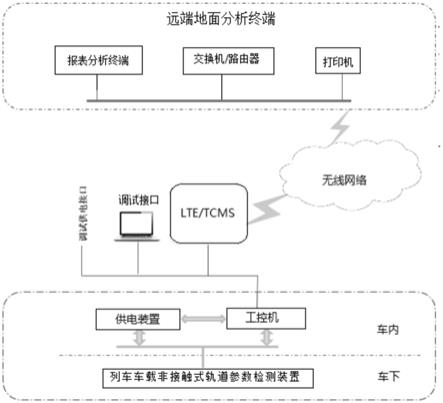
1.本实用新型涉及轨道检测领域,尤其涉及一种列车车载非接触式轨道参数检测装置及系统。
背景技术:
2.轨道的几何参数检测对高速列车组实际运行的安全性起着至关重要的作用。当前轨道参数检测技术一般通过特定的激光位移传感器、加速度传感器和陀螺仪传感器等来检测轨道几何参数变化,但这种方式测量信号在长线传输过程中抗干扰能力弱,导致测量结果精度偏低,误差较大,并且误差校正是根据人的主观经验确定,没有确切的理论基础。
技术实现要素:
3.本实用新型的目的在于提供一种列车车载非接触式轨道参数检测装置,从而解决现有技术中存在的前述问题。
4.为了实现上述目的,本实用新型采用的技术方案如下:
5.一种列车车载非接触式轨道参数检测装置,包括轨检梁箱体、设置在所述轨检梁箱内的激光检测装置、用于传输信号的轨检梁连接器以及用于安装固定轨检梁箱的安装结构,所述安装结构设置在所述轨检梁箱的上方,所述激光检测装置包括惯性包、两个2d激光位移传感器和两个伺服加速度传感器,且所述 2d激光位移传感器和所述伺服加速度传感器分别设置在所述轨检梁箱体的两端,所述惯性包设置在所述轨检梁箱体中部;
6.所述惯性包内设置有采集电路板和陀螺传感器,所述陀螺传感器和所述伺服加速度传感器分别于所述采集电路板相连;所述采集电路板于所述轨检梁连接器相连;
7.所述2d激光位移传感器与所述轨检梁连接器相连。
8.优选的,所述安装结构包括吊环螺母和托装座;所述吊环螺母设置在所述轨检梁箱体两端以用于安装吊环或钢丝绳固定所述轨检梁箱体;所述托装座设置在所述两个吊环螺母之间,用于连接预先焊接在列车底部的工字横梁。
9.优选的,所述2d激光位移传感器包括2d激光面和遮光罩,所述2d激光面和所述遮光罩位于所述轨检梁箱体下方且所述遮光罩位于所述2d激光面上方。
10.优选的,所述连接器采用ip67连接器。
11.本实用新型的另一个目的在于提供一种列车车载非接触式轨道参数检测系统,所述系统包括列车车载非接触式轨道参数检测装置、工控机和供电装置,所述工控机和所述列车车载非接触式轨道参数检测装置均与所述供电装置相连,所述工控机包括数据处理装置和功能控制装置,所述数据处理装置与所述列车车载非接触式轨道参数检测装置的连接器相连,所述数据处理装置接收轨检列车车载非接触式轨道参数检测装置上传的所有数据,所述功能控制装置接收来自所述数据处理装置处理后的数据。
12.优选的,所述功能控制装置包括交换机板卡,所述功能控制装置通过所述交换机板卡与车载网络lte连接。
13.优选的,所述列车车载非接触式轨道参数检测系统还包括远端地面分析终端,所述远端地面分析终端通过所述车载网络lte实现数据传输过程。
14.本实用新型的有益效果是:
15.本实用新型提供了一种车载非接触式轨道检测装置及系统,该装置包括激光位移传感器、加速度传感器和陀螺仪传感器,这三个传感器集成在轨道梁箱体内,能够统一完成各传感器的信号采集过程,将数据传给数据处理装置及时进行处理;也能有效地避免模拟小信号在长线传输过程中带来的干扰问题,使得该系统的信号抗干扰能力更强,误差更小,精度更高。
附图说明
16.图1是实施例1中提供的车载非接触式轨道检测装置立体示意图;
17.图2是实施例2中提供的车载非接触式轨道检测系统的原理框图;
18.图3是采用实施例2中提供的车载非接触式轨道检测系统进行数据传输过程原理图;
19.1是连接器,2是托装座,3是轨检梁箱体,4是吊环螺母,5是遮光罩,6是 2d激光面;
20.图4是采用实施例2中的车载非接触式轨道检测系统进行轨距检测原理图;
21.图5是采用实施例2中的车载非接触式轨道检测系统进行轨道高低不平顺检测原理图;
22.图6是采用实施例2中的车载非接触式轨道检测系统进行轨道水平不平顺检测方法;
23.图7是采用实施例2中的车载非接触式轨道检测系统进行轨道方向不平顺检测原理图;
24.图8是采用实施例2中的车载非接触式轨道检测系统进行钢轨磨耗检测原理图;
25.图9是采用实施例2中的车载非接触式轨道检测系统进行轨道曲率检测原理图;
26.图10是采用实施例2中的车载非接触式轨道检测系统进行三角坑检测原理图。
具体实施方式
27.为了使本实用新型的目的、技术方案及优点更加清楚明白,以下结合附图,对本实用新型进行进一步详细说明。应当理解,此处所描述的具体实施方式仅仅用以解释本实用新型,并不用于限定本实用新型。
28.实施例1
29.本实施例提供了一种列车车载非接触式轨道参数检测装置,如图1所示,包括轨检梁箱体、设置在所述轨检梁箱内的激光检测装置、用于传输信号的轨检梁连接器以及用于安装固定轨检梁箱的安装结构,所述安装结构设置在所述轨检梁箱的上方,所述激光检测装置包括惯性包、两个2d激光位移传感器和两个伺服加速度传感器,且所述2d激光位移传感器和所述伺服加速度传感器分别设置在所述轨检梁箱体的两端,所述惯性包设置在所述轨检梁箱体中部;
30.所述惯性包内设置有采集电路板和陀螺传感器,所述陀螺传感器和所述伺服加速度传感器分别于所述采集电路板相连;所述采集电路板于所述轨检梁连接器相连;
31.所述2d激光位移传感器与所述轨检梁连接器相连。
32.本实施例中采用的所述安装结构包括吊环螺母和托装座;所述吊环螺母设置在所述轨检梁箱体两端以用于安装吊环或钢丝绳固定所述轨检梁箱体;所述托装座设置在所述两个吊环螺母之间,用于连接预先焊接在列车底部的工字横梁。
33.本实施例中的所述2d激光位移传感器包括2d激光面和遮光罩,所述2d激光面和所述遮光罩位于所述轨检梁箱体下方且所述遮光罩位于所述2d激光面上方。
34.本实施例中的所述连接器采用ip67连接器。
35.实施例2
36.本实施例提供一种列车车载非接触式轨道参数检测系统,如图2和图3所示,所述系统包括列车车载非接触式轨道参数检测装置、工控机和供电装置,所述工控机和所述列车车载非接触式轨道参数检测装置均与所述供电装置相连,所述工控机包括数据处理装置和功能控制装置,所述数据处理装置与所述列车车载非接触式轨道参数检测装置的连接器相连,所述数据处理装置接收轨检列车车载非接触式轨道参数检测装置上传的所有数据,所述功能控制装置接收来自所述数据处理装置处理后的数据。
37.本实施例中,所述功能控制装置包括交换机板卡,所述数据控制装置通过所述交换机板卡与车载网络lte连接。
38.本实施例中的所述列车车载非接触式轨道参数检测系统还包括所述远端地面分析终端,所述远端地面分析终端通过所述车载网络lte实现数据传输过程。
39.具体实施过程
40.本研究采用实施例2中的轨道参数检测系统,运用机器视觉、惯性计算等原理实现对轨道几何参数、轨道全断面、车体加速度的在线检测,具体包括以下检测内容:
41.1.轨距检测方法
42.定义:在轨道同一横截面、钢轨顶面以下16mm处、左右两根钢轨之间的最小内侧距离相对于标准轨距值1435mm的偏差。
43.检测原理示意图如图4所示,采用激光三角测距原理,利用2d激光传感器对轨面和内轨腰、轨底进行扫描,运用高速图像处理技术对轮廓曲线进行提取和分析,确定轨距的变化,加上两2d安装的距离,计算合成动态的轨距值,进而得到轨距变化率。
44.2.轨道高低不平顺检测方法
45.定义:轨道高低不平顺是指左右轨顶面纵向起伏变化。
46.对轨道高低不平顺检测原理图如图5所示,采用该装置测得左、右轨检梁的垂向加速度大小,通过两次积分得到相对惯性位移,结合2d测得左右轨检梁上点相对轨面的垂直位移,作差得到轨顶面相对惯性基准的位移。轨检梁惯性包测得整个轨检梁的姿态对数据进行修正补偿(倾角仪测得其与大地的夹角,摇头陀螺测得轨检梁的摇动,侧滚陀螺测得轨检梁的侧向滚动)。最终对数据滤波得到短波,中波,及部分长波。
47.3.轨道水平不平顺检测方法
48.定义:轨道同一横断面内左右钢轨顶面的高度差,检测原理图如图6所示。
49.轨检梁惯性包测得整个轨检梁相对大地平面的角度(倾角仪测得其与大地的夹角,摇头陀螺测得轨检梁的摇动,侧滚陀螺测得轨检梁的侧向滚动)。
50.二维激光测得与轨道顶面的距离,进而得与横梁的夹角。结合上面得到的整个轨
检梁相对大地平面的角度作差得到轨顶面与大地的绝对角度,通过换算得到绝对水平超高值。绝对水平超高值通过转换,过滤超高设计值,得到相对水平值。
51.4.轨道方向不平顺检测方法
52.定义:轨向指钢轨内侧面轨距点沿轨道纵向水平位置的变化,检测原理图如图7所示。
53.轨检梁的横向加速度大小,通过两次积分得到相对惯性位移,结合2d测得左右轨检梁上点相对轨面的横位移,作差得到轨侧面相对惯性基准的位移。轨检梁惯性包测得整个轨检梁的姿态对数据进行修正补偿(倾角仪测得其与大地的夹角,摇头陀螺测得轨检梁的摇动,侧滚陀螺测得轨检梁的侧向滚动)。最终对数据滤波得到短波,中波,及部分长波。
54.5.钢轨磨耗检测方法
55.定义:垂直磨耗:在钢轨顶面宽1/3处的测量值;侧面磨耗:在钢轨踏面(标准断面)下16mm处的测量值,其中钢轨磨耗检测原理图如图8所示。
56.采用全断面廓形技术:运用非接触、数字化、光学图像技术将轨距检测系统中提取的全部轨头轮廓图形与标准轨头轮廓进行对比,提取磨耗检测点位置的变化值就是磨耗值。
57.6.轨道曲率检测方法
58.定义:曲率测量定义为一定弦长的曲线轨道(如30m)对应之园心角θ(度 /30米)。度数大、曲率大、半径小;反之,度数小、曲率小、半径大,曲率检测原理图如图9所示。
59.7.三角坑检测方法
60.定义:三角坑反映了轨顶的平面性。若轨顶abcd四点不在一个平面上,c点到abd三点组成平面的垂直距离h为扭曲,三角坑检测原理图如图10所示。
61.三角坑使车辆产生三点支撑一点悬空,特别是当列车从圆曲线向缓和曲线运行时,由于超高顺坡不良引起的三角坑,易造成轮重减载,发生脱轨掉道事故。
62.三角坑为按水平值一定基长换算得到,对一转向架来说,三角坑基长取 2.5m,对一车体来说,基长取18m,即18m内最大水平的差。
63.通过采用本实用新型公开的上述技术方案,得到了如下有益的效果:
64.本实用新型提供了一种车载非接触式轨道检测装置及系统,该装置包括激光位移传感器、加速度传感器和陀螺仪传感器,这三个传感器集成在轨道梁箱体内,能够统一完成各传感器的信号采集过程,将数据传给数据处理装置及时进行处理;也能有效地避免模拟小信号在长线传输过程中带来的干扰问题,使得该系统的信号抗干扰能力更强,误差更小,精度更高。
65.以上所述仅是本实用新型的优选实施方式,应当指出,对于本技术领域的普通技术人员来说,在不脱离本实用新型原理的前提下,还可以做出若干改进和润饰,这些改进和润饰也应视本实用新型的保护范围。