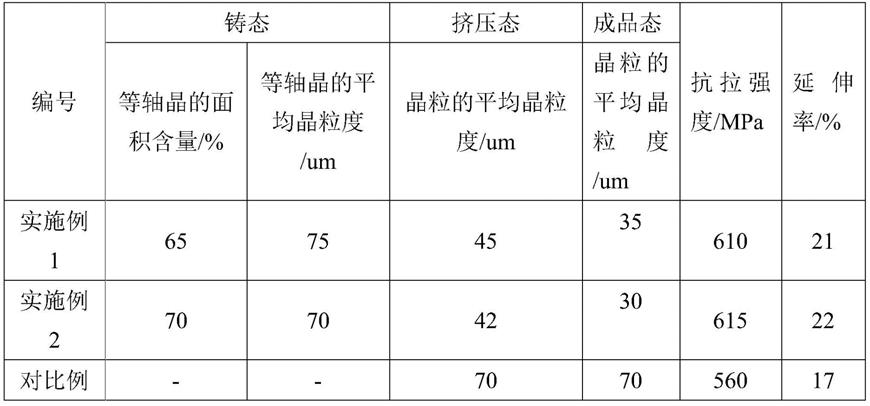
1.本发明涉及一种黄铜线材的制备方法。
背景技术:
2.复杂黄铜属于以铜,锌为主要元素,同时加入镍,铁,锰,硅,铝,铅等金属中的一种或多种,获得优于普通黄铜的耐磨性,耐蚀性,强度,硬度,切削性的合金材料,其广泛被用于船舶及化工零件,如冷凝管、齿轮、螺旋桨、轴承、衬套及阀体等,电子电器零件,如连接器、接插件、螺丝等,因此使得复杂黄铜的开发具备很强的材料应用针对性,而c6782合金线材就是其中一种。
3.目前生产的c6782合金线材主要采用配料
→
铸造
→
挤压
→
拉丝
→
退火
→
酸洗,重复拉丝
→
退火
→
酸洗,至到成品规格。采用该工艺可以生产出力学性能满足要求的合金线材(日本标准jis3250,抗拉强度490mpa以上,延伸率10%以上),但是该工艺中存在多次退火,生产出的线材晶粒粗大,硬度不均匀,相组织存在局部不均匀性,直接导致客户在使用时存在打孔排屑困难,切削困难,折弯性能差,耐腐蚀性能差。而导致多次退火的主要原因在于,挤压后线材组织不均匀,力学性能存在各向异向,拉丝过程中,线材的力学性能也存在各向异向,如果不进行退火,将在拉丝过程中产生断裂。而挤压后线材组织不均匀与铸造时铸锭组织的不均匀存在很大的关系,因此,获得组织均匀的铸锭组织至关重要。
4.因此,针对c6782合金线材的制备工艺需要进一步改进。
技术实现要素:
5.本发明所要解决的技术问题是提供一种线材晶粒细小从而获得力学性能、易切削、折弯性能以及耐腐蚀性能优良的黄铜线材的制备方法。
6.本发明解决上述技术问题所采用的技术方案为:一种黄铜线材的制备方法,其特征在于:该黄铜的质量百分比组成为cu:55%~62%,mn:0.5%~1.5%,fe:0.2%~0.5%,al:0.3%~0.8%,pb:0.2%~0.5%,余量为zn和不可避免的杂质;工艺流程包括:配料
→
熔炼
→
半连铸
→
挤压
→
联合拉拔;所述配料包括按照成分配比所需的光亮线、锌锭、电解锰、铁铜合金、铝丝;所述熔炼包括以下制备步骤:
7.1)逐渐调高电压至400v将炉体升温,加入光亮线和铁铜合金,用煅烧木炭覆盖,升温直至全部熔化;
8.2)电压降至200v,熔体温度控制在1100℃~1120℃,分批次加入电解锰,后加入铝丝;
9.3)温度降低到1060℃~1080℃,加入锌锭,完成溶解,搅拌均匀捞渣;
10.4)取样,光谱化验成分至合格;
11.5)加入精炼剂、除渣剂,精炼完成后温度控制在980℃~1000℃;
12.6)成分复样;
13.7)熔体温度升至1000℃~1080℃,喷火5~15s。
14.作为优选,所述半连铸具体工艺为:熔体处于还原气氛中,通过浇管进入结晶器内,铸造温度为1030~1080℃,拉铸速度为200~300r/min。
15.作为优选,所述结晶器下方设置有二次冷却水套,铸锭出结晶器后进入二次冷却水套,二次冷却水套的冷却水从上到下分三层,每层冷却水通过沿二次冷却水套周向上间隔开设的多个进水孔流入,每层冷却水的水压保持在0.15~0.2mpa,且从上到下水压依次增大,上层冷却水距离结晶器出口50mm~100mm,冷却水与铸锭径向之间的夹角为45
°
~50
°
;中层冷却水距离结晶器出口80mm~200mm,冷却水与铸锭径向之间的夹角为50
°
~55
°
;下层冷却水距离结晶器出口200mm~400mm,冷却水与铸锭径向之间的夹角为55
°
~60
°
。
16.二次冷却水可以极大减轻铸锭组织应力,消除铸锭内部存在的裂纹,避免挤压线材开裂,同时多层冷却水可以通过阶梯冷却在保证更低的铸造应力的同时,可以有更加长程的冷却梯度,铸锭轴向更大的过冷度,保证更多、更细的轴向晶。
17.随着铸锭出结晶器,依次经过三层冷却水,三层冷却水的水压和喷射角度不同,在铸锭的同一部位所产生的冷却效果也不相同,随着角度的加大冲击铸锭的方向剪切力减小,沿着铸锭轴向的水压加大,附着在铸锭的水量加大,加快冷却,形成轴向长程冷却梯度,获得大量的轴向等轴晶,明显细化组织晶粒,均匀组织。
18.作为优选,所述半连铸铸锭的微观组织中,等轴晶的面积含量在60%以上,所述等轴晶的平均晶粒度为70~80um。
19.作为优选,所述挤压温度650℃~680℃。680℃以上会使得挤压线材晶粒出现长大,低于650℃挤压线材表面出现丝线,毛糙等问题。
20.作为优选,所述挤压后线坯的微观组织中,晶粒的平均晶粒度为40~50um。
21.作为优选,该黄铜线材的平均晶粒度≤40um。
22.与现有技术相比,本发明的优点在于:
23.1)本发明通过控制熔炼工艺,获得成分均匀的熔体,为后续的半连铸获得组织均匀的铸锭做好准备工作,从而使得挤压后可直接联合拉拔,而省去传统工艺中的中间退火,避免了材料晶粒粗大,相组织分布不均,物理力学性能呈现各向异性,从而获得优良的力学性能、易切削、折弯性能以及耐腐蚀性能。
24.2)该黄铜线材的平均晶粒度≤40um,黄铜合金的晶粒得到了细化,因此,材料的强度和塑性都得到了提高,该黄铜线材的抗拉强度在600mpa以上,延伸率在20%以上,且易切削、折弯性能以及耐腐蚀性能优良。
附图说明
25.图1为本发明实施例1的铸态的微观组织;
26.图2为本发明实施例1的挤压态的微观组织;
27.图3为发明实施例2的铸态的微观组织;
28.图4为本发明实施例2的挤压态的微观组织;
29.图5为本发明对比例的铸态的微观组织;
30.图6为本发明对比例的挤压态的微观组织。
具体实施方式
31.以下结合附图实施例对本发明作进一步详细描述。
32.实施例1
33.黄铜成分:cu 58.6%,mn 1.25%,fe 0.5%,al 0.5%,pb 0.45%,zn余量。
34.规格φ6.0mm黄铜线材的具体生产过程如下:
35.a、配料:包括光亮线、锌锭、电解锰、铁铜合金、铝丝;
36.b、熔炼,具体包括以下制备步骤:
37.1)逐渐调高电压至400v将炉体升温,加入光亮线和铁铜合金,用煅烧木炭覆盖,升温直至全部熔化;
38.2)电压降至200v,熔体温度控制在1100℃~1120℃,分批次加入电解锰,后加入铝丝;
39.3)温度降低到1060℃~1080℃,加入锌锭,完成溶解,搅拌均匀捞渣;
40.4)取样,光谱化验成分至合格;
41.5)加入精炼剂、除渣剂,精炼完成后温度控制在980℃~1000℃;
42.6)成分复样;
43.7)熔体温度升至1000℃~1080℃,喷火5~15s。
44.c、半连铸:熔体处于还原气氛中,通过浇管进入结晶器内,铸造温度为1030~1080℃,拉铸速度为200r/min。结晶器下方设置有二次冷却水套,铸锭出结晶器后进入二次冷却水套,二次冷却水套的冷却水从上到下分三层,每层冷却水通过沿二次冷却水套周向上间隔开设的多个进水孔流入,牵引拉铸开始后,开启二次冷却水,上层冷却水的水压为0.15mpa,中层冷却水的水压为0.17mpa,下层冷却水的水压为0.2mpa。上层冷却水距离结晶器出口80mm,冷却水与铸锭径向之间的夹角为45
°
~50
°
;中层冷却水距离结晶器出口100mm,冷却水与铸锭径向之间的夹角为50
°
~55
°
;下层冷却水距离结晶器出口200mm,冷却水与铸锭径向之间的夹角为55
°
~60
°
,铸锭直径φ145mm。
45.d、采用1250挤压机,铸锭经过燃气加热炉加热至640℃,转移至中频保温炉,保温温度设置在670℃,铸锭可以均匀加热铸锭内部和外部,出中频炉,挤压毛坯φ6.4mm。
46.e、酸洗采用hcl+fecl3+h2o体系清洗,清洗采用酸洗
→
清洗
→
冲洗
→
肥皂水洗。
47.f、拉丝直接采用拉拔机生产,拉丝速度在80~120m/min,拉丝工艺为φ6.4mm
→
6.0mm。
48.实施例2
49.黄铜成分:cu 58.6%,mn 1.15%,fe 0.45%,al 0.5%,pb 0.41%,zn余量。
50.规格φ10.5mm黄铜线材的具体生产过程如下:
51.a、配料:包括光亮线、锌锭、电解锰、铁铜合金、铝丝;
52.b、熔炼,具体包括以下制备步骤:
53.1)逐渐调高电压至400v将炉体升温,加入光亮线和铁铜合金,用煅烧木炭覆盖,升温直至全部熔化;
54.2)电压降至200v,熔体温度控制在1100℃~1120℃,分批次加入电解锰,后加入铝丝;
55.3)温度降低到1060℃~1080℃,加入锌锭,完成溶解,搅拌均匀捞渣;
56.4)取样,光谱化验成分至合格;
57.5)加入精炼剂、除渣剂,精炼完成后温度控制在980℃~1000℃;
58.6)成分复样;
59.7)熔体温度升至1000℃~1080℃,喷火5~15s。
60.c、半连铸:熔体处于还原气氛中,通过浇管进入结晶器内,铸造温度为1030~1080℃,拉铸速度为280r/min。结晶器下方设置有二次冷却水套,铸锭出结晶器后进入二次冷却水套,二次冷却水套的冷却水从上到下分三层,每层冷却水通过沿二次冷却水套周向上间隔开设的多个进水孔流入,牵引拉铸开始后,开启二次冷却水,上层冷却水的水压为0.15mpa,中层冷却水的水压为0.17mpa,下层冷却水的水压为0.2mpa。上层冷却水距离结晶器出口100mm,冷却水与铸锭径向之间的夹角为45
°
~50
°
;中层冷却水距离结晶器出口150mm,冷却水与铸锭径向之间的夹角为50
°
~55
°
;下层冷却水距离结晶器出口250mm,冷却水与铸锭径向之间的夹角为55
°
~60
°
,铸锭直径φ145mm。
61.d、采用1250挤压机,铸锭经过燃气加热炉加热至640℃,转移至中频保温炉,保温温度设置在680℃,铸锭可以均匀加热铸锭内部和外部,出中频炉,挤压毛坯φ11.4mm。
62.e、酸洗采用hcl+fecl3+h2o体系清洗,清洗采用酸洗
→
清洗
→
冲洗
→
肥皂水洗。
63.f、拉丝直接采用拉拔机生产,拉丝速度在100m/min,拉丝工艺为φ11.4mm
→
10.5mm。
64.对比例的成分为:cu 58.8%,mn 1.35%,fe 0.4%,al 0.55%,pb 0.5%,zn余量。工艺流程为配料
→
铸造
→
挤压
→
拉丝
→
退火
→
酸洗,规格φ11.2mm的线材的具体生产步骤为:
65.a、配料:包括光亮线、锌锭、电解锰、铁铜合金、铝丝;
66.b、熔炼,将配料一次性加入到熔炼炉中进行熔炼,用煅烧木炭覆盖,升温直至全部熔化,加入精炼剂,除渣剂,精炼完成,温度在980℃~1000℃,温度升至1050℃,喷火10s左右。
67.c、半连铸:熔体处于还原气氛中,通过浇管进入结晶器内,铸造温度为1030~1080℃,拉铸速度为280r/min,铸锭直径φ145mm。
68.d、采用1250挤压机,挤压毛坯φ13.8mm,挤压温度680℃。
69.e、酸洗采用hcl+fecl3+h2o体系清洗,清洗采用酸洗
→
清洗
→
冲洗
→
肥皂水洗。
70.f.拉丝直接采用拉拔机生产,拉丝速度在80~120m/min,拉丝工艺为φ13.8mm
→
酸洗
→
φ12.5
→
退火530℃+3h
→
酸洗
→
φ11.2
→
退火270℃+4h。
71.对得到的两个实施例和1个对比例进行微观组织和力学性能检测。
72.力学性能检测:按照《gb/t 228.1-2010金属材料拉伸试验第1部分:室温试验方法》在电子万能力学性能试验机上进行,采用宽度为12.5mm的带头试样,拉伸速度为5mm/min。
73.晶粒度检测:按照ys/t 347-2004晶粒度平均尺寸测试试验第5部分,在单位面积内,采用比较法,面积法,截距法测试金相的晶粒度
74.切削性检测:采用数控车床,单边切削量2mm,转速1000r/min,进刀速到10mm/min,按照hpb63-3切削性100%进行比对。
75.折弯性能检测:按照gb/t 238-2013金属线材折弯性能第六部分:室温23℃
±
5℃,
将线材固定位置,设定一定折弯区域,然后90
°
弯曲,重复双折弯。
76.抗脱锌检测:按照gb/t 10119-2008黄铜材料耐脱锌性能测试第6部分,采用水浴锅,采用氯化铜溶液浸泡试样,浸泡溶液的量按照250ml/100mm2配置,溶液温度75℃
±
2℃,时间24h。
77.参见图1、图3所示,本实施例铸态的微观组织为等轴晶,等轴晶的面积含量在60%以上,等轴晶的平均晶粒度为70~80um;参见图2、图4所示,本实施例挤压态的微观组织的晶粒的平均晶粒度为40~50um。参见图5所示,对比例铸态的微观组织为条形的枝晶,参见图6所示,挤压态晶粒的平均晶粒度为70um,相对于本发明铸态组织的平均晶粒度,因此,材料的各向异向严重,后续拉丝过程中需退火才能达到所需尺寸。
78.表1本发明实施例和对比例的微观组织和力学性能
[0079][0080]
表2本发明实施例和对比例的机械性能
[0081]
编号切削性能/%折弯性能抗脱锌/um实施例145不断裂60实施例240不断裂70对比例22断裂200