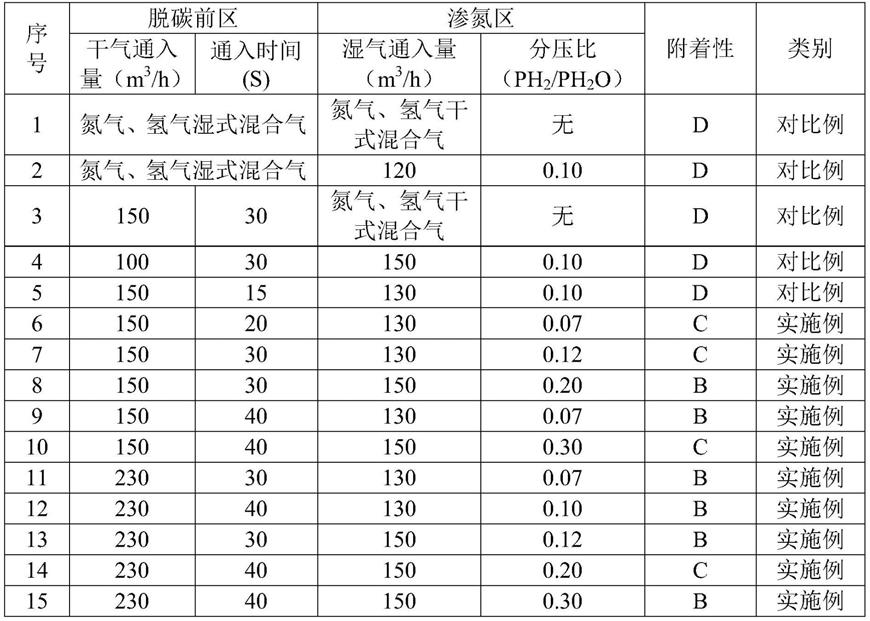
1.本发明涉及取向硅钢制备技术领域,具体涉及一种提高低温高磁感取向硅钢附着性的方法。
背景技术:
2.高磁感取向硅钢广泛应用于各种大、中型变压器的制造。与一般取向硅钢相比,高磁感取向硅钢具有铁损低、磁感应强度高、磁致伸缩小等优点,以其制作的变压器产品具有空载损耗低、噪声低、体积小等特点。因此高磁感取向硅钢越来越多的受到用户欢迎,使用量也逐年加大。目前高磁感取向硅钢有两种生产方式:一种是在热轧工序采用板坯高温加热热轧,即高温高磁感取向硅钢的制备工艺;另一种是采用低温加热热轧、后工序渗氮处理,即低温高磁感取向硅钢的制备工艺。相比而言,采用低板坯加热温度辅以渗氮工艺制造高磁感取向硅钢(即后一种工艺)可大幅降低生产制造成本。
3.制备低温高磁感取向硅钢时,通常需要将硅含量为3%-3.5%的原料板坯经过热轧、常化、一次或多次冷轧等处理步骤,从而形成最终的钢板厚度。成品厚度的钢带还需要在连续炉内进行脱碳退火及渗氮处理,主要目的一是完成初次再结晶使基体中有足够的初次晶粒,二是将碳含量脱至0.003%以下以保证后续高温退火工序中钢带处于单一的α相,三是利用渗氮增加钢带中抑制剂的有效含量。脱碳退火还有一个很重要的作用,即在钢带表面形成一层致密均匀的氧化薄膜,该薄膜将在高温退火过程中发挥至关重要的作用。脱碳退火完成后,将mgo与其他添加剂加入到水中搅拌制成浆体,然后涂覆在钢板表面并干燥,高温退火后涂敷的氧化镁与脱碳退火形成的氧化膜发生如下反应:2mgo+sio2→
mg2sio4。反应形成硅酸镁底层后,在其外表面涂敷磷酸盐绝缘涂层,最终形成硅酸镁底层-磷酸盐绝缘涂层的双层结构。
4.在分析评价取向硅钢底层好坏时,附着性是很重要的一项指标。所谓附着性是指底层与基板的结合程度,附着性不良的硅钢片在纵剪分条或连续冲片时,带钢承受的张力会使边部的涂层脱落,从而严重影响绝缘效果,急剧增加涡流损耗,甚至造成变压器击穿等恶性事故。随着国家电网改造的深入推进,装机容量越来越大,大中型变压器比例增加,为防止铁芯材料叠片层间发生短路,涡流损耗快速增大造成铁芯材料被击穿,提高高磁感取向硅钢附着性及电阻已成为技术发展的要求。目前的低温高磁感取向硅钢依然存在硅酸镁底层附着性不好的问题。
5.中国发明专利cn2018105285532公开了一种提高高温hib附着性的方法,将经过常化、冷轧工艺制备得到的高温hib送入退火炉,向退火炉内通入一定量氨气进行正常脱碳退火处理,随后按照常规工艺进行高温退火、拉伸平整,最终得到附着性提高的高温hib。该方案在现有高温hib连续式脱碳退火炉中通入适量氨气腐蚀钢板表面,提高了钢板表面铁基体的腐蚀程度,控制渗氮量10-20ppm时成品底层钉轧效果明显,附着性大幅提升,c级以上达到100%,b级以上达到80%。分析可知该方案虽然提供了一种提高高温hib钢附着性的方法,但是在脱碳退火工艺上高温高磁感取向硅钢与低温高磁感取向硅钢无相似性,两者并
不具有可比性或参考借鉴意义。此外该方案仅控制渗氮过程,而本技术同时控制了脱碳和渗氮两个过程,在这一点上也存在较大差异。
6.中国发明专利cn2016108433452公开了一种提高低温铸坯加热高磁感取向硅钢底层质量的退火隔离剂,其配方为:9%-14%的硅钢级氧化镁、0.3%-1.0%的tio2、0.05%-1.2%的sb2(so4)3、余量为水,其中硅钢级氧化镁的柠檬酸活性值为50-120sec,粘度为15-60c.p。该退火隔离剂解决了目前低温铸坯加热高磁感取向硅钢所面临的最大问题,即底层缺陷问题,使得涂层外观优良、附着性达到c级以上,层间电阻大进而大幅提升了高磁感取向硅钢的产品质量。
7.中国发明专利cn2008100410852公开了具有良好底层的取向硅钢生产的硅酸镁喷涂方法及装置,将经过轧制及脱碳退火的取向硅钢带钢送入等离子喷涂硅酸镁室内进行喷涂处理,进而提高了硅酸镁底层附着性。
8.中国发明专利cn2005101108993公开了一种具有良好底层的低温加热生产取向硅钢的方法,将采用通常工艺生产的取向硅钢板坯在1280℃以下加热后进行热轧、一次或者二次冷轧,得到成品板厚后再依次进行渗氮、脱碳退火、涂敷隔离剂、高温退火处理。在渗氮工艺中加热段露点控制在-15℃至-40℃,在常规渗氮温度下渗氮时间为5-50秒,渗氮介质为nh3,露点控制在-40℃以下,保护气氛为h2和n2的混合气体,气氛露点(即渗氮露点)在-15℃至-40℃之间。在后续的脱碳退火工艺中,在常规脱碳退火温度下将气氛露点控制在50-75℃。在涂敷隔离剂工艺中,利用水化率在1.5%-6%的硅钢专用mgo制成退火隔离剂浆液,并在隔离剂浆液中加入重量百分比为0.1%-10%的一种或者两种以上na、k、zn、ca、cr、zr、sr、ti、sb的氧化物或者盐类化合物,制成的浆液涂敷在渗氮脱碳后的钢板表面。
9.上述发明专利分别从退火隔离剂涂液、硅酸镁喷涂方式以及在退火隔离剂中添加k、zn、ca、cr、zr、sr、ti、sb的氧化物或者盐类等方面阐述了提高低温高磁感取向硅钢附着性的方法,均未涉及或说明脱碳退火及渗氮工艺究竟如何影响附着性,而实际生产过程中脱碳退火及渗氮工艺的控制对附着性有着重要影响。
技术实现要素:
10.本发明的目的在于提供一种提高低温高磁感取向硅钢附着性的方法,该方法包括以下步骤:将经过常化、冷轧工艺制备得到的低温高磁感取向硅钢送入常规连续式脱碳退火炉中,在脱碳退火前区通入氮气、氢气干式混合气,在脱碳退火后区(均热炉2后区)通入氮气、氢气湿式混合气进行脱碳,在渗氮区通入氮气、氢气湿式混合气以及氨气进行渗氮,最后涂覆mgo隔离剂并继续后处理即可。
11.进一步的,低温高磁感取向硅钢的制备过程如下:经转炉冶炼、连铸后得到连铸板坯,将连铸板坯加热至1100-1200℃,接着热轧、常化酸洗、冷轧即可。
12.更进一步的,低温高磁感取向硅钢的成品厚度控制在0.18mm-0.30mm之间。
13.进一步的,在脱碳退火前区通入的氮气、氢气干式混合气的通入量为150-230m3/h,混合气中氢气所占的体积百分比为30%-50%。
14.更进一步的,脱碳退火前区氮气、氢气干式混合气的通入时长为20-40sec。
15.进一步的,在脱碳退火后区通入的氮气、氢气湿式混合气露点为45-65℃,分压比p
h2o
/p
h2
为0.3-0.5,利用该混合气将低温高磁感取向硅钢中的碳脱至0.003%以下。
16.进一步的,在渗氮区通入氮气、氢气湿式混合气的同时,通入氨气进行渗氮(即氮气、氢气湿式混合气与氨气同时通入)。
17.更进一步的,渗氮时氮气、氢气湿式混合气的分压比p
h2o
/p
h2
为0.05-0.20,通入量为80-150m3/h,混合气中氨气所占体积百分比为5%-12%,渗氮温度控制在840-890℃。
18.进一步的,所述后处理具体如下:涂覆完mgo隔离剂后,经高温(1170-1220℃)退火、拉伸平整退火后,得到附着性提高的低温高磁钢取向硅钢最终成品。
19.本发明在现有常规低温高磁感取向硅钢制备工艺基础上,通过调整脱碳退火气氛分布及渗氮气氛等工艺参数,实现了提高低温高磁感取向硅钢附着性的目的。研究发现,在退火炉脱碳前区通入一定量的氮气、氢气干式混合气,降低脱碳前区分压比,在此条件下主要发生si与氧的氧化反应,生成层片状sio2;而后通入高分压比的氮气、氢气湿式混合气进行脱碳,同时生成fe的氧化物及球状sio2,增加了钢中总氧量,有效提高氧化层的厚度;渗氮区通入低分压比的氮气、氢气湿式混合气,减少了氧化层的还原。一般来说,脱碳退火后氧化层的结构和厚度直接影响底层质量和附着性,通过上述工艺条件可获得合适厚度的氧化层结构,钢板表面涂覆氧化镁后形成的玻璃膜较常规工艺条件更连续致密。
20.与现有提高低温高磁感取向硅钢附着性的方法相比,本发明方法能有效提高钢中总氧量、增加氧化层厚度、改善氧化层结构,经高温退火处理后生成致密的硅酸镁底层,附着性大幅度提高,最终产品均可达c级以上,大部分达到b级。
附图说明
21.图1为本发明设备及工艺流程图。
22.其中1-加热炉,2-均热炉,3-气氛隔离装置,4-hef炉,5-均热炉。
具体实施方式
23.为使本领域普通技术人员充分理解本发明的技术方案和有益效果,以下结合具体实施例及附图进行进一步说明。
24.一种提高低温高磁感取向硅钢附着性的方法,整个工艺流程为:常化
→
冷轧
→
脱碳退火
→
高温退火
→
拉伸平整处理,具体过程如下:
25.如附图1所示,经转炉冶炼、连铸得到连铸板坯,将其加热到1100-1200℃后热轧、常化酸洗,冷轧至0.18-0.30mm得到成品厚度的低温高磁感取向硅钢。低温高磁感取向硅钢经加热炉1加热至脱碳温度后进入均热炉2,在均热炉2前区通入氮气、氢气干式混合气。该混合气中氢气所占体积百分比为30%-50%,通入时长为20-40sec,通入量为150-230m3/h。然后在均热炉2后区通入氮气、氢气湿式混合气进行脱碳,混合气露点45-65℃,分压比p
h2o
/p
h2
为0.3-0.5。经此处理后将碳脱至0.003%以下,并进行初次再结晶,形成表面氧化层。在均热炉2和hef炉4之间设置有气氛隔离装置3,主要用于隔离均热炉2中的高分压比湿式混合气。脱碳后的带钢进入hef炉4后,通入氮气、氢气湿式混合气,分压比p
h2o
/p
h2
为0.05-0.30,通入量为80-150m3/h。在通入氮气、氢气湿式混合气的同时通入氨气进行渗氮,整个混合气中氨气所占的体积百分比为5%-12%,渗氮温度控制840-890℃。经过脱碳、渗氮处理的带钢继续进入均热炉5完成本发明的核心处理流程,后续冷却涂覆氧化镁隔离剂,接着在1170-1220℃下高温退火、拉伸平整退火,最终得到附着性大幅提高的低温高磁钢取向硅
钢产品。
26.为了充分说明本发明方法的有效性和技术效果,选取了相同制备工艺及成分的常规低温高磁取向硅钢,按照本发明方法进行了连续脱碳退火工艺试验并和常规工艺进行了对比,结果如下表所示:
27.表1不同工艺条件制得的低温高磁取向硅钢附着性对比表
[0028][0029]
从表1可以看出,对比例1、2在脱碳前区通入氮气、氢气湿式混合气,氧含量偏低使得生成的氧化层较薄,进而导致成品硅酸镁底层较薄,附着性不好。对比例3在脱碳退火前区通入氮气、氢气干式混合气,虽然增加了氧化层厚度,但渗氮区通入的氮气、氢气干式混合气对氧化层有还原作用,造成氧化层不均匀成品附着性依然较差。对比例4脱碳前区通入的氮气、氢气干式混合气气量较少,对比例5脱碳前区通入的氮气、氢气干式混合气时间较短,均未达到提高成品附着性的效果。本发明在现有常规低温高磁感取向硅钢制备工艺基础上,通过调整脱碳退火气氛分布及渗氮气氛等工艺参数,实现了提高低温高磁感取向硅钢附着性的目的,测试结果表明产品的附着性都在c级以上,大部分都能达到b级。
[0030]
以上仅列举了本发明部分较佳实施方式,并不构成对本发明的任何限制,基于本发明做出的任何简单变换、修改均落入本发明的保护范围之内。