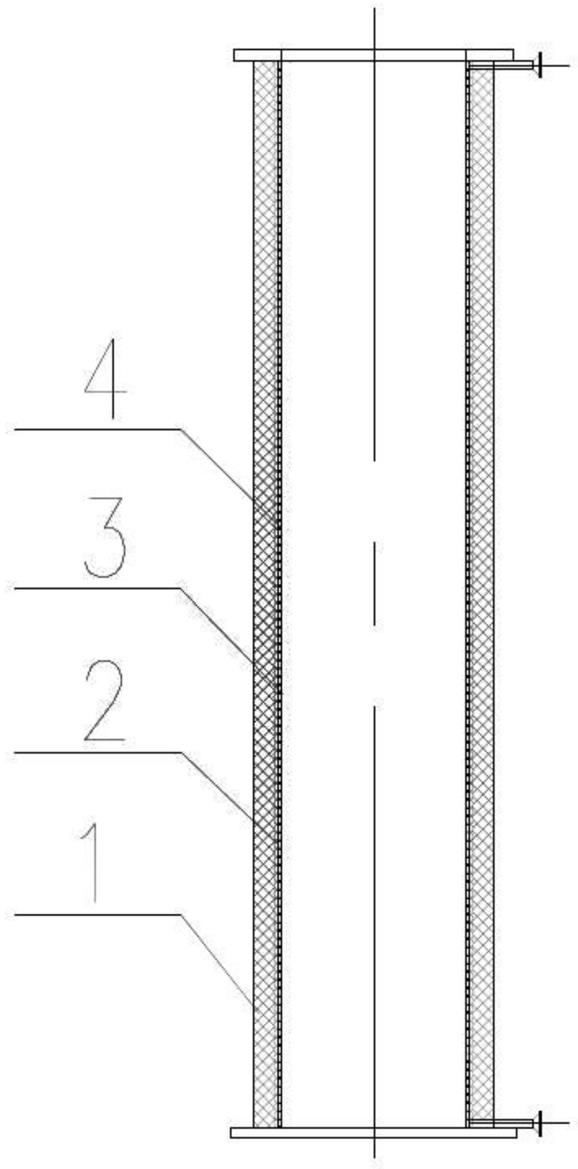
1.本实用新型涉及煤焦炉领域,具体地涉及一种焦炉节能及其煤气氢资源利用装置,尤其适用于焦炉炼焦过程不同熟焦期荒煤气富氢综合一种膜式固定床催化剂荒煤气余热回收及氢利用上升管。
背景技术:
2.在炼焦工艺中,炼焦煤在焦炉中被隔绝空气加热干馏,生成焦炭,同时,产生大量的荒煤气,焦炉通常是由多个碳化室(炉膛)并列而成,每个碳化室设置有荒煤气上升管出口,煤在1000
±
50℃碳化室内炼焦过程中干馏出高达850℃左右的高温荒煤气,荒煤气经过碳化室荒煤气出口进入上升管组件,经过氨水减温后进入集气管。炼焦过程中,荒煤气的馏出在炼焦过程的不同时间的馏分不同,炼焦前期干馏出的荒煤气含有大分子煤焦油为主,炼焦后期干馏出的荒煤气则以轻质小分子煤气为主要组份,炼焦后期的熟焦期轻质小分子煤气主要是h2和ch4组成,其中h2占到40~60%。目前,这部分煤气中的氢气基本上是制成煤气,作为燃料烧掉了,氢是重要的化工资源,可以作为加氢反应原料轻质化大分子煤焦油。炼焦过程的后期产生荒煤气的煤气中富氢,且温度很高,也就有很高的化学活性。焦炉需要控制炭化室顶部空间里的荒煤气温度(炉顶空间温度控制),根据《焦炉技术管理规程》规定,炉顶空间温度宜控制在800
±
50℃,不宜超过850℃,炉顶空间温度过高,则焦炉煤气在炭化室顶部产生二次裂解,大量的沉积碳附着在炭化室顶部,空间温度过高,也会造成化产回收焦油质量不合格,如焦油比重增大、粘度增大、脱水困难。按推焦计划提前10分钟~20分钟打开上升管盖(最多不得超过三个),并同时关闭桥管水封翻板阀,打开远离上升管的除尘孔盖,吸入空气,烧去炭化室顶部的石墨。在焦炉生产中,常见的消除石墨方法有:用压缩空气吹扫石墨、烧空炉清扫石墨、推焦头顶部装刮刀清除石墨,前两种方法最后都离不开人工敲打,用人工清扫或敲打很难有多大成效,对大焦炉来说就有一定困难。
3.煤焦油焦化生产过程的副产品,是一个组分上万种的复杂混合物 ,目前已从中分离并认定的单种化合物约 500 余种 ,约占煤焦油总量的 55%,其中包括苯、二甲苯、萘等 174 种中性组分;酚、甲酚等 63 种酸性组分和1 13 种碱性组分脚。某些组分虽然价值很高,但在煤煤焦油中的含量很少,占 l%以上的品种仅有 13 种,它们是萘、菲、萤蒽、芴、蒽、芘(熔点150℃)、苊、咔唑、2一甲基萘、1一甲基萘、氧芴和甲酚。煤焦油中的很多化合物是塑料、合成橡胶、农药、医药、耐高温材料及国防工业的贵重原料 ,也有一部分多环烃化合物是石油化工所不能生产和替代的。煤焦油主要用来加工生产轻油、酚油、萘油及改质沥青等,再经深加工后制取苯、酚、萘、蒽等多种化工原料,虽然产品数量较多、用途广泛,但是相对煤焦油中的 500多种化合物来讲,还是少得很。煤焦油简单加工后的利用价值不大,国内外普遍看好的是其深加工精制产品的应用。国内外煤焦油加工工艺大同小异,都是脱水、分馏,煤焦油加工的主要研究方向是增加产品品种、提高产品质量等级、节约能源和保护环境。
4.煤焦油加氢精致的作用是脱硫、脱氮、脱氧和加氢饱和,加氢过程使煤焦油中的一
部分不饱和烯烃和芳烃键达到饱和,煤焦油在该工段的脱硫、脱氮和脱氧率分别达到96%、85%以及97%以上,达到裂化原料的要求。产品的氢/碳比从原料油的1.11提高至1.58,使煤焦油在该工段实现部分轻质化。加氢裂化段进一步脱除原料油中的硫、氮、氧等杂原子,并且使产品进一步轻质化,原料大部分加氢裂化生成汽油、柴油等轻质馏分。经过裂化工段后,杂原子的脱除率均可达到99.5%以上,氢/碳比可达到1.62。煤焦油经过三段加氢后,产品油更加轻质清洁,经过精馏后,即可获得高价值的石脑油馏分油和柴油馏分油。
5.煤焦油加氢随焦油重油转化率增加,氢耗先快速增加后缓慢增加,油收率与氢耗类似最后增加,气产率呈增加趋势。氢气是焦油重油加氢裂化反应的反应物,油产率和气产率是焦油重油加氢裂化反应的并行产物。随着反应温度和反应时间的增加,焦油重油的加氢反应深度增加,参与反应的氢气增加,因此氢耗增加。焦油重油反应初期,大量稠环裂解的中间产物需要加氢稳定,因此随反应深度提高,初期氢耗增加迅速;而反应后期,大量难以裂解的稠环有机物大部分已经裂解 ,生成了环数较少的单环或双环分子 的油产物。后期虽然单环芳烃难以加氢裂化,但芳环类型化合物上的支链在高温下会发生进一步的裂解反应,生成分子尺寸更小的有机物,其裂解得到小分子气体的速率更快,所以气产率后期生成速度变快。由于前期已经有大量稠环芳烃不饱和加氢,因此后期氢耗量减少,表现在反应后期氢耗增加趋于缓慢。氢耗和油产率的变化规律反映了焦油重油加氢裂化反应并行反应的规律。稠环物质发生脱氢、开环和脱烷基反应分解为分子量较小的油产物分子后,稠环大分子裂化减少。同时,小分子油数量增加,加氢裂解速度增加,因此油产率选择性反而转低。同理,生成的气产率选择性随转化率增加不断增加,原因为随反应转化率提高,小分子油裂解生成的气体量增加,气产率增加。从油产率选择性和气产率选择性在转化率后期的变化规律可以看出焦油重油催化加氢裂解工艺中,合适的选择温度和时间等对控制油产物的选择性非常重要。即低温反应条件下反应时间和反应温度均为影响脱氮率的决定性因素;高温反应条件下,反应温度是影响脱氮的决定性因素。340℃ 以上,脱氮率都能达到 95% 以上,低温条件下,通过延长反应时间也能到达较高脱氮率。
6.含有40~60%氢的焦炉煤气在炼焦后工艺很难分离氢。造成氢气资源的浪费。
7.总之,馏出荒煤气在碳化室、上升管、桥管处结焦,浪费了荒煤气资源、给安全生产带来很大隐患、增加了上产过程设备维护维修劳动强度和难度、降低了焦炉生产率,其原因就是大分子荒煤气裂解所致,同时煤焦油的轻质化加工需要加氢,煤气中含有40~60%的氢资源又得不到应用,使得焦炉工艺过程中还有很多技术难点与痛点:
8.1、大分子煤焦油的裂解反应,会造成大量的沉积碳附着在炭化室顶部、上升管和桥管,给安全生产带来很大隐患、增加了上产过程设备维护维修劳动强度和难度;
9.2、煤焦油中含硫、含氮很难脱出,进一步利用或燃烧会产生硫化物、氮化物的环境污染,脱硫、脱硝增加过程成本;
10.3、碳化室顶部石墨燃烧除焦,浪费能源、浪费资源、降低了焦炉生产率;
11.4、大分子煤焦油裂解降低焦油收率,降低了效益;
12.5、荒煤气低温焦石墨温度高,浪费后续氨水喷注的能耗,浪费余热。
技术实现要素:
13.本实用新型的目的在于提供一种余热回收及氢气利用膜固定床催化剂上升管,其
原理是按照专利申请号cn202010620326.x《一种焦炉氢气利用方法及其系统》的方法将焦炉结焦后期碳化室干馏出的富氢荒煤气通过管渠导入另外一个刚加完煤的碳化室或上升管后,使该碳化室新加入的焦煤干馏出的大分子荒煤气和另一个结焦后期碳化室干馏出的富氢荒煤气混合,混合后的富氢荒煤气在通过一种余热回收及氢气利用加一层薄膜的固定床催化剂上升管流出的过程中利用余热回收控制反应温度、利用上升管接触荒煤气表面的膜式固定床催化剂地催化,使富氢荒煤气在合适的温度及催化剂作用下发生定向反应,消除现存焦炉生产过程的技术瓶颈问题。提高上升管的可靠性高和稳定性,有利于系统长期稳定、安全运行,尤其使该系统热氢资源得以综合利用。
14.本实用新型的技术方案为:一种膜式固定床催化剂荒煤气余热回收及氢利用上升管,包括上升管的壳体和桥管三通(7),上升管内通有富氢荒煤气,该上升管壳体内侧包括筒壁保温层(1)、温控及余热回收装置、防腐陶瓷层(3)、膜式固定床催化剂层(4);上升管的壳体管壁内层为筒壁保温层(1),筒壁保温层(1)内部设有温控及余热回收装置,温控及余热回收装置内通有带走荒煤气的余热的工质;且温控及余热回收装置外层表面附着有防腐陶瓷层(3),或者附着有防腐陶瓷层(3)及膜式固定床催化剂层(4)合二为一的混合层,当温控及余热回收装置外层表面单独附着有防腐陶瓷层(3)时,和富氢荒煤气接触的温控及余热回收装置外表面还要附着一层膜式固定床催化剂层(4)。
15.作为本实用新型的一个优选实施例,所述温控及余热回收装置为筒壁温控及余热回收装置(2)和/或中心温控及余热回收装置(6);当温控及余热回收装置为筒壁温控及余热回收装置(2)时,筒壁温控及余热回收装置(2)设置在筒壁保温层(1)内层,当温控及余热回收装置为中心温控及余热回收装置(6)时,中心温控及余热回收装置(6)设置在上升管壳体中心径向向外布置方向上,且保证该位置为上升管中心径向向外荒煤气流场和温度场均匀的位置。
16.作为本实用新型的一个优选实施例,还包括上升管的壳体中心设置的搅拌装置(5),该搅拌装置(5)能实现旋转或移动部件功能,通过部件的转动或移动形成荒煤气的搅动,实现荒煤气紊流度强化。
17.作为本实用新型的一个优选实施例,所述搅拌装置(5)设置在上升管中心,搅拌装置(5)上设有导流叶片,搅拌装置(5)表面附着有防腐陶瓷层(3),防腐陶瓷层(3)外层再附着膜式固定床催化剂层(4),或者附着有防腐陶瓷层(3)及膜式固定床催化剂层(4)合二为一的混合层。
18.作为本实用新型的一个优选实施例,所述桥管三通(7)内表面附着有膜式固定床催化剂层(4),或者是桥管三通(7)的局部内表面附着有膜式固定床催化剂层(4)。
19.作为本实用新型的一个优选实施例,还包括在上升管内部或碳化室顶增加网式固定床。
20.作为本实用新型的一个优选实施例,还包括在上升管内部骨架(8)表面附着一层膜式固定床催化剂层(4)。
21.本实用新型的技术效果:
22.本实用新型的一种膜式固定床催化剂荒煤气余热回收及氢利用上升管与现有技术相比,具有以下优点:
23.1、本实用新型焦炉氢气利用控制、调整、诱导大分子煤焦油的裂解反应,消除了炭
化室顶部沉积碳的附着;
24.2、加入固定床催化剂层就可以促进加氢目标化反应,促进大分子裂解后的轻质化,增加轻收率,提高煤焦油附加值。
25.3、本实用新型通过富氢裂解控制实现适当加氢反应,使大分子煤焦油裂解加氢,提高焦油收率,显著提高焦化效益。
26.4、本实用新型可以使荒煤气中的有机硫通过加氢反应形成无机硫,容易采用化学方法脱硫脱硝,减少环境污染,降低焦炉或焦油深加工处理成本。
27.5、本实用新型富氢管渠进行冷却余热回收,节能减排。
28.6、实用新型轻质化后的荒煤气低温焦石墨温度降低,可显著降低后续氨水喷注量,提高余热回收量。
29.7、本实用新型富氢荒煤气在通过一种余热回收及氢气利用膜固定床催化剂上升管流出的过程中利用余热回收控制反应温度、利用上升管接触荒煤气表面的膜式固定床催化剂催化,使富氢荒煤气在合适的温度及催化剂作用下发生定向反应,消除现存焦炉生产过程的技术瓶颈问题。提高上升管的可靠性高和稳定性,有利于系统长期稳定、安全运行。
30.8、本实用新型可以降低现有焦炉荒煤气450℃的结焦点,回收荒煤气更多的余热,减少后续喷注高压氨水的机械能消耗和氨水消耗量;所述膜式固定床催化剂层4附着于余热回收控温装的荒煤气侧防腐陶瓷层3的外表面,荒煤气流过表面时富氢荒煤气可以在此表面的膜式固定床催化剂层4的作用下,产生定向轻质化反应,生产目标产品,提高煤焦油轻收率,提高煤焦油附加值。
31.9、在附着于筒壁温控及余热回收装置2外层膜式固定床催化剂层4催化作用下,发生定向反应,提高焦油轻质化产品收率,提高经济效益,同时降低了荒煤气露点温度,降低了可以回收荒煤气的余热,提高了节能效益,防止了凝析温度点以下的结焦,回收利用节省了凝析温度点以下以上的余热,降低了冷却氨水的喷洒量,节省了氨水循环的机械消耗。
附图说明
32.图1为本实用新型实施例一结构示意图;
33.图2为本实用新型实施例二结构示意图;
34.图3为本实用新型实施例三结构示意图;
35.图4为本实用新型实施例四结构示意图;
36.图5为本实用新型图局部结详细构示意图;
37.图6为本实用新型骨架表面附有固定床催化剂层的示意图;
38.其中,筒壁保温层1、筒壁温控及余热回收装置2、防腐陶瓷层3、固定床催化剂层4、搅拌装置5、中心温控及余热回收装置6、桥管三通7、骨架8。
具体实施方式
39.为使本实用新型实施例的目的、技术方案和优点更加清楚,下面将结合本实用新型实施例中的附图,对本实用新型实施例中的技术方案进行清楚、完整地描述,显然,所描述的实施例是本实用新型一部分实施例,而不是全部的实施例。通常在此处附图中描述和示出的本实用新型实施例的组件可以以各种不同的配置来布置和设计。因此,以下对在附
图中提供的本实用新型的实施例的详细描述并非旨在限制要求保护的本实用新型的范围,而是仅仅表示本实用新型的选定实施例。基于本实用新型中的实施例,本领域普通技术人员在没有做出创造性劳动前提下所获得的所有其他实施例,都属于本实用新型保护的范围。
40.应注意到:相似的标号和字母在下面的附图中表示类似项,因此,一旦某一项在一个附图中被定义,则在随后的附图中不需要对其进行进一步定义和解释。
41.下面通过具体实施例并结合附图对本实用新型作进一步说明。
42.如各图所示,一种膜式固定床催化剂荒煤气余热回收及氢利用上升管,包括:筒壁保温层1、温控及余热回收装置、防腐陶瓷层3、膜式固定床催化剂层4、搅拌装置5、桥管三通7,所述温控及余热回收装置、搅拌装置5的外表面均附有防腐陶瓷层3,或者附着有防腐陶瓷层3及膜式固定床催化剂层4合二为一的混合层;所述温控及余热回收装置内通用可以带走余热的工质,工质在温度控制信息作用下,通入适当温度压力的工质取出反应条件以上的剩余温度下的热量,进行余热回收利用,该实用新型可以降低现有焦炉荒煤气450℃的结焦点,回收荒煤气更多的余热,减少后续喷注高压氨水的机械能消耗和氨水消耗量;所述膜式固定床催化剂层4附着于余热回收控温装的荒煤气侧防腐陶瓷层3的外表面,荒煤气流过表面时富氢荒煤气可以在此表面的膜式固定床催化剂层4的作用下,产生定向轻质化反应,生产目标产品,提高煤焦油轻收率,提高煤焦油附加值。通过各部分不同的组合可以形成不同的技术方案,以下给出四个实施例是上述各种装置的不同组合形成的技术方案。
43.如图1或5所示,优选地实施例一,为温控及余热回收装置只包括筒壁包含有筒壁温控及余热回收装置2时的技术方案:所述筒壁温控及余热回收装置2位于上升管壳体和隔热层1内侧筒体,其筒壁温控及余热回收装置2外层附着有防腐陶瓷层3,防腐陶瓷层3外面附有固定床催化剂层膜4,或者附着有防腐陶瓷层3及膜式固定床催化剂层4合二为一的混合层,荒煤气流经上升管内侧时,筒壁温控及余热回收装置2内通有带走荒煤气的余热的工质,通过上升管管壁的内筒壁温控及余热回收装置2控制温度,当筒壁温控及余热回收装置2外层表面附着有防腐陶瓷层3时,和富氢荒煤气接触的一侧附着有膜式固定床催化剂层4;富氢荒煤气在流经筒壁时,在附着于筒壁温控及余热回收装置2外层膜式固定床催化剂层4催化作用下,发生定向反应,提高焦油轻质化产品收率,提高经济效益,同时降低了荒煤气露点温度,降低了可以回收荒煤气的余热,提高了节能效益,防止了凝析温度点以下的结焦,回收利用节省了凝析温度点以下以上的余热,降低了冷却氨水的喷洒量,节省了氨水循环的机械消耗。
44.如图2所示,优选地实施例二,为包含有筒壁温控及余热回收装置2和搅拌装置5,搅拌装置5可以实现旋转或移动部件的技术方案,所述筒壁温控及余热回收装置2位于上升管壳体和隔热层1内侧筒体,其筒壁温控及余热回收装置2外层,附着有防腐陶瓷层3,防腐陶瓷层3附有固定床催化剂层膜4,或者筒壁温控及余热回收装置2外层附着防腐陶瓷层3和膜式固定床催化剂层4合二为一的混合层,当筒壁温控及余热回收装置2外层表面附着有防腐陶瓷层3时,靠近富氢荒煤气通道的一侧附着有膜式固定床催化剂层4,荒煤气流经上升管内表面时,在膜式固定床催化剂层4作用下发生加氢裂化反应使荒煤气产生轻质化反应。同时,还设置有搅拌装置5,作为本实用新型的一个具体实施例,搅拌装置上可以设置有搅拌棒或者设置有导流叶片,或者搅拌装置设置为其他旋转、垂直移动的扰动形式,使上升管
内荒煤气在流动过程中,发生径向紊流度,增加荒煤气与催化剂的接触,促进反应进行。
45.作为本实用新型的一个优选实施例,搅拌装置5可以实现旋转或移动部件,转动或移动部件由位于上升管顶部的马达驱动来实现,搅拌装置5通过中心轴的转动形成转动或移动,形成荒煤气的搅动,实现荒煤气紊流度强化,增大反应速度和深度的目的,搅拌装置5的作用还可以起到在线维护上升管的目的,中心轴能够实现转动或移动。
46.作为本实用新型的一个优选实施例,上述搅拌装置5上设有旋转的导流叶片,搅拌装置5表面附着有防腐陶瓷层3,防腐陶瓷层3外层再附着膜式固定床催化剂层4,也可以是防腐陶瓷层3外层再附着膜式固定床催化剂层4的二合一。
47.如图3所示,优选地实施例三,为包含上升管筒壁保温层1、温控及余热回收装置、防腐陶瓷层3、膜式固定床催化剂层4和桥管三通7的技术方案,此时,温控及余热回收装置在上升管管壁上(见筒壁温控及余热回收装置2)+位于上升管中心径向向外布置的合适位置上(见中心温控及余热回收装置6);所述上升管中心径向向外布置的合适位置为上升管中心径向向外荒煤气流场、温度场均匀的位置上。
48.如图4所示,优选地实施例四,为包含筒壁保温层1、筒壁温控及余热回收装置2、防腐陶瓷层3、膜式固定床催化剂层4、搅拌装置5、中心温控及余热回收装置6和三通桥管7的技术方案,所述温控及余热回收装置在上升管管壁上(见筒壁温控及余热回收装置2)+位于上升管中心径向向外布置的合适位置上(见中心温控及余热回收装置6)+转动移动扰动膜式固定床催化剂层4,或者是其中任意两项的组合;所述转动移动扰动膜式固定床催化剂层4上升管内筒设置有搅拌装置5,该装置能够转动或移动,通过转动或移动形成荒煤气的搅动,实现荒煤气紊流度强化。作为本实用新型的一个优选实施例,该装置还包括在上升管内部或碳化室顶增加网式固定床。
49.如图6所示的骨架8表面附有膜式固定床催化剂层4的示意图。骨架8可以为网状结构,也可以塔盘式或填料式,在不是占有较大流通面积的上升管内布置,以增大荒煤气与催化剂接触面积,促进加氢反应。
50.上述筒壁保温层1、温控及余热回收装置、防腐陶瓷层3、膜式固定床催化剂层4、搅拌装置5和三通桥管7均为现有部件,作为本实用新型的一个具体实施例,筒壁保温层1采用耐高温保温棉实现,温控及余热回收装置采用带有温度调节系统的盘管,或者夹套,或者夹套加盘管实现(见:实用新型专利:焦炉上升管高效余热回收装置及其防结焦方法,专利申请号cn201611134129.7,或实用新型专利:一种基于自动控制的蓄热式余热回收设备及其回收方法,专利申请号cn201410461904.4)。
51.在本说明书的描述中,参考术语“一个实施例”、“一些实施例”、“示意性实施例”、“示例”、“具体示例”、或“一些示例”等的描述意指结合该实施例或示例描述的具体特征、结构、材料或者特点包含于本实用新型的至少一个实施例或示例中。在本说明书中,对上述术语的示意性表述不一定指的是相同的实施例或示例。而且,描述的具体特征、结构、材料或者特点可以在任何的一个或多个实施例或示例中以合适的方式结合。
52.尽管已经示出和描述了本实用新型的实施例,本领域的普通技术人员可以理解 :在不脱离本实用新型的原理和宗旨的情况下可以对这些实施例进行多种变化、修改、替换和变型,本实用新型的范围由权利要求及其等同物限定。