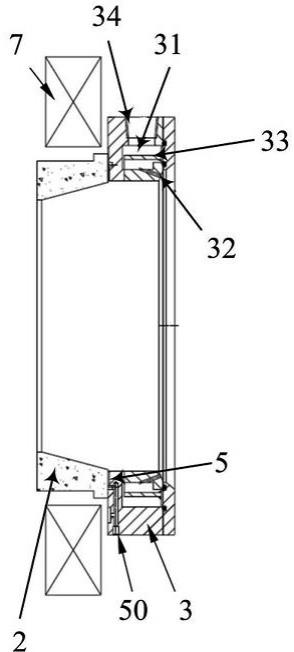
1.本发明涉及铸造技术领域,尤其涉及一种铝合金铸锭水平连铸设备。
背景技术:
2.目前,铝合金铸锭主要通过立式半连续铸造技术生产。同立式铸造相比,水平连铸技术具有投资少、成材率高、安全系数高、能够实现真正的连续铸造等优势,在铝合金铸锭生产方面具有很好的应用前景。但水平连铸存在的若干问题影响了该技术的应用推广。比较显著的问题有两个,一是由于重力的作用,使铸锭在横截面上受到的冷却不均匀,从而导致铸锭组织性能的差异,这一点在大规格铸锭的生产过程中表现的尤为明显;二是水平连铸生产持续时间远比立式铸造要长,如何在长时间的铸造过程中实现连续稳定的润滑也是一个难点。
3.国内外有多项专利旨在解决上述问题。专利cn200410020665.5提出了一种用于铝合金、镁合金低频电磁场水平连续铸造工艺,该工艺在铸造过程引入电磁场作用,通过磁场与熔体的交互作用达到细化晶粒、均匀组织的目的。但该工艺没有解决铸造过程中的连续润滑问题,在长时间连续铸造过程中难以保证铸锭的表面质量。美国专利us7077186提出了一种水平连铸方法,该方法在结晶器和铸坯之间引入了两种气体以起到润滑和减少一次冷却的目的,其中石墨环肩部气体较易和铝熔体反应,促进氧化膜形成以平衡静液压力;中部的气体不易和铝反应,主要起到润滑的作用。该方法能够实现铸造过程的连续润滑,但需要多孔透气石墨作为结晶器的主要材质,成本较高且长时间使用易出现氧化现象导致透气性变差。专利us7143809提出了一种水平连铸装置,该装置在结晶器和铸坯之间引入了气体和润滑油以起到润滑的目的,但该装置也需要多孔透气石墨作为油和气的渗透通道,而多孔透气石墨仅有几家多外厂商可以生产,导致成本较高且暂时没有国产材料可以替代。
技术实现要素:
4.有鉴于此,本发明实施例提供一种铝合金铸锭水平连铸设备,主要通过在导筒和结晶器之间设置供油部,实现无需使用石墨环即可达到为结晶器与铸锭之间持续供润滑油的效果。
5.为达到上述目的,本发明主要提供如下技术方案:本发明实施例提供一种铝合金铸锭水平连铸设备,包括:中间包、导筒、结晶器和铸造设备;导筒和结晶器均为筒状结构,导筒与中间包连接,结晶器与导筒连接,铸造设备设置于结晶器的外部;中间包用于储存铝液,导筒用于将中间包流出的铝液导入结晶器,结晶器用于将铝液凝固成铸锭,铸造设备用于对铸锭进行牵引和切割;其中,结晶器上设置有供油部,供油部用于由导筒和结晶器之间向结晶器的内壁提供润滑油。
6.可选的,供油部包括供油管路和微供油端;微供油端为设置于结晶器上的多个供油孔;或者,微供油端为设置于结晶器和导筒之间的环形缝隙;供油管路与微供油端相连接,供油管路用于通过微供油端向结晶器的内壁提供润滑油。
7.可选的,还包括:分流转接板,分流转接板设置于中间包与导筒之间;分流转接板上设置有下方弧形孔和两个侧方弧形孔,中间包内的铝液分别通过下方弧形孔和两个侧方弧形孔流入结晶器。
8.可选的,导筒与分流转接板为一体结构,导筒与分流转接板均由耐火材料制备而成;结晶器由紫铜制备而成。
9.可选的,下方弧形孔的宽度大于等于15mm,且小于等于50mm;下方弧形孔的圆心角大于等于60
°
,且小于等于100
°
;任一侧方弧形孔的宽度大于等于15mm,且小于等于40mm;任一侧方弧形孔的圆心角大于等于15
°
,且小于等于30
°
。
10.可选的,结晶器上设置有冷却水腔和喷水嘴,冷却水腔与喷水嘴连通,冷却水腔用于存储冷却水,喷水嘴用于向铸锭表面喷射冷却水。
11.可选的,冷却水腔为环形的腔体,冷却水腔围绕结晶器的周向设置,结晶器上还设置有冷却水入口,冷却水腔与冷却水入口连通,冷却水腔内设置有阻水板;喷水嘴的数量为多个,多个喷水嘴围绕结晶器的周向均匀分布,多个喷水嘴与冷却水入口位于阻水板的两侧;阻水板用于使冷却水均匀的由多个喷水嘴喷射。
12.可选的,还包括:电磁搅拌线圈,电磁搅拌线圈套接于导筒外周,电磁搅拌线圈用于搅拌铝液。
13.可选的,铸造设备包括:铸锭牵引装置和铸锭切割装置,铸锭牵引装置包括可调式压下辊和链板机;链板机和铸锭切割装置设置于结晶器的外部,且在链板机的铸锭牵引方向上依次排布;可调式压下辊与链板机连接,链板机用于牵引铸锭在铸锭牵引方向上移动,可调式压下辊用于对链板机上的铸锭压下固定,铸锭切割装置用于锯切铸锭;其中,可调式压下辊为气动压下,以使可调式压下辊的压下距离可调。
14.本发明实施例提出的一种铝合金铸锭水平连铸设备,主要通过通过在导筒和结晶器之间设置供油部,实现无需使用石墨环即可达到为结晶器与铸锭之间持续供润滑油的效果。现有技术中,连续铸造常采用多孔透气石墨作为向结晶器内输送润滑油的主要部件,多孔透气石墨成本较高且长时间使用易出现氧化现象导致透气性变差。与现有技术相比,本技术文件中,在本发明采用导筒和结晶器之间设置供油部,在铸锭成形过程中,通过供油部持续向结晶器内壁提供润滑油,避免石墨在长时间和高温熔体接触下可能产生的氧化现象,在降低成本的同时延长了铸造的持续时间。
附图说明
15.图1为本发明实施例提供的一种铝合金铸锭水平连铸设备的整体结构示意图;图2为本发明实施例提供的一种铝合金铸锭水平连铸设备的局部结构示意图;图3为本发明实施例提供的一种铝合金铸锭水平连铸设备中分流转接板的结构示意图;图4为本发明实施例提供的一种铝合金铸锭水平连铸方法的流程图。
具体实施方式
16.为更进一步阐述本发明为达成预定发明目的所采取的技术手段及功效,以下结合附图及较佳实施例,对依据本发明提出的一种铝合金铸锭水平连铸设备其具体实施方式、结构、特征及其功效,详细说明如后。
17.如图1-2所示,本发明实施例提供了一方面,本发明实施例提供一种铝合金铸锭水平连铸设备,包括:中间包1、导筒2、结晶器3和铸造设备4;导筒2和结晶器3均为筒状结构,导筒2与中间包1连接,结晶器3与导筒2连接,铸造设备4设置于结晶器3的外部;中间包1用于铝液的储存,导筒2用于将中间包1流出的铝液导入结晶器3,结晶器3用于铝液凝固形成铸锭,铸造设备4用于对铸锭进行牵引和切割;其中,结晶器3上设置有供油部,供油部用于由导筒2和结晶器3之间向结晶器3内壁提供润滑油。
18.中间包1为铝液中转储存的容器,在铸造过程中,中间包1内的铝液经由导筒2传送至结晶器3,供油部连通外部供油端,具体可以为供油泵,供油泵打开后,润滑油经由供油部向结晶器3流动,并通过导筒2和结晶器3连接的侧壁之间将润滑油传送至结晶器3内壁。供油部的具体形式可以为多种,旨在使得润滑油在结晶器3的周向上均匀的进入结晶器3靠近导筒2的一侧,进而在铸锭成形和移动的过程中,润滑油将充满结晶器3和铸锭之间,起到润滑结晶器3和铸锭接触面的作用,供油泵经过供油部持续提供润滑油,进而实现铸造过程的连续稳定的润滑。
19.本发明实施例提出的一种铝合金铸锭水平连铸设备,主要通过通过在导筒和结晶器之间设置供油部,实现无需使用石墨环即可达到为结晶器与铸锭之间持续供润滑油的效果。现有技术中,连续铸造常采用多孔透气石墨作为向结晶器内输送润滑油的主要部件,多孔透气石墨成本较高且长时间使用易出现氧化现象导致透气性变差。与现有技术相比,本技术文件中,在本发明采用导筒和结晶器之间设置供油部,在铸锭成形过程中,通过供油部持续向结晶器内壁提供润滑油,避免石墨在长时间和高温熔体接触下可能产生的氧化现象,在降低成本的同时延长了铸造的持续时间。
20.可选的,供油部包括供油管路50和微供油端5;微供油端为设置于结晶器3上的多个供油微孔,多个供油微孔位于结晶器3用于连接导筒2的一侧侧壁上,多个供油微孔围绕结晶器3上的周向上均匀分布;或者,微供油端5为设置于结晶器3和导筒2之间的环形缝隙;供油管路50与微供油端5相连接,供油管路50用于经过微供油端5向结晶器3的内
壁提供润滑油。
21.供油管路50为在结晶器3上加工的用于向微供油端5传送润滑油的通道,供油管路50一端连接油泵,另一端连接微供油端5。微供油端5可以为位于导筒2和结晶器3之间的独立的供油部件,也可以是在导筒2和/或结晶器3上加工的可供油的区域,例如,一种实施例中,微供油端5为多个供油微孔,供油微孔由导筒2和结晶器3相互靠近的侧壁上加工而成,多个供油微孔彼此独立,另一种实施例中,结晶器3上靠近导筒2的侧壁上加工的环状的凹陷,使得结晶器3和导筒2之间在靠近结晶器3内壁处形成一圈环状的供油环,供油环作为微供油端5。此外,微供油端5不局限于以上两种形式,旨在可以为在结晶器3和导筒2之间的连接位置为结晶器3内壁供油均在被发明的保护范围之内。
22.进一步的,如图3所示,装置还包括分流转接板6,分流转接板6设置于中间包1的出口与导筒2之间。分流转接板6上设置有下方弧形孔61和两个侧方弧形孔62,下方弧形孔61和两个侧方弧形孔62分别对应于中间包1的出口的下方和两侧,用于使由中间包1的出口流出的铝液从结晶器3的下部和两侧进入结晶器3。
23.分流转接板6由耐火材料制成,有三个弧形孔分布在分流转接板6的底部和两侧,目的是让铝液从中下部进入结晶器3,使结晶器3下部的铝液温度高于上部,这样可以和结晶器3冷却上弱下强相补偿,使结晶器3内熔体温度场分布趋于均匀。下方弧形孔的宽度大于等于15mm,且小于等于50mm;下方弧形孔的圆心角大于等于60
°
,且小于等于100
°
;任一侧方弧形孔的宽度大于等于15mm,且小于等于40mm;任一侧方弧形孔的圆心角大于等于15
°
,且小于等于30
°
。
24.此外,导筒2与分流转接板6可以为一体结构,导筒2与分流转接板6均由耐火材料制成。结晶器3由紫铜通过紫铜锻件机加而成,结晶器3内径/厚度范围是50mm-300mm。
25.进一步的,结晶器3上还设置有冷却水腔31和喷水嘴32,冷却水腔31与喷水嘴32连通,冷却水腔31用于存储冷却水,喷水嘴32用于向铸锭表面喷射冷却水。
26.具体的,冷却水腔31为环形的腔体,冷却水腔31围绕结晶器3的周向设置,结晶器3上还设置有冷却水入口34,冷却水腔31与冷却水入口34连通,冷却水腔31内部周向设置环形的阻水板33。喷水嘴32的数量为多个,多个喷水嘴32周向均匀分布在结晶器3的出口处,多个喷水嘴32与冷却水入口34位于阻水板33的两侧。阻水板33用于使进入冷却水腔31的冷却水均匀的由多个喷水嘴32喷出。
27.喷水嘴32为铸造过程提供冷却作用。冷却水进入冷却水腔31后,由于阻水板33的阻碍作用,冷却水腔31不会直接由相近的喷水嘴32喷出,而是会先充满阻水板33与冷却水入口34一侧的冷却水腔31内壁之间,进而绕过阻水板33进入阻水板33与喷水嘴32一侧的冷却水腔31内壁之间,继而由喷水嘴32喷出,保证每一个喷水嘴32的冷却水流量相同,进而保证铸锭的均匀降温。
28.可选的,装置还包括电磁搅拌线圈7,电磁搅拌线圈7套接于导筒2外周,电磁搅拌线圈7用于搅拌铝液。
29.电磁搅拌线圈7由紫铜管缠绕而成,表面经绝缘处理,匝数的范围是50匝-100匝;铜管内部通水冷却。电磁搅拌线圈7通过在熔体中施加电磁搅拌起到细化晶粒和减少偏析的作用。
30.具体的,如图1所示,铸造设备4包括铸锭牵引装置和铸锭切割装置41,铸锭牵引装
置包括可调式压下辊42和链板机43。链板机43和铸锭切割装置41设置于结晶器3的出口的外部,且在铸锭牵引装置的铸锭牵引方向上依次排布。可调式压下辊42均与链板机43连接,使用时,将引锭头放置于链板机43上,引锭头用于在链板机43的作用下与结晶器3对接,链板机43用于牵引铸锭在铸锭牵引方向上移动,可调式压下辊42用于对链板机43上的铸锭压下固定,铸锭切割装置41用于铸锭的锯切。其中,可调式压下辊42采用气动压下,以使可调式压下辊42的压下距离可调。
31.中间包1是铝液中转储存的容器,铝液从中间包1通过分流转接板6进入结晶器3。结晶器3内部设有微供油端5和冷却水腔31,可以在铸造过程中提供润滑和冷却作用。导筒2外设有电磁搅拌线圈7,可以在铸造时施加电磁搅拌。铸锭在可调式压下辊42和链板机43的共同作用下以设定的速度沿水平方向牵引,达到一定长度后通过铸锭切割装置41上的同步锯在线锯切。
32.其中,可调式压下辊42采用气动压下,以使可调式压下辊42用于不同规格铸锭的压下固定,可压的铸锭直径/厚度的范围为50 mm-300 mm。链板机43运转速度调节范围为50 mm/min-400 mm/min。可调式压下辊42和链板机43的配合,可以实现宽口径铸锭规格的灵活调整。可调式压下辊42可以自适应铸锭的直径或厚度。链板机43可以在较宽的范围内调节速度,且和铸锭接触区域长,有助于提高铸锭牵引的稳定性。
33.另一方面,如图4所示,本发明实施例还提供一种铝合金铸锭水平连铸的方法,采用上述铝合金铸锭水平连铸设备实现,方法按照以下步骤进行:为结晶器3提供冷却水;为结晶器3提供润滑油;将铝液引入结晶器3;铝液形成坯壳后启动铸造设备4;铸锭引出后,开启电磁搅拌线圈7的励磁电源;开启铸锭切割装置41进行切头;关闭励磁电源,停止为结晶器3提供润滑油,停止为结晶器3提供冷却水。
34.更具体的,上述方法的具体实现过程如下:引锭头由链板机43送入结晶器3内10 mm-30 mm;为结晶器3提供冷却水;冷却水引入冷却水腔31,并由喷水嘴32喷出,作用至引锭头表面;为结晶器3提供润滑油,润滑油进过供油部进入结晶器3的内壁,在结晶器3的内壁出现润滑油后,将铝液引入引锭头、结晶器3和分流转接板6组成的空腔中;铝液在空腔中静置凝固10s-90 s,形成坯壳后,启动铸造设备4开始铸造,启动前的停留时间和铸锭的直径成反相关关系;初始启动速度为20 mm/min-100 mm/min,启动速度和铸锭的直径成反相关关系;在铸锭被引出200 mm后开启电磁搅拌线圈7的励磁电源;电磁搅拌线圈7的励磁电流频率范围为5 hz-50 hz,励磁电流频率和铸锭的直径成反相关关系;当引锭头完全通过铸锭切割装置41的同步锯300 mm-600 mm后,开启铸锭切割装置41进行切头,切头结束后定尺锯切;铸造结束后,首先关闭励磁电源,然后停止为结晶器3提供润滑油,最后停止为结
晶器3提供冷却水。
35.以上所述,仅为本发明的具体实施方式,但本发明的保护范围并不局限于此,任何熟悉本技术领域的技术人员在本发明揭露的技术范围内,可轻易想到变化或替换,都应涵盖在本发明的保护范围之内。因此,本发明的保护范围应以所述权利要求的保护范围为准。