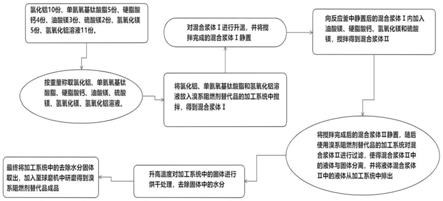
1.本发明涉及阻燃剂领域,更具体的说是一种溴系阻燃剂替代品生产制备方法。
背景技术:
2.溴系阻燃剂分解温度大多在200℃-300℃左右,与各种高聚物的分解温度相匹配,因此能在最佳时刻于气相及凝聚相同时起到阻燃作用,有添加量最小,效果最好的美称,但溴系阻燃剂在它们阻燃高聚物在燃烧时会生成较多的烟、腐蚀性气体和有毒气体,且使被阻燃基材的抗紫外线稳定性降低,故需要一种同样拥有阻燃效果的溴系阻燃剂替代品。
技术实现要素:
3.为克服现有技术的不足,本发明提供一种溴系阻燃剂替代品生产制备方法,其有益效果为本发明可以制作出同样拥有阻燃效果且不会产生有毒气体的溴系阻燃剂替代品。
4.一种溴系阻燃剂替代品生产制备方法,包括以下步骤:
5.(a)按重量称取原料,称取氯化铝10-12份、单氨氧基钛酸脂3-7份、硬脂酸钙2-5份、油酸镁1-5份、硫酸镁2-4份、氢氧化镁5-7份、氢氧化铝溶液8-12份;
6.(b)将氯化铝、单氨氧基钛酸脂和氢氧化铝溶液放入溴系阻燃剂替代品的加工系统中,以搅拌速度为400-650r/min温度为25-35℃的环境条件下开始搅拌,得到混合浆体ⅰ;
7.(c)在温度为55-65℃的环境下,将搅拌完成的混合溶液ⅰ静置0.5-1h;
8.(d)向反应釜中静置后的混合溶液ⅰ内加入油酸镁、硬脂酸钙、氢氧化镁和硫酸镁,以550-750r/min的搅拌速度搅拌得到混合浆体ⅱ;
9.(e)将搅拌完成后的混合浆体ⅱ静置1-1.5h,随后使用溴系阻燃剂替代品的加工系统对混合浆体ⅱ进行过滤,使得混合浆体ⅱ中的液体与固体分离,并将液体混合浆体ⅱ中的液体从加工系统中排出;
10.(f)在80-100℃的温度条件下对加工系统中的固体进行烘干处理,去除固体中的水分。
11.(g)最终将加工系统中的去除水分固体取出,加入至球磨机中研磨1-1.5h 得到溴系阻燃剂替代品成品。
12.优选地,所述步骤(d)中在进行搅拌时处在40-55℃的环境下。
13.优选地,所述步骤(d)中加入油酸镁、硬脂酸钙、氢氧化镁和硫酸镁时,先加入三分之一重量的油酸镁、硬脂酸钙、氢氧化镁和硫酸镁进行搅拌,再依次加入剩余的三分之二重量的上述物料。
14.优选地,每次加入三分之一重量的油酸镁、硬脂酸钙、氢氧化镁和硫酸镁后均以550-750r/min的搅拌速度搅拌0.5h。
15.优选地,所述步骤(e)中在45-60℃的环境下对混合浆体ⅱ进行静置。
附图说明
16.下面结合附图和具体实施方法对本发明做进一步详细的说明。
17.图1为实施例1的流程图;
18.图2为实施例2的流程图;
19.图3为实施例3的流程图;
20.图4为实施例4的流程图;
21.图5为溴系阻燃剂替代品的加工系统的结构示意图一;
22.图6为溴系阻燃剂替代品的加工系统的结构示意图二;
23.图7为连接部的结构示意图;
24.图8为加工部的结构示意图;
25.图9为驱动部的结构示意图;
26.图10为驱动部的局部放大示结构意图;
27.图11为温控部的结构示意图;
28.图12为配合部的局部放大结构示意图。
具体实施方式
29.实施例1:
30.(a)按重量称取原料,称取氯化铝10份、单氨氧基钛酸脂5份、硬脂酸钙4份、油酸镁3份、硫酸镁2份、氢氧化镁5份、氢氧化铝溶液11份;;
31.(b)将氯化铝、单氨氧基钛酸脂和氢氧化铝溶液放入溴系阻燃剂替代品的加工系统中,以搅拌速度为450r/min温度为28℃的环境条件下开始搅拌,搅拌 1h得到混合浆体ⅰ;
32.(c)在温度为55℃的环境下,将搅拌完成的混合溶液ⅰ静置0.5h;
33.(d)向反应釜中静置后的混合溶液ⅰ内先加入三分之一重量的油酸镁、硬脂酸钙、氢氧化镁和硫酸镁,以550r/min的搅拌速度温度为40℃的条件下搅拌 0.5h,再依次加入剩余的三分之二重量的油酸镁、硬脂酸钙、氢氧化镁和硫酸镁,每次加入物料后均以550r/min的搅拌速度温度为40℃的条件下搅拌0.5h,得到混合浆体ⅱ;
34.(e)将搅拌完成后的混合浆体ⅱ在45℃的环境下静置1.2h,随后使用溴系阻燃剂替代品的加工系统对混合浆体ⅱ进行过滤,使得混合浆体ⅱ中的液体与固体分离,并将液体混合浆体ⅱ中的液体从加工系统中排出;
35.(f)在85℃的温度条件下对加工系统中的固体进行烘干处理,去除固体中的水分。
36.(g)最终将加工系统中的去除水分固体取出,加入至球磨机中研磨1h得到溴系阻燃剂替代品成品。
37.使用本制备方法能够制作出可替代溴系阻燃剂的同样具备阻燃效果的阻燃剂成品,同时不会产生较多的烟、腐蚀性气体和有毒气体,进而对救援人员和火灾中的伤员进行一定程度的保护作用。
38.实施例2:
39.(a)按重量称取原料,称取氯化铝10份、单氨氧基钛酸脂4份、硬脂酸钙2份、油酸镁3份、硫酸镁5份、氢氧化镁5份、氢氧化铝溶液9份;;
40.(b)将氯化铝、单氨氧基钛酸脂和氢氧化铝溶液放入溴系阻燃剂替代品的加工系
统中,以搅拌速度为500r/min温度为30℃的环境条件下开始搅拌,搅拌 1.5h得到混合浆体ⅰ;
41.(c)在温度为60℃的环境下,将搅拌完成的混合溶液ⅰ静置0.5h;
42.(d)向反应釜中静置后的混合溶液ⅰ内先加入三分之一重量的油酸镁、硬脂酸钙、氢氧化镁和硫酸镁,以600r/min的搅拌速度温度为45℃的条件下搅拌 0.5h,再依次加入剩余的三分之二重量的油酸镁、硬脂酸钙、氢氧化镁和硫酸镁,每次加入物料后均以650r/min的搅拌速度温度为45℃的条件下搅拌0.5h,得到混合浆体ⅱ;
43.(e)将搅拌完成后的混合浆体ⅱ在50℃的环境下静置1.3h,随后使用溴系阻燃剂替代品的加工系统对混合浆体ⅱ进行过滤,使得混合浆体ⅱ中的液体与固体分离,并将液体混合浆体ⅱ中的液体从加工系统中排出;
44.(f)在90℃的温度条件下对加工系统中的固体进行烘干处理,去除固体中的水分。
45.(g)最终将加工系统中的去除水分固体取出,加入至球磨机中研磨1.2h 得到溴系阻燃剂替代品成品。
46.实施例3:
47.(a)按重量称取原料,称取氯化铝11份、单氨氧基钛酸脂6份、硬脂酸钙5份、油酸镁4份、硫酸镁3份、氢氧化镁7份、氢氧化铝溶液10份;;
48.(b)将氯化铝、单氨氧基钛酸脂和氢氧化铝溶液放入溴系阻燃剂替代品的加工系统中,以搅拌速度为550r/min温度为30℃的环境条件下开始搅拌,搅拌 1.2h得到混合浆体ⅰ;
49.(c)在温度为60℃的环境下,将搅拌完成的混合溶液ⅰ静置0.5h;
50.(d)向反应釜中静置后的混合溶液ⅰ内先加入三分之一重量的油酸镁、硬脂酸钙、氢氧化镁和硫酸镁,以575r/min的搅拌速度温度为50℃的条件下搅拌0.5h,再依次加入剩余的三分之二重量的油酸镁、硬脂酸钙、氢氧化镁和硫酸镁,每次加入物料后均以640r/min的搅拌速度温度为52℃的条件下搅拌0.5h,得到混合浆体ⅱ;
51.(e)将搅拌完成后的混合浆体ⅱ在48℃的环境下静置1.4h,随后使用溴系阻燃剂替代品的加工系统对混合浆体ⅱ进行过滤,使得混合浆体ⅱ中的液体与固体分离,并将液体混合浆体ⅱ中的液体从加工系统中排出;
52.(f)在95℃的温度条件下对加工系统中的固体进行烘干处理,去除固体中的水分。
53.(g)最终将加工系统中的去除水分固体取出,加入至球磨机中研磨1.4h 得到溴系阻燃剂替代品成品。
54.实施例4:
55.(a)按重量称取原料,称取氯化铝12份、单氨氧基钛酸脂7份、硬脂酸钙4份、油酸镁1份、硫酸镁4份、氢氧化镁7份、氢氧化铝溶液12份;;
56.(b)将氯化铝、单氨氧基钛酸脂和氢氧化铝溶液放入溴系阻燃剂替代品的加工系统中,以搅拌速度为600r/min温度为32℃的环境条件下开始搅拌,搅拌 1.8h得到混合浆体ⅰ;
57.(c)在温度为63℃的环境下,将搅拌完成的混合溶液ⅰ静置0.5h;
58.(d)向反应釜中静置后的混合溶液ⅰ内先加入三分之一重量的油酸镁、硬脂酸钙、氢氧化镁和硫酸镁,以700r/min的搅拌速度温度为55℃的条件下搅拌0.5h,再依次加入剩
余的三分之二重量的油酸镁、硬脂酸钙、氢氧化镁和硫酸镁,每次加入物料后均以725r/min的搅拌速度温度为55℃的条件下搅拌 0.5h,得到混合浆体ⅱ;
59.(e)将搅拌完成后的混合浆体ⅱ在56℃的环境下静置1.5h,随后使用溴系阻燃剂替代品的加工系统对混合浆体ⅱ进行过滤,使得混合浆体ⅱ中的液体与固体分离,并将液体混合浆体ⅱ中的液体从加工系统中排出;
60.(f)在95℃的温度条件下对加工系统中的固体进行烘干处理,去除固体中的水分。
61.(g)最终将加工系统中的去除水分固体取出,加入至球磨机中研磨1.5h 得到溴系阻燃剂替代品成品。
62.如图5-12所示,所述步骤f中使用的加工系统包括加工部101、滤网102、中轴201、温控部103和搅拌浆301,滤网102设置在加工部101内,多个温控部103均设置在加工部101内,中轴201能够沿着加工部101竖直方向上下运动,中轴201能够绕着以自身圆心转动,中轴201上设置有多个搅拌浆301,加工部101底部设置有开口,开口处设置有控制阀。
63.在将物料加入至加工部101后操作中轴201绕着自身圆心为轴转动,进而使得连接在中轴201上的多个搅拌浆301跟随中轴201转动,进而使得多个搅拌浆301完成对物料的搅拌任务,同时多个温控部103为可控热板,工作人员可通过调节多个温控部103散发出的热量从而调节加工部101内部的温度,进而实现本制备方法中的多种温度需求,同时工作人员可在操作中轴201绕着自身圆心为轴转动的同时,操作中轴201沿着加工部101竖直方向上下运动,进而使得多个搅拌浆301跟随中轴201上下移动,进而使得多个搅拌浆301对物料进行全面搅拌,使得各个成分混合均匀,进而加快制备效率,工作人员可将控制阀打开,从而将混合浆体ⅱ中的液体排出,使得混合浆体ⅱ中的液体与固体分离,便于后续对混合浆体ⅱ中的固体进行烘干操作的进行。
64.所述步骤f中使用的加工系统还包括连接部305、滑动部306、驱动部402 和滑槽403,连接部305上转动连接有多个搅拌浆301,多个搅拌浆301上分别固定连接有多个滑动部306,中轴201上滑动连接有驱动部402,多个滑槽403 均固定连接在驱动部402上,多个滑动部306能够被多个滑槽403拨动,在多个滑动部306未被拨动时多个搅拌浆301处于倾斜姿态。
65.在工作人员将控制阀打开,从而将混合浆体ⅱ中的液体排出后,工作人员通过调节多个温控部103发出的热量从而使得加工部101内部的温度升高,从而开始对混合浆体ⅱ中的固体进行烘干操作,此时工作人员可操作中轴201向下运动,从而将多个搅拌浆301插入混合浆体ⅱ中的固体中,随后工作人员操作驱动部402在中轴201上向下滑动,进而使得驱动部402上的多个滑槽403 拨动多个滑动部306移动,从而将多个倾斜的搅拌浆301转动至水平姿态,随后再操作中轴201向上运动,进而使得多个水平姿态的搅拌桨盛起部分固体向上运动,当多个水平姿态的搅拌桨抬起至离开混合浆体ⅱ中的固体界面后,操作驱动部402在中轴201上向上滑动,进而使得驱动部402上的多个滑槽403 拨动多个滑动部306移动,从而将多个倾斜的搅拌浆301转回原始姿态,从而使得多个水平姿态的搅拌桨上的固体自然滑下,反复上述操作,从而使得固体能够均匀接收多个温控部103发出的热量,从而加快烘干效率。
66.所述步骤f中使用的加工系统还包括限位杆303和扭簧304,多个限位杆 303均固定连接在多个限位杆303,连接部305与多个搅拌浆301之间设置有多个扭簧304。
67.多个扭簧304能够给多个搅拌浆301施加力,从而使得多个搅拌浆301的在不受外力的条件下始终顶在多个限位杆303上,进而使得多个搅拌浆301处于倾斜姿态,从而便于多个滑槽403驱动多个搅拌浆301转动,完成加快烘干效率的效果。
68.所述步骤f中使用的加工系统还包括盛放槽302,多个盛放槽302均分别设置在多个搅拌浆301上。
69.多个盛放槽302的设置能够便于多个搅拌浆301盛放更多的固体原料,从而进一步加快烘干效率。
70.所述步骤f中使用的加工系统还包括配合部502、圆盘401、液压缸ⅰ501 和限位条404,限位条404设置在圆盘401内,圆盘401内滑动连接有两个配合部502,两个配合部502分别固定连接在两个液压缸ⅰ501的伸缩杆上,两个液压缸ⅰ501能够跟随中轴201同轨迹移动,圆盘401固定连接在驱动部402上。
71.工作人员可通过控制两个液压缸ⅰ501的伸缩杆伸缩,从而操作两个配合部 502上下移动,两个配合部502上下移动从而在限位条404的限制下驱动圆盘 401上下运动,进而使得驱动部402上下运动,从而完成加快烘干效率的目的,圆盘401的设置能够使得两个液压缸ⅰ501能够在不跟随中轴201转动的情况下,驱动驱动部402上下运动,进而便于对驱动部402施加动力源。
72.所述步骤f中使用的加工系统还包括减速电机202、连接杆203和液压缸
ⅱꢀ
204,中轴201转动连接在连接杆203上,电机202固定连接在连接杆203上,中轴201固定连接在电机202的输出轴上,连接杆203固定连接在两个液压缸ⅱ204的伸缩杆上,两个液压缸ⅱ204固接在加工部101上。
73.工作人员可驱动两个液压缸ⅱ204的伸缩杆上下移动,从而驱动连接杆203 上下移动,进而驱动中轴201上下移动,完成加快搅拌效率和烘干效率的目的,电机202转动能够带动中轴201转动,中轴201转动从而完成搅拌工作。