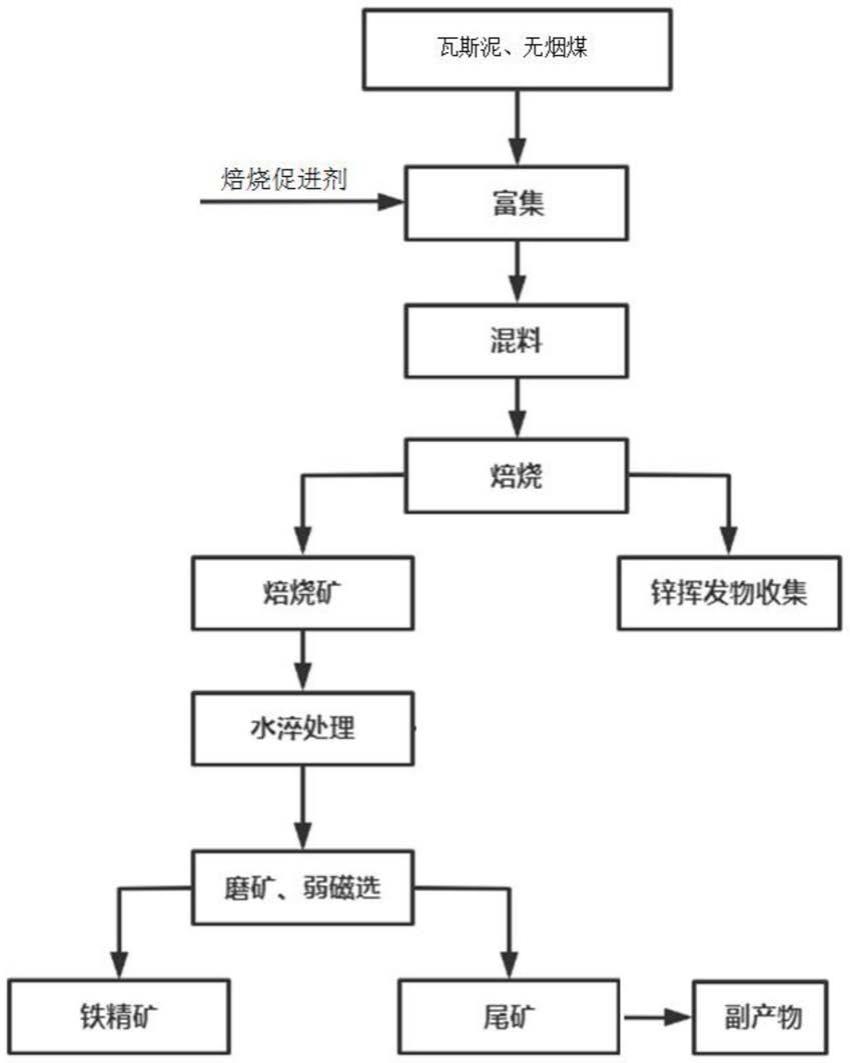
1.本发明属于冶金固废处理技术领域,具体涉及一种回收高炉瓦斯灰尘中锌和铁的方法。
背景技术:
2.钢铁产业是国民经济的重要支柱产业,产业涉及面广、关联度高,在经济建设、社会发展、国防建设等方面发挥着重要作用。在钢铁冶炼过程中产生大量的烟尘灰(电炉炼钢粉尘、高炉瓦斯灰等),总数超过7000万吨/年,其中含有大量铁、锌、铅等有价值元素。钢铁厂烟尘灰中主要由铁的氧化物、氧化锌、二氧化硅、氧化钙等组成,而这些物质在高炉炼铁过程中属于有害物质,会在高炉内循环富集,温度降低时冷凝形成细小颗粒,黏附或沉积在炉料的孔隙中,恶化料柱透气性,形成了窑内结圈现象,从而严重影响了高炉炉况的正常运行。若能将这些元素分离提纯,则可变废为宝,得到宝贵的再生资源,既达到环境治理目的,又可解决我国铁矿、锌矿资源短缺的问题。
3.高炉瓦斯灰是炼铁高炉冶炼过程产生的副产物,通常来说每炼1吨生铁产生10-150kg的炉尘,根据不同除尘收集部位,其fe、zn、c含量均不同,其中zn含量低的有1%左右,高的可达到15%左右,但大多数zn含量约在3-13%,除此之外其主要含fe和c, fe含量约在20%-45%,c含量约在10%-26%。高炉瓦斯灰无法直接有效利用,若未经处理的情况下直接返回高炉冶炼系统,将造成高炉结瘤、影响高炉正常工作,甚至影响高炉寿命。若不能回收有效利用,既造成环境污染,又造成资源浪费。如果可以回收了瓦斯中的锌,回收得到的富锌料可用于深度提锌,回收锌后剩余的部分含锌低且富含铁和碳,可作为高炉炼铁的原料返回高炉冶炼系统再利用,从而很好地利用了高炉瓦斯烟尘中的有价成分。
4.目前,高炉瓦斯灰主要利用方式为火法冶锌。火法冶锌工艺由于瓦斯灰中铁含量较高的因素导致回转窑结瘤,当结瘤严重时必须处理,处理一次结瘤需要停工3-7天,不但影响企业产量还将使工作成本上升。而从回收资源的利用角度分析,锌、铁、碳均为可回收资源,将瓦斯灰中铁、锌、碳分开富集可以提高瓦斯灰的经济价值,但是目前还缺少能够有效将铁、锌、碳分开富集的方式,使瓦斯灰具有更高的利用价值。
5.cn107604110a公开了一种从高炉瓦斯灰中选铁的方法,该方法将高炉瓦斯灰通入风力分级-风磁分选系统进行处理,通过风力分级将大颗粒瓦斯灰分离出来得到风选铁精矿;通过风磁分选将细粒度瓦斯灰中的磁性物料分离出来得到磁选铁精矿,风选铁精矿和磁选铁精矿直接返回烧结、冶炼工序使用;由布袋除尘器捕集到的二次瓦斯灰为富锌矿粉,该方法利用鼓风机和通风道长度的配合将粒度大、质量中的颗粒分选富集出来,再利用磁选法回收物料中的金属铁,该方法不引入化学药剂,不添加水,能够实现高效干法分选,铁元素的回收率可达87%以上。
6.风磁分选的原料是基于高炉瓦斯灰中金属元素锌、铁、铅以及非金属元素碳的密度差进行的重选分离富集。虽然他们的密度差异满足重选分离的必要条件,但在实际应用过程中,高炉瓦斯灰的粒度较小,金属元素颗粒以及含碳颗粒无法克服空气介质中的湍流
影响,只能随着空气流随机进入产品槽,造成错配物含量增加,恶化重选分离效果。
7.因此,需要提出一种更加科学合理的方法来处理高炉瓦斯灰,提高其经济效益。
技术实现要素:
8.本发明的目的是提供一种回收高炉瓦斯灰尘中锌和铁的方法,克服现有技术的不足,通过在高炉瓦斯灰添加焙烧促进剂,实现既能在一定的温度下、较短时间内同时有效回收瓦斯灰中的稀有金属资源(如锌等),又不影响瓦斯灰中铁的回收率,从而提高其整体的经济效益。此外,其尾渣副产物都为无污染的重要工业原料,可以保护周边环境,避免污染。
9.为实现上述目的,本发明采用以下技术方案实现。
10.一种回收高炉瓦斯灰尘中锌和铁的方法,其特征在于,包括富集、混料、焙烧、水淬处理和磨矿-弱磁选回收,实现锌和铁的有效回收,具体步骤如下:1)富集,将高炉烟尘和废渣通过流化床去除混杂的泥土杂质,富集处理,富集后得到含全铁品位≥30%、含锌品位≥12%的瓦斯泥;2)混料,在瓦斯泥中加入瓦斯泥总质量15%~25%的无烟煤,再加入瓦斯泥总质量5%~10%的焙烧促进剂,所述焙烧促进剂是含nahco3和caco3的均匀复配物,nahco3与caco3的质量比控制在1:3.9~4.2;将瓦斯泥、无烟煤、焙烧促进剂用混合搅拌机混合1h~2h,使三者混合均匀;3)焙烧,将混合均匀后的物料装入带有烟气回收系统的回转窑中进行还原焙烧,焙烧温度为1100~1350℃,焙烧时间为2h~3h;4)水淬处理,对步骤3)排出的焙烧矿进行水淬处理,冷却至常温;5)磨矿-弱磁选回收,将水淬处理且干燥后的物料给入磨矿-弱磁选设备,磨矿粒度区间为80%~95%,弱磁选后获得铁品位为80%以上的铁精矿和尾渣;尾渣中的钙化物、钠化物可进行再次溶解并回收处理,制作副产物硫酸钙、硫酸钠和氧化钙,进行二次利用。
11.在所述步骤3)中的还原焙烧过程中进行主动抽气,抽出的气体由烟气回收系统进行处理,通过烟气回收系统收集获得锌元素的沉泥产品,获得95%以上的锌挥发率。
12.所述焙烧促进剂中的nahco3与caco3的优选质量比为1:4。
13.所述nahco3为化学纯,其有效成分占比97.9~99.9%,粒度为180~380μm;所述caco3取材于石灰石煅烧,其有效成分占比为75~85%,粒度为150~350μm所述主动抽气的压力为-0.2~-0.8个大气压。
14.所述回转窑可以替换为反射窑或隧道窑。
15.所述弱磁选设备为湿式永磁筒式磁选机,筒表面平均磁感应强度为160~260mt 。
16.所述烟气回收系统中设有旋风除尘器和静电式布袋除尘器。
17.本发明焙烧促进剂的反应原理如下:第一步:2zns+3o2=2zno+2so22nahco3=na2co3+h20+co2第二步:caco3=cao+co2第三步:na2co3=co2+na2o第四步:co2+c=2co第五步:3znofe2o4+c=3zno+2fe3o4+co
zno+co=zn+co2由以上化学反应可知,caco3和nahco3在试验温度下会发生分解反应,生成co2, co2与环境中过量的碳反应生成还原性更强的co,在c和co共同的还原作用下,更容易将铁锌氧化物还原出来,从而能够起到加快企业的生产效率。
18.因为两种物质的分解温度不同,nahco3比caco3更容易分解。在高温下nahco3很容易因快速分解而消耗殆尽,起不到在整个还原过程中提供co2的效果,而na2co3,caco3由于分解速度较慢,在整个还原焙烧过程中可以通过分解反应,持续释放co2,再通过碳的气化反应可以为环境提供源源不断的高效还原剂co。而zns与炉内的o2反应所生成的so2,也可以被cao和na2o所吸收,形成caso4、na2so4等工业副产物。
19.与现有技术相比,本发明的有益效果是:1)本发明采用的焙烧促进剂nahco3比caco3,可以实现较高的zn回收率,并且对铁资源的回收利用无影响,含有锌的沉泥产品可以单独分离、富集、制备氧化锌等产品,也可以直接出售给相关产品的冶炼生产厂家,提高了钢铁厂烟尘灰的综合处理能力,提高了生产利润率,保护了周边环境;2)本发明采用的焙烧促进剂nahco3比caco3,可以实现在较低的焙烧温度和较短的焙烧时间下获得较高的zn挥发率,与传统工艺相比减少了能耗,提高了焙烧效率;3)本发明采用的焙烧促进剂nahco3比caco3,可以实现还原气体的循环利用,减少了焦炭使用,与传统工艺相比节省了物料成本的同时减少了有害气体的排放,实现了绿色清洁高效的生产模式;4)本发明采用的焙烧促进剂nahco3比caco3,能提高高炉瓦斯灰尘的碱度,增大混合物料熔点,同时焙烧促进剂和高炉瓦斯灰尘中其他氧化物形成反应竞争机制,控制液相熔融物生成,降低物料的粘附能力,抑制了结圈现象;5)本发明采用的焙烧促进剂nahco3比caco3,铁精矿的回收率达到80%~95%,另外焙烧促进剂最终混入回转窑的尾渣中,尾渣中的钙化物、钠化物可进行再次溶解并回收处理,制作副产物硫酸钙、硫酸钠和氧化钙,进行二次利用,提高了经济效益。
附图说明
20.图1为本发明实施例的工艺流程图。
具体实施方式
21.下面将结合附图对本发明的技术方案进行清楚、完整地描述,显然,所描述的实施例是本发明部分实施例,而不是全部的实施例。
22.为了更清楚地说明本发明具体实施方式或现有技术中的技术方案,下面将对具体实施方式作简单地说明。因此,以下对本发明的实施例的详细描述并非旨在限制要求保护的本发明的范围,而是仅仅表示本发明的选定实施例。
23.本实施例中所用的高炉瓦斯灰尘的多元素分析结果见表1所示。
24.表1高炉瓦斯灰分析结果(%)元素csalsicamgfeznti含量26.681.395.865.474.101.0738.6416.600.19
高炉瓦斯灰尘中的全铁含量为38.64%,碳含量为26.68%,锌含量为16.60%。
25.见图1,是本发明一种回收高炉瓦斯灰尘中锌和铁的方法的工艺流程图,在实验室条件下对高炉瓦斯灰尘进行综合回收研究。实验室采用的中试线回转窑长50m,内径1.2m,衬有50mm厚度耐火材料,沿窑长方向埋设8支热电偶,实现连续测温。物料由窑尾加入,焙烧后物料由窑头排出,落入水淬池;窑头设有烧嘴,采用灌装液化气做燃料,烧嘴和窑内负压可调,回转窑主体倾斜角1~8
°
可调,转速0~20转/分钟可调。
26.如用于规模化生产中时,回转窑也可以替换为反射窑或隧道窑。烟气回收系统中可设置旋风除尘器和静电式布袋除尘器,使不同比重的锌沉泥和飞灰能更好的分离。
27.本发明一种回收高炉瓦斯灰尘中锌和铁的方法,包括富集、混料、焙烧、水淬处理和磨矿-弱磁选回收,实现锌和铁的有效回收,具体步骤如下:1)富集,将高炉烟尘和废渣通过流化床去除混杂的泥土杂质,富集处理,富集后得到含全铁品位38.64%、锌含量16.60%、碳含量为26.68%的瓦斯泥;2)混料,在瓦斯泥中加入瓦斯泥总质量20%的无烟煤,再加入瓦斯泥总质量8%的焙烧促进剂,焙烧促进剂是含nahco3和caco3的均匀复配物,nahco3和caco3的质量比控制在1:4;将瓦斯泥、无烟煤、焙烧促进剂用磁力搅拌器混合搅拌机混合1.3h,使三者混合均匀;3)焙烧,取混合均匀后的物料倒入焙烧皿中,晃动焙烧器皿使料层高度均匀一致,当料层厚度达到50mm时停止加料,然后取少量的细小均匀的无烟煤颗粒均匀覆盖料层表面,装入带有烟气回收系统的回转窑中进行还原焙烧,焙烧温度为1300℃,焙烧2.5h后,断电降温,焙烧料随炉自然冷却。在焙烧过程及冷却过程中,每隔15min进行一次主动抽气,当炉温降到850℃时,将焙烧器皿移出,同时将烟气回收系统中收集的含锌沉泥进行沉淀、过滤,烘干,以备后续进行锌的分离及制备氧化锌;4)水淬处理,对步骤3)中出炉的焙烧器皿立即放入事先准备好的盛有足够多水量的陶瓷容器中,保证水深能够淹没焙烧器皿进行水淬处理,待温度冷却至30℃以下时将焙烧器皿取出;将焙烧器皿置于烘箱中进行烘烤干燥,当容器中的水分全部挥发后进行称重并检测其中zn元素的含量,焙烧器中混合物的锌品位为0.68%,通过计算可得,锌挥发率达到了96.31%;5)磨矿-弱磁选回收,将水淬处理且干燥后的物料给入磨矿-弱磁选设备,磨矿粒度为93%,使用湿式永磁筒式磁选机进行弱磁选,弱磁感应强度为260mt,可获得全铁品位80%以上的铁精矿和尾渣;尾渣中的钙化物、钠化物可进行再次溶解并回收处理,制作副产物硫酸钙、硫酸钠和氧化钙,进行二次利用。
28.实施例中,nahco3为化学纯,其有效成分占比97.9~99.9%,粒度为180~380μm;caco3取材于石灰石煅烧,其有效成分占比为75~85%,粒度为150~350μm。主动抽气的压力为-0.2~-0.8个大气压。
29.表2 实施例回转炉内结圈物质多元素分析结果(%)从表2可以看出,焙烧促进剂的加入可以有效地减少回转炉内结圈表面物质中低熔点化合物(如al、si、ca等)的含量,避免了对回转炉内结圈表面的频繁清理,可以有效的
提高钢铁厂的经济效益,并且焙烧促进剂的加入对zn元素的挥发起到了高效的促进作用,多种zn的化合物都得到了充分的还原反应,同时原料的消耗降低,向环境中排放的有害气体含量也必然会大幅减少。
30.当然,本发明还可以有其它多种实施例,在不背离本发明精神及其实质的情况下,熟悉本领域的技术人员可根据本发明作出各种相应的改变与变形,但这些相应的改变与变形都应属于本发明权利要求的保护范围。