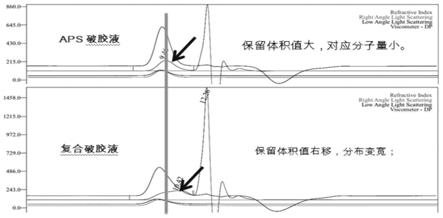
1.本发明涉及生物制剂技术领域,尤其涉及一种油水井解堵用的复合生物酶制剂及使用方法。
背景技术:
2.由于受地质、工程、排采因素的影响,管线及地层中存在细菌、聚合物及酸不溶物等堵塞,造成有些油气井产量低,产量递减快,水井达不到配注要求,使得油气井生产、水井注水达不到预期的效果,随着油田勘探开发的进程,钻完井、固井、压裂、注水等各种措施都会对油层造成伤害,低产低效井中约一半以上的井为井底附近污染堵塞造成的。
3.现有技术中解针此项问题,采用的常规解堵措施一般包括酸化法和氧化法。酸化法是利用盐酸、土酸、多氢酸、泡沫酸、稠化酸、乳化酸等酸化技术进行水井解堵,但传统的酸化法通常只能作用于近井地带,处理半径小,难以深入地层,低渗透及堵塞严重的层,酸液不能进入,并且酸化法使用的各种酸腐蚀性强,造成近井地带过度溶蚀,腐蚀生产套管等问题严重;而氧化法又存在着施工安全风险高、施工工艺复杂,氧气运输、存放危险性大,对设备腐蚀性强的问题。因此,需要提出一种油水井解堵用的复合生物酶制剂及使用方法。
技术实现要素:
4.本发明的目的是为了解决现有技术中存在的缺点,而提出的一种油水井解堵用的复合生物酶制剂及使用方法。
5.为了实现上述目的,本发明采用了如下技术方案:
6.一种油水井解堵用的复合生物酶制剂,包括a剂和b剂,所述a剂为复合生物酸,且所述a剂由a1有机酯混合物和a2生物酸主剂组成,所述a1有机酯混合物占比10%,所述a2生物酸主剂占比15%,其余为水;所述b剂为复合生物酶制剂,且所述b剂由生物酶和生物表面活性剂组成,所述生物酶占比5-15%,所述生物表面活性剂占比3-8%,其余为水。
7.优选地,所述a1有机酯混合物包括过酸叔丁酯、烯丙酯、过苯甲酸叔丁酯和过氧三氟乙酸叔丁酯。
8.优选地,所述a2生物酸主剂包括生物基丁二酸、盐酸、氢氟酸、土酸、多氢酸、泡沫酸、稠化酸和乳化酸。
9.优选地,所述生物酶包括甘露聚糖特异酶、淀粉特异酶、泥浆特异酶、纤维素酶、黄原胶裂解酶和脂肪酶。
10.优选地,所述生物表面活性剂为微生物在代谢过程中分泌出的具有表面活性的产物,包括糖脂、脂肽或中性类脂衍生物。
11.一种油水井解堵用的复合生物酶制剂的使用方法,其特征在于,包括以下步骤:
12.s1、预处理地层,将a剂复合生物酸用作前置液,预处理地层,a1有机酯混合物溶蚀碳酸盐,并与无机垢等堵塞物生成有机酸盐,解除无机垢造成的堵塞;
13.s2、隔离处理,预处理地层后视情况打一段隔离液;
14.s3、主处理地层,注入b剂复合生物酶制剂,将酸溶性物质处理为可溶性物质,溶蚀堵塞岩层的有机物质和聚合物残渣;
15.s4、顶替处理,主处理地层后视情况打入顶替液。
16.本发明具有以下有益效果:
17.本复合降解剂是一种复合生物酶降解剂,a1有机酯混合物可作为a2生物酸主剂的前体和引发剂,在油藏环境中在酶的催化作用下生成有机弱酸,有效溶蚀碳酸盐,并与无机垢等堵塞物生成有机酸盐具有高的溶解性,彻底解除无机垢造成的堵塞,而复合生物酶制剂通过调整产品复配成分及比例,可有效解除水井各种复杂堵塞难题,且所使用的生物表面活性剂间位阻大,有效抑制分散后的乳液再聚集,同时具有耐温、耐盐、作用快的优点。本复合降解剂的使用在与地层接触前,只生成低数量级的氢离子,随着缓释酸液接触地层、酸岩反应的进行,化学平衡被打破,继续生成氢离子,随着缓释酸液流向深部地层,地层得到深度酸化,解决了传统的酸化法通常只能作用于近井地带,处理半径小,难以深入地层的问题,同时施工难度要远小于氧化法的管道铺设施工,不存在施工安全风险高、施工工艺复杂,氧气运输、存放危险性大,对设备腐蚀性强的问题。
附图说明
18.图1为不同破胶液的凝胶色谱分析结果图;
19.图2为破胶液分子量分布结果图;
20.图3为填砂管生物酶解除残胶伤害实验表格图;
21.图4为填砂管生物酶解除残胶伤害结果数据分布图;
22.图5为aps破胶液岩心伤害试验结果图;
23.图6为复合破胶液岩心伤害试验结果图;
24.图7为破胶液岩心伤害实验结果对比图;
25.图8为gxx解堵后油压与日注量变化图。
具体实施方式
26.下面将结合本发明实施例中的附图,对本发明实施例中的技术方案进行清楚、完整地描述,显然,所描述的实施例仅仅是本发明一部分实施例,而不是全部的实施例。
27.一种油水井解堵用的复合生物酶制剂,其特征在于,包括a剂和b剂,所述a剂为复合生物酸,且所述a剂由a1有机酯混合物和a2生物酸主剂组成,所述a1有机酯混合物占比10%,所述a2生物酸主剂占比15%,其余为水;所述b剂为复合生物酶制剂,且所述b剂由生物酶和生物表面活性剂组成,所述生物酶占比5-15%,所述生物表面活性剂占比3-8%,其余为水。
28.所述a1有机酯混合物包括过酸叔丁酯、烯丙酯、过苯甲酸叔丁酯和过氧三氟乙酸叔丁酯。
29.所述a2生物酸主剂包括生物基丁二酸、盐酸、氢氟酸、土酸、多氢酸、泡沫酸、稠化酸和乳化酸。
30.所述生物酶包括甘露聚糖特异酶、淀粉特异酶、泥浆特异酶、纤维素酶、黄原胶裂解酶和脂肪酶。
31.所述生物表面活性剂为微生物在代谢过程中分泌出的具有表面活性的产物,包括糖脂、脂肽或中性类脂衍生物。
32.一种油水井解堵用的复合生物酶制剂的使用方法,其特征在于,包括以下步骤:
33.s1、预处理地层,将a剂复合生物酸用作前置液,预处理地层,a1有机酯混合物溶蚀碳酸盐,并与无机垢等堵塞物生成有机酸盐,解除无机垢造成的堵塞;
34.s2、隔离处理,预处理地层后视情况打一段隔离液;
35.s3、主处理地层,注入b剂复合生物酶制剂,将酸溶性物质处理为可溶性物质,溶蚀堵塞岩层的有机物质和聚合物残渣;
36.s4、顶替处理,主处理地层后视情况打入顶替液。
37.本发明中,在实际对降解剂进行使用时,为保证降解剂的使用效果,对其进行两步实施,首先采用室内试验,并对室内试验效果进行对比分析,在确定效果合格后再投入具体施工案例,并对施工案例进行对比分析。
38.室内试验包括以下步骤:
39.(1)对残胶的降解作用,配制0.5%hpg溶液1l,加入50ppm的aps,于90℃反应2h后,在离心机中6000rpm离心20min,收集沉淀物(未完全破胶胶团),并用滤纸擦干块状胶团表面水分,备用。
40.(2)对残胶降解率的影响,用刀片切割未破胶胶团,称取2-3g残胶,与生物酶解堵剂50ml(注入水配制;酶浓度为300ppm)一同加入反应釜中于120℃反应一定时间。待反应釜冷却后,将解堵液倒入离心管中,6000rpm离心30min。倾去上清液,取出沉淀物,并用滤纸吸干表面水分,称重,计算残胶降解率。
41.实验结果表明,在酶浓度为500ppm时,24h对残胶的降解率可达80%以上,并且随着浓度的增加,降解率也不断提高,但增加幅度逐渐平缓。而低于500ppm时降解率较低。因此,现场应用建议生物酶解堵体系中酶的浓度为500-1000ppm。
42.(3)破胶液分子量对比,凝胶色谱(gpc)可以用于高聚物的相对分子质量分析以及相对分子质量分布的测试。通过凝胶色谱分析破胶液中分子量分布情况,可以观察到酶对瓜胶的催化降解作用。
43.压裂液体系:0.4%hpg+0.1%杀菌剂+0.12%碳酸钠+0.05%温度稳定剂+1%kcl+0.1%调理剂+0.6%交联剂;破胶液制备:向压裂液体系中分别加入aps(80ppm)和复合破胶剂(30ppm酶+50ppm aps)95℃放置24h,备用。
44.不同破胶液的凝胶色谱分析结果如图1所示,gpc谱图中示差检测器信号(箭头所指)为浓度检测信号,从示差信号可以看出,aps破胶液的保留体积(横坐标)大于复合破胶液,说明aps破胶液分子量大于复合破胶液。从示差检测信号(浓度信号)强度值及进样浓度的差别上看,复合破胶液中高分子物质浓度也远小于aps破胶液。
45.破胶液分子量分布结果如图2所示,复合破胶液的数均分子量mn,重均分子量mw都远小于单独aps破胶液,是aps破胶液的10%,并且分子量分布mw/mn明显变宽,说明复合破胶过程伴随着瓜胶分子的降解、生成更多小分子物质。瓜胶分子量的大幅度降低,有助于减小瓜胶分子对地层的伤害作用。
46.(4)静态腐蚀速率,在常压、温度为90℃条件下,将已打磨、称重的试片分别放入恒温的加有解堵剂溶液中(根据每平方厘米试片表面积解堵剂溶液用量10ml),浸泡3h,取出
试片清洗,干燥处理后称量,计算平均腐蚀速率。
47.实验后解堵剂颜色基本不变,挂片表面无点蚀等明显腐蚀痕迹。生物酶解堵剂和优化剂腐蚀速率均较低,因此,该体系在施工过程中不会对管道、设备产生明显的腐蚀。
48.(5)动态腐蚀速率,将等体积的原油与解堵体系液在玻璃瓶中混合,摇匀,90℃水浴中放置2h后,取出冷却,在100目筛网上过滤,用柴油清洗筛上的残余物,如清洗后残留物是固体物质则为淤泥,如为液体物质则为乳状液。
49.将原油滴在玻璃上,加少量解堵体系液,在显微镜下进行观察,如果原油液滴周围形成了可见的牢固的膜,则说明原油有形成游泥的倾向。
50.实验结果说明,生物酶解堵体系与原油混合后无淤泥产生,原油液滴周围也没有见到牢固的膜,也没有乳状液生成。因此生物酶解堵体系与地层原油配伍性较好。
51.(6)解堵模拟,采用填砂管进行生物酶解堵模拟实验。考察加入破胶液前后以及解堵后的流速变化,考察生物酶对胶囊破胶液的降解情况。
52.实验方法为:
①
石英砂(20-40目)、硅胶(100-200目)1:1混合装入填砂管。测定孔隙体积;
②
制备冀东压裂体系胶囊破胶液和复合破胶液(酶+胶囊);
③
伤害过程:加2pv破胶液;
④
解堵处理:加0.5pv 30ppm酶液,对照加水;
⑤
试验结果计算,以水相流速变化率表示。
53.填砂管生物酶解除残胶伤害实验表格如图3所示,填砂管生物酶解除残胶伤害结果数据分布如图4所示,实验结果表明,破胶液堵塞后的流速比堵塞前的流速有大幅的降低,解堵后流速各有不同程度的恢复,其中加酶解堵后的流速恢复最好。生物酶解堵对氧化破胶液伤害有很好的解除堵塞效果,恢复率可达76.2%,远高于对照实验结果。
54.(7)岩心伤害试验,压裂液体系:0.4%hpg+0.1%杀菌剂+0.12%碳酸钠+0.05%温度稳定剂+1%kcl+0.1%调理剂+0.6%交联剂;破胶液制备:向压裂液体系中分别加入aps(100ppm,破胶液粘度4.5mpa
·
s)和复合破胶剂(30ppm酶+50ppm aps,破胶液粘度2.2mpa
·
s)95℃放置1天,1500rpm离心15min得上清液,清液用于岩心伤害试验。
55.aps破胶液岩心伤害试验结果、复合破胶液岩心伤害试验结果图以及破胶液岩心伤害实验结果对比分别如图5、图6和图7所示,实验结果表明,使用aps+酶复合破胶,破胶液对岩心的平均伤害比单独使用aps破胶小5%左右。
56.具体施工案例为冀东油田压裂转注井解堵现场试验,包括以下内容:
57.(1)井况,高xx为为高尚堡油田高深北区g5断块的一口注水井,按照高5断块东部区域ⅳ油组低渗储层整体压裂方案部署要求,已对该井83#、84#、86#、87b#、88#、89#层实施分段压裂。该井压裂后注水,注水4天后因注入压力过大停注。
58.(2)gxx井堵塞原因分析,高深某区断块es32+3ⅳ+
ⅴ
油组油藏为低孔低渗储层,根据《中国石油冀东油田公司注水水质管理规定》中《冀东油田水质控制指标》,该井水质要求a1级,实际注入为a2级,中途一度出现因水质问题停注现象,可能存在因水质出现的结垢等颗粒阻塞;另一方面,压裂施工结束后,约300m3压裂液残留地层未返排,瓜尔胶残胶等易生成滤饼阻塞地层,导致注水压力过高无法正常生产。
59.(3)gxx井解堵依据,考虑本井压裂措施后仍有大量压裂液未及时返排,瓜尔胶残胶可能对地层造成堵塞伤害,同时由于后期注水水质造成的地层结垢或粘土膨胀运移等造成的地层堵塞,本次施工采用生物酶复合解堵剂技术对gxx井进行解堵施工,达到降压增注的目的。
60.(4)施工方案,
61.液体名称配液量(m3)前置液优化剂(生物酸)100隔离液80生物酶解堵剂160顶替液80
62.(5)gxx井解堵施工结果,经生物酶解堵后,视吸水系数增大至2.2,地层吸水能力提高了6-7倍。注水压力、注入量至今保持稳定(统计期截止2017.5.4,注水累积112天增注3420方),水井降压增注效果显著。
63.(6)gxx解堵后油压与日注量变化如图8所示,在该区块应用复合生物酶解堵技术33井次,有效井次32次,有效率96.9%,其中油井12次,水井21次截止目前累计增油38625m3,水井累计增注64652m3,有效率和增油量得到显著升高。
64.以上所述,仅为本发明较佳的具体实施方式,但本发明的保护范围并不局限于此,任何熟悉本技术领域的技术人员在本发明揭露的技术范围内,根据本发明的技术方案及其发明构思加以等同替换或改变,都应涵盖在本发明的保护范围之内。