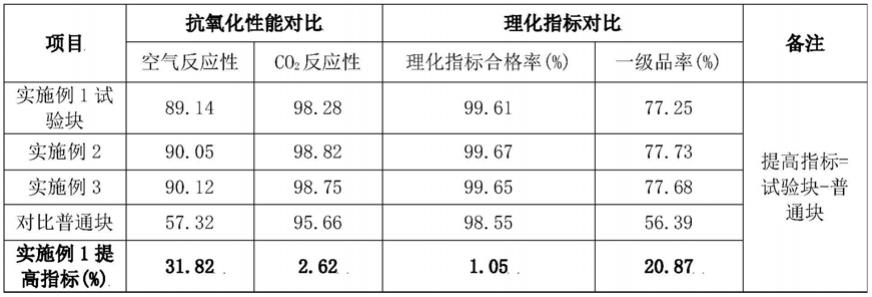
1.本发明涉及铝用炭素产品制备技术领域,特别涉及一种铝用炭素产品高端化新型材料组分以及该铝用炭素产品高端化新型材料的制备方法。
背景技术:
2.铝用阳极是铝电解生产的重要消耗品,电解铝用预焙阳极主要是利用石油焦、沥青等原料混合成型,随着近年来资源相对匮乏,石油焦的品级也不断劣化,最终导致预焙阳极质量也在下降,从而影响下游电解铝的生产成本,降低阳极净耗是降低铝电解生产的有效途径之一。当前,生产铝电解用预焙阳极的原料石油焦品质不断恶化,因而如何降低这一部分消耗已成为电解铝厂降低生产成本关注的重要问题。
3.目前,影响电解铝用预焙阳极质量的关键因素之一是阳极的抗氧化性能差,不但增加阳极消耗,更严重的是在电解槽内形成大量炭渣,选择性氧化是炭渣形成的主要原因,炭渣对电解槽运行危害极大。使用有害杂质(如v、na、ni、ca、fe等)含量低的优质石油焦原料生产阳极,减少有害杂质对氧化反应的催化作用,这是目前工业上常用的方法,但会增加生产成本,且国内优质石油焦原料供应不足。针对国内阳极用石油焦质量不断恶化,有害杂质元素不断升高,致使阳极抗氧化性能变差的现状。为此,本发明提供一种铝用炭素产品高端化新型材料组分及该铝用炭素产品高端化新型材料的制备方法。
技术实现要素:
4.本发明的目的在于克服现有技术的缺陷,提供一种铝用炭素产品高端化新型材料,以石油焦、沥青为主料,再加入一定比例的抗氧化添加剂后经高温焙烧成型,该新型材料制备方法通过预先制备抗氧化添加剂,把抗氧化添加剂加入主料后预压成型,再经过高温焙烧而得,这样可以采用低成本石油焦生产高质量指标的阳极的生产方式,在保证阳极具备抗氧化性能的同时(其空气反应性残余率≥85%,co2反应性残余率≥90%),降低阳极原料生产成本,从源头上减少炭渣的产生。
5.为了实现上述目的,本发明提供的一种铝用炭素产品高端化新型材料,原料组分包括:阳极主料为石油焦和沥青,辅料为抗氧化添加剂,所述抗氧化添加剂在所述阳极主料内添加的重量比例为0.4%~0.6%;
6.所述抗氧化添加剂主要成分按照重量比例为:石墨粉10%~15%、硼酸7%~12%、硬脂酸钠15%~24%、铝灰30%~55%、sic粉22.5%~35%、氧化锆10%~30%和适量纯净水,所述铝灰粒径小于165μm,优选粒径为50μm~150μm,所述铝灰主要为金属铝、铝氧化物、铝氮化物和盐熔剂组成的混合物。
7.进一步的,所述抗氧化添加剂的堆积密度小于1.0g/cm3,外观粒度为粉末状固体;优选的堆积密度为0.5~0.6g/cm3,外观粒度分布200~300目的占90%以上。
8.为了实现上述目的,本发明还提供制备一种铝用炭素产品高端化新型材料的制备方法,具体包括以下步骤:
9.s1原料预混,称取阳极主料石油焦和沥青,所述主料预先经粉碎过筛处理,放入到配料系统内一次混捏均匀并保持一定的主料粒度;
10.s2添加抗氧剂,称取预先制备好的抗氧化添加剂0.4%~0.6%加入到步骤s1配料系统内进行二次混捏糊料预压成型为炭素阳极生块;
11.s3焙烧,将步骤s2所述炭素阳极生块装炉,选择炉况较好的焙烧炉按照焙烧曲线进行单独焙烧形成炭素阳极熟块;
12.s4出炉冷却,将步骤s3所述炭素阳极熟块在焙烧炉内随炉降温冷却后取出递送到阳极组装车间浇铸得到铝用炭素产品新型材料。
13.进一步的,步骤s1所述粉碎过筛处理是指所述石油焦为粒径≤20mm颗粒料和粉料,所述颗粒料包括0.15mm<粒径≤1mm的微颗粒料10%~20%;1mm<粒径≤3mm的细颗粒料30%~40%;3mm<粒径≤6mm的中颗粒料10%~20%以及6mm<粒径≤14mm的粗颗粒料20%~30%;
14.所述沥青为粒径≤1mm煤沥青粉料,所述沥青重量为石油焦的10%~15%;
15.所述一次混捏的时间90min~120min,转速350~400rpm,主料混捏后15mm<粒径≤25mm。
16.进一步的,步骤s2所述二次混捏的时间180min~200min,转速80~100rpm,混捏后所述抗氧化添加剂均匀粘接分布在所述主料颗粒周围,再经过预压成型为均匀的炭素阳极生块。
17.进一步的,步骤s3所述焙烧曲线参数为:焙烧采用15h~20h火焰周期焙烧曲线,升温速率控制在5~10℃/min,火道终温为750℃~850℃保温1h~2h预成型固化以去除水分和有机质;继续原升温速率升温到阳极最终温度达到1080℃~1100℃并保温10h~15h,升温炉室火道负压为-0.1kpa~0.2kpa,火道间温差控制在
±
10℃以内。
18.进一步的,步骤s4所述随炉降温冷却的终了温度40℃~50℃,时间20~30min,保持一定温度取出在大气环境中使得炭素阳极熟块更加均衡,保证了预焙阳极性能的均质性方便浇铸成型。
19.相比于现有技术,本发明具有如下有益效果:
20.1、本发明提供的铝用炭素产品高端化新型材料,石油焦中钒、镍等金属元素的含量不断提高,这些微量元素的存在会起到催化阳极氧化损耗的负面作用,使得阳极空气反应消耗成为铝电解生产中阳极净耗的重要部分,通过对阳极选择性氧化机理的系统研究,为了提高铝用阳极抗氧化性能,通过对在石油焦中加入阳极抗氧化添加剂,研制出了一种铝用阳极抗氧化添加剂,可提高预焙阳极的抗氧化性能,进而实现提高预焙阳极质量,降低预焙阳极成本的目的。使用阳极抗氧化添加剂,有效解决了低品质石油焦生产高质量阳极。添加本阳极抗氧化添加剂后,可以采用低成本石油焦生产高质量指标阳极的生产方式,在保证阳极抗氧化性能的同时(空气反应性残余率≥85%,co2反应性残余率≥90%),降低阳极原料生产成本,从源头上减少炭渣的产生。
21.2、本发明提供的铝用炭素产品高端化新型材料主要作用:在煅后焦质量一定的情况下,炭阳极中加入抗氧化添加剂,可以提高沥青乳化作用,增强沥青对煅后焦颗粒的浸润性能,减少颗粒间和颗粒内部孔隙,降低空气渗透性。同时抗氧化添加剂中含有抑制气体反应的成分,降低反应损失,增强颗粒间的结合力,降低炭阳极在电解使用过程中由于氧化造
成的颗粒脱落,从而提高炭阳极反应残极率。本发明针对新型炭素预焙阳极添加一定比例的抗氧化剂,对电解铝用阳极质量进一步提高。铝用预焙阳极加入抗氧化剂,不会对电解铝电解质影响。铝用预焙阳极加入抗氧化剂不含重金属元素,不会对电解铝原铝质量造成影响。减少阳极掉渣、脱落等,极大的降低电解铝工人的劳动强度。
22.3、本发明提供的铝用炭素产品高端化新型材料及制备方法主要特点:可以用低成本的石油焦生产出高质量的阳极炭块,降低碳素生产成本;大幅度提高阳极抗氧化性,减少电解碳耗、降低电解工劳动强度,稳定电解槽生产参数,提高铝水质量;同时抗氧化添加剂中含有抑制气体反应的成分,降低反应损失,增强颗粒间的结合力,降低炭阳极在电解使用过程中由于氧化造成的颗粒脱落,从而提高炭阳极反应残极率。
23.4、本发明的新型炭素预焙阳极添加抗氧化添加剂,主要表现在“五项常规理化指标”、“空气渗透率”以及“抗氧化性”等指标都有了大幅度的提高,尤其是“抗氧化性”中的“空气反应性和co2反应性残极率”指标分别提高了30%~35%和3%~7%,在铝厂电解槽使用后“残极规整度”、“电解槽电流效率”和“单台电解槽每天铝水产量”比普炭块都有明显优势。增加高硫、高钒石油焦和外购煅后焦采购量,添加0.4%~0.6%比例的抗氧化添加剂后,使炭块“空气和co2反应性残极率”指标同时还能分别满足≥85%和≥90%的目标,从而降低炭块煅后焦原料成本。
具体实施方式
24.为了使本发明的目的、技术方案及优点更加清楚明白,以下结合实施例,对本发明作进一步的详细说明,以使本领域技术人员能够充分理解本发明的技术内容。应理解,以下实施例用于对本发明进行进一步说明,不能理解为对本发明保护范围的限制,本领域的技术人员根据本发明的上述内容作出的一些非本质的改进和调整均属于本发明的保护范围。下述示例具体的工艺参数等也仅是合适范围中的一个示例,即本领域技术人员可以通过本文的说明做合适的范围内选择,而并非要限定于下文示例的具体数值。
25.本发明提供制备一种铝用炭素产品高端化新型材料的制备方法,具体包括以下步骤:(1)原料预混,称取阳极主料石油焦和沥青,主料预先经粉碎过筛处理,放入到配料系统内一次混捏均匀并保持一定的主料粒度;粉碎过筛处理是指石油焦为粒径≤20mm颗粒料和粉料,颗粒料包括0.15mm<粒径≤1mm的微颗粒料10%~20%;1mm<粒径≤3mm的细颗粒料30%~40%;3mm<粒径≤6mm的中颗粒料10%~20%以及6mm<粒径≤14mm的粗颗粒料20%~30%;沥青为粒径≤1mm煤沥青粉料,沥青重量为石油焦的10%~15%;一次混捏的时间90min~120min,转速350~400rpm,主料混捏后主料粒度15mm<粒径≤25mm。
26.(2)添加抗氧剂,称取预先制备好的抗氧化添加剂0.4%~0.6%加入到步骤(1)配料系统内进行二次混捏糊料预压成型为炭素阳极生块;二次混捏的时间180min~200min,转速80~100rpm,二次混捏后抗氧化添加剂均匀粘接分布在主料颗粒周围,再经过预压成型为均匀的炭素阳极生块;抗氧化添加剂主要成分按照重量比例为:石墨粉10%~15%、硼酸7%~12%、硬脂酸钠15%~24%、铝灰30%~55%、sic粉22.5%~35%、氧化锆10%~30%和适量纯净水,铝灰粒径小于165μm,优选粒径为50μm~150μm,铝灰主要为金属铝、铝氧化物、铝氮化物和盐熔剂组成的混合物;抗氧化添加剂的堆积密度小于1.0g/cm3,外观粒度为粉末状固体;优选的堆积密度为0.5~0.6g/cm3,外观粒度分布200~300目的占90%以
上。具体的,抗氧化添加剂的预先制备的制备方法包括如下步骤:1、在配料机中依次加入铝灰、石墨粉、sic粉和氧化锆分别按比例调配,以搅拌转速500~550rpm,搅拌时间10min~15min搅拌均匀。2、在搅拌下加入水相,并搅拌5min~10min混合均匀。3、在搅拌下加入硼酸粘接补强相后,再搅拌下加入硬脂酸钠助剂,继续搅拌30min~35min混合均匀。4、在筛网制粒机中用200~300目的滤网过滤出料形成堆积密度小于1.0g/cm3的粉末状固体,并不断的搅拌以防止抗氧化添加剂过早硬化,不利于与阳极主料混合。该抗氧化添加剂中铝灰、石墨粉在纯净水、硼酸和硬脂酸钠的作用下与sic、zro2快速硬化成型,在焙烧时发生反应,其中sic、zro2晶须能填充残留的少量微孔,提高致密性,有效隔绝预焙阳极与空气的接触,且该涂层在使用过程中与预焙阳极的炭基体紧密结合,不易开裂脱落,与预焙阳极的炭基体粘结性较强,有效保护了预焙阳极。
27.(3)焙烧,将步骤(2)炭素阳极生块装炉,选择炉况较好的焙烧炉按照焙烧曲线进行单独焙烧形成炭素阳极熟块;焙烧曲线参数为:焙烧采用15h~20h火焰周期焙烧曲线,升温速率控制在5~10℃/min,火道终温为750℃~850℃保温1h~2h预成型固化以去除水分和有机质;继续原升温速率升温到阳极最终温度达到1080℃~1100℃并保温10h~15h,升温炉室火道负压为-0.1kpa~0.2kpa,火道间温差控制在
±
10℃以内。
28.(4)出炉冷却,将步骤(3)炭素阳极熟块在焙烧炉内随炉降温冷却后取出递送到阳极组装车间浇铸得到铝用炭素产品新型材料;随炉降温冷却的终了温度40℃~50℃,时间20~30min,保持一定温度取出在大气环境中使得炭素阳极熟块更加均衡,保证了预焙阳极性能的均质性方便浇铸成型。
29.实施例1
30.本发明的铝用炭素产品高端化新型材料的制备方法,预先根据生产需求,并依据抗氧化添加剂的重量比例:石墨粉10%~15%、硼酸7%~12%、硬脂酸钠15%~24%、铝灰30%~55%、sic粉22.5%~35%、氧化锆10%~30%和适量纯净水的预先制备的制备方法进行制备抗氧化添加剂(参见表1的方案1):1、在配料机中依次加入铝灰32.5kg、石墨粉10.5kg、sic粉24.5kg和氧化锆10kg分别按比例调配,以搅拌转速500rpm,搅拌时间12min搅拌均匀。2、在搅拌下加入纯净水15kg,并搅拌10min混合均匀。3、在搅拌下加入硼酸7.5kg粘接补强相后,再搅拌下加入硬脂酸钠15kg助剂,继续搅拌35min混合均匀。4、在筛网制粒机中用250目的滤网过滤出料形成堆积密度小于0.65g/cm3的粉末状固体,并不断的搅拌以防止抗氧化添加剂过早硬化,不利于与阳极主料混合。
31.表1该铝用炭素产品高端化新型材料的制备方法中抗氧化添加剂的组分
32.抗氧化添加剂组分方案1方案2方案3石墨粉10%~15%10.51211硼酸7%~12%7.58.58硬脂酸钠15%~24%151615.5铝灰30%~55%32.53031.5sic粉22.5%~35%24.522.522.5氧化锆10%~30%101111.5纯净水(混合造粒成型)1512.517.5
33.具体的铝用炭素产品高端化新型材料的制备方法,称取阳极主料石油焦和沥青总
量4800kg,辅料抗氧化添加剂重量比例以0.4%计为19.2kg(方案1的抗氧化添加剂)。
34.(1)原料预混,称取阳极主料石油焦和沥青,主料预先经粉碎过筛处理,放入到配料系统内一次混捏均匀并保持一定的主料粒度;粉碎过筛处理是指石油焦为粒径≤20mm颗粒料和粉料,沥青重量为石油焦的12.5%(600kg);一次混捏的时间120min,转速400rpm,主料混捏后主料粒度20mm。
35.(2)添加抗氧剂,称取预先制备好的抗氧化添加剂0.4%(19.2kg)加入到步骤(1)配料系统内进行二次混捏糊料预压成型为炭素阳极生块;二次混捏的时间200min,转速80rpm,二次混捏后抗氧化添加剂均匀粘接分布在主料颗粒周围,再经过预压成型为均匀的炭素阳极生块。
36.(3)焙烧,将步骤(2)炭素阳极生块装炉,选择炉况较好的焙烧炉按照焙烧曲线进行单独焙烧形成炭素阳极熟块;焙烧曲线参数为:焙烧采用15h火焰周期焙烧曲线,升温速率控制在10℃/min,火道终温为850℃保温2h预成型固化以去除水分和有机质;继续原升温速率升温到阳极最终温度达到1100℃并保温13h,升温炉室火道负压为-0.1kpa,火道间温差控制在
±
5℃以内。
37.(4)出炉冷却,将步骤(3)炭素阳极熟块在焙烧炉内随炉降温冷却后取出递送到阳极组装车间浇铸得到铝用炭素产品新型材料;随炉降温冷却的终了温度50℃,时间30min,保持一定温度取出在大气环境中使得炭素阳极熟块更加均衡,保证了预焙阳极性能的均质性方便浇铸成型。
38.实施例2
39.本发明的铝用炭素产品高端化新型材料的制备方法,称取阳极主料石油焦和沥青总量5000kg,辅料抗氧化添加剂重量比例以0.6%计为30kg(方案3的抗氧化添加剂);
40.(1)原料预混,称取阳极主料石油焦和沥青,主料预先经粉碎过筛处理,放入到配料系统内一次混捏均匀并保持一定的主料粒度;粉碎过筛处理是指石油焦为粒径≤20mm颗粒料和粉料,沥青重量为石油焦的15%(750kg);一次混捏的时间110min,转速360rpm,主料混捏后主料粒度25mm。
41.(2)添加抗氧剂,称取预先制备好的抗氧化添加剂0.6%(30kg)加入到步骤(1)配料系统内进行二次混捏糊料预压成型为炭素阳极生块;二次混捏的时间190min,转速100rpm,二次混捏后抗氧化添加剂均匀粘接分布在主料颗粒周围,再经过预压成型为均匀的炭素阳极生块。
42.(3)焙烧,将步骤(2)炭素阳极生块装炉,选择炉况较好的焙烧炉按照焙烧曲线进行单独焙烧形成炭素阳极熟块;焙烧曲线参数为:焙烧采用16h火焰周期焙烧曲线,升温速率控制在5.5℃/min,火道终温为770℃保温2h预成型固化以去除水分和有机质;继续原升温速率升温到阳极最终温度达到1080℃并保温12h,升温炉室火道负压为-0.2kpa,火道间温差控制在
±
2℃以内。
43.(4)出炉冷却,将步骤(3)炭素阳极熟块在焙烧炉内随炉降温冷却后取出递送到阳极组装车间浇铸得到铝用炭素产品新型材料;随炉降温冷却的终了温度50℃,时间30min,保持一定温度取出在大气环境中使得炭素阳极熟块更加均衡,保证了预焙阳极性能的均质性方便浇铸成型。
44.实施例3
45.本发明的铝用炭素产品高端化新型材料的制备方法,称取阳极主料石油焦和沥青总量5200kg,辅料抗氧化添加剂重量比例以0.5%计为26kg(方案2的抗氧化添加剂);
46.(1)原料预混,称取阳极主料石油焦和沥青,主料预先经粉碎过筛处理,放入到配料系统内一次混捏均匀并保持一定的主料粒度;粉碎过筛处理是指石油焦为粒径≤20mm颗粒料和粉料,沥青重量为石油焦的10%(520kg);一次混捏的时间100min,转速380rpm,主料混捏后主料粒度23mm。
47.(2)添加抗氧剂,称取预先制备好的抗氧化添加剂0.5%(26kg)加入到步骤(1)配料系统内进行二次混捏糊料预压成型为炭素阳极生块;二次混捏的时间180min,转速90rpm,二次混捏后抗氧化添加剂均匀粘接分布在主料颗粒周围,再经过预压成型为均匀的炭素阳极生块。
48.(3)焙烧,将步骤(2)炭素阳极生块装炉,选择炉况较好的焙烧炉按照焙烧曲线进行单独焙烧形成炭素阳极熟块;焙烧曲线参数为:焙烧采用18h火焰周期焙烧曲线,升温速率控制在7.5℃/min,火道终温为800℃保温1.5h预成型固化以去除水分和有机质;继续原升温速率升温到阳极最终温度达到1090℃并保温14h,升温炉室火道负压为-0.15kpa,火道间温差控制在
±
8℃以内。
49.(4)出炉冷却,将步骤(3)炭素阳极熟块在焙烧炉内随炉降温冷却后取出递送到阳极组装车间浇铸得到铝用炭素产品新型材料;随炉降温冷却的终了温度45℃,时间28min,保持一定温度取出在大气环境中使得炭素阳极熟块更加均衡,保证了预焙阳极性能的均质性方便浇铸成型。本发明给出三个实施例的铝用炭素产品高端化新型材料性能测试表2所示。
50.表2铝用炭素产品高端化新型材料性能测试结果
[0051][0052]
主要表现在“五项常规理化指标”、“空气渗透率”以及“抗氧化性”等指标都有了大幅度的提高,尤其是“抗氧化性”中的“空气反应性和co2反应性残极率”指标分别提高了30%~35%和3%~7%,在铝厂电解槽使用后“残极规整度”、“电解槽电流效率”和“单台电解槽每天铝水产量”比普炭块都有明显优势。增加高硫、高钒石油焦和外购煅后焦采购量,添加0.4%~0.6%比例的抗氧化添加剂后,使炭块“空气和co2反应性残极率”指标同时还能分别满足≥85%和≥90%的目标,从而降低炭块煅后焦原料成本。
[0053]
需要指出的是,上述较佳实施例仅为说明本发明的技术构思及特点,其目的在于让熟悉此项技术的人士能够了解本发明的内容并据以实施,并不能以此限制本发明的保护范围。凡根据本发明精神实质所作的等效变化或修饰,都应涵盖在本发明的保护范围之内。