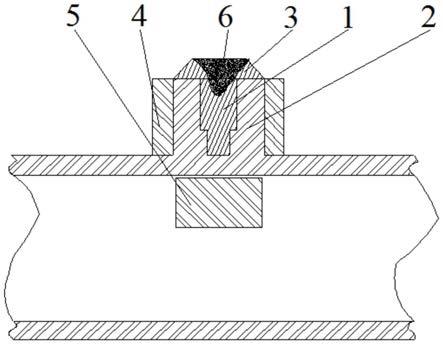
1.本发明涉及铸造技术领域,更具体地说涉及一种解决铸件缩松的铸造方法。
背景技术:
2.现在的汽车零部件,例如汽车排气管或者涡轮增压器壳体等产品结构都设计有螺栓,螺栓的作用是方便和其它零部件进行组装装配;产品铸造时,螺栓与管壁相连的位置会形成热节区,现有铸造生产工艺方案,需要在热节部位设置冒口,通过冒口对热节部位进行补缩,解决热节部位缩松的缺陷,但是这种生产工艺,工艺出品率低,生产成本高,后续还需要进行冒口去除,清理等工序,步骤较为繁琐。此外,由于螺栓所在的位置都不固定,每个产品上的螺栓数量在3~6个左右,有些螺栓根据铸造分型工艺可以放置冒口,但还有些螺栓位置在铸件的管壁位置,根据铸造分型,这些螺栓无法放置冒口,因此无法避免产品出现缩松等质量缺陷。
3.因此,如何提供一种能解决上述问题的铸造方法是本领域技术人员亟需解决的技术问题。
技术实现要素:
4.本发明的目的在于提供一种解决铸件缩松的铸造方法,以解决通过设置冒口解决热节部位缩松缺陷时,工艺出品率低,生产成本高的问题;以及孤立热节部位无法设置冒口,无法避免成品出现缩松等质量缺陷的问题。
5.本发明的目的是通过以下技术方案实现的:一种解决铸件缩松的铸造方法,应用于设计有螺栓的铸件,并且所述螺栓处于孤立热节区域,铸造时将所述螺栓浇筑成凸台,所述凸台的中间部位为螺纹孔加工区域,所述凸台的外周为非加工区域;
6.在所述凸台远离所述铸件中心轴的一端延伸增加余量加工区域,以使缩松区域避开所述非加工区域。
7.优选的,在上述一种解决铸件缩松的铸造方法中,所述余量加工区域的轴向高度为4~8mm。
8.优选的,在上述一种解决铸件缩松的铸造方法中,铸件造型时,在所述凸台型腔的的周向放置冷铁环。
9.优选的,在上述一种解决铸件缩松的铸造方法中,所述冷铁环的厚度为10~20mm。
10.优选的,在上述一种解决铸件缩松的铸造方法中,铸件造型时,在型芯中嵌入冷铁块,所述冷铁块的中心轴与所述凸台的中心轴同轴。
11.优选的,在上述一种解决铸件缩松的铸造方法中,所述凸台与所述冷铁块的隔砂间距为2~3mm。
12.优选的,在上述一种解决铸件缩松的铸造方法中,通过工艺模拟,确定所述余量加工区域的具体形态尺寸。
13.优选的,在上述一种解决铸件缩松的铸造方法中,使用magma模拟软件进行工艺模
拟。
14.经由上述的技术方案可知,与现有技术相比,本发明公开提供了一种解决铸件缩松的铸造方法,无需设置冒口,将螺栓浇筑成凸台,并且在凸台远离铸件中心轴的一端延伸增加余量加工区域,使缩松区域处于余量加工区域和凸台的螺纹孔加工区域内,避开了凸台的非加工区域,进而保证了成品品质,提高了工艺出品率,解决了因无法放置冒口,产品容易出现缩松、缩孔等质量缺陷的问题。
附图说明
15.为了更清楚地说明本发明实施例或现有技术中的技术方案,下面将对实施例或现有技术描述中所需要使用的附图作简单地介绍,显而易见地,下面描述中的附图仅仅是本发明的一些实施例,对于本领域普通技术人员来讲,在不付出创造性劳动的前提下,还可以根据这些附图获得其他的附图。
16.图1为未增加加工余量时铸件的主视图;
17.图2为图1中缩松区域的局部放大图;
18.图3为未增加加工余量时铸件的侧视图;
19.图4为本发明增加加工余量时铸件的主视图;
20.图5为未增加加工余量时,通过magma模拟软件得到的铸件缩松状态的模拟图;
21.图6为本发明增加加工余量时,通过magma模拟软件得到的铸件缩松状态的模拟图。
22.图1~图6中:
23.1为螺纹孔加工区域、2为非加工区域、3为余量加工区域、4为冷铁环、5为冷铁块、6为缩松区域。
具体实施方式
24.为使本发明的目的、技术方案和优点更加清楚,下面将对本发明的技术方案进行详细的描述。显然,所描述的实施例仅仅是本发明一部分实施例,而不是全部的实施例。基于本发明中的实施例,本领域普通技术人员在没有做出创造性劳动的前提下所得到的所有其它实施方式,都属于本发明所保护的范围。
25.以下,结合附图对实施例作详细说明。此外,下面所示的实施例不对权利要求所记载的发明的内容起任何限定作用。另外,下面实施例所表示的构成的全部内容不限于作为权利要求所记载的发明的解决方案所必需的。
26.请参考附图1~3和5
27.对比例1
28.解决铸件缩松的铸造方法,应用于设计有螺栓的铸件,并且螺栓处于孤立热节区域,铸造时将螺栓浇筑成凸台,凸台的中间部位为螺纹孔加工区域1,凸台的外周为非加工区域2;
29.铸件造型时,在凸台型腔的的周向放置冷铁环4;冷铁环的厚度为15mm;
30.铸件造型时,在型芯中嵌入冷铁块5,冷铁块5的中心轴与凸台的中心轴同轴;凸台与冷铁块5的隔砂间距为2.5mm。
31.请参阅附图4和6
32.实施例1
33.解决铸件缩松的铸造方法,应用于设计有螺栓的铸件,并且螺栓处于孤立热节区域,铸造时将螺栓浇筑成凸台,凸台的中间部位为螺纹孔加工区域1,凸台的外周为非加工区域2;
34.在凸台远离铸件中心轴的一端延伸增加余量加工区域3;余量加工区域3的轴向高度为6mm;
35.铸件造型时,在凸台型腔的的周向放置冷铁环4;冷铁环的厚度为15mm;
36.铸件造型时,在型芯中嵌入冷铁块5,冷铁块5的中心轴与凸台的中心轴同轴;凸台与冷铁块5的隔砂间距为2.5mm。
37.实施例2
38.解决铸件缩松的铸造方法,应用于设计有螺栓的铸件,并且螺栓处于孤立热节区域,铸造时将螺栓浇筑成凸台,凸台的中间部位为螺纹孔加工区域1,凸台的外周为非加工区域2;
39.在凸台远离铸件中心轴的一端延伸增加余量加工区域3;余量加工区域3的轴向高度为4mm;
40.铸件造型时,在凸台型腔的的周向放置冷铁环4;冷铁环的厚度为20mm;
41.铸件造型时,在型芯中嵌入冷铁块5,冷铁块5的中心轴与凸台的中心轴同轴;凸台与冷铁块5的隔砂间距为2mm。
42.实施例3
43.解决铸件缩松的铸造方法,应用于设计有螺栓的铸件,并且螺栓处于孤立热节区域,铸造时将螺栓浇筑成凸台,凸台的中间部位为螺纹孔加工区域1,凸台的外周为非加工区域2;
44.在凸台远离铸件中心轴的一端延伸增加余量加工区域3;余量加工区域3的轴向高度为8mm;
45.铸件造型时,在凸台型腔的的周向放置冷铁环4;冷铁环的厚度为10mm;
46.铸件造型时,在型芯中嵌入冷铁块5,冷铁块5的中心轴与凸台的中心轴同轴;凸台与冷铁块5的隔砂间距为3mm。
47.对比例1中铸件成品的缩松区域及成品品质与实施例1~3中铸件成品的缩松区域及成品品质的对比结果,如表1所示。
48.表1
[0049][0050]
结论:本技术实施例1~3中,将螺栓浇筑成凸台,通过在凸台远离铸件中心轴的一端延伸增加余量加工区域,保证了缩松区域处于余量加工区域和凸台的螺纹孔加工区域内,避开了凸台的非加工区域,进而保证了成品品质,提高了工艺出品率,解决了因无法放置冒口,产品容易出现缩松、缩孔等质量缺陷的问题。
[0051]
通过在凸台的周向设置冷铁环,同时在靠近凸台与管壁连接位置的型芯中嵌入冷铁块,保证了凸台外周的冷却速度,以及凸台与管壁连接处的冷却速度,进而保证了最终的缩松区域呈v型结构,并且处于余量加工区域和凸台的螺纹孔加工区域的顶部中心,使缩松区域巧妙避开凸的台非加工区域。
[0052]
其中需要说明的是:实施例1~3中,通过工艺模拟,确定余量加工区域3的具体形态尺寸。
[0053]
进一步的,用magma模拟软件进行工艺模拟。
[0054]
通过magma模拟软件进行工艺模拟可以确定出余量加工区域3的具体形态尺寸,进而保证缩松区域避开凸台非加区域的同时,余量加工区域的用材最少。
[0055]
本发明公开提供的解决铸件缩松的铸造方法,无需设置冒口,将螺栓浇筑成凸台,在凸台远离铸件中心轴的一端延伸增加余量加工区域,同时在凸台的周向设置冷铁环,在靠近凸台与管壁连接位置的型砂中嵌入冷铁块,保证了凸台外周的冷却速度,以及凸台与管壁连接处的冷却速度,进而保证了最终的缩松区域呈v型结构,并且处于余量加工区域和凸台的螺纹孔加工区域的顶部中心,使缩松区域巧妙避开凸的台非加工区域,进而保证了成品品质,提高了工艺出品率,解决了因无法放置冒口,产品容易出现缩松、缩孔等质量缺陷的问题。
[0056]
可以理解的是,上述各实施例中相同或相似部分可以相互参考,在一些实施例中未详细说明的内容可以参见其他实施例中相同或相似的内容。本发明提供的多个方案包含本身的基本方案,相互独立,并不互相制约,但是其也可以在不冲突的情况下相互结合,达到多个效果共同实现。
[0057]
以上所述,仅为本发明的具体实施方式,但本发明的保护范围并不局限于此,任何熟悉本技术领域的技术人员在本发明揭露的技术范围内,可轻易想到变化或替换,都应涵盖在本发明的保护范围之内。因此,本发明的保护范围应以所述权利要求的保护范围为准。