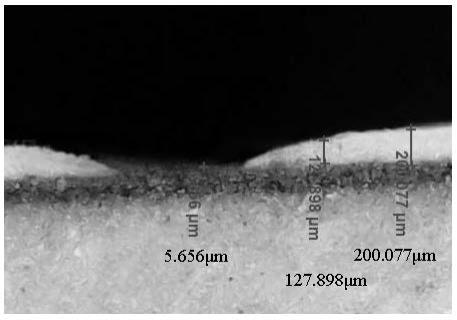
1.本发明涉及一种水晶勾勒效果装饰陶瓷岩板及制备方法,属于陶瓷砖生产制造技术领域。
背景技术:
2.目前市场上抛釉陶瓷砖产品与岩板产品种类繁多,为了提高产品竞争力,陶瓷厂家不仅致力于丰富产品的花色选择,而且还通过各种手段提高产品附加价值。
3.中国专利cn113183292a公开一种数控模具效果陶瓷砖的制备方法,通过电脑设计模具图案并由陶瓷喷墨花机在平面砖坯上喷墨打印具有排开或拨开性能的功能墨水,实现产品的自然起伏效果。中国专利cn110668792a公开一种立体幻彩干粒抛陶瓷大板及其制备方法,通过在釉面布撒干粒熔块烧制获得平整釉面效果。但是上述产品的装饰效果单一,缺乏特殊的附加装饰价值。
技术实现要素:
4.针对上述问题,本发明提供一种水晶勾勒效果装饰陶瓷岩板及制备方法,所述方法由于凹槽部位填充了颜色透明熔块,在烧成后凹槽处的颜色透明熔块会形成带色玻璃相,而颜色透明熔块的周边是不透明面釉层,上层是透明釉层,在此条件下,釉面效果形成反差,表面看上去具有凹凸起伏的多层次以及水晶透感般的装饰效果。
5.第一方面,本发明提供一种水晶勾勒效果装饰陶瓷岩板的制备方法。所述制备方法包括以下步骤:在砖坯表面施第一面釉;在施第一面釉后的砖坯表面喷墨打印油性拨开墨水;在喷墨打印油性拨开墨水后的砖坯表面施第二面釉;第二面釉被油性拨开墨水拨开形成具有凹槽的起伏纹理;在施第二面釉后的砖坯表面喷墨打印图案;在喷墨打印图案后的砖坯表面定位布撒颜色透明熔块以使得所述颜色透明熔块填充在凹槽处;在定位布撒颜色透明熔块后的砖坯表面施透明釉并烧成,烧成后颜色透明熔块形成的带色玻璃相层与凹槽周围的不透明面釉层以及位于釉面表面的由透明釉烧成得到的透明釉层形成反差,得到所述水晶勾勒效果装饰陶瓷岩板。
6.较佳地,所述第一面釉和/或第二面釉的始融温度为1170~1190℃。
7.较佳地,所述第一面釉和/或第二面釉的化学组成包括:以质量百分比计,sio2:54~56%、al2o3:23~26%、碱土金属氧化物:0.6~1.2%、碱金属氧化物:7.3~9.0%、zro2:4.9~6.5%。
8.较佳地,所述第一面釉的施加方式为喷釉,比重为1.30~1.35g/cm3,施釉量为300~320g/m2。
9.较佳地,所述第二面釉的施加方式为喷釉,比重为1.55~1.57g/cm3,施釉量为650~680g/m2。
10.较佳地,所述颜色玻璃熔块的布撒量为400~500g/m2。
11.较佳地,所述透明釉包含的透明熔块的化学组成包括:以质量百分比计,sio2:63~66%、al2o3:11~14%、cao:11~13%、mgo:1~2%、k2o:4.2~5.1%、na2o:0.2~0.5%、zno:1.8~2.3%。
12.较佳地,所述透明釉的施加方式为淋釉,施釉量为1000~1200g/m2。
13.较佳地,所述烧成为低温慢烧;最高烧成温度为1154~1161℃,烧成周期为107~110min。
14.第二方面,本发明还提供上述任一项所述的制备方法获得的水晶勾勒效果装饰陶瓷岩板。
附图说明
15.图1是本发明水晶勾勒效果装饰陶瓷岩板的结构示意图;其中,1是砖坯层,2是面釉层,3是颜色透明熔块层,4是透明釉层;图2是面釉层被拨开的截面效果图;图3是对比例1的颜色透明熔块位置的局部放大缺陷图;图4是对比例2的低比重面釉的拨开截面效果图。
具体实施方式
16.通过下述实施方式进一步说明本发明,应理解,下述实施方式仅用于说明本发明,而非限制本发明。在没有特殊说明的情况下,各百分含量指质量百分含量。
17.以下示例性说明本发明所述水晶勾勒效果装饰陶瓷岩板的制备方法。“勾勒”指的是凹凸起伏纹理构成的线条形状。
18.将陶瓷基料压制为砖坯。陶瓷基料的化学组成不受限制,采用本领域常用的陶瓷基料配方即可。一些实施方式中,所述陶瓷基料的化学组成包括:以质量百分比计,sio2:62~67%、al2o3:20~25%、碱土金属氧化物:0.2~2%、碱金属氧化物:4~7%。例如,所述陶瓷基料的化学组成包括:以质量百分比计,sio2:62~67%、al2o3:20~25%、fe2o3:0.06~0.1%、tio2:0.1~0.5%、cao:0.1~0.5%、mgo:0.1~1.0%、k2o:2.0~3.0%、na2o:2.5~3.5%、烧失:4.5~6.5%。
19.可通过干压成型制备砖坯。砖坯可为平坯。
20.将砖坯干燥。例如采用干燥窑干燥。干燥时间可为1~1.2h,干燥后砖坯的水分控制在0.5wt%以内。
21.在干燥后的砖坯表面施第一面釉。第一面釉的作用是遮盖砖坯底色和瑕疵,促进喷墨发色,以及避免油性剥开墨水直接作用于砖坯导致砖面露底,同时第一面釉还对颜色透明熔块(也可以称为颜色熔块)布撒处砖坯上升的气泡起到缓冲作用,这是因为颜色透明熔块形成液相后,砖坯中气体很难再向上排气,此时面釉层还未形成熔融液,中间存在大量空隙,因此可以对砖坯排出的气体形成存储作用。由于砖坯出干燥窑后含水率较低,砖面平整度差,施第一道面釉还利于提高平整度。另外,干燥后的砖坯温度较高,因此后续于第一
面釉表面喷墨打印油性拨开墨水时,第一面釉形成的面釉层已经被热干,所以第一面釉基本不会与油性拨开墨水排斥形成拨开效果。
22.所述第一面釉为低温面釉。一些实施方式中,所述第一面釉的始融温度为1170~1190℃。
23.所述第一面釉的化学组成包括:以质量百分比计,sio2:54~56%、al2o3:23~26%、碱土金属氧化物:0.6~1.2%、碱金属氧化物:7.3~9.0%、zro2:4.9~6.5%。在第一面釉中氧化锆的含量不宜过低,否则面釉发黄调,不利于喷墨图案发色。作为示例,第一面釉的化学组成包括:以质量百分比计,烧失:4.00~5.00%、sio2:54.89~55.78%、al2o3:23.87~25.45%、fe2o3:0.21~0.41%、tio2:0.06~0.08%、cao:0.55~0.87%、mgo:0.18~0.29%、k2o:4.89~5.62%、na2o:2.58~3.34%、p2o5:0.21~0.40%、zro2:4.96~6.35%,zno:0.07~0.10%。
24.所述第一面釉的施加方式为喷釉。一些实施方式中,第一面釉的比重为1.30~1.35g/cm3,施釉量为300~320g/m2。通过薄喷的方式施加第一面釉,具有较高平整度。如果第一面釉的施加量过多,会导致整体面釉层过厚而延长砖坯气体向上排放周期,不利于砖坯气体及时排出,导致最上层透明釉层存在大量气泡。
25.在施第一面釉后的砖坯表面喷墨打印油性拨开墨水。可根据版面利用设计矢量图形成效果网,并依据所述效果网打印油性拨开墨水得到纹理图案。一些实施方式中,通过处理所需要的设计图案,将设计图案中的纹理、曲线经过路线的方式提取,制成与设计图案相对应的设计矢量文件,经处理好的设计文件上传到数码喷墨机中,在砖坯经过施第一面釉后,进入到数码喷墨机的位置,数码喷墨机将按照处理好的设计图案喷洒油性拨开墨水,油性拨开墨水覆盖的位置与设计图案相对应的纹理、曲线相一致。油性拨开墨水的组成和来源不受限制,采用本领域常用的油性拨开墨水即可。
26.在打印油性拨开墨水前,可以控制砖坯的表面温度为35~40℃。当然,打印油性墨水后可不再烘干。
27.在喷墨打印油性拨开墨水后的砖坯表面施第二面釉。第二面釉可在油性拨开墨水的作用下被剥开形成具有凹槽的起伏纹理。第二面釉优选和第一面釉具有相同的配方体系,这样能够提高釉层之间的适应性。
28.所述第二面釉的化学组成包括:以质量百分比计,sio2:54~56%、al2o3:23~26%、碱土金属氧化物:0.6~1.2%、碱金属氧化物:7.3~9.0%、zro2:4.9~6.5%。作为示例,第二面釉的化学组成包括:以质量百分比计,烧失:4.00~5.00%、sio2:54.89~55.78%、al2o3:23.87~25.45%、fe2o3:0.21~0.41%、tio2:0.06~0.08%、cao:0.55~0.87%、mgo:0.18~0.29%、k2o:4.89~5.62%、na2o:2.58~3.34%、p2o5:0.21~0.40%、zro2:4.96~6.35%、zno:0.07~0.10%。
29.同样优选地,所述第二面釉的始融温度为1170~1190℃。
30.在实验中发现,若第一面釉和第二面釉使用高温面釉,由于颜色色料本身熔点较低,其会在面釉未达熔融点时已经形成熔融液,此时面釉层之间还未封闭,由于面釉层熔融温度跟颜色色料之间温差过大,颜色熔块层形成熔融液后封闭,面釉层却依旧存在较大空隙促使砖坯气体通过面釉层持续排出上升,大量气体会冲破透明熔块层,导致出现大量火山口。
31.第二面釉的施加方式为喷釉。一些实施方式中,第二面釉的比重为1.55~1.57g/cm3,施釉量为650~680g/m2,在此范围内利于面釉层对于砖坯排气起到缓冲作用,同时第二面釉的施釉量较高,这样拨开效果更加明显,拨开位置具有显著的凹槽细节肌理。如果第二面釉的施釉量较低,会导致拨开较为平整,无法呈现凹凸起伏纹理,不利于颜色熔块填充到凹槽。
32.本发明对于第二面釉的控制可和油性拨开墨水的矢量图对应。如果矢量图构成以细线斑点为主,第二面釉的施釉量可适当减少,避免降低凹槽效果,这是因为此时油性拨开墨水的用量少,拨开受到较大阻力。
33.在施第二面釉后的砖坯表面喷墨打印图案。喷墨打印图案的纹理和颜色根据版面设计作出适应性变化。可以采用数码喷墨打印机打印。使用的陶瓷墨水可有蓝色、棕色、桔黄色、柠檬黄、黑色、红色等。
34.在喷墨打印图案后的砖坯表面定位布撒颜色透明熔块以使得所述颜色透明熔块填充在凹槽处。具体为,先在喷墨打印后的砖坯表面定位布施胶水。布施胶水的位置是凹槽需要色彩装饰的位置(即需要布施颜色透明熔块的位置)。可采用数码胶水机来定位布施胶水。胶水的材质没有特别限定,可以是本领域公知的胶水。定位布施胶水后,在砖坯表面布撒颜色透明熔块。颜色透明熔块的布施方法可为数码干粒机布干粒和/或皮带式布料机布干粒。可用震动筛网分散,通过回收设备将多余部分回收,只留下需要装饰部分。
35.颜色透明熔块的布撒量可为400~500g/m2。采用这样的布撒量,可以将颜色透明熔块最大化布撒在凹槽处,保证凹槽处有颜色熔块填充。然后,去除多余的颜色透明熔块,实现仅在凹槽处进行颜色水晶装饰。去除方式可为吹走或抽走等。例如可以利用回收抽风机抽走多余的颜色熔块。
36.所述颜色透明熔块包括:以重量份计,透明熔块100份,釉用色料1~2份。例如将透明熔块与釉用色料干混得到颜色透明熔块。透明熔块的化学组成包括:以质量百分比计,sio2:63~66%、al2o3:11~14%、cao:11~13%、mgo:1~2%、k2o:4.2~5.1%、na2o:0.2~0.5%、zno:1.8~2.3%。作为示例,所述透明熔块的化学组成包括:以质量百分比计,烧失:0.23~0.25%、sio2:63.00~65.90%、al2o3:11.00~13.95%、cao:11.00~13.00%、fe2o3:0.05~0.20%、tio2:0.05~0.10%、mgo:1.00~2.00%、k2o:4.21~5.10%、na2o:0.23~0.35%、zno:1.80~2.30%。釉用色料根据装饰颜色需求作出适应性变化。
37.颜色透明熔块中含有较多色料,因此整体熔点(始融温度)会较低,如果在透明釉表面大量布撒会使得透明熔块被透明釉包裹,容易在釉面形成针孔。本发明的制备方法不仅能够解决颜色透明熔块熔点低导致被包裹后容易产成大量气泡造成产品缺陷的问题,同时将颜色透明熔块层和其他釉层拉开装饰层次,以及解决釉层之间由于膨胀系数不一致导致釉层开裂现象。
38.在定位布撒颜色透明熔块后的砖坯表面施透明釉。
39.所述透明釉是含有透明熔块的熟料釉。作为优选,颜色透明熔块与透明釉含有的透明熔块是同一个配方体系,如此能够减少两者釉层差异造成的釉层开裂。相比生料透明釉,含有透明熔块的透明釉形成的釉层气泡少,利于提高釉层整体透感。一些实施方式中,透明釉包含的透明熔块的化学组成包括:以质量百分比计,sio2:63~66%、al2o3:11~14%、cao:11~13%、mgo:1~2%、k2o:4.2~5.1%、na2o:0.2~0.5%、zno:1.8~2.3%。作
为示例,所述透明熔块的化学组成包括:以质量百分比计,烧失:0.23~0.25%、sio2:63.00~65.90%、al2o3:11.00~13.95%、cao:11.00~13.00%、fe2o3:0.05~0.20%、tio2:0.05~0.10%、mgo:1.00~2.00%、k2o:4.21~5.10%、na2o:0.23~0.35%、zno:1.80~2.30%。釉用色料根据装饰颜色需求作出适应性变化。
40.所述透明釉包含的透明熔块的粒径为80~250目。
41.上述透明釉的始融温度为920~1030℃。砖坯中多数矿物在900~950℃会进行碳酸盐分解产生大量气体,将透明釉的始融温度控制在该范围能够避免各装饰层次之间温差太大,导致砖坯气体不能及时排出造成的缺陷。一些实施方式中,所述面釉的始融温度高于透明釉160~260℃。
42.除了透明熔块以外,所述透明釉还包括水和釉用胶水。一些实施方式中,所述透明釉包括:以重量份计,透明熔块45~52份,水8~12份,釉用胶水38~43份。所述透明釉的施加方式可为淋釉。
43.所述透明釉的施釉量为1000~1200g/m2。由于颜色透明熔块处会产生扩散,为了拉开透明釉层之间层次,在一定有效范围内通过施加大量透明釉,可以利于釉层拉开层次,使得颜色装饰位置上层存在透明釉层。
44.将施透明釉后的砖坯干燥。可采用电窑干燥。干燥温度为110~120℃,干燥后砖坯水分控制在0.3wt%以内。
45.烧成。例如进入辊道窑低温慢烧。为了促进气泡排出,烧成制度采取低温慢烧,来保证镜面度与透感。例如,烧成周期为107~110min,最高烧成温度为1154~1161℃。
46.本发明所述制备方法通过工艺革新,利用颜色透明熔块、透明釉层搭配凹凸工艺使产品具有别致的装饰效果。由于凹槽部位填充了颜色透明熔块,在烧成后凹槽处的颜色透明熔块会形成带色玻璃相,而颜色透明熔块的周边是不透明面釉层,上层是透明釉层,在此条件下,釉面效果形成反差,表面看上去具有凹凸起伏的多层次以及水晶透感般的装饰效果。一些实施方式中,所述岩板的规格为长1800~3600mm
×
宽900~1800mm
×
厚10.5~12.5mm。
47.下面进一步例举实施例以详细说明本发明。同样应理解,以下实施例只用于对本发明进行进一步说明,不能理解为对本发明保护范围的限制,本领域的技术人员根据本发明的上述内容作出的一些非本质的改进和调整均属于本发明的保护范围。下述示例具体的工艺参数等也仅是合适范围中的一个示例,即本领域技术人员可以通过本文的说明做合适的范围内选择,而并非要限定于下文示例的具体数值。
48.实施例1
49.水晶勾勒效果装饰陶瓷岩板的制备方法包括以下步骤:步骤1.将普通陶瓷基料压制为砖坯;步骤2.将砖坯在干燥窑中干燥,干燥时间为1~1.2h,干燥坯水分控制在0.5wt%以内;步骤3.在砖坯表面施第一面釉;第一面釉的化学组成包括:以质量百分比计,烧失:4.00~5.00%、sio2:54.89~55.78%、al2o3:23.87~25.45%、fe2o3:0.21~0.41%、tio2:0.06~0.08%、cao:0.55~0.87%、mgo:0.18~0.29%、k2o:4.89~5.62%、na2o:2.58~3.34%、p2o5:0.21~0.40%、zro2:4.96~6.35%、zno:0.07~0.10%;第一面釉的比重
1.30~1.35g/cm3,施釉量300~320g/m2;步骤4.在施第一面釉后的砖坯表面喷墨打印油性拨开墨水;步骤5.在喷墨打印油性拨开墨水后的砖坯表面施第二面釉;第二面釉的化学组成包括:以质量百分比计,烧失:4.00~5.00%、sio2:54.89~55.78%、al2o3:23.87~25.45%、fe2o3:0.21~0.41%、tio2:0.06~0.08%、cao:0.55~0.87%、mgo:0.18~0.29%、k2o:4.89~5.62%、na2o:2.58~3.34%、p2o5:0.21~0.40%、zro2:4.96~6.35%、zno:0.07~0.10%;第二面釉的比重为1.55~1.57g/cm3,施釉量为650~680g/m2;步骤6.在施第二面釉后的砖坯表面喷墨打印图案;步骤7.在喷墨打印图案后的砖坯表面采用数码胶水干粒机布撒颜色透明熔块,仅在凹槽处留下颜色熔块,将多余的颜色透明熔块抽走;步骤8.在布撒颜色透明熔块后的砖坯表面淋透明釉;所述透明釉包含的透明熔块的化学组成包括:以质量百分比计,烧失:0.23~0.25%、sio2:63.00~65.90%、al2o3:11.00~13.95%、cao:11.00~13.00%、fe2o3:0.05~0.20%、tio2:0.05~0.10%、mgo:1.00~2.00%、k2o:4.21~5.10%、na2o:0.23~0.35%、zno:1.80~2.30%;透明釉的施釉量为1000~1200g/m2;步骤9.将施透明釉后的砖坯干燥,干燥温度为110~120℃,干燥后砖坯水分控制在0.3wt%以内;步骤10.入辊道窑低温慢烧,烧成周期为107~110min,最高烧成温度为1154~1161℃。
50.该实施例得到的水晶勾勒效果装饰陶瓷岩板在凹槽部位填充了颜色透明熔块,在烧成后凹槽处的颜色透明熔块会形成带色玻璃相,而颜色透明熔块的周边是不透明面釉层,上层是透明釉层,在此条件下,釉面效果形成反差,表面看上去具有凹凸起伏的多层次以及水晶透感般的装饰效果。
51.对比例1
52.与实施例1基本相同,区别仅在于:所述第一面釉和/或第二面釉的化学组成包括:以质量百分比计,烧失:3.82%、sio2:50.58%、al2o3:33.69%、fe2o3:0.21%、tio2:0.08%、cao:1.20%、mgo:1.45%、k2o:4.27%、na2o:2.13%、zro2:2.49%、zno:0.08%。面釉层的始融温度较高,在透明釉层完全闭合后,砖坯已经通过面釉层向上排气,导致颜色熔块装饰透明釉层中出现大量火山口,其缺陷效果如图3所示。
53.对比例2
54.与实施例1基本相同,区别仅在于:第二面釉的比重低于1.40g/m3。由于面釉水分含量比较大,油性拨开墨水两侧的面釉干燥速度比较慢,墨水难以剥开面釉,油性拨开墨水剥开效果平缓,凹凸立体感较差,不利于颜色透明熔块的填充,其拨开效果如图4。