kg;s4、钢铁尘泥预处理:将钢铁尘泥堆放阴凉通风处晾干,使其含水量小于10%,然后进行12h烘干处理(烘干条件105℃),以脱除钢铁尘泥中的游离水,取出后在干燥空气中冷却,采用球磨机进行粉磨加工,使物料的比表面积达到350m2/kg;s5、球磨混合:将预处理后的钢渣、煤气残渣、赤泥和钢铁尘泥按比例放入行星磨中混合均匀;s6、压制成型:将步骤s5得到的干料混合物加入其质量8%的水,然后将混合料放入模具,经液压压力机压制成球(球团尺寸φ30mm
×
20mm);s7、烧结改性:将步骤s6压制成型后的球团放入加盖刚玉坩埚(坩埚尺寸φ150mm
×
200mm),再将坩埚置于马弗炉中,烧结改性;s8、鼓风急冷:将步骤s7烧结改性后的钢渣进行鼓风急冷,得到改性钢渣。
26.所述步骤s3中赤泥堆放于阴凉晾干,每天搅拌1次,使其含水量为10%;所述行星式球磨机分散时间为20min,磨机速率为200r/min。
27.所述步骤s4中钢铁尘泥堆放于阴凉晾干,每天搅拌1次,使其含水量小于10%;所述球磨机粉磨时间为20min,球磨速率为48r/min。
28.所述步骤s5将预处理后的钢渣、煤气残渣、赤泥和钢铁尘泥按比例放入行星磨中混合均匀;所述行星磨混匀时间为10min,磨机速率为200r/min。
29.所述步骤s6中,压制成型的压力为10mpa。
30.所述步骤s7中,烧结改性为:以10℃/min升至1200℃,保温1.5h。
31.上述改性钢渣的应用,将步骤s8中改性钢渣经破碎至1~3mm颗粒、粉磨至表面积400m2/kg,采用干式强磁选,得到的产物海绵铁和改性钢渣粉,海绵铁可应用于炼铁行业,改性钢渣粉应用于水泥混凝土的制备。
32.所述磁选机磁选强度为1.5t,磁选机转速为10r/min。
33.实施例2本发明利用工业固体废弃物改性钢渣,所述改性钢渣包括钢渣和复合改性剂,所述复合改性剂包括煤气化残渣、赤泥和钢铁尘泥组成;所述钢渣和复合改性剂的质量比为70:30;所述复合改性剂中煤气化残渣、赤泥和钢铁尘泥的质量比为2:2:3。
34.所述钢渣中各组分的质量百分比为sio210~20%,al2o31~7%,fe2o32~33%,mgo3~12%,cao30~50%,feo3~15%,na2o0.01~3%,k2o0.01~3%,so30.26%,p2o51~6%,所述煤气残渣中各组分的质量百分比为sio230~60%,al2o314~21%,fe2o312~24%,mgo2~6%,cao8~20%,k2o1~3%,na2o1~3%,so30.1~2%,p2o50.01~1%,tio20.1~2%,烧失量10~40%,所述赤泥中各组分的质量百分比为sio25~30%,al2o315~30%,fe2o310~40%,mgo0.1~2%,cao10~20%,k2o0.01~1%,na2o1~10%,tio21~8%,烧失量9~15%,所述钢铁尘泥中各组分的质量百分比为sio21~10%,al2o30.1~12%,fe2o320~50%,feo10~40%,mgo0.1~12%,cao0.1~45%,k2o0.01~6%,na2o0.01~3%,zno0.01~5%,c0.01~20%,cl0.01~4.5%,so30.01~2%,烧失量9~20%。
35.上述改性钢渣的制备方法,包括以下步骤:s1、钢渣预处理:钢渣经颚式破碎机破碎1~3mm颗粒后,将颗粒放入碳化箱中碳化40h(碳化条件:co2浓度15%,温度20
±
1℃,湿度85%
±
1),碳化后的钢渣烘干12h(烘干条件
105℃),而后放入球磨机中(转速48r/min),将钢渣粉磨至比表面积150m2/kg;s2、煤气化残渣预处理:煤气化残渣经颚式破碎机破碎1~3mm颗粒,将破碎后的煤气化残渣颗粒烘干12h(烘干条件105℃)备用;将s1中的150m2/kg钢渣和煤气化残渣按比例混合,放入球磨机中粉磨,粉磨至比表面积300m2/kg;s3、赤泥预处理:将赤泥堆放晾干,使其含水量为12%,而后进行12h烘干处理(烘干条件105℃),以脱除赤泥中的游离水,取出后在干燥空气中冷却,采用行星式球磨机进行分散,使物料的比表面积达到450m2/kg;s4、钢铁尘泥预处理:将钢铁尘泥堆放阴凉通风处晾干,使其含水量小于10%,然后进行12h烘干处理(烘干条件105℃),以脱除钢铁尘泥中的游离水,取出后在干燥空气中冷却,采用球磨机进行粉磨加工,使物料的比表面积达到450m2/kg;s5、球磨混合:将预处理后的钢渣、煤气残渣、赤泥和钢铁尘泥按比例放入行星磨中混合均匀;s6、压制成型:将步骤s5得到的干料混合物加入其质量10%的水,然后将混合料放入模具,经液压压力机压制成球(球团尺寸φ30mm
×
20mm);s7、烧结改性:将步骤s6压制成型后的球团放入加盖刚玉坩埚(坩埚尺寸φ150mm
×
200mm),再将坩埚置于马弗炉中,烧结改性;s8、鼓风急冷:将步骤s7烧结改性后的钢渣进行鼓风急冷,得到改性钢渣;所述步骤s3中赤泥堆放于阴凉晾干,每天搅拌1次,使其含水量为12%;所述行星式球磨机分散时间为30min,磨机速率为200r/min。
36.所述步骤s4中钢铁尘泥堆放于阴凉晾干,每天搅拌1次,使其含水量小于10%;所述球磨机粉磨时间为15min,球磨速率为48r/min。
37.所述步骤s5将预处理后的钢渣、煤气残渣、赤泥和钢铁尘泥按比例放入行星磨中混合均匀;所述行星磨混匀时间为15min,磨机速率为200r/min。
38.所述步骤s6中,压制成型的压力为15mpa。
39.所述步骤s7中,烧结改性为:以10℃/min升至1250℃,保温2h。
40.上述改性钢渣的应用,将步骤s8中改性钢渣经破碎至1~3mm颗粒、粉磨至表面积500m2/kg,采用干式强磁选,得到的产物海绵铁和改性钢渣粉,海绵铁可应用于炼铁行业,改性钢渣粉应用于水泥混凝土的制备。
41.所述磁选机磁选强度为2t,磁选机转速为30r/min。
42.实施例3本发明利用工业固体废弃物改性钢渣,所述改性钢渣包括钢渣和复合改性剂,所述复合改性剂包括煤气化残渣、赤泥和钢铁尘泥组成;所述钢渣和复合改性剂的质量比为75:25;所述复合改性剂中煤气化残渣、赤泥和钢铁尘泥的质量比为1.5:3:4。
43.所述钢渣中各组分的质量百分比为sio210~20%,al2o31~7%,fe2o32~33%,mgo3~12%,cao30~50%,feo3~15%,na2o0.01~3%,k2o0.01~3%,so30.26%,p2o51~6%,所述煤气残渣中各组分的质量百分比为sio230~60%,al2o314~21%,fe2o312~24%,mgo2~6%,cao8~20%,k2o1~3%,na2o1~3%,so30.1~2%,p2o50.01~1%,tio20.1~2%,烧失量10~40%,所述赤泥中各组分的质量百分比为sio25~30%,al2o315~30%,fe2o310~40%,mgo0.1~2%,cao10~20%,k2o0.01~1%,na2o1~10%,tio21~8%,烧失量9~15%,所述钢铁尘泥中各组分的质量百
分比为 sio
2 1~10%,al2o
3 0.1~12%,fe2o
3 20~50%,feo 10~40%,mgo 0.1~12%,cao 0.1~45%,k2o 0.01~6%,na2o 0.01~3%,zno 0.01~5%,c 0.01~20%,cl 0.01~4.5%,so
3 0.01~2%,烧失量9~20%。
44.本发明还包括上述改性钢渣的制备方法,包括以下步骤:上述改性钢渣的制备方法,包括以下步骤:s1、钢渣预处理:钢渣经颚式破碎机破碎1~3mm颗粒后,将颗粒放入碳化箱中碳化56h(碳化条件:co2浓度15%,温度20
±
1℃,湿度85%
±
1),碳化后的钢渣烘干12h(烘干条件105℃),而后放入球磨机中(转速48r/min),将钢渣粉磨至比表面积200 m2/kg;s2、煤气化残渣预处理:煤气化残渣经颚式破碎机破碎1~3mm颗粒,将破碎后的煤气化残渣颗粒烘干12h(烘干条件105℃)备用;将s1中的200 m2/kg钢渣和煤气化残渣按比例混合,放入球磨机中粉磨,粉磨至比表面积350 m2/kg;s3、赤泥预处理:将赤泥堆放晾干,使其含水量为15%,而后进行12h烘干处理(烘干条件105℃),以脱除赤泥中的游离水,取出后在干燥空气中冷却,采用行星式球磨机进行分散,使物料的比表面积达到550 m2/kg;s4、钢铁尘泥预处理:将钢铁尘泥堆放阴凉通风处晾干,使其含水量小于10%,然后进行12h烘干处理(烘干条件105℃),以脱除钢铁尘泥中的游离水,取出后在干燥空气中冷却,采用球磨机进行粉磨加工,使物料的比表面积达到500 m2/kg;s5、球磨混合:将预处理后的钢渣、煤气残渣、赤泥和钢铁尘泥按比例放入行星磨中混合均匀;s6、压制成型:将步骤s5得到的干料混合物加入其质量11%的水,然后将混合料放入模具,经液压压力机压制成球(球团尺寸φ30 mm
ꢀ×ꢀ
20 mm);s7、烧结改性:将步骤s6压制成型后的球团放入加盖刚玉坩埚(坩埚尺寸φ150 mm
ꢀ×ꢀ
200 mm),再将坩埚置于马弗炉中,烧结改性;s8、鼓风急冷:将步骤s7烧结改性后的钢渣进行鼓风急冷,得到改性钢渣。
45.所述步骤s3中赤泥堆放于阴凉晾干,每天搅拌1次,使其含水量为15%;所述行星式球磨机分散时间为15min,磨机速率为 200r/min。
46.所述步骤s4中钢铁尘泥堆放于阴凉晾干,每天搅拌1次,使其含水量小于10%;所述球磨机粉磨时间为30min,球磨速率为 48r/min。
47.所述步骤s5将预处理后的钢渣、煤气残渣、赤泥和钢铁尘泥按比例放入行星磨中混合均匀;所述行星磨混匀时间为20min,磨机速率为 200r/min。
48.所述步骤s6中,压制成型的压力为20 mpa。
49.所述步骤s7中,烧结改性为:以10℃/ min升至1300℃,保温2.5h。
50.上述改性钢渣的应用,将步骤s8中改性钢渣经破碎至1~3mm颗粒、粉磨至表面积600 m2/kg,采用干式强磁选,得到的产物海绵铁和改性钢渣粉,海绵铁可应用于炼铁行业,改性钢渣粉应用于水泥混凝土的制备。
51.所述磁选机磁选强度为3t,磁选机转速为20r/min。
52.本发明中钢渣经碳化后,钢渣的易磨性得到了提高,粉磨功指数平均值提高了10~20mj/t,钢渣的粉磨能耗得到了降低。
53.本发明中煤气残渣符合gb/t 1596-2005《用于水泥和混凝土中的粉煤灰》的s70要
求,密度小于2 .6g/cm3,活性指数7d≥55%、28d≥75%,放射性复合gb 6566中建筑主体材料规定制备要求。细化后的gb/t 1596-2005依据hj 557-2010《固体废物 浸出毒性浸出方法 水平振荡法》测试表明,其8项重金属指标均低于gb/t 14848-2017《地下水质量标准》中的标准限值。
54.本发明所述的钢渣、煤气化残渣混磨,基于粒级与活性双重协同优化效应,利用易磨性相对较好粗颗粒的煤气残渣和较差细颗粒钢渣,形成微球磨效应,由于钢渣含铁量高,容易团聚,粗颗粒煤气残渣形成新的研磨介质,分散钢渣的团聚体,促进钢渣颗粒的比表面积增大和活性的提高,达到颗粒细度和活性的双重协同优化。
55.本发明所述的赤泥为拜耳法赤泥,主要矿物是赤铁矿,含有少量的二氧化硅、钛矿物、勃姆石和硅铝酸钠水合物。依据hj 557-2010《固体废物 浸出毒性浸出方法 水平振荡法》测试表明,其8项重金属指标均低于gb/t 14848-2017《地下水质量标准》中的标准限值。
56.本发明所述的钢铁尘泥由氧化铁皮、高炉瓦斯灰、转炉og泥组成,富含fe、c、zn等有价元素。其中高炉瓦斯灰为灰黑色粉状,铁含量较低,粒度在1mm以下,亲水性差。转炉og泥铁含量较高,亲水性好。氧化铁皮铁含量到,呈灰色略带光泽的细鳞片状,亲水性中等。
57.实验分析:安定性测试。f-cao的测试根据yb/t 140-2009《钢渣化学分析方法》,用乙二醇为萃取剂,以edta络合滴定法测定;f-mgo利用硝酸铵-乙醇作为提取剂测定。
58.重金属测试。根据gb 5085.3-2007《危险废物鉴别标准—浸出毒性鉴别》标准,参照hj 557-2009《固体废物浸出毒性浸出方法水平振荡法》的要求,测试原料中重金属元素cd、zn、pb、ni、cu、as、hg、cr 进行分析。
59.钢渣的胶砂实验。主要研究钢渣的胶凝活性以及复合胶凝材料的水化硬化性能。胶砂试块根据gb/t17671-1999《水泥胶砂强度检验方法(iso法)》制备;使用的40 mm
×
40 mm
×
160 mm的标准试验模,胶砂试块的复合胶凝材料由磨细钢渣粉(410 m2/kg)与磷石膏(350 m2/kg)按9:1比例组成,水灰比(w/c)为0.5,胶砂比为1:3。用水泥胶砂搅拌机搅拌,首先通过30 s的低速搅拌后加入标准砂1 350 g(胶砂比为1:3),当搅拌机搅拌至60 s后再高速搅拌30 s,静停90 s,最后进行60 s的高速搅拌。将搅拌后的砂浆,浇筑到40 mm
×
40 mm
×
160 mm标准试模中,将试模放到振动台上振动成型,然后置于标准条件下(温度20 ℃
±
1 ℃,相对湿度不低于90%)养护24 h后将试模拆除,将拆模后的试块放入bwj-iii型水泥自动养护中(温度20 ℃
±
1 ℃),养护至龄期测定其胶砂强度。
60.钢渣的活性指数。根据gb/t 20491-2006《用于水泥和混凝土的钢渣粉》来测定改性钢渣的活性指数。式为具体计算方式:
ꢀꢀꢀꢀꢀꢀꢀ
(1)式中a—钢渣粉的活性指数(%);r
t
—钢渣试样胶砂相应龄期的强度,单位为兆帕(mpa);r0—对比纯水泥试样胶砂相应龄期的强度,单位为兆帕(mpa)。
61.将实施例1-3制备的改性钢渣分别命名为s1、s2和s3,采用xrd、sem分析改性后钢渣的组成和结构。
62.改性钢渣的保温时间图2为实施例2不同保温时间对铁的各项指标影响。为考察保温时间对改性钢渣回收铁各项指标的影响,设保温时间为变量,保温时间范围选择0.5-3h,改性温度为1250℃,每隔0.5h取样,其他条件如配料比、原料粒度和磨选条件不变。从图2可以看出,随保温时间延长,铁金属化率显著升高,从0.5h的32%提高到2h的88,之后略有降低;铁品位先升高,在2h后降低,整体变化幅度较小,在86%左右;铁回收率逐渐升高,从0.5h的68%提高到2h的92%左右,之后变化基本趋于平缓,在91%左右;硫含量随保温时间延长逐渐下降,但降低幅度有限(0.42%-0.36%)。试验现象发现,保温时间3 h的改性钢渣产物样品表面对比其他几个保温时间的样品呈较明显的褐色,考虑保温时间过长,改性钢渣中的碳消耗,还原气氛无法维持,改性产物受到氧化,导致铁金属化率下降,影响铁回收率无法进一步提高。
63.改性钢渣的改性温度图3为实施例2不同改性温度对铁的各项指标影响。为考察改性温度对改性钢渣回收铁各项指标的影响,设改性温度为变量(1100℃-1350℃),保温时间范围选择2h,每隔0.5h取样,其他条件如配料比、原料粒度和磨选条件不变。从图3可以看出,整体上,改性温度升高对各项指标的影响均是有益的。改性温度从1100 ℃升高到1300 ℃,改性钢渣产物的铁金属化率明显提高,从61%左右提高到92%;所得海绵铁的铁品位和铁回收率同步提高(79.04%-9.03%),铁回收率从80%左右提高到92%左右;硫含量逐渐降低(0.45%-0.27%)。但改性温度在1350 ℃时,铁各项指标变化趋势变小,铁品位小幅降低。结合铁金属化率,对比不同温度下的改性钢渣产物样品外观发现,温度较低时(1100 ℃-1150 ℃),改性钢渣产物样品呈颗粒状,且存在少量未反应的原料颗粒,可解释说明改性反应未完全发生;温度适中时(1200 ℃-1300 ℃),改性钢渣产物样品呈黑色较疏松的结块,内部有孔隙,这种结构比较有利于后续的破碎磨细;温度较高1350 ℃改性钢渣产物形成致密结块,后续破碎磨细较困难,该温度下的改性钢渣产物与后续磨选条件不适宜,部分铁颗粒未充分解离,可能是导致铁品位下降的主要原因。改性钢渣的微观结构图4-7为本发明实施例3经2.5h保温、改性温度1300℃后得到的改性钢渣产物样品,对样品切面进行sem观察,所制备改性钢渣的sem-eds图一、二、三和四,结合eds分析改性钢渣产物的微观结构。图4-7的改性钢渣产物中,灰色区域是渣相,主要元素为ca、si、al(见a点eds图),说明改性钢渣中的含铝硅酸盐引起渣相成分的变化;亮白色区域主要为金属铁相(见b点eds图),主要环形连续分布在靠近内外气孔边缘附近,金属铁相向气孔方向扩散聚集的趋势相似。金属铁相内部出现一定量的暗白色区域,主要元素为fe和s(见c点eds图),这说明改性钢渣产物中,金属铁相生长过程中夹杂含铁硫化物,导致所得海绵铁产品中硫含量显著升高。
64.图8-9为本发明实施例3磁选后海绵铁的sem-eds图一和图二。从图中可以看出,在经过粉磨磁选后的铁颗粒粒度大部分粒度在40 μm左右,铁颗粒表面铁含量较高(见点2 eds图),夹杂的杂质含量较低,以ca、si、o元素为主(见点1 eds图),但杂质与铁颗粒嵌布更紧密,考虑到磨矿的能耗和铁颗粒的延展性,在-0.048 mm约占72%的粒度条件下进一步磨细降低粒度很难继续提高解离效果。磁选后海绵铁的成分分析见表1。
65.改性钢渣的胶凝性能将实施例1-3得到的改性钢渣粉分别命名为s1、s2、s3、原钢渣s0与po 42.5水泥进行胶砂强度对比试验,分析原钢渣及改性钢渣粉的活性指数。钢渣粉的比表面积为400 m2/kg。将原始钢渣粉和改性钢渣粉为分别替代p
·
o 42.5水泥质量分数的30%,混合均匀后,进行水泥胶砂试验,测试胶砂块7 d和28 d抗压强度,并与纯水泥样品c0抗压强度对比,测试结果如表2所示。
66.从表2可以看出,原钢渣的早期强度较低。7 d的抗压强度为26.6 mpa,活性指数为69.1%,后期强度慢慢提高,28 d的抗压强度为37.6 mpa,活性指数为71.8%。与水泥相比,原钢渣的7 d抗折强度低30.9%,抗压强度低28.2%。经高温改性后的钢渣粉与原钢渣相比,其7 d、28 d的抗折强度和抗压强度的都得到了提高,7 d抗折强度增长幅度在9.8~21.6%,28 d抗折强度增长幅度在16.4~23.9%,抗折性能最高的s2试件7 d和28 d抗折强度分别达到6.2 mpa和8.3 mpa,较s0试件提高了21.6%和23.9%。s1~s3胶砂试件的7 d和28 d抗压强度较s0试件增长幅度在9.8~22.6%和9.3~21.0%。经高温改性钢渣粉试件s2的7 d和 28 d抗压强度较s0试件提高了22.6%和21.0%,分别达到32.6 mpa和45.5 mpa,同时其活性指数较原钢渣胶砂试件s0分别提高了22.6%和20.9%,28 d活性指数达到了86.8%,达到gb/t20491-2006《用于水泥和混凝土中的钢渣粉》中一级钢渣粉的活性指数≥80%的技术要求。实验结果表明,高温改性钢渣粉中的胶凝物相较原钢渣显著的提高,进而促进了钢渣胶凝活性的增强。与p
·
o 42.5水泥相比,改性钢渣中的胶凝物相c3s、c2s、c3a的含量还是较低,因此改性钢渣的胶砂抗折强度和抗压强度的测试值相比纯水泥的测试值要低。本发明采用复合改性剂的方法为增强钢渣的胶凝活性,通过选择廉价的高钙废弃物制备复合改性剂,提高体系的ca/si比,可使体系的胶凝性能得到有效的提升。
67.改性钢渣粉的安定性图10为本发明实施例1-3的改性钢渣与原钢渣的f-cao和f-mgo含量图,图中s0为
原钢渣、s1为实施例1制备的改性钢渣、s2为实施例2制备的改性钢渣、s3为实施例3制备的改性钢渣。由图中可见,钢渣在高温改性的过程中,复合改性剂(煤气化残渣、钢铁尘泥和赤泥)能够显著的降低原钢渣中f-mgo和f-cao的含量。改性后钢渣粉s1、s2、s3 中f-cao含量由原钢渣的3.02%分别降低至1.86%、1.33%和1.76%,与原钢渣相比较f-cao下降幅度分别达到38.4%、56.0%和41.7%;同时f-mgo含量由2.31%分别将至2.22%、1.99%和2.08%,下降幅度3.9%、13.9%和10.0%。s2样品中f-mgo含量相比较s1样品中的下降了0.23%,这说明液相中mgo参与了体系的热化学反应。
68.导致钢渣体积不稳定的主要原因是f-cao和f-mgo的水化引起的体积膨胀,利用复合改性剂对钢渣进行高温改性,得到的改性钢渣可较好的消除f-cao和f-mgo导致的体积不稳定。同时钢渣可以直接用于水泥混凝土中,不需要后期再进行陈化处理。高温处理可以促进f-cao和f-mgo与复合改性剂中sio2、al2o3等成分发生热化学反应,从而降低钢渣中f-mgo和f-cao含量。
69.改性钢渣粉净浆材料的物相组成图11为本发明实施例2不同龄期钢渣粉净浆材料的xrd图。xrd显示了净浆试块的主要矿物相为ca(oh)2、c2s和c3s、c-s-h凝胶和aft。c2s和c3s的存在说明了复合胶凝材料体系的不完全水化。图中c-s-h凝胶未显示清晰的衍射峰。随着水化反应的进行,c2s和c3s的衍射峰降低,ca(oh)2衍射峰的强度增加。因为在常温下,c3s与水反应生成的产物是c-h-s凝胶和ca(oh)2晶体。伴随着水化反应的持续进行,c-s-h凝胶的产生量越来越多,最终试样获得了更高的抗压强度。原料体系中的caso4与铝酸盐进一步反应,最终形成了钙矾石(aft),参与胶凝材料强度的发展过程,这进一步加强了强度发展的进程。从图中可以看出,随着水化龄期的延长aft的衍射峰逐渐加强。复合胶凝材料中fe2o3、mgo的衍射峰依然存在,并没有随着水化反应的进行减弱或者消失,说明这些矿物为惰性矿物,不会发生水化反应。为了方便理解本发明的上述技术方案,以下通过具体使用方式上对本发明的上述技术方案进行详细说明。
70.与现有技术相比,本发明具有以下技术效果:1)本发明利用煤气化残渣、赤泥和钢铁尘泥作为复合改性剂对钢渣进行改性,有效利用了钢渣中有价组分的同时,提升了钢渣的胶凝活性、安定性。
71.2)本发明采用碳化工艺,有效的降低了钢渣的粉磨功指数。同时基于粒级与活性双重协同优化效应,将钢渣、煤气化残渣混磨,形成微球磨效应,提高了粉磨效率。
72.3)本发明基于以废治废的思路,使各种废弃物发挥协同利用功效。充分利用煤气化残渣、钢铁尘泥中的残碳作为还原剂,回收钢渣、赤泥、煤气化残渣、钢铁尘泥中的有价金属组分,同时残碳的利用有效降低了焙烧温度,实现了资源的回收利用。
73.4)本发明回收的海绵铁品位可达65~90%,可以作为炼铁原料;5)制备方法易行、工艺流程简单,可以实现废弃物的规模化利用,最终达到环保、节能、资源化利用的目的。
74.综上所述,借助于本发明的上述技术方案,能够解决钢渣、钢铁尘泥、赤泥、煤气化残渣无法有效利用,污染环境的问题,从而达到有效利用钢渣、煤气化残渣、钢铁尘泥和赤泥的同时提升钢渣的胶凝活性、安定性,同时变废为宝,实现废弃物的规模化利用,产生较高的经济价值,实现固体废弃物的绿色可持续发展,节能环保,资源化利用的目的。
75.以上所述仅为本发明的较佳实施例而已,并不用以限制本发明,凡在本发明的精神和原则之内,所作的任何修改、等同替换、改进等,均应包含在本发明的保护范围之内。