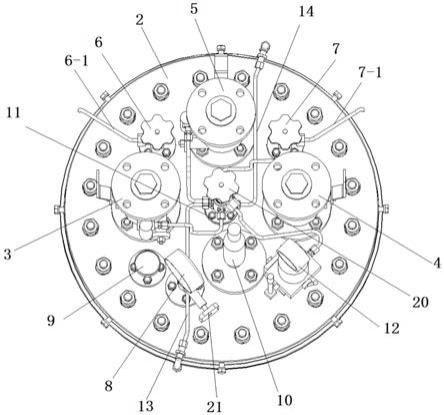
1.本实用新型属于铁路罐车技术领域,涉及一种液化气体铁路压力罐车顶部加排系统及压力罐车。
背景技术:
2.液化气体铁路罐车(以下简称压力罐车)主要用于装运液化石油气、丁二烯、二甲醚等介质。压力罐车由罐体与走行装置组成,罐体上设置有加排系统,加排系统用来实现介质的充装和卸载功能。近年来,随着压力罐车装液、卸液站点装卸设施的不断升级,原有压力罐车加排系统的适应性、可操作性、安全性逐渐降低,且在运用过程中存在一定的安全隐患。
技术实现要素:
3.针对现有技术中的缺陷和不足,本实用新型提供了一种液化气体铁路压力罐车顶部加排系统及压力罐车,确保罐车具有介质的充装、卸载功能并保障罐车在使用过程中的安全。
4.为达到上述目的,本实用新型采取如下的技术方案:
5.一种液化气体铁路压力罐车顶部加排系统,包括设在罐车罐体顶部的人孔颈法兰和设在人孔颈法兰上的人孔法兰盖,还包括设在人孔法兰盖上并贯穿人孔法兰盖伸至罐体内的第一装卸阀、第二装卸阀、第三装卸阀、低位检查阀和高位检查阀、安装在人孔法兰盖上并能连通至罐体内的压力表和温度计、安装在人孔法兰盖上且底部伸至罐体内并且底部密封的磁力浮球液位计以及安装在人孔法兰盖上的油压分配器和手压油泵;
6.所述第一装卸阀和第二装卸阀进口端分别连接有进出液管路,且两个进出液管路均伸至罐体内底部,第一装卸阀和第二装卸阀的出口端设有进出液法兰接口以与装卸液站点的液体管路连接;所述第三装卸阀进口端连通罐体内,第三装卸阀出口端设有气体法兰接口以与装卸液站点的气体管路连接;
7.所述低位检查阀进口端连接有低位检查内管,低位检查内管伸至罐体内底部,低位检查阀出口端设有低位检查阀口接管;高位检查阀进口端连接有高位检查内管,高位检查内管伸至罐体内最大允许充装量位置处,高位检查阀出口端设有高位检查阀口接管;
8.所述手压油泵连通至油压分配器,油压分配器分别连通第一装卸阀、第二装卸阀、第三装卸阀、第一远程控制管路和第二远程控制管路;所述第一远程控制管路和第二远程控制管路对称设在罐体外部两侧并延伸至罐体中下部,且在第一远程控制管路和第二远程控制管路末端分别设有手动切断阀。
9.本实用新型还包括如下技术特征:
10.具体的,在人孔法兰盖上设有防护罩筒,在防护罩筒上设有能开关的罩筒盖;防护罩筒、罩筒盖和人孔法兰盖围成了密闭式防护腔体;所述第一装卸阀、第二装卸阀、第三装卸阀、低位检查阀、高位检查阀、压力表、温度计和磁力浮球液位计的上部以及油压分配器
和手压油泵均位于该密闭式防护腔体内。
11.具体的,所述防护罩筒通过螺栓固定在人孔法兰盖上;所述罩筒盖一端与防护罩筒铰接,罩筒盖另一端设有把手和锁扣;锁扣下端设有锁盒,锁盒安装在防护罩筒外侧壁上;锁扣能伸入锁盒内,并能在锁盒内的锁扣下端上锁以固定锁扣从而关闭罩筒盖;装卸介质时,罩筒盖开启,装卸完成及运输途中罩筒盖关闭。
12.具体的,所述低位检查阀口接管、高位检查阀口接管、第一远程控制管路和第二远程控制管路均伸出防护罩筒外壁。
13.具体的,所述油压分配器包括一体式结构的:法兰座和法兰座上的筒形分配腔;法兰座能固定安装在人孔法兰盖上,在筒形分配腔的侧壁上设有五个螺纹通孔用以分别连接第一装卸阀、第二装卸阀、第三装卸阀、第一远程控制管路和第二远程控制管路;在筒形分配腔顶部设有螺纹通孔用以安装第一截止阀,该第一截止阀连通所述手压油泵,手压油泵能通过油压分配器控制第一装卸阀、第二装卸阀和第三装卸阀的开启和关闭。
14.具体的,所述压力表为耐振压力表,温度计为双金属温度计,温度计伸入罐体内的部分套有温度计护管。
15.具体的,所述压力表下端通过第二截止阀连接至罐体内。
16.具体的,所述人孔法兰盖通过螺柱和螺母固定在人孔颈法兰上。
17.一种压力罐车,包括罐体,还包括所述的液化气体铁路压力罐车顶部加排系统,该加排系统设在罐体顶部。
18.本实用新型与现有技术相比,有益的技术效果是:
19.本实用新型能确保罐车具有介质的充装、卸载功能并保障罐车在使用过程中的安全。
20.本实用新型加排系统中阀件、仪表均布置在人孔法兰盖上,布局紧凑,方便操作。
21.本实用新型紧急切断阀设置双侧远程控制管路,异常情况下在压力罐车两侧的底部均可实现切断阀的紧急切断,保障压力罐车的装、卸液安全。
22.本实用新型设置高、低位检查阀,有效控制罐车充装时罐内液体的充装量和罐车卸液时罐内液体的残留量,提高车辆在重车、空车状态下的运行安全性。
23.本实用新型设置液位计、压力表,对介质实现状态监测,保障压力罐车使用安全。
24.本实用新型设置密闭式防护罩筒,保护加排系统中阀件、仪表免遭意外破坏。
附图说明
25.图1为本实用新型去掉防护罩筒后的整体结构图;
26.图2为本实用新型在罐体上的安装示意图;
27.附图标号含义:
28.1.人孔颈法兰,2.人孔法兰盖,3.第一装卸阀,4.第二装卸阀,5.第三装卸阀,6.低位检查阀,6
‑
1.低位检查阀口接管,7.高位检查阀,7
‑
1.高位检查阀口接管,8.压力表,9.温度计,10.磁力浮球液位计,11.油压分配器,12.手压油泵,13.第一远程控制管路,14.第二远程控制管路,15.防护罩筒,16.罩筒盖,17.把手,18.锁扣,19.锁盒,20.第一截止阀,21.第二截止阀,100.罐体。
29.以下结合说明书附图和具体实施方式对本实用新型做具体说明。
具体实施方式
30.遵从上述技术方案,以下给出本实用新型的具体实施例,需要说明的是本实用新型并不局限于以下具体实施例,凡在本技术技术方案基础上做的等同变换均落入本实用新型的保护范围。下面结合实施例对本实用新型做进一步详细说明。
31.实施例1:
32.如图1至2所示,本实施例给出一种液化气体铁路压力罐车顶部加排系统,包括设在罐车罐体100顶部的人孔颈法兰1和设在人孔颈法兰1上的人孔法兰盖2,还包括设在人孔法兰盖2上并贯穿人孔法兰盖2伸至罐体100内的第一装卸阀3、第二装卸阀4、第三装卸阀5、低位检查阀6和高位检查阀7、安装在人孔法兰盖2上并能连通至罐体100内的压力表8和温度计9、安装在人孔法兰盖2上且底部伸至罐体100内并且底顶部密封的磁力浮球液位计10以及安装在人孔法兰盖2上的油压分配器11和手压油泵12。
33.具体的,第一装卸阀3和第二装卸阀4下端分别连接有进出液管路,且两个进出液管路均伸至罐体100内底部,第一装卸阀3和第二装卸阀4的上端设有进出液法兰接口以与装卸液站点的液体管路连接;第三装卸阀5下端连通罐体100内,第三装卸阀5上端设有气体法兰接口以与装卸液站点的气体管路连接。本实施例中的第一装卸阀、第二装卸阀和第三装卸阀均为常规结构,本实施例中的第一装卸阀、第二装卸阀和第三装卸阀均采用qgqy41f
‑
25
‑
2型紧急切断阀(下文提到的紧急切断阀均为第一装卸阀、第二装卸阀和第三装卸阀);该紧急切断阀为直通式结构,两端均采用凹凸面法兰,顶部装有阀盖进行密封,该紧急切断阀还包括阀杆、先导阀瓣、球阀、浮动阀瓣、小弹簧等部件。该紧急切断阀的开启过程为:先搬动手压油泵的手柄使油压达到3mpa,阀门的拨杆开始转动,先导阀瓣开启,介质通过阀杆周围的间隙进入球阀间的空腔,并逐渐在其中建立压力,当浮动阀瓣两侧压力达到平衡时,在小弹簧力的推动下,浮动阀瓣迅速开启,此时能听到轻微并清晰的撞击声,由先导阀开启至浮动阀瓣开启间隔在一分钟内,之后平稳缓慢打开球阀即可进行正常装卸工作。该紧急切断阀的关闭过程为:装卸完毕后,松开手压油泵的手柄,卸除油压,紧急切断阀关闭,最后关闭球阀。
34.低位检查阀6进口端连接有低位检查内管,低位检查内管伸至罐体100内底部,低位检查阀6出口端设有低位检查阀口接管6
‑
1;高位检查阀7进口端连接有高位检查内管,高位检查内管伸至罐体100内最大允许充装量位置处,高位检查阀7出口端设有高位检查阀口接管7
‑
1。本实施例中的低位检查阀6和高位检查阀7均为常规结构,在排液时,如果开启低位检查阀6后低位检查阀口接管6
‑
1没有液体流出,则认为排液干净;高位检查内管高度,是环境温度为50℃时液位在罐内的极限位置。当液位到达此高度时,打开高位检查阀7,会有液体喷出。液面一般不允许达到此位置。当磁力浮球液位计10失灵时,可以起到安全估量最高液位的作用,但禁止使用高位检查阀7控制液面高度。
35.手压油泵12连通至油压分配器11,油压分配器11分别连通第一装卸阀3、第二装卸阀4、第三装卸阀5、第一远程控制管路13和第二远程控制管路14;第一远程控制管路13和第二远程控制管路14对称设在罐体100外部两侧并延伸至罐体100中下部,且在第一远程控制管路13和第二远程控制管路14末端分别设有手动切断阀。
36.在人孔法兰盖2上设有防护罩筒15,在防护罩筒15上设有能开关的罩筒盖16;防护罩筒15、罩筒盖16和人孔法兰盖2围成了密闭式防护腔体;第一装卸阀3、第二装卸阀4、第三
装卸阀5、低位检查阀6、高位检查阀7、压力表8、温度计9和磁力浮球液位计10的上部以及油压分配器11和手压油泵12均位于该密闭式防护腔体内。
37.防护罩筒15通过螺栓固定在人孔法兰盖2上;罩筒盖16一端与防护罩筒15铰接,罩筒盖16另一端设有把手17和锁扣18;锁扣18下端设有锁盒19,锁盒19安装在防护罩筒15外侧壁上;锁扣18能伸入锁盒19内,并能在锁盒19内的锁扣18下端上锁以固定锁扣18从而关闭罩筒盖16;装卸介质时,罩筒盖16开启,装卸完成及运输途中罩筒盖16关闭。
38.低位检查阀口接管6
‑
1、高位检查阀口接管7
‑
1、第一远程控制管路13和第二远程控制管路14均伸出防护罩筒15外壁。
39.油压分配器11包括一体式结构的:法兰座和法兰座上的筒形分配腔;法兰座能固定安装在人孔法兰盖2上,在筒形分配腔的侧壁上设有五个螺纹通孔用以分别连接第一装卸阀3、第二装卸阀4、第三装卸阀5、第一远程控制管路13和第二远程控制管路14;在筒形分配腔顶部设有螺纹通孔用以安装第一截止阀20,该第一截止阀20连通手压油泵12,手压油泵12能通过油压分配器11控制第一装卸阀3、第二装卸阀4和第三装卸阀5的开启和关闭。
40.压力表8为耐振压力表,温度计9为双金属温度计,温度计9伸入罐体100内的部分套有温度计护管。
41.压力表8下端通过第二截止阀21连接至罐体100内,便于更换压力表8。
42.人孔法兰盖2通过螺柱和螺母固定在人孔颈法兰1上。
43.在另一个实施例中,给出一种压力罐车,包括罐体100,还包括实施例1中的液化气体铁路压力罐车顶部加排系统,该加排系统设在罐体100顶部。
44.本实用新型的紧急切断操作过程:如出现异常需要紧急关闭阀门中断装卸时,如果操作者在车顶走板上,可扳动手压油泵上的卸压手柄;如操作者在车下,可打开位于车辆两侧罐体中下部的手动切断阀;这两种办法均可让液压管路排油卸压,使得紧急切断阀阀杆上升,切断介质通路,达到紧急切断的目的。
45.本实用新型中的磁力浮球液位计为常规结构,其使用方法为:充装作业前,检查液位计各零部件是否完好无损,确认后方可进行操作;充装作业前,拧下保护罩,用手轻轻拉动液位计测量杆,直到感觉到其与浮球磁性耦合时,即可进行液位测量;充装作业时,目视液位计测量杆与液位计连接体白色尼龙定位套上平面位置处的刻度值,通过此刻度值,查h
‑
v表,即可得到充装液体的容积;充装作业完成后,用手轻轻地向下推动液位计的测量杆,使其脱离浮球的磁性耦合,恢复到初始位置,即可拧上保护罩,完成液位测量作业;罐体检修时,为防止损坏液位计测量杆,可将液位计测量杆从导管中抽出;先取下白色尼龙定位套,严格保护测量杆端部的强磁性元件,严禁吸附任何铁磁性材料,并应避免受热及撞击;罐车大、中修时,应重新更换液位计导管内底部的防冻液,重量大约100克,防冻温度为
‑
40℃;磁力液位计测量罐内介质液位高度允许误差为2.5%,轨道衡复验充装量后,应通过调整液位计上调整螺母的高度,对标尺刻度进行校正。
46.本实用新型中最大充装重量的控制方法为:首先,可以根据温度计所显示的温度数据,通过密度求得最大充装量时介质的容积;然后通过液位高度与罐体容积对照表,得到该容积在液位计上显示的高度;控制此高度,就等于控制了最大充装量;在装载完毕后,车辆的实际充装重量应由轨道衡来测定。
47.本实用新型中的装卸操作过程如下:
48.打开人孔罩筒盖,旋下紧急切断阀阀盖,连接气、液相接管,关闭与紧急切断阀相连的球阀(或截止阀);关闭手压油泵的卸压手柄(顺时针旋转),打开油路控制阀,推动手压油泵注压手柄给手压油泵加压;当油压增至3mpa左右时,紧急切断阀的工作油缸开始工作(油缸活塞的移动和凸轮转动可以观察到),活塞杆的动作将打开紧急切断阀;紧急切断阀中的先导阀瓣打开,约半分钟后阀内传出轻微响声,说明主阀瓣也自动开启,此时可打开球阀进行装卸作业。
49.装卸工作完成后,扳动手压油泵上的卸压手柄(逆时针转动)卸压,紧急切断阀自动关闭,随即将球阀(或截止阀)关闭,保持密封,再拆除接管,加装紧急切断阀阀盖,并扣紧人孔罩筒盖。