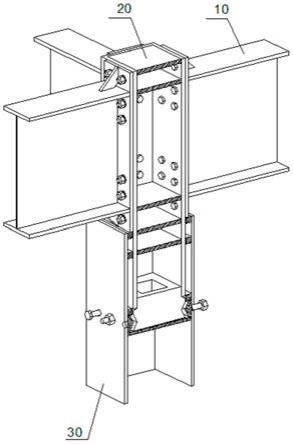
1.本技术涉及一种装配式箱型柱的连接节点及包含其的建筑物,适用于钢结构节点的技术领域。
背景技术:
2.目前,钢结构连接大多采用焊接或螺栓连接或者栓焊结合连接。传统梁柱全焊接节点中,梁上下翼缘及腹板与柱现场施焊,这种连接形式虽然为刚性连接,但节点延性差,地震中容易发生脆性破坏,且需现场施焊,大大影响了施工速度与质量,造成环境污染,不适于装配式钢结构,同时由于焊接面积大,容易产生较大的残余应力,影响节点的受力性能。另一方面,建筑产业化需要钢结构构件能快速装拆,传统栓焊混合连接节点或焊接节点,当建筑达到使用年限,或者需要改造迁移时,焊缝部分需要破坏性拆除,降低了拆除效率,同时也不利于构件的重复利用。
3.中国专利申请201110123542.4公开了一种内衬管式矩形钢管柱-h型钢梁连接节点,包括矩形钢管柱,h型钢梁、内衬管和螺栓,h型钢梁的翼缘与两段矩形钢管柱外壁焊接连接,h型钢梁腹板与两段矩形钢管柱外壁焊接连接,内衬管与两段矩形钢管柱通过螺栓连接。该连接节点具有的技术缺陷包括:矩形钢管柱和内衬管仅通过螺栓连接,连接强度不高,承载力不强;h型钢梁的翼缘和腹板与两段矩形钢管柱外壁焊接连接,不仅增加了现场的焊接作业,提高了作业难度,更重要的是无法进行装配式作业,降低了作业效率,而且也不便于拆卸,无法重复利用;矩形钢管柱和内衬管内部没有设置任何的加劲件,使得结构的承载力有限,也没有通过合理配置加劲件的位置并合理布置梁柱的位置,使得结构能够发挥其最大承载性能。
4.现有技术中需要一种受力合理、承载性能高、便于拆装、作业效率高、可重复利用的连接节点。
技术实现要素:
5.本技术的目的是设计一种装配式箱型柱的连接节点及包含其的建筑物,其具有受力合理、承载力强,拆装简单便捷,作业效率高,可重复利用且可模块化生产等技术优势。
6.本技术涉及一种装配式箱型柱的连接节点,所述装配式箱型柱包括插入式短柱和箱型柱,钢梁与所述插入式短柱通过端板连接,所述插入式短柱插入所述箱型柱中并与所述箱型柱嵌固接合;其中,所述插入式短柱的下端设有嵌固件,所述箱型柱中设有与所述插入式短柱的嵌固件相配合的嵌固座。
7.其中,所述箱型柱的本体可以为箱型截面,本体内依次设置有多道加强环和加劲板,第一道加强环与柱顶平齐,所述嵌固座设置在最后一道加强环和所述加劲板之间;所述嵌固座可以通过顶紧螺栓与所述本体连接,所述顶紧螺栓与所述本体的内螺纹连接;所述本体上还可以设有复位螺栓,所述复位螺栓穿过所述本体,所述嵌固座与所述复位螺栓可以形成整体,所述复位螺栓的外端设有复位螺母,所述嵌固座可以为嵌固滑块。
8.其中,所述插入式短柱可以包括框体,所述框体的上端设有上顶板,所述框体内设有与上顶板平行的至少一个加强板,所述框体的侧面设有螺栓孔,所述嵌固件设在所述框体的底部;所述框体内设有四道加强板,第一道加强板与所述钢梁的顶面齐平,第二道加强板与所述钢梁的底面齐平,第三道加强板与所述箱型柱的第一道加强环对齐,第四道加强板与所述箱型柱的第二道加强环对齐;所述钢梁还可以包括钢梁本体和加劲板,所述端板上设置螺栓孔,单边螺栓插入所述端板上的螺栓孔和所述插入式短柱的框体侧面的螺栓孔以将所述端板和所述插入式短柱的所述框体连接,所述端板的底部与所述箱型柱顶部的第一道加强环对齐顶紧。
9.本技术还涉及一种建筑物,包括钢梁和装配式箱型柱,所述钢梁和所述装配式箱型柱的连接节点为如上所述的连接节点。
10.本技术的装配式箱型柱的连接节点及包含其的建筑物,具有以下技术优势:
11.(1)将柱的现场焊缝连接转化为通过插入式短柱与箱型柱本体的嵌固连接,提高了安装效率,同时拆除时不需要进行破坏性的拆除,拆除方便快捷,此连接方式可用于重复利用的钢结构装配式建筑;
12.(2)将梁与柱的刚接节点转化为端板连接,提高了钢梁的安装效率,同时梁的剪力通过梁端板与柱顶刨平顶紧传递给柱,梁的弯矩转换为螺栓的拉力,有效减少了螺栓数量节省成本;
13.(3)该节点的施工速度快、安装精度高,构造简单、传力明确、承载力高,施工条件不受作业环境影响,能够显著降低施工成本,解决了现场焊接工作量大、不方便装卸等问题;
14.(4)梁柱采用单边螺栓连接,避免了梁柱的栓焊连接问题,连接节点均可工厂化生产,无需现场加工,相关嵌固件均为标准件,可批量定制,因此本技术的节点结构可以形成模块化产品并投入市场,具有节能环保和绿色低碳的效果,可以大幅提升装配效率,对装配式钢结构的产业化发展起到关键性作用,具有极高的经济效益;
15.(5)该节点通过插入式短柱、箱型柱和钢梁的配合设计,尤其是其中通过插入式短柱框体内设置的多道加强板、箱型柱内设置的多道加强环的位置相互配合,以及顶紧螺栓和复位螺栓的设置,使得本技术的连接节点受力合理、承载力强,拆装简单便捷,方便操作,相比于现有技术中的结构具有显著的技术效果和明显的技术优势。
附图说明
16.图1是本技术的装配式节点的示意图。
17.图2是本技术的装配式节点的内部结构示意图。
18.图3是本技术装配式箱型柱的箱型柱的示意图。
19.图4是本技术的箱型柱的内部结构示意图。
20.图5是本技术装配式箱型柱的插入式短柱的示意图。
21.图6是本技术的插入式短柱的内部结构示意图。
22.图7是与本技术的装配式箱型柱连接的钢梁示意图。
23.图8是含有本技术的装配式箱型柱的装配式节点的示意图。
具体实施方式
24.为使本技术的目的、技术方案和优点更加清楚明白,下文中将结合附图对本技术的实施例进行详细说明。需要说明的是,在不冲突的情况下,本技术中的实施例及实施例中的特征可以相互任意组合。
25.如图1和2所示,本技术的装配式箱型柱的连接节点,包括插入式短柱20和箱型柱30,钢梁10与插入式短柱20通过端板连接,插入式短柱20插入箱型柱30中并与箱型柱30嵌固接合。其中,插入式短柱20的下端设有嵌固件24,箱型柱30中设有与插入式短柱20的嵌固件24相配合的嵌固座34。
26.如图3和4所示,箱型柱30的本体31为箱型截面,本体31内设置有加强环32和加劲板33。在图示实施方式中,第一道加强环与柱顶平齐,第二道加强环与第一道加强环间隔设置,第三道加强环与第二道加强环间隔设置,加劲板与第三道加强环间隔设置。在第三道加强环和加劲板之间设置有嵌固座34,嵌固座34通过顶紧螺栓35和复位螺栓36与本体31连接。顶紧螺栓35与本体的内螺纹连接,通过扭动顶紧螺栓35实现嵌固座34的顶紧。复位螺栓36穿过本体31,复位螺栓36与嵌固座34例如通过焊接形成为整体,复位螺栓36的外端可以设有复位螺母。拆卸时,先松开顶紧螺栓,然后扭动复位螺栓的螺母实现嵌固座的复位。在图4所示实施方式中,嵌固座可以设置成嵌固滑块的形式。
27.如图5和6所示,插入式短柱包括框体21,框体21的上端设有上顶板,上顶板的上沿与框体的上沿齐平,上顶板起到加劲作用。框体21内设有与上顶板平行的至少一个加强板22,框体21的侧面设有螺栓孔23,框体21的底部设有嵌固件24。图6所示实施例中,框体21内设有四道加强板,加强板可以采用与上顶板相同的形式。其中,第一道加强板与钢梁的顶面齐平,第二道加强板与钢梁的底面齐平,第三道加强板与箱型柱的柱顶加强环对齐,第四道加强板与箱型柱的第二道加强环对齐。框体21底部的嵌固件24能够与箱型柱30内的嵌固座嵌合,并通过拧紧紧固螺栓紧固。本技术的嵌固件可以采用铸造件,嵌固件与插入式短柱的框体采用全熔透焊接。本技术中,插入式短柱的框体厚度与箱型柱的本体厚度之比可以为0.1-20,优选为0.1-10。
28.如图7-8所示,本技术的钢梁包括钢梁本体10、端板12和加劲板13,端板12上设置螺栓孔14,通过单边螺栓15与插入式短柱连接,端板底部16与箱型柱顶部的加强环齐平顶紧。本技术通过插入式短柱与箱型柱底端嵌固方式的连接避免了钢柱的现场焊接,梁柱通过端板顶紧柱顶,同时通过单边螺栓与柱本体连接避免了梁柱刚接时的现场焊接,同样此方法也可以拓展为柱中间位置使用。
29.本技术通过插入式短柱、箱型柱和钢梁的配合设计使得本技术的装配式箱型柱的连接节点受力合理、承载力强,具体技术手段包括:插入式短柱下端的嵌固件和箱型柱下端的嵌固座互相嵌固连接;插入式短柱框体内设有分别与钢梁的顶面齐平、与钢梁的底面齐平、与箱型柱的柱顶加强环对齐、与箱型柱的第二道加强环对齐的四道加强板;钢梁的端板底部与箱型柱顶部的加强环齐平顶紧。本技术通过上述结构特征的组合设计,合理地布置了插入式短柱、箱型柱和钢梁的位置,并通过插入式短柱框体内设置的多道加强板以及箱型柱内设置的多道加强环的位置相互配合,使得本技术的连接节点受力合理、承载力强,相比于现有技术中的结构具有明显的技术优势和显著的技术效果。另外,本技术还通过顶紧螺栓和复位螺栓的设置,使得嵌固件能够与嵌固座牢固地连接,并且能够通过操作复位螺
栓实现简单拆卸,从而使得本技术的连接节点拆装简单便捷,而且可以重复利用。
30.本技术还涉及一种建筑物,其具有如上所述的装配式箱型柱的连接节点,除上述连接节点以外的其他部件均可以采用现有技术中已有的形式,不再赘述。
31.虽然本技术所揭露的实施方式如上,但所述的内容只是为了便于理解本技术而采用的实施方式,并非用以限定本技术。任何本技术所属技术领域内的技术人员,在不脱离本技术所揭露的精神和范围的前提下,可以在实施的形式上及细节上作任何的修改与变化,但本技术的专利保护范围,仍须以所附的权利要求书所界定的范围为准。