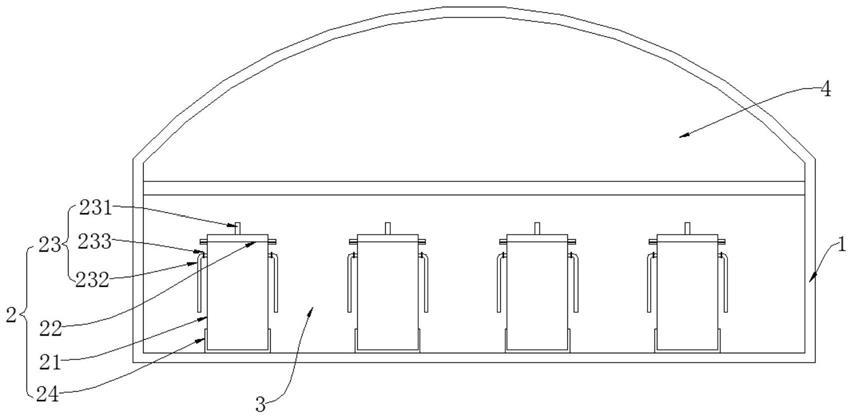
1.本实用新型涉及炭化设备技术领域,具体而言,涉及一种双气氛炭化装置。
背景技术:
2.有机固废包括农作物秸秆、林业固废、木业加工废弃物、养殖业粪污、生活垃圾,以及对环境不友好的危废等有机物;对有机固废进行科学化处置和资源化利用是建设无废城市的重点工作之一;有机固废具有固废分散、种类繁多、运输效率低等特点,处置难度较大;其中,对有机固废进行炭化是目前常见的处置工艺。
3.传统的炭化过程主要为将待炭化的有机固废放置于炭化罐内,通过燃料在炭化罐外部燃烧产生热量来对炭化罐进行加热,实现炭化罐内有机固废的炭化,炭化过程中需要耗费大量的燃料,经济性不高。
技术实现要素:
4.本实用新型解决的问题是目前有机物的炭化过程经济性不高和安全环保方面的麻烦。
5.为解决上述问题,本实用新型提供一种双气氛炭化装置,包括工业窑炉,以及至少一个设置于所述工业窑炉内的炭化箱;
6.所述炭化箱外部构成燃烧室;
7.所述炭化箱包括箱体、箱盖,以及将所述箱体与所述燃烧室连通的气体通道。
8.可选地,所述工业窑炉内设置有移动装置。
9.可选地,所述工业窑炉包括隧道窑或环形炉。
10.可选地,还包括与所述燃烧室相通的二次燃烧装置;所述二次燃烧装置上设置有气体入口以及燃料入口。
11.可选地,所述炭化箱还包括固定架,所述箱体与所述固定架滑动连接。
12.可选地,所述炭化箱的数量为多个;多个所述炭化箱于所述工业窑炉内呈单元式布置;呈单元式布置的多个所述炭化箱以多层多排组合的方式进行布置。
13.可选地,所述气体通道包括至少一个设置于所述箱盖上的气嘴。
14.可选地,所述气体通道还包括至少一个设置于所述箱体上的导气管。
15.可选地,所述导气管的一端连接于所述箱体的上部,另一端向靠近所述箱体的底部的方向延伸。
16.可选地,所述导气管通过快速接头与所述箱体相连。
17.与现有技术相比,本实用新型提供的双气氛炭化装置具有如下优势:
18.本实用新型提供的双气氛炭化装置,能够克服传统炭化工艺的不足,利用现有的工业窑炉,结合炭化箱,利用炭化过程中产生的气化气体的燃烧,实现对有机固废的炭化,不仅有利于减少燃料的使用,提高炭化过程的经济性,同时,还不单独占用工业用地,减少建设投资,降低成本;此外,通过与工业窑炉协同炭化,炭化的品质稳定,炭化彻底,可以得
到品质更高的炭。
附图说明
19.图1为本实用新型中双气氛炭化装置的结构简图;
20.图2为本实用新型中炭化箱的正视图;
21.图3为本实用新型中炭化箱的侧视图;
22.图4为本实用新型中呈单元式布置的炭化箱的结构简图。
23.附图标记说明:
[0024]1‑
工业窑炉;2
‑
炭化箱;21
‑
箱体;22
‑
箱盖;23
‑
气体通道;231
‑
气嘴;232
‑
导气管;2321
‑
通气孔;233
‑
快速接头;24
‑
固定架;241
‑
定位块;3
‑
燃烧室;4
‑
二燃室;5
‑
框架。
具体实施方式
[0025]
下面详细描述本实用新型的实施例,所述实施例的示例在附图中表示,其中自始至终相同或类似的标号表示相同或类似的元件或具有相同或类似功能的元件。下面通过参考附图描述的实施例是示例性的,旨在用于解释本实用新型,而不能理解为对本实用新型的限制,基于本实用新型的实施例,本领域普通技术人员在没有作出创造性劳动的前提下所获得的所有其他实施例,都属于本实用新型保护的范围。
[0026]
在本实用新型的描述中,需要理解的是,术语“中心”、“纵向”、“横向”、“长度”、“宽度”、“厚度”、“上”、“下”、“前”、“后”、“左”、“右”、“竖直”、“水平”、“顶”、“底”、“内”、“外”、“顺时针”、“逆时针”、“轴向”、“周向”、“径向”等指示的方位或位置关系为基于附图所示的方位或位置关系,仅是为了简化描述,而不是指示或暗示所指的装置或元件必须具有特定的方位、以特定的方位构造和操作,因此不能理解为对本实用新型的限制。
[0027]
此外,术语“第一”、“第二”仅用于简化描述,而不能理解为指示或暗示相对重要性,或隐含指明所指示的技术特征的数量。由此,限定为“第一”、“第二”的特征可以明示或者隐含地包括一个或者更多个该特征。在本实用新型的描述中,“多个”的含义是两个或两个以上,除非另有明确具体的限定。
[0028]
在本实用新型中,除非另有明确的规定和限定,第一特征在第一特征之“上”或之“下”,可以包括第一特征和第二特征直接接触,也可以包括第一特征和第二特征不是直接接触而是通过它们之间的另外的特征接触。而且,第一特征在第二特征“之上”、“上方”和“上面”包括第一特征在第二特征的正上方和斜上方,或仅仅表示第一特征水平高度高于第二特征。第一特征在第二特征“之下”、“下方”和“下面”包括第一特征在第二特征正下方和斜下方,或仅仅表示第一特征水平高度低于第二特征。
[0029]
为使本实用新型的上述目的、特征和优点能够更为明显易懂,下面结合附图对本实用新型的具体实施例做详细的说明。
[0030]
为解决目前有机固废的炭化过程经济性不高的问题,本实用新型提供一种双气氛炭化装置,参见图1所示,该双气氛炭化装置包括工业窑炉1,以及至少一个设置于工业窑炉1内的炭化箱2,炭化箱2内用于对有机固废提供缺氧气氛,实现无氧炭化;炭化箱2外部构成燃烧室3,即工业窑炉1的炉体内,相邻炭化箱2之间,以及炭化箱2与炉体内壁之间的空间,均为燃烧室3,燃烧室3内为有氧燃烧气氛;炭化箱2内用于存放待炭化的有机固废,通过燃
烧室内的燃烧产生的热量,来对炭化箱2进行加热,实现对炭化箱2内有机固废的炭化。
[0031]
具体的,参见图2、图3所示,本技术中的炭化箱2包括箱体21、箱盖22,以及将箱体21与燃烧室3连通的气体通道23。
[0032]
其中箱体21是炭化箱2的主体结构,该箱体21中具有放置有机固废的空腔;该箱体21的形状以及大小可根据有机固废的种类以及工业窑路1的形状及尺寸而定;本技术优选该箱体21为长方体结构,一方面便于导热,另一方面,便于将秸秆等有机固废经压缩打包后直接放置于该箱体21内,从而减少对有机固废进行破碎的步骤,简化炭化工序,提高炭化效率;该箱体21也可以为圆柱体结构,一方面便于对生活垃圾等有机固废进行炭化,另一方面便于将炭化箱2在工业窑炉1内进行布置。
[0033]
箱盖22用于在将待炭化的有机固废放置于箱体21中后,对箱体21内的空间进行密封;箱盖22的形状与箱体21的形状相适配;为便于开启与关闭,本技术优选箱盖22与箱体21采用扣盖式设计;由于有机固废在炭化过程中会产生气化气体,本技术进一步在炭化箱2中设置将箱体21与燃烧室3连通的气体通道23,随着炭化的进行,箱体21内的压力逐渐升高,当箱体21内的压力高于箱体21外侧燃烧室3内的压力时,箱体21内产生的气化气体从气体通道23喷出,进入燃烧室3,在燃烧室3内的高温环境下,喷出的气化气体在燃烧室3内直接燃烧,进而通过气化气体燃烧产生的热量来对炭化箱2进行加热,从而减少燃料的使用,提高炭化过程的经济性。
[0034]
本技术提供的双气氛炭化装置,通过炭化箱2与现有的工业窑炉1相结合,仅需要在炭化开始时,利用现有的工业窑炉1产生的烟气,或添加少量的燃料进行点火即可,在工业窑炉1内燃烧温度升高后,可通过炭化箱2内溢出的气化气体的燃烧来实现对炭化箱2的加热,从而在减少燃料使用、保证工业窑炉1正常生产的情况下,协同完成有机固废的炭化。
[0035]
该双气氛炭化装置工作过程中,首先对待炭化的有机固废进行打包压缩,将打包压缩后的有机固废放置于箱体21中,盖上箱盖22;利用工业窑炉1配套的载料小车等设备,将装有有机固废的炭化箱2放置于工业窑炉1内,在工业窑炉1现有的行走小车的带动下,使得该炭化箱2从工业窑炉1的入口进,经过一定距离的行走,从工业窑炉1的出口出货;其中炭化箱2在工业窑炉1内行走的距离根据工业窑炉1内的温度等而定,本技术优选该炭化箱2在工业窑炉1内行走的距离为140m~200m;炭化箱2在工业窑炉1内行走的过程中,工业窑炉1的不同位置具有不同的温度场,炭化箱2经过的温度整体趋势为首先从低到高,在该过程中炭化箱2内的有机固废进行充分炭化,然后温度再逐渐降低,进行降温;炭化箱2在工业窑炉1内行走的过程中,炭化箱2内的有机固废开始释放气化气体,使得炭化箱2内的压力逐渐升高,气化气体通过气体通道23进入燃烧室3内进行燃烧,进而通过燃烧进一步为炭化提供热量,提高炭化的效率以及炭化效果,直至炭化产生的气化气体烧尽,再经过梯度降温,使得从工业窑炉1中出来后,炭化箱2中的有机固废即转化为炭化好的炭化产品。
[0036]
本实用新型提供的双气氛炭化装置,能够克服传统炭化工艺的不足,利用现有的工业窑炉1,或者改造工业窑炉1,结合炭化箱2,利用炭化过程中产生的气化气体的燃烧,实现对有机固废的炭化,不仅有利于减少燃料的使用,提高炭化过程的经济性,同时,还不单独占用工业用地,减少建设投资,降低成本;此外,通过与工业窑炉1协同炭化,利用工业窑炉1自身不同位置处的温度场实现炭化,从而不需要通过额外的投资来建设并控制炭化过程所需要的温度场,并且炭化的品质稳定,炭化彻底,可以得到品质更高的炭。
[0037]
本实用新型提供的双气氛炭化装置,若原料为农作物秸秆、林业固废等,炭化后的产品为植物炭,可以直接用于炭肥还田,降低碳排放,也可继续深加工做成活性炭,进一步提升附加值;通过将炭化箱2设置于燃烧室3内,炭化过程中,产生的气体直接在燃烧室3内燃烧,并将燃烧产生的热量用于自身炭化加热,使得该炭化过程无煤气产生,从而能够避免炭化过程中产生二次污染。
[0038]
现有的炭化过程中,通常将炭化产生的煤气从双气氛炭化装置中引出后再加以利用;该过程中,在对煤气进行利用之前,需要通过相应的净化过程对煤气进行净化后,才能加以利用;并且,在将炭化产生的煤气引出、净化过程中,不可避免的会造成损耗,从而造成热损失,降低对热量的利用率;本技术通过将炭化过程中产生的气化气体直接燃烧的方法,在气化气体能源利用的方式上明显不同于传统炭化工艺,不需要另行建设气化气体的收集装置,不需要对煤气进行净化,也不需要燃烧器,通过气化气体直接自燃,给炭化箱2自身直接加热,安全简捷,热损失小,能效高,有利于在减小环保压力的同时,减小安全隐患。
[0039]
使用本实用新型提供的双气氛炭化装置进行炭化时,原料为压缩的秸秆等有机固废,产品为高品质的碳,无废水、废气、废渣产生,不对环境造成破坏,不增加环保压力。
[0040]
此外,由于本实用新型提供的双气氛炭化装置通过工业窑炉1与炭化箱2协同作用来实现炭化,炭化后产生的烟气通过工业自身的烟气出口进行排放或二次利用即可,不需要再单独设置烟气出口以及后续的烟气处理装置,一方面有利于减少排放,另一方面有利于减少建设投资。
[0041]
以有机固废为秸秆为例,对本实用新型提供的双气氛炭化装置进行说明;从物质守恒的角度,每3吨秸秆产出1吨碳,按照秸秆含水率15%计算,则炭化后的气体质量达到1.55吨,该部分气体直接经过燃烧,不仅可以气化水,其热量全部转化到工业窑炉1的烟气中,因此,在工业窑炉1与砖瓦和陶瓷等协同炭化过程中,不仅没有占用工业窑炉1的能源,还通过气化气体的燃烧补充了热量,使得砖瓦或陶瓷的烧制出料间隔时间有一定的缩短,因此,完全可以抵消炭化箱2在工业窑炉1内的占位,从而不影响工业窑炉1的生产效率。
[0042]
本技术中的工业窑炉1可以是内部设置有移动装置的任意结构形式的窑炉,以便于通过设置于工业窑炉1内的移动装置带动炭化箱2在工业窑炉1内移动,进而在移动过程中实现对炭化箱2内有机固废的炭化。
[0043]
本技术优选工业窑炉1包括隧道窑或环形炉,炭化过程中,可以通过将炭化箱2放置于隧道窑或环形炉内,单独进行炭化;也可以通过将炭化箱2与隧道窑或环形炉内原有的砖瓦、陶瓷等产品相间布置,使得炭化过程与隧道窑或环形炉原有的生产过程协同作用,在完成隧道窑或环形炉原有生产的基础上,实现炭化过程。
[0044]
为保证炭化过程的顺利进行,本技术进一步优选该双气氛炭化装置还包括与燃烧室3相通的二次燃烧装置,该二次燃烧装置上设置有用于补充氧气或空气的气体入口,以及用于补充燃料的燃料入口;炭化过程中,燃烧室3内未能充分燃烧的可燃气体进入二次燃烧装置内,同时,可以通过设置在二次燃烧装置上的气体入口向二次燃烧装置内补充适量的空气或氧气,以使未能充分燃烧的可燃气体在二次燃烧装置内进一步充分燃烧,避免产生二噁英等有毒有害气体;还可以将冷却段产生的热空气补充入二次燃烧装置内,以便于在补充氧气助燃的同时,提高热量的利用率;此外,在二次燃烧装置内温度较低时,还可通过燃料入口向二次燃烧装置内补充燃料,以保证气体在二次燃烧装置内充分燃烧。
[0045]
该二次燃烧装置可以是二燃室4,该二燃室4可以设置于工业窑炉1的外侧,也可以设置于工业窑炉1的腔室内;本技术优选该二燃室4设置于工业窑炉1的外侧;进一步的,二燃室4设置于工业窑炉1的外侧时,该二燃室4可以设置于工业窑炉1的上方,也可以设置于工业窑炉1的侧方。
[0046]
为便于理解,本技术以二燃室4设置于工业窑炉1的上方为例进行说明;二燃室4上设置有用于补充氧气或空气的气体入口,以及用于补充燃料的燃料入口,且二燃室4与工业窑炉1相通。
[0047]
具体的,本技术优选在工业窑炉1的顶板上设置有若干通孔(图中未示出),以便于使得燃烧室3内未能充分燃烧的可燃气体通过该通孔进入二燃室4内,同时,可以通过二燃室4上的气体入口向二燃室4内补充适量的空气或氧气,以使未能充分燃烧的可燃气体在二燃室4内进一步充分燃烧,避免产生二噁英等有毒有害气体;还可以将冷却段产生的热空气通过通孔补充入二燃室4内,以便于在补充氧气助燃的同时,提高热量的利用率;在二燃室4内温度较低时,还可通过燃料入口向二燃室4内补充燃料,以保证气体在二燃室4内充分燃烧。
[0048]
该二燃室4的具体形状可自行设计;为便于保温,本技术优选该二燃室4的顶部截面为圆形或椭圆形等拱形结构。
[0049]
为便于将炭化箱2推入工业窑炉1,或便于将炭化箱2从工业窑路1内拉出,本技术优选炭化箱2还包括固定架24,箱体21与固定架24滑动连接,从而通过箱体21在固定架24上的滑动,实现炭化箱2的推入与拉出。
[0050]
本技术优选该固定架24为钢制的框架结构,同时,该固定架24上装有与箱体21相适配的滑槽(图中未示出),以便于实现箱体21与固定架24的滑动连接。
[0051]
该固定架24可以仅与单个的炭化箱2相连,也可以通过一个固定架24来同时与两个或多个炭化箱2相连,以便于提高炭化箱2的稳定性。
[0052]
进一步的,本技术优选该固定架24上设置有定位块241,以便于通过该定位块241在推入时来对炭化箱2进行定位。
[0053]
炭化箱2的数量可根据需求进行设置;本技术优选炭化箱2的数量为多个;多个炭化箱2可以以单层、单排的方式进行布置,也可以以单层多排的方式进行布置,还可以以多层多排的方式进行布置;为提高炭化效率,本技术优选多个炭化箱2于工业窑炉1内呈单元式布置;呈单元式布置的多个炭化箱2以多层多排组合的方式进行布置。
[0054]
具体的,参见图4所示,为实现多个炭化箱2的单元式布置,本技术优选每一布置单元均包括一钢制的、具有多层的框架5,每一层上均布置有至少一排炭化箱2,本技术优选框架5的每一层上均布置有四排炭化箱2,形成如同抽屉式的布置方式;框架5的具体层数,以及每一层上炭化箱2的排数,即框架5的实际尺寸,可根据工业窑炉1的实际尺寸以及行走小车的实际尺寸进行设计。
[0055]
此外,为进一步提高稳定性,在两个或多个炭化箱2同层布置时,本技术进一步优选将相邻炭化箱2相连;具体连接方式,可选用铰链连接等现有的连接方式,本技术不对相邻炭化箱2之间的连接方式进行具体限定。
[0056]
进一步的,本技术优选炭化箱2上的气体通道23包括至少一个设置于箱盖22上的气嘴231,以便于通过该气嘴231将炭化箱2内受热过程中产生的气化气体排出。
[0057]
本技术优选该气嘴231为从箱盖22上伸出的管状结构;结合本技术中具有多层结构的框架5,多个炭化箱2于框架5上呈多层布置,位于下层的炭化箱2中产生的气化气体从箱盖22上的气嘴231喷出后,于喷嘴231出口附近进行燃烧,由于该喷嘴231贴近上一层的炭化箱2的底部,该燃烧过程中产生的热量,能够更好的对上一层的炭化箱2进行加热,从而有利于提高对热量利用率,提高炭化效率,进一步减少燃料的使用量。
[0058]
进一步的,本技术中炭化箱2上的气体通道23还包括至少一个设置于箱体21上的导气管232,以便于通过设置于导气管232将箱体21部位产生的气化气体引入燃烧室3中。
[0059]
本技术优选导气管232的一端连接于箱体21的上部,另一端向靠近箱体21的底部的方向延伸,即导气管232的另一端向靠近燃烧室3底部的方向延伸,以便于将气化气体引至燃烧室3的底部,利用燃烧室3底部较高的温度,使得引出的气化气体能够顺利的直接燃烧,释放热量。
[0060]
进一步的,本技术优选导气管232上设置有若干通气孔2321,以提高气化气体在燃烧室3内分布的均匀性,从而提高燃烧的均匀性,进而提高燃烧室3内热量分布的均匀性,提高炭化效率以及炭化质量。
[0061]
其中导气管232可以通过螺栓等紧固件与箱体21相连;由于工业窑炉1内温度较高,与降温后的温差较大,考虑温差变化引起的连接稳定性等问题,本技术优选导气管232通过快速接头233与箱体21相连,在提高连接稳定性与可靠性的同时,还降低对导气管232进行安装的难度;其中快速接头233可选用现有的快速接头,本技术不对快速接头233的具体结构形式进行限定。
[0062]
虽然本公开披露如上,但本公开的保护范围并非仅限于此。本领域技术人员,在不脱离本公开的精神和范围的前提下,可进行各种变更与修改,这些变更与修改均将落入本实用新型的保护范围。