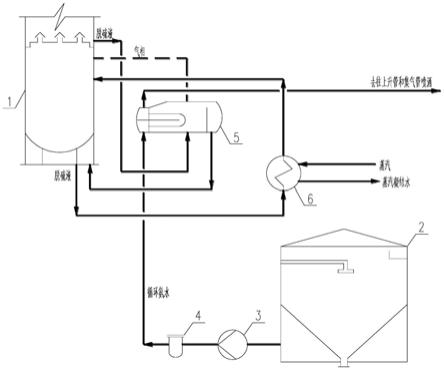
1.本发明涉及焦炉煤气净化脱硫脱氰技术领域,尤其涉及一种循环氨水余热用于真空碳酸钾脱硫再生热源的循环系统及工艺。
背景技术:
2.真空碳酸钾脱硫工艺的能耗主要源自真空解吸过程,由于现有工艺中普遍采用蒸汽气提的方式对脱硫富液进行解吸,解吸过程需要蒸发大量水蒸汽作为气提气,因此所需热量较高。传统的真空碳酸钾脱硫工艺通常采用以下四种方式加热脱硫液,以获取解吸热量。第一种,利用蒸汽加热;第二种,与初冷器余热水换热;第三种,将脱硫液送至初冷器上部,直接利用荒煤气余热;第四种,与循环氨水换热。
3.上述四种方式在经济性、运行可靠性,改造可行性等方面各有不足,具体如下:
4.第一种方式:蒸汽加热未能利用余热,能耗极高,经济性不合理。
5.第二种方式:初冷器顶部设余热水段,虽然也利用了余热,但未能实现脱硫液与荒煤气直接一次换热,而是经过中间余热水的二次换热,造成换热效率低,同时增加了投资和占地。
6.第三种方式:增设循环脱硫液槽及循环脱硫液泵,将脱硫液打入初冷器上部与荒煤气直接换热,不使用蒸汽,又节约了循环水,在四种方式中经济性最好;但对于已投产的改造项目,特别是初冷器面积不能改变的情况下,不具备可行性。
7.第四种方式:与循环氨水换热虽然利用了余热,但循环氨水中杂质较多,易堵塞管道,故系统运行的可靠性差。为防止堵塞,常采用不锈钢材质的螺旋板换热器,且设置用于独立换热的离心泵,故投资较高。此外,循环氨水换热后温度较低,严重时会影响上升管和集气管的喷氨效果。
技术实现要素:
8.本发明提供了一种循环氨水余热用于碳酸钾脱硫再生热源的循环系统及工艺,将用于上升管和集气管喷洒的循环氨水,过滤后先送至氨水再沸器换热,作为再生塔真空解吸的热源,不足部分用蒸汽补充;具有工艺流程新颖、节能降耗的优点,适合适用于已建项目的改造。
9.为了达到上述目的,本发明采用以下技术方案实现:
10.一种循环氨水余热用于真空碳酸钾脱硫再生热源的系统,包括再生塔、焦油氨水分离槽、循环氨水泵、氨水过滤器、氨水再沸器及蒸汽再沸器;所述再生塔的下部设断塔盘,断塔盘上方的再生塔上设脱硫液出口一,断塔盘下方的再生塔上设脱硫液气相入口及脱硫液入口一;再生塔的底部设脱硫液出口二及脱硫液入口二;所述焦油氨水分离槽的下部设循环氨水出口,通过管道依次连接循环氨水泵、氨水过滤器及氨水再沸器的管程入口,氨水再沸器的管程出口通过管道连接设于焦炉上升管和集气管处的氨水喷洒装置;再生塔的脱硫液出口一通过管道连接氨水再沸器的壳程入口,氨水再沸器的壳程出口通过管道连接再
生塔的脱硫液入口二;氨水再沸器的顶部设气相出口通过管道连接再生塔的脱硫液气相入口;再生塔的脱硫液出口二通过管道连接蒸汽再沸器的脱硫液入口,蒸汽再沸器的脱硫液出口通过管道连接再生塔的脱硫液入口一,蒸汽再沸器还设有蒸汽入口及蒸汽凝结水出口。
11.所述氨水再沸器为固定管板式再沸器,材质为碳钢。
12.所述氨水再沸器的壳程入口设于壳体中部,壳程出口设于远离管程入口的壳体一端,壳程入口与壳程出口之间的壳体内设溢流板。
13.所述氨水过滤器的过滤精度为300微米,并设有反冲洗装置。
14.一种循环氨水余热用于真空碳酸钾脱硫再生热源的工艺,包括如下过程:
15.1)焦油氨水分离槽上部的氨水流入下部的筒体中,启动循环氨水泵将焦油氨水分离槽中的循环氨水抽出,循环氨水经过氨水过滤器过滤后送至氨水再沸器,与自再生塔中断塔盘上方流出的脱硫液换热,换热后的脱硫液返回再生塔的底部进行再生解吸;
16.2)换热后的循环氨水温度为65~68℃,送至焦炉的上升管和集气管处,用于荒煤气喷洒降温;
17.3)再生塔底的脱硫液送入蒸汽再沸器中,与蒸汽再沸器中通入的压力为0.4~0.6mpa的饱和蒸汽换热后返回再生塔底部,用于补足再生塔内脱硫液再生解吸所用的热量。
18.与现有技术相比,本发明的有益效果是:
19.1)运行成本低;主要利用循环氨水余热作为脱硫富液再生热源,节省了大量蒸汽的消耗,经济性较好。
20.2)投资省;焦油氨水分离槽来的循环氨水经过滤后杂质含量较低,不易堵塞管道,且对碳钢材质的设备几乎无腐蚀性,因此氨水再沸器的材质可以选择普通碳钢,大大减少了投资成本;用于换热的循环氨水量与用于上升管和集气管处喷洒的循环氨水量一致,循环氨水泵实现一泵两用,进一步节省了投资;
21.3)工艺路线新颖,特别适合技改项目,尤其对于初冷器面积不能增加的情况,本发明具有无法取代的优势;
22.4)本发明同样适用于真空碳酸钠脱硫等类似工艺。
附图说明
23.图1是本发明所述循环氨水余热用于碳酸钾脱硫再生热源的循环系统的结构示意图。
24.图中:1.再生塔 2.焦油氨水分离槽 3.循环氨水泵 4.氨水过滤器 5.氨水再沸器 6.蒸汽再沸器
具体实施方式
25.下面结合附图对本发明的具体实施方式作进一步说明:
26.如图1所示,本发明所述一种循环氨水余热用于真空碳酸钾脱硫再生热源的系统,包括再生塔1、焦油氨水分离槽2、循环氨水泵3、氨水过滤器4、氨水再沸器5及蒸汽再沸器6;所述再生塔1的下部设断塔盘,断塔盘上方的再生塔1上设脱硫液出口一,断塔盘下方的再
生塔1上设脱硫液气相入口及脱硫液入口一;再生塔1的底部设脱硫液出口二及脱硫液入口二;所述焦油氨水分离槽2的下部设循环氨水出口,通过管道依次连接循环氨水泵3、氨水过滤器4及氨水再沸器5的管程入口,氨水再沸器5的管程出口通过管道连接设于焦炉上升管和集气管处的氨水喷洒装置;再生塔1的脱硫液出口一通过管道连接氨水再沸器5的壳程入口,氨水再沸器5的壳程出口通过管道连接再生塔1的脱硫液入口二;氨水再沸器5的顶部设气相出口通过管道连接再生塔1的脱硫液气相入口;再生塔1的脱硫液出口二通过管道连接蒸汽再沸器5的脱硫液入口,蒸汽再沸器6的脱硫液出口通过管道连接再生塔1的脱硫液入口一,蒸汽再沸器6还设有蒸汽入口及蒸汽凝结水出口。
27.所述氨水再沸器5为固定管板式再沸器,材质为碳钢。
28.所述氨水再沸器5的壳程入口设于壳体中部,壳程出口设于远离管程入口的壳体一端,壳程入口与壳程出口之间的壳体内设溢流板。
29.所述氨水过滤器6的过滤精度为300微米,并设有反冲洗装置。
30.一种循环氨水余热用于真空碳酸钾脱硫再生热源的工艺,包括如下过程:
31.1)焦油氨水分离槽2上部的氨水流入下部的筒体中,启动循环氨水泵3将焦油氨水分离槽2中的循环氨水抽出,循环氨水经过氨水过滤器4过滤后送至氨水再沸器5,与自再生塔1中断塔盘上方流出的脱硫液换热,换热后的脱硫液返回再生塔1的底部进行再生解吸;
32.2)换热后的循环氨水温度为65~68℃,送至焦炉的上升管和集气管处,用于荒煤气喷洒降温;
33.3)再生塔1底的脱硫液送入蒸汽再沸器6中,与蒸汽再沸器6中通入的压力为0.4~0.6mpa的饱和蒸汽换热后返回再生塔1底部,用于补足再生塔1内脱硫液再生解吸所用的热量。
34.循环氨水中的杂质较多,易堵塞管道,致使常规采用循环氨水作为脱硫液再生热源的工艺可靠性差,并且需要采用不锈钢材质的换热器。本发明将用于上升管和集气管喷洒的循环氨水经过滤后,作为脱硫富液再生解吸的热源,通过设置氨水过滤器5,并将过滤精度设置为300微米,大于300微米的颗粒脱除率可达95%以上,从而避免了堵塞问题。氨水腐蚀性很弱,氨水再沸器5采用碳钢材质即可,节约了投资成本。
35.与氨水再沸器5换热的氨水量与用于上升管和集气管喷洒的循环氨水量一致。荒煤气在集气管内冷却时,一般要求喷洒氨水的压力为~300kpa(表压);本发明中,循环氨水泵3可一泵两用,无需设置用于独立换热的离心泵。在改造项目中,经核算满足扬程的情况下,也无需额外增加离心泵。
36.循环氨水不可无限制的取热,这是因为煤气冷却主要靠循环氨水的蒸发,温度过低不易蒸发,也达不到预期的雾化程度。此外,温度较低的情况下,会使集气管底部剧烈冷却,冷凝的焦油粘度较大,易使集气管堵塞。因此,单纯为了循环氨水的余热利用而过度降低循环氨水的温度,会得不偿失。进入集气管前的煤气露点温度同装入煤的水分含量有关,当装入煤全部水分为9%左右时,要求循环氨水的温度为60~63℃,为保证氨水蒸发的推动力,喷洒氨水温度应高于煤气露点(5℃左右),因此,本发明将用于喷洒的循环氨水的进水端温度控制在65~68℃。
37.再生塔1内用于脱硫液解吸再生热量不足的部分用蒸汽补足,本发明通过蒸汽再沸器6来实现(少数情况下,如循环氨水量较大且温度较高时,脱硫液再生热量可完全由循
环氨水的余热提供,不需要额外补入蒸汽)。
38.以年产焦炭200万吨的焦化厂为例,假设循环氨水的初始温度为75℃,经氨水再沸器换热后的温度为68℃,则可以满足再生塔脱硫富液解吸所需热量的85%左右,特殊情况,如脱硫塔入口煤气含硫量较高(超过10g/nm3)的时候,采用两级脱硫塔串联操作,再生塔对应设置2台,脱硫再生需要的热量更多,但采用本发明所述工艺也可满足40%的热量需求;而一般认为,循环氨水换热占比30%以上就具备较好的经济性。
39.以上所述,仅为本发明较佳的具体实施方式,但本发明的保护范围并不局限于此,任何熟悉本技术领域的技术人员在本发明揭露的技术范围内,根据本发明的技术方案及其发明构思加以等同替换或改变,都应涵盖在本发明的保护范围之内。