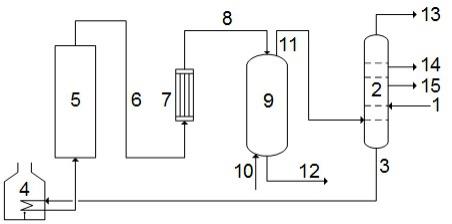
1.本发明涉及一种中间相沥青的生产方法和生产系统。
背景技术:
2.中间相沥青是一种向列型液晶,具有光学各向异性,是重要的碳材料前驱体,可用于制备高附加值的中间相沥青基碳纤维、针状焦、泡沫炭等碳材料。中间相沥青的特殊结构特征,赋予这些材料具有优良耐热性、高导热系数以及高电导率等特性,在航空航天、精密电子、能源等诸多领域具有广阔的应用前景。用于制备中间相沥青的原料具有明显的多样性,如纯芳烃、石油沥青、煤焦油、煤沥青、煤液化残渣等,原料的差异导致了制备方法、制备工艺的多样性。目前常用的中间相沥青的制备方法有:直接热缩聚法、催化改性法、共炭化法和加氢改性法等。
3.cn106497591a公开了一种催化合成中间相沥青的制备方法,采用净化沥青、纯芳烃化合物、三氟化硼或三氟化硼乙醚络合物催化聚合,先将催化剂三氟化硼络合物或三氟化硼按反应物料质量比1:100-1:200装入低温反应釜,加热温度100-260℃,压力控制在0.5-2mpa反应,冷却后的固相组分中加入吡啶,加热至100-150℃,过滤出反应生成的固体,除去三氟化硼后获得高纯聚合沥青,再通过进一步热聚合、小分子脱除制得中间相沥青。
4.cn 107384462a给出一种催化裂化油浆两段临氢改质-热缩聚制备中间相沥青的方法,以环烷基原油催化裂化油浆经减压蒸馏,切取其沸点在380~540℃之间的馏分作为原料,先在380~450℃,氮气初压4mpa,恒温恒压反应1~10h,得到石油沥青。石油沥青在400~440℃下,氢初压6mpa,自升压反应1~8h,得到一次氢化沥青。一次氢化沥青在420~480℃,氮气初压4mpa下,继续恒温反应1~8h,得到一次产物。然后一次产物在400~440℃,氢初压6mpa下,自升压反应1~8h,得到二次氢化沥青。之后二次氢化沥青在420~480℃,压力4mpa下,反应2~16h,得到高品质的中间相沥青。
5.cn104818041a公开了一种以加氢裂化尾油制备中间相沥青的方法,以加氢裂化尾油为原料,加入1~8wt%的酚醛树脂或丁苯橡胶为共炭化添加剂,在高压釜中于380~420℃、6~10mpa、惰性气体气氛和搅拌条件下炭化6~15h得到中间相沥青。作为优选:所述的加氢裂化尾油为环烷基原油常压渣油的加氢裂化尾油,所述惰性气体包括氩气或氮气,搅拌条件为400~900r/min。
6.综上所述,目前中间相沥青制备过程中大多数都采用间歇操作,如反应釜,为制备优质中间相沥青,通常采用两种或多种工艺进行复合,工艺较为复杂。而添加与原料隶属于不同类别的添加剂,因添加剂与原料的结合状况无法确定,经过后续加工、炭化、石墨化处理后可能会出现气孔等缺陷,影响中间相沥青的可纺性及碳纤维的性能。此外,对于反应釜设备,特别是在高温反应区域,其边壁效应较为严重,容易在反应釜器壁、反应釜底部生成不溶于喹啉的焦炭状物质,严重影响中间相沥青的均匀性及品质。
技术实现要素:
7.针对现有技术中存在的不足,本发明主要目的是提供一种中间相沥青的生产方法和生产系统,所述中间相沥青的生产方法不仅目的产物收率高、品质可控性好,且可以实现长周期稳定连续生产。
8.本发明第一方面提供一种中间相沥青的生产方法,所述生产方法包括如下内容:原料经加热后进入反应单元a,反应流出物经快速降温后进入反应单元b与载气接触进行处理,处理后得到油气产物和中间相沥青,油气产物进一步进入分馏系统进行处理。
9.上述中间相沥青的生产方法中,反应单元b得到的油气产物进入分馏系统进行处理,分馏后得到气体、汽油、柴油和循环油。
10.上述中间相沥青的生产方法中,所述反应单元a设置1个以上反应器,优选设置2~4个反应器,进一步优选设置2个或3个反应器,更进一步优选设置2个反应器。当设置2个以上反应器时,所述反应器之间以串联方式连接。
11.上述中间相沥青的生产方法中,所述反应单元a的操作条件为:温度380~500℃,优选400~480℃;压力为常压~5mpa,优选常压~2mpa,物料在反应器内停留时间为0.1~50h,优选0.2~48h。
12.上述中间相沥青的生产方法中,所述反应单元a设置2个反应器,分别为第一反应器和第二反应器,所述原料油经加热后进入第一反应器,反应后得到第一流出物,第一流出物进入第二反应器,反应后得到第二流出物,第二流出物经调温后进入反应单元b。
13.上述中间相沥青的生产方法中,所述第一反应器的操作条件为:温度为420~500℃,优选为440~470℃;压力为常压~5mpa(表压),物料在第一反应器内的停留时间为0.15~24h,优选为0.15-5h。所述第二反应器的操作条件为:温度为380~420℃,优选为400~420℃;压力为常压~5mpa,物料在第二反应器内的停留时间为0.5~48h,优选为12~48h。进一步优选所述第一反应器的操作温度比第二反应器的操作温度高10~60℃,优选为20~50℃。物料在第一反应器内的停留时间比物料在第二反应器内的停留时间短0.05~47h,优选为2~40h。
14.上述中间相沥青的生产方法中,反应单元a得到的反应流出物经快速降温后进入反应单元b,所述快速降温后的温度降至350~400℃,优选350~380℃;降温速率为50~650℃/s,优选为50~200℃/s。
15.上述中间相沥青的生产方法中,所述原料优选先与来自反应单元b的油气产物在分馏系统中进行换热,换热后原料(换热后的原料温度控制为200~250℃)和分馏系统底部循环油一起从分馏系统底部抽出,进一步经加热至指定温度(加热炉出口温度控制在300~350℃)后进入反应单元a进行反应。
16.上述中间相沥青的生产方法中,所述原料可以为煤系原料和/或石油系原料,其中煤系原料可以是煤焦油、煤焦油沥青、煤液化残渣中的一种或多种,进一步优选煤系原料先除去喹啉不溶物;所述石油系原料可以是乙烯焦油、催化裂化油浆、渣油、石油沥青、加氢尾油中的一种或多种。
17.上述中间相沥青的生产方法中,所述反应单元b设置一个以上的反应器。
18.上述中间相沥青的生产方法中,所述反应单元a为连续式反应器,可以为管式反应器,也可为连续搅拌釜反应器,优选管式反应器。
19.上述中间相沥青的生产方法中,所述反应单元b的操作条件为:反应器顶部压力为-0.5~1mpa(表压),优选-0.3~0.5mpa(表压),反应温度为350-520℃,优选400~500℃,停留时间2~10h,优选3~5h,空速为60~900l/( kg
·
h),优选90~300 l/( kg
·
h)。
20.上述中间相沥青的生产方法中,所述载气可以为水蒸气、氮气、惰性气体中的一种或几种,优选为水蒸汽或氮气;其中所述惰性气体为氦气、氖气、氩气、氪气、氙气中的一种或几种。
21.上述中间相沥青的生产方法中,所述反应单元b得到的中间相沥青产物收率45~55wt%,软化点220~280℃,且中间相形态呈广域型光学结构。
22.上述中间相沥青的生产方法中,分馏系统中得到的循环油质量循环比控制为0.5~1.5,优选0.5~1.0,所述的循环比为循环油与原料质量比。
23.上述中间相沥青的生产方法中,循环油的10%馏出温度为350℃~420℃,优选380℃~ 400℃,90%馏出温度为450℃~520℃,优选480~500℃。
24.本发明第二方面提供一种中间相沥青的生产系统,所述生产系统包括加热炉,其用于接收来自分馏系统的原料和循环油;反应单元a,其用于接收并处理来自加热炉的原料;急冷装置,其用于接收并处理来自反应单元a的反应流出物;反应单元b,其用于接收并处理来自急冷装置处理后的物料和载气,处理后得到油气产物和中间相沥青;分馏系统,其用于接收来自反应单元b的油气产物和原料,处理后得到气体、汽油、柴油和循环油。
25.上述中间相沥青的生产系统中,所述反应单元a设置1个以上反应器,优选设置2~4个反应器,进一步优选设置2个或3个反应器,更进一步优选设置2个反应器。当设置2个以上反应器时,所述反应器之间以串联方式连接。
26.上述中间相沥青的生产系统中,所述反应单元a设置2个反应器,分别为第一反应器和第二反应器,所述原料油经加热后进入第一反应器,反应后得到第一流出物,第一流出物进入第二反应器,反应后得到第二流出物,第二流出物经调温后进入反应单元b。
27.上述中间相沥青的生产系统中,所述急冷装置可以是急冷锅炉、盘式油急冷器、烟气急冷器等中的一种,优选急冷锅炉。
28.上述中间相沥青的生产系统中,所述反应单元a中的反应器采用连续式反应器,具体可以为管式反应器,也可为连续搅拌釜反应器,优选管式反应器。
29.上述中间相沥青的生产系统中,所述反应单元b中的反应器采用连续式反应器。
30.本发明第三方面提供一种采用上述方法生产的中间相沥青,所述中间相沥青的软化点220~280℃,氢碳比小于0.6,且中间相形态呈广域型光学结构。
31.与现有技术相比,本发明中间相沥青的生产方法和生产系统的有益效果主要体现在以下方面:1、本发明提供的中间相沥青生产系统中通过增设急冷装置,将反应单元a得到的反应产物在极短时间内迅速降温处理,可以大幅度降低中间相沥青产物中类似焦炭固体物的含量,提高了中间相沥青的品质,尤其是可纺性。
32.2、本发明提供的中间相沥青生产方法中,将分馏系统得到的循环油循环回反应单
元a,由于循环油中含有一定量的环烷环稠合的芳烃,在后续的液相炭化过程中,可提高体系的热稳定性和流变性,同时提高中间相沥青的收率。
33.3、本发明提供的中间相沥青生产方法中,通过综合调控反应单元a、急冷装置、反应单元b的操作条件,实现整个生产系统稳定长周期运行,同时得到软化点和光学结构等性能满足要求的中间相沥青。尤其当反应单元a中采用两个反应器时,第一反应器内温度高于第二反应器,但停留时间短于第二反应器,可以保证反应单元a中一方面发生足够程度的热裂化反应,同时防止发生过量的热聚合反应,在第一反应器中尽可能多地生成初始中间相小球,然后让其在后续中间相形成过程中作为中间相生成的核,起到引发剂的作用。在第二反应器中,反应温度比第一反应器低,可以有效降低体系中大分子自由基的缩合反应速率,缓和炭化反应,从而防止体系粘度增长过快,改善体系流动性,使得第一反应器中生成的中间相小球得以更充分的长大、融并,改善中间相沥青的软化点和光学结构。
34.4、本发明提供的中间相沥青生产方法便于控温且工艺条件灵活可控,可连续生产性能稳定的中间相沥青产品,中间相形态其呈广域型光学结构,软化点220~280℃,氢碳比小于0.6。
附图说明
35.图1为本发明第一种实施方式中间相沥青的生产系统示意图。
36.图2为本发明第二种实施方式中间相沥青的生产系统示意图。
具体实施方式
37.下面结合附图及实施例对本发明方法进行更进一步的详细说明,但以下实施例不构成对本发明方法的限制。
38.如图1和图2所示,本发明提供一种中间相沥青的生产系统,包括如下内容:加热炉4,其用于接收来自分馏系统的原料1和循环油3;反应单元a5,其用于接收并处理来自加热炉4加热后的原料;图1中所述反应单元a包括1个反应器,图2中所述反应单元a5包括2个反应器,分别为第一反应器16和第二反应器17,第一反应器的反应流出物18进入第二反应器;急冷装置7,其用于接收并处理来自反应单元a5的反应流出物6,将反应流出物6迅速降温至指定温度;反应单元b9,其用于接收并处理来自急冷装置7处理后的物料8和载气10,在载气10的作用下,物料8处理后得到油气产物11和中间相沥青12,中间相沥青12作为产品出装置;分馏系统2,其用于接收来自反应单元b9的油气产物11和原料1,原料1与油气产物11在分馏系统进行换热,油气产物分馏处理后得到气体13、汽油14、柴油15和循环油3,原料1和循环油3一起从分馏系统流出并进入加热炉4。
39.本发明实施例和比较例中所用原料为催化油浆,具体性质见表1。实施例和比较例中各反应单元的操作条件见表2,反应结果见表3。
40.表1 原料性质
实施例1采用图1所示生产系统,所述反应单元a包括1个反应器,所述急冷装置降温速率为180℃/s,原料性质见表1,操作条件见表2,反应结果见表3。
41.实施例2采用图2所示的生产系统,所述反应单元a包括2个反应器,分别为第一反应器16和第二反应器17,第一反应器的反应流出物18进入第二反应器17。所述急冷装置降温速率为180℃/s,原料性质见表1,操作条件见表2,反应结果见表3。
42.实施例3采用图2所示的生产系统,与实施例2相比,操作条件略有调整,所述急冷装置降温速率为150℃/s,原料性质见表1,操作条件见表2,反应结果见表3。
43.对比例1采用图1所示生产系统,与实施例1相比,没有设置急冷装置,所述反应单元a得到的反应产物直接进入反应单元b,原料性质见表1,操作条件见表2,反应结果见表3。
44.对比例2采用图2所示的生产系统,与实施例2相比,没有设置急冷装置,所述反应单元a得到的反应产物直接进入反应单元b,原料性质见表1,操作条件见表2,反应结果见表3。
45.对比例3采用图2所示的生产系统,与实施例2相比,反应单元a中第一反应器和第二反应器的操作条件有调整,原料性质见表1,操作条件见表2,反应结果见表3。
46.表2 操作条件
表3 反应结果及产品性质