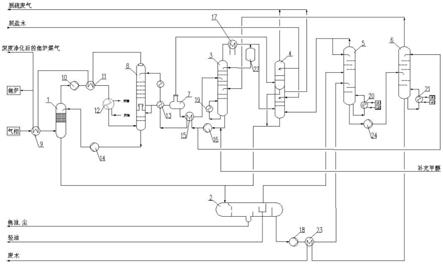
1.本实用新型涉及焦炉煤气净化技术领域,尤其涉及一种焦炉煤气的深度净化系统。
背景技术:
2.焦炉煤气是炼焦过程中得到的重要副产品,近些年对焦炉煤气的组成成分的研究已经相当成熟。焦炉煤气属于中热值然气,氢气含量50%~60%,甲烷 22%~24%,其中包含巨大的利用价值。在生产焦炭的同时会产生大量焦炉煤气,如果按照生产1吨焦炭产生430立方米的焦炉煤气计算,我国全年焦炉煤气发生量基本维持在1800亿立方米,其中45
‑
50%左右的焦炉煤气返回焦炉,剩余的焦炉煤气相当于国家“西气东输”设计年输气量的2倍以上。因此,如何回收利用好焦炉煤气对实现资源的循环利用和经济的可持续发展具有重要意义。在焦炉煤气综合利用之前焦炉煤气的净化就成了重中之重。在焦炉煤气综合利用之前焦炉煤气的净化就成了重中之重,而焦炉煤气净化中的核心问题就是脱硫。
3.目前,焦炉煤气常用的脱硫方法为干法脱硫和湿法脱硫。干法脱硫主要是利用氢氧化铁与其他制剂合成的脱硫催化剂脱除煤气中的h2s,经过再生的脱硫剂可重新使用。干法脱硫主要应用于气量较小的焦炉煤气脱硫或脱硫精度高的二次脱硫。湿法脱硫工艺是利用液体脱硫剂脱除焦炉煤气中的h2s和hcn,目前常用的湿法脱硫有改良ada法、萘醌法、胶法、frc法、th法、hpf法、 pds法、opt法、络合铁法、氨水催化法。规模较大焦化企业通常采用湿法脱硫。湿法脱硫过程中,为了避免脱硫废液中副反应盐类累积,会排出少量废液。以前采取的措施是将排出的脱硫废液送入配煤系统,但这种方式会产生环保问题,污染环境。
4.伴随着新环保政策的出台,脱硫废液的处理已经成为焦化行业一大难题,至今国内尚未形成较为完整、经济又环保的脱硫废液处理方法。综上,焦炉煤气脱硫面临着干法脱硫投资、成本过高,不能适应焦炉煤气规模化的要求,而传统湿法脱硫存在废液无法处理的难题。另外,目前焦炉煤气在深度净化过程中,还存在对脱硫、脱萘等精度不够,不能保证后续装置的安
‑
稳
‑
常
‑
满
‑
优运行。主要表现在以下三个方面:
5.(1)深度净化后的焦炉煤气含硫、氨超标,影响后续净化及合成的正常运行。
6.一般焦炉煤气只是作为燃料气来使用时,要求h2s低于500mg/nm3,氨含量低于100mg/nm3,但实际运行中酸气和氨时有超标现象,影响后系统稳定运行。随着焦化规模扩大,产业集聚化,焦炉煤气成为重要的化工原料气来使用,焦炉煤气用途的改变,就造成了原焦炉煤气深度净化的设计指标远不能满足现使用指标要求。
7.(2)深度净化后的焦炉煤气含焦油和萘严重影响压缩机正常运行,主要原因是焦炉煤气夹带焦油、萘含量高,压缩时气温升高焦油气化结焦;以及萘冷凝结晶,造成压缩机萘堵,使压缩机无法正常运行,被迫停修,有时仅开1
‑
2 天就要停车抢修,使生产十分被动,往往都是1开2备或1开3备的局面。
8.(3)由于粗脱硫不正常造成精脱硫的脱硫剂提前失效,影响生产操作,主要是硫穿透,被迫提前更换脱硫剂,由此发生的脱硫剂更换频繁,运行费用增加。
技术实现要素:
9.为解决目前焦炉煤气在深度净化过程中存在会影响后系统稳定运行、会造成压缩机堵塞及会造成精脱硫的脱硫剂提前失效而增加运行费用的技术问题,本实用新型提供一种焦炉煤气的深度净化系统。
10.为解决上述技术问题,本实用新型采用的技术方案是:
11.一种焦炉煤气的深度净化系统,其包括预洗塔、脱硫塔、热再生塔、水洗塔、共沸塔、甲醇水分离塔、富甲醇闪蒸槽和四相分离器,所述预洗塔为超重力旋转装置,四相分离器为卧式三堰型气
‑
液
‑
液
‑
液分离器,其中:气柜经第一换热器与预洗塔下部的气相进口连接,预洗塔底部的液相出口与四相分离器的进料口连接,预洗塔的气体出口经第一压缩机、第二换热器和第三换热器与脱硫塔下部的进气口连接,脱硫塔顶部的出气口与第二换热器连接,脱硫塔底部的出液口经第二压缩机与预洗塔上部的液相进口连接,脱硫塔中下部的出液口经第四换热器与富甲醇闪蒸槽的进液口连接,富甲醇闪蒸槽顶部的出气口与水洗塔中上部的进气口连接,水洗塔顶部的出气口与脱硫废气管道连接,富甲醇闪蒸槽底部的出液口经第五换热器与热再生塔中上部的进液口连接,热再生塔底部的出液口经第三压缩机和第五换热器与脱硫塔上部的进液口连接,热再生塔顶部的出气口经第六换热器与水洗塔下部的进气口连接,第六换热器连接冷凝液储罐的进液口,冷凝液储罐的出液口与热再生塔上部的进液口连接,水洗塔底部的出液口与四相分离器的进料口连接,四相分离器的气相出口与共沸塔中部的进气口连接,四相分离器的重相流体出口与重油管道连接,四相分离器的轻相流体出口与轻油管道连接,四相分离器的中间相流体出口经第四压缩机和第七换热器与共沸塔中部的进液口连接,共沸塔顶部的出气口与水洗塔下部的进气口连接,共沸塔底部的出液口经第五压缩机与甲醇水分离塔中部的进液口连接,甲醇水分离塔顶部的出气口与热再生塔中部的进气口连接,甲醇水分离塔底部的出液口与第七换热器连接。
12.可选地,所述预洗塔包括传动装置、转轴和预洗壳体,传动装置与转轴一端连接,转轴另一端连接有转子,转子设于预洗壳体内腔的中下部,预洗壳体的顶部中间连接有气体出口,预洗壳体的底部连接有液相出口,预洗壳体的一侧底部连接有气相进口,预洗壳体的另一侧中上部连接有液相进口,液相进口连接有l形液体管道,l形液体管道的竖直管延伸至转子中部,l形液体管道的竖直管上安装有若干个液相喷嘴,预洗壳体内腔的顶部设有除沫器,除沫器底部与转子顶部之间安装有分隔板,转子顶部中间与分隔板之间通过第一密封垫密封,转子底部中间两侧与转轴之间分别通过第二密封垫和第三密封垫密封,转子内部填充有填料层。
13.可选地,所述四相分离器包括分离壳体,分离壳体内腔从左至右分为入口段ⅰ、沉降分离段ⅱ和采集段ⅲ;
14.所述入口段ⅰ设置有气液分离器、挡板和镇静板,进料口设于分离壳体外部并与分离壳体顶部连接,气液分离器安装于进料口下面,镇静板底端与分离壳体底部连接,挡板顶端与分离壳体顶部连接并位于气液分离器和镇静板之间;所述沉降分离段ⅱ安装有聚结器;所述采集段ⅲ设置有重相流体溢流堰、重相流体收集槽、轻相流体收集槽和中间相流体溢流堰,重相流体溢流堰设置于聚结器一侧并与分离壳体底部连接,重相流体收集槽顶端与分离壳体底部连接并位于聚结器与重相流体溢流堰之间,重相流体收集槽侧壁的顶部和底部各安装有一个第一液位计,重相流体收集槽底部连接有重相流体出口,重相流体收集
槽上方的分离壳体顶部和底部各安装有一个第二液位计,轻相流体收集槽设置于重相流体溢流堰一侧,轻相流体收集槽的前墙为轻相流体溢流堰,轻相流体溢流堰的高度低于轻相流体收集槽的后墙的高度,轻相流体收集槽内的顶部和底部各设有一个第三液位计,轻相流体收集槽底部连接有轻相流体出口,轻相流体出口位于分离壳体外部,轻相流体收集槽上方设置有除雾器,气相出口设于分离壳体外面并与除雾器连接,中间相流体溢流堰设置于轻相流体收集槽一侧并与分离壳体底部连接,中间相流体溢流堰与分离壳体尾部的空间形成中间相流体收集槽,中间相流体溢流堰一侧的顶部和底部各设有一个第四液位计,中间相流体溢流堰一侧的分离壳体底部连接有中间相流体出口。
15.可选地,所述入口段ⅰ、沉降分离段ⅱ和采集段ⅲ的长度比例为1:3.2
‑
4.2: 2。
16.可选地,所述镇静板顶端与位于分离壳体顶部的第二液位计处于同一水平面;所述挡板底端高于镇静板顶端400
‑
500mm,挡板底端低于气液分离器底端不小于200mm,所述聚结器的高度与轻相流体溢流堰的高度相同,所述重相流体溢流堰的高度高出轻相流体收集槽底端200
‑
500mm,轻相流体溢流堰高度为四相分离器直径的1/2
‑
3/4,轻相流体收集槽的后墙高度高出除雾器底端200mm,中间相流体溢流堰的高度比轻相流体溢流堰的高度低20
‑
100mm。
17.本实用新型的有益效果是:
18.通过设置预洗塔,并设置预洗塔为超重力旋转装置,使得脱苯后的焦炉煤气可以在预洗塔内通过超重力旋转技术进行杂质的初步脱除,通过预洗塔的预处理,可以深度脱除脱苯后的焦炉气内的尘、苯、焦油、萘、氨和硫等有害物质,解决了焦炉煤气中的硫、氨超标会影响后系统的稳定运行的问题,能够提高系统运行的稳定性;还解决了焦炉煤气中的焦油、萘会造成压缩系统堵塞的问题,避免在后续工段可能造成的堵塞异常。进一步地,通过设置脱硫塔、热再生塔、水洗塔、共沸塔、甲醇水分离塔、富甲醇闪蒸槽和四相分离器等设备,提供了一种采用低温甲醇洗技术来进一步脱除焦炉煤气中成分复杂的杂质的系统,既可以保证净化气指标,又可通过甲醇再生循环利用解决焦化脱硫废液无法根治处理的难题,还解决了粗脱硫不正常会造成精脱硫的脱硫剂提前失效而增加运行费用的问题。
19.通过本实用新型实施例提供的系统和方法,满足了焦炉煤气增压输送以及后续的深度净化需求,达到了生产化学品合成系统净化需要的目的。本实用新型具有投资少,设备体积和占地面积小,脱除焦炉煤气中焦油尘、萘等杂质效率高、能耗低、洗涤效率高等优点。另外,通过本实用新型深度净化后的焦炉煤气返回焦炉后无需再脱硫,也没有难处理的脱硫废液产生,使得后续生产化工产品精脱硫催化及使用寿命至少延长一年以上。
附图说明
20.图1是本实用新型的系统组成示意图。
21.图2是图1中预洗塔的结构示意图。
22.图3是图1中四相分离器的结构示意图。
具体实施方式
23.下面将结合附图和实施例对本实用新型作进一步地详细描述。
24.如图1所示,本实用新型实施例提供了一种焦炉煤气的深度净化系统,其包括预洗
塔1、脱硫塔8、热再生塔3、水洗塔4、共沸塔5、甲醇水分离塔6、富甲醇闪蒸槽7和四相分离器2,所述预洗塔1为超重力旋转装置,四相分离器 2为卧式三堰型气
‑
液
‑
液
‑
液分离器,其中:气柜经第一换热器9与预洗塔1下部的气相进口103连接,预洗塔1底部的液相出口102与四相分离器2的进料口 201连接,预洗塔1的气体出口107经第一压缩机10、第二换热器11和第三换热器12与脱硫塔8下部的进气口连接,脱硫塔8顶部的出气口与第二换热器11 连接,脱硫塔8底部的出液口经第二压缩机14与预洗塔1上部的液相进口109 连接,脱硫塔8中下部的出液口经第四换热器13与富甲醇闪蒸槽7的进液口连接,富甲醇闪蒸槽7顶部的出气口与水洗塔4中上部的进气口连接,水洗塔4 顶部的出气口与脱硫废气管道连接,富甲醇闪蒸槽7底部的出液口经第五换热器15与热再生塔3中上部的进液口连接,热再生塔3底部的出液口经第三压缩机16和第五换热器15与脱硫塔8上部的进液口连接,热再生塔3顶部的出气口经第六换热器17与水洗塔4下部的进气口连接,第六换热器17连接冷凝液储罐22的进液口,冷凝液储罐22的出液口与热再生塔3上部的进液口连接,水洗塔4底部的出液口与四相分离器2的进料口201连接,四相分离器2的气相出口202与共沸塔5中部的进气口连接,四相分离器2的重相流体出口203 与重油管道连接,四相分离器2的轻相流体出口204与轻油管道连接,四相分离器2的中间相流体出口205经第四压缩机18和第七换热器23与共沸塔5中部的进液口连接,共沸塔5顶部的出气口与水洗塔4下部的进气口连接,共沸塔5底部的出液口经第五压缩机24与甲醇水分离塔6中部的进液口连接,甲醇水分离塔6顶部的出气口与热再生塔3中部的进气口连接,甲醇水分离塔6底部的出液口与第七换热器23连接。
25.本实用新型的系统应用在焦炉煤气初冷、电捕焦油、预冷、脱硫、中间冷却、除氨、终冷和洗脱苯后,用来脱除焦炉煤气内含的尘、苯、焦油、萘、氨以及各种形态硫等杂质,以满足焦炉煤气增压输送以及后续的深度净化,达到生产化学品合成系统净化的需要。
26.可选地,如图2所示,所述预洗塔1包括传动装置101、转轴115和预洗壳体108,传动装置101与转轴115一端连接,转轴115另一端连接有转子104,转子104设于预洗壳体108内腔的中下部,预洗壳体108的顶部中间连接有气体出口107,预洗壳体108的底部连接有液相出口102,预洗壳体108的一侧底部连接有气相进口103,预洗壳体108的另一侧中上部连接有液相进口109,液相进口109连接有l形液体管道,l形液体管道的竖直管延伸至转子104中部, l形液体管道的竖直管上安装有若干个液相喷嘴111,预洗壳体108内腔的顶部设有除沫器106,除沫器106底部与转子104顶部之间安装有分隔板105,转子 104顶部中间与分隔板105之间通过第一密封垫110密封,转子104底部中间两侧与转轴115之间分别通过第二密封垫112和第三密封垫113密封,转子104 内部填充有填料层114。
27.可选地,所述填料层114的孔隙率80%~99%;填料层114的填料采用大波纹丝网填料和小波纹丝网填料。在靠近转轴115处设置长度占预洗壳体108半径5%~10%长度的小波纹填料,优选为5%~8%。大波纹丝网填料的平均孔径为 5~10mm,优选为4~8mm;小波纹丝网填料的平均孔径为1~5mm,优选为2~4 mm。这种填料方式有利于液相洗涤液的均匀雾化,提高对杂质的捕集效果,大波纹填料可以减小气液相阻力,提高填料的抗堵塞能力。
28.可选地,如图3所示,所述四相分离器2包括分离壳体218,分离壳体218 内腔从左至右分为入口段ⅰ、沉降分离段ⅱ和采集段ⅲ;所述入口段ⅰ设置有气液分离器206、挡板207和镇静板208,进料口201设于分离壳体218外部并与分离壳体218顶部连接,气液分离器206
安装于进料口201下面,镇静板208 底端与分离壳体218底部连接,挡板207顶端与分离壳体218顶部连接并位于气液分离器206和镇静板208之间;所述沉降分离段ⅱ安装有聚结器209;所述采集段ⅲ设置有重相流体溢流堰217、重相流体收集槽219、轻相流体收集槽220 和中间相流体溢流堰216,重相流体溢流堰217设置于聚结器209一侧并与分离壳体218底部连接,重相流体收集槽219顶端与分离壳体218底部连接并位于聚结器209与重相流体溢流堰217之间,重相流体收集槽219侧壁的顶部和底部各安装有一个第一液位计213,重相流体收集槽219底部连接有重相流体出口203,重相流体收集槽219上方的分离壳体218顶部和底部各安装有一个第二液位计212,轻相流体收集槽220设置于重相流体溢流堰217一侧,轻相流体收集槽220的前墙为轻相流体溢流堰214,轻相流体溢流堰214的高度低于轻相流体收集槽220的后墙215的高度,轻相流体收集槽220内的顶部和底部各设有一个第三液位计210,轻相流体收集槽220底部连接有轻相流体出口204,轻相流体出口204位于分离壳体218外部,轻相流体收集槽220上方设置有除雾器222,气相出口202设于分离壳体218外面并与除雾器222连接,中间相流体溢流堰 216设置于轻相流体收集槽220一侧并与分离壳体218底部连接,中间相流体溢流堰216与分离壳体218尾部的空间形成中间相流体收集槽221,中间相流体溢流堰216一侧的顶部和底部各设有一个第四液位计211,中间相流体溢流堰216 一侧的分离壳体218底部连接有中间相流体出口205。
29.其中,气液分离器206和镇静板208是入口段ⅰ的常规部件,其中气液分离器206的主要功能是实现气
‑
液预分离,实际应用中可有多种形式,其作用是把液体在填料顶部或某一高度上进行均匀的初始分布或再分布,用来提高传质、传热的有效表面,改善相间接触,从而提高塔的分离效率。镇静板208的主要作用是减缓入口段ⅰ液相区的两相波动,也兼有液
‑
液
‑
液预分离的功能,但主要是抑制波动为沉降分离段ⅱ提供稳定的操作条件。聚结器209主要是通过促进轻相(比如油滴)在板面的聚结来提高分离效率,同时也具有抑制沉降分离段ⅱ液相区波动的功能。
30.可选地,所述入口段ⅰ、沉降分离段ⅱ和采集段ⅲ的长度比例为1:3.2
‑
4.2: 2。
31.可选地,所述镇静板208顶端与位于分离壳体218顶部的第二液位计212 处于同一水平面;所述挡板207底端高于镇静板208顶端400
‑
500mm,挡板207 底端低于气液分离器206底端不小于200mm。
32.可选地,所述聚结器209的高度与轻相流体溢流堰214的高度(h1)相同,所述重相流体溢流堰217的高度高出轻相流体收集槽220底端200
‑
500mm,轻相流体溢流堰214高度为四相分离器直径的1/2
‑
3/4,轻相流体收集槽220的后墙215高度(h2)高出除雾器222底端200mm,中间相流体溢流堰216的高度 (h3)比轻相流体溢流堰214的高度低20
‑
100mm。
33.通过在采集段ⅲ设置了重相流体溢流堰217、轻相流体溢流堰214和中间相流体溢流堰216三块溢流堰板和重相流体收集槽219、轻相流体收集槽220和中间相流体收集槽221三个液相收集槽,因此四相分离器2采集段ⅲ的长度大于普通分离器,但也因为如此设置,使得操作过程中的液
‑
液界面得到较好的控制,从而保证分离过程的稳定进行,从而减小或避免了工况波动对沉降分离段ⅱ过程的影响。本实用新型实施例中四相分离器2的液
‑
液界面的控制源于两个方面:一是三块溢流堰板和三个液相收集槽结构使液
‑
液界面同时受到轻相/中间相和重相流体静压的控制,因而比较稳定;二是轻相流体收集槽220和中间相流体收集槽221为操作过程中上、下游(进、出口)流量的波动提供了缓冲空间,从而减小或避
免了工况波动对沉降段分离过程的影响。通过设置镇静板208及聚结器209等部件,确保较低的横向流速使得液相区流体有足够的停留时间实现液
‑
液
‑
液沉降分离,同时有利于分散相的沉降或浮升,还减少液相区的波动,缩短分离时间,减小设备尺寸。
34.本实用新型之所有采用图3所示的四相分离器2,是综合考虑实际分离工况下沉降分离段ⅱ末端的压力分布的影响因素包括:轻相流体溢流堰214高度和三堰板的高差、溢流堰顶的液层厚度和溢流堰顶的液层流速和轻相收集槽220底部的流动阻力而作出的。
35.上述焦炉煤气的深度净化系统的焦炉煤气的深度净化方法,包括如下步骤:
36.s1,洗脱苯后的焦炉煤气在第一换热器9和第二换热器11中与脱硫塔8深度净化后的焦炉煤气换热到20
‑
25℃,换热后的焦炉煤气从预洗塔1下部送入预洗塔1中,同时来自脱硫塔8底部的煤气洗涤剂经第二压缩机14加压后从预洗塔1上部送入预洗塔1;其中,预洗塔1为超重力旋转装置。
37.洗脱苯后的焦炉煤气中含有尘、苯、焦油、萘、氨以及各种形态硫等杂质。通常,洗脱苯后的焦炉煤气中含有焦油尘5
‑
15mg/m3,萘10
‑
200mg/m3,氨15
‑
100mg/m3,硫小于500mg/m3及其它微量杂质。
38.s2,换热后的焦炉煤气与煤气洗涤剂在预洗塔1内逆流或错流接触进行预处理,预处理后的煤气洗涤剂在预洗塔1的超重力作用下在预洗塔1内壁聚集后排出至四相分离器2。
39.由于洗脱苯后的焦炉煤气中包括尘、苯、焦油、萘、氨以及各种形态硫等杂质,因此,本实用新型实施例先通过采用超重力旋转技术的预洗塔1对洗脱苯后的焦炉煤气进行预处理,以初步脱除洗脱苯后的焦炉煤气中的尘、苯、焦油、萘、氨以及各种形态硫等杂质。
40.具体地,在预洗塔1内,煤气洗涤剂经预洗塔1的液相喷嘴111均匀分布后进入填料层114,在传动装置101、转轴115和转子104作用下,煤气洗涤剂被分裂成液体微元(液膜、液丝和液滴)并与洗脱苯后的焦炉煤气逆流接触来脱除洗脱苯后的焦炉煤气中的杂质。由于预洗塔1为超重力旋转装置,使得本实用新型实施例是利用超重力旋转技术来进行杂质的脱除的。超重力旋转技术的切割粒径达到10
‑8m的数量级,煤气洗涤剂经过填料层114后的粒径几乎达到分子级别,再在超重力旋转装置中聚集后与杂质一并脱出。本实用新型实施例利用超重力旋转技术对洗脱苯后的焦炉煤气进行预处理,可以强化洗涤效果,降低洗涤的粒径切割尺寸,同时通过液相喷雾和超重力作用下,使液滴分布更加均匀,与焦炉煤气中杂质接触面更大,从而提升对杂质的洗脱效果。超重力旋转装置具有良好的粒子捕集效果、气相压降小,旋转填料不易堵塞等特点,以此来达到深度脱除焦炉气内的尘、苯、焦油、萘、氨和硫等有害物质,从而满足焦炉煤气增压输送以及后续的深度净化,达到生产化学品合成系统净化需要的目的。脱除杂质后的焦炉煤气经过除沫器106除沫后得到预处理后的焦炉煤气,脱除杂质后的煤气洗涤剂被甩至预洗壳体108内壁并由液相出口102流入四相分离器2。
41.焦炉煤气预处理是在不同温度、压力、洗涤剂下试验发现焦炉煤气中的萘在<20℃时易结晶析出。为避免低温下萘结晶造成设备、管道的堵塞,本实用新型实施例通过新增预洗塔1,并利用预洗甲醇来脱除焦炉煤气中的萘。由于预洗甲醇中含有粗苯,苯与萘均属于芳香类化合物,根据相似相容原理,萘基本溶解到煤气洗涤剂中。
42.进一步地,本实用新型实施例通过试验确定最佳的预处理焦炉煤气的最合适温度
在20
‑
25℃,煤气洗涤剂至少包括甲醇和粗苯,煤气洗涤剂还可以包括脱盐水、乙醇、洗油和焦油中的一种或两种及两种以上的组合,煤气洗涤剂温度小于20℃时具有很好的预处理效果。在这些条件下对洗脱苯后的焦炉煤气进行预处理后,实践证明,对焦油灰尘的捕集效率达到99%以上,能够完全除去3 μm以上的颗粒;对萘的脱除率80%以上;对焦油和尘的脱除率达到60%以上;对有机硫脱除率达到85%以上;对氨的脱除率达到50%以上;对苯的脱除率达到50%以上;这种脱除率使得预处理后的焦炉煤气满足了后续压缩以及深度净化的要求。
43.s3,预处理后的焦炉煤气经第一压缩机10加压到0.3
‑
1.0mpa后与脱硫塔8 深度净化后的焦炉煤气在第二换热器11中进行一级冷却,再经过第三换热器12 深冷至
‑
22~
‑
28℃后进入脱硫塔8,在脱硫塔8内经过两级脱出焦炉煤气中的杂质,得到深度净化后的焦炉煤气,深度净化后的焦炉煤气经过第一换热器9和第二换热器11复热后,42
‑
50%的深度净化后的焦炉煤气减压到8
‑
10kpa后作为返炉煤气用于焦炉加热,其余用于生产化学品。
44.s4,脱硫塔8下部脱硫得到的含硫甲醇富液被第四换热器13复热至25~35℃后进入富甲醇闪蒸槽7进行减压闪蒸,闪蒸压力为2
‑
8bar,闪蒸出的气体经水洗塔4回收甲醇后作为脱硫废气排出系统,富甲醇闪蒸槽7底部的闪蒸富液经第五换热器15复热至80
‑
100℃后进入热再生塔3进行再生,再生后的贫甲醇经第三压缩机16加压、第五换热器15冷却至
‑
20~
‑
40℃后送至脱硫塔8上部作为吸收剂,热再生塔3塔顶得到的含硫气体经第六换热器17冷却并经冷凝液储罐22 回收夹带的甲醇后送水洗塔4洗涤,水洗塔4洗涤后的焦炉煤气作为脱硫废气排出系统。
45.富甲醇闪蒸槽7闪蒸出的气体为h2、ch4等。热再生塔3塔顶得到的含硫气体为h2s浓度较高的气体。吸收有酸性气组分的甲醇溶液通过减压闪蒸,加热再生等操作手段实现再生后循环使用。贫甲醇温度为
‑
20~
‑
40℃时,既能满足脱硫精度的需要,又可借助常用冷却介质的冷却。
46.s5,预洗塔1预处理后的煤气洗涤剂与水洗塔4塔底排出的含甲醇溶液混合,混合后的混合物送至四相分离器2进行气液分离,四相分离器2分离出的溶解气体排出至共沸塔5进行洗涤,四相分离器2分离出的焦油尘由四相分离器2的重相流体出口203排出,四相分离器2分离出的石脑油由四相分离器2 的轻相流体出口204排出,四相分离器2分离出的中间相作为煤气洗涤剂经甲醇水分离塔6排出的废水经第七换热器23换热到80
‑
100℃后再经第四压缩机18 加压送入共沸塔5回收洗涤剂。
47.预洗塔1预处理后的煤气洗涤剂中含有焦油、尘、粗苯、萘、氨、有机硫等杂质。
48.s6,共沸塔5塔顶的不凝气经水洗塔4水洗回收甲醇后作为脱硫废气排出系统,共沸塔5塔底的甲醇/水混合物经第五压缩机24加压后送至甲醇水分离塔 6进行精馏提纯,甲醇水分离塔6塔顶的甲醇蒸汽返回热再生塔3中部,甲醇水分离塔6塔底的废水经第七换热器23降温后送出系统。
49.脱硫塔8中的甲醇在吸收酸性气体的同时还吸收了工艺气中的nh3,这会对低温甲醇洗系统(脱硫塔8、热再生塔3、水洗塔4、共沸塔5、甲醇水分离塔6和富甲醇闪蒸槽7)造成一定的影响。低温下nh3在甲醇中的溶解度远高于co2和h2s等酸性气体在甲醇中的溶解度,因此,很容易在甲醇洗系统中累积。co2和h2s等酸性气体溶解到甲醇中后会使得甲醇的ph值降低,造成低温甲醇洗系统设备的腐蚀。为了减少设备的腐蚀、延长设备的使用年限和运行
周期,现低温甲醇洗工艺都会允许系统中存在一定含量的nh3,常温下nh3在甲醇中的溶解度是h2s的10多倍,是co2的60多倍,含nh3的甲醇最终进入到热再生塔3中再生,溶解在甲醇中的nh3会在热再生塔3解吸,随着酸性气进入到热再生塔3塔顶的水冷器,由于水冷器将酸性气降温,酸性气中的甲醇被冷凝下来。但是必须要严格控制nh3在低温甲醇洗系统中的含量,如果nh3含量低会造成设备腐蚀的加剧;nh3含量高则会造成甲醇热再生系统铵盐结晶,堵塞热再生塔3顶部的换热器;当nh3含量高到一定程度就会造成工艺气中硫含量超标。所以必须要控制好低温甲醇洗系统中的nh3含量,因而本实用新型实施例需要在净化时将氨气浓度控制在一定范围,即维持循环使用的贫甲醇(在脱硫塔8、热再生塔3、水洗塔4、共沸塔5、甲醇水分离塔6、富甲醇闪蒸槽7 和四相分离器2中循环的)中nh3含量小于20
×
10
-6
ppm,ph值在8
‑
10。
50.依据焦炉煤气中h2s浓度的不同,在0.3
‑
1.0mpa,温度
‑
20~
‑
40℃甲醇中的溶解度为0.9~6nm3h2s/m3,co2在0.3
‑
1.0mpa,温度
‑
20~
‑
40℃在甲醇中的溶解度为0.8~5nm
3 co2/m3,可以确定脱硫塔8中贫甲醇的用量(即进入脱硫塔8中的贫甲醇用量,包括从热再生塔3塔底进入的贫甲醇和外界隔断时间补充的甲醇)为1.30
‑
1.50kg/m3焦炉煤气。
51.焦炉煤气成分复杂,杂质众多,其气体组分包括co、h2、co2、ch4、h2s、有机硫、c2h4、c2h6、c3h8、c4h
10
、hcn、n2、ar以及焦油、脂肪酸、单酚、复酚、石脑油、蒽油、萘油、飞灰等。在这些组分中除co、h2有效组分和ch4、 n2、ar以及烃类属惰性气体外,其余所有组分包括co2和硫化物都是需要脱除的有害杂质,可见其净化任务的艰巨。随伴随着焦化企业退城入园、升级改造等政策的实施,规模化、高端化成为焦化行业的发展方向,对焦炉煤气脱硫的要求也随之提高,采用低温甲醇洗净化方法可以干净地脱除焦炉煤气中的各种有害成分,诸如co2、h2s、cos、c4h4s、hcn、nh3、h2o、c2以上烃类(包括轻油、芳香烃、石脑油、烯烃及胶质物等)以及其他羰基化合物等,而其它任何净化工艺都无法做到。另外,采用低温甲醇洗脱除焦炉煤气中成分复杂的硫杂质,既可以保证净化气指标,又可通过甲醇再生循环利用解决焦化脱硫废液无法根治处理的难题。
52.可选地,所述预洗塔1的操作条件为:操作温度15~20℃、操作压力3~6kpa、填料比表面积500~4000m2/m3,填料旋转频率为30~60hz,气液比1000~6000。
53.可选地,所述煤气洗涤剂至少包括甲醇、洗油和焦油。
54.可选地,所述脱硫塔8两级脱出焦炉煤气中的杂质后,深度净化后焦炉煤气中的硫含量≤0.1ppm,二氧化碳含量≤2.5%,无焦油尘、萘和氨。
55.可选地,所述预洗塔1内煤气洗涤剂用量(即从脱硫塔8底部进入预洗塔1 的洗涤剂用量)为0.20
‑
32kg/m3焦炉煤气。
56.进一步地,一般焦炉煤气组成如下表一所示:
57.表一
[0058][0059]
由于焦炉煤气中co2含量小于3%,炼焦煤硫含量为0.7%,相比大型煤气化煤气中硫浓度提高4
‑
8倍,因此相对于大型煤气化工艺,本实用新型实施例不需要通过硫化氢浓缩
塔来提高酸性气的浓度,通过热再生塔3并将所废气集中经过水洗塔4处理即可达到要求的酸性气浓度回收硫浓度。因此,相对于大型煤气化工艺,本实用新型实施例具有整个后续流程缩短,投资显著降低,占地面积小,环保效益好的效果。
[0060]
可以理解的是,以上实施方式仅仅是为了说明本实用新型的原理而采用的示例性实施方式,然而本实用新型并不局限于此。对于本领域内的普通技术人员而言,在不脱离本实用新型的精神和实质的情况下,可以做出各种变型和改进,这些变型和改进也视为本实用新型的保护范围。