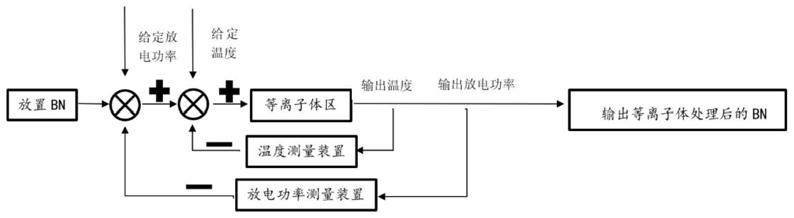
oh基团(羟基)的填料。
16.所述控制器对等离子体区的当前放电功率p和放电功率p进行比较,若p》p,则降低电源的输出电压,若p<p,则增加电源的输出电压。
17.在大气压低温等离子体对待处理填料进行处理过程中,温度测量装置监测等离子体区的温度t,并传输至控制器。所述控制器对等离子体区的温度t和处理温度t进行比较,若t》t,则利用冷却设备降低等离子体区的温度。
18.在大气压低温等离子体对待处理填料进行处理过程中,放电功率测量装置监测等离子体发生器的当前放电功率p,并传输至控制器。
19.基于低温等离子体的无机填料高通量羟基化方法所采用的装置,包括传送带、辊对辊装置、电源、等离子体发生器、控制器、温度测量装置和放电功率测量装置。
20.所述传送带用于盛放和传送无机填料粉末。
21.所述对辊装置带动传送带移动,令无机填料粉末移动到等离子体区域。
22.所述电源为等离子体发生器供电。
23.等离子体发生器在等离子体发生区产生大气压低温等离子体。所述大气压低温等离子体对位于等离子体区待处理填料进行处理,得到接枝-oh基团(羟基)的填料。
24.所述温度测量装置监测等离子体区的温度t,并传输至控制器。所述控制器对等离子体区的温度t和处理温度t进行比较,若t》t,则利用冷却设备降低等离子体区的温度。
25.所述放电功率测量装置监测等离子体发生器的当前放电功率p,并传输至控制器。
26.所述控制器对等离子体区的当前放电功率p和放电功率p进行比较,若p》p,则降低电源的输出电压,若p<p,则增加电源的输出电压。
27.所述控制器控制电源的放电电压。
28.本发明的技术效果是毋庸置疑的,本发明通过低温等离子体处理进行无机填料高通量羟基化,提供了一种无机填料功能化的新方法。该方法通过结合了辊对辊处理和直接通过空气激发的等离子体的装置来改善复合材料热传导能力,处理成本低,可在室温非真空下进行,同时还可以通入四氟化钛,氧气等其他气体以接枝不同的基团。
29.本发明方法操作简便,所需条件易于达成,经过等离子体高通量处理的无机填料质量好、接枝效果优越,整个过程不涉及溶剂,不产生有毒副产物,该装置可以方便地作为模块安装在工业装配线上。本专利将介质阻挡沿面放电低温等离子体和辊对辊处理装置结合,在露天条件下通过空气激发的低温等离子体实现了对无机填料的高通量功能化,进而改善了聚合物基复合材料的热导。这是一种通用的、环境友好的、可扩展的方法。
30.本发明的对驱动电源的要求低,103~109hz的脉冲或交流电源皆可。
31.本发明与工业流水线兼容性好:超小型样机每小时的无机填料处理量可达500g,装置可直接安装于工业流水线。
32.本发明可通用且环境友好,本发明可在固、液体材料上有效接枝羟基,且是一种通用的(不受固体形状影响)、环境友好的(不涉及有毒溶剂且未生成对环境有害的副产物)填料功能化方法。
33.本发明可扩展性强,本发明通过改变处理装置所处的气氛环境,可以方便地接枝更多种类基团。
34.本发明使等离子体处理能够适用于工业高通量生产,本专利中所使用的沿面放电
低温等离子体无需真空或稀有气体激发,宏观温度小于70℃且放电稳定、均匀,与聚合物工业生产线的兼容性较高,可用于高通量生产。
35.本发明有望代替适用范围小、污染严重的传统功能化方法,一般的化学功能化方法仅能接枝一种基团或仅能处理一种填料,本装置可方便地通过改变装置内气氛以接枝不同的功能基团,且可处理所有固体填料。如通入四氟化碳气体,可以在氧化铝填料上接枝氟基团,从而显著提高聚合物的热稳定性、耐化学腐蚀性和抗氧化性及绝缘性。如果将气氛改为氮气,则可接枝-no2,它可以改变钛酸钡的极性和反应活性从而改变其亲水性。或是通入氧气以接枝-o2,这种基团可以起到引发剂的作用,消耗自由基,阻碍聚合反应的发生。或通入氢气以达到原位还原、清洁的目的。此外,整个过程不涉及试剂且无有害、污染副产物产生。
附图说明
36.图1为方法示意图;
37.图2为装置示意图;
38.图3为沿面介质阻挡放电照片;
39.图4为处理前后氮化硼的fitr测试结果;
40.图5为处理前后聚合物基氮化硼复合材料的fitr测试结果;
41.图6为处理前后聚合物基氮化硼复合材料的导热系数;
42.图中:传送带1、等离子体发生器2、待处理填料3。
具体实施方式
43.下面结合实施例对本发明作进一步说明,但不应该理解为本发明上述主题范围仅限于下述实施例。在不脱离本发明上述技术思想的情况下,根据本领域普通技术知识和惯用手段,做出各种替换和变更,均应包括在本发明的保护范围内。
44.实施例1:
45.参见图1至图6,基于低温等离子体的无机填料高通量羟基化方法,包括以下步骤:
46.1)将待处理的氮化硼粉末3平铺在传送带1上。所述传送带1的材料包括聚酰亚胺。
47.所述氮化硼粉末3颗粒平均粒径为1μm~5μm。
48.2)利用辊对辊装置带动传送带1移动,使平铺的氮化硼粉末3经过等离子体区。
49.所述辊对辊装置包括用于带动聚酰亚胺传送带1移动的若干滚辊。
50.3)在处理温度t下,控制器向电源发送控制信号,令电源向位于聚酰亚胺传送带1上方的等离子体发生器2放电。
51.所述电源向等离子体发生器2传输交流电。
52.4)等离子体发生器2受电后,在等离子体区产生大气压低温等离子体,放电功率记为p。
53.所述等离子体区为等离子体发生器2与传送带1之间的区域。
54.所述等离子体发生器2沿空气表面介质阻挡放电。
55.5)当氮化硼粉末3移动到等离子体区内时,所述大气压低温等离子体对位于等离子体区氮化硼粉末3进行处理,得到接枝-oh基团(羟基)的氮化硼。
56.所述控制器对等离子体区的当前放电功率p和放电功率p进行比较,若p》p,则降低电源的输出电压,降低放电功率,若p<p,则增加电源的输出电压,增大放电功率。
57.在大气压低温等离子体对氮化硼粉末3进行处理过程中,温度测量装置监测等离子体区的温度t,并传输至控制器。所述控制器对等离子体区的温度t和处理温度t进行比较,若t》t,则利用冷却设备降低等离子体区的温度。
58.在大气压低温等离子体对氮化硼粉末3进行处理过程中,放电功率测量装置监测等离子体发生器2的当前放电功率p,并传输至控制器。
59.实施例2:
60.基于低温等离子体的无机填料高通量羟基化方法见实施例1,该方法所采用的装置包括聚酰亚胺传送带1、辊对辊装置、电源、等离子体发生器2、控制器、温度测量装置和放电功率测量装置。
61.所述传送带1用于盛放和传送氮化硼。
62.所述对辊装置氮化硼带动传送带1移动,令氮化硼移动到等离子体区域。
63.所述电源为等离子体发生器2供电。
64.等离子体发生器2在等离子体发生区产生大气压低温等离子体。所述大气压低温等离子体对位于等离子体区氮化硼粉末3进行处理,得到接枝-oh基团(羟基)的氮化硼。
65.所述温度测量装置监测等离子体区的温度t,并传输至控制器。所述控制器对等离子体区的温度t和处理温度t进行比较,若t》t,则利用冷却设备降低等离子体区的温度。
66.所述放电功率测量装置监测等离子体发生器的当前放电功率p,并传输至控制器。
67.所述控制器对等离子体区的当前放电功率p和放电功率p进行比较,若p》p,则降低电源的输出电压,若p<p,则增加电源的输出电压。
68.所述控制器控制电源的放电电压。
69.实施例3:
70.参见图1至图3,基于低温等离子体的无机填料高通量羟基化方法,包括以下步骤:
71.1)将待处理的氮化铝粉末3平铺在传送带1上。所述传送带1的材料包括聚酰亚胺。
72.所述氮化铝粉末3颗粒平均粒径为1μm~5μm。
73.2)利用辊对辊装置带动传送带1移动,使平铺的氮化铝粉末3移动到等离子体区。
74.所述辊对辊装置包括用于带动聚酰亚胺传送带1移动的若干滚辊。
75.3)在处理温度t下,控制器向电源发送控制信号,令电源向位于聚酰亚胺传送带1上方的等离子体发生器2放电。
76.所述电源向等离子体发生器2传输交流电。
77.4)等离子体发生器2受电后,在等离子体区产生大气压低温等离子体,放电功率记为p。
78.所述等离子体区为等离子体发生器2与传送带1之间的区域。
79.所述等离子体发生器2沿空气表面介质阻挡放电。
80.5)所述大气压低温等离子体对位于等离子体区氮化铝粉末3进行处理,得到接枝-oh基团(羟基)的氮化铝。
81.所述控制器对等离子体区的当前放电功率p和放电功率p进行比较,若p》p,则降低电源的输出电压,降低放电功率,若p<p,则增加电源的输出电压,增大放电功率。
82.在大气压低温等离子体对氮化铝粉末3进行处理过程中,温度测量装置监测等离子体区的温度t,并传输至控制器。所述控制器对等离子体区的温度t和处理温度t进行比较,若t》t,则利用冷却设备降低等离子体区的温度。
83.在大气压低温等离子体对氮化铝粉末3进行处理过程中,放电功率测量装置监测等离子体发生器2的当前放电功率p,并传输至控制器。
84.实施例4:
85.基于低温等离子体的无机填料高通量羟基化方法见实施例3,该方法所采用的装置包括聚酰亚胺传送带1、辊对辊装置、电源、等离子体发生器2、控制器、温度测量装置和放电功率测量装置。
86.所述传送带1用于盛放和传送氮化铝。
87.所述对辊装置氮化铝带动传送带1移动,令氮化硼移动到等离子体区域。
88.所述电源为等离子体发生器2供电。
89.等离子体发生器2在等离子体发生区产生大气压低温等离子体。所述大气压低温等离子体对位于等离子体区氮化铝粉末3进行处理,得到接枝-oh基团(羟基)的氮化铝。
90.所述温度测量装置监测等离子体区的温度t,并传输至控制器。所述控制器对等离子体区的温度t和处理温度t进行比较,若t》t,则利用冷却设备降低等离子体区的温度。
91.所述放电功率测量装置监测等离子体发生器的当前放电功率p,并传输至控制器。
92.所述控制器对等离子体区的当前放电功率p和放电功率p进行比较,若p》p,则降低电源的输出电压,若p<p,则增加电源的输出电压。
93.所述控制器控制电源的放电电压。
94.实施例5:
95.基于低温等离子体的无机填料高通量羟基化方法,包括以下步骤:
96.1)将待处理的氧化铝粉末3平铺在传送带上。
97.所述氧化铝粉末3颗粒平均粒径为1μm~5μm。
98.2)利用辊对辊装置带动传送带移动,使平铺的氧化铝粉末3移动到等离子体区。
99.所述辊对辊装置包括用于带动聚酰亚胺传送带移动的若干滚辊。
100.3)在处理温度t下,控制器向电源发送控制信号,令电源向位于聚酰亚胺传送带上方的等离子体发生器放电。
101.所述电源向等离子体发生器传输交流电。
102.4)等离子体发生器受电后,在等离子体区产生大气压低温等离子体,放电功率记为p。
103.所述等离子体区为等离子体发生器与传送带之间的区域。
104.所述等离子体发生器沿空气表面介质阻挡放电。
105.5)所述大气压低温等离子体对位于等离子体区氧化铝粉末3进行处理,得到接枝-oh基团(羟基)的氧化铝。
106.所述控制器对等离子体区的当前放电功率p和放电功率p进行比较,若p》p,则降低电源的输出电压,若p<p,则增加电源的输出电压。
107.在大气压低温等离子体对氧化铝粉末3进行处理过程中,温度测量装置监测等离子体区的温度t,并传输至控制器。所述控制器对等离子体区的温度t和处理温度t进行比
较,若t》t,则利用冷却设备降低等离子体区的温度。
108.在大气压低温等离子体对氧化铝粉末3进行处理过程中,放电功率测量装置监测等离子体发生器的当前放电功率p,并传输至控制器。
109.所述控制器对等离子体区的当前放电功率p和放电功率p进行比较,若p》p,则降低电源的输出电压,若p<p,则增加电源的输出电压。
110.所述控制器控制电源的放电电压。
111.实施例6:
112.基于低温等离子体的无机填料高通量羟基化方法见实施例5,该方法所采用的装置包括聚酰亚胺传送带1、辊对辊装置、电源、等离子体发生器2、控制器、温度测量装置和放电功率测量装置。
113.所述传送带1用于盛放和传送氧化铝。
114.所述对辊装置氧化铝带动传送带1移动,令氮化硼移动到等离子体区域。
115.所述电源为等离子体发生器2供电。
116.等离子体发生器2在等离子体发生区产生大气压低温等离子体。所述大气压低温等离子体对位于等离子体区氧化铝粉末3进行处理,得到接枝-oh基团(羟基)的氧化铝。
117.所述温度测量装置监测等离子体区的温度t,并传输至控制器。所述控制器对等离子体区的温度t和处理温度t进行比较,若t》t,则利用冷却设备降低等离子体区的温度。
118.所述放电功率测量装置监测等离子体发生器的当前放电功率p,并传输至控制器。
119.所述控制器对等离子体区的当前放电功率p和放电功率p进行比较,若p》p,则降低电源的输出电压,若p<p,则增加电源的输出电压。
120.所述控制器控制电源的放电电压。
121.实施例7:
122.基于低温等离子体的无机填料高通量羟基化方法,包括以下步骤:
123.1)将待处理的石墨烯粉末3平铺在传送带上。
124.所述石墨烯粉末3颗粒平均粒径为1μm~5μm。
125.2)利用辊对辊装置带动传送带移动,使平铺的石墨烯粉末3移动到等离子体区。
126.所述辊对辊装置包括用于带动聚酰亚胺传送带移动的若干滚辊。
127.3)在处理温度t下,控制器向电源发送控制信号,令电源向位于聚酰亚胺传送带上方的等离子体发生器放电。
128.所述电源向等离子体发生器传输交流电。
129.4)等离子体发生器受电后,在等离子体区产生大气压低温等离子体,放电功率记为p。
130.所述等离子体区为等离子体发生器与传送带之间的区域。
131.所述等离子体发生器沿空气表面介质阻挡放电。
132.5)所述大气压低温等离子体对位于等离子体区石墨烯粉末3进行处理,得到接枝-oh基团(羟基)的石墨烯。
133.所述控制器对等离子体区的当前放电功率p和放电功率p进行比较,若p》p,则降低电源的输出电压,若p<p,则增加电源的输出电压。
134.在大气压低温等离子体对石墨烯粉末3进行处理过程中,温度测量装置监测等离
子体区的温度t,并传输至控制器。所述控制器对等离子体区的温度t和处理温度t进行比较,若t》t,则利用冷却设备降低等离子体区的温度。
135.在大气压低温等离子体对石墨烯粉末3进行处理过程中,放电功率测量装置监测等离子体发生器的当前放电功率p,并传输至控制器。
136.所述控制器对等离子体区的当前放电功率p和放电功率p进行比较,若p》p,则降低电源的输出电压,若p<p,则增加电源的输出电压。
137.所述控制器控制电源的放电电压。
138.实施例8:
139.基于低温等离子体的无机填料高通量羟基化方法见实施例7,该方法所采用的装置包括聚酰亚胺传送带1、辊对辊装置、电源、等离子体发生器2、控制器、温度测量装置和放电功率测量装置。
140.所述传送带1用于盛放和传送石墨烯。
141.所述对辊装置石墨烯带动传送带1移动,令氮化硼移动到等离子体区域。
142.所述电源为等离子体发生器2供电。
143.等离子体发生器2在等离子体发生区产生大气压低温等离子体。所述大气压低温等离子体对位于等离子体区石墨烯粉末3进行处理,得到接枝-oh基团(羟基)的石墨烯。
144.所述温度测量装置监测等离子体区的温度t,并传输至控制器。所述控制器对等离子体区的温度t和处理温度t进行比较,若t》t,则利用冷却设备降低等离子体区的温度。
145.所述放电功率测量装置监测等离子体发生器的当前放电功率p,并传输至控制器。
146.所述控制器对等离子体区的当前放电功率p和放电功率p进行比较,若p》p,则降低电源的输出电压,若p<p,则增加电源的输出电压。
147.所述控制器控制电源的放电电压。
148.实施例9:
149.将经过5分钟本方法处理的氮化硼掺入环氧树脂,制备环氧树脂基氮化硼复合材料,实施例包含以下步骤:
150.1)取适量氮化硼纳米粉末平铺于聚酰亚胺输送带上,所选的氮化硼粉末3颗粒平均粒径为1μm~5μm,平铺厚度控制在30μm左右。
151.2)如图2,通过辊对辊装置将平铺的氮化硼粉末3移动到等离子体区,等待后续处理。
152.3)低温等离子体处理:如图1,设定温度为70摄氏度、施加交流电压放电功率为30w,利用交流电源驱动空气表面介质阻挡放电产生大气压低温等离子体。峰值电压约为5.9kv,频率约为14.5khz,处理时间约为5分钟。等离子体区输出温度和放电功率再经过温度测量装置和放电测量装置负反馈至电源,以调节至合适的温度和放电功率。
153.4)等离子体处理结果分析:收集等离子区处理完毕的氮化硼粉末3进行取样分析,使用傅里叶变换红外光谱仪识别本装置处理前后的氮化硼样品的表面基团。如图4所示,两个氮化硼样本都有一个大约3407cm-1的峰,这可能是由于拉伸振动的-oh(羟基)产生的,说明氮化硼粉末3已成功接枝-oh基团(羟基),即证明了低温等离子体高通量氮化硼接枝方法的有效实施。
154.5)环氧复合材料的制备:首先在环氧树脂中加入适量的乙醇,在80℃下搅拌溶解,
同时将处理后的和未处理的氮化硼粉末3分散到乙醇溶剂中,超声30分种。然后将氮化硼粉末3/乙醇溶液加入到已冷却的乙醇/环氧树脂溶液中,进行超声分散。然后将其整体置于60℃的油浴中,使得乙醇溶剂挥发干净。接着再将固化剂甲基六氢邻苯二甲酸酐加入混合液中,同时保持强烈的机械搅拌,再真空脱气直至混合液中无气泡。最后将混合液浇注到干净的模具中,先在80℃下预固化,然后再在135℃下固化,待固化完后待其冷却至室温后取出试样。
155.6)复合材料的导热系数测定:图5为环氧树脂、未处理的氮化硼/环氧树脂复合材料、处理后的氮化硼/环氧树脂复合材料的导热系数比较。结果表明,处理后的氮化硼/环氧树脂复合材料的导热系数(0.44w/(m
·
k))比同等氮化硼含量的未处理的氮化硼/环氧树脂复合材料(0.36w/(m
·
k))提高了22.1%。
156.实施例10:
157.将经过5分钟本方法处理的氮化铝掺入聚二偏氟乙烯,制备聚二偏氟乙烯基氮化铝复合材料,实施例包含以下步骤:
158.1)取适量氮化铝纳米粉末平铺于聚酰亚胺输送带上,所选的氮化铝粉末颗粒平均粒径为1μm~5μm,平铺厚度控制在30μm左右。
159.2)通过辊对辊装置将平铺的氮化铝粉末移动到等离子体区,等待后续处理。
160.3)低温等离子体处理:设定温度为90摄氏度、施加交流电压放电功率为40w,利用交流电源驱动空气表面介质阻挡放电产生大气压低温等离子体。峰值电压约为4.9kv,频率约为16.5khz,处理时间约为5分钟。等离子体区输出温度和放电功率再经过温度测量装置和放电测量装置负反馈至电源,以调节至合适的温度和放电功率。
161.4)等离子体处理结果分析:收集等离子区处理完毕的氮化铝粉末进行取样分析,使用傅里叶变换红外光谱仪识别本装置处理前后的氮化铝样品的表面基团。
162.5)聚二偏氟乙烯复合材料的制备:首先在聚二偏氟乙烯中加入适量的二甲基甲酰胺,在80℃下搅拌溶解,同时将处理后的和未处理的氮化铝粉末分散到二甲基甲酰胺溶剂中,超声30分种。然后将氮化铝粉末/二甲基甲酰胺溶液加入到已冷却的二甲基甲酰胺/聚二偏氟乙烯溶液中,进行超声分散。然后将其整体置于60℃的油浴中,使得乙醇溶剂挥发干净。接着再将固化剂甲基六氢邻苯二甲酸酐加入混合液中,同时保持强烈的机械搅拌,再真空脱气直至混合液中无气泡。最后将混合液浇注到干净的模具中,先在80℃下预固化,然后再在135℃下固化,待固化完后待其冷却至室温后取出试样。