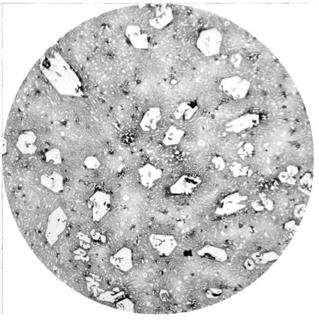
1.本发明涉及一种高铬铸铁用变质剂,属于金属材料及加工技术领域。
背景技术:
2.高铬铸铁是继普通白口铸铁、镍硬铸铁之后发展起来的第三代白口铸铁,由于具有良好的耐磨性,是公认的性能优良的耐磨材料,在采矿、水泥、冶金、电力等方面应用广泛。高铬铸铁一般含铬量在12%~28%之间,铬的大量加入使得白口铁中的m3c型碳化物变成m7c3型碳化物,m7c3型碳化物具有很高的硬度,使得高铬铸铁有良好的耐磨性。耐磨高铬铸铁也有不足之处,由于高铬铸铁硬度很高,所以在一些使用工况较恶劣的情况下,往往会因为韧性差而失效,从而影响正常生产,因此,在保证硬度不降低前提下提高高铬铸铁的韧性就显得尤为重要。通常认为:硬度和冲击韧性是一对矛盾,一个材料的硬度升高,韧性必然下降,但是材料的金相组织决定性能,只要将高铬铸铁的组织进一步细化,就能同时提高硬度和冲击韧性,细化晶粒是能同时提高硬度和韧性的唯一途径,通过对铁水采取净化措施以及使用高铬铸铁变质剂可以达到细化晶粒的目的。
3.近年来,关于提高高铬铸铁韧性、耐磨损和使用寿命及性能方面科研工作者进行了大量研究,国内开发了几种高铬铸铁变质剂材料。目前,高铬铸铁变质剂主要有以下几种:
4.专利cn 103667865a,公开了“一种超抗磨高铬多合金磨球及其复合变质加工工艺”,该超抗磨高铬多合金磨球化学成分是:c:2.0%~3.0%、si:0.30%~1.00%、mn:0.20%~1.00%、cr:11.00%~14.00%、s:0~0.05%、p:0~0.05%、mo:0.05%~0.20%、b:0.003%~0.010%、ti:0.010%~0.030%、v:0.05%~0.15%的以及余量的fe为原料,其中,ti和b的重量比大于2.5,v和ti的重量比大于3。该专利通过二次特殊的复合变质处理加工而成,其发明所述特殊的变质处理是两步变质处理,一次是在炉内变质处理加入硼铁、钼铁和钛铁,第二次变质处理是在铁水冲入浇包时进行处理,变质剂是由工业硝酸钾20%,稀土硅铁(75%),稀土镁硅铁(5%)组成。该专利采用两次变质处理,第二次变质处理所用原材料其中一个是工业硝酸钾,硝酸钾是强氧化剂,与有机物接触能引起燃烧和爆炸。因此,用硝酸钾作为变质剂显然有安全隐患。专利cn 109439834a,公开了“一种用于高铬铸铁的复合稀土变质剂及其变质处理工艺”,所述复合稀土变质剂由以下几种原材料组成(重量百分比):3-8型稀土镁硅球化剂2-4份,30型稀土硅2-3.5份,氯化钾1-1.5份,60铌铁合金2-3份,其中3-8型稀土镁硅球化剂和30型稀土硅中的稀土为铈元素,60铌铁合金的纯度≥60%;专利所述,当铁水温度在1420-1500℃之间时,把变质剂采用冲入法进行处理,高铬合金使用本发明变质剂及变质工艺之后,可以使得高铬合金的碳化物分布均匀,使得脆性断裂时扩展路径受的阻碍,同时,提高了高铬合金的韧性。其中大量使用了稀土合金,还使用了铌铁合金,铌铁更是非常昂贵的材料,铌铁的使用无疑会增加不少生产成本,这种变质剂显然不适合在工业生产中批量使用,专利中对于变质剂的机理没有进行深入分析和表述。
5.专利cn 1718816a,公开了“钇基稀土硅钙铁合金及其制备方法和用途”,所述钇基
稀土硅铁合金的化学成分为(重量%):re5-60%、ca0.5-15%、ba0-15%、sr0-10%、si5-55%、al0-30%、mg0-8%、nb0-10%、b0-5%、ti0-15%、v0-15%、zr0-15%其余为铁及少量杂质元素。其形状为不规则颗粒状或制成包芯线。该专利只是描述了变质剂可用于改变碳化物形态、大小、分布,表述了可以净化铁液,使碳化物呈现不连续状或团球状,但对于变质的机理没有进行分析,也没有相应的抗磨合金铸铁的金相照片证明效果。专利cn 107475599a,提出了“一种针对btmcr26的复合变质处理技术”,该专利发明的变质剂是稀土、硼和钒。专利所述按铁液重量百分比添加稀土0.5%、硼0.12%、钒1%,专利所述,在熔炼过程中向铁液中通入10-20min氩气,砂型温度控制在200~250℃,浇注时间控制在5~10min。其中没有提及通过变质处理是不是改变了碳化物的形态,没有描述具体的组织形貌是否得到了改善,且发明所述的稀土、硼、钒均为常见的加入合金,使用方法也很常规。专利cn 107686872b,披露了“一种用于细化钢铁中碳化物的变质剂”,所述变质剂重量百分比为:混合稀土10~50%、稀土硅铁10~25%、硅铝钙合金30~50%和其它微量合金元素m15~40%,所述微量合金元素m由下述重量百分比的原料组成:zr 25~60%、cu 10~60%、sb25~50%、bi 22~50%和b 2~20%,专利所述混合稀土、稀土硅铁、硅铝钙合金的总重量不低于所述变质剂重量的60%,所述稀土硅铁中的稀土的重量不低于所述稀土硅重量的20%,所述硅铝钙合金中的钙的重量不低于所述硅铝钙合金重量的13%。该专利所述通过变质剂的加入可以改善碳化物,对于碳化物怎么改变,改变了什么没有进行详细描述,也没说清楚细化碳化物的机理是什么,且专利中使用了大量的稀土合金(混合稀土、稀土硅铁),稀土属于我国的稀有资源,稀土的大量使用显然不符合我国的国情。
6.综上所述,通过对比分析目前变质剂专利,可以发现,目前有关变质剂存在以下不足:
7.(1)目前有关钢铁材料的变质剂几乎都以稀土合金为主要元素,稀土是我国的稀缺资源,所以稀土的大量使用,成本高,也不符合我国的基本国情;
8.(2)目前所述变质剂基本都含有硅元素,实际生产中,高铬铸铁中硅的含量需要严格控制,另外,高铬铸铁自身的硅含量有的已经超标,再使用含有硅元素的变质剂,对于高铬铸铁的性能有影响,所以研制一种不含硅的变质剂迫在眉睫;
9.(3)目前高铬铸铁类的变质剂铬镍含量都不太高,多加有稀土合金使用,添加量也不小;
10.(4)目前所述变质剂,对于变质的机理多没有详细的描述,原理若不确定则变质作用不同情况下会不太相同,变质的效果和稳定性尚待研究。
11.为此,急切需要开发一种低成本,性能良好,不使用稀有元素和昂贵原材料,且不含硅的高铬铸铁变质剂。
技术实现要素:
12.本发明的目的是克服上述不足而提供一种高铬铸铁用变质剂及其制备方法。
13.为实现上述目的,本发明采用以下技术方案:
14.一种高铬铸铁用变质剂,其质量百分比组成为:cr:71~75%,ni:10~11.5%,mo:0.9~1.3%,mn:1.1~1.45%,v:0.2~0.28%,zn:0.7~1.2%,cu:0.8~1.0%,b:0.18~0.25%,n:0.15~0.2%,zr:0.15~0.2%,nb:0.26~0.3%,co:0.15~0.2%,余量为fe及
杂质。
15.所述的高铬铸铁用变质剂,其质量百分比组成中cr含量优选:74~75%。
16.所述的高铬铸铁用变质剂,其质量百分比组成中ni含量优选:11~11.5%。
17.所述的高铬铸铁用变质剂为合金金属粉末,优选粉末粒度为50μm~150μm,松装密度为3.2~3.5g/cm3,流动性<30s/50g,氧含量<100ppm。
18.上述高铬铸铁用变质剂的制备方法,包括步骤如下:
19.(1)按照所述的合金成分的质量百分比组成配料,称取原料电解铬、不锈钢304和316l、镍铁、电解锰、电解钒、1#锌锭、电解铜、硼砂、氮化铬、锆铁、铌铁、电解钴、钼铁;
20.(2)将原料进行预处理:将原料混合均匀后在260~380℃温度条件下进行保温处理,保温时间控制2~6小时,烘干原材料里面的水分和氧化锈;
21.(3)原料的熔炼:将预处理后的原料放入真空感应中频电炉进行熔炼,熔炼后把合金液浇注到事先准备好的金属型中,浇注合金预制块,合金液冷却之后,得到合金预制块;
22.(4)将合金预制块用破碎机破碎成粒度为30~50mm的颗粒,真空包装;
23.(5)利用金属超声雾化制备装置将破碎后的颗粒制备成金属粉末,真空条件下,先熔化然后将液态合金倒入雾化器进行雾化成粉末,粉末冷却后真空包装。
24.上述制备方法中,步骤(2)所述的保温时间根据装炉料的多少进行调整,装炉料500kg以下,保温2小时,500kg~1000kg保温3~4小时,1000kg以上保温4~6小时。
25.步骤(3)所述的熔炼以电炉额定功率40~50%进行升温熔炼,当合金料全部熔化之后,此时合金液温度在1400~1480℃,保温5~10分钟。
26.步骤(5)所述现有金属超声雾化制备装置一般由熔炼炉、雾化罐、超声雾化器、粉末收集罐、真空充气系统、馈液系统、控制系统构成。熔化合金块的温度为1350~1400℃,合金块熔化之后,将液态合金倒入雾化器进行雾化,全过程进行真空操作。雾化之后得到的粉末粒度50μm~150μm,松装密度3.2~3.5g/cm3,流动性<30s/50g,氧含量<100ppm。
27.所述的高铬铸铁用变质剂,其基本原理是采用铬为主要元素,首先是容易与高铬铸铁铁液进行结合,另外,变质剂中除铬之外还有镍、钼、铜等稀有元素,变质剂的加入相当于外来形核,不仅能够提供形核的质点,还可以因为高铬铸铁形核之后,阻断高铬铸铁共晶碳化物的生长,达到细化晶粒、细化碳化物的目的,从而提高高铬铸铁的韧性和强度。
28.本发明的有益效果是:
29.(1)本发明所述高铬铸铁变质剂不含稀土合金,符合我国资源保护政策。因为稀土合金不仅是我国的稀有资源,而且就全世界来看,稀土也是稀缺资源,所以不含有稀土合金的高铬铸铁变质剂不仅成本低,也符合我们的基本国情和可持续发展的需要。
30.(2)本发明所述高铬铸铁变质剂便于吸收。因为71%以上均为cr元素,另外含有ni:10~11.5%,ni的加入更有利于改进高铬铸铁的耐磨性和韧性,有利于综合性能的提高。cr和ni加在一起大概约81~86.5%,这样的变质剂便于高铬铸铁吸收和利用。
31.(3)本发明高铬铸铁变质剂不含si,不会影响高铬铸铁的耐磨性。本发明所述高铬铸铁变质剂,其化学成分不含有si元素,在实际生产中,高铬铸铁最终的si含量尽可能控制0.4~0.6%,这对于提高高铬铸铁的韧性、耐磨性有利,由于原材料层次不齐,而实际生产厂家大多炉内高铬铸铁铁液的si已经超过0.6%,如果再开发一种含si的高铬铸铁变质剂,会因为变质之后高铬铸铁最终的si的增高,影响高铬铸铁的韧性和耐磨性,因此含si的高
铬铸铁变质剂显然不受使用厂家欢迎,为此,本发明的高铬铸铁变质剂由于不含有si,不会因为使用本发明的变质剂而使得最终的si含量超标,所以,本发明的高铬铸铁变质剂必定会收到市场的青睐。
32.(4)本发明变质剂可使高铬铸铁力学性能明显提升。高铬铸铁使用本发明所述高铬铸铁变质剂之后,硬度由hrc58~60,提高至hrc63~65,硬度提高了hrc5左右,而且冲击韧性还由5~8j,提高至8~12j,冲击韧性提高了3~4j,这说明变质剂的使用不仅提高硬度还提高韧性,众所周知,韧性和硬度是一对矛盾,硬度的提高,韧性必然下降,但是如果细化了晶粒,就会使得硬度和韧性同时提高,从以上可以看出,高铬铸铁在使用本发明变质剂之后,综合性能得到了提升,归根原因是变质剂的使用细化了晶粒。
33.(5)本发明所述高铬铸铁用变质剂,使用时,待浇包内有1/5~1/4铁水时,将变质剂直接投入浇包内,进行冲入法使用,使用按照铁液的0.2~0.25%计算,使用方便,用量适中。
34.(6)将几种高铬铸铁变质剂在btmcr26上使用后,性能改善如下表所示,可以看出本发明变质剂是综合性价比非常高的一种变质剂。
35.表1为几种高铬铸铁变质剂在btmcr26上使用后,指标对比情况。
36.附图说明
37.图1为未使用本发明变质剂的高铬铸铁金相组织,200
×
(4%硝酸酒精腐蚀);化学成分组成:c:3.3%,si:0.46%,mn:1.1%,cr:26.3%,b:0.04%,v:0.38%,mo:0.61%,ni:0.55%,cu:0.53%,s、p0.03%,余量为fe及杂质。
38.图2为使用本发明变质剂之后高铬铸铁金相组织,200
×
(4%硝酸酒精腐蚀),(应用实例3),化学成分组成:c:3.3%,si:0.46%,mn:1.1%,cr:26.3%,b:0.04%,v:0.38%,mo:0.61%,ni:0.55%,cu:0.53%,s、p0.03%,余量为fe及杂质。
具体实施方式
39.下面结合具体实施例对本发明进一步说明。
40.实施例1
41.高铬铸铁用变质剂的制备:
42.(1)第一步,准备原材料。
43.称取电解铬、不锈钢304和316l、镍铁、电解锰、电解钒、1#锌锭、电解铜、硼砂、氮化铬、锆铁、铌铁、电解钴、钼铁,按照最终化学成分范围为:cr:71%,ni:10%,mo:1.3%,mn:1.1%,v:0.2%,zn:0.7%,cu:0.8%,b:0.18%,n:0.15%,zr:0.15%,nb:0.26%,co:0.15%,分别称取一定的质量分数进行配料。
44.(2)第二步,原材料预处理。
45.将第一步称取的原材料,混合均匀,放入箱式炉中,在300℃温度条件下进行保温,保温时间控制2~6小时,保温时间根据装炉料的多少进行调整,装炉料500kg以下,保温2小时,彻底烘干原材料里面的水分和氧化锈。
46.(3)第三步,原料的熔炼。
47.将第二步预处理的原材料放入真空感应中频电炉进行熔炼,以电炉额定功率50%进行升温熔炼,当合金料全部熔化之后,此时合金液温度1400~1480℃,保温8分钟,即可出炉,把合金液浇注到事先准备好的金属型中,浇注合金预制块,合金液冷却之后,得到合金预制块。
48.(4)第四步,破碎合金块。
49.将第三步制备的合金预制块,用破碎机破碎成粒度为30~50mm的颗粒,然后将颗粒真空包装。
50.(5)第五步,雾化合金块。
51.将第四步制备的合金块利用金属超声雾化制备装置将合金预制块制备成金属粉末(这种合金粉末即为本发明的高铬铸铁变质剂),熔化合金块的温度为1350~1400℃,合金块熔化之后,将合金液态倒入雾化器进行雾化,全过程进行真空操作。金属超声雾化制备装置一般由熔炼炉、雾化罐、超声雾化器、粉末收集罐、真空充气系统、馈液系统、控制系统构成。雾化之后得到的粉末粒度50μm~150μm,松装密度3.2~3.5g/cm3,流动性<30s/50g,氧含量<100ppm。
52.(6)第六步,粉末冷却。
53.将第五步得到的合金粉末(高铬铸铁变质剂)冷却至常温(25~30℃)。
54.(7)第七步,包装合金粉末。
55.将第六步得到的合金粉末(高铬铸铁变质剂)按照每一袋1kg进行包装,采用牛皮纸(牛皮纸袋内有塑料薄膜)进行真空包装。
56.(8)第八步,质量检测。
57.将第六步制备的合金粉末(高铬铸铁变质剂)每个批次进行抽查质量检验,检测粉末尺寸与化学成分指标,合格者入库。
58.上述本发明所述高铬铸铁变质剂的制备方法,其中所涉及的原材料由商购可以获得,所涉及的设备和工艺操作均是本技术领域的技术人员所熟知的。
59.实施例2
60.高铬铸铁用变质剂的制备:
61.(1)第一步,准备原材料。
62.称取电解铬、不锈钢304和316l、镍铁、电解锰、电解钒、1#锌锭、电解铜、硼砂、氮化铬、锆铁、铌铁、电解钴、钼铁,按照最终化学成分范围为:cr:75%,ni:11.5%,mo:01.3%,mn:1.45%,v:0.28%,zn:1.2%,cu:1.0%,b:0.25%,n:0.2%,zr:0.2%,nb:0.3%,co:0.2%,分别称取一定的质量分数进行配料。
63.(2)第二步,原材料预处理。
64.将第一步称取的原材料,混合均匀,放入的箱式炉中,在260℃温度条件下进行保温,保温时间控制2~6小时,保温时间根据装炉料的多少进行调整,装炉料500kg~1000kg保温3~4小时。彻底烘干原材料里面的水分和氧化锈。
65.(3)第三步,原料的熔炼。
66.将第二步预处理的原材料放入真空感应中频电炉进行熔炼,以电炉额定功率40%进行升温熔炼,当合金料全部熔化之后,此时合金液温度1400~1480℃,保温10分钟,即可出炉,把合金液浇注到事先准备好的金属型中,浇注合金预制块,合金液冷却之后,得到合金预制块。
67.(4)第四步,破碎合金块。
68.将第三步制备的合金预制块,用破碎机破碎成粒度为30~50mm的颗粒,然后将颗粒真空包装。
69.(5)第五步,雾化合金块。
70.将第四步制备的合金块利用金属超声雾化制备装置将合金预制块制备成金属粉末(这种合金粉末即为本发明的高铬铸铁变质剂),熔化合金块的温度为1350~1400℃,合金块熔化之后,将合金液态倒入雾化器进行雾化,全过程进行真空操作。金属超声雾化制备装置一般由熔炼炉、雾化罐、超声雾化器、粉末收集罐、真空充气系统、馈液系统、控制系统构成。雾化之后得到的粉末粒度50μm~150μm,松装密度3.2~3.5g/cm3,流动性<30s/50g,氧含量<100ppm。
71.(6)第六步,粉末冷却。
72.将第五步得到的合金粉末(高铬铸铁变质剂)冷却至常温(25~30℃)。
73.(7)第七步,包装合金粉末。
74.将第六步得到的合金粉末(高铬铸铁变质剂)按照每一袋1kg进行包装,采用牛皮纸(牛皮纸袋内有塑料薄膜)进行真空包装。
75.(8)第八步,质量检测。
76.将第六步制备的合金粉末(高铬铸铁变质剂)每个批次进行抽查质量检验,检测粉末尺寸与化学成分指标,合格者入库。
77.实施例3
78.高铬铸铁用变质剂的制备:
79.(1)第一步,准备原材料。
80.称取电解铬、不锈钢304和316l、镍铁、电解锰、电解钒、1#锌锭、电解铜、硼砂、氮化铬、锆铁、铌铁、电解钴、钼铁,按照最终化学成分范围为:cr:72.5%,ni:11%,mo:1.2%,mn:1.25%,v:0.25%,zn:0.9%,cu:0.9%,b:0.20%,n:0.17%,zr:0.17%,nb:0.28%,
co:0.17%,分别称取一定的质量分数进行配料。
81.(2)第二步,原材料预处理。
82.将第一步称取的原材料,混合均匀,放入箱式炉中,在380℃温度条件下进行保温,保温时间控制2~6小时,保温时间根据装炉料的多少进行调整,装炉料1000kg以上保温4~6小时。彻底烘干原材料里面的水分和氧化锈。
83.(3)第三步,原料的熔炼。
84.将第二步预处理的原材料放入真空感应中频电炉进行熔炼,以电炉额定功率50%进行升温熔炼,当合金料全部熔化之后,此时合金液温度1400~1480℃,保温5分钟,即可出炉,把合金液浇注到事先准备好的金属型中,浇注合金预制块,合金液冷却之后,得到合金预制块。
85.(4)第四步,破碎合金块。
86.将第三步制备的合金预制块,用破碎机破碎成粒度为30~50mm的颗粒,然后将颗粒真空包装。
87.(5)第五步,雾化合金块。
88.将第四步制备的合金块利用金属超声雾化制备装置将合金预制块制备成金属粉末(这种合金粉末即为本发明的高铬铸铁变质剂),熔化合金块的温度为1350~1400℃,合金块熔化之后,将合金液态倒入雾化器进行雾化,全过程进行真空操作。金属超声雾化制备装置一般由熔炼炉、雾化罐、超声雾化器、粉末收集罐、真空充气系统、馈液系统、控制系统构成。雾化之后得到的粉末粒度50μm~150μm,松装密度3.2~3.5g/cm3,流动性<30s/50g,氧含量<100ppm。
89.(6)第六步,粉末冷却。
90.将第五步得到的合金粉末(高铬铸铁变质剂)冷却至常温(25~30℃)。
91.(7)第七步,包装合金粉末。
92.将第六步得到的合金粉末(高铬铸铁变质剂)按照每一袋1kg进行包装,采用牛皮纸(牛皮纸袋内有塑料薄膜)进行真空包装。
93.(8)第八步,质量检测。
94.将第六步制备的合金粉末(高铬铸铁变质剂)每个批次进行抽查质量检验,检测粉末尺寸与化学成分指标,合格者入库。
95.下面各应用实例所用的本发明高铬铸铁用变质剂,变质剂重量百分比组成见表2,制备方法同实施例1。在实际使用过程中,需要严格控制高铬铸铁铁液中氧的含量(<50ppm)。
96.表2变质剂实例一览表(%)
97.实例序号crnimomnvzncubnzrnbco171.0510.530.911.110.210.710.840.180.150.1520.260.15272.2311.031.211.220.251.200.860.1850.250.1590.300.20372.6510.441.31.310.280.910.940.190.170.1620.260.17474.0811.51.111.090.211.130.990.210.160.200.2710.19575.0011.030.991.450.261.111.000.220.150.180.2930.18674.9511.431.211.210.2470.810.860.250.1630.1660.2740.152
98.应用实例1:
99.本实例的高铬铸铁用变质剂(表2中1号方案)在cr15上使用步骤如下:
100.⑴
第一步,配置原材料。称取所需重量的原材料:生铁、废钢、硅铁、锰铁、铬铁、硼铁、钒铁、镍、铜、稀土硅铁。
101.⑵
第二步,原料的熔炼。根据材质成分要求,各种炉料均应干净且不含杂质。当铁液熔炼温度达到1540~1550℃时,出铁到处理包内。
102.⑶
第三步,变质处理。浇包内冲入1/5~1/4铁水时,将本发明制得的高铬铸铁用变质剂0.2%投入浇包。
103.⑷
第四步,浇注。将第三步处理好的铁液,待反应完毕后打渣,静置,然后浇注。
104.⑸
第五步,浇注成型。待铁水温度为1350~1380℃时,将处理好的铁水浇注铸型中。
105.⑹
第六步,清理,抛光。将第五步制备的铸件进行清理打磨和抛光,待用。
106.⑺
第七步,清理打磨。
107.⑻
第八步,热处理。对铸件进行热处理,600℃以下每小时升温速度控制在50~80℃,并分别在300℃和600℃进行保温1小时,600℃后,快速升温至~980℃进行保温,保温时间达到后,进行风冷淬火。淬火完毕后一般立即进行回火,回火温度260℃,回火时间3小时。
108.⑼
第九步,抛丸、检测尺寸与性能,入库。
109.⑽
第十步,利用光谱仪分析高铬铸铁的重量百分比含量为:c:3.0%,si:0.55%,mn:1.1%,cr:15.3%,b:0.05%,v:0.28%,mo:0.4%,ni:0.5%,cu:0.5%,re:0.028%,s:0.03%,p:0.03%,余量为fe及杂质。
110.⑾
热处理后铸件力学性能指标:hrc61,冲击韧性:9j/cm2,耐磨性提高25%。
111.应用实例2:
112.本实例的高铬铸铁用变质剂(表2中2号方案)在cr20上使用步骤如下:
113.⑴
第一步,配置原材料。称取所需重量的原材料:生铁、废钢、硅铁、锰铁、铬铁、硼铁、钒铁、镍、铜、稀土硅铁。
114.⑵
第二步,原料的熔炼。根据材质成分要求,各种炉料均应干净且不含杂质。当铁液熔炼温度达到1540~1545℃时,出铁到处理包内。
115.⑶
第三步,变质处理。浇包内冲入1/5~1/4铁水时,将本发明高铬铸铁用变质剂0.23%投入浇包。
116.⑷
第四步,浇注。将第三步处理好的铁液,待反应完毕后打渣,静置,然后浇注。
117.⑸
第五步,浇注成型。待铁水温度为1350~1380℃时,将处理好的铁水浇注铸型中。
118.⑹
第六步,清理,抛光。将第五步制备的铸件进行清理打磨和抛光,待用。
119.⑺
第七步,清理打磨。
120.⑻
第八步,热处理。对铸件进行热处理,600℃以下每小时升温速度控制在50~80℃,并分别在300℃和600℃进行保温1小时,600℃后,快速升温至~990℃进行保温,保温时间达到后,进行风冷淬火。淬火完毕后一般立即进行回火,回火温度270℃,回火时间3.5小时。
121.⑼
第九步,抛丸、检测尺寸与性能,入库。
122.⑽
第十步,利用光谱仪分析高铬铸铁的重量百分比含量为:c:3.2%,si:0.56%,mn:1.2%,cr:20.6%,b:0.03%,v:0.18%,mo:0.51%,ni:0.65%,cu:0.53%,re:0.038%,s:0.03%,p:0.03%,余量为fe及杂质。
123.⑾
热处理后铸件力学性能指标:hrc62.5,冲击韧性:10.5j/cm2,耐磨性提高26%。
124.应用实例3:
125.本实例的高铬铸铁用变质剂(表2中3号方案)在cr24上使用步骤如下:
126.⑴
第一步,配置原材料。称取所需重量的原材料:生铁、废钢、硅铁、锰铁、铬铁、硼铁、钒铁、镍、铜、稀土硅铁。
127.⑵
第二步,原料的熔炼。根据材质成分要求,各种炉料均应干净且不含杂质。当铁液熔炼温度达到1540~1545℃时,出铁到处理包内。
128.⑶
第三步,变质处理。浇包内冲入1/5~1/4铁水时,将本发明高铬铸铁用变质剂0.25%投入浇包。
129.⑷
第四步,浇注。将第三步处理好的铁液,待反应完毕后打渣,静置,然后浇注。
130.⑸
第五步,浇注成型。待铁水温度为1350~1380℃时,将处理好的铁水浇注铸型中。
131.⑹
第六步,清理,抛光。将第五步制备的铸件进行清理打磨和抛光,待用。
132.⑺
第七步,清理打磨。
133.⑻
第八步,热处理。对铸件进行热处理,600℃以下每小时升温速度控制在50~80℃,并分别在300℃和600℃进行保温1小时,600℃后,快速升温至~1020℃进行保温,保温时间达到后,进行风冷淬火。淬火完毕后一般立即进行回火,回火温度400℃,回火时间4小时。
134.⑼
第九步,抛丸、检测尺寸与性能,入库。
135.⑽
第十步,利用光谱仪分析高铬铸铁的重量百分比含量为:c:3.3%,si:0.46%,mn:1.1%,cr:24.3%,b:0.04%,v:0.38%,mo:0.61%,ni:0.55%,cu:0.53%,re:0.033%,s:0.03%,p:0.03%,余量为fe及杂质。
136.⑾
热处理后铸件力学性能指标:hrc63.5,冲击韧性:11.5j/cm2,耐磨性提高28%。
137.应用实例4:
138.本实例的高铬铸铁用变质剂(表2中4号方案)在cr26上使用步骤如下:
139.⑴
第一步,配置原材料。称取所需重量的原材料:生铁、废钢、硅铁、锰铁、铬铁、硼铁、钒铁、镍、铜、稀土硅铁。
140.⑵
第二步,原料的熔炼。根据材质成分要求,各种炉料均应干净且不含杂质。当铁液熔炼温度达到1540~1545℃时,出铁到处理包内。
141.⑶
第三步,变质处理。浇包内冲入1/5~1/4铁水时,将本发明高铬铸铁用变质剂0.25%投入浇包。
142.⑷
第四步,浇注。将第三步处理好的铁液,待反应完毕后打渣,静置,然后浇注。
143.⑸
第五步,浇注成型。待铁水温度为1350~1380℃时,将处理好的铁水浇注铸型中。
144.⑹
第六步,清理,抛光。将第五步制备的铸件进行清理打磨和抛光,待用。
145.⑺
第七步,清理打磨。
146.⑻
第八步,热处理。对铸件进行热处理,600℃以下每小时升温速度控制在50~80℃,并分别在300℃和600℃进行保温1小时,600℃后,快速升温至~1050℃进行保温,保温时间达到后,进行风冷淬火。淬火完毕后一般立即进行回火,回火温度400℃,回火时间4小时。
147.⑼
第九步,抛丸、检测尺寸与性能,入库。
148.⑽
第十步,利用光谱仪分析高铬铸铁的重量百分比含量为:c:3.4%,si:0.46%,mn:1.2%,cr:26.3%,b:0.04%,v:0.28%,mo:0.61%,ni:0.45%,cu:0.53%,re:0.035%,s:0.03%,p:0.03%,余量为fe及杂质。
149.⑾
热处理后铸件力学性能指标:hrc64.5,冲击韧性:11.5j/cm2,耐磨性提高30%。
150.应用实例5:
151.本实例的高铬铸铁用变质剂(表2中5号方案)在cr30上使用步骤如下:其他步骤与应用实例4相同。
152.⑴
利用光谱仪分析高铬铸铁的重量百分比含量为:c:3.5%,si:0.56%,mn:1.2%,cr:30.3%,b:0.04%,v:0.28%,mo:0.64%,ni:0.55%,cu:0.63%,re:0.029%,s:0.03%,p:0.03%,余量为fe及杂质。
153.⑵
热处理后铸件力学性能指标:hrc65.5,冲击韧性:10.5j/cm2,耐磨性提高29%。
154.实施例6
155.本实例的高铬铸铁用变质剂(表2中6号方案)在cr35上使用步骤如下:其他步骤与应用实例4相同。
156.⑴
利用光谱仪分析高铬铸铁的重量百分比含量为:c:3.6%,si:0.53%,mn:1.1%,cr:35.3%,b:0.04%,v:0.38%,mo:0.62%,ni:0.55%,cu:0.63%,re:0.038%,s:0.03%,p:0.03%,余量为fe及杂质。
157.⑵
热处理后铸件力学性能指标:hrc65.5,冲击韧性:9.5j/cm2,耐磨性提高30%。以上是结合具体实施例对本发明的详细介绍,本发明的保护范围不限于此。