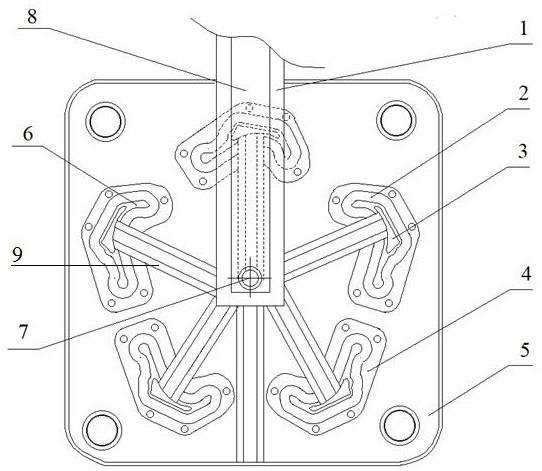
1.本发明涉及铝合金铸造设备,具体是一种可多根同时铸造的异形铝合金铸锭结晶装置。
背景技术:
2.铝合金铸锭制备是铝加工材生产的头道工序,主要是为铝加工材后续挤压、轧制、锻造等热加工变形过程提供原材料坯料,目前铝合金铸锭截面形状主要以尺寸规则的圆形、矩形和空心圆三种为主,以易于后续热加工变形。近年来,随着铝合金锻件产品的应用领域拓展,需求量不断增大,对锻件变形坯料的需求也越来越大。由于铝合金锻件产品往往为非规则形状,为减少加工环节、控制锻件产品的组织性能,近年来发展了一种采用半连续铸造方式直接铸造截面形状接近锻件终端尺寸,形状不规则铸锭的半连续铸造新方式。公开号为cn103978170a的中国专利申请,公布了一种铝合金近终形铸锭用半连续铸造结晶器,该结晶器提供了非规则形状近终形铸锭的铸造装备设计方式,铸锭可无需挤压成坯而直接锻造加工变形,为锻件生产提供了一种新工艺形式。
3.采用半连续铸造方式制备非规则截面形状铸锭的难点和关键环节主要包括:
①
相比于形状规则的圆形和矩形铸锭,异形的非规则面铸锭内部不同区域间的冷却强度差异较大,冷却强度不一致;
②
铸锭成型和质量控制难度要求显著提高,工艺控制不当极易导致锭坯出现通心开裂、表面挂瘤、冷隔成层等严重质量缺陷,甚至无法顺利成型;
③
生产中为实现工业化规模适用性,即综合平衡制备成本和质量控制,往往需要满足多根铸锭同时制备并且每根铸锭质量一致的控制要求,这就给铸造过程中各个铸锭的熔体均匀分配、冷却差异控制以及内部冶金质量等要素带来了极大挑战,导致多根同时铸造过程无法实现或同铸次之间铸锭质量差异大,综合成品率极低。
技术实现要素:
4.为了解决上述问题,本技术提供了一种异形铝合金铸锭结晶装置,结晶器为多组设置,生产效率高,对非规则形状的铝合金铸锭熔体能够均匀分配、冷却,保证铸锭产品质量。本发明采用的技术方案如下:一种可多根同时铸造的异形铝合金铸锭结晶装置,包括熔体流槽和数个结晶器单元;所述结晶器单元包括保温顶、结晶器和与结晶器匹配的引锭底座,所述保温顶设于结晶器上方,所述结晶器的中心设有铸锭的成型腔,所述引锭底座包括结晶器的成型腔配合的座体;所述熔体流槽的出口端分别经由等长的分流槽连通各个结晶器单元,所述熔体流槽位于分流槽的上部。
5.上述可多根同时铸造的异形铝合金铸锭结晶装置,所述熔体流槽的出口端设有分流口,所述分流口与分流槽分别连通,所述结晶器单元以分流口为中心呈圆周布置。
6.上述可多根同时铸造的异形铝合金铸锭结晶装置,所述结晶器的底部设有数个导向柱,所述导向柱相对结晶器向外延伸倾斜设置;所述座体的侧面设有数个向外延伸倾斜设置的导向杆,所述导向杆的设置位置与导向柱一一对应,每对所述导向杆内侧面与导向柱的外侧面可贴近配合。
7.上述可多根同时铸造的异形铝合金铸锭结晶装置,所述引锭底座的底面可滑动与平台连接。
8.上述可多根同时铸造的异形铝合金铸锭结晶装置,所述座体的顶部设有倒锥形的引导头,所述引导头比座体顶部表面高2~20mm,引导头的上下直径差为0.5~10mm。
9.上述可多根同时铸造的异形铝合金铸锭结晶装置,所述结晶器单元还包括对应于结晶器的成型腔设置的分流盘,所述分流盘连通分流槽的出口端,所述分流盘设在保温顶内且两者底面平齐。
10.上述可多根同时铸造的异形铝合金铸锭结晶装置,所述分流盘设有入流口、侧壁出口和底面出口,铝熔体经入流口流入后再通过侧壁出口和底面出口进入结晶器内,所述底面出口采用网袋结构。
11.上述可多根同时铸造的异形铝合金铸锭结晶装置,所述结晶器侧壁上设有若干个用于输送冷却水水孔,所述水孔连通水箱与成型腔,所述水孔沿成型腔的外周轮廓均匀分布;若干个所述水孔出水端口内设有可拆卸的堵塞。
12.上述可多根同时铸造的异形铝合金铸锭结晶装置,所述结晶器的成型腔上端口边缘设有若干用于润滑油流入的溢流孔,每个溢流孔面积为1.5 ~ 5.5mm2,相邻两个溢流孔的间距5~35mm。
13.本发明的有益效果:其一,多个结晶器均独立设置,利用连通器原理可实现多个结晶器内金属液面高度一致,实现一次成型多个铸锭,提高生产效率。
14.其二,结晶器以分流口为中心呈圆周布置,使液态金属流入各个结晶器的长度一致,确保铸造过程中金属流入各结晶器入口端的温降一致,保证铸锭质量。
15.其三,结晶器水孔采用未封堵和封堵的联合冷却方式来调整铸锭因截面形状变化而带来的异形结晶器不同区域间冷却强度差异,实现各区域冷却强度值均匀一致。
16.其四,结晶器底部和引锭底座外侧对应设计导向柱和导向杆,通过摩擦力实现引锭底座配合结晶器的自动对中功能,减小了人工手动调整的工作量。
17.其五,引锭底座中心设计成倒锥形圆台引导头,既能提供铸造初始阶段对铸锭的牵引力,使其顺利移出结晶器,同时也便于铸造结束后铸锭与引锭底座的吊装脱离。
附图说明
18.图1为本发明实施例一的俯视示意图;图2为本发明实施例一的竖向截面剖切的结构示意图;图3为本发明实施例一的分流盘俯视结构示意图;图4为本发明实施例一的单个结晶器俯视结构示意图;图5为本发明实施例一的单个结晶器竖向截面剖切的局部示意图;
图6为本发明实施例一的水孔封堵原理示意图;图7为本发明实施例一的引锭底座俯视结构示意图;图8为本发明实施例一的引锭底座竖向截面剖切的结构示意图。
19.图9为本发明实施例二的俯视示意图;图10为本发明实施例二的单个结晶器俯视结构示意图。
20.图中:熔体流槽1、保温顶2、分流盘3、结晶器4、水箱5、引锭底座6、分流口7、铝熔体8、分流槽9、入流口3-1、侧壁出口3-2、底面出口3-3、润滑油腔4-1、水孔4-2、堵塞4-3、导向柱4-4、内壁4-5、定位孔4-6、水槽4-7、溢流孔4-1-1、座体6-1、引导头6-2、导向杆6-3、滑块6-4。
具体实施方式
21.本发明是一种可多根同时铸造的异形铝合金铸锭结晶装置,设有多个结晶器,实现同时制备多个异形、非规则形状的铝合金铸锭。结晶器4的数量可以根据实际需求设定。下面通过两个实施例,结合附图对本发明进一步解释说明。
22.实施例一如图1所示,所需铝铸锭是非规则的截面形状,本实施例的结晶装置包括熔体流槽1、五个保温顶2、五个分流盘3、五组结晶器4、五个引锭底座6、分流口7和五个分流槽9。每组结晶器4铸造成型的铝锭形状可参考图4所显示的结晶器4的成型腔。每组结晶器4上方均设有保温顶2,结晶器4的下方一一对应有引锭底座。
23.熔体流槽1用于向结晶器4内输送铝熔体8,其出口端设有分流口7。五组结晶器4以分流口7为中心呈圆周布置,分流口7与各组结晶器4之间的距离相同。铝熔体8经熔体流槽1到达分流口7,依据连通器原理,在分流口7处铝熔体8均匀分流,经各个分流槽9流入设于其末端的分流盘3。
24.分流盘3设在保温顶2内,且分流盘3底面与保温顶2底面平齐。如图3所示,分流盘3为耐高温硬质网袋结构,铝熔体8经入流口3-1后分别经侧壁出口3-2和网袋式的底面出口3-3进入结晶器4内。分流盘3的作用是使高温铝熔体8均匀流向异形结晶器4内,确保铸锭周围各位置的流入温度一致,避免因截面形状变化和铝熔体8流量流速变化导致流入结晶器4内不同区域温度出现波动差异。
25.结晶器4采用铝合金材质,再结合图2所示,结晶过程是在水箱5内完成的,因此结晶器4整体设于水箱5内,具体是通过定位孔4-6安装在水箱5平台上,如此共用水箱5中的冷却水以确保各结晶器4内冷却水的压力和流量同时变化,保持各个铸锭质量一致性。结晶器4的内腔即为铝合金铸锭的成型腔。结晶器4的顶部设有润滑油腔4-1、侧部设有若干水孔4-2、底部设有数个向外倾斜的导向柱4-4。
26.润滑油腔4-1与结晶器4成型腔顶部的交界处设有若干溢流孔4-1-1,润滑油经溢流孔4-1-1沿结晶器4成型腔的内壁4-5均匀下滑并形成一层连续油膜,用于润滑铸锭的表面。单个溢流孔4-1-1面积1.5 ~ 5.5mm2,相邻两个溢流孔4-1-1间距5mm~35mm,内壁4-5的表面粗糙度为ra 1.0μm~ra 2.0μm。
27.结合图4,水孔4-2分布在结晶器4的成型腔的外周,直径为ф1.2mm~ф8.5mm,水孔4-2相对于铸锭中心线即竖直方向的倾斜角度为 20
˚
~70
˚
。如此水箱5内的冷却水,便可经
水槽4-7、水孔4-2实现对铝熔体8的冷却结晶成型。
28.如图5所示,在结晶器4的内壁4-5的下端与水孔4-2末端交界处设置一个小锥面,即可设置堵塞4-3,用于堵住水孔4-2。图4中显示,实心圆点处即为设置了堵塞4-3,有连续封堵,也有单个封堵。通过封堵结晶器4内不同区域的冷却水孔4-2,实现对不同区域冷却强度值的调整,进而保证铸造顺利。结晶器4各个区域冷却强度的要求与铸造合金品种和铸造工艺相关,采用堵塞4-3则可以根据铸锭形状变化、工艺要求等灵活调整不同区域的冷却强度值。参考图6,水孔4-2封堵规则如图6所示,结晶器4内任意一个水孔a,与其左右相邻的两个水孔b、水孔c分别连线,当线段ab与线段ac面向铸锭一侧形成的夹角小于155
°
时,则孔a封堵。
29.引锭底座6采用合金钢经机械加工制成。结合图7和图8,引锭底座6侧面外围设计若干导向杆6-3以与导向柱4-4对应配合。在铸造开始前,如图2所示,导向杆6-3紧密贴合导向柱4-4,并利用机械摩擦力推动引锭底座6在水平方向相对移动,实现与结晶器4的自动配合和对中,对中后座体6-1外边缘与内壁4-5之间的间隙范围为1~5mm,既能防止两者磕碰,又防止铝熔体8漏流,提高生产效率和铸锭精度。
30.引锭底座6顶部设有倒锥形的引导头6-2,引导头6-2比座体6-1顶部表面高2~20mm,引导头6-2的上下直径差为0.5~10mm。倒锥形的引导头6-2既能够保证铸造初始阶段其对铸锭保持足够大的拉力,使铸造过程顺利进行,同时在铸造结束后也能防止铸锭无法与引锭底座6顺利脱离的现象,保证生产连续性和铸锭质量。
31.引锭底座6底部设有滑块6-4,能够使引锭底座6在引锭平台的水平方向上自由移动。
32.实施例二本实施例针对另一种异形形状的铝合金铸锭设置的结晶装置,参考图9和图10。除铸锭外形不同外,该结晶装置在结构上与实施例一的主要区别在于:1)结晶器4形状和单元数量不同:针对本实施例的铸锭形状,设置了四组异形的结晶器单元,结晶器单元的分布依旧是以分流口7为中心呈圆周布置,四组结晶器单元为左右上下对称设置。
33.2)水孔4-2的设置不同:本实施例在结晶器4的成型腔外周设有内外两排水孔4-2,并且内外两排水孔4-2 的倾斜角度不同,两者角度差为10
˚
~50
˚
。如此设计,在铸造过程中冷却内外两排水孔4-2流出的水柱呈交错且无交汇状态冲击到铸锭表面,形成强烈冷却作用。同时,依据该铸锭形状变化,采用交错封堵和连续封堵的配合方式来调整结晶器4内不同区域的冷却强度值。
34.本实施例的结晶装置在其余结构和使用原理上,与实施例一相同。
35.上述两个实施例中,结晶装置的铸造原理为:a)铝熔体8经熔体流槽1到达分流口7,在分流口7处铝熔体8均匀分流,经各个分流槽9流入设于其末端的分流盘3;b)铝熔体8经分流盘3均匀流入结晶器4的成型腔内;c)内壁4-5上已覆盖有润滑油,引导头6-2将铝熔体8引入成型腔,冷却水经水孔4-2冲击到铸锭表面使其结晶成型。