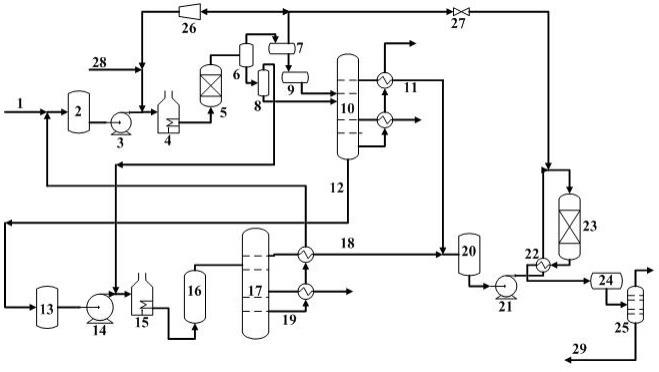
1.本发明属于石油炼制领域,具体地涉及一种渣油生产乙烯装置原料的系统及方法。
背景技术:
2.渣油作为原油中馏分最重、性质最差的部分,一直是炼油企业加工的难点。现阶段,大多企业的渣油加氢工艺均采用固定床渣油加氢技术,精制油为催化裂化装置提供原料。近年来,随着原油的重质化和劣质化,渣油中的残炭、重金属和沥青质等含量越来越高,大大增加了固定床渣油加氢装置的加工难度,而沸腾床渣油加氢技术由于催化剂处于流化状态,可在线置换,因此,可以处理性质更差的渣油原料。与固定床渣油加氢技术相比,具有原料油适应性广,运行周期长等特点。但各馏分的杂质含量仍然较高,需要后续加工处理才能作为最终产品或下游装置的合格进料。
3.目前,国外较成熟的沸腾床渣油加氢技术主要包括法国axens公司开发的h-oil工艺技术和美国chevron公司开发的lc-fining工艺技术。国内沸腾床渣油加氢技术经过多年的研究开发,现已进入工业化阶段。如中国石油化工股份有限公司抚顺石油化工研究院开发了strong沸腾床渣油加氢技术。该技术在2014年在金陵石化分公司的工业示范装置上首次进行工艺试验和长周期稳定考察,获得了理想的结果。同时,随着车用燃料市场日趋饱和,车用汽柴油年需求量增幅逐年降低,且国内炼油企业产能严重过剩,造成生产车用燃料的利润空间也越来越小,会严重影响沸腾床渣油加氢装置的效益。而乙烯装置、重整装置和合成氨等生产化工原料的装置原料一直存在较大缺口,严重制约了我国化工行业的发展。这些装置主要以石脑油为原料,如何增产合格石脑油是解决该问题的关键。
4.石油焦化(petroleum coking)加工过程也是重质油热转化过程之一。该技术以重质油为原料,在高温和长反应时间的条件下,进行深度热裂化和缩合反应,原料转化为气体、石脑油、柴油、蜡油和石油焦。石油焦化过程的原料几乎可以全部转化,并生成大量石油焦。石油焦化技术作为一种低成本的工艺技术,现广泛应用于各炼化企业。石油焦化过程主要包括延迟焦化、流化焦化和灵活焦化等等。
5.cn1087665a公开了一种由渣油制取乙烯原料油的方法,是用渣油经过焦化的热加工而得到的。渣油焦化后,大部分裂化成石脑油及轻柴油,一部分在焦化塔内缩合成焦炭,另一部分重组分则作为循环油。如使用石蜡基原油的渣油,焦化石脑油及轻柴油可以不需要精制而直接作为水蒸汽裂解的原料油。该方法采用单一焦化工艺技术,焦化蜡油循环操作,最大量生产石脑油和轻柴油,且采用较好的石蜡基原料时,石脑油才能直接作为乙烯装置的原料,对渣油原料适应性较差。
技术实现要素:
6.针对现有技术的不足,本发明提供了一种渣油生产乙烯装置原料的系统及方法,该系统可以将渣油生产为合格的乙烯装置原料,轻质油收率进一步提高,同时系统内的热
量得到充分利用,降低了能耗,减少了设备,经济性和环保性进一步增强。
7.本发明的渣油生产乙烯装置原料的系统,包括如下内容:沸腾床加氢反应区、焦化反应区和石脑油加氢反应区。
8.所述沸腾床加氢反应区包括沸腾床加氢单元、高低压分离单元、沸腾床分馏单元。
9.所述的沸腾床加氢单元一般包括原料缓冲罐i、进料泵i、加热炉i、沸腾床加氢反应器、供氢设备和相应管线;其中所述的供氢设备包括提供补充氢、循环氢的设备及相应管线;其中,原料缓冲罐i入口连接渣油原料管线,原料缓冲罐i出口经管线与进料泵i连接,进料泵i和供氢设备经管线与加热炉i入口连接,加热炉i出口经管线与沸腾床加氢反应器进料口连接;沸腾床加氢反应器出料口经管线与高低压分离单元连接;所述的高低压分离单元一般包括热高压分离器、热低压分离器、冷高压分离器、冷低压分离器及相应管线;其中热高压分离器入口经管线与沸腾床加氢反应器出料口连接,气相出口经管线与冷高压分离器入口连接,液相出口经管线与热低压分离器入口连接;热低压分离器轻质石油馏分出口经引出管线连接冷低压分离器入口管线,热低压分离器液相出口经管线与分馏塔入口连接;冷高压分离器气相出口经管线与供氢设备连接,冷高压分离器液相出口经管线与冷低压分离器入口连接;冷低压分离器出口经管线与沸腾床分馏单元原料入口连接;其中热低压分离器和冷低压分离器之间设置冷却设备,所述冷却设备为空气冷却器和水冷却器;冷低压分离器和沸腾床分馏单元之间设置换热设备或加热设备,用于将冷低压分离器分离出的液相物料的升温。
10.所述的沸腾床分馏单元包括分馏塔i及相应管线;分馏塔i塔底出口经管线与焦化反应区原料入口连接,蜡油馏分出口与蜡油排出管线连接,柴油馏分出口与柴油排出管线连接,石脑油馏分出口与石脑油加氢反应区进料管线连接。
11.焦化反应区包括焦化单元和焦化分馏单元;所述的焦化单元包括原料缓冲罐ii、进料泵ii、加热炉ii和焦炭塔;其中,原料缓冲罐ii入口经管线与分馏塔i塔底出口连接,原料缓冲罐ii出口经管线与进料泵ii连接,进料泵ii经管线与加热炉ii连接,加热炉ii经管线与焦炭塔入口连接。
12.所述的焦化分馏单元包括分馏塔ii及相应管线;其中,分馏塔ii入口经管线与焦炭塔顶部出口连接,焦化蜡油馏分出口与焦化蜡油排除管线连接,焦化柴油馏分出口与焦化柴油排出管线连接,焦化石脑油馏分出口与石脑油加氢反应区原料管线连接;其中,焦化蜡油排出管线可以与渣油原料管线连接或直接出系统。
13.所述的石脑油加氢反应区包括石脑油加氢单元、低压分离单元和汽提单元;所述的石脑油加氢单元包括原料缓冲罐iii、进料泵iii、加热炉iii或开工炉、石脑油加氢反应器和相应管线;原料缓冲罐iii入口经管线与石脑油加氢反应区进料管线连接,出口与进料泵iii入口连接,进料泵iii出口与加热炉iii或开工炉入口连接,加热炉iii或开工炉出口和沸腾床加氢单元的供氢设备经管线与石脑油加氢反应器入口连接,石脑油加氢反应器出口经低压分离单元连接汽提单元;所述的低压分离单元一般为冷低压分离器;所述的汽提单元一般为汽提塔,塔顶出口与酸性气排出管线连接,塔底出口与精制石脑油排出管线连接;其中精制石脑油作为乙烯装置进料。
14.本发明系统中,所述的沸腾床分馏单元,优选设置柴油换热设备和石脑油换热设备;蜡油馏分出口经管线依次与柴油换热设备、石脑油换热设备和蜡油排出管线连接,柴油
馏分出口经管线依次与柴油换热设备和柴油出系统管线连接,石脑油馏分出口经管线依次与石脑油换热设备和石脑油加氢反应区进料管线连接;所述的柴油换热设备用于蜡油馏分与柴油馏分的换热,石脑油换热设备用于石脑油与蜡油馏分的换热。
15.本发明系统中,所述的焦化分馏单元,优选设置焦化柴油换热设备和焦化石脑油换热设备;焦化蜡油馏分出口经管线依次与焦化柴油换热设备、焦化石脑油换热设备和焦化蜡油排出管线连接,焦化柴油馏分出口经管线依次与焦化柴油换热设备和焦化柴油排出管线连接,焦化石脑油馏分出口经管线依次与焦化石脑油换热设备和石脑油加氢反应区原料管线连接;焦化蜡油排出管线可以与渣油原料管线连接或直接出系统。所述的焦化柴油换热设备用于焦化蜡油馏分与焦化柴油馏分的换热,焦化石脑油换热设备用于焦化石脑油与焦化蜡油馏分的换热。根据上述设置,石脑油加氢单元可以取消加热炉iii或开工炉。
16.本发明系统中,石脑油加氢单元内的优选设置反应进料与出料之间的换热热备,充分利用反应单元的热量,减少热量损失。
17.本发明系统中,各反应区内的反应单元数量、规模以及各单元内的设备个数及可以根据实际需要进行设置,各反应区内的阀门和流量控制设置为本领域技术人员熟知。
18.本发明系统中,优选将沸腾床加氢反应区内的热低压分离器轻质石油馏分出口引出管线分两路,一路与焦化反应区内的进料泵ii与加热炉ii之间的管线连通,另一路经冷却设备与冷低压分离器入口连接。进一步优选取消热低压分离器轻质石油馏分出口与冷低压分离器入口之间的冷却设备,取消冷低压分离器液相出口与沸腾床分馏单元之间的换热或加热设备以及连接管线。
19.本发明的渣油生产乙烯装置原料的方法,包括如下内容:(1)沸腾床加氢反应区内,渣油原料和氢气在沸腾床加氢单元进行加氢反应,加氢反应生成油经高低压分离单元气液分离,液相进入沸腾床分馏单元进行分馏得到石脑油馏分(馏程范围40℃~230℃)、柴油馏分(馏程范围230℃~360℃)、蜡油馏分(馏程范围360℃~500℃)和未转化馏分(馏程范围大于500℃);(2)焦化反应区内,步骤(1)中的未转化馏分作为焦化原料在焦化单元进行焦化反应,焦化生成油进入焦化分馏单元进行分馏,得到焦化石脑油馏分(馏程范围40℃~240℃)、焦化柴油馏分(馏程范围240℃~370℃)和焦化蜡油馏分(馏程范围370℃~510℃);(3)石脑油加氢反应区内,步骤(1)得到的石脑油馏分、步骤(2)得到的焦化石脑油馏分和氢气在石脑油加氢单元内进行加氢精制反应,加氢精制油经汽提脱除h2s和nh3后,得到合格的乙烯装置原料。
20.本发明方法中,步骤(1)所述的渣油原料可以为常压渣油和/或减压渣油。
21.本发明方法中,步骤(1)所述的加氢反应条件为:反应温度410~440℃、反应压力16~20mpa、体积空速0.25~1.0h-1
。加氢反应中采用的催化剂为常用沸腾床渣油加氢催化剂,一般为圆柱条型或微球型,如抚顺石油化工研究院生产的fem-10、fzc-10、fzc-24或fzc-28等。
22.本发明方法中,步骤(1)中的加氢反应生成油在高低压分离单元中的一种分离过程如下:加氢反应生成油首先进入热高压分离器,气相进入冷高压分离器,液相进入热低压分离器,热低压分离器轻质石油馏分(馏程一般为40~300℃气相馏分)经过冷却设备冷却后进行入冷低压分离器,冷低压分离器得到的液相加热或换热后进入分馏单元,冷高压分离
气相作为富氢气体循环使用,液相进入冷低压分离器,冷低压分离器气相去酸性气脱硫单元,液相进入分馏单元。所述热高压分离器操作条件为:压力16~18mpa、温度300~400℃,优选350~400℃;热低压分离器操作条件为:压力2~3mpa,温度300~400℃,优选350~400℃;冷高压分离器操作条件为:压力16~18mpa、温度一般小于50℃;冷低压分离器操作条件为:压力2~3mpa,温度一般小于50℃。所述冷低压分离器得到的液相一般温度为40~50℃,需要加热或换热至240~250℃后进入分馏单元,所述的热低压分离器轻质石油馏分优选引出部分或全部与焦化原料进行混合,混合可以直接在管线重进行,或在混合器中进行,混合后进入加热炉ii。轻质石油馏分引出比例可以根据实际需要进行调整。所述的热低压分离器轻质石油馏分优选引出部分(小于80%)时,冷低压分离器分离得到的液相量减少,可以降低换热或加热设备的负荷,当引出部分超过80%(如全部引出)时,可以取消换热或加热设备,液相直接进入分馏单元。这是由于冷低压分离器的液相来源于冷高压分离器的液相组分和热低压分离器的气相组分,当热低压分离器将轻质石油馏分引出大部分时,冷低压分离器中的液相生成量减少,可以不需加热直接进入分馏单元。
23.本发明方法中,步骤(1)所述的柴油馏分、蜡油馏分可以直接出系统。
24.本发明方法中,步骤(2)所述的焦化反应一般在焦炭塔内进行,焦化原料进入焦炭塔前,经加热炉ii加热至反应温度,焦化反应条件为:反应温度为480~530℃,焦炭塔压力0.1~0.3mpa,循环比0~1,注水量1%~2%。优选焦化原料进入加热炉ii前,先与步骤(1)中的热低压分离器分离出的轻质石油馏分混合;焦化反应条件为:反应温度为480~530℃,焦炭塔压力0.1~0.3mpa,循环比0~1,无须注水。
25.本发明方法中,步骤(2)所述的焦化蜡油优选进入沸腾床加氢反应区与渣油原料混合,进行加氢反应。
26.本发明方法中,步骤(3)所述的加氢精制反应条件为:反应压力一般为0.5~6.0mpa,最好为2.0~4.0mpa,反应压力可根据进料泵适当调节,以满足反应需要;反应温度为150~350℃,最好为200~280℃;体积空速为1.0~10.0h-1
,最好为2.0~6.0 h-1
;氢油体积比为100~800:1,最好在250~500:1。
27.本发明方法中,步骤(3)使用的加氢精制催化剂可以是商品加氢精制催化剂,可以采用氧化态或硫化态催化剂,优选硫化态催化剂,如以钼镍、钨镍或钨钼镍三组分为活性组分的硫化态加氢精制催化剂,此类催化剂具有较高的加氢活性,可以在相地较缓和的条件下进行烯烃加氢反应。优选采用钨钼镍三组分为活性组分的加氢精制催化剂,如抚顺石油化工研究院研制生产的fh-40c高活性加氢催化剂。加氢精制催化剂一般以氧化铝为载体,以w-mo-ni为活性组分,活性组分以重量计在催化剂中的含量不小于16%,一般为16%~30%。在使用前无需再对催化剂进行预硫化,加氢后精制石脑油烯烃含量小于1%,满足乙烯装置的进料指标要求。
28.本发明将沸腾床工艺和焦化工艺进行巧妙的结合,以渣油为原料生产满足乙烯装置合格的进料。该系统及方法具有很好的灵活性不会因为原料油性质的变化影响精制石脑油(乙烯装置进料)的性质,在此基础上提高了精制石脑油收率,特别适合作为乙烯装置的原料。
29.首先,将沸腾床反应区的热低压分离器内的轻质石油馏分引出部分或全部以气相形式与焦化原料进行预先混合,该部分馏分的温度为350~400℃,并且与焦化原料油具有良
好的互溶性,能够均匀地提高原料油温度,降低加热炉ii能耗,同时由于混合后原料油温度的升高,减小了加热炉管之间的温度差(即减弱了原料油的分子动能),减弱了原料油与热炉管之间热裂解效应,而不易结焦的轻质石油馏分提高原料油在加热炉管内轴向流速的同时,在径向方向也降低了原料油与管壁的直接接触机率,上述共同作用,减缓结焦速度。其次,混有轻质石油馏分的原料油在进入焦炭塔后,能够及时带走焦化反应得到的轻组分,减少了其停留时间,避免了轻组分的过度热裂解等副反应,提高了轻质油收率。
30.来自热低压分离器的轻质石油馏分不需要进入冷低压分离器,所以可以省掉二者之间的冷却设备(空气冷却器和水冷却器)。该轻质石油馏分的分馏过程由“需要加热至240~250℃进入沸腾床分馏单元转移至不需要加热直接进入焦化分馏单元,避免了该轻质石油馏分被冷却后再加热的2次能量浪费。
31.本发明系统在完成上述生产任务的基础上,将各反应区内的热量进行了充分利用,相比于单独的沸腾床工艺、焦化工艺及石脑油加氢工艺,降低了能耗和减少了设备。首先,沸腾床反应区内的石脑油和焦化反应内的焦化石脑油对各自反应区内的蜡油进行充分取热,由于沸腾床得到的石脑油中烯烃含量较低(通常低于10wt%),与焦化石脑油混合后,反应热能够满足装置内反应的需要,因此石脑油反应区在不设置加热炉的情况下,也可以满足产品质量要求和长周期稳定运行。如果沸腾床反应区内的石脑油和焦化反应内的焦化石脑油不进行取热操作,进入石脑油反应区,由于石脑油加氢单元会产生较多反应热,可以与混合石脑油原料换热,达到或接近反应所需温度,因此也仅需要设置开工炉或低负荷的加热炉。石脑油加氢单元所需氢气由部分沸腾床反应区内的循环氢经减压后获得,无需设置新氢压缩机和循环氢压缩机。
附图说明
32.图1为本发明方法一种具体流程示意图。
33.图2为本发明方法第二种具体流程示意图。
34.其中:1-渣油原料,2-原料油缓冲罐i,3-进料泵i,4-加热炉i,5-沸腾床加氢反应器,6-热高压分离器,7-冷高压分离器,8-热低压分离器,9-冷低压分离器,10-分馏塔i,11-石脑油,12-未转化油,13-原料油缓冲罐ii,14-进料泵ii,15加热炉ii,16-焦炭塔,17-分馏塔ii,18-焦化石脑油,19-焦化蜡油,20-原料油缓冲罐iii,21-进料泵iii,22-换热器,23-石脑油加氢反应器,24-低压分离器,25-汽提塔,26-循环氢压缩机,27-减压阀,28-补充氢,29-精制石脑油。
具体实施方式
35.下面结合附图和具体实施例对本发明方法进行详细的描述。
36.如图1所示,本发明的渣油生产乙烯装置原料的一种实现方式:在沸腾床加氢反应区,渣油原料1经过原料缓冲罐i 2和进料泵i 3,与氢气混合后在加热炉i 加热后进入沸腾床加氢反应器5,生成油经分离,进入分馏塔i10进行分馏,富氢气体在冷高压分离器7分离后,经循环氢压缩机26循环使用,得到石脑油11,塔底未转化油12进入焦化反应区的原料油缓冲罐ii13,经过进料泵ii14与沸腾床加氢反应区的热低压分离器8的轻质馏分油混合后,进入加热炉ii15和焦炭塔16,塔顶液体产品进入分馏塔ii17,得到焦化石脑油18,焦化蜡油
19返回沸腾床渣油加氢装置与渣油原料1混合,作为稀释油,焦化石脑油18与石脑油11混合后,进入原料油缓冲罐iii 20,经过进料泵21升压后,与换热器22换热,达到反应所需温度后,冷高压分离器7分离部分氢气经减压阀27与石脑油混合,进入石脑油加氢反应器23进行加氢精制反应,精制油经低压分离器24进入汽提塔25,汽提塔底精制石脑油29为合格的乙烯装置进料。焦化汽油18和石脑油11分别与本单元生产的蜡油换热后混合,再与石脑油加氢单元精制石脑油换热,可以达到加氢反应所需的温度,因此,石脑油加氢单元可以不设置加热炉或开工炉如图2所示,本发明的渣油生产乙烯装置原料的第二种实现方式:渣油原料1经过原料缓冲罐i 2和进料泵i 3,与氢气混合后在加热炉i 加热后进入沸腾床加氢反应器5,生成油进入热高压分离器6,气相进入冷高压分离器7分离后,经循环氢压缩机26循环使用,液相进入热低压分离器8,热低压分离器8轻质馏分油经过冷却设备冷却后进行入冷低压分离器9,液相进入分馏塔i10进行分馏,得到石脑油11,塔底未转化油12进入焦化反应区的原料油缓冲罐ii13,经过进料泵ii14后,需注入的水量约占进料重量的1.5%,进入加热炉ii15和焦炭塔16,塔顶液体产品进入分馏塔ii17,得到焦化石脑油18,焦化蜡油19返回沸腾床渣油加氢装置与渣油原料1混合,作为稀释油,焦化石脑油18与石脑油11混合后,进入原料油缓冲罐iii 20,经过进料泵21升压后,与换热器22换热,达到反应所需温度后,冷高压分离器7分离部分氢气经减压阀27与石脑油混合,进入石脑油加氢反应器23进行加氢精制反应,精制油经低压分离器24进入汽提塔25,汽提塔底精制石脑油29为合格的乙烯装置进料。经过本发明系统及方法得到的精制石脑油,产品可以达到如下性质:精制油烯烃含量小于1%,链烷烃含量较高,其他性质均满足乙烯装置对原料油的要求。
37.下面的实施例将对本发明作进一步说明。
38.实验使用催化剂为工业应用的加氢处理催化剂,为抚顺石油化工研究院研制生产的硫化态fh-40c加氢催化剂,其理化性质指标见表1。本发明实施例及对比例中的沸腾床加氢反应条件为:反应温度427℃、反应压力16.8mpa、体积空速0.30h-1
催化剂为fem-10;焦化反应条件为:反应温度为496℃,焦炭塔压力0.15mpa,循环比0.3,注水量1.6%,实施例及对比例涉及的百分含量均为质量百分含量。
39.实施例1按照图1的工艺流程,以渣油原料1为原料油(性质见表2),热低压分离器引出全部轻质油馏分(温度为350~400℃)与焦化原料(温度为一般为常温)混合后,经加热炉加热至焦化反应温度进入焦炭塔;沸腾床加氢反应区的石脑油与焦化反应区的石脑油混合后,温度为220℃,进入石脑油加氢单元,反应条件为:反应压力2.8mpa﹑体积空速3.0h-1
、反应器入口温度237℃,氢油体积比280。产品性质列于表3。焦化反应单元的加热炉前取消注水。热低压分离器和冷低压分离器之间不设置冷却设备。冷低压分离器和分馏单元之间不设置加热设备。石脑油加氢单元不设置加热炉和开工炉。
40.实施例2按照图2的工艺流程,以渣油原料2(性质见表2)为原料油,热低压分离器引出全部轻质油馏分进入冷却设备冷却40℃,进入冷低压分离器,冷低压分离器分离得到的液相温度为40℃经换热器加热245℃,进入沸腾床分馏塔;
沸腾床渣油加氢反应区的石脑油与焦化反应区的石脑油混合后温度为215℃,进入石脑油加氢单元,反应条件为:反应压力3.5mpa﹑体积空速2.6h-1
、反应器入口温度233℃,氢油体积比310。热低压分离器和冷低压分离器之间设置冷却设备。冷低压分离器和分馏单元之间设置加热设备。石脑油加氢单元不设置加热炉和开工炉。产品性质列于表3。
41.比较例1采用渣油原料1,采用沸腾床加氢工艺(同实施例2)和石脑油加氢工艺简单组合(即原料经沸腾床加氢工艺处理后,得到的石脑油馏分直接进入石脑油加氢精制)。沸腾床石脑油原料进入石脑油加氢反应区的温度为36℃,石脑油加氢单元设置加热炉,设置新氢压缩机和循环氢压缩机,石脑油收率为10.1%。
42.比较例2采用渣油原料1,采用焦化工艺(同实施例2)和石脑油加氢工艺组合(即原料经焦化工艺处理后,得到的石脑油馏分直接进入石脑油加氢精制),焦化石脑油原料进入石脑油加氢反应区的温度为33℃,石脑油加氢单元设置加热炉,新氢压缩机和循环氢压缩机,石脑油收率为16.2%。
43.表1 催化剂的理化性质指标表2 原料油性质表3 实施例产品性质
本发明的渣油生产乙烯装置原料的系统及方法,相比于对比例最大限度的利用了系统中各部分的能量,减少了设备,降低了焦化反应对轻质油的裂解,提高了整体的轻质油收率,进一步实施例1相比与实施例2,减少设备、降低能耗的同时,焦化反应区的加热炉的清焦周期也得到了延长。