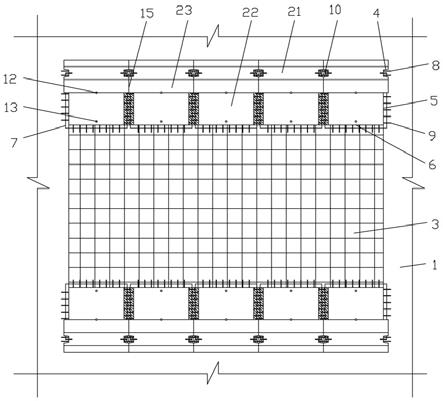
1.本发明涉及水利市政工程技术领域,尤其涉及一种先墙后底装配式渠槽结构及施工方法。
背景技术:
2.目前水利或市政工程的渠槽设计及施工大多数都是采用传统的现浇式施工,施工中存在着支模、拆模工序多难度大的缺点,渠槽侧墙由于是壁薄模板,模板的稳定较差,混凝土采用人工入仓困难较大,施工时需要大量人工,模板混凝土浇筑费用较高,且不宜保障质量。
3.上述传统人工现浇施工,存在施工速度慢、材料浪费大、质量难控制、施工现场管理难度大、施工工期长、这些都是现浇式渠槽施工的通病和缺点。
4.现有的渠槽装配式结构和施工方法采用了标准化设计、工厂化生产和装配化施工提高了质量、生产效率、缩短了施工周期。装配式渠槽采用预制和现浇混合装配式结构及施工方法,其中先墙后底法装配式渠槽首先在工厂预制钢筋混凝土“l”型侧墙,然后在已经浇筑好的混凝土垫层上进行预制“l”型侧墙的装配安装,组装成渠槽两侧的侧墙,最后在施工现场进行渠槽两侧侧墙间的现浇底板钢筋混凝土浇筑,形成完整的渠槽。
5.现有的装配式渠槽,以小型的一体化预制结构渠槽为主流,大中型整体预制结构的渠槽存在重量太大,运输、安装困难等缺点,其应用前景是较好的。但存在着预制渠槽构件品种繁多、结构复杂、装配难度大、拼装缝隙多、接缝止水效果差漏水严重、实用性差、耐久性差的问题,特别是止水结构不够合理导致拼装缝漏水严重,致使引发地基沉陷,垮塌进而引起预制渠槽发生严重变形,甚至歪斜垮塌,影响过水无法正常使用,减少了渠槽的使用寿命。
6.相邻两块构件没有联接结构或联接结构不合理、不可靠,整体性能差,在温度变化应力、地基沉降变形或其他外力作用影响下,会导致构件错位发生漏水渗水,止水缝起鼓开裂变形,拼接缝隙变化,进而影响整个渠槽的正常使用和使用寿命。
7.如授权公告号cn209412788u公开的一种装配式渠道止水连接结构,其方案在相邻的渠槽之间还设置有与止水槽相适配的止水条,相邻的渠槽之间设置有两个圆柱状砼销,单纯的止水条结构和砼销并不能有效保证渠槽间的止水效果以及渠槽间连接的牢固稳定。
8.同时在渠槽施工时,存在着装配式“l”型侧墙底板底部与混凝土垫层平面之间的缝隙座浆充填不实问题。“l”型侧墙构件在安装时极易出现座地不实现象,即使座底砂浆铺垫的很平整,也会因为吊装安装时侧墙构件不能一次就位,需要反复多次调整平面位置才能准确就位,所以多次反复对准就位发生碰撞砂浆就造成了座底砂浆流淌,致使砂浆表面不平,当构件对准位置座定后会出现构件歪斜,出现构件竖向不垂直、高程不准、或相邻构件错台较大的问题,致使构件安装精度降低,或出现“l”型侧墙底板的下平面与垫层之间出现较大缝隙构件底部座浆不实的缺陷,致使渠槽存在质量缺陷,影响渠槽的使用寿命。
9.因此,如何提供一种结构简单,生产安装方便,能够可靠有效传递左右相邻两块预
制渠槽的内力的结构,可保证预制渠槽拼装缝止水结构有效止水,彻底解决预制渠槽拼装缝的防漏防渗问题,如何控制好座底砂浆流淌,减少砂浆表面不平,如何提高构件安装精度,如何控制好侧墙底板与垫层之间出现缝隙,如何克服构件底部座浆不实的缺陷,如何提高渠槽安装质量,提高渠槽的使用寿命是目前急需解决的问题,已成为预制渠槽需进一步完善优化的技术问题。
技术实现要素:
10.本发明为了解决装配式渠槽整体性能差、止水效果不佳、构件座底不实的问题,提供一种先墙后底装配式渠槽结构及施工方法,解决现有的装配式“l”型侧墙构件没有止水或止水结构不够合理、止水效果差漏水严重的问题,解决构件之间没有联接结构或联接结构不合理、不可靠整体性能差的问题,解决构件座底不实的问题。
11.为实现上述目的,本发明所采用的技术方案是:一种先墙后底装配式渠槽结构,包括基础垫层、对称布设在基础垫层两侧的“l”型侧墙构件以及浇筑在两侧侧墙构件之间的现浇底板,每侧的所述侧墙构件为并排布设的多块,每块侧墙构件包括竖直布设的长边直墙、水平布设的短边底板以及腋角;所述长边直墙两侧均竖向开设有“[”形止水凹槽,所述短边底板两侧均水平开设有矩形止水沟槽,所述短边底板一侧面为纵向端面,所述纵向端面为短边底板与现浇底板的接合面;所述止水凹槽、止水沟槽和所述纵向端面内均预埋有止水带,所述止水凹槽内预埋有止裂钢筋,止水沟槽和所述纵向端面内预埋有结构钢筋;所述止水带、止裂钢筋和结构钢筋均向外突出于侧墙构件;相邻两个侧墙构件的所述止水凹槽和止水沟槽连通、且之间浇筑有混凝土以形成“l”形止水柱;所述短边底板底面开设有网格状灌浆凹槽,所述短边底板上分别竖向开设有注浆孔和出浆孔以连通灌浆凹槽,灌浆凹槽内填充有水泥砂浆;所述基础垫层上预埋有矩形支撑架,所述侧墙构件布设在支撑架上以定位。
12.进一步地,所述长边直墙和短边底板预制浇筑呈“l”形,长边直墙和短边底板之间布设所述腋角;所述长边直墙内侧壁为竖直面、外侧壁向下倾斜为斜面。
13.进一步地,所述止水凹槽两侧向外倾斜扩张以形成等腰梯形状,止水凹槽竖向贯穿所述长边直墙,止水凹槽内的止水带两侧对称布设所述止裂钢筋,每侧止裂钢筋为竖向排布的多个,相邻两个侧墙构件之间的止裂钢筋上下错位排布。
14.进一步地,所述短边底板两侧向内收缩以形成所述止水沟槽,止水沟槽水平布设、且与止水凹槽呈“l”形连通,止水沟槽和止水凹槽内的止水带相交呈“l”形;所述止水沟槽的止水带两侧布设有所述结构钢筋,每侧结构钢筋为横向排布的多个,相邻两个侧墙构件之间的结构钢筋左右错位排布。
15.进一步地,所述纵向端面上的止水带与侧墙构件两侧的“l”形止水带相交,纵向端面上的结构钢筋分布在止水带的上下两侧,纵向端面上的止水带和结构钢筋均伸入所述现浇底板内浇筑成型;所述止水柱包裹所述止水带、止裂钢筋与结构钢筋。
16.进一步地,所述注浆孔和出浆孔均贯穿所述短边底板,注浆孔与灌浆凹槽中部连通,出浆孔与灌浆凹槽边缘连通;所述支撑架包括矩形架体以及布设在架体四周侧的锚筋,
所述短边底板布设在所述架体上。
17.基于上述一种先墙后底装配式渠槽结构的一种先墙后底装配式渠槽施工方法,包括以下步骤:步骤1:首先进行一仓底板长度10m即5块侧墙构件长度单元的基础垫层的测量放线,再进行每一块侧墙构件长度单元的一个支撑架单元位置的测量放线,并标示出支撑架平面位置及高程、同时做出标记;步骤2:摊铺浇筑基础垫层,浇筑前架立支撑架,首先根据标记位置预埋锚筋,而后锚筋上焊接架体;步骤3:工厂预制侧墙构件,将止水带、止裂钢筋和结构钢筋按照设计标准预埋在侧墙构件内;步骤4:在基础垫层上标注每一块侧墙构件的位置以及高程;预制好的侧墙构件依次稳定吊装至基础垫层上,短边底板直接接触基础垫层或坐落在支撑架上,保证安装精度在设计范围内;步骤5:每块侧墙构件安装到位后、立即用测量仪器校核侧墙构件的平面位置和短边底板的水平度或长边直墙的垂直度及高程都应在允许误差范围内,同时检查安装位置及拼装缝隙;步骤6:5块预制“l”型侧墙构件为一仓,根据步骤1-5,完成安装5-10仓侧墙构件后,开展每块短边底板与基础垫层之间的灌浆作业,灌浆前先对短边底板四周边缘进行填缝,而后通过灌浆机连通注浆孔向短边底板与基础垫层之间、灌浆凹槽内灌入水泥砂浆直至浆液从出浆孔溢出;步骤7:灌浆完成后,将侧墙构件之间的拼装缝采用硅酮结构密封胶塞缝补牢;开展大面积现浇底板的浇筑作业,同时对相邻侧墙构件间的止水凹槽和止水沟槽进行二期混凝土的浇筑以形成止水柱;待浇筑止水沟槽内二期混凝土浇筑完成,再把大面积现浇底板的常态混凝土与止水沟槽内的二期混凝土相连接合起来混合浇筑,形成一个底板整体,最后浇筑止水凹槽内的二期混凝土;步骤8:灌浆作业、现浇底板和止水柱浇筑完成5-10仓底板长度的装配式渠槽的施工后,根据步骤1-7再进行下个5-10仓底板长度的渠槽新的施工循环。
18.进一步地,基础垫层存在不水平或高程较低引起短边底板与基础垫层出现缝隙,应在缝隙间加垫钢垫片垫起构件,使侧墙构件处于水平;灌浆采用纯水泥浆或采用细沙水泥浆,纯水泥浆灌浆的水:水泥的水灰比为1:1.5-2.5,细沙水泥浆灌浆的水泥:细沙:水的配合比为1:1:0.5。
19.进一步地,灌浆采用低压力灌浆法以防止灌浆抬动侧墙引起侧墙构件位移,灌浆压力控制在0.1-0.2mp以内。
20.进一步地,止水沟槽内二期混凝土的浇筑采用微型混凝土输送泵或砂浆灌浆机浇筑,混凝土输送导管沿止水沟槽往内伸至止水凹槽底部、由下往上由内向外逐层逐段浇筑;止水凹槽内的二期混凝土的浇筑采用微型混凝土输送泵或吊罐法浇筑,浇筑时采用两根混凝土输送导管布置在止水带左右两侧、输送塌落度较低的一级配混凝土或自密实混凝土、从下至上浇筑。
21.通过上述技术方案,本发明的有益效果是:本发明结构设计合理,止水柱浇筑在凹槽空腔和沟槽空腔内,止水柱包裹止水带,同时止水柱与止水带充分连接形成一个整体,止住了预制侧墙构件凹槽空腔、沟槽空腔内端面的缝隙,起到止水防渗的作用。
22.本发明的止水柱、止裂钢筋和结构钢筋浇筑一体成型,联接起了左右相邻侧墙构件并牢固连接,通过止水柱、止裂钢筋和结构钢筋的结合相邻构件形成一个整体,大大的增强了渠槽结构的整体性和相邻侧墙构件的抗变形能力,确保了预制渠槽的抗渗抗漏能力。
23.本发明的止水柱、止裂钢筋和结构钢筋相互配合,增加了止水柱强度,同时止水柱镶嵌在相邻构件内,起到栓塞的作用,能防止相邻侧墙构件左右错动变形,起到稳固结构的作用。
24.本发明纵向端面的止水带被浇筑在大面积现浇底板混凝土内,和新浇混凝土形成一个整体共同形成一个止水,起到了止水防水的作用。大面积现浇底板混凝土与纵向端面位置的结构钢筋结合形成一个整体,大大的增强了“l”型装配式渠槽结构与底板的整体性和“l”型装配式渠槽结构与底板的抗变形能力,确保了预制渠槽的抗渗抗漏能力。
25.本发明通过灌水泥浆充填短边底板与基础垫层之间的缝隙,使短边底板与基础垫层之间的缝隙充填座浆饱满,克服侧墙构件底部座浆不实的缺陷,由于是采用了后注砂浆保证了座浆饱满,克服了铺底砂浆流淌的问题,使侧墙构件安装便捷,提高了安装精度,提高了渠槽安装质量,进而提高了渠槽的使用寿命。
26.本发明的灌浆凹槽结构加上在基础垫层中预埋支撑架或在基础垫层上直接放置侧墙构件,实现了侧墙构件与基础垫层之间的干硬性连接,避免了提前摊铺的砂浆与侧墙构件碰撞而发生座底砂浆流淌,致使砂浆表面不平的弊端,很好的解决了构件歪斜,构件竖向不垂直、高程不准、或相邻构件错台较大的问题和缺陷。
附图说明
27.图1是本发明一种先墙后底装配式渠槽结构的整体主视图。
28.图2是本发明一种先墙后底装配式渠槽结构的整体俯视图。
29.图3是本发明一种先墙后底装配式渠槽结构的侧墙构件示意图。
30.图4是本发明一种先墙后底装配式渠槽结构的相邻侧墙构件拼装示意图之一。
31.图5是本发明一种先墙后底装配式渠槽结构的相邻侧墙构件拼装示意图之二。
32.图6是本发明一种先墙后底装配式渠槽结构的止水柱示意图。
33.图7是本发明一种先墙后底装配式渠槽结构的灌浆凹槽示意图。
34.图8是本发明一种先墙后底装配式渠槽结构的侧墙构件俯视图。
35.图9是本发明一种先墙后底装配式渠槽结构的支撑架示意图。
36.图10是本发明一种先墙后底装配式渠槽结构的架体布设示意图。
37.附图中标号为:1为基础垫层,2为侧墙构件,21为长边直墙,22为短边底板,23为腋角,3为现浇底板,4为止水凹槽,5为止水沟槽,6为纵向端面,7为止水带,8为止裂钢筋,9为结构钢筋,10为止水柱,11为灌浆凹槽,12为注浆孔,13为出浆孔,141为架体,142为锚筋,143为斜撑杆,15为拼装缝。
具体实施方式
38.下面结合附图对本发明的具体实施方式做详细描述:如图1~图10所示,一种先墙后底装配式渠槽结构,包括基础垫层1、对称布设在基础垫层1两侧的“l”型侧墙构件2以及浇筑在两侧侧墙构件2之间的现浇底板3,每侧的所述侧墙构件2为并排布设的多块,多块侧墙构件2首尾相连形成渠槽的两边侧墙。
39.本装配式渠槽结构为预制和现浇混合式结构。侧墙构件2为预制件,在工厂预制侧墙构件2,施工现场现浇筑基础垫层1,现场安装侧墙构件2、在现场安装一段后,再在施工现场浇筑现浇底板3部分和预制的“l”型侧墙构件2一同构成渠槽整体,构成一整套的先墙后底装配式渠槽的部件结构制作及安装。装配式渠槽截面为矩形,总宽9.0m,高4.7m。
40.本实施例中,每块侧墙构件2包括竖直布设的长边直墙21、水平布设的短边底板22以及腋角23。所述长边直墙21和短边底板22预制浇筑呈“l”形、共同组成“l
”ꢀ
形预制侧墙构件2整体,长边直墙21和短边底板22之间布设所述腋角23。
41.所述长边直墙21内侧壁为竖直面、外侧壁向下倾斜为斜面,进而其上顶和下底不同厚度;长边直墙21高4.7m,宽2.0m,顶厚0.4m,底厚0.6m。
42.所述短边底板22作为装配式渠槽底板的一部分,其长2.0m,宽1.7m,厚0.6m,短边底板22只占渠槽整个底板宽度的一部分。由于短边底板22面积较大可以减少侧墙构件2对地面的压强并使侧墙构件2站立稳定,起到稳定构件的作用,适应中大型装配式渠槽。
43.所述长边直墙21两侧均竖向开设有“[”形止水凹槽4。具体的,所述止水凹槽4两侧向外倾斜扩张以形成等腰梯形状,止水凹槽4竖向贯穿所述长边直墙21,其长度从长边直墙21顶部竖向延伸至底部。止水凹槽4开口宽度240mm,底宽200mm,凹槽深度150mm,相邻两块侧墙构件2的止水凹槽4构成“[]”型凹槽空腔。
44.所述短边底板22两侧均水平开设有矩形止水沟槽5。具体的,所述短边底板22两侧向内收缩150mm、与止水凹槽4底边齐平以形成所述止水沟槽5。止水沟槽5水平布设、且与止水凹槽4呈“l”形交汇连通,相邻两块侧墙构件2的止水沟槽5构成沟槽空腔。
45.所述短边底板22周侧包括三侧面,其中相对应的两侧面为止水沟槽5,剩余的一侧面为纵向端面6,所述纵向端面6为短边底板22与现浇底板3的接合面。
46.纵向端面6是平直状、直接与新浇大面积现浇底板3混凝土对接浇筑,纵向端面6作为预制的短边底板22和现场新浇的现浇底板3的大面积常态混凝土结合部,存在着现浇底板3新混凝土收缩至新老混凝土接合面出现收缩缝隙。
47.相邻侧墙构件2之间形成拼装缝15,上述的收缩缝和拼装缝15需要加装止水,才能达到不渗水不漏水的效果,从而确保渠槽的防水要求。
48.为了保证装配式渠槽的止水效果,所述止水凹槽4、止水沟槽5和所述纵向端面6内均预埋有止水带7,止水带7采用中埋直板式橡胶止水带,其型号为cb651-200mm*6mm型,止水带7宽200mm,厚6mm或8mm。
49.所述止水带7向外突出于侧墙构件2。止水带7在安装时,预制侧墙构件2时先将橡胶止水带7的1/2宽度的半边埋入构件内、作为橡胶止水带7的预埋部分,止水带7在预制侧墙构件2中的预埋宽度为止水带7宽度的一半,即100mm;止水带7另外1/2宽度的半边留在构件外边、作为橡胶止水带7的外露部分,外露部分与后期浇筑在止水沟槽5、止水凹槽4的二期混凝土结合,进而止水带7与侧墙构件2形成一个整体。
50.具体的,止水带7沿止水凹槽4、止水沟槽5和纵向端面6布置,止水沟槽5和止水凹槽4内的止水带7相交呈“l”形。止水带7首先沿止水凹槽4中间由长边直墙21顶部往下敷设至短边底板22的止水沟槽5接头处、折弯拐向短边底板22的止水沟槽5、沿止水沟槽5敷设至短边底板22的纵向端面6, 所述纵向端面6上的止水带7与侧墙构件2两侧的“l”形止水带7相交汇。
51.短边底板22纵向端面6预留的止水带7被浇筑在大面积现浇底板3混凝土内、此位置的止水带7和现浇底板3的混凝土形成一个整体、共同形成一个止水,起到了收缩缝的止水防水的作用。
52.相邻两个侧墙构件2的所述止水凹槽4和止水沟槽5连通、且之间浇筑有二期混凝土以形成“l”形止水柱10。即止水柱10填充在凹槽空腔和沟槽空腔内,凹槽空腔是止水凹槽4位置止水带7的存放空间和用于浇筑二期混凝土包裹外露部分止水带7的空间;沟槽空腔是止水沟槽5位置止水带7的存放空间和用于浇筑二期混凝土包括外露部分止水带7的空间。
53.在凹槽空腔和沟槽空腔内,拼装缝15左右两边侧墙构件2预留的半边止水带7均被新浇筑的二期混凝土包裹,与混凝土充分连接形成一个整体,被包裹的橡胶止水带7和二期混凝土共同形成一个混凝土止水柱10,止住了预制侧墙构件2凹槽空腔、沟槽空腔内端面的缝隙,起到拼装缝15止水防渗的作用。
54.为了提高止水柱10的强度,防止二期混凝土出现裂缝,所述止水凹槽4内预埋有止裂钢筋8,止水沟槽5和所述纵向端面6内预埋有结构钢筋9,所述止裂钢筋8和结构钢筋9均向外突出于侧墙构件2。
55.具体的,所述止水凹槽4内的止水带7左右两侧对称布设所述止裂钢筋8,每侧止裂钢筋8为竖向排布的多个,每侧的止裂钢筋8距离止水带7为50mm,止裂钢筋8间距为200mm。
56.止裂钢筋8预先埋入“l”型侧墙构件2内一部分、外露一部分,钢筋外露部分的长度为250mm,埋入侧墙构件2内的钢筋长度为600mm,采用直径φ12mm螺纹钢筋。相邻两个侧墙构件2之间的止裂钢筋8上下错位排布,防止侧墙构件2安装时钢筋相互干扰,竖向错位布置间距为50mm。
57.所述止水沟槽5的止水带7上下两侧布设有所述结构钢筋9,每侧结构钢筋9为横向排布的多个,每侧结构钢筋9距离止水带7为250mm,钢筋间距200mm。止水沟槽5内预留有外露的结构钢筋9,结构钢筋9在原施工图纸长度的基础上加长150mm,即外露部分的结构钢筋9长度为250mm。
58.相邻两个侧墙构件2之间的结构钢筋9左右错位排布,防止侧墙构件2安装时钢筋相互干扰,水平方向错位布置间距为50mm。
59.所述止水柱10包裹所述止水带7、止裂钢筋8与结构钢筋9。止水柱10镶嵌在相邻侧墙构件2的凹槽空腔和沟槽空腔内,起到栓塞作用,能防止相邻侧墙构件左右错动变形,起到稳固结构的作用。
60.同时止水柱10和止裂钢筋8、结构钢筋9的共同作用,联接起了左右相邻侧墙构件并牢固连接,通过二期混凝土与止裂钢筋8、结构钢筋9的结合使得相邻侧墙构件2形成一个整体,大大的增强了渠槽结构的整体性和相邻侧墙构件2的抗变形能力,确保了预制渠槽的抗渗抗漏能力。
61.止水柱10通常采用细石混凝土或自密实混凝土浇筑,细石粒径应为5-7mm,最大不能大于10mm。也可采用钢纤维或聚丙烯纤维混凝土浇筑,由于钢纤维或聚丙烯纤维混凝土的止裂性能强,因此无需设置止裂钢筋8,同时结构钢筋9无需加长,维持原来设计的外露长度100mm。
62.所述纵向端面6上的结构钢筋9分布在止水带7的上下两侧,纵向端面6上的止水带7和结构钢筋9均伸入所述现浇底板3内浇筑成型。纵向端面6上预留有外露的结构钢筋9,此位置的结构钢筋9外伸至现浇底板3的大面积混凝土内、与现浇底板3的钢筋进行牢固连接,可以和大面积混凝土牢固结合形成整体,大大增加了“l”型装配式渠槽结构与底板的抗变形能力,确保了预制渠槽的抗渗抗漏能力。
63.本实施例中,所述短边底板22底面开设有网格状灌浆凹槽11,所述短边底板22上分别竖向开设有注浆孔12和出浆孔13以连通灌浆凹槽11,灌浆凹槽11内填充有水泥砂浆。
64.所述注浆孔12和出浆孔13均贯穿所述短边底板22,注浆孔12与灌浆凹槽11中部连通,出浆孔13与灌浆凹槽11边缘连通。所述灌浆凹槽11截面为半圆形槽孔,其深度为30mm即半径r=30mm,灌浆凹槽11最外侧距离短边底板22边缘80mm。
65.注浆孔12是灌浆主通道,一端连接网络联通状的灌浆凹槽11的中央槽孔、另一端连接灌浆机的灌浆管。注浆孔12是在短边底板22中预留的一个通孔,长度为短边底板22的厚度为600mm,注浆孔12直径为40mm,布置在短边底板22的中心位置。
66.出浆孔13布置在短边底板22边缘处的网络联通状的灌浆凹槽11位置上,一端连接网络联通状的灌浆凹槽11的边槽孔、另一端为自由端与大气相联通。出浆孔13是在短边底板22中预留的一个通孔,长度为底板的厚度为600mm,出浆孔13直径为40mm。出浆孔13的作用是当短边底板22底部平面和基础垫层1的缝隙灌满水泥浆液后,浆液就从出浆孔13上口溢出,表明浆液已经灌满缝隙。
67.施工安装时“l”型侧墙构件2坐落在基础垫层1上,二者接合时若因基础垫层1表面不太平整,需要加钢垫片调整“l”型侧墙构件2短边底板22底部水平度和侧墙的垂直度以及侧墙构件2的高程。
68.为了避免上述状况、保证侧墙构件2安装的精准度,所述基础垫层1上预埋有矩形支撑架,所述侧墙构件2布设在支撑架上以定位。
69.支撑架就是在基础垫层1内预埋的钢质支撑框架,所述支撑架包括矩形架体141以及布设在架体141四周侧的锚筋142,所述短边底板22布设在所述架体141上。架体141采用40*40的国标三角钢制作,支撑架出露基础垫层1上表面部分的长度为0-10mm,不允许低于基础垫层1表面。
70.为防止支撑架变形,在架体141的四个内角焊接安装有斜撑杆143,斜撑杆143可以用同等规格的三角钢或直径φ22mm以上的钢筋制作,斜撑杆143长300mm。架体141边缘距离短边底板22边缘50mm,架体141长度为2000-150-150-50-50=1600mm,宽度为2000
ꢀ‑
50-50=1900mm。
71.支撑架起到支撑“l”型侧墙构件2底部的作用,同时还可以封闭短边底板22外缘四周的现浇底板3底部与基础垫层1之间的缝隙,起到灌浆缝隙的封闭作用。
72.支撑架相对应布置安装在“l”型侧墙构件2的平面位置和相对应的高程,预埋支撑架的下半部埋入基础垫层1中,上部出露部分根据“l”型侧墙构件2的高度确定支撑架的高
程和水平度,支撑架坐落在“l”型侧墙构件2的正下方。
73.施工安装时“l”型侧墙构件2的短边底板22底部向下坐落在预埋支撑架上,因支撑架事先在基础垫层1中预埋时就已经校正好水平位置和高程,所以可以将侧墙构件2直接坐落在预埋支撑架上。
74.本发明相邻侧墙构件2的止水带7、止水柱10浇筑形成一个整体,起到止水防渗作用;同时止水柱10、止裂钢筋8和结构钢筋9浇筑成型,增强侧墙构件2的抗变形能力,同时止水柱10镶嵌在相邻侧墙构件2内,塞紧了凹槽空腔和沟槽空腔,起到栓塞的作用,能防止相邻构件左右错动变形,起到稳固结构的作用。
75.一种先墙后底装配式渠槽施工方法,包括以下步骤:步骤1:首先进行一仓底板长度10m、即渠槽两侧各5块侧墙构件2长度单元的基础垫层1或支撑架的测量放线,再进行每一块侧墙构件2长度单元的一个支撑架单元位置的精确测量放线,标示出每一个预埋支撑架的四个边角的水平平面位置及高程。
76.在基础垫层1或预埋支撑架对应的四个角上插上短钢筋,做好高程标记,以方便高程控制。
77.步骤2:摊铺浇筑基础垫层1,浇筑时应控制好基础垫层1的高程和不平整度,特别注意基础垫层1不能高于设计标高,设计基础垫层1厚度一般为100-150mm。
78.基础垫层1为装配式渠槽底板钢筋混凝土下面的一个结构层,起到找平层和封闭层的作用,它由素混凝土制作铺装,起到支承侧墙构件2底部作用。
79.当采用基础垫层1中预埋支撑架时,在基础垫层1浇筑前架立支撑架:步骤如下,步骤21:首先根据放线后的标记位置预埋锚筋142,即钻孔插锚筋142,锚筋142直径大于φ18mm,总长度为250-300 mm,插入地下部分长度为160-220 mm,外露岩土地面长度为80-90mm,即低于基础垫层1表面10-20 mm,以方便焊接架体141;步骤22:而后锚筋142上焊接架体141,锚筋142安设为每个预埋支撑架对应的四个边角位置和支撑架的每根三角钢长度方向的1/2部位位置。支撑架安装焊接时需严格控制好平面位置尺寸和高程,支撑架上平面的平面位置尺寸允许误差为
±
5mm,高程允许误差为
±
3mm。
80.步骤3:工厂预制侧墙构件2,将止水带7、止裂钢筋8和结构钢筋9按照设计标准预埋在侧墙构件2内。橡胶止水带7安装应横平竖直,止水带7表面应干净清洁,不得有油渍污染,外伸长度应确保达到设计要求100mm。
81.步骤4:侧墙构件2拼装前在基础垫层1上标注每一块侧墙构件2的位置以及高程,给安装提供准确的位置尺寸,每块侧墙构件2的拼装缝15隙设计为14mm。
82.预制好的侧墙构件2依次稳定吊装至基础垫层1上,短边底板22直接接触基础垫层1或坐落在支撑架上,保证安装精度在设计范围内,步骤如下,步骤41:采用汽车吊吊运安装侧墙构件2,从最前面的一块开始吊运安装,依次首尾排列安装,吊运时吊车的钢丝绳卡扣在侧墙构件2的吊点上,工人应站在侧墙构件2的外侧用绳索拴住构件控制构件的转动方向,人员不允许站在构件的下面,确保安全;步骤42:等前面的一块安装就位、经过位置及拼装缝15检查合格后,用支撑杆进行固定牢固,防止倾倒歪斜,然后再进行下一块侧墙构件2的吊运安装。吊装时应轻吊轻放不能粗暴操作,应保护好预制侧墙构件2和橡胶止水带7及止裂钢筋8、结构钢筋9,防止碰撞损
伤。
83.吊运安装“l”型侧墙构件2时,应将侧墙构件2安放平稳,构件底部保持水平,四个边角的水平度误差不应超过10mm,以方便安装就位。吊运安装时应将侧墙构件2轻轻平稳吊运到待安装区域,并按允许误差范围控制水平平面位置、缓慢落地。
84.需要说明的是:1.当在基础垫层1上安装构件时,若基础垫层1不水平或高程较低的情况下,“l”型侧墙构件2短边底板22底面与基础垫层1出现缝隙,这时应在缝隙间加垫钢垫片垫起侧墙构件2,使侧墙构件2底部处于水平状态,或使侧墙处于垂直状态,同时应使构件符合设计高程。
85.2. 当在预埋支撑架上安装“l”型侧墙构件2时,因支撑架是预先控制好平面位置和高程的、都在允许误差范围内,吊运安装后一般不需要再加装钢垫片,只需把水平平面位置对准即可达到安装标准,但应进行高程和垂直度的校核。特殊的情况下出现支撑架顶面有较大的水平和高程误差时,也应在支撑架上面加装钢垫片加以修复调整,垫起“l”型侧墙构件2,使其达到设计要求。
86.步骤5:每块侧墙构件2安装到位后、立即用测量仪器校核侧墙构件2的平面位置和短边底板22的水平度或长边直墙21的垂直度及高程都应在允许误差范围内,同时和前一块侧墙构件2不能出现较大的错台,相邻的两块侧墙构件2板的错台误差应控制在10mm以内。
87.检查安装位置及拼装缝15隙,即拼装时应仔细检查侧墙构件2的安装位置和拼装缝15隙,力求精确到位,符合要求不能有大的偏差,否者返工重做。每块侧墙构件2的拼装缝15隙设计为14mm,安装位置最大偏差应控制在5mm以内,高程误差不大于5mm,拼装缝15最大偏差控制在3mm以内。
88.步骤6:5块预制“l”型侧墙构件2为一仓,根据步骤1-5,完成安装5-10仓侧墙构件2后,开展每块短边底板22与基础垫层1之间接缝面的灌浆作业,灌浆作业按灌浆规范执行,步骤如下,步骤61:灌浆前先对短边底板22四周边缘进行填缝封堵防止后期漏浆。
89.封堵采用细水泥砂浆进行填缝,封堵范围是以每块侧墙构件2为一个单元、每块“l”型侧墙构件2短边底板22的底平面与基础垫层1之间的四周缝隙,砂浆进入缝隙内封堵宽度应不小于50mm,要封堵严密确保灌浆是不漏浆。
90.步骤62:缝隙封堵完成后,经过三天水泥砂浆的强度增长后允许进行灌浆作业。
91.步骤63:灌浆作业以每块侧墙构件2为一个单元进行灌浆,可以采用对每块构件的单孔灌浆、也可以采用对相邻几块构件的多头灌浆。灌浆采用一般的灌浆机即可。
92.灌浆可采用纯水泥浆也可以采用细沙水泥浆,还可以采用灌浆效果最好的“一型支座灌浆料”、又称客运专线预制简支箱梁盆式橡胶支座专用支座灌浆料。
93.若采用纯水泥浆灌浆,纯水泥浆灌浆的水:水泥的水灰比为1:1.5-2.5;若采用细沙水泥浆灌浆,细沙水泥浆灌浆的水泥:细沙:水的配合比为1:1:0.5,为增加细沙水泥浆的流动性和防止细沙沉淀可添加0.3%的砂浆稳塑剂;若采用“一型支座灌浆料”灌浆,“一型支座灌浆料”的配合比为粉料:水=1:0.15。
94.步骤64:通过灌浆机的灌浆管连通注浆孔12向短边底板22与基础垫层1之间、灌浆凹槽11内灌入水泥砂浆直至浆液从出浆孔13溢出。
95.短边底板22的下平面预留网状联通的灌浆凹槽11结构,通过灌水泥浆或细沙水泥浆充填短边底板22与基础垫层1之间的缝隙,灌浆时浆液从灌浆凹槽11下面流淌不会堵塞
灌浆凹槽11,当缝隙灌满后最后才会灌满灌浆凹槽11,当灌浆凹槽11全部灌满后浆液才会从出浆孔13溢出。因短边底板22底面的灌浆凹槽11处于缝隙的最上部是最容易把缝隙灌浆灌满的。
96.缝隙灌满的标志为出浆孔13出浆并稳定一分钟以上时间,使浆液充分灌满缝隙和“l”型侧墙构件2短边底板22底部的灌浆凹槽11,标志此段灌浆结束。
97.需要说明的是:1. 灌浆采用低压力灌浆法,灌浆压力控制在0.1-0.2mp以内,防止灌浆压力过大抬动侧墙构件2引起侧墙构件2的位移。
98.2. 当装配式渠槽有坡度时灌浆应从低的一端向高的一端灌起,当渠槽坡度很小时可以将安装后的侧墙构件2分为若干段分别进行灌浆。
99.3.侧墙构件2与基础垫层1的缝隙一般只进行一次性灌浆,若灌浆料收缩率过大也可以进行二次补灌。
100.步骤7:灌浆作业完成后,等待3天后即可进行大面积现浇底板3混凝土的浇筑,浇筑前先将侧墙构件2之间的拼装缝15采用硅酮结构密封胶塞缝补牢,密封胶封堵入拼装缝15内10-20mm。
101.开展大面积现浇底板3的浇筑作业,同时对相邻侧墙构件2间的止水凹槽4和止水沟槽5进行二期混凝土的浇筑以形成止水柱10。
102.一般短边底板22所对应的沟槽空腔内二期混凝土应和大面积现浇底板3混凝土同时进行浇筑,但是沟槽空腔应先行一步浇筑,待沟槽空腔内二期混凝土浇筑完成,再把大面积现浇底板3的常态混凝土与沟槽空腔内的二期混凝土相连接合起来混合浇筑,形成一个底板整体,最后浇筑凹槽空腔内的二期混凝土,步骤如下,步骤71:相邻两块侧墙构件2的止水沟槽5拼接形成沟槽空腔,浇筑沟槽空腔内二期混凝土,采用微型混凝土输送泵或砂浆灌浆机来浇筑,浇筑时用人工手持混凝土输送导管沿止水沟槽5往内伸至长边直墙21底部、由下往上由内向外逐层逐段浇筑,往外慢慢拔导管,使二期混凝土浇筑饱满,应注意浇筑对橡胶止水带7的影响,保证止水带7的位置正确,保证止水带7上面和下面混凝土充填密实。
103.步骤72:相邻两块侧墙构件2的止水凹槽4拼接形成凹槽空腔,凹槽空腔内二期混凝土的浇筑采用从下至上的方法浇筑,浇筑时采用塌落度较低的一级配混凝土,也可以采用自密实混凝土浇筑。
104.浇筑时可以采用微型混凝土输送泵或吊罐法来浇筑,但是混凝土输送导管应有两根,即一机拖二管,两根导管分别布置在橡胶止水带7的左右两侧,同步浇筑,同步提升导管,确保混凝土均匀浇筑,确保橡胶止水带7位置正确不发生偏移。
105.沟槽空腔内二期混凝土浇筑完成后应尽快浇筑凹槽空腔内二期混凝土,时间应在3-6天以内浇筑,以保证新老混凝土的接触面更好结合。由于先浇筑沟槽空腔内的二期混凝土,随后及时浇筑凹槽空腔的二期混凝土,凹槽空腔内的二期混凝土有很大的重量压力至使能与沟槽空腔内的二期混凝土结合很好,形成一个整体,可以起到防渗防水的作用。
106.步骤8:灌浆作业、现浇底板3和止水柱10浇筑完成5-10仓底板长度、即50-100m装配式渠槽的施工后,根据步骤1-7再进行下个5-10仓底板长度的渠槽新的施工循环。
107.以上所述之实施例,只是本发明的较佳实施例而已,并非限制本发明的实施范围,故凡依本发明专利范围所述的构造、特征及原理所做的等效变化或修饰,均应包括于本发明申请专利范围内。