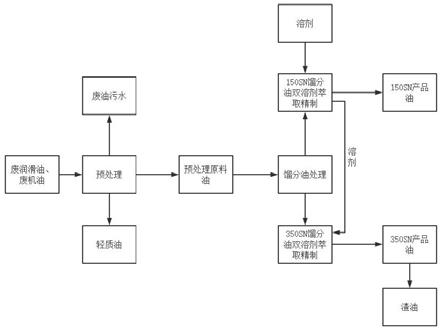
1.本发明涉及废油再生技术领域,具体地说,涉及一种废润滑油、机油的精制再生工艺。
背景技术:
2.润滑油种类繁多,特性和用途也各不相同,但所有的润滑油在使用过程中,由于受到各种污染和物理化学作用而逐渐老化变质,因此润滑油在使用一定期限后必须更换新油,这更换下来的油即为废矿物油。废矿物油属于有机石油烃类,不降解、有毒,故污染性较大,如果抛弃或处置不当,不仅浪费资源,而且对环境造成较大危害。大量的分析检测和众多的生产实践都证明了实际上废润油中真正的变质成分并不多,而且大多集中在极性化合物中,再生过程中如能将这些变质组分除去,就可生产高质量的基础油,采取与天然油同样的添加剂配方,就可以生产出高质量的润滑油品。
3.目前以各种废弃润滑油为原料循环再生炼制基础油工艺技术通常有“薄膜真空蒸馏和加氢精制”技术,“硫酸
‑
白土”技术、“拔头蒸馏—酸—石灰乳—白土”技术、“预处理—蒸馏—糠醛—白土”技术。薄膜真空蒸馏和加氢精制技术工艺投资大,设备技术复杂,而且需要具备更高品质的废油,实用性不佳;传统的硫酸白土技术不仅收率低、质量差,而且二次污染严重,目前已不允许应用到废弃润滑油为原料循环再生炼制基础油工艺,因此需要一种新的废弃润滑油为原料循环再生炼制基础油工艺。
技术实现要素:
4.本发明的目的在于提供一种废润滑油、机油的精制再生工艺,以解决上述背景技术中提出的问题。
5.一种废润滑油、机油的精制再生工艺,包含以下步骤:步骤一:将废油过滤,再进行预处理得到废油污水、预处理原料油和轻质油,废油污水进行去污处理;步骤二:将步骤一得到的预处理原料油馏分油得到150sn馏分油和350sn馏分油;步骤三:将步骤二得到的150sn馏分油双溶剂萃取得到150sn产品油;步骤四:将步骤二得到的350sn馏分油双溶剂萃取得到350sn产品油。
6.作为进一步优选,所述步骤一中的废油具体为废润滑油和废机油的一种。
7.作为进一步优选,所述步骤一中预处理的过程如下:s1:将废油加压通入原料换热器与馏分油回收塔中循环回流液换热升温;s2:将换热升温后的废油加热后进入闪蒸罐除去水分,闪蒸罐控制为负压;s3:将脱去水分的废油通入脱轻质油塔中真空加热脱去轻质油,得到预处理原料油和轻质油。
8.作为进一步优选,所述s2中废油和s3中脱轻质油塔均使用电加热,当产出轻质油后均使用轻质油作为加热源。
9.作为进一步优选,所述步骤二中馏分油的具体过程为将预处理原料油通过加热炉升温至340℃后放入馏分油回收塔真空操作,在馏分油回收塔的中上部抽出150sn馏分油,在馏分油塔下部抽出350sn馏分油。
10.作为进一步优选,所述步骤三中150sn馏分油双溶剂萃取过程如下:l1:将150sn馏分油与溶剂混合后通入150sn馏分油预分离器进行初分;l2:将150sn馏分油预分离器内初分后的150sn馏分油与溶剂混合物的上层物料缓冲后通入150sn馏分油萃取塔,150sn馏分油预分离器下层抽出液加压送入150sn抽出液冷却器中冷却后,进入150sn抽出液分离罐进行溶剂与油相的分离,油相与一次抽余液一并进入150sn萃取塔;l3:在150sn萃取塔下部完成溶剂对馏分油中芳烃、烯烃等杂质的萃取,将150sn馏分油萃取塔的上层抽出液经加压预热后送入溶剂回收塔进行少量溶剂回收,将回收溶剂后的150sn抽出液从溶剂回收塔下部抽出并加压后,以上部进料的方式送入150sn汽提塔进行汽提,经汽提后的150sn抽余液送入150sn脱气塔脱气冷却后得到150sn产品油;l4:150sn萃取塔底抽出液一部分去150sn馏分油预分离器,另一部分经脱轻塔脱轻后,进入再生塔再生,循环使用。
11.作为进一步优选,所述l1中溶剂具体为nmp和c9两种。
12.作为进一步优选,所述l3中溶剂回收塔为升降膜蒸发器的结构,且溶剂回收塔回收的溶剂会送入分离罐中,与分离罐中的溶剂集中回收。
13.作为进一步优选,所述步骤三中350sn馏分油双溶剂萃取过程如下:m1:将350sn馏分油送入刮膜蒸发器进行分离得到渣油与350油相;m2:刮膜蒸发器上部采出的350sn油相通入350sn精馏塔下部;m3:将精馏后的350油相与溶剂一起放入350sn预分离器进行油相初分,从350sn预分离器下部取出初分后溶剂加压冷却后通入入150sn分离罐;m4:将350sn预分离器上部的350sn一次抽余液送入350sn缓冲罐,再打入350sn萃取塔内完成溶剂对350sn馏分油中芳烃、烯烃等杂质的萃取,萃取完成后将350sn萃取塔底抽出液一部分回流到350sn预分离器;m5:将350sn预分离器顶部采出350sn二次抽余液通入缓冲罐后,再加压预热后进入350sn溶剂回收塔中进行350sn二次抽余液中的少量溶剂回收;m6:将350sn溶剂回收塔下部的采出液通入350sn釜液罐加压后通入350sn汽提塔进行汽提,再经350sn脱气塔脱气,回收热量后得到350sn产品油。
14.作为进一步优选,所述350sn馏分油双溶剂萃取使用的溶剂具体为nmp和c9,所述m5中350sn溶剂回收塔为升降膜蒸发器的结构。
15.作为进一步优选,所述m6中的回收热量用于m5中的余热。
16.作为进一步优选,150sn馏分油双溶剂萃取和350sn馏分油双溶剂萃取使用的溶剂相同且相互使用。
17.与现有技术相比,本发明的有益效果:1.再生基础油质量优良,可达到或接近天然石油基础油标准。
18.2.通过以废油通入脱轻质油塔中真空加热得到的轻质油作为加热源,实现的能源的综合利用,且不会产生废料。
19.3.产品收率高,通过以分油得到150sn馏分油和350sn馏分油,150sn馏分油和350sn馏分油分别进行双溶剂萃取,使得废润滑油中基础油成分得到充分的利用。
20.4.在双溶剂的回收循环利用中,采用了双效蒸发技术,即利用前级蒸发器的气相给下级蒸发器提供热源,与常用的一效蒸发相比,更能节约能源。
附图说明
21.图1为本发明工艺流程图;图2为本发明150sn馏分油双溶剂萃取工艺流程图;图3为本发明350sn馏分油双溶剂萃取工艺流程图。
具体实施方式
22.本发明公开了一种废润滑油、机油的精制再生工艺,以下通过具体实施例对本发明作进一步详述。
23.本实施例的废润滑油、机油的精制再生工艺,包含以下步骤:步骤一:将废油过滤,再进行预处理得到废油污水、预处理原料油和轻质油,废油污水进行去污处理;步骤二:将步骤一得到的预处理原料油馏分油得到150sn馏分油和350sn馏分油;步骤三:将步骤二得到的150sn馏分油双溶剂萃取得到150sn产品油;步骤四:将步骤二得到的350sn馏分油双溶剂萃取得到350sn产品油。
24.具体的,步骤一中的废油具体为废润滑油和废机油的一种。
25.本实施例中,步骤一中预处理的过程如下:s1:将废油加压通入原料换热器与馏分油回收塔中循环回流液换热升温;s2:将换热升温后的废油加热后进入闪蒸罐除去水分,闪蒸罐控制为负压;s3:将脱去水分的废油通入脱轻质油塔中真空加热脱去轻质油,得到预处理原料油和轻质油。
26.具体的,s2中废油和s3中脱轻质油塔均使用电加热,当产出轻质油后均使用轻质油作为加热源。
27.进一步的,步骤二中馏分油的具体过程为将预处理原料油通过加热炉升温至340℃后放入馏分油回收塔真空操作,在馏分油回收塔的中上部抽出150sn馏分油,在馏分油塔下部抽出350sn馏分油。
28.本实施例中,步骤三中150sn馏分油双溶剂萃取过程如下:l1:将150sn馏分油与溶剂混合后通入150sn馏分油预分离器进行初分;l2:将150sn馏分油预分离器内初分后的150sn馏分油与溶剂混合物的上层物料缓冲后通入150sn馏分油萃取塔,150sn馏分油预分离器下层抽出液加压送入150sn抽出液冷却器中冷却后,进入150sn抽出液分离罐进行溶剂与油相的分离,油相与一次抽余液一并进入150sn萃取塔;l3:在150sn萃取塔下部完成溶剂对馏分油中芳烃、烯烃等杂质的萃取,将150sn馏分油萃取塔的上层抽出液经加压预热后送入溶剂回收塔进行少量溶剂回收,将回收溶剂后的150sn抽出液从溶剂回收塔下部抽出并加压后,以上部进料的方式送入150sn汽提塔进行
汽提,经汽提后的150sn抽余液送入150sn脱气塔脱气冷却后得到150sn产品油;l4:150sn萃取塔底抽出液一部分去150sn馏分油预分离器,另一部分经脱轻塔脱轻后,进入再生塔再生,循环使用。
29.具体的,l1中溶剂具体为nmp和c9两种。
30.进一步的,l3中溶剂回收塔为升降膜蒸发器的结构,且溶剂回收塔回收的溶剂会送入分离罐中,与分离罐中的溶剂集中回收。
31.本实施例中,步骤三中350sn馏分油双溶剂萃取过程如下:m1:将350sn馏分油送入刮膜蒸发器进行分离得到渣油与350油相;m2:刮膜蒸发器上部采出的350sn油相通入350sn精馏塔下部;m3:将精馏后的350油相与溶剂一起放入350sn预分离器进行油相初分,从350sn预分离器下部取出初分后溶剂加压冷却后通入入150sn分离罐;m4:将350sn预分离器上部的350sn一次抽余液送入350sn缓冲罐,再打入350sn萃取塔内完成溶剂对350sn馏分油中芳烃、烯烃等杂质的萃取,萃取完成后将350sn萃取塔底抽出液一部分回流到350sn预分离器;m5:将350sn预分离器顶部采出350sn二次抽余液通入缓冲罐后,再加压预热后进入350sn溶剂回收塔中进行350sn二次抽余液中的少量溶剂回收;m6:将350sn溶剂回收塔下部的采出液通入350sn釜液罐加压后通入350sn汽提塔进行汽提,再经350sn脱气塔脱气,回收热量后得到350sn产品油。
32.具体的,350sn馏分油双溶剂萃取使用的溶剂具体为nmp和c9,m5中350sn溶剂回收塔为升降膜蒸发器的结构。
33.进一步的,m6中的回收热量用于m5中的余热。
34.以上显示和描述了本发明的基本原理、主要特征和本发明的优点。本行业的技术人员应该了解,本发明不受上述实施例的限制,上述实施例和说明书中描述的仅为本发明的优选例,并不用来限制本发明,在不脱离本发明精神和范围的前提下,本发明还会有各种变化和改进,这些变化和改进都落入要求保护的本发明范围内。本发明要求保护范围由所附的权利要求书及其等效物界定。