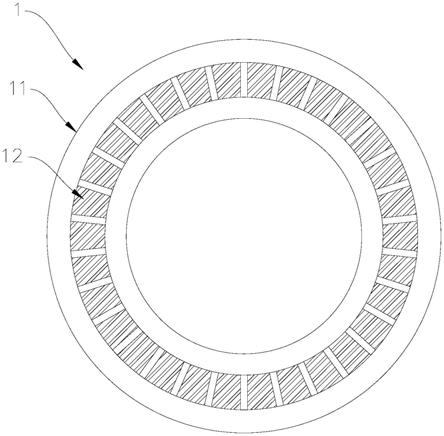
1.本实用新型涉及成型设备技术领域,具体涉及一种捣料压环和金刚石全齿玻璃磨轮捣料装置。
背景技术:
2.现有一种金刚石全齿玻璃磨轮具有沿自身周向均匀布置且有间隔布置的多个磨削体,为成型该多个相互独立的磨削体,模具上设置有多个相互独立的粉料内腔。由于各个独立内腔中的粉料在加热成型过程中无法相互流动,若在投料过程中粉料未被压紧压实,成型后磨轮的磨料体出现料虚和不均匀的问题而影响产品性能。故成型前需要对每个粉料内腔里的粉料进行捣料和压实处理。现有的捣料和压实处理方法为采用捣料棒对各个粉料内腔进行下压和捣实。
3.现有的该捣料和压实方法存在的问题是,一般的金刚石全齿玻璃磨轮具有30个以上的磨削体,捣料工作非常繁琐且效率低下,制造成本较高。
技术实现要素:
4.本实用新型的目的在于提供一种针对金刚石全齿玻璃磨轮的、保证产品质量和有效提高工作效率的捣料压环。
5.本实用新型的目的在于提供一种保证产品质量和有效提高工作效率的金刚石全齿玻璃磨轮捣料装置。
6.本实用新型提供的捣料压环具有捣料端部,捣料端部上具有压制面;捣料压环还包括环形主体和多个凸体,多个凸体从环形主体上背离环形主体伸出,多个凸体沿环形主体的周向有间隔地布置;凸体上远离环形主体的一端为捣料端部,捣料端部的端面为压制面。
7.由上述方案可见,捣料压环上设置环形布置的多个用于捣料的凸体,能对成型模具上环形布置的数十个粉料内腔配合以同时进行捣料压紧处理,有效提高工作效率且降低工作难度,降低制造成本。
8.进一步的方案是,凸体沿环形主体的轴向延伸。
9.由上可见,此设置符合大多金刚石全齿玻璃磨轮上磨削体的轮廓,提高适用性。
10.进一步的方案是,压制面的朝向与凸体的延伸方向相同。
11.另一进一步的方案是,压制面倾斜于凸体的延伸方向设置。
12.更进一步的方案是,捣料端部具有相对设置的高部和矮部;在环形主体的轴向上,高部相对于矮部远离环形主体;在环形主体的径向上,高部相对于矮部远离环形主体的轴心。
13.由上可见,可根据金刚石全齿玻璃磨轮工作面的设置方式来选择采用水平的压制面或是倾斜的压制面,提高适用性。
14.进一步的方案是,凸台与环形主体之间阶梯状连接而在环形主体上形成限位受力
部,限位受力部位于凸台的外周。
15.由上可见,限位受力部能与成型模具的顶面配合以对凸体的压制深度进行限制。
16.进一步的方案是,在凸体的延伸方向的投影上,凸体呈扇环状。
17.本实用新型提供的金刚石全齿玻璃磨轮捣料装置包括成型模具和捣料压环;捣料压环采用上述的捣料压环;成型模具上设置有沿其周向布置的多个粉料内腔,粉料内腔的入口朝上;捣料压环与成型模具可拆卸连接,成型模具与捣料压环同心设置,捣料端部通过入口进入粉料内腔。
18.进一步的方案是,金刚石全齿玻璃磨轮捣料装置还包括装置主体、上压板、下压板和驱动单元;上压板和下压板自上往下依次设置在装置主体上;上压板和下压板的其中一个为固定件,上压板和下压板中的另一个为移动件,移动件移动可使上压板和下压板的距离改变,移动件由驱动单元驱动;成型模具设置在下压板上,上压板与捣料压环相对。
19.进一步的方案是,下压板为移动件,上压板向上移动时,上压板和下压板的距离减小。
20.由上述方案可见,进行捣料压制工作前,只需要把已配合的成型模具和捣料压环放置到下压板上并由定位机构定位后,启动驱动单元,下压板上升使上压板与捣料压环抵接并使凸体进一步进入粉料内腔,从而将粉料内腔内的磨削层粉末原料捣实,有效提高工作效率且降低工作难度,降低制造成本。
附图说明
21.图1为本实用新型金刚石全齿玻璃磨轮捣料装置第一实施例的示意图。
22.图2为本实用新型金刚石全齿玻璃磨轮捣料装置第一实施例中成型模具的俯视图。
23.图3为本实用新型金刚石全齿玻璃磨轮捣料装置第一实施例中捣料压环的仰视图。
24.图4为本实用新型金刚石全齿玻璃磨轮捣料装置第一实施例中捣料压环的剖视图。
25.图5为本实用新型金刚石全齿玻璃磨轮捣料装置第一实施例中捣料压环与成型模具的剖视图。
26.图6为本实用新型金刚石全齿玻璃磨轮捣料装置第二实施例中捣料压环的剖视图。
27.图7为本实用新型金刚石全齿玻璃磨轮捣料装置第三实施例的示意图。
具体实施方式
28.金刚石全齿玻璃磨轮捣料装置第一实施例
29.参见图1,本实用新型的金刚石全齿玻璃磨轮捣料装置包括装置主体91、下压板92、上压板93、液压缸94、成型模具2和本实用新型的捣料压环1。上压板93和下压板92自上往下依次设置在装置主体91上,上压板93作为固定件固定设置在装置主体91的顶部,下压板92作为移动件通过导向杆组件沿高度方向可滑动地设置在装置主体91的中部;液压缸94固定设置在装置主体91的底座上且位于下压板92的下方,液压缸94作为下压板92的驱动单
元,液压缸94用于驱动下压板92上升或下降移动。
30.成型模具2固定在下压板92上,捣料压环1可拆卸地安装在成型模具2之上且与上压板93相对。液压缸94启动使下压板92上升并逐渐靠近上压板93,过程中捣料压环1与上压板93抵接,且捣料压环1逐渐压入成型模具2,从而对成型模具2内的粉料进行捣料和压实处理。
31.参见图2,成型模具2上设置有沿其周向均匀布置的三十个粉料内腔21,相邻的粉料内腔21之间由挡壁22相隔而相互独立,21粉料内腔21的内轮廓呈扇环状,粉料内腔21的入口朝上。
32.参见图3和图4,捣料压环1包括环形主体11和沿环形主体11的周向均匀布置的三十个凸体12,多个凸体12从环形主体11上沿环形主体11的轴向背离环形主体11伸出,且多个凸体12沿环形主体11的周向有间隔地布置,凸体12上远离环形主体11的一端为捣料端部121,捣料端部121的轴向端面为压制面120,压制面120的朝向为环形主体11的轴向。如图3所示,在凸体12的延伸方向的投影上,凸体12呈扇环状,凸体12的外轮廓与粉料内腔21(图2示)的内轮廓匹配。
33.另外,如图4所示,凸台12与环形主体11之间阶梯状连接而在环形主体11上形成限位受力部111,限位受力部111位于凸台12的外周。
34.再结合图5,捣料压环1与成型模具2配合时,捣料压环1与成型模具2可拆卸连接,成型模具2与捣料压环1同心设置,捣料端部121通过粉料内腔21的朝上的入口进入粉料内腔21。
35.捣料压环1上设置环形布置的多个用于捣料的凸体12,能对成型模具2上环形布置的数十个粉料内腔21配合以同时进行捣料压紧处理,有效提高工作效率且降低工作难度,降低制造成本。
36.金刚石全齿玻璃磨轮捣料装置第二实施例
37.参见图6,本实施例中,捣料压环3的压制面320倾斜于凸体32的延伸方向设置。捣料端部321具有相对设置的高部322和矮部323,在环形主体31的轴向上,高部322相对于矮部323远离环形主体31;在环形主体31的径向上,高部322相对于矮部323远离环形主体31的轴心。
38.金刚石全齿玻璃磨轮捣料装置第三实施例
39.参见图7,本实施例中,下压板96作为固定件固定设置在装置主体95的下部,上压板97作为移动件可升降移动地设置在下压板96的上方,驱动单元98设置在上压板97的上方以驱动上压板97升降移动。
40.最后需要强调的是,以上所述仅为本实用新型的优选实施例,并不用于限制本实用新型,对于本领域的技术人员来说,本实用新型可以有各种变化和更改,凡在本实用新型的精神和原则之内,所做的任何修改、等同替换、改进等,均应包含在本实用新型的保护范围之内。