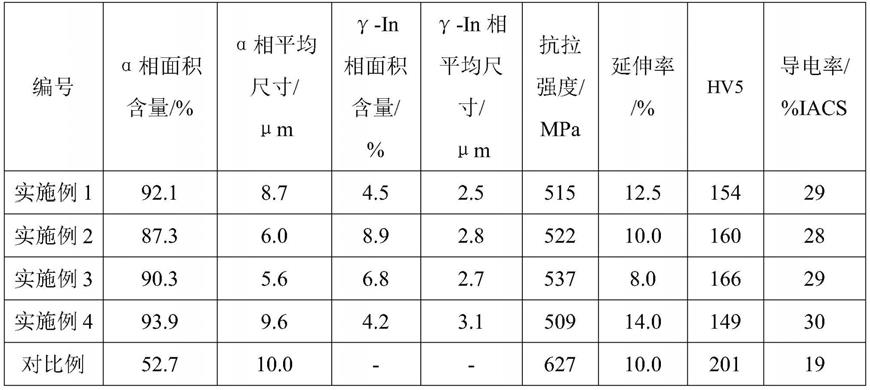
1.本发明属于铜合金技术领域,具体涉及一种黄铜合金及其制备方法。
背景技术:
2.黄铜合金因其具备良好的冷热加工性能,且使用成本较低,因此,市场上电器插头基本选用黄铜材料加工制备。以一种圆角插头件为例,生产上大多采用“高速车削,钻孔
→
电镀”的方式加工,要求材料具备良好的切削加工性能、冷铆性能、直线度、电镀性能和导电性能。当前常使用黄铜合金牌号为h62和c3602。其中以c3602为代表的铅黄铜切削性能良好,然而随着人类健康意识的提高,无铅化必然成为未来发展趋势。h62材料低铅环保,冷铆性能良好,但切削性能较差,无法大规模使用高速车床加工制备。其他无铅材料包括含铋黄铜,硅黄铜,锡黄铜等。含铋黄铜切削性能接近铅黄铜,但材料自裂倾向明显,一般圆角插头规格在φ5mm以下,经过钻孔加工后材料冷铆性能无法满足使用要求,且电镀性能一般,废料不易回收处理,因此存在诸多限制。含硅无铅黄铜切削性能一般,电镀性能较差,镀层易脱落,一般硅黄铜常用于制备大规格热锻用棒材。含锡(锡含量在0.8wt%左右)无铅黄铜耐脱锌腐蚀性能良好,黄铜因内部组织存在大量γ硬质相,车削时易损刀,一般加工至规格φ5mm以下时硬度可达到hv180以上,材料冷铆性能较差。
3.当前市场上已开发应用的无铅黄铜均存在诸多问题,为满足未来市场需求,亟需开发一款满足φ5mm以下棒材加工,且兼具良好切削性能、冷铆性能、电镀性能和导电性能的黄铜合金。
技术实现要素:
4.本发明所要解决的第一个技术问题是提供一种兼具良好切削性能、冷铆性能、电镀性能和导电性能的环保黄铜合金。
5.本发明解决第一个技术问题所采用的技术方案为:一种黄铜合金及其制备方法,其特征在于:该黄铜的质量百分比组成为cu:61~65wt%、pb:<0.1wt%、in:0.1~1.0wt%、sn:0.2~0.5wt%、ni:0.1~0.5wt%,余量为zn和不可避免的杂质。
6.作为优选,该黄铜的微观组织中含有α相、微量β相以及γ-in相,所述α相的面积含量为85~95%,γ-in相的面积含量为4~10%。其中γ-in相比例下限控制在4%,保证材料具备良好的切削性能,γ-in相比例控制上限在10%,避免材料脆性增加,影响成品冷铆性能和材料冷加工性能。
7.作为优选,所述γ-in相的平均尺寸≤5μm,所述α相的平均尺寸≤10μm。控制尺寸大小有利于使γ-in相弥散分布,避免出现γ-in相大面积聚集,降低材料冷铆性能。同时控制α相晶粒尺寸有利于形成更多γ-in相粒子分布于晶界中,从而提高材料切削性能
8.作为优选,还包括la,ce,mg,mn,zr中的至少一种,总量为0.01~0.2wt%。
9.添加其他微量有益元素,如la,ce元素,有利于细化晶粒,起到除杂、净化作用,减少夹杂弱化晶界。添加mg,mn元素,熔炼过程主要起到除氧还原作用,同时适量mg元素有利
于改善材料切削性能。适量mn元素有利于改善材料耐磨性能,降低圆角插头在插拔过程中的阻力,从而提高抗变形能力。添加适量zr元素,能够提高材料抗高温软化性能,间接提高圆角插头的使用寿命。
10.作为优选,该黄铜的抗拉强度为500~550mpa,硬度hv5为140~170,延伸率为5~18%,导电率≥27%iacs。
11.作为优选,该黄铜的切削率为c3600的80%以上,冷铆开裂时压缩比在80%以上,经车削后,黄铜的表面粗糙度ra在1μm以下。
12.本发明所要解决的第二个技术问题是一种黄铜合金的制备方法。
13.本发明解决第二个技术问题所采用的技术方案为:一种黄铜合金的制备方法,其特征在于:包括以下制备步骤:
14.1)熔炼:按所需成分进行配料,熔炼温度控制在950~1000℃;
15.2)铸造:采用水平连铸,其中牵引节距:35~40mm;反推节距:1~3mm;牵引速度:10~20mm/s;反推速度1~3mm/s;
16.3)挤压:挤压温度为650~750℃,铸锭挤压比为350~600:1;挤压铸锭得到毛坯;
17.4)盘拉:毛坯加工率控制在40~65%,得到线坯;
18.5)退火:退火温度为300~420℃,加热时间60~150min。
19.6)联合拉拔:将线坯置于联合拉拔机进行拉伸,拉伸速率为40~80m/min,加工率控制在8~20%。
20.铸锭质量的好坏间接影响成品的质量,控制牵引节距、反推节距、牵引速率以及反推速率,能够在一定程度消除柱状晶粒,扩大等轴晶粒区域,使等轴晶粒区域占比达到60~90%,且平均晶粒尺寸在0.1~0.5mm范围。控制晶粒尺寸细小使得in元素分布更加弥散均匀,一定程度上改善切削性能。
21.挤压比控制在为350~600:1,挤压温度范围为650~750℃。较大的挤压比有利于控制挤压组织α相晶粒尺寸在10~30μm,合理的挤压温度有利于线坯正常挤压出料,同时控制α相比例在75~90%范围,提高材料的塑性和加工性能。
22.盘拉工序控制加工率在40~65%,相对较高的加工率有利于破碎晶粒,达到良好细晶效果,得到α相平均晶粒尺寸在5~20μm。
23.退火温度设置在300~420℃,组织β相比例降低,α相比例提升至85~98%。材料塑性提高,改善材料的冷铆性能。
24.联合拉拔工序控制加工率在8~20%。相对较低的加工率能够控制成品硬度在140~170hv范围,延伸率在5~18%。一方面有效控制成品棒材硬度,能够保证材料冷铆性能满足使用,同时后续无需进行成品低温退火,保证成品棒材直线度良好,满足车床高速加工要求和避免因退火软化出现变形和弯曲。
25.作为优选,所述步骤3)中,挤压前对铸锭进行加热,加热工艺分三阶段进行,预热阶段:温度控制在200~300℃,加热时间20~30min;加热阶段:温度控制在400~600℃,加热时间10~30min;保温阶段:650~750℃,加热时间10~30min。
26.挤压加热分三阶段进行,第一阶段主要起到铸锭预热作用,温度控制在200~300℃。较比于传统直接加热至高温的方式,能够尽可能维持原有组织形貌和大小,避免过热造成晶粒长大。第二阶段起到升温过渡作用,若温度设置过高,则造成铸锭升温过快,铸锭内
层与外层温度不一致(表面高,芯部低),降低组织均匀性。若温度设置过低,则加热至第三阶段温度上升幅度过大,不利于精准控制铸锭出炉温度。因此第二阶段温度控制在400~600℃,有利于铸锭芯部与表面温度保持一致,且间接有效控制铸锭出炉后温度偏差在5~15℃以内。第三阶段主要起到铸锭保温作用,控制铸锭加热温度在设定挤压温度范围之内。
27.作为优选,所述步骤5)中,退火工艺分二阶段进行,预热阶段:温度控制在150~250℃,升温时间5~20min;保温阶段:温度控制在300~420℃,加热时间60~150min。
28.退火工序采用阶梯退火,第一阶段退火温度设置在150~250℃,由于前道次拉伸加工率较大,材料开始错位回复且出现再结晶的趋势,内部组织结构基本不出现变化。第二阶段退火温度设置在300~420℃,组织β相比例降低,α相比例提升至85~98%。材料塑性提高,改善材料的冷铆性能。同时经过第一阶段低温回复退火,第二阶段退火后组织晶粒尺寸基本不变化,α相晶粒平均尺寸增幅<5μm。
29.与现有技术相比,本发明的优点在于:
30.1)本发明的黄铜合金采用低锡,锡含量在0.2~0.5wt%,相比较于高锡黄铜,基体中γ硬质相的含量降低,降低了车削时的损刀情况,添加一定量in元素,in类似pb,bi等元素具备一定易切削能力,且在一定条件下能够与sn元素结合形成γ-in低熔点脆性相,该γ-in低熔点脆性相弥散分布于α与β相界上,材料切削时热量产生,在该热量下将γ-in相熔化从而起到断削的作用,因此,弥补了低sn所产生的硬质相不足的问题,且更有利于断削而提高了材料的整体切削性;另外,由于γ硬质相的含量降低,材料的塑性增加,提高了材料的铆压性能;同时in元素能够增加材料临界电流密度,从而带来导电性能的提升。
31.2)本发明黄铜合金的抗拉强度为500~550mpa,硬度hv5为140~170,延伸率为5~18%,导电率≥27%iacs;切削率为c3600的80%以上,冷铆开裂时压缩比在80%以上,经车削后,黄铜的表面粗糙度ra在1μm以下,具备良好的切削、耐磨、导电、电镀性能,满足圆角插头加工、使用要求。
附图说明
32.图1为本发明实施例1的车削屑末形貌。
33.图2为本发明对比例的车削屑末形貌。
具体实施方式
34.以下结合附图实施例对本发明作进一步详细描述。
35.本发明提供4个实施例和1个对比例,具体成分见表1。
36.实施例1
37.1)熔炼:按所需成分要求配比,使用原料包括电解板,铟锭,锡锭,纯镍,锌锭,镧铈合金。原料依次加入工频炉内升温,熔炼温度控制在990℃。
38.2)铸造:采用水平连铸工艺生产铸锭,其中牵引节距:35mm;反推节距:2mm;牵引速度:12mm/s;反推速度2mm/s。铸锭规格为:φ145mm。
39.3)挤压:挤压前对铸锭进行加热,加热工艺分三阶段进行。预热阶段:温度控制在300℃,加热时间25min;加热阶段:温度控制在600℃,加热时间30min;保温阶段:710℃,加热时间30min。使用1800t挤压机挤压规格为φ8mm的毛坯。
40.4)盘拉:毛坯酸洗后使用倒立式盘拉机拉伸,加工率为60%。拉伸后线坯规格为φ5mm
41.5)退火:拉伸后的线坯置于井式炉内退火,退火工艺分二阶段进行,预热阶段:温度控制在150℃,升温时间15min;保温阶段:温度控制在380℃,加热时间120min。
42.6)联合拉拔:将坯料置于2t联合拉拔机进行拉伸。拉伸速率为60m/min,加工率为9%,成品规格为φ4.77mm。
43.7)矫直定尺:成品棒材进行矫直定尺,包装入库。
44.实施例2
45.1)熔炼:按所需成分要求配比,使用原料包括电解板,铟锭,锡锭,纯镍,锌锭,金属镁。原料依次加入工频炉内升温,熔炼温度控制在980℃。
46.2)铸造:采用水平连铸工艺生产铸锭,其中牵引节距:36mm;反推节距:2mm;牵引速度:14mm/s;反推速度2mm/s。铸锭规格为:φ145mm。
47.3)挤压:挤压前对铸锭进行加热,加热工艺分三阶段进行。预热阶段:温度控制在280℃,加热时间25min;加热阶段:温度控制在580℃,加热时间30min;保温阶段:680℃,加热时间20min。使用1800t挤压机挤压规格为φ7.5mm的毛坯。
48.4)盘拉:毛坯酸洗后使用倒立式盘拉机拉伸,加工率为52%。拉伸后线坯规格为φ5.2mm
49.5)退火:拉伸后的线坯置于井式炉内退火,退火工艺分二阶段进行,预热阶段:温度控制在160℃,升温时间20min;保温阶段:温度控制在400℃,加热时间90min。
50.6)联合拉拔:将坯料置于2t联合拉拔机进行拉伸。拉伸速率为50m/min,加工率为16%,成品规格为φ4.77mm。
51.7)矫直定尺:成品棒材进行矫直定尺,包装入库。
52.实施例3
53.1)熔炼:按所需成分要求配比,使用原料包括电解板,铟锭,锡锭,纯镍,锌锭,金属锰和铜锆合金。原料依次加入工频炉内升温,熔炼温度控制在1000℃。
54.2)铸造:采用水平连铸工艺生产铸锭,其中牵引节距:38mm;反推节距:2mm;牵引速度:12mm/s;反推速度2mm/s。铸锭规格为:φ145mm。
55.3)挤压:挤压前对铸锭进行加热,加热工艺分三阶段进行。预热阶段:温度控制在300℃,加热时间30min;加热阶段:温度控制在580℃,加热时间20min;保温阶段:680℃,加热时间25min。使用1800t挤压机挤压规格为φ7.8mm的毛坯。
56.4)盘拉:毛坯酸洗后使用倒立式盘拉机拉伸,加工率控制在54%。拉伸后线坯规格为φ5.3mm
57.5)退火:拉伸后的线坯置于井式炉内退火,退火工艺分二阶段进行,预热阶段:温度控制在180℃,升温时间12min;保温阶段:温度控制在360℃,加热时间150min。
58.6)联合拉拔:将坯料置于2t联合拉拔机进行拉伸。拉伸速率为50m/min,加工率控制在19%,成品规格为φ4.77mm。
59.7)矫直定尺:成品棒材进行矫直定尺,包装入库。
60.实施例4
61.1)熔炼:按所需成分要求配比,使用原料包括电解板,铟锭,锡锭,纯镍,锌锭。原料
依次加入工频炉内升温,熔炼温度控制在990℃。
62.2)铸造:辅助使用电磁搅拌设备,采用水平连铸工艺生产铸锭,其中牵引节距:35mm;反推节距:2mm;牵引速度:12mm/s;反推速度2mm/s。铸锭规格为:φ145mm。
63.3)挤压:挤压前对铸锭进行加热,加热工艺分三阶段进行。预热阶段:温度控制在300℃,加热时间30min;加热阶段:温度控制在600℃,加热时间30min;保温阶段:700℃,加热时间20min。使用1800t挤压机挤压规格为φ8mm的毛坯。
64.4)盘拉:毛坯酸洗后使用倒立式盘拉机拉伸,加工率为61%。拉伸后线坯规格为φ5.0mm
65.5)退火:拉伸后的线坯置于井式炉内退火,退火工艺分二阶段进行,预热阶段:温度控制在220℃,升温时间16min;保温阶段:温度控制在390℃,加热时间120min。
66.6)联合拉拔:将坯料置于2t联合拉拔机进行拉伸。拉伸速率为60m/min,加工率为9%,成品规格为φ4.77mm。
67.7)矫直定尺:成品棒材进行矫直定尺,包装入库。
68.对比例
69.1)熔炼:按所需成分要求配比,使用原料包括黄铜角料,紫铜角料,黄铜镀锡角料,黄铜镀镍角料,铜铁中间合金,金属硅,铜磷合金。原料依次加入工频炉升温,熔炼温度为1020℃。
70.2)铸造:采用半连铸铸造工艺,铸造温度为1000℃。得到铸锭规格为:φ145mm。
71.3)挤压:使用1800t挤压机挤压规格为φ6.4mm的毛坯。挤压温度为600℃。
72.4)均匀化退火:对挤压坯进行均匀化退火,退火温度为500℃,保温3h。
73.5)盘拉:毛坯酸洗后使用倒立式盘拉机拉伸,加工率为31%。拉伸后线坯规格为φ5.3mm。
74.6)退火:对线坯进行软化退火,退火温度为400℃,升温30min,保温240min。
75.7)成品拉伸:毛坯酸洗后使用2t联合拉拔机进行拉伸。拉伸速率为50m/min,加工率为20%,成品规格为φ4.77mm。
76.8)矫直定尺:成品棒材进行矫直定尺,包装入库。
77.对得到的实施例和对比例进行相关检测,具体见表2、表3。
78.力学性能检测:按照《gb/t 228.1-2010金属材料拉伸试验第1部分:室温试验方法》在电子万能力学性能试验机上进行,采用宽度为12.5mm的带头试样,拉伸速度为5mm/min。
79.导电率检测:按照《gb/t 3048.2-2007电线电缆电性能试验方法第2部分:金属材料电阻率试验》,本检测仪器为zfd微电脑电桥直流电阻测试仪,样品宽度为20mm,长度为500mm。
80.微观组织检测:根据ys/t 347-2004《铜及铜合金平均晶粒度测定方法》和ys/t449-2002《铜及铜合金铸造和加工制品显微组织检验方法》对材料微观组织性能进行评定。前者主要用于平均晶粒度评定,后者主要用于相面积含量评定
81.切削指数:根据ys-t 647-2007《铜锌铋碲合金棒》附录b中切削性能检测方法进行评定,设c36000(hpb63-3)的切削指数为100%。
82.表面粗糙度测试条件:参考gb/t 1031-2009《表面结构轮廓法表面粗糙度参数及
其数值》,使用表面粗糙度测量仪对车削后棒材表面进行测量。
83.所测表面粗糙度ra值越低,说明样品表面越光滑,间接说明材料切削性能优异,同时也有利于提高材料电镀性能。
84.冷铆测试条件:φ4.77mm棒材在数控车床上加工至长30mm的端子、端子铆接端钻内径φ3.0mm、深度6mm的孔,铆接端在端子铆压测试机缓慢施加1~3kn压力,直至φ3.0孔壁出现裂纹时停止施加压力,记录铆压开裂时孔外径变化的压缩比。在同等冷铆测试条件下,冷铆开裂时压缩比越大,说明材料冷铆性能越好。
85.车削测试条件:在数控车床上进行,其中车床转速为2000r/min,进刀量0.2mm,进给速度50mm/min。
86.表1本发明实施例和对比例的成分/wt%
87.编号cuinsnnipbzn其他实施例162.50.660.320.110.08余0.03la+0.03ce实施例261.80.570.290.220.09余0.04mg实施例362.40.740.350.180.07余0.05zr+0.02mn实施例463.10.760.330.100.07余 对比例58.6/0.820.0430.06余0.01fe+0.31si+0.1p
88.表2本发明实施例和对比例的微观组织及力学性能
[0089][0090]
表3本发明实施例和对比例的性能
[0091]