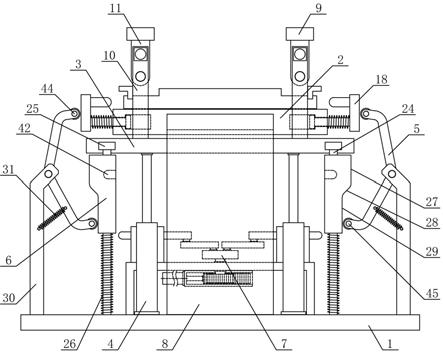
1.本发明属于加工机械设备领域,尤其涉及一种用于工件定位的加工平台。
背景技术:
2.机械工件是组成机械不可分拆的单个制件,它在自动化工业中起着重要的作用,机械工件包括零部件的联接,起支承作用的零部件,起润滑作用的润滑系统和密封零部件,传递运动和能量的传动系统的零部件。在对机械工件进行加工的过程中,主要是将待加工的机械工件放置至加工平台上,再利用数控加工机头将工件进行车、铣、刨、钻、磨等加工,在对工件进行上述加工时,需要利用工件固定设备将工件平稳牢固的压紧固定于加工平台,现有的工件固定设备主要采用气缸驱动压紧板将工件压紧固定,工件在气缸的作用下稳定的放置固定于加工平台上,在利用气缸将工件固定加工的过程中,当固定工件用的气缸由于故障而难以继续平稳的对工件进行压紧固定,工件在失去外部压紧力的情况下放置于加工平台上,因此利用加工机头对工件进行加工会造成工件位置产生偏移歪斜,不仅会导致工件加工产生误差,造成工件报废,严重的甚至还会造成工件倾倒而将加工机头损坏和对加工工人造成伤害,现有的工件加工平台在将工件进行放置加工时,需要工人将工件准确的放置至加工平台上,现有的加工平台没有设置工件位置自动纠偏调整机构,难以实现对工件在放置固定过程中自动实现纠偏对中定位,因此对工人放置工件的位置要求较高,工人劳动强度较大且工件放置加工效率较低,难以满足工件加工使用的需要。
技术实现要素:
3.本发明所要解决的技术问题是克服现有技术中所存在的上述不足,而提供一种结构设计合理,能够高效平稳的将工件对中定位并压紧固定,提高工件加工的效率和质量,满足加工使用需要的用于工件定位的加工平台。
4.为了解决上述技术问题,本发明所采用的技术方案是:一种用于工件定位的加工平台,其特征在于:所述用于工件定位的加工平台包括工件加工底座、工件放置平台、往复升降压板、工件压紧气缸、定位往复摆板、推板升降导板和锁紧限位机构,所述工件放置平台、往复升降压板和工件加工底座从上至下依次水平设置,所述工件放置平台两侧分别对称固定设置有加工支承立板,加工支承立板两端与工件加工底座连接固定,所述往复升降压板下侧与工件加工底座之间竖直均匀设置有多个工件压紧气缸,所述往复升降压板上方两侧分别水平设置有工件加工压板,两块工件加工压板分别设置于工件放置平台上方两侧,工件加工压板两端的往复升降压板上分别竖直固定设置有压料升降立板,工件加工压板两侧端部分别固定设置有转动调节连板,转动调节连板端部转动连接于对应侧的压料升降立板中部,压料升降立板上端外侧固定设置有压板定位支架,压料升降立板上端垂直设置有压板定位导杆,压板定位导杆沿水平方向滑动设置于压板定位支架和压料升降立板,压板定位支架内侧的压板定位导杆上固定设置有推杆弹簧挡板,推杆弹簧挡板与压板定位支架之间的压板定位导杆上套装设置有导杆复位弹簧,压板定位导杆外侧端部固定设置有
调节拉杆连板,转动调节连板上对应位置设置有与压板定位导杆相适配的压板定位杆孔,所述工件放置平台两侧分别水平设置有承推往复导板,承推往复导板上部沿工件放置平台侧水平固定设置有工件定位推板,承推往复导板下部沿工件放置平台侧两端分别水平固定设置有承推平移导杆,承推平移导杆水平滑动设置于工件放置平台,承推平移导杆沿工件放置平台侧端部固定设置有平移限位挡板,工件放置平台内水平设置有与平移限位挡板相适配的承推平移通道,承推往复导板与工件放置平台之间的承推平移导杆上套装设置有推板平移弹簧,所述工件加工底座上方两侧对称设置有推板升降导板,推板升降导板水平设置于往复升降压板下侧,推板升降导板两端的工件加工底座上分别竖直固定设置有往复升降导杆,往复升降导杆上端固定设置有提升限位挡板,推板升降导板竖直滑动设置于往复升降导杆,推板升降导板下侧的往复升降导杆上套装设置有推板提升弹簧,推板升降导板外侧表面从上至下依次设置有夹料定位竖面、推料对中斜面和复位导向竖面,推料对中斜面上下两侧与夹料定位竖面和复位导向竖面之间采用弧面过渡连接,所述工件加工底座上方两侧分别竖直固定设置有摆板往复支座,定位往复摆板为c形结构,定位往复摆板中部铰接连接于摆板往复支座上侧端部,工件加工底座上方两侧的定位往复摆板对称设置,定位往复摆板上侧端部相邻设置于承推往复导板外侧表面,定位往复摆板下侧端部相邻设置于推板升降导板外侧表面,定位往复摆板下侧两端与摆板往复支座之间设置有摆板复位拉簧,所述锁紧限位机构水平固定设置于往复升降压板下侧中部的工件加工底座上,锁紧限位机构包括锁紧限位支架、限位往复转轴、推杆限位气缸和限位平移销杆,锁紧限位支架水平固定设置于往复升降压板下侧中部的工件加工底座上,限位往复转轴竖直转动连接于锁紧限位支架中部,限位往复转轴下端水平固定设置有限位往复齿轮,限位往复齿轮一侧的锁紧限位支架上水平固定设置有齿板平移支架,齿板平移支架内水平滑动设置有与限位往复齿轮啮合连接的往复平移齿板,推杆限位气缸水平固定设置于齿板平移支架一侧,推杆限位气缸输出端与往复平移齿板端部固定连接,所述限位往复转轴上端水平固定设置有限位往复转盘,限位往复转盘两侧的锁紧限位支架上分别固定设置有销杆往复导板,锁紧限位支架两侧的销杆往复导板上分别水平滑动设置有限位平移销杆,限位往复转盘上部沿径向方向的两端与对应侧的限位平移销杆之间分别设置有平移推拉连杆,平移推拉连杆两端分别铰接连接于限位往复转盘外侧和限位平移销杆端部,所述推板升降导板沿锁紧限位机构侧水平设置有与限位平移销杆相适配的锁紧限位杆槽。
5.进一步地,所述往复升降压板下侧的多个工件压紧气缸采用同一路气源并联驱动。
6.进一步地,所述转动调节连板相邻的压料升降立板上固定设置有限位承板角块,限位承板角块设置于压料升降立板沿定位往复摆板侧中部。
7.进一步地,所述定位往复摆板上侧端部转动连接有推板平移导轮,定位往复摆板下侧端部转动连接有承推摆动导轮。
8.本发明与现有技术相比,具有以下优点和效果:本发明结构设计合理,通过工件加工压板两侧的转动调节连板端部转动连接于对应侧的压料升降立板中部,压板定位导杆沿水平方向滑动设置于压板定位支架和压料升降立板,转动调节连板上对应位置设置有与压板定位导杆相适配的压板定位杆孔,当需要将工件放置至工件放置平台上侧时,转动调节连板带动工件加工压板摆动,使得工件加工压板被摆动调节至工件放置平台两侧,使能避
免工件加工压板对工件放置至工件放置平台上时产生阻挡,确保工件能够被便捷顺畅的放置至工件放置平台上,当转动调节连板摆动调节至竖直位置,利用压板定位导杆与压板定位杆孔的配合连接使能确保转动调节连板稳定的处于竖直位置,确保工件放置平台两侧的工件加工压板能够分别位于工件上方两侧,通过往复升降压板下侧与工件加工底座之间竖直均匀设置有多个工件压紧气缸,利用多个工件压紧气缸竖直向下拉动往复升降压板,往复升降压板能够带动两侧的工件加工压板将工件平稳牢固的压紧固定于工件放置平台,利用多个工件压紧气缸采用同一路气源并联驱动,确保往复升降压板能够在多个工件压紧气缸的带动下平稳准确的升降运动,利用转动调节连板相邻的压料升降立板上固定设置有限位承板角块,使得在转动调节连板进行摆动调节时,限位承板角块能够平稳准确的对转动调节连板进行承托放置,通过工件加工底座上方两侧的推板升降导板水平设置于往复升降压板下侧,推板升降导板竖直滑动设置于往复升降导杆,推板升降导板下侧的往复升降导杆上套装设置有推板提升弹簧,使得在工件压紧气缸带动往复升降压板沿竖直方向进行升降运动时,推板升降导板能够在往复升降压板的下压力和推板提升弹簧的上弹力作用下平稳顺畅的往复升降运动,通过工件放置平台两侧的承推往复导板上部水平固定设置有工件定位推板,承推往复导板下部的承推平移导杆水平滑动设置于工件放置平台,承推往复导板与工件放置平台之间的承推平移导杆上套装设置有推板平移弹簧,当承推往复导板在外力作用下向工件放置平台侧移动时,工件定位推板能够水平推动工件放置平台上的工件,因此在工件放置平台两侧的承推往复导板同步相向进行平移运动时,工件定位推板能够实现对工件纠偏对中定位,确保工件能够平稳准确的放置固定于工件放置平台上,在承推往复导板失去外部推力时,承推往复导板能够在推板平移弹簧的作用下自动平移复位,通过推板升降导板外侧表面从上至下依次设置有夹料定位竖面、推料对中斜面和复位导向竖面,定位往复摆板中部铰接连接于摆板往复支座上侧端部,定位往复摆板下侧两端与摆板往复支座之间设置有摆板复位拉簧,使得在推板升降导板从上至下运动过程中,工件加工底座两侧的定位往复摆板能够在推板升降导板的推动作用下同步相向进行摆动,使能利用定位往复摆板推动承推往复导板向工件放置平台侧移动实现对工件的纠偏对中定位,利用摆板复位拉簧对定位往复摆板的弹力牵拉,使得定位往复摆板下端始终压紧贴合于推板升降导板外侧表面,确保定位往复摆板能够便捷顺畅的往复摆动,利用定位往复摆板上侧端部转动连接有推板平移导轮,定位往复摆板下侧端部转动连接有承推摆动导轮,能够有效降低定位往复摆板工作运行时的阻力,利用上述结构,使得在工件压紧气缸带动往复升降压板竖直向下运动时,往复升降压板能够与定位往复摆板产生连动作用,使得工件能够在移动对中定位后再被平稳牢固的压紧固定,提高工件放置加工的便捷性和准确性,在工件压紧气缸带动往复升降压板竖直向上运动时,推板升降导板能够在推板提升弹簧的作用下同步向上移动,使得工件放置平台两侧的工件定位推板能够同步与工件脱离接触,确保完成加工的工件能够被便捷顺畅的取离,通过锁紧限位机构水平固定设置于往复升降压板下侧中部的工件加工底座上,推杆限位气缸输出端的往复平移齿板与限位往复齿轮啮合连接,限位往复转盘两侧与对应侧的限位平移销杆之间分别设置有平移推拉连杆,推板升降导板沿锁紧限位机构侧水平设置有与限位平移销杆相适配的锁紧限位杆槽,使得在往复升降压板推动推板升降导板竖直向下运动至所需位置,使得工件放置平台上的工件被对中定位和压紧固定后,利用推杆限位气缸带动限位往复转盘进行转动,使得限位往复转盘两侧
的限位平移销杆与对应侧推板升降导板的锁紧限位杆槽配合连接,实现对推板升降导板的锁紧限位,使得当工件压紧气缸产生故障而难以对往复升降压板实现有效的拉力,导致工件加工压板难以对工件产生平稳牢固的压紧固定力时,利用锁紧限位机构对推板升降导板锁紧限位,使得工件放置平台两侧的工件定位推板能够始终将工件限位压紧固定,能够有效避免工件在加工时产生偏移歪斜而导致工件加工产生误差报废,实现对工件在加工过程中定位固定进行双重保险,有效提高工件加工的效率和质量,降低工件加工过程中的报废率和加工安全隐患,通过这样的结构,本发明结构设计合理,能够高效平稳的将工件对中定位并压紧固定,提高工件加工的效率和质量,满足加工使用的需要。
附图说明
9.图1是本发明一种用于工件定位的加工平台的主视结构示意图。
10.图2是本发明一种用于工件定位的加工平台的左视结构示意图。
11.图3是本发明的往复升降压板及其相关机构的主视结构示意图。
12.图4是本发明的往复升降压板及其相关机构的左视结构示意图。
13.图5是本发明的往复升降压板及其相关机构的左视a处示意图。
14.图6是本发明的往复升降压板及其相关机构的主视使用状态示意图。
15.图7是本发明的工件放置平台及其相关机构的主视结构示意图。
16.图8是本发明的锁紧限位机构的主视结构示意图。
17.图9是本发明的锁紧限位机构的俯视结构示意图。
18.图中:1.工件加工底座,2.工件放置平台,3.往复升降压板,4.工件压紧气缸,5.定位往复摆板,6.推板升降导板,7.锁紧限位机构,8.加工支承立板,9.工件加工压板,10.压料升降立板,11.转动调节连板,12.压板定位支架,13.压板定位导杆,14.推杆弹簧挡板,15.导杆复位弹簧,16.调节拉杆连板,17.压板定位杆孔,18.承推往复导板,19.工件定位推板,20.承推平移导杆,21.平移限位挡板,22.承推平移通道,23.推板平移弹簧,24.往复升降导杆,25.提升限位挡板,26.推板提升弹簧,27.夹料定位竖面,28.推料对中斜面,29.复位导向竖面,30.摆板往复支座,31.摆板复位拉簧,32.锁紧限位支架,33.限位往复转轴,34.推杆限位气缸,35.限位平移销杆,36.限位往复齿轮,37.齿板平移支架,38.往复平移齿板,39.限位往复转盘,40.销杆往复导板,41.平移推拉连杆,42.锁紧限位杆槽,43.限位承板角块,44.推板平移导轮,45.承推摆动导轮。
具体实施方式
19.为了进一步描述本发明,下面结合附图进一步阐述一种用于工件定位的加工平台的具体实施方式,以下实施例是对本发明的解释而本发明并不局限于以下实施例。
20.如图1和图2所示,本发明一种用于工件定位的加工平台,包括工件加工底座1、工件放置平台2、往复升降压板3、工件压紧气缸4、定位往复摆板5、推板升降导板6和锁紧限位机构7,工件放置平台2、往复升降压板3和工件加工底座1从上至下依次水平设置,工件放置平台2两侧分别对称固定设置有加工支承立板8,加工支承立板8两端与工件加工底座1连接固定,往复升降压板3下侧与工件加工底座1之间竖直均匀设置有多个工件压紧气缸4,多个工件压紧气缸4采用同一路气源并联驱动,如图3、图4、图5和图6所示,本发明的往复升降压
板3上方两侧分别水平设置有工件加工压板9,两块工件加工压板9分别设置于工件放置平台2上方两侧,工件加工压板9两端的往复升降压板3上分别竖直固定设置有压料升降立板10,工件加工压板9两侧端部分别固定设置有转动调节连板11,转动调节连板11端部转动连接于对应侧的压料升降立板10中部,压料升降立板10上端外侧固定设置有压板定位支架12,压料升降立板10上端垂直设置有压板定位导杆13,压板定位导杆13沿水平方向滑动设置于压板定位支架12和压料升降立板10,压板定位支架12内侧的压板定位导杆13上固定设置有推杆弹簧挡板14,推杆弹簧挡板14与压板定位支架12之间的压板定位导杆13上套装设置有导杆复位弹簧15,压板定位导杆13外侧端部固定设置有调节拉杆连板16,转动调节连板11上对应位置设置有与压板定位导杆13相适配的压板定位杆孔17,利用压板定位导杆13与压板定位杆孔17的配合连接使能确保转动调节连板11稳定的处于竖直位置,多个工件压紧气缸4竖直向下拉动往复升降压板3,往复升降压板3能够带动两侧的工件加工压板9将工件平稳牢固的压紧固定于工件放置平台2,转动调节连板11相邻的压料升降立板10上固定设置有限位承板角块43,限位承板角块43设置于压料升降立板10沿定位往复摆板5侧中部,在转动调节连板11进行摆动调节时,限位承板角块43能够平稳准确的对转动调节连板11进行承托放置。
21.如图7所示,本发明的工件放置平台2两侧分别水平设置有承推往复导板18,承推往复导板18上部沿工件放置平台2侧水平固定设置有工件定位推板19,承推往复导板18下部沿工件放置平台2侧两端分别水平固定设置有承推平移导杆20,承推平移导杆20水平滑动设置于工件放置平台2,承推平移导杆20沿工件放置平台2侧端部固定设置有平移限位挡板21,工件放置平台2内水平设置有与平移限位挡板21相适配的承推平移通道22,承推往复导板18与工件放置平台2之间的承推平移导杆20上套装设置有推板平移弹簧23,本发明的工件加工底座1上方两侧对称设置有推板升降导板6,推板升降导板6水平设置于往复升降压板3下侧,推板升降导板6两端的工件加工底座1上分别竖直固定设置有往复升降导杆24,往复升降导杆24上端固定设置有提升限位挡板25,推板升降导板6竖直滑动设置于往复升降导杆24,推板升降导板6下侧的往复升降导杆24上套装设置有推板提升弹簧26,推板升降导板6外侧表面从上至下依次设置有夹料定位竖面27、推料对中斜面28和复位导向竖面29,推料对中斜面28上下两侧与夹料定位竖面27和复位导向竖面29之间采用弧面过渡连接,本发明的工件加工底座1上方两侧分别竖直固定设置有摆板往复支座30,定位往复摆板5为c形结构,定位往复摆板5中部铰接连接于摆板往复支座30上侧端部,工件加工底座1上方两侧的定位往复摆板5对称设置,定位往复摆板5上侧端部相邻设置于承推往复导板18外侧表面,定位往复摆板5下侧端部相邻设置于推板升降导板6外侧表面,定位往复摆板5下侧两端与摆板往复支座30之间设置有摆板复位拉簧31,定位往复摆板5上侧端部转动连接有推板平移导轮44,定位往复摆板5下侧端部转动连接有承推摆动导轮45,在往复升降压板3推动推板升降导板6从上至下运动过程中,工件加工底座1两侧的定位往复摆板5能够在推板升降导板6的推动作用下同步相向进行摆动,使能利用定位往复摆板5推动承推往复导板18向工件放置平台2侧移动实现对工件的纠偏对中定位。
22.如图8和图9所示,本发明的锁紧限位机构7水平固定设置于往复升降压板3下侧中部的工件加工底座1上,锁紧限位机构7包括锁紧限位支架32、限位往复转轴33、推杆限位气缸34和限位平移销杆35,锁紧限位支架32水平固定设置于往复升降压板3下侧中部的工件
加工底座1上,限位往复转轴33竖直转动连接于锁紧限位支架32中部,限位往复转轴33下端水平固定设置有限位往复齿轮36,限位往复齿轮36一侧的锁紧限位支架32上水平固定设置有齿板平移支架37,齿板平移支架37内水平滑动设置有与限位往复齿轮36啮合连接的往复平移齿板38,推杆限位气缸34水平固定设置于齿板平移支架37一侧,推杆限位气缸34输出端与往复平移齿板38端部固定连接,限位往复转轴33上端水平固定设置有限位往复转盘39,限位往复转盘39两侧的锁紧限位支架32上分别固定设置有销杆往复导板40,锁紧限位支架32两侧的销杆往复导板40上分别水平滑动设置有限位平移销杆35,限位往复转盘39上部沿径向方向的两端与对应侧的限位平移销杆35之间分别设置有平移推拉连杆41,平移推拉连杆41两端分别铰接连接于限位往复转盘39外侧和限位平移销杆35端部,推板升降导板6沿锁紧限位机构7侧水平设置有与限位平移销杆35相适配的锁紧限位杆槽42,利用锁紧限位机构7对推板升降导板6锁紧限位,使得工件放置平台2两侧的工件定位推板19能够始终将工件限位压紧固定,能够有效避免工件在加工时产生偏移歪斜而导致工件加工产生误差报废,实现对工件在加工过程中定位固定进行双重保险,有效提高工件加工的效率和质量,降低工件加工过程中的报废率和加工安全隐患。
23.采用上述技术方案,本发明一种用于工件定位的加工平台在使用的时候,通过工件加工压板9两侧的转动调节连板11端部转动连接于对应侧的压料升降立板10中部,压板定位导杆13沿水平方向滑动设置于压板定位支架12和压料升降立板10,转动调节连板11上对应位置设置有与压板定位导杆13相适配的压板定位杆孔17,当需要将工件放置至工件放置平台2上侧时,转动调节连板11带动工件加工压板9摆动,使得工件加工压板9被摆动调节至工件放置平台2两侧,使能避免工件加工压板9对工件放置至工件放置平台2上时产生阻挡,确保工件能够被便捷顺畅的放置至工件放置平台2上,当转动调节连板11摆动调节至竖直位置,利用压板定位导杆13与压板定位杆孔17的配合连接使能确保转动调节连板11稳定的处于竖直位置,确保工件放置平台2两侧的工件加工压板9能够分别位于工件上方两侧,通过往复升降压板3下侧与工件加工底座1之间竖直均匀设置有多个工件压紧气缸4,利用多个工件压紧气缸4竖直向下拉动往复升降压板3,往复升降压板3能够带动两侧的工件加工压板9将工件平稳牢固的压紧固定于工件放置平台2,利用多个工件压紧气缸4采用同一路气源并联驱动,确保往复升降压板3能够在多个工件压紧气缸4的带动下平稳准确的升降运动,利用转动调节连板11相邻的压料升降立板10上固定设置有限位承板角块43,使得在转动调节连板11进行摆动调节时,限位承板角块43能够平稳准确的对转动调节连板11进行承托放置,通过工件加工底座1上方两侧的推板升降导板6水平设置于往复升降压板3下侧,推板升降导板6竖直滑动设置于往复升降导杆24,推板升降导板6下侧的往复升降导杆24上套装设置有推板提升弹簧26,使得在工件压紧气缸4带动往复升降压板3沿竖直方向进行升降运动时,推板升降导板6能够在往复升降压板3的下压力和推板提升弹簧26的上弹力作用下平稳顺畅的往复升降运动,通过工件放置平台2两侧的承推往复导板18上部水平固定设置有工件定位推板19,承推往复导板18下部的承推平移导杆20水平滑动设置于工件放置平台2,承推往复导板18与工件放置平台2之间的承推平移导杆20上套装设置有推板平移弹簧23,当承推往复导板18在外力作用下向工件放置平台2侧移动时,工件定位推板19能够水平推动工件放置平台2上的工件,因此在工件放置平台2两侧的承推往复导板18同步相向进行平移运动时,工件定位推板19能够实现对工件纠偏对中定位,确保工件能够平稳准确的放
置固定于工件放置平台2上,在承推往复导板18失去外部推力时,承推往复导板18能够在推板平移弹簧23的作用下自动平移复位,通过推板升降导板6外侧表面从上至下依次设置有夹料定位竖面27、推料对中斜面28和复位导向竖面29,定位往复摆板5中部铰接连接于摆板往复支座30上侧端部,定位往复摆板5下侧两端与摆板往复支座30之间设置有摆板复位拉簧31,使得在推板升降导板6从上至下运动过程中,工件加工底座1两侧的定位往复摆板5能够在推板升降导板6的推动作用下同步相向进行摆动,使能利用定位往复摆板5推动承推往复导板18向工件放置平台2侧移动实现对工件的纠偏对中定位,利用摆板复位拉簧31对定位往复摆板5的弹力牵拉,使得定位往复摆板5下端始终压紧贴合于推板升降导板6外侧表面,确保定位往复摆板5能够便捷顺畅的往复摆动,利用定位往复摆板5上侧端部转动连接有推板平移导轮44,定位往复摆板5下侧端部转动连接有承推摆动导轮45,能够有效降低定位往复摆板5工作运行时的阻力,利用上述结构,使得在工件压紧气缸4带动往复升降压板3竖直向下运动时,往复升降压板3能够与定位往复摆板5产生连动作用,使得工件能够在移动对中定位后再被平稳牢固的压紧固定,提高工件放置加工的便捷性和准确性,在工件压紧气缸4带动往复升降压板3竖直向上运动时,推板升降导板6能够在推板提升弹簧26的作用下同步向上移动,使得工件放置平台2两侧的工件定位推板19能够同步与工件脱离接触,确保完成加工的工件能够被便捷顺畅的取离,通过锁紧限位机构7水平固定设置于往复升降压板3下侧中部的工件加工底座1上,推杆限位气缸34输出端的往复平移齿板38与限位往复齿轮36啮合连接,限位往复转盘33两侧与对应侧的限位平移销杆35之间分别设置有平移推拉连杆41,推板升降导板6沿锁紧限位机构7侧水平设置有与限位平移销杆35相适配的锁紧限位杆槽42,使得在往复升降压板3推动推板升降导板6竖直向下运动至所需位置,使得工件放置平台2上的工件被对中定位和压紧固定后,利用推杆限位气缸34带动限位往复转盘39进行转动,使得限位往复转盘39两侧的限位平移销杆35与对应侧推板升降导板6的锁紧限位杆槽42配合连接,实现对推板升降导板6的锁紧限位,使得当工件压紧气缸4产生故障而难以对往复升降压板3实现有效的拉力,导致工件加工压板9难以对工件产生平稳牢固的压紧固定力时,利用锁紧限位机构7对推板升降导板6锁紧限位,使得工件放置平台2两侧的工件定位推板19能够始终将工件限位压紧固定,能够有效避免工件在加工时产生偏移歪斜而导致工件加工产生误差报废,实现对工件在加工过程中定位固定进行双重保险,有效提高工件加工的效率和质量,降低工件加工过程中的报废率和加工安全隐患。通过这样的结构,本发明结构设计合理,能够高效平稳的将工件对中定位并压紧固定,提高工件加工的效率和质量,满足加工使用的需要。
24.本说明书中所描述的以上内容仅仅是对本发明所作的举例说明。本发明所属技术领域的技术人员可以对所描述的具体实施例做各种各样的修改或补充或采用类似的方式替代,只要不偏离本发明说明书的内容或者超越本权利要求书所定义的范围,均应属于本发明的保护范围。