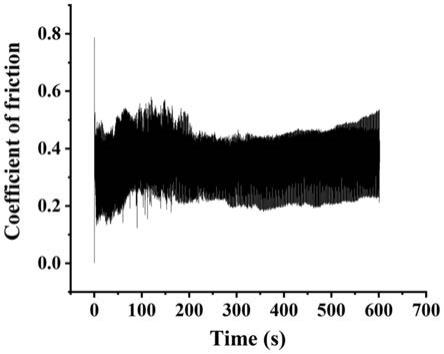
1.本发明属于高温润滑剂和废弃物再利用领域,涉及一种以高炉矿渣为原料制备钢铁成型用高温润滑剂的方法。
背景技术:
2.钢渣是炼钢过程中为了去除钢中杂质而副产的物质;其主要化学成分包括cao、fe2o3、sio2、al2o3、mgo、mno、tio2、p2o5以及feo等。钢渣的产生率为粗钢产量的8%
‑
15%,目前国外发达国家的钢渣利用率较高,如日本的钢渣利用率达到95%以上,德国和美国的钢渣利用率达到98%,而国内钢渣的利用率相对较低,如转炉钢渣的利用率仅为10
‑
20%。国内钢铁企业产生的钢渣不能及时处理,致使大量钢渣占用土地,污染环境;然而钢渣并非不可用的固体废弃物,其中含有大量的渣钢、氧化钙、铁以及氧化镁等可利用组分,以及大量的有益的化学元素,充分利用渣中的有用成分,以提高钢渣的回收效益;我国主要将钢渣用于地基回填、道路铺筑、水泥原料和净水剂等;所以,为使钢铁企业创造经济和环境效益,选择合适的处理工艺和利用途径以便尽可能多地回收钢渣中的金属料,提高尾渣的综合利用率是十分必要和迫切的。
3.钢铁行业中的钢渣占用土对环境钢铁行业中的钢渣废弃物被用于工程和建筑行业,如中国公开专利号为cn111187039a、提出通过固化剂等将高炉矿渣制成复合基层材料用于高速公路等基层材料,中国专利公告号cn101391457b提出了低品位矿渣再利用的方法,将矿渣与石膏粉水泥强化剂等混合制备多孔砖水泥。环境保护以及资源循环利用的要求,需要寻找钢渣更多领域和回收和利用,以实现对钢渣废弃物的有效处理和高值化利用。
技术实现要素:
4.要解决的技术问题
5.为了避免现有技术的不足之处,本发明提出一种以高炉矿渣为原料制备钢铁成型用高温润滑剂的方法,是一种钢渣再利用的方法。
6.为了提高钢渣的高值利用,本发明以钢渣为主要原料,通过水热合成的方式将钢渣转化为具有较低剪切强度的高温润滑剂,并且用于钢铁的热轧过程。此发明一方面可提高钢渣的利用率,减少因堆放和填埋造成的土壤污染和水体污染等,实现钢渣的资源化处理;另一方面可降低外部购入高温润滑剂所造成的成本,有很高的经济效益。
7.技术方案
8.一种以高炉矿渣为原料制备钢铁成型用高温润滑剂的方法,其特征在于步骤如下:
9.步骤1:对低品位尾料钢渣进行磁选,磁选全铁小于10%钢渣;对磁选出的钢渣进行后续筛分出≤5mm钢渣,并进行湿法球磨;
10.步骤2:将钢渣与水按1︰0.3
‑
0.8的重量比加入到球磨机中,掺入以上物料总重千分之二的减水助磨剂,使钢渣料浆浆体细度通过0.05mm方孔筛筛余小于15%时,出磨得到
钢渣料浆;
11.步骤3:对出磨的钢渣料浆进行磁选,使磁选后的钢渣料浆中金属铁的含量<0.3%的钢渣混合料;
12.步骤4:将钢渣混合料与氧化钠、氧化硅、氧化硼和水的质量比6︰2︰1︰1︰10进行混合得混合料a;
13.步骤5:将混合料a用磁力搅拌器搅拌30~50min,超声处理5~10min后倒入聚四氟乙烯内衬高压反应釜中,保持体积填充比为20~60%;
14.步骤6:将密封好的反应釜放入均相水热反应仪中,设置温度参数为200~300℃,反应时间为10~60h,压力为10
‑
30mpa,反应结束后冷却至室温,将最终反应物过滤,干燥即得到高温润滑剂。
15.所述助磨剂组分是:木质磺酸钙与三乙醇胺的质量百分比为4︰1。
16.所述步骤3的磁选采用料浆磁选机。
17.所述氧化钠的粒度为50μm。
18.所述氧化硅的粒度为30μm。
19.所述氧化硼的粒度为80μm。
20.有益效果
21.本发明提出的一种以高炉矿渣为原料制备钢铁成型用高温润滑剂的方法,将低品位尾料钢渣磁选全铁小于10%钢渣,和水球磨掺入减水助磨剂;出磨的钢渣料浆与氧化钠、氧化硅、氧化硼:水进行混合得混合料,放入均相水热反应仪反应,结束后冷却至室温,将最终反应物过滤,干燥即可得到所需高温润滑剂。
22.有益效果具体为:
23.(1)本发明提出了一种用钢铁矿渣为主要原料制备高温润滑剂的方法,制得的高温润滑剂可用于钢铁企业的热轧过程。本发明通过水热反应将筛选的废弃物矿渣粉末通过二次利用,转化为高温润滑剂,使废弃钢渣变废为宝,可降低外部购入高温润滑剂所造成的成本,提高社会经济效益。
24.(2)本发明中的废弃矿渣粉末可以重复利用,转化制备的润滑剂润滑效果较好;本发明制备的润滑剂可以降低生产成本,社会效益明显;同时可以保护生产高温润滑剂所用的自然资源,增加废弃钢渣的高附加值使用途径,促进废弃钢渣循环再利用。
25.(3)矿渣中含有的主要是一些高熔点的氧化物,通过与氧化钠,氧化硼的混合并在高温高压下反应可以形成具有较低熔点的玻璃,玻璃相在高温下变成熔融态,在摩擦界面易于剪切,进而可以降低摩擦系数,提高轧辊的耐磨寿命和轧制效率。
26.(4)此发明一方面可提高钢渣的利用率,减少因堆放和填埋造成的土壤污染和水体污染等,实现钢渣的资源化处理,具有良好的经济、社会和环境效益,符合国家的固体废弃物综合利用的政策导向。
27.本发明润滑剂的检测方法如下:
28.摩擦磨损性能通过umt
‑
tribolab(bruker,germany)摩擦磨损试验机的球
‑
盘模式进行评价,对偶球为高速钢(hss)球,温度为室温
‑
1000℃,载荷5
‑
200n,线速度0.05
‑
0.4m/s,摩擦半径15mm,运行时间10min。
附图说明
29.图1:实施例1中润滑剂的摩擦系数曲线
30.实施例1中所制备的润滑涂层在500℃下的摩擦系数随时间变化曲线。可以看出,在前200秒,摩擦系数有一定的波动,但仍维持在0.4左右,200秒以后,摩擦系数下降至0.37,而后摩擦系数虽有少量升高,仍处于一个较低的值。
31.图2:实施例2中润滑剂的摩擦系数曲线
32.实施例2中所制备的润滑涂层在700℃下的摩擦系数随时间变化曲线。可以看出,摩擦系数虽有一定的波动,但仍维持在0.35左右。较低的摩城系数意味着由矿渣制备的高温润滑剂具有良好的高温润滑性能。
33.图3:实施例3中润滑剂的摩擦系数曲线
34.实施例3中所制备的润滑涂层在900℃下的摩擦系数随时间变化曲线。可以看出,摩擦系数从最初的0.4左右,降低至0.24。从实施例1
‑
3可以看出,随着温度的升高,所制得的润滑剂的摩擦系数降低,说明在高温下,所制得的润滑剂的润滑效果更好,这主要是因为,在较高温度下,所制得的物质易于形成熔体玻璃,在摩擦的界面易于剪切,进而产生润滑效果。
具体实施方式
35.现结合实施例、附图对本发明作进一步描述:
36.本发明实施例的技术方案如下:
37.将低品位尾料钢渣进行筛分、磁选和球磨,将磁选出的全铁含量大于35%的钢渣返回钢铁企业进行冶金再利用,磁选后的全铁小于10%钢渣,继续进行后续筛分出≤5mm钢渣,筛分出的≤5mm的钢渣进行湿法球磨,钢渣和水按1:(0.3
‑
0.8)的重量比加入到球磨机中,掺入以上物料总重千分之二的减水助磨剂,使钢渣料浆浆体细度通过0.05mm方孔筛筛余小于15%时,出磨;
38.所述助磨剂组分是:木质磺酸钙和三乙醇胺;质量百分比为:4:1
39.出磨的钢渣料浆经料浆磁选机进行磁选,使磁选后的钢渣料浆中金属铁的含量<0.3%;
40.将钢渣混合料与氧化钠(粒度50μm)、氧化硅(粒度30μm)、氧化硼(粒度80μm):水按质量比6:2:1:1:10进行混合得混合料a。
41.将混合料a用磁力搅拌器搅拌30~50min,超声处理5~10min。将混合均匀的溶液a倒入聚四氟乙烯内衬高压反应釜中,保持体积填充比20~60%之间。
42.将密封好的反应釜放入均相水热反应仪中,设置温度参数为200~300℃,反应时间为10~60h,压力为10
‑
30mpa,反应结束后冷却至室温,将最终反应物过滤,干燥即可得到所需高温润滑剂。
43.具体实施例:
44.实施例1:
45.将低品位尾料钢渣进行筛分、磁选和球磨,将磁选后的全铁小于10%钢渣,继续进行后续筛分出≤5mm钢渣,将筛分出的≤5mm的钢渣进行湿法球磨,钢渣和水按1:0.5的重量比加入到球磨机中,掺入以上物料总重千分之二的减水助磨剂(木质磺酸钙和三乙醇胺的
质量百分比为:4:1),使钢渣料浆浆体细度通过0.05mm方孔筛筛余小于15%时,出磨;
46.出磨的钢渣料浆经料浆磁选机进行磁选,使磁选后的钢渣料浆中金属铁的含量<0.3%;
47.将钢渣混合料与氧化钠(粒度50μm)、氧化硅(粒度30μm)、氧化硼(粒度80μm):水按质量比6:2:1:1:10进行混合得混合料a。
48.将混合料a用磁力搅拌器搅拌30min,超声处理10min。将混合均匀的溶液a倒入聚四氟乙烯内衬高压反应釜中,保持体积填充比30%。
49.将密封好的反应釜放入均相水热反应仪中,设置温度参数为200℃,反应时间为30h,压力为25mpa,反应结束后冷却至室温,将最终反应物过滤,干燥即可得到所需高温润滑剂。
50.将制备好的润滑剂喷涂在316不锈钢上形成厚度为60μm左右的润滑涂层,而后用umt
‑
tribolab(bruker,germany)评估润滑剂/涂层的润滑摩擦磨损性能。对偶球为高速钢(hss)球,载荷10n,线速度0.1m/s,摩擦半径10mm,运行时间10min,umt的升温速率为30℃/min,实验温度500℃
51.所述高温润滑剂的摩擦系数较小,0.37,且数据稳定。相比于无润滑条件,所诉润滑剂可以降低摩擦系数60%以上。摩擦系数曲线如附图1所示
52.实施例2:
53.将低品位尾料钢渣进行筛分、磁选和球磨,将磁选后的全铁小于10%钢渣,继续进行后续筛分出≤5mm钢渣,将筛分出的≤5mm的钢渣进行湿法球磨,钢渣和水按1:0.5的重量比加入到球磨机中,掺入以上物料总重千分之二的减水助磨剂(木质磺酸钙和三乙醇胺的质量百分比为:4:1),使钢渣料浆浆体细度通过0.05mm方孔筛筛余小于15%时,出磨;
54.出磨的钢渣料浆经料浆磁选机进行磁选,使磁选后的钢渣料浆中金属铁的含量<0.3%;
55.将钢渣混合料与氧化钠(粒度50μm)、氧化硅(粒度30μm)、氧化硼(粒度80μm):水按质量比6:2:1:1:10进行混合得混合料a。
56.将混合料a用磁力搅拌器搅拌30min,超声处理10min。将混合均匀的溶液a倒入聚四氟乙烯内衬高压反应釜中,保持体积填充比30%。
57.将密封好的反应釜放入均相水热反应仪中,设置温度参数为200℃,反应时间为30h,压力为25mpa,反应结束后冷却至室温,将最终反应物过滤,干燥即可得到所需高温润滑剂。
58.将制备好的润滑剂喷涂在316不锈钢上形成厚度为60μm左右的润滑涂层,而后用umt
‑
tribolab(bruker,germany)评估润滑剂/涂层的润滑摩擦磨损性能。对偶球为高速钢(hss)球,载荷10n,线速度0.1m/s,摩擦半径10mm,运行时间10min,umt的升温速率为30℃/min,实验温度700℃
59.所述高温润滑剂的摩擦系数较小,0.35,且数据稳定。相比于无润滑条件,所诉润滑剂可以降低摩擦系数65%以上。摩擦系数曲线如附图2所示
60.实施例3:
61.将低品位尾料钢渣进行筛分、磁选和球磨,将磁选后的全铁小于10%钢渣,继续进行后续筛分出≤5mm钢渣,将筛分出的≤5mm的钢渣进行湿法球磨,钢渣和水按1:0.5的重量
比加入到球磨机中,掺入以上物料总重千分之二的减水助磨剂(木质磺酸钙和三乙醇胺的质量百分比为:4:1),使钢渣料浆浆体细度通过0.05mm方孔筛筛余小于15%时,出磨;
62.出磨的钢渣料浆经料浆磁选机进行磁选,使磁选后的钢渣料浆中金属铁的含量<0.3%;
63.将钢渣混合料与氧化钠(粒度50μm)、氧化硅(粒度30μm)、氧化硼(粒度80μm):水按质量比6:2:1:1:10进行混合得混合料a。
64.将混合料a用磁力搅拌器搅拌30min,超声处理10min。将混合均匀的溶液a倒入聚四氟乙烯内衬高压反应釜中,保持体积填充比30%。
65.将密封好的反应釜放入均相水热反应仪中,设置温度参数为200℃,反应时间为30h,压力为25mpa,反应结束后冷却至室温,将最终反应物过滤,干燥即可得到所需高温润滑剂。
66.将制备好的润滑剂喷涂在316不锈钢上形成厚度为60μm左右的润滑涂层,而后用umt
‑
tribolab(bruker,germany)评估润滑剂/涂层的摩擦磨损性能。对偶球为高速钢(hss)球,载荷10n,线速度0.1m/s,摩擦半径10mm,运行时间10min,umt的升温速率为30℃/min,实验温度900℃
67.所述高温润滑剂的摩擦系数较小,0.24,且数据稳定。相比于无润滑条件,所诉润滑剂可以降低摩擦系数50%以上。摩擦系数曲线如附图3所示。