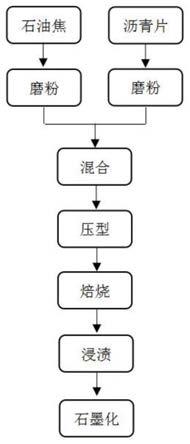
1.本发明涉及石墨制备技术领域,具体为一种短流程制备石墨的方法。
背景技术:
2.石墨材料具有诸多优良性能,被广泛应用在国民经济中各个领域,石墨材料的发展具有很大前景。然而,石墨产业也面临诸多问题:生产流程复杂,耗时长,能耗高。这使得石墨的生产效率降低,成本增加。如何快速节能的生产出产品是石墨产业迫切需要解决的问题。
3.现有的石墨生产其主要工艺流程为原料破碎磨粉、混捏、轧片、二次磨粉、压型、焙烧、浸渍、二次焙烧、石墨化等,焙烧和浸渍一般需要二至三次,公开号为cn102898142b,名称为《一种用于电火花加工的模具石墨材料的制备方法》的发明专利中,就公开了这样的方法,其中焙烧和石墨化作业耗时长,一次焙烧600~800h、二次焙烧490~620h、石墨化150~220h,在实际大批量生产中,从原料到石墨成品,短则3个月,长则半年甚至更久,这大大降低了石墨的生产效率。此外,混捏、浸渍、焙烧、石墨化都是在高温下进行,其中焙烧和石墨化耗时长,温度高,能源消耗较大,随着国家节能降耗的进一步实施,石墨产品发展面临较大挑战;因此,亟需一种短流程制备石墨的方法来解决这个问题。
技术实现要素:
4.本发明的目的在于提供一种短流程制备石墨的方法,以解决石墨制备过程较长、能耗高的问题。
5.为实现上述目的,本发明提供如下技术方案:一种短流程制备石墨的方法,包括以下具体步骤:
6.s1、原料磨粉:分别将煅后石油焦和沥青片磨成细粉并筛分;
7.s2、压型:按粒级以一定比例配置煅后石油焦细粉、沥青片细粉物料,充分混匀后压型;
8.s3、焙烧-浸渍:将压型后的成型生坯在隔绝空气下焙烧,焙烧结束后待冷却至一定温度,焙烧品直接在沥青液中浸渍;
9.s4、石墨化:对浸渍品石墨化处理。
10.在步骤s1中较优的,将煅后石油焦磨成细粉,并筛分为<0.074mm、0.074~0.15mm、0.15~0.5mm、0.5~1.0mm四个粒级的物料。
11.在步骤s1中较优的,采用气流磨将沥青片磨成d50为2~10μm的细粉。
12.在步骤s2中较优的,配置物料具体包括:以重量份数计,分别称取<0.074mm、0.074~0.15mm、0.15~0.5mm、0.5~1.0mm的煅后石油焦细粉30~50、10~30、5~20、0~10份,称取沥青片细粉20~30份。
13.在步骤s2中较优的,压型具体包括:将混匀的物料装入模具中等静压压型,成型压力为160~240mpa,压型时间为10~30min。
14.在步骤s3中较优的,焙烧结束后冷却至250~350℃,直接将焙烧品取出浸渍。
15.在步骤s3中较优的,浸渍温度为200~300℃,浸渍时间2~6h。
16.在步骤s3中较优的,焙烧最高温度为900℃,在400℃以下升温速率为10℃/h,400~700℃,升温速率为5℃/h,700℃以上升温速率为10℃/h。
17.在步骤s4中较优的,石墨化最高温度为3000℃,其中25~800℃阶段升温速率2~10℃/h,800~3000℃升温速率为30~90℃/h。
18.在步骤s4中较优的,石墨化处理前,先待浸渍品冷却,并刮去其表面的沥青。
19.与现有技术相比,本发明的有益效果是:
20.1、该短流程制备石墨的方法,在原料磨粉的制备阶段,采用将煅后石油焦和沥青片磨成细粉并混合压型的方式,省去了传统的混捏、轧片、二次磨粉等工序,提高了生产效率,降低了能耗,同时,保证了沥青粉与石油焦的均匀混合,还在工艺上减少了沥青的用量,有利于石墨性能提高。
21.2、该短流程制备石墨的方法,在焙烧后的冷却阶段,不等其冷却至常温,而是在250~350℃,就将焙烧品直接取出浸渍,不仅节省了传统冷却至室温的时间,同时还省去了浸渍前焙烧品预热环节,进一步节省了时间,降低了能耗。
22.3、该短流程制备石墨的方法,在浸渍后不进行二次焙烧等步骤,而是直接将浸渍品置于石墨化炉中进行石墨化,节省了原有工艺中多次焙烧的步骤,提高了生产效率,有利于降低能耗。
23.4、该短流程制备石墨的方法,省去了传统浸渍后的焙烧环节,在石墨化时采取分段升温的方式,利用石墨化炉的升温阶段进行类似焙烧的过程,进一步提高了效率,降低了能耗。
24.5、该短流程制备石墨的方法,相比普通的石墨生产流程,生产周期大幅缩短,实际试制时节省可达60天,并且经核算,生产同样产量的石墨,降低了至少30%能耗。
25.6、该短流程制备石墨的方法,在省去大量步骤后,通过优化原料粒度组成、焙烧和石墨升温曲线,使得所制产品仍具有优良的性能。
附图说明
26.图1为本发明的流程示意图。
具体实施方式
27.参阅图1,一种短流程制备石墨的方法,包括以下具体步骤:
28.分别将煅后石油焦和沥青片磨成细粉并筛分,在一种较优的实施方式中,将煅后石油焦磨成细粉,并筛分为<0.074mm、0.074~0.15mm、0.15~0.5mm、0.5~1.0mm四个粒级的物料,另外,可以采用气流磨将沥青片磨成d50为2~10μm的细粉;
29.按粒级以一定比例配置煅后石油焦细粉、沥青片细粉物料,可选的,以重量份数计,分别称取<0.074mm、0.074~0.15mm、0.15~0.5mm、0.5~1.0mm的煅后石油焦细粉30~50、10~30、5~20、0~10份,称取沥青片细粉20~30份,充分混匀后压型,具体的,可以将混匀的物料装入模具中等静压压型,成型压力为160~240mpa,压型时间为10~30min;
30.将压型后的成型生坯在隔绝空气下焙烧,较优的,焙烧最高温度为900℃,在400℃
以下升温速率为10℃/h,400~700℃,升温速率为5℃/h,700℃以上升温速率为10℃/h,焙烧结束后冷却,在一种较优的实施方式中,焙烧结束后冷却至250~350℃,焙烧品冷却至一定温度后,直接取出置于沥青液中浸渍,浸渍温度可以为200~300℃,浸渍时间可以为2~6h;
31.对浸渍品石墨化处理,该步骤最好在浸渍品冷却,并刮去其表面的沥青后进行,在一种较优的实施方式中,石墨化最高温度为3000℃,其中25~800℃阶段升温速率2~10℃/h,800~3000℃升温速率为30~90℃/h。
32.以下为三个较优的实施例,其中,煅后石油焦和沥青片原料均取自同一批次,且使用的设备均相同:
33.实施例1
34.(1)原料磨粉:
35.分别将煅后石油焦和沥青片磨成细粉,其中将石油焦磨至小于1.0mm,并筛分为<0.074mm、0.074~0.15mm、0.15~0.5mm、0.5~1.0mm四个粒级品种物料,沥青粉磨至d50为5μm。
36.(2)压型
37.分别取<0.074mm、0.074~0.15mm、0.15~0.5mm、0.5~1.0mm四个粒级煅后石油焦细粉各30、20、15、5份,取沥青片细粉30份,并混合均匀,随后将混匀物料装入模具中等静压压型,成型压力为180mpa,压型时间为20min。
38.(3)焙烧-浸渍
39.将成型生坯在隔绝空气下焙烧,焙烧最高温度为900℃,在400℃以下升温速率为10℃/h,400~700℃升温速率为5℃/h,700℃以上升温速率为10℃/h。待焙烧结束后冷却至300℃时,将焙烧品取出,置于浸渍罐中,在250℃浸渍3h。
40.(4)石墨化
41.待浸渍品冷却后,刮去表面沥青,并置于石墨化炉中石墨化处理,石墨化最高温度为3000℃,在25~800℃阶段,升温速率5℃/h,在800~3000℃阶段,升温速率为60℃/h。
42.待冷却后取样测试产品性能,其体密为1.80g/cm3,抗压强度42.0mpa,抗折强度20.5mpa,电阻率8.8μωm,500℃下热膨胀系数3.5*10-6
/℃,各向性能均表现优越。
43.实施例2
44.(1)原料磨粉
45.分别将煅后石油焦和沥青片磨成细粉,其中将石油焦磨至小于1.0mm,并筛分为<0.074mm、0.074~0.15mm、0.15~0.5mm、0.5~1.0mm四个粒级品种物料,沥青粉磨至d50为2μm。
46.(2)压型
47.分别取<0.074mm、0.074~0.15mm、0.15~0.5mm三个粒级煅后石油焦细粉各40、25、10份,取沥青片细粉25份,并混合均匀,随后将混匀物料装入模具中等静压压型,成型压力为160mpa,压型时间为30min。
48.(3)焙烧-浸渍
49.将成型生坯在隔绝空气下焙烧,焙烧最高温度为900℃,在400℃以下升温速率为10℃/h,400~700℃升温速率为5℃/h,700℃以上升温速率为10℃/h。待焙烧结束后冷却至
350℃时,将焙烧品取出,置于浸渍罐中,在300℃浸渍2h。
50.(4)石墨化
51.待浸渍品冷却后,刮去表面沥青,并置于石墨化炉中石墨化处理,石墨化最高温度为3000℃,在25~800℃阶段,升温速率10℃/h,在800~3000℃阶段,升温速率为90℃/h。
52.待冷却后取样测试产品性能,其体密为1.78g/cm3,抗压强度40.3mpa,抗折强度18.8mpa,电阻率9.4μωm,500℃下热膨胀系数3.4*10-6
/℃,各向性能均表现优越。
53.实施例3
54.(1)原料磨粉
55.分别将煅后石油焦和沥青片磨成细粉,其中将石油焦磨至小于1.0mm,并筛分为<0.074mm、0.074~0.15mm、0.15~0.5mm、0.5~1.0mm四个粒级品种物料,沥青粉磨至d50为10μm。
56.(2)压型
57.分别取<0.074mm、0.074~0.15mm、0.15~0.5mm、0.5~1.0mm四个粒级煅后石油焦细粉各50、20、10、5份,取沥青片细粉30份,并混合均匀,随后将混匀物料装入模具中等静压压型,成型压力为180mpa,压型时间为20min。
58.(3)焙烧-浸渍
59.将成型生坯在隔绝空气下焙烧,焙烧最高温度为900℃,在400℃以下升温速率为10℃/h,400~700℃升温速率为5℃/h,700℃以上升温速率为10℃/h。待焙烧结束后冷却至250℃时,将焙烧品取出,置于浸渍罐中,在200℃浸渍6h。
60.(4)石墨化
61.待浸渍品冷却后,刮去表面沥青,并置于石墨化炉中石墨化处理,石墨化最高温度为3000℃,在25~800℃阶段,升温速率2℃/h,在800~3000℃阶段,升温速率为30℃/h。
62.待冷却后取样测试产品性能,其体密为1.83g/cm3,抗压强度47.9mpa,抗折强度22.5mpa,电阻率9.2μωm,500℃下热膨胀系数3.6*10-6
/℃,各向性能均表现优越。
63.以上仅为本发明的较佳实施例,但本发明的保护范围并不局限于此,任何熟悉本技术领域的技术人员在本发明揭露的技术范围内,可轻易想到的变化或替换,都应涵盖在本发明的保护范围之内。因此,本发明的保护范围应该以权利要求所界定的保护范围为准。
64.本发明未详述之处,均为本技术领域技术人员的公知技术。