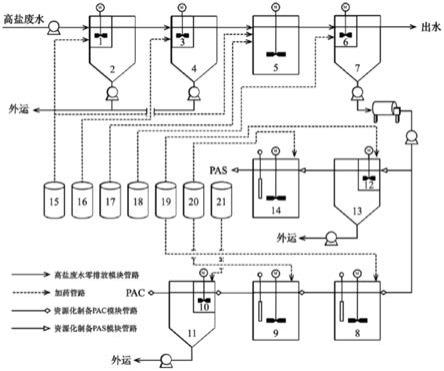
1.本实用新型属于固废资源化处理技术领域,涉及一种用高盐废水零排放系统污泥制备高分子铝盐混凝剂的装置。
背景技术:
2.近年来,高盐废水由于生产量大、腐蚀性强、对环境污染较为严重而备受关注。欧盟早在2000年便颁布社会公约以防止水体受到高盐废水的污染。针对该问题,北京、上海、河南、河北、贵州、四川等省份先后颁布地方标准,对废水盐分的排放浓度进行限制。目前,随着我国对工业生产排放要求的提高,化学工业正处于转型升级的重要阶段,煤化工、石油、天然气、火电等行业均会产生大量的高盐废水,在水资源短缺和水环境严重污染的双重压力下,高盐废水零排放技术正在迅速兴起。
3.针对高盐废水的高氯特点,现有除氯技术主要有膜分离、蒸发结晶、化学沉淀法、吸附法、离子交换法、电解法、氧化法和萃取法等。尽管目前对于高盐废水中氯离子的去除方法较多,但大多处于实验室研究阶段,还存在技术产业化应用瓶颈。膜分离或蒸发结晶工艺已经工程应用,但存在投资成本高、工艺流程复杂、运行管理难度高的问题;对高盐废水中氯离子进行吸附或萃取又存在吸附剂再生和萃取剂反萃的问题,容易造成氯离子重新富集,从而产生新的高盐废水;电解法去除氯离子工艺的能耗较高,产生的cl2、h2等气体存在一定的安全隐患,对工程安全设施和管理的要求极高;化学沉淀法处理高盐废水工艺流程简单,但适用的难溶化合物较少,化学药剂使用量及固废生成量大,这限制了该技术的实际应用。如果能寻求低成本药剂,并实现固废资源化,则能大大提升沉淀法的实际应用价值。
4.超高石灰铝法是传统化学沉淀法的改进,通过向含氯溶液中加入价格相对低廉的钙系盐和铝系盐与氯离子结合生成弗里德尔盐沉淀(ca4al2cl2(oh)
12
),实现氯离子去除。虽然超高石铝法工艺具有操作简便、除氯效果较好等诸多优点,但其药剂使用量大以及固废生成量大的缺陷仍然存在。武杰等曾在《高氯含量废水中氯离子的去除研究》(现代化工,2016,36(4):101-103)中对钙、铝系盐的投加量进行了优化,在ca/al/cl摩尔比为10:4:1的最优条件下,每处理1t氯离子浓度为300mmol/l 的高盐废水,将消耗钙系盐0.168t,铝系盐0.098t,产生固废(弗里德尔盐沉淀) 0.29t。每去除1g氯离子,将产生7.9g弗里德尔盐沉淀。若处理不当,将会造成土地资源占用问题,甚至严重破坏生态环境。因此,解决高盐废水零排放工艺中污泥的后续处理、处置和资源化问题,是零排放工艺具备技术可靠性的关键。
5.中国专利cn211198829u公开了一种降低脱硫废水中氯离子浓度的反应装置,其原理是利用铝冶炼过程中产生的副产品铝灰,再投入石灰乳,与高氯脱硫废水反应,生成弗里德尔盐沉淀,实现烟气脱硫废水中氯离子的去除。该装置在运行时主要存在两方面的缺陷,一是先投入铝灰再投入石灰乳,在非碱性环境下,铝灰难溶于水沉降在反应器底部,不利于共沉淀反应的进行,对脱硫废水中氯离子的去除效果较差;二是采用铝灰作为除氯剂,杂质含量较高,铝元素含量较低且差异较大,无法精准把控反应的投加量。不仅会引入其他杂质对废水进行二次污染,反应过程产生的大量类水滑石无机沉淀物也难以焚烧,脱水后填埋
还会造成土地资源占用问题。
6.中国专利cn111252793a公开了一种聚合氯化铝(pac)的制备方法,包括选取铝矾土、高钙石和无烟煤为原料,将上述原料粉碎后进行混合粉磨得混合物料,将混合物料进行成球处理,然后放入到旋转炉的高温区进行煅烧;混合物料在进入高温区时,部分无烟煤燃尽,在旋转炉中氧气不足的情况下生产活性炭;将煅烧后的物料与高浓度盐酸进行聚合反应,得到黄色液体-pac溶液,在此过程中,活性炭吸附黄色液体-pac溶液中颜色,得白色液体-pac溶液。该制备方法主要存在两方面的不足,一是选用原料种类过多,且铝矾土中al2o3质量分数要求不低于 50%,高钙石中cao质量分数不低于80%,对于原料的选材过于苛刻,生产方法普适性较差;二是生产过程过于复杂,需要进行成球处理以及旋转炉煅烧等高能耗生产步骤将铝源转化为易与酸反应的铝酸钙,且盐酸用量过多不适用于pac的大规模生产。
7.因此,针对现有高盐废水零排放工艺产生的大量固废的出路问题,本实用新型提出了一种回收高盐废水除氯沉淀物制备高分子铝盐混凝剂的工艺技术路线,在解决固废出路的同时补偿零排放系统运行成本。铝盐混凝剂的生产过程相对于传统的混凝剂更加简便、低耗,能够真正实现固废资源化的理念。
技术实现要素:
8.本实用新型的目的就是为了提供一种用高盐废水零排放系统污泥制备高分子铝盐混凝剂的装置与工艺,在解决固废出路的同时补偿零排放系统运行成本,以真正实现固废资源化的理念。
9.本实用新型的目的可以通过以下技术方案来实现:
10.本实用新型的技术方案之一提供了一种用高盐废水零排放系统污泥制备高分子铝盐混凝剂的装置,包括沿高盐废水处理方向依次连接的除镁除硫池、除氯反应池、除氯沉淀池和除氯沉淀物资源化模块。
11.进一步的,当资源化目标产物为pac时,所述除氯沉淀物资源化模块包括依次连接除氯沉淀池的沉淀物出口的第一酸浸池、第一中和池和除钙池;
12.当资源化目标产物为pas时,所述除氯沉淀物资源化模块包括依次连接除氯沉淀池的沉淀物出口的第二酸浸池和第二中和池。
13.更进一步的,所述的除钙池后面还设有第四沉淀池,所述的第二酸浸池与第二中和池之间还设有第五沉淀池。
14.更进一步的,所述的第一酸浸池和第二酸浸池还分别连接酸浸液加药器。
15.更进一步的,所述的第一中和池和第二中和池还分别连接碱化剂加药器。
16.更进一步的,所述的除钙池还连接有除钙剂加药器。
17.进一步的,所述的除镁除硫池前面还设有预沉池,所述的预沉池与除镁除硫池之间还设有第一沉淀池,所述的除镁除硫池与除氯反应池之间还设有第二沉淀池,所述的除氯沉淀池与除氯沉淀物资源化模块之间还设有第三沉淀池。
18.进一步的,所述的预沉池还连接装有石灰浆液的氧化钙加药器,所述的除镁除硫池还连接除镁除硫剂加药器,所述的除氯反应池还分别连接氧化钙加药器和除氯剂加药器,所述的除氯沉淀池还连接絮凝剂加药器。
19.本实用新型的技术方案之二提供了一种利用高盐废水零排放系统污泥制备高分子铝盐混凝剂的方法,包括以下步骤:
20.(1)待处理高盐废水送入预沉池中,加入石灰浆液,沉淀处理,所得出水再送入到除镁除硫池中,所得沉淀物外运回用;
21.(2)往除镁除硫池中加入除镁除硫剂,进行除镁除硫处理,处理完成后的泥水混合液再经沉降分离后,所得沉淀外运,所得出水流入除氯反应池;
22.(3)往除氯反应池中加入石灰浆液与除氯剂,使得含有的氯离子生成复合物沉淀,再投加絮凝剂,沉降处理,所得出水排出,所得沉淀物送入除氯沉淀物资源化模块中进行除氯沉淀物资源化处理;
23.(4)当资源化目标产物为pac时,步骤(3)所得沉淀物经脱水后,先送至第一酸浸池,加入酸浸液处理,随后排入第一中和池中,加入碱化剂调节ph,接着,送入除钙池中,在除钙剂作用下除去钙离子,最后,沉降分离后,得到黄色液体,即为液态pac产品;
24.(5)当资源化目标产物为pas时,步骤(3)所得沉淀物经脱水后,先送至第二酸浸池,加入酸浸液处理,沉降分离后,所得酸液排入第二中和池中,加入碱化剂,得到黄色液体即为液态pas产品。
25.进一步的,步骤(1)中,高盐废水在预沉池中的停留时间为0.5-12h,沉淀处理的时间为0.5-24h;
26.步骤(2)中,所述的除镁除硫剂为氧化钙、氢氧化钠、碳酸钠、铝酸钠或碳酸氢钠中的一种或多种,除镁除硫池中的水力停留时间为0.1-12h,泥水混合液沉降分离的时间为0.1-12h;
27.步骤(3)中,所述除氯剂为氧化铝、铝酸钠、氢氧化铝、硅酸铝或磷酸铝中的一种或多种,除氯反应池的水力停留时间为0.1-12h,除氯沉淀池的水力停留时间为0.1-14h。
28.进一步的,步骤(4)中,第一酸浸池中加入的酸浸液为硝酸、醋酸或盐酸中的一种或几种的复合;
29.步骤(5)中,第二酸浸池中加入的酸浸液为硫酸或草酸中的一种或两种的复合。
30.进一步的,步骤(5)中,所述的除钙剂为硫酸铝、硫酸、十二水硫酸铝钾、硫酸钾或硫酸镁中的一种或几种;
31.步骤(4)和步骤(5)中,所述的碱化剂为氧化钙、氢氧化钠、碳酸钠、碳酸氢钠或氨水中的一种或多种。
32.与现有技术相比,本实用新型具有以下优点:
33.(1)高盐废水零排放工艺模块能够实现废水中污染物的分步去除,并且能够实现固废的分类资源化,通过钙系盐和铝系盐投加量的优化,在满足cl-去除率达到60%的基础上,吨水处理所产生的固废量较少,仅为传统超高石灰铝法工艺的 30-50%;
34.(2)以沉淀的形式分步去除高盐废水中的盐分,避免了重金属离子、镁离子等杂质对除氯沉淀物纯度的影响,在实现固废分类资源化的同时,减少除氯沉淀物资源化过程的除杂步骤,有利于简化铝盐混凝剂制备工艺,保障产品品质;
35.(3)本工艺无需膜分离和蒸发结晶单元,流程短、运行简便、投资成本低,在实现高盐废水零排放的同时,将沉淀物有效的资源化利用,从而实现沉淀物的“零排放”,能够减少环境污染和资源浪费,具有显著的经济和环境效益;
36.(4)将高盐废水零排放工艺进行除氯并形成类水滑石沉淀物(弗里德尔盐)资源化,实现了物质的循环利用,缓解零排放工艺的污泥处理处置压力,避免污泥填埋造成的二次污染问题;
37.(5)在回收固废制备铝盐混凝剂的工艺模块中,由于生成的除氯沉淀物属于碱式盐,极易与酸反应,无需对原料焙烧以提高活性,酸浸池的温度条件远低于传统混凝剂制备工艺的温度条件,在减少能耗与酸用量的同时,实现了铝的高效提取,浸出率高达98%;
38.(6)资源化制备的铝盐混凝剂产品氧化铝含量、盐基度、重金属含量等指标均达到国家标准gb/t22627-2014或hg/t5006-2016的要求,具有纯度高、适用范围广等诸多优点。每吨高盐废水可生产100-150l高盐基度铝盐混凝剂,具有显著的社会、经济和环境效益。
附图说明
39.图1为本实用新型的工艺流程图;
40.图2为实施例2中氧化钙及除氯剂配比除氯效果及在此配比下进行酸浸的铝溶出率的影响。
41.图3为实施例2中为期12天的生产性实证(0.5m3/h)各阶段出水水质。
42.图4为实施例2中为期12天的生产性实证(0.5m3/h)各阶段出水水质(氯离子浓度等)
43.图5为实施例2中氯离子去除形成的类水滑石沉淀物资源化制备铝盐混凝剂过程的酸浸条件及盐基度调节的优化结果。
44.图6为实施例2中碱化剂浓度为30g/l(pac-a)以及10g/l(pac-b)条件下制备所得pac的傅立叶红外光谱(ftir)对比图。
45.图7为实施例2中采用资源化制得的pac与某化工有限公司生产的商用pac (pac-c)针对某造纸厂造纸废水的混凝效果对比图。
46.图8为实施例3中采用资源化制得的pas与某化工有限公司生产的商用pas (pas-c)针对某城镇污水厂进水的混凝效果对比图。
47.图中标记说明:
48.1-预沉池,2-第一沉淀池,3-除镁除硫池,4-第二沉淀池,5-除氯反应池,6
‑ꢀ
除氯沉淀池,7-第三沉淀池,8-第一酸浸池,9-第一中和池,10-除钙池,11-第四沉淀池,12-第二酸浸池,13-第五沉淀池,14-第二中和池,15-氧化钙加药器,16
‑ꢀ
除镁除硫剂加药器,17-除氯剂加药器,18-絮凝剂加药器,19-酸浸液加药器,20
‑ꢀ
碱化剂加药器,21-除钙剂加药器,22-进水泵。
具体实施方式
49.下面结合附图和具体实施例对本实用新型进行详细说明。本实施例以本实用新型技术方案为前提进行实施,给出了详细的实施方式和具体的操作过程,但本实用新型的保护范围不限于下述的实施例。
50.下面先对本实用新型的用高盐废水零排放系统污泥制备高分子铝盐混凝剂的装置进行详细说明。
51.参见图1所示,本实用新型的用高盐废水零排放系统污泥制备高分子铝盐混凝剂
的装置,包括沿高盐废水处理方向依次连接的预沉池、除镁除硫池、除氯反应池、除氯沉淀池和除氯沉淀物资源化模块。
52.在一些实施方式中,当资源化目标产物为pac时,所述除氯沉淀物资源化模块包括依次连接除氯沉淀池的沉淀物出口的第一酸浸池、第一中和池和除钙池;
53.当资源化目标产物为pas时,所述除氯沉淀物资源化模块包括依次连接除氯沉淀池的沉淀物出口的第二酸浸池和第二中和池。
54.更具体的,所述的除钙池后面还设有第四沉淀池,所述的第二酸浸池与第二中和池之间还设有第五沉淀池;所述的第一酸浸池和第二酸浸池还分别连接酸浸液加药器。更进一步的,所述的第一中和池和第二中和池还分别连接碱化剂加药器;所述的除钙池还连接有除钙剂加药器。
55.本实用新型装置中各部分的反应原理分别如下:
56.1)预沉池:高盐废水(脱硫废水)通过进水泵提升进入预沉池,控制氧化钙加药器将石灰浆液加入预沉池中,调节高盐废水ph值(去除部分重金属)并充当混凝剂促进脱硫废水中的悬浮物沉降,产生的污泥回流至烟气脱硫系统的石膏旋流器作为石膏回收;预沉池的石灰投加量可高于混凝需求量,将部分硫酸根转化为硫酸钙去除(见式(1)),但需要控制ph以防镁离子大量去除影响石膏品质。当高盐废水中的钙镁离子、悬浮物等浓度较低时,预沉池这一工序也可以省去。
57.so
42-+ca
2+
→
caso4↓ꢀꢀ
(1)
58.2)除镁除硫池:预沉池出水进入到除镁除硫池,通过投加除镁除硫剂(通常为石灰)去除脱硫废水中的镁离子与硫酸根,此时的ph值同样利于重金属离子沉淀。镁离子的去除可以避免出水回流脱硫塔造成泡沫问题,硫酸根的去除可以减少后续对氯离子去除的干扰。产生的污泥主要成分为硫酸钙和氢氧化镁,如镁盐含量较低同样可回流至旋流器;如镁盐含量较高则可作为含镁固废回收。反应见式(1)和(2)。
59.2oh-+mg
2+
→
mg(oh)2↓ꢀꢀ
(2)
60.3)除氯反应池:废液经过除镁除硫池处理后再自流入除氯反应池,通过投加含铝除氯剂,废液中的氯离子生成弗里德尔盐沉淀(反应见式(3)-(5)),经过絮凝池投加絮凝剂可加速污泥沉降。沉降分离后的污泥用输送泵送至压滤机脱水。除弗里德尔盐沉淀外,还有少量的钙矾石沉淀生成,反应式见(6)-(8)。
61.alo
2-+2h2o
→
al(oh)
4-ꢀꢀꢀꢀꢀꢀꢀꢀꢀꢀꢀꢀꢀꢀꢀꢀꢀꢀꢀꢀꢀꢀꢀꢀꢀꢀ
(3)
62.4ca(oh)2+2al(oh)
4-→
ca4al2(oh)
14
↓
+2oh-ꢀꢀꢀꢀꢀꢀꢀꢀ
(4)
63.ca4al2(oh)
14
↓
+2cl-→
ca4al2(oh)
12
cl2↓
+2oh-ꢀꢀꢀꢀꢀ
(5)
64.alo
2-+2h2o+2oh-→
al(oh)
6-ꢀꢀꢀꢀꢀꢀꢀꢀꢀꢀꢀꢀꢀꢀꢀꢀꢀꢀꢀꢀꢀ
(6)
65.al(oh)
63-+3ca
2+
→
[ca3al(oh)6]
3+
ꢀꢀꢀꢀꢀꢀꢀꢀꢀꢀꢀꢀꢀꢀꢀꢀꢀꢀ
(7)
[0066]
2[ca3al(oh)6]
3+
+3so
42-→
ca6al2(oh)
12
(so4)3↓ꢀꢀꢀꢀꢀꢀꢀ
(8)
[0067]
除氯沉淀物资源化模块主要是将以弗里德尔盐为主要成分的除氯沉淀物转化为高分子铝盐混凝剂,若资源化目标产物为pac,则具体反应单元包括酸浸池、中和池和除钙池,各反应器的反应原理如下:
[0068]
第一酸浸池:除氯沉淀池产生的污泥经机械脱水后排入酸浸池,通过加入定量的盐酸作为酸浸液,污泥中的弗里德尔盐沉淀与少量的钙矾石沉淀在一定温度下几乎全部溶
解,反应式见(9)和(10)。
[0069]
ca4al2(oh)
12
cl2↓
+12h
+
→
2ca
2+
+4alb+2cl-+12h2o
ꢀꢀ
(9)
[0070]
ca6al2(oh)
12
(so4)3↓
+12h
+
→
3ca
2+
+2alb+3caso4↓
+12h2o
ꢀꢀꢀ
(10)第一中和池:酸浸池出水进入中和池,通过加入碱化剂与酸液进行中和反应(反应见式(11)),在一定温度下中和液中的氯化铝发生聚合反应生成pac,反应式见(12)和(13)。
[0071]
oh-+h
+
→
h2o
ꢀꢀꢀꢀꢀꢀꢀꢀꢀꢀꢀꢀꢀꢀꢀꢀꢀꢀꢀꢀꢀꢀꢀꢀꢀꢀꢀꢀꢀꢀꢀꢀꢀꢀꢀꢀ
(11)
[0072]
2alcl3+12h2o
→
al2(oh)ncl
6-n
+nhcl+(12-n)h2o
ꢀꢀꢀꢀꢀꢀꢀꢀꢀ
(12)
[0073]
mal2(oh)ncl
6-n
++mxh2o
→
[al2(oh)ncl
6-n
·
xho](1≤n≤5,m≤10,x《12)
ꢀꢀ
(13)
[0074]
除钙池:中和池出水进入除钙池,通过添加除钙剂去除pac中所含的钙离子,以此提高pac产品中的氧化铝含量,产生的除钙沉淀物回流至烟气脱硫系统的石膏旋流器作为石膏回收,反应式见(1)。
[0075]
若资源化目标产物为pas,则具体反应单元包括酸浸池和中和池,各反应器的反应原理如下:
[0076]
第二酸浸池:除氯沉淀池产生的污泥经机械脱水后排入酸浸池,通过加入定量的硫酸作为酸浸液,在一定温度下同步实现铝的提取以及钙的去除,产生的除钙沉淀物(反应式见(1))回流至烟气脱硫系统的石膏旋流器作为石膏回收,反应式见(14) 和(15)。
[0077]
ca4al2(oh)
12
cl2↓
+12h
+
+4so
42-→
2alb+4caso4↓
+2cl-+12h2o
ꢀꢀꢀꢀ
(14)
[0078]
ca6al2(oh)
12
(so4)3↓
+3so
42-+12h
+
→
2alb+6caso4↓
+12h2o
ꢀꢀꢀꢀꢀꢀ
(15)
[0079]
(2)第二中和池:沉降分离后的酸浸液进入中和池,通过加入碱化剂与酸液进行中和反应(反应见式(11)),在一定温度下中和液中的硫酸铝发生聚合反应生成 pas,反应式见(16)和(17)。
[0080]
al2(so4)3+12h2o
→
al2(oh)n(so4)
3-n/2
+n/2h2so4+(12-n)h2o
ꢀꢀ
(16)
[0081]
mal2(oh)n(so4)
3-n/2
+mxh2o
→
[al2(oh)n(so4)
3-n/2
·
xh2o](1≤n≤5,m≤10,x《12) (17)
[0082]
在一些实施方式中,请再参见图1所示,所述的预沉池与除镁除硫池之间还设有第一沉淀池,所述的除镁除硫池与除氯反应池之间还设有第二沉淀池,所述的除氯沉淀池与除氯沉淀物资源化模块之间还设有第三沉淀池。优选的,第一沉淀池、第二沉淀池、第三沉淀池的底部均设有污泥排口,并通过污泥输送泵外运或排放至后续处理流程中。
[0083]
在一些实施方式中,请再参见图1所示,所述的预沉池还连接装有石灰浆液的氧化钙加药器,所述的除镁除硫池还连接除镁除硫剂加药器,所述的除氯反应池还分别连接氧化钙加药器和除氯剂加药器,所述的除氯沉淀池还连接絮凝剂加药器。
[0084]
下面继续对利用高盐废水零排放系统污泥制备高分子铝盐混凝剂的方法进行详细说明。
[0085]
在一些实施方式中,基于上述装置,还提出了一种利用高盐废水零排放系统污泥制备高分子铝盐混凝剂的方法,其工艺流程如图1所示,包括以下步骤:
[0086]
(1)待处理高盐废水送入预沉池中,加入石灰浆液,沉淀处理,所得出水再送入到除镁除硫池中,所得沉淀物外运回用;
[0087]
(2)往除镁除硫池中加入除镁除硫剂,进行除镁除硫处理,处理完成后的泥水混合液再经沉降分离后,所得沉淀外运,所得出水流入除氯反应池;
[0088]
(3)往除氯反应池中加入石灰浆液与除氯剂,使得含有的氯离子生成复合物沉淀,再投加絮凝剂,沉降处理,所得出水排出,所得沉淀物送入除氯沉淀物资源化模块中进行除氯沉淀物资源化处理;
[0089]
(4)当资源化目标产物为pac时,步骤(3)所得沉淀物经脱水后,先送至第一酸浸池,加入酸浸液处理,随后排入第一中和池中,加入碱化剂调节ph,接着,送入除钙池中,在除钙剂作用下除去钙离子,最后,沉降分离后,得到黄色液体,即为液态pac产品;
[0090]
(5)当资源化目标产物为pas时,步骤(3)所得沉淀物经脱水后,先送至第二酸浸池,加入酸浸液处理,沉降分离后,所得酸液排入第二中和池中,加入碱化剂,得到黄色液体即为液态pas产品。
[0091]
更具体的,步骤(1)中,高盐废水在预沉池中的停留时间为0.5-12h,沉淀处理的时间为0.5-24h。
[0092]
更具体的,步骤(2)中,所述的除镁除硫剂为氧化钙、氢氧化钠、碳酸钠、铝酸钠或碳酸氢钠中的一种或多种,除镁除硫池中的水力停留时间为0.1-12h,泥水混合液沉降分离的时间为0.1-12h。
[0093]
更具体的,步骤(3)中,所述除氯剂为氧化铝、铝酸钠、氢氧化铝、硅酸铝或磷酸铝中的一种或多种,除氯反应池的水力停留时间为0.1-12h,除氯沉淀池的水力停留时间为0.1-14h。优选的,除氯沉淀池中所用的絮凝剂可以为阳离子、阴离子或非离子型聚丙烯酰胺(pam)、季铵型絮凝剂、聚胺型-低分子量有机絮凝剂中的一种或几种。
[0094]
更具体的,进一步的,步骤(4)中,第一酸浸池中加入的酸浸液为硝酸、醋酸或盐酸中的一种或几种的复合;步骤(5)中,第二酸浸池中加入的酸浸液为硫酸或草酸中的一种或两种的复合。优选的,酸浸池中的反应温度控制在30-90℃,所通入的酸浸液的浓度为50-650g/l。
[0095]
更具体的,步骤(5)中,所述的除钙剂为硫酸铝、硫酸、十二水硫酸铝钾、硫酸钾或硫酸镁中的一种或几种。优选的,除钙剂的浓度控制为5-100g/l。
[0096]
更具体的,步骤(4)和步骤(5)中,所述的碱化剂为氧化钙、氢氧化钠、碳酸钠、碳酸氢钠或氨水中的一种或多种。优选的,两个中和池中的温度也应控制在 30-100℃,碱化剂的浓度满足为5-80g/l,投加碱化剂后的搅拌溶解时间为0.1-10h。
[0097]
以上实施方式可以任一单独实施,也可以任意两两组合或更多的组合实施。
[0098]
下面结合具体实施例对上述实施方式进行更详细的说明。
[0099]
实施例1:
[0100]
一种高盐废水零排放回收固废制备铝盐混凝剂的工艺,其工艺流程如附图1 所示,包括高盐废水零排放工艺模块和固废回收制备铝盐混凝剂工艺模块。
[0101]
高盐废水零排放工艺模块包括依次连接的高盐废水进水泵22、预沉池1、第一沉淀池2、除镁除硫池3、第二沉淀池4、除氯反应池5、除氯沉淀池6、第三沉淀池7。预沉池1还与氧化钙加药器15连接,除镁除硫池3还与除镁除硫剂加药器16连接,除氯反应池还与氧化钙加药器15和除氯剂加药器17连接,除氯沉淀池6 还与絮凝剂加药器18连接。
[0102]
若资源化目标产物为pac,则所述的回收固废制备铝盐混凝剂工艺模块包括依次连接第三沉淀池7的第一酸浸池8、第一中和池9、除钙池10、第四沉淀池11。第一酸浸池8还与酸浸液加药器19连接,第一中和池9还与碱化剂加药器20连接,除钙池10还与除钙剂加药
器21连接。
[0103]
若资源化目标产物为pas,则所述的回收固废制备铝盐混凝剂工艺模块包括依次连接第三沉淀池7的第二酸浸池12、第五沉淀池13、第二中和池14。第二酸浸池12还与酸浸液加药器19连接,第二中和池14还与碱化剂加药器20连接。
[0104]
具体步骤如下:
[0105]
待处理的高盐废水由进水泵22进入预沉池1,通过氧化钙加药器15将石灰浆液投加入预沉池1中,调节脱硫废水ph值(去除部分重金属)并充当混凝剂促进脱硫废水中的悬浮物沉降。第一沉淀池2产生的污泥经污泥输送泵回用。
[0106]
第一沉淀池2出水进入到除镁除硫池3,通过除镁除硫剂加药器16投加除镁剂去除脱硫废水中的镁离子与硫酸根。镁离子的去除可以避免回水出现泡沫,硫酸根的去除可以减少后续对氯离子去除的干扰。第二沉淀池4产生的污泥主要成分为硫酸钙以及少部分氢氧化镁,经污泥输送泵直接回流。
[0107]
泥水混合液经第二沉淀池4沉降分离后,出水流入除氯反应池5,通过氧化钙加药器15投加石灰浆液,除氯剂加药器17投加除氯剂,废水中的氯离子生成复合物沉淀。经过除氯沉淀池6由絮凝剂加药器18投加絮凝剂可以使得污泥更好的沉降。第三沉淀池7出水可直接回用。
[0108]
若资源化目标产物为pac,则第三沉淀池7产生的污泥用污泥输送泵送至脱水机进行脱水,经由污泥输送泵送至第一酸浸池8,通过酸浸液加药器19加入酸浸液可将污泥几乎全部溶解。酸液随后排入第一中和池9,碱化剂加药器20投加碱化剂,液态pac经调节ph后排入除钙池10,通过除钙剂加药器21加入除钙剂,钙离子的去除可提高pac产品中的氧化铝质量分数。经第四沉淀池11沉降分离后,最终产生的黄色液体即为液态pac产品。
[0109]
若资源化目标产物为pas,则第三沉淀池7产生的污泥用污泥输送泵送至脱水机进行脱水,经由污泥输送泵送至第二酸浸池12,通过酸浸液加药器19加入酸浸液可同步实现铝的提取以及钙的去除。经第五沉淀池13沉降分离后,酸液随后排入第二中和池14,碱化剂加药器20投加碱化剂,最终产生的黄色液体即为液态 pas产品。
[0110]
实施例2
[0111]
针对某电厂烟气脱硫废水ca
2+
、mg
2+
、so
42-和cl-浓度分别为1500、1000、3000 和5000mg/l,处理后需达到ca
2+
《50mg/l,mg
2+
《20mg/l,so
42-《50mg/l, cl-《2500mg/l,除氯沉淀物生产制备的pac各项指标需满足水处理剂国家标准 gb/t22627-2014的要求。
[0112]
以实施例1中工艺为基础,构建了处理水量0.5m3/h的生产性实证工程,对某电厂实际烟气脱硫废水进行处理及生产性实证。该工艺运行分为三阶段,连续运行 16天,第一阶段是工程调试,第二阶段为处理脱硫废水原水(2~12d),第三阶段的处理对象则为该电厂脱硫废水四联箱出水(13~16d)。
[0113]
如图3和图4所示,预沉池1所用氧化钙浓度为1~3kg/m3,随着氧化钙的投加,脱硫废水中的悬浮物被高效去除,经第一沉淀池2沉降分离后,出水浊度约为90~120ntu,上清液进入除镁除硫池3。按照电力行业标准《火电厂石灰石-石膏湿法脱硫废水水质控制指标》(dl/t997-2006)规定,预沉池1出水重金属含量可稳定达到该标准(表1),因此该反应池出水进行深度除镁或者除氯形成的沉淀物重金属含量可维持很低水平,不会影响沉淀物资源化的产品质量。第一沉淀池2 产生的污泥脱水后进行x射线能谱分析(eds)(表2),结果表明
沉淀物性质与脱硫石膏类似。按照《固体废物浸出毒性浸出方法硫酸硝酸法》(hj/t299-2007) 进行重金属离子测定,结果显示仅锌和汞离子有检出,分别为0.015mg/l和 0.00019mg/l,其他重金属离子均未检出。因此,第一沉淀池2产生的污泥属于普通固废,可排入石膏脱水系统回用。
[0114]
表1生产性实证实验(0.5m3/h)进出水重金属含量分析
[0115]
指标初始值预沉池dl/t 997-2006cr(mg/l)未检出未检出≤1.5ni(mg/l)0.00190.0013≤1.0zn(mg/l)0.00220.001≤2.0hg(mg/l)0.001未检出≤0.05cd(mg/l)未检出未检出≤0.1as(mg/l)未检出未检出≤0.5
[0116]
表2第一沉淀池中沉淀物的eds元素含量数据表
[0117]
元素质量百分比(%)原子百分比(%)c15.3018.39o41.8227.11f3.983.67mg4.033.43al2.151.58s12.5416.64ca20.1829.18总量100.00100.00
[0118]
第一沉淀池2出水进入除镁除硫池3,所用除镁除硫剂为氧化钙,控制加药浓度为10~14kg/m3,经第二沉淀池4沉降分离后,上清液进入除氯反应池5。
[0119]
通过除镁除硫剂的投加,第二沉淀池4出水中镁离子含量为0.5~1.0mmol/l,实现了镁离子的高效去除,避免出水回用导致脱硫塔出现大量泡沫;硫酸根浓度为在11.6~14.2mmol/l,处于较低水平,可降低其对后续除氯过程的干扰;钙离子平均浓度由进水的18.6mmol/l大幅度提升至64.8mmol/l。由于预沉池1投加氧化钙后出水几乎不含重金属离子,因此第二沉淀池4产生的污泥也不属于危废,可随第一沉淀池2产生的污泥一同脱水并回用,或作为电厂固废处理。
[0120]
第二沉淀池4出水溢流进入除氯反应池5,所用除氯剂为氧化钙和偏铝酸钠,通过研究氧化钙与偏铝酸钠的配比对除氯效果以及类水滑石沉淀在pac制备工艺中铝的最大溶出量的影响,确定了氧化钙与偏铝酸钠投加量的最优配比(图2)。
[0121]
如图2所示,随着al/cl的增加,氯离子的去除率以及生成的沉淀物中氧化铝的质量分数均呈现出上升趋势,但当al/cl达到1.5后虽然沉淀物中氧化铝的质量分数仍然持续增加,氯离子的去除率却趋于平缓。结果表明,进一步提高al/cl对于溶液中残留的铝离子浓度没有显著影响。当ca/cl高于2.4时,氯离子的去除率上升趋于平缓且除氯沉淀物中氧化铝的质量分数快速下降,当ca/cl低于2.4时,溶液中残留的铝离子浓度过高,因此最佳al/cl和ca/cl分别为1.5和2.4。
[0122]
在保证氯离子去除率的前提下,提升资源化产物(pac)中铝的含量,氧化钙及除氯剂投加量分别为18~24kg/m3和16~20kg/m3。由于使用的废水为电厂每天的实际脱硫废水,水质波动较大(87.32~157.7mmol/l),导致出水氯离子的波动性较大,在调试阶段,氯离子去除率仅达到35%。通过调整氧化钙和除氯剂加药量 (即当污染物去除率处于较稳定水平时,生产性实证工程进入稳定运行阶段,其在图3(a)中体现的尤为明显),除氯反应池5氯离子去除率可达59.4~69.1%;ph可维持碱性,为12.4~12.8;钙离子和硫酸根离子浓度始终保持在1mmol/l以下,基本实现完全去除。
[0123]
除氯反应池5出水溢流进入除氯沉淀池6,所用絮凝剂为阴离子型聚丙烯酰胺 (pam),投加量为55~60g/m3。经第三沉淀池7沉降分离后,上清液可回用于脱硫塔。通过调整pam加药量,可以使得稳定运行阶段零排放工艺模块出水浊度降低至17.6~40ntu。通过对第三沉淀池7产生的类水滑石沉淀物(弗氏盐)进行x 射线荧光光谱(xrf)分析,得到各氧化物种类及质量分数(表3)。由表3可知,除氯沉淀物中氧化铝质量分数高达20.09%,且不含重金属离子,有利于后续资源化制备铝盐混凝剂。
[0124]
表3除氯沉淀物的xrf分析(以氧化物计)
[0125]
成分质量分数(%)成分质量分数(%)cao70.3213so32.0481al2o320.0872mgo0.7354cl4.3370sio20.1468na2o2.2188fe2o30.1054
[0126]
在本实例中,回收固废制备铝盐混凝剂工艺模块的资源化目标产物为pac。第三沉淀池7产生的除氯沉淀物经污泥脱水机脱水后,由污泥输送泵排入第一酸浸池8,控制温度为80~85℃,所用酸浸液为盐酸,控制浓度为220~230g/l。通过投加盐酸使污泥全部溶解,其中铝离子浸出率高达98%(图5)。酸液随后排入第一中和池9,控制温度为30~70℃,所用碱化剂为氧化钙,控制浓度为30~35g/l。通过投加氧化钙,可提高pac盐基度最高至81%。中和液随后排入除钙池10,所用除钙剂为硫酸,投加量为50~55g/l。通过加入硫酸去除pac中的钙离子,经第四沉淀池11沉降分离后,产生的硫酸钙污泥随第一沉淀池2产生的污泥一同回用,出水即为pac。最终固废资源化得到的液态pac产品各项指标与国家标准《水处理剂聚合氯化铝》(gb/t22627-2014)的对比见表4。
[0127]
图6为实施例2工艺条件下碱化剂浓度为30g/l(pac-a)以及10g/l(pac-b) 条件下制备所得pac的傅立叶红外光谱(ftir)对比图,两种pac均存在相似的吸收峰,但pac-a在649.94cm-1
处的吸收峰是al-oh的整体弯曲震动峰和水中
ꢀ‑
oh的吸收峰叠加造成的,而pac-b的红外图谱中并未出现此类吸收峰。因此,红外光谱分析表明,聚合氯化铝产物pac-a中有聚合态铝的存在,即pac-a样品为目标产物——pac。
[0128]
表4聚合氯化铝产品各项指标与gb/t22627-2014对比
[0129][0130][0131]
现有某造纸厂造纸废水,浊度为196ntu,色度为183,cod为104mg/l, uv254为0.939。如附图7所示,使用碱化剂浓度分别为30g/l和10g/l条件下制备所得的pac产品分别对某造纸厂造纸废水进行混凝实验,并将商用pac(天津市鼎盛鑫化工有限公司,pac)与二者的混凝效果做对比,其浊度与色度的去除效果接近商用pac,其cod与uv254的去除效果优于商用pac。在投加量为60mg/l 时(以铝计),经本工艺生产的pac产品处理后的造纸废水,色度和浊度去除率分别达到81%和98%,cod去除率为41.5%。
[0132]
通过处理水量0.5m3/h的生产性实证工程证明即使进水水质波动幅度较大,高盐废水零排放工艺模块依然可稳定运行并保持一定的去除率,适合应用于实际废水的处理,且本工艺对于脱硫废水的原水以及四联箱的出水均可以达到预期的效果。每m3脱硫废水产生的除氯沉淀物可制备100l性能优越的高盐基度pac。
[0133]
实施例3
[0134]
某垃圾焚烧发电厂ca
2+
、mg
2+
、so
42-、cl-浓度分别为2.4mg/l、0.48mg/l、 1717.9mg/l、5225.6mg/l的洗烟废水,处理后控制cl-低于2600mg/l,通过氯离子去除形成的复合盐沉淀物资源化过程生产制备的pas需满足国家标准《水处理剂聚硫酸铝》(hg/t5006-2016)。
[0135]
本实施例与实施例2大致相同,但由于洗烟废水悬浮物及钙、镁离子浓度较低,因此废水经高盐废水进水泵22直接排入除镁除硫池3。
[0136]
除镁除硫池3所用除硫剂为氧化钙,控制投加量为3~6kg/m3。出水经第二沉淀池4分离后,上清液进入除氯反应池5。对第二沉淀池4产生的污泥脱水后通过 xrf对沉淀物元素组成及质量分数进行分析(表5),结果表明,第二沉淀池沉淀物主要成份为硫酸钙,与脱硫石膏类似。按照《固体废物浸出毒性浸出方法硫酸硝酸法》(hj/t299-2007)进行重金属离子的测定,结果表明无重金属离子检出,因此第二沉淀池沉淀物可脱水后作为常规固废处置或石膏产品回用。
[0137]
表5第二沉淀池沉淀物xrf分析(以元素计)
[0138][0139][0140]
第二沉淀池4出水溢流进入除氯反应池5,所用除氯剂为偏铝酸钠,控制氧化钙及除氯剂投加量分别为16~18kg/m3和16~20kg/m3。通过氧化钙和除氯剂投加,除氯反应池5氯离子去除率可达54.3~60.8%,同时可基本实现钙、镁、硫酸根离子的完全去除。出水溢流进入除氯沉淀池6,所用絮凝剂为pam,投加量为 55~60g/m3。通过pam的投加,在第三沉淀池7实现泥水分离,出水可回用与脱硫塔。对第三沉淀池7产生的除氯沉淀物进行xrf分析(表6),结果表明,氧化铝质量分数高达21.48%,且不含重金属离子,有利于后续资源化制备铝盐混凝剂。
[0141]
在本实例中,回收固废制备铝盐混凝剂工艺模块的资源化目标产物为pas。第三沉淀池7产生的除氯沉淀物经污泥脱水机脱水后,由污泥输送泵排入第二酸浸池12,控制温度为85~90℃,所用酸浸液为硫酸,控制浓度为120~125g/l。通过投加硫酸同步实现铝的提取以及钙的去除,经第四沉淀池13沉降分离后,污泥主要成分为硫酸钙,可随第一沉淀池2污泥一同排入石膏脱水系统回用。酸液随后排入第二中和池14,控制温度为40~45℃,所用碱化剂为氢氧化钠,投加量为 25~30g/l。通过投加氢氧化钠,pas盐基度最高升至60.3%。最终固废资源化得到的液态pas产品各项指标与国家标准《水处理剂聚硫酸铝》(hg/t5006-2016)的对比见表7。
[0142]
表6除氯沉淀物xrf分析(以氧化物计)
[0143]
成分质量分数(%)成分质量分数(%)cao68.2485so32.0217al2o321.4823mgo0.4627cl4.2479sio20.1219na2o2.2491fe2o30.1123
[0144]
表7聚合硫酸铝产品各项指标与hg/t5006-2016对比
[0145]
[0146][0147]
图8为实施例3中采用资源化制得的pas与某化工有限公司生产的商用pas (pas-c)针对某城镇污水厂进水的混凝效果对比图,使用碱化剂浓度分别为30 g/l和10g/l条件下制备所得的pas产品分别对某造纸厂造纸废水进行混凝实验,并将商用pas(河南正远化工有限公司,pac)与二者的混凝效果做对比,其浊度的去除效果接近商用pas,其cod与uv
254
的去除效果优于商用pas,且对污水 ph的影响相对较弱。在投加量为60mg/l时(以铝计),经本工艺生产的pas产品处理后的某城镇污水厂进水,其色度、浊度去除率分别达到100%和92%,cod 去除率高达83%,已符合《城镇污水处理厂污染物排放标准》(gb18918-2002) 一级a排放标准。
[0148]
总的来说,本实用新型技术路线的应用不仅能够实现高盐废水的零排放,还能针对现有除氯沉淀物资源化利用途径匮乏的问题,将除氯形成的类水滑石沉淀物 (弗里德尔盐)作为原料制备污水或废水处理行业使用的混凝剂。其氧化铝质量分数、盐基度以及重金属含量等各项指标分别满足水处理剂国家标准 gb/t22627-2014和hg/t5006-2016的要求,能够有效去除污水与废水中cod、 uv254、浊度、色度等污染物指标,为实现固废资源化理念提供新思路。
[0149]
上述的对实施例的描述是为便于该技术领域的普通技术人员能理解和使用实用新型。熟悉本领域技术的人员显然可以容易地对这些实施例做出各种修改,并把在此说明的一般原理应用到其他实施例中而不必经过创造性的劳动。因此,本实用新型不限于上述实施例,本领域技术人员根据本实用新型的揭示,不脱离本实用新型范畴所做出的改进和修改都应该在本实用新型的保护范围之内。