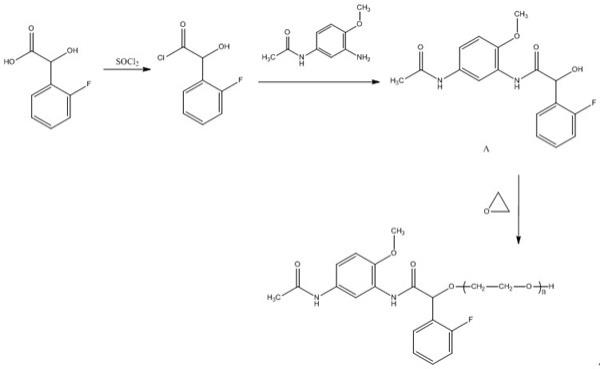
1.本发明涉及硅片刻蚀技术领域,特别是关于一种单晶硅片的碱刻蚀抛光方法。
背景技术:
2.在太阳能电池生产过程中,刻蚀抛光工艺是至关重要的一步。刻蚀抛光分为干法刻蚀和湿法刻蚀,其中湿法刻蚀是使用混合酸例如氢氟酸、硝酸和乙酸的酸性溶液进行酸刻蚀,或使用氢氧化钠或氢氧化钾等碱性溶液进行碱刻蚀。酸刻蚀能够控制刻蚀速率,刻蚀后晶片的表面形态好,但是酸刻蚀的刻蚀速率过快导致晶片的平整度退化;相比酸刻蚀,碱刻蚀的刻蚀速率低,但是碱刻蚀能够提高晶片的平整度,因此可获得具有优异平整度的晶片。现有的酸刻蚀和碱刻蚀方法均有一定的缺陷,无法满足目前单晶硅片的刻蚀抛光需求,因此需要对现有刻蚀抛光技术进行改进。
3.cn102969392a公开了一种太阳能单晶硅电池的单面抛光工艺,通过前道工艺、背面抛光、丝网印刷与烧结三大步骤,用包含甲基三乙基氢氧化铵、异丙醇、十二烷基三甲基氯化铵的抛光液进行抛光,具有无金属离子污染、硅片减薄量低、抛光液调整方便、设备成本低的优点。cn110416364a公开了一种单晶perc背面刻蚀领域,在硅片正面采用水膜保护的条件下,利用氢氟酸水溶液中对硅片背面扩散后形成的psg进行去除,通过预清洗、碱抛光、碱清洗、酸清洗步骤,提高了背面钝化的效果,电池片的转化效率提升,并且降低了工艺成本。但目前单晶硅片的碱刻蚀抛光方法仍具有许多缺陷,如硅片表面反射率、刻蚀抛光损失等方面仍有待提高,且随着太阳能电池技术的发展,对于太阳能电池硅片的要求越来越高。因此,仍有必要对现有的单晶硅片的刻蚀抛光方法进行改进。
4.上述背景技术旨在辅助理解本发明的发明构思及技术方案,其并不必然属于本专利申请的现有技术,在没有明确的证据表明上述内容在本专利申请的申请日前已公开的情况下,上述背景技术不应当用于评价本技术技术方案的新创性。
技术实现要素:
5.为解决上述背景技术中提及的至少一种技术问题,本发明提供了一种单晶硅片的碱刻蚀抛光方法,利用包含非离子表面活性剂、酒石酸钠等组分的碱性抛光液对单晶硅进行刻蚀抛光,实现了较低温度下的刻蚀抛光,刻蚀温度降低,能耗减少,刻蚀抛光效果好,硅片表面反射率、电池的转化效率得到有效提高。
6.本发明解决其技术问题所采用的技术方案是:根据上述目的,本发明一方面提供了一种碱性抛光液,其包含质量比为1:0.5-0.8的含氟非离子表面活性剂、酒石酸钠。
7.根据本发明,含氟非离子表面活性剂在碱性抛光液中的质量百分含量为0.2-0.5%。
8.根据本发明,酒石酸钠的添加量在碱性抛光液中的质量百分含量为0.1-0.4%。
9.根据本发明,含氟非离子表面活性剂具有式(i)所示结构式:
ꢀ
(i);其中,n为5-12的自然数。
10.上述含氟非离子表面活性剂的制备方法,包括下述步骤:1)d-邻氟扁桃酸和氯化亚砜在催化剂的作用下反应得到d-邻氟扁桃酰氯;2)3-氨基-4-甲氧基乙酰苯胺、d-邻氟扁桃酰氯在催化剂的作用下发生酰胺化反应得到产物a;3)产物a与引发剂在110-140℃下搅拌10-30min,0.1-0.5mpa下滴加环氧乙烷,继续搅拌反应即得含氟非离子表面活性剂。
11.根据本发明,步骤1)中,d-邻氟扁桃酸和氯化亚砜的摩尔比为1:1.1-1.4。
12.根据本发明,步骤1)中,催化剂为四丁基卤化铵或苄基三乙基卤化铵。
13.根据本发明,步骤2)中,3-氨基-4-甲氧基乙酰苯胺、d-邻氟扁桃酰氯的摩尔比为1:1.1-1.5。
14.根据本发明,步骤2)中,催化剂为吡啶、二甲氨基吡啶、4-氨基吡啶中的任一种。
15.根据本发明,步骤3)中,产物a与环氧乙烷的摩尔比为1:7-15。
16.根据本发明,步骤3)中,所述引发剂为过氧化物引发剂和n,n-二甲基苯胺的混合物,过氧化物引发剂、n,n-二甲基苯胺的质量比为1:0.5-2。
17.在本发明中,首先将d-邻氟扁桃酸进行酰氯化反应制得d-邻氟扁桃酰氯,接着与3-氨基-4-甲氧基乙酰苯胺反应生成产物a,然后利用产物a中的羟基与环氧乙烷聚合后的端环氧基反应制得含氟非离子表面活性剂,方法简单,过程易控,收率高,将该含氟非离子表面活性剂添加到碱性抛光液中,能够增加各组分的分散性,减少因团聚而造成的表面划痕;含氟非离子表面活性剂与酒石酸钠混合使用,减少了抛光液的各向异性,可实现在45-55℃下的刻蚀抛光,刻蚀抛光温度降低,能耗减少,还可加快抛光速率,提高抛光效果,增加表面反射率、提高光电转换效率,这可能是因为含氟非离子表面活性剂与酒石酸钠之间具有一定的协同作用,能够有效去除表面金属,减少金属离子的影响,提高抛光效率,且有助于抛光液对硅片表面的浸润,加快刻蚀速率,使硅片表面的刻蚀更加均匀,获得的硅片更加平整,粗糙度低。
18.所述碱性抛光液中还包含研磨颗粒、甘油、有机胺化合物。本发明提供上述碱性抛光液,可实现较低温度下的刻蚀抛光,刻蚀速率快,刻蚀抛光效果好,减少了硅片表面的侵蚀,平整度高。
19.根据本发明,研磨颗粒为氧化硅或氧化镧,粒径为20-60nm,研磨颗粒在碱性抛光液中的质量百分含量为5-10%。
20.根据本发明,甘油在碱性抛光液中的质量百分含量为0.1-1%
根据本发明,有机胺化合物为乙醇胺、异丙醇胺、三乙醇胺、二甘醇胺、异丁醇胺、二异丙醇胺、2-乙氨基乙醇、2-甲氨基乙醇中的任一种,有机胺化合物在碱性抛光液中的质量百分含量为0.5-2%。
21.根据本发明,碱性抛光液的ph为8.8-10。
22.本发明另一方面提供了一种单晶硅片的碱刻蚀抛光方法,包括下述步骤:1)预处理:利用氢氟酸溶液对单晶硅片进行预处理,去除背面的磷硅玻璃层;2)刻蚀抛光:将前述所述碱性抛光液中各组分混合均匀后,调节ph至8.8-10,对硅片背面进行刻蚀抛光,抛光过程中利用微波辅助处理;3)清洗:对抛光后的硅片依次进行碱清洗、酸清洗、水洗。
23.根据本发明,表面预处理过程中,氢氟酸溶液的质量百分数为5-15%,预处理温度为30-40℃。利用氢氟酸溶液对单晶硅表面进行预处理,可有效去除单晶硅背面的磷硅玻璃层,去除效率高,减少对后续刻蚀抛光的影响。
24.根据本发明,表面刻蚀抛光过程中,温度为40-50℃,时间为2-6min,微波处理的功率为200-400w。单晶硅片经预处理去除表面磷硅玻璃层后,利用包含含氟非离子表面活性剂、酒石酸钠的碱性抛光液对硅片进行刻蚀抛光,不仅能降低刻蚀抛光温度,减少能耗,还可实现刻蚀速率快、抛光效果好、硅片损失少、降低表面粗糙度的目的。
25.根据本发明,碱清洗过程中,碱性溶液为包含氢氧化钾、过硫酸钾的混合水溶液,其中氢氧化钾的质量分数为2-5%,过硫酸钾的质量分数为0.5-2%,碱清洗时间为1-3min,温度为20-25℃。
26.根据本发明,酸清洗过程中,酸性溶液为包含氢氟酸、氯化钠的混合水溶液,其中氢氟酸的质量分数为8-15%,氯化钠的质量分数为1-2%;酸洗温度为20-25℃,时间为2-5min。
27.根据本发明,水洗过程中的温度为20-30℃,时间为5-30min。
28.对刻蚀抛光后的硅片依次进行碱清洗、酸清洗、水洗,与简单的清洗相比,本发明提供的清洗方法能够很好的去除硅片表面残留的抛光液、金属离子等,从而获得较高反射率、电池转化效率、表面平整度的单晶硅片。
29.本发明的另一方面还提供了一种单晶硅片,由上述碱刻蚀抛光方法处理得到。
30.本发明的另一方面还还提供了前述所述碱性抛光液在单晶硅片的碱刻蚀抛光中的应用。
31.本发明具有如下有益效果:1)本发明提供了一种单晶硅片的碱刻蚀抛光方法,利用该方法对单晶硅片进行刻蚀抛光,实现了较低温度下的刻蚀抛光,刻蚀抛光效果好,速度快,硅片减薄量低,可增加最终得到的太阳能电池片对长波的吸收,提高光伏太阳能电池片的转换效率;2)碱刻蚀抛光过程中,以包含含氟非离子表面活性剂、酒石酸钠的抛光液进行抛光,含氟非离子表面活性剂、酒石酸钠之间具有一定的协同作用,能够有效去除表面金属,减少金属离子的影响,提高抛光液对硅片表面的浸润,从而加快刻蚀速率,使硅片表面的刻蚀更加均匀,提高抛光效果,增加表面反射率、提高光电转换效率;3)碱刻蚀抛光后,对单晶硅片依次进行碱清洗、酸清洗、水洗,可以清洗掉抛光过程中产生的金属离子,去除了抛光带来的各种污染,与简单的清洗相比具有更良好的效果,
从而使硅片获得较高综合性能。
32.本发明为实现上述目的而采用了上述技术方案,弥补了现有技术的不足,设计合理,操作方便。
附图说明
33.为让本发明的上述和/或其他目的、特征、优点与实例能更明显易懂,所附附图的说明如下:图1是含氟非离子表面活性剂的合成路线图;图2为本发明单晶硅片的刻蚀抛光效果测试结果示意图;图3为本发明单晶硅片的刻蚀速度测试结果示意图;图4为本发明刻蚀抛光后单晶硅片的表面粗糙度测试结果示意图。
具体实施方式
34.为使本发明的上述目的、特征和优点能够更为明显易懂,下面结合附图对本发明的具体实施方式做详细的说明。
35.在本发明的具体实施例中,含氟非离子表面活性剂的合成路线图如图1所示,具体经由下述方法制备得到:1)d-邻氟扁桃酸加入到2-5重量倍的二氯甲烷中,加入催化剂,搅拌均匀后加入氯化亚砜,d-邻氟扁桃酸和氯化亚砜的摩尔比为1:1.1-1.4,100-120℃下搅拌反应6-10h,常压蒸馏,得到d-邻氟扁桃酰氯;2)按照摩尔比1:1.1-1.5,将3-氨基-4-甲氧基乙酰苯胺、d-邻氟扁桃酰氯加入到二氯甲烷中,加入催化剂,室温下搅拌反应8-16h,减压蒸发溶剂,剩余物用二氯甲烷萃取,依次用盐酸、去离子水清洗得到产物a;3)产物a与引发剂在110-140℃下搅拌反应10-30min,0.1-0.5mpa下滴加环氧乙烷,产物a、环氧乙烷的摩尔比为1:7-15,继续搅拌反应1-5h即得含氟非离子表面活性剂。
36.在本发明的具体实施例中,单晶硅片的碱刻蚀抛光方法,包括下述步骤:1)表面预处理:利用质量分数为5-15%的氢氟酸溶液对单晶硅片进行预处理,去除背面的磷硅玻璃层;2)表面刻蚀抛光:将5-10重量份研磨颗粒、0.1-1重量份甘油、0.1-0.4重量份酒石酸钠、0.5-2重量份有机胺化合物、0.2-0.5重量份含氟非离子表面活性剂、余量去离子水混合均匀得到抛光液,调节ph至8.8-10,对硅片进行表面刻蚀抛光,温度为40-50℃,时间为2-6min,抛光过程中利用微波处理进行辅助,微波处理的功率为200-400w;3)表面清洗:对抛光后的硅片依次进行碱清洗、酸清洗、水洗;碱清洗过程中,碱性溶液为包含2-5wt%的氢氧化钾、0.5-2wt%的过硫酸钾的混合水溶液,碱清洗时间为1-3min,温度为20-25℃;酸清洗过程中,酸性溶液为包含8-15wt%的氢氟酸、1-2wt%的氯化钠的混合水溶液,酸洗温度为20-25℃,时间为2-5min;水洗过程中,温度为20-30℃,时间为5-30min。
37.作为上述方案的改进,在抛光后的表面清洗过程中,酸清洗所用酸性溶液中还添
加有0.1-0.15wt%的三丁基焦磷酸铵、0.02-0.05wt%的2-(三氟甲基)异烟酸。单晶硅片经刻蚀抛光后,表面会残留一些抛光液,还可能残留一定的二氧化硅、金属氧化物等,利用碱性溶液、酸性溶液、去离子水进行清洗,表面金属离子等的去除不完全,会影响硅片的性能;在具体实施方式中发现,酸性溶液中添加少量的三丁基焦磷酸铵和2-(三氟甲基)异烟酸后可能有助于增加对金属离子的溶解能力,增加溶液对电子的夺取能力,减少在硅片表面的附着,从而加快清洗速率,提高清洗效率,减少对硅片的腐蚀,从而进一步降低表面粗糙度,减小减薄量。
38.以下具体描述本技术。
39.实施例1:本实施例提供了一种含氟非离子表面活性剂,具体经由下述方法制备得到:1)将20.4重量份d-邻氟扁桃酸加入到60重量份的二氯甲烷中,加入0.2重量份四丁基卤化铵,搅拌均匀后加入17.8重量份氯化亚砜,115℃下搅拌反应8h,常压蒸馏,得到21.2gd-邻氟扁桃酰氯,摩尔收率为93.9%;2)将18.1重量份3-氨基-4-甲氧基乙酰苯胺、步骤1)制得的d-邻氟扁桃酰氯加入到40重量份二氯甲烷中,加入0.08重量份4-氨基吡啶,利用氢氧化钠溶液调节ph至9.6,室温下搅拌反应12h,减压蒸发溶剂,剩余物用二氯甲烷萃取,依次用盐酸、去离子水清洗得到30.5g产物a,摩尔收率为91.8%;3)产物a与0.5重量份过氧化苯甲酰/n,n-二甲基苯胺混合物(重量比1:1)在120℃下搅拌20min,0.2mpa下滴加52重量份环氧乙烷,继续搅拌反应即得含氟非离子表面活性剂。
40.含氟非离子表面活性剂进行测试,结果显示ms(771.18);1h-nmr结果显示,在3.35附近为与醚键相连亚甲基氢的化学位移,3.44ppm附近为与醚键相连的甲基氢的化学位移,在7.0-7.2ppm附近为苯基上氢的化学位移,9.05ppm附近为酰胺基团中氢的化学位移;
13
c-nmr结果显示,165.9ppm附近出现酰胺碳的吸收峰,110-150ppm之间出现苯环碳的吸收峰,60-80ppm之间出现了与醚键相连的碳吸收峰。根据以上结果可以判断,含氟非离子表面活性剂成功制备。
41.实施例2:本实施例提供一种单晶硅片的碱刻蚀抛光方法,包括下述步骤:1)表面预处理:利用10wt%的氢氟酸溶液对单晶硅片进行预处理,去除背面的磷硅玻璃层;2)表面刻蚀抛光:将8重量份氧化镧(粒径为50nm,下同)、0.6重量份甘油、0.3重量份酒石酸钠、1重量份2-甲氨基乙醇、0.4重量份实施例1制得的含氟非离子表面活性剂、89.7重量份去离子水混合均匀得到抛光液,对硅片背面进行刻蚀抛光,温度为50℃,时间为8min,抛光过程中利用微波处理进行辅助;微波处理的功率为300w;3)表面清洗:对抛光后的硅片依次进行碱清洗、酸清洗、水洗,烘干即得;碱清洗过程中,碱性溶液为包含4wt%的氢氧化钾、1wt%的过硫酸钾的混合水溶液,碱清洗时间为2min,温度为23℃;酸清洗过程中,酸性溶液为包含12wt%的氢氟酸、1.6wt%的氯化钠的水溶液,酸洗温度为23℃,时间为4min;
水洗过程中,温度为25℃,时间为10min。
42.实施例3:本实施例提供另一种单晶硅片的碱刻蚀抛光方法,与实施例2的不同之处仅在于,抛光液由8重量份氧化镧、0.6重量份甘油、0.16重量份酒石酸钠、1重量份2-甲氨基乙醇、0.4重量份实施例1制得的含氟非离子表面活性剂、89.84重量份去离子水混合均匀制得。
43.实施例4:本实施例提供另一种单晶硅片的碱刻蚀抛光方法,与实施例2的不同之处仅在于,抛光液由8重量份氧化镧、0.6重量份甘油、0.2重量份酒石酸钠、1重量份2-甲氨基乙醇、0.4重量份实施例1制得的含氟非离子表面活性剂、89.8重量份去离子水混合均匀制得。
44.实施例5:本实施例提供另一种单晶硅片的碱刻蚀抛光方法,与实施例2的不同之处仅在于,抛光液由8重量份氧化镧、0.6重量份甘油、0.32重量份酒石酸钠、1重量份2-甲氨基乙醇、0.4重量份实施例1制得的含氟非离子表面活性剂、89.68重量份去离子水混合均匀制得。
45.实施例6:本实施例提供另一种单晶硅片的碱刻蚀抛光方法,与实施例2的不同之处仅在于,抛光液由8重量份氧化镧、0.6重量份甘油、0.4重量份酒石酸钠、1重量份2-甲氨基乙醇、0.4重量份实施例1制得的含氟非离子表面活性剂、89.6重量份去离子水混合均匀制得。
46.实施例7:本实施例提供另一种单晶硅片的碱刻蚀抛光方法,与实施例2的不同之处仅在于,抛光液由8重量份氧化镧、0.6重量份甘油、1重量份2-甲氨基乙醇、0.4重量份实施例1制得的含氟非离子表面活性剂、90重量份去离子水混合均匀制得,即未添加酒石酸钠。
47.实施例8:本实施例提供另一种单晶硅片的碱刻蚀抛光方法,与实施例2的不同之处仅在于,抛光液由8重量份氧化镧、0.6重量份甘油、0.3重量份酒石酸钠、1重量份2-甲氨基乙醇、90.1重量份去离子水混合均匀制得,即未添加含氟非离子表面活性剂。
48.实施例9:本实施例提供另一种单晶硅片的碱刻蚀抛光方法,与实施例2的不同之处仅在于,在步骤3)的酸清洗过程中,酸性溶液中还添加有0.12wt%的三丁基焦磷酸铵、0.03wt%的2-(三氟甲基)异烟酸。
49.实施例10:本实施例提供另一种单晶硅片的碱刻蚀抛光方法,与实施例9的不同之处仅在于,在步骤3)的酸清洗过程中,酸性溶液中未添加三丁基焦磷酸铵。
50.实施例11:本实施例提供另一种单晶硅片的碱刻蚀抛光方法,与实施例9的不同之处仅在于,在步骤3)的酸清洗过程中,酸性溶液中未添加2-(三氟甲基)异烟酸。
51.试验例1:刻蚀抛光效果评价:以实施例2-8制得的单晶硅片为试验样品,利用d8反射率测试仪测试表面反射率,并将刻蚀抛光后的单晶硅片经退火、镀膜、丝网印刷等工艺制成太阳能电池,测试电池转化效率,测得结果如图2所示。
52.图2是经本发明所述刻蚀抛光方法制得的单晶硅片的反射率和电池转化效率,图中b代表反射率,代表电池转化效率,如图所示,实施例2和4、5方法所得硅片的反射率和电池转化效率较高,实施例3和6方法所得硅片的反射率和电池转化效率明显低于实施例2,可知,含氟非离子表面活性剂、酒石酸钠的添加比例对刻蚀抛光效果具有明显的影响,当碱性抛光液中两者的比例在1:0.5-0.8时,可获得较高的抛光效果,提高单晶硅片的反射率和电池转化效率;实施例7和8的反射率和电池转化效率与实施例2比具有较大的差距,说明含氟非离子表面活性剂、酒石酸钠之间具有协同作用,当两者同时添加时可提高抛光液的刻蚀抛光效果。
53.试验例2:刻蚀速度:利用ade的ultragate9700测量实施例2-8中刻蚀抛光前后晶片的中心厚度,刻蚀速度利用下述公式进行计算:刻蚀速度=(刻蚀前厚度-刻蚀后厚度)/刻蚀时间,测得结果如图3所示。
54.图3是刻蚀速度的测量结果,如图3所示,实施例2的刻蚀速度为0.071μm/s,实施例4和5的刻蚀速度不低于0.065μm/s,可见,本发明提供的碱性抛光液具有较高的刻蚀抛光速度,对比实施例2-8,实施例3和6的刻蚀速度明显低于实施例2,实施例7和8的刻蚀速度最低,显然,相比仅添加含氟非离子表面活性剂或酒石酸钠,在碱性抛光液中同时添加两者,具有一定的协同作用,可加快刻蚀速度。
55.试验例3:表面粗糙度:以实施例2-11制得的单晶硅片为试验样品,利用mitsutoyo corporation的surftestsj-201p测量单晶硅片的表面粗糙度,测得结果如图4所示。
56.图4是刻蚀抛光后的单晶硅片的表面粗糙度,观察图4可知,相比仅添加含氟非离子表面活性剂(实施例7)或酒石酸钠(实施例8),实施例2-6的碱性抛光液中同时添加两者,获得了较低的表面粗糙度,且实施例2和4、5的碱性抛光液中含氟非离子表面活性剂、酒石酸钠的比例在1:0.5-0.8范围内,表面粗糙度最低,说明含氟非离子表面活性剂和酒石酸钠具有一定的协同作用,可加快刻蚀抛光速度,减少表面损失;还可以看出,实施例9-11的表面粗糙度与实施例2之间具有一定的差距,说明刻蚀抛光后的酸清洗过程中,在酸性溶液中同时添加三丁基焦磷酸铵、2-(三氟甲基)异烟酸,具有协同作用,可加快清洗速率,提高清洗效率,减少对硅片的腐蚀,降低表面金属离子等对硅片的影响,降低表面粗糙度。
57.试验例4:减薄量测试:以实施例2-11中刻蚀抛光前后的单晶硅片为试验样品,利用前后质量差计算其减薄量,结果如表1所示。
58.表1单晶硅片的减薄量 减薄量(g)实施例20.48实施例90.38实施例100.45实施例110.46表1是刻蚀抛光前后的单晶硅片的减薄量,从表1可以看出,实施例2的单晶硅片的减薄量为0.48g,减薄量低,相比实施例2,实施例9具有更低的减薄量,实施例10和11的减薄
量与实施例2无明显差距,显然,刻蚀抛光后的酸清洗过程中,利用包含三丁基焦磷酸铵、2-(三氟甲基)异烟酸的酸性溶液进行清洗,可加快清洗速度,避免因长时间清洗造成的硅片的损失。
59.上述实施例中的常规技术为本领域技术人员所知晓的现有技术,故在此不再详细赘述。
60.本文中所描述的具体实施例仅仅是对本发明精神作举例说明。本发明所属技术领域的技术人员可以对所描述的具体实施例做各种修改或补充或采用类似的方式替代,但并不会偏离本发明的精神或者超越所附权利要求书所定义的范围。
61.本发明未尽事宜均为公知技术。