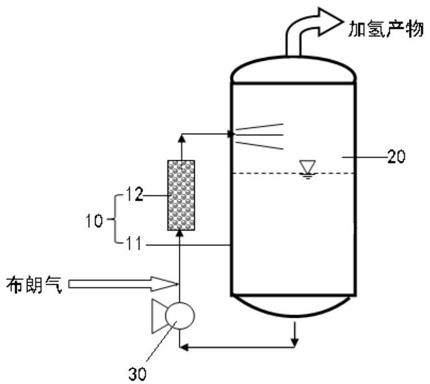
1.本发明涉及催化加氢领域,具体而言,涉及一种布朗气参与的催化加氢方法。
背景技术:
2.布朗气(氢氧气)最早是由澳大利亚科学家布朗教授提出,其定义为:严格地按照水(h2o)分子式中氢氧摩尔当量配比,将普通水在专有的电解液中电解以后而产生的具有活性的氢氧混合气体。现有文献表明其具有资源丰富,清洁环保和可再生性,安全可靠,变温特性,内爆特性及催化特性。目前主要应用于汽车助燃节油,汽车引擎除碳以及水焊机焊接等领域。
3.对催化加氢的目的主要在于:清除硫氮及其它有害物质,保护环境及发动机;同时提高燃油动力和燃烧效率。现有的催化加氢的方法主要包括有物理脱硫、化学脱硫、生物脱硫等方法出现,但真正运用于工业的主要就是化学脱硫当中的加氢脱硫和氧化脱硫。加氢脱硫具有较好的脱硫率,收率较高,但是必须使用昂贵的催化剂,且催化剂对原料油的要求严格,否则催化剂容易失活;此外还存在投资高和运行费高等缺点。而氧化脱硫法的投资和成本大大低于加氢脱硫,易于脱除存受空间位阻影响的硫,但是缺点是工艺不够成熟,需要添加助剂才能使氧化过程完全,氧源和助氧化原料价格也相当昂贵,同时还存在燃油收率低于加氢脱硫,砜、亚砜与烃类的分离占有较大的工艺投资等缺点。
4.鉴于上述问题的存在,需要提供一种能够同时满足投资和运行成本低,加氢效率高及产品收率高的催化加氢的方法。
技术实现要素:
5.本发明的主要目的在于提供一种布朗气参与的催化加氢方法,以解决现有的催化加氢方法无法同时满足投资和运行成本低,加氢效率高及产品收率高的问题。
6.为了实现上述目的,本发明提供了一种布朗气参与的催化加氢方法,布朗气包括氢离子和氧离子,且布朗气中的氢元素和氧元素的重量比为2:1,布朗气参与的催化加氢方法包括:布朗气与目标有机物进行轻质化,得到混合物;布朗气与目标有机物进行催化加氢反应,得到加氢产物。
7.进一步地,目标有机物为轻质燃油,且轻质燃油的沸点为50~350℃,密度≤0.9g/m3,api≥31.1的烃类有机物或混合物,催化加氢反应的温度为70~300℃,反应压力为0.05~0.1mpa,布朗气与目标有机物的体积比为(80~200):1。
8.进一步地,轻质燃油选自汽油、柴油和航空煤油组成的组中的一种或多种。
9.进一步地,当目标有机物为焦化柴油,催化加氢反应的温度为100~120℃,反应压力为0.05~0.08mpa,气油体积比为80~200;当目标有机物为催化柴油,催化加氢反应的温度为90~140℃,反应压力为0.05~0.08mpa,气油体积比为(80~200):1。
10.进一步地,当目标有机物为汽油,催化加氢反应的温度为70~120℃,反应压力为0.05~0.08mpa,布朗气与目标有机物的体积比为(80~200):1;当目标有机物为航空煤油,
催化加氢反应的温度为90~150℃,反应压力为0.05~0.08mpa,布朗气与目标有机物的体积比为(80~200):1。
11.进一步地,目标有机物为常压渣油、减压渣油和其它重质油,催化加氢反应的温度为350~400℃,反应压力为0.05~0.1mpa,布朗气与目标有机物的体积比为(80~200):1。
12.进一步地,目标有机物为常压渣油、减压渣油和api<10的重质油中的一种或多种,催化加氢反应的温度为380~400℃。
13.进一步地,轻质化步骤的时间为1~100s。
14.应用本发明的技术方案,本技术在轻质化的过程,由于使用一种特殊的反应器,延长两种离子的复合时间,使得轻质化过程中布朗气中的氢离子和氧离子能够与待处理的有机物进行结合,且仍呈现出离子状态。使上述轻质化产物进行催化加氢反应,能够大大降低催化加氢反应过程中的反应活化能,这使得上述催化反应不需要在催化剂的作用下进行也能够具有较高的反应速率,同时具有较低的能耗,以及较为优异的加氢效率和加氢产物的收率。
附图说明
15.构成本技术的一部分的说明书附图用来提供对本发明的进一步理解,本发明的示意性实施例及其说明用于解释本发明,并不构成对本发明的不当限定。在附图中:
16.图1为实施例1
‑
1中经过催化加氢过程中采用的反应装置。
17.其中,上述附图包括以下附图标记:
18.10、卫星环绕式减压塔釜;11、主塔釜;12、子反应器;20、精馏段;30、离心泵。
具体实施方式
19.需要说明的是,在不冲突的情况下,本技术中的实施例及实施例中的特征可以相互组合。下面将结合实施例来详细说明本发明。
20.正如背景技术所描述的,现有的催化加氢方法无法同时满足投资和运行成本低,加氢效率高及产品收率高的问题。为了解决上述技术问题,本技术提供了一种布朗气参与的催化加氢方法,布朗气包括氢离子和氧离子,且布朗气中的氢元素和氧元素的重量比为2:1,布朗气参与的催化加氢方法包括:布朗气与目标有机物进行轻质化,得到混合物;布朗气与目标有机物进行催化加氢反应,得到加氢产物。
21.按照布朗气定义,2摩尔氢与1摩尔氧严格比例混合的气体都被称为布朗气。因此,用氧气钢瓶与氢气钢瓶按比例配出的混合气体是布朗气,用常规电解水在两极上产生并混合的气体也是布朗气。但是本技术中使用的布朗气为同时含有氢离子和氧离子的布朗气,这种布朗气可以通过布朗气发生器产生。上述布朗发生器可以是本领域常用的布朗气发生装置,比如和利氢能或大业能源等企业生产的布朗气发生器。
22.本技术采用的布朗气中含有大量的氢离子和氧离子,且上述两种离子均具有非常高的反应活性,很容易形成氢气和氧气分子。本技术在轻质化的过程,由于使用一种特殊的反应器,延长两种离子的复合时间,使得轻质化过程中布朗气中的氢离子和氧离子能够与待处理的有机物进行结合,且仍呈现出离子状态。使上述轻质化产物进行催化加氢反应,能够大大降低催化加氢反应过程中的反应活化能,这使得上述催化反应不需要在催化剂的作
用下进行也能够具有较高的反应速率,同时具有较低的能耗,以及较为优异的加氢效率和加氢产物的收率。
23.上述轻质化过程和催化加氢反应可以在本领领域常用的反应装置中进行,只要能满足布朗气中的氢离子和氧离子稳定存在即可。优选地,上述轻质化过程和催化加氢过程在申请号为202110315815.9中所示的减压精馏塔中进行。其包括:卫星环绕式减压塔釜和精馏段;卫星环绕式减压塔釜包括主塔釜和呈卫星式环绕设置在主塔釜外部的多个子反应器;主塔釜设置有第一出口和多个喷射入口,且主塔釜的顶部具有开口;子反应器设置有第二出口和第一进口,喷射入口一一对应地与各子反应器的第二出口相连通,第一出口与第一进口相连通;其中,各喷射入口的喷射方向可调节或者至少两个喷射入口的喷射方向有交叉,且子反应器的容积小于主塔釜的容积;精馏段位于主塔釜上方,并与主塔釜的顶部开口相连通,精馏段的顶部设置有轻组分出口。主塔釜内还设置有非淹没式撞击流组件,非淹没式撞击流组件设置在各喷射入口的喷射方向上,用于对喷射入口的喷出物料进行非淹没式撞击、空化及剪切;各第一出口与第一进口通过循环管路相连,且循环管路上还设置有强制循环泵。
24.卫星环绕式减压塔釜除了主塔釜以外,还包括小体积的呈卫星式环绕设置在主塔釜外部的多个子反应器。在对常压渣油进行减压精馏的过程中,常压渣油原料可以通过子反应器进入,并将进入减压塔釜的渣油通过多个子反应器多次循环,也可以将新鲜的常压渣油和主塔釜第一出口返回的油料在子反应器中混合后再送入主塔釜,从而形成一个循环状态。一方面,新鲜常压渣油和釜中油料的不断循环,能够用最快捷最简便的方式令物料在质量传递、热量传递和能量传递上达到工艺要求,是一种高效的反应器。另一方面,新鲜常压渣油和釜中油料通过子反应器进入喷射入口后,因各喷射入口的喷射方向可调节或者至少两个喷射入口的喷射方向有交叉,实际喷入过程可使至少两股物料在喷入后会产生碰撞。且这种碰撞因是液相在气相环境中进行,为非淹没式撞击过程,因此能够发生一定的氢转移反应,促使常压渣油和循环油料发生浅度轻质化反应,从而对于提高减压精馏塔氢组分的质量和拔出率有相当好的作用。进入减压塔釜的常压渣油和塔釜油料通过子反应器不断循环、碰撞和闪蒸,产生了气相的轻质油并进入上方的精馏段进行减压精馏,以分离出汽油馏分、柴油馏分和残余馏分,精馏塔顶部则采出轻组分气相。
25.根据催化加氢目的的不同,上述催化加氢过程可以分为加氢精制过程和加氢裂化过程。加氢精制过程用于去除目标有机物中的硫、氮及氧等杂原子或金属杂质,加氢裂化过程用于使高分子量的重质油发生加氢、裂化和异构化反应,转化为轻质油(汽油、煤油、柴油、加氢裂化或裂解制烯烃的原料)的过程。
26.在一种优选的实施例中,目标有机物为轻质燃油,且轻质燃油的沸点为50~350℃,密度≤0.9g/m3,api≥31.1的烃类有机物或混合物,催化加氢反应的温度为70~300℃,反应压力为0.05~0.1mpa,布朗气与目标有机物的体积比为(80~200):1。对轻质燃油进行催化加氢反应,能够去除轻质燃油中杂质原子,进而使其得到精制。将催化加氢过程中的反应温度、反应压力及原料的用量限定在上述范围内有利于进一步提高轻质燃油的催化加氢效率和催化加氢效果。优选地,上述轻质燃油包括但不限于汽油、柴油和航空煤油组成的组中的一种或多种。
27.当轻质燃油的种类不同时,催化加氢的反应活性也不相同。为了有针对性地提高
各种类轻质燃油的催化加氢效果,需要针对具体的轻质燃油的种类进一步优选催化加氢的条件。
28.在一种优选的实施例中,当目标有机物为焦化柴油,催化加氢反应的温度为100~120℃,反应压力为0.05~0.08mpa,气油体积比为80~200。当目标有机物为催化柴油,催化加氢反应的温度为90~140℃,反应压力为0.05~0.08mpa,气油体积比为(80~200):1。在一种优选的实施例中,当目标有机物为汽油,催化加氢反应的温度为70~120℃,反应压力为0.05~0.08mpa,布朗气与目标有机物的体积比为(80~200):1;当目标有机物为航空煤油,催化加氢反应的温度为90~150℃,反应压力为0.05~0.08mpa,布朗气与目标有机物的体积比为(80~200):1。
29.高分子量的重质油在应用过程中大多需要通过加氢裂化反应转化为轻质产品油。为了进一步提高加氢裂化的效率,发明人针对产量较多的重质油的加氢裂化条件进行了研究。在一种优选的实施例中,目标有机物为常压渣油、减压渣油和api<10的重质油中的一种或多种,催化加氢反应的温度为350~400℃,反应压力为0.05~0.1mpa,布朗气与目标有机物的体积比为(80~200):1。重质油催化加氢过程中的温度、压力和原料比包括但不限于上述范围,而将其限定在上述范围内有利于进一步提高催化加氢的效率和轻质产品油的产率。更优选地,目标有机物为常压渣油、减压渣油和api<10的重质油中的一种或多种,催化加氢反应的温度为380~400℃。
30.上述api<10的重质油包括但不限于超重质原油、沥青质原油、页岩油、油砂油、油罐垢油等。
31.为了进一步提高轻质化的效果,从而有利于进一步提高催化加氢的效果,优选地,轻质化步骤的时间为1~100s。
32.以下结合具体实施例对本技术作进一步详细描述,这些实施例不能理解为限制本技术所要求保护的范围。
33.(一)炼厂焦化柴油加布朗气实验。
34.实施例1
‑135.催化加氢反应在申请号为202110315815.9_中所示的减压精馏塔中进行,结构如图1所示。
36.减压精馏塔包括卫星环绕式减压塔釜10和精馏段20;卫星环绕式减压塔釜包括主塔釜11和呈卫星式环绕设置在主塔釜外部的子反应器12;主塔釜11设置有第一出口和多个喷射入口,且主塔釜的顶部具有开口;子反应器12设置有第二出口和第一进口,喷射入口与子反应器的第二出口相连通,第一出口与第一进口相连通;子反应器12的容积小于主塔釜11的容积;精馏段20位于主塔釜11上方,并与主塔釜11的顶部开口相连通,精馏段20的顶部设置有轻组分出口。主塔釜11底部设有循环油管路和底油排除管路;主塔釜11中设有非淹没式撞击流构件,所有物料在子反应器12内一次反应后,液体泵均将物料从子反应器12送入主塔釜11内,进行非淹没式强化的二次反应。在实验室中试规模的实验中,子反应进料通过一台离心泵30作为物料运动的动力,离心泵30流量为6m3/h;微型反应器压力为0.08~0.1mpa;主塔釜11内的4012g物料与左侧子反应器12进行循环使用,以保证物料的充分反应。
37.具体过程如下:主反应器的容积为9l,加料4012g在进入子反应器后进行非淹没式
撞击的二次反应。催化加氢过程中,反应工艺条件如下:反应温度100℃,压力0.08~0.1mpa,气油比为100:1,不加入催化剂,物料停留时间为60min。
38.经催化加氢处理后,汽油馏分(c5‑
c
11
)收率为36.9wt%,柴油馏分(c
12
‑
c
24
)收率为63.1wt%。
39.实施例1
‑240.与实施例1
‑
1的区别为:催化加氢过程中,反应温度120℃,压力0.08~0.1mpa,气油比为120:1,物料停留时间为60min。
41.经催化加氢处理后,汽油馏分(c5‑
c
11
)收率为44.5wt%,柴油馏分(c
12
‑
c
24
)收率为55.5wt%。
42.实施例1
‑343.与实施例1
‑
1的区别为:催化加氢过程中,反应温度80℃,压力0.08~0.1mpa,气油比为80:1,物料停留时间为60min。
44.经催化加氢处理后,汽油馏分(c5‑
c
11
)收率为27.3wt%,柴油馏分(c
12
‑
c
24
)收率为72.7wt%。
45.对比例1
46.与实施例1
‑
1的区别为:采用氢气和氧气按摩尔比2:1混合得到的布朗气代替实施例1中使用的布朗气。经催化加氢处理后,汽油馏分(c5‑
c
11
)收率为12.5wt%,柴油馏分(c
12
‑
c
24
)收率为87.5wt%。
47.(二)炼厂催化柴油加布朗气实验
48.实施例2
‑149.反应器装置:同实施例1
‑
1。
50.与实施例1
‑
1的区别为:催化加氢反应的原料为催化柴油,反应温度为90℃,反应压力为0.08mpa,气油比为80:1。
51.经过催化氢化,所有非活性含硫分子均被氢化为硫化氢或被氧化为砜或亚砜,部分柴油轻质化为汽油。硫脱除率100wt%;产出24wt%的汽油(高效的轻质化结果)。
52.而现有的催化柴油加氢的条件为反应温度≥380℃,反应压力为5
‑
10mpa,氢油比为300~500:1,需要加入催化剂。通过比较可知采用本技术提供的方法能够大大降低反应温度,同时还不需要加入催化剂,从而能够大大降低催化加氢的工艺成本。
53.实施例2
‑254.反应器装置:同实施例1
‑
1。
55.与实施例1
‑
1的区别为:催化加氢反应的原料为催化柴油,反应温度为140℃,反应压力为0.08mpa,汽油比为120:1。
56.经过催化氢化,所有非活性含硫分子均被氢化为硫化氢或被氧化为砜或亚砜,部分柴油轻质化为汽油。硫脱除率100wt%;产出34.2wt%的汽油(高效的轻质化结果)。
57.实施例2
‑358.反应器装置:同实施例1
‑
1。
59.与实施例1
‑
1的区别为:催化加氢反应的原料为催化柴油,反应温度为110℃,反应压力为0.08mpa,汽油比为100:1。
60.经过催化氢化,所有非活性含硫分子均被氢化为硫化氢或被氧化为砜或亚砜,部
分柴油轻质化为汽油。硫脱除率100wt%;产出28.6wt%的汽油(高效的轻质化结果)。
61.实施例2
‑462.反应器装置:同实施例1
‑
1。
63.与实施例1
‑
1的区别为:催化加氢反应的原料为催化柴油,反应温度为80℃,反应压力为0.2mpa,汽油比为60:1。
64.经过催化氢化,所有非活性含硫分子均被氢化为硫化氢或被氧化为砜或亚砜,部分柴油轻质化为汽油。硫脱除率92wt%;产出19.2wt%的汽油(高效的轻质化结果)。
65.对比例2
66.与实施例2
‑
1的区别为:采用氢气和氧气按摩尔比2:1混合得到的布朗气代替实施例1中使用的布朗气。经催化加氢处理后,硫脱除率36wt%;产出8.8wt%的汽油馏分。
67.从以上的描述中,可以看出,本发明上述的实施例实现了如下技术效果:采用的布朗气中含有大量的氢离子和氧离子,且上述两种离子均具有非常高的反应活性。轻质化的过程,由于使用一种特殊的反应器,延长两种离子的复合时间,导致布朗气中的氢离子和氧离子能够与待处理的有机物进行结合。使上述轻质化产物进行催化加氢反应,能够大大降低催化加氢反应过程中的反应活化能,这使得上述催化反应不需要在催化剂的作用下进行也能够具有较高的反应速率,同时具有较低的能耗,以及较为优异的加氢效率和加氢产物的收率。
68.需要说明的是,本技术的说明书和权利要求书中的术语“第一”、“第二”等是用于区别类似的对象,而不必用于描述特定的顺序或先后次序。应该理解这样使用的术语在适当情况下可以互换,以便这里描述的本技术的实施方式例如能够以除了在这里描述的那些以外的顺序实施。
69.以上所述仅为本发明的优选实施例而已,并不用于限制本发明,对于本领域的技术人员来说,本发明可以有各种更改和变化。凡在本发明的精神和原则之内,所作的任何修改、等同替换、改进等,均应包含在本发明的保护范围之内。