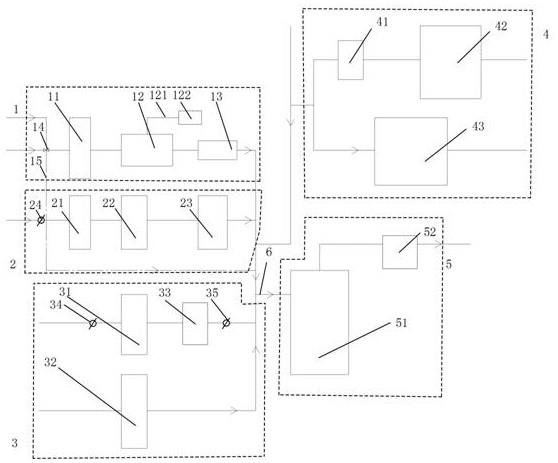
1.本实用新型涉及石油炼化裂化装置技术领域,具体涉及一种加氢裂化尾气回收利用系统。
背景技术:
2.在石油加氢裂化的生产过程中,会产生大量的含氢尾气和含烃尾气,以往各装置燃料气系统单独设立,装置自产的干气和低分气单独并入各自装置燃料系统,多余排至火炬,然而这种处理方式效率低,不稳定,不能够充分利用尾气,另有其他装置燃烧外购天然气,造成多余干气和低分气浪费。
技术实现要素:
3.本实用新型的目的就是针对现有技术存在的缺陷,提供一种加氢裂化尾气回收利用系统。
4.本实用新型的技术方案是:
5.加氢裂化尾气回收利用系统,包括低分气提氢单元、裂化除硫单元、裂化液化气处理单元、改质干气处理单元、燃料气处理单元和燃料气管线,所述低分气提氢单元、裂化除硫单元、裂化液化气处理单元和改质干气处理单元的尾气出口并联设置并与所述燃料气管线连通,所述燃料气管线的出口端与所述燃料气处理单元连通;
6.所述燃料气处理单元包括燃料气处理单元分液罐和加氢裂化燃烧炉,所述燃料气处理单元分液罐的入口与所述燃料气管线连接且出口与所述加氢裂化燃烧炉连接。
7.优选的,所述低分气提氢单元包括依次通过管线串联的除油罐、提氢吸附塔和吸气压缩机;
8.所述除油罐与生产线上游的加氢裂化装置连接,所述提氢吸附塔设置有氢气出料管并与外部氢气储罐连通,所述吸气压缩机的出料管与所述燃料气管线连通。
9.优选的,所述除油罐的入口处设置有三通的跨线阀,所述跨线阀的一侧设置有尾气跨线的支线,所述尾气跨线的出口端与所述燃料气管线连通。
10.优选的,所述裂化除硫单元包括依次通过管线串联的含硫干气冷却器、含硫干气分液罐、除硫单元脱硫塔和脱硫干气分液罐,所述脱硫干气分液罐的出料管与所述燃料气管线连通。
11.优选的,所述裂化液化气处理单元包括液化气汽化器、液化气脱硫塔、液态烃聚结器、脱硫前液化气水冷器和液化气冷却器,所述液化气脱硫塔、液态烃聚结器、脱硫前液化气水冷器和液化气冷却器依次通过管线连接,所述液化气冷却器的出料管与所述燃料气管线连通;
12.所述液化气冷却器设置有一条支线并与所述液化气汽化器连通,所述液化气汽化器的出料管与所述燃料气管线连通。
13.优选的,所述改质干气处理单元包括干气分液罐、改质干气单元脱硫塔和改质干
气单元燃料气分液罐,所述干气分液罐和改质干气单元脱硫塔依次通过管线串联,所述干气分液罐的出料管与所述燃料气管线连通;
14.所述干气分液罐设置有回流支线并与所述改质干气单元燃料气分液罐连通。
15.本实用新型与现有技术相比较,具有以下优点:
16.本系统将加氢裂化多个装置的尾气汇集并统一处理,可以有效地降低尾气处理成本且利用尾气中的有效成分进行二次利用,同时通过对不稳定的尾气进行统一收集和统一处理,可以有效的提高利用效率,将尾气转换为可供利用的优质资源,节能环保,降低消耗和成本。
附图说明
17.图1为本实用新型的结构示意图;
18.图中:1
‑
低分气提氢单元,2
‑
裂化除硫单元,3
‑
裂化液化气处理单元,4
‑
改质干气处理单元,5
‑
燃料气处理单元,6
‑
燃料气管线;
19.11
‑
除油罐,12
‑
提氢吸附塔,121
‑
氢气出料管,122
‑
氢气储罐,13
‑
吸气压缩机,14
‑
跨线阀,15
‑
尾气跨线,21
‑
含硫干气分液罐,22
‑
除硫单元脱硫塔,23
‑
脱硫干气分液罐,24
‑
含硫干气冷却器,31
‑
液化气脱硫塔,32
‑
液化气汽化器,33
‑
液态烃聚结器,34
‑
脱硫前液化气水冷器,35
‑
液化气冷却器,41
‑
干气分液罐,42
‑
改质干气单元脱硫塔,43
‑
改质干气单元燃料气分液罐,51
‑
燃料气处理单元分液罐,52
‑
加氢裂化燃烧炉。
具体实施方式
20.以下将以图式揭露本实用新型的多个实施方式,为明确说明起见,许多实务上的细节将在以下叙述中一并说明。然而,应了解到,这些实务上的细节不应用以限制本实用新型。也就是说,在本实用新型的部分实施方式中,这些实务上的细节是非必要的。此外,为简化图式起见,一些习知惯用的结构与组件在图式中将以简单的示意的方式绘示之。
21.实施例一
22.参照图1所示,加氢裂化尾气回收利用系统,包括低分气提氢单元1、裂化除硫单元2、裂化液化气处理单元3、改质干气处理单元4、燃料气处理单元5和燃料气管线6,低分气提氢单元1、裂化除硫单元2、裂化液化气处理单元3和改质干气处理单元4并联设置以进行尾气的前期的汇集和初步处理,然后通过燃料气管线6通入燃料气处理单元5,该系统可以将裂化炼化装置生产过程产生的尾气进行统一收集处理,提高了原料的利用率,降低了生产的成本。
23.燃料气处理单元5包括串联的燃料气处理单元分液罐51和加氢裂化燃烧炉52,各个单元通过燃料气管线6输送过来的燃料气进入燃料气处理单元分液罐51进行分液然后通入加氢裂化燃烧炉52进行燃烧处理,从而对尾气进行再次利用,降低了能源的消耗同时也避免了对环境的污染。
24.实施例二
25.参照图1所示,与实施例一基本相同,所不同在于,自加氢裂化和加氢改质来的脱硫后低分气进入低分气提氢单元1,气体依次通过除油罐11,缓冲后进入提氢吸附塔12,在多层吸附剂的选择吸附下,全部脱除其中的杂质,得到纯度大于99.99%的产品氢气送出界
区,做到氢气回收,资源利用,节能降耗。吸附剂中吸附的杂质组分及部分氢气通过顺放气罐中氢气冲洗解吸后,经低分气解吸气压缩机13升压至0.45mpa送往燃料气管线6。
26.虚线:如果低分气提氢单元1停止使用时,加氢裂化和加氢改质装置产的低分气(含有95%氢气)通过跨线阀14和尾气跨线15直接进入燃料气管线6。
27.加氢裂化主汽提塔顶回流罐和脱丁烷塔顶回流罐排放气混合并进入裂化除硫单元2,流体经含硫干气冷却器24冷却至40℃后进入含硫干气分液罐21分液,分液后气体进入除硫单元脱硫塔22与塔顶贫液逆流接触,脱除硫化氢,脱硫后干气自塔顶经脱硫干气分液罐23分液后送往燃料气管线6。
28.实施例三
29.参照图1所示,与实施例一基本相同,所不同在于,加氢裂化液化气自脱丁烷塔回流罐流入裂化液化气处理单元3,流体进入(e1302)脱硫前液化气水冷器34进行冷却,然后经过液化气脱硫塔31、液态烃聚结器33进入液化气冷却器35,然后分两路,一路送往燃料气管线6;另一路送入液化气汽化器32,处理后送往燃料气管线6。
30.自加氢改质主汽提塔顶回流罐的高压富液罐顶混合气体送入改质干气处理单元4,气体送入改质干气单元脱硫塔42进行脱硫,脱硫后的干气经脱后干气分液罐41分液后至燃料气管线6;当加氢改质自产干气停止并入燃料气管线6时直接经过改质干气单元燃料气分液罐43至加氢改质装置各个炉子燃烧。
31.本实用新型并不限于上述的实施方式,在本领域技术人员所具备的知识范围内,还可以在不脱离本实用新型宗旨的前提下做出各种变化,变化后的内容仍属于本实用新型的保护范围。