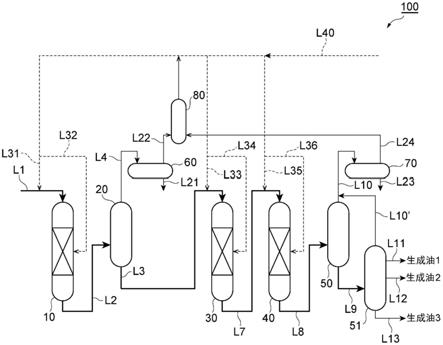
1.本发明涉及润滑油基础油的制造方法。
背景技术:
2.一直以来,对由蜡成分得到润滑油基础油的方法进行了各种研究。例如,专利文献1中公开了对含蜡原料进行加氢处理、催化加氢脱蜡、加氢精制而制造润滑油基础油的方法。
3.现有技术文献
4.专利文献
5.专利文献1:日本特表2006
‑
502297号公报
技术实现要素:
6.发明要解决的问题
7.润滑油基础油根据使用目的而存在有多种,各制品中所要求的低温性能和粘度特性不同,因此,期望得到大量相当于目标制品的馏分。
8.根据相当于目标制品的馏分(制品馏分)而使用重质的馏分(重质成分)作为原料的情况下,优选通过原料的加氢裂化而使重质成分轻质化。另一方面,将接近于目标制品的轻质的馏分(轻质成分)用于原料的情况下,原料如果加氢裂化,则生成低沸点物,有收率降低的担心。
9.因此,现有的制造方法中,需要根据原料的种类而大幅变更制造工艺。
10.本发明的目的在于,提供:能以相同反应装置和相同催化剂对轻质蜡和重质蜡这两者进行处理、能够效率良好地由各原料制造润滑油基础油的、润滑油基础油的制造方法。
11.用于解决问题的方案
12.本发明的一侧面涉及一种润滑油基础油的制造方法,其具备如下工序:第一加氢处理工序,使100℃下的运动粘度低于6mm2/秒的轻质蜡在含有加氢处理催化剂的第一反应器中流通,使上述加氢处理催化剂与上述轻质蜡在温度t1下接触,得到第一处理油;第二加氢处理工序,使100℃下的运动粘度为6mm2/秒以上的重质蜡在上述第一反应器中流通,使上述加氢处理催化剂与上述重质蜡在温度t2下接触,得到第二处理油;和,基础油制造工序,由含有选自由上述第一处理油和上述第二处理油组成的组中的至少一种的原料油得到润滑油基础油。该制造方法中,上述加氢处理催化剂是在通过氨程序升温脱附法而测得的总酸位的量a1为0.5mmol/g以上的无机氧化物载体中负载有选自元素周期表第6族、第8族、第9族和第10族的元素中的1种以上的金属的催化剂,上述温度t2为高于上述温度t1的温度。
13.上述制造方法中,可以以相同反应器(第一反应器)和相同催化剂对轻质蜡和重质蜡这两者进行处理。上述制造方法中,通过使用特定的催化剂并调整处理温度,从而对于轻质蜡,可以抑制裂化且脱硫,对于重质蜡,可以通过加氢裂化而轻质化且脱硫。因此,可以效率良好地通过由轻质蜡得到的第一处理油和由重质蜡得到的第二处理油这两处理油制造
具有适合的低温性能和粘度特性的润滑油基础油。
14.一方式中,在上述无机氧化物载体中,通过氨程序升温脱附法而测得的酸位中的在300℃以上的温度范围测定的酸位的量a2可以为0.2mmol/g以下。
15.一方式中,上述轻质蜡中的硫成分可以为10质量ppm以上且低于1500质量ppm,上述重质蜡中的硫成分可以为100质量ppm以上且5000质量ppm以下。
16.一方式中,上述轻质蜡的15℃下的密度可以为0.76g/cm3以上且低于0.835g/cm3,上述重质蜡的15℃下的密度可以为0.835g/cm3以上且0.88g/cm3以下。
17.一方式中,上述温度t1可以为250℃以上且低于350℃,上述温度t2可以为350℃以上且450℃以下。
18.一方式中,上述基础油制造工序可以包括如下工序:通过上述原料油的加氢异构化脱蜡而得到脱蜡油的工序;通过上述脱蜡油的加氢精制而得到加氢精制油的工序;和,通过上述加氢精制油的蒸馏而得到上述润滑油基础油的工序。
19.一方式中,上述基础油制造工序可以包括如下工序:通过上述原料油的蒸馏而得到基础油馏分的工序;通过上述基础油馏分的加氢异构化脱蜡而得到脱蜡油的工序;通过上述脱蜡油的加氢精制而得到加氢精制油的工序;和,通过上述加氢精制油的蒸馏而得到上述润滑油基础油的工序。
20.发明的效果
21.根据本发明,提供一种润滑油基础油的制造方法,其可以以相同反应装置和相同催化剂对轻质蜡和重质蜡这两者进行处理,能够效率良好地由各原料制造润滑油基础油。
附图说明
22.图1为示出用于实施一实施方式的润滑油基础油的制造方法的、润滑油基础油制造装置的一例的流程图。
具体实施方式
23.以下,参照附图的同时对本发明的适合的实施方式进行说明。需要说明的是,附图的说明中,对相同要素标注相同符号,省略重复的说明。另外,附图为了便于理解而扩展了一部分而绘制,尺寸比率等不限定于附图中记载的情况。
24.本实施方式的润滑油基础油的制造方法具备如下第一加氢处理工序:使100℃下的运动粘度低于6mm2/秒的轻质蜡在含有加氢处理催化剂的第一反应器中流通,使加氢处理催化剂与轻质蜡在温度t1下接触,得到第一处理油。
25.另外,本实施方式的润滑油基础油的制造方法还具备如下第二加氢处理工序:使100℃下的运动粘度为6mm2/秒以上的重质蜡在第一反应器中流通,使上述加氢处理催化剂与上述重质蜡在温度t2下接触,得到第二处理油。第一加氢处理工序与第二加氢处理工序的顺序没有特别限定,可以在实施了第一加氢处理工序后的第一反应器中进行第二加氢处理工序,也可以在实施了第二加氢处理工序后的第一反应器中进行第一加氢处理工序。本实施方式中,温度t2为高于温度t1的温度,重质蜡中的硫成分的比例大于轻质蜡中的硫成分的比例。
26.另外,本实施方式的润滑油基础油的制造方法还具备如下基础油制造工序:由含
有选自由第一处理油和第二处理油组成的组中的至少一种的原料油得到润滑油基础油。
27.本实施方式中,加氢处理催化剂是在通过氨程序升温脱附法而测得的总酸位的量a1为0.5mmol/g以上的无机氧化物载体中负载有选自元素周期表第6族、第8族、第9族和第10族的元素中的1种以上的金属的催化剂。
28.本实施方式的润滑油基础油的制造方法中,可以在相同反应器(第一反应器)中对轻质蜡和重质蜡这两者进行处理。另外,上述制造方法中,通过使用特定的催化剂并调整处理温度,从而对于轻质蜡,可以抑制裂化且脱硫,对于重质蜡,可以通过加氢裂化而轻质化且脱硫。因此,可以效率良好地通过由轻质蜡得到的第一处理油和由重质蜡得到的第二处理油这两处理油制造具有适合的低温性能和粘度特性的润滑油基础油。
29.以下,对本实施方式的润滑油基础油的制造方法中的各工序进行详述。
30.(第一加氢处理工序)
31.第一加氢处理工序为使轻质蜡在含有加氢处理催化剂的第一反应器中流通,使加氢处理催化剂与轻质蜡在温度t1下接触,得到第一处理油的工序。
32.加氢处理催化剂与轻质蜡可以在氢的存在下接触。即,第一加氢处理工序可以为使轻质蜡和氢在第一反应器中流通的工序。
33.轻质蜡是100℃下的运动粘度低于6mm2/秒的蜡。轻质蜡的100℃下的运动粘度可以为4.5mm2/秒以下。另外,从容易得到适合作为润滑油基础油的馏分的观点出发,轻质蜡的100℃下的运动粘度优选3mm2/秒以上、更优选3.5mm2/秒以上。
34.轻质蜡的15℃下的密度例如可以为0.76g/cm3以上,优选0.77g/cm3以上。另外,轻质蜡的15℃下的密度例如可以低于0.835g/cm3,优选0.82g/cm3以下。
35.轻质蜡中的硫成分例如可以为10质量ppm以上,可以为50质量ppm以上,可以为100质量ppm以上。另外,轻质蜡中的硫成分可以低于1500质量ppm,可以为1000质量ppm以下,可以为500质量ppm以下。通过使用这种轻质蜡,从而第一加氢处理工序中,容易得到抑制轻质蜡的裂化且充分脱硫了的处理油。需要说明的是,本说明书中,硫成分是指,依据jis k 2541
‑
6中记载的“原油和石油制品
‑
硫成分试验方法
‑
第6部:紫外荧光法”而测得的值。
36.轻质蜡也可以称为将正构烷烃作为主成分的烃油。轻质蜡中的正构烷烃的含量例如为50质量%以上、优选55质量%以上、更优选60质量%以上。
37.轻质蜡中可以包含油分。轻质蜡中的油分例如可以为20质量%以下,可以为15质量%以下。本说明书中,油分是指,依据jis k 2235中记载的“石油蜡”而测得的值。
38.轻质蜡例如可以为石油来源的蜡,可以为通过ft反应而合成的合成油来源的蜡,而且可以为通过溶剂脱蜡工艺而得到的蜡。
39.加氢处理催化剂是在无机氧化物载体中负载有选自元素周期表第6族、第8族、第9族和第10族的元素中的1种以上的金属的催化剂。
40.在无机氧化物载体中,通过氨程序升温脱附法而测得的总酸位的量a1为0.5mmol/g以上。用于处理轻质蜡的脱硫催化剂通常使用有裂化活性的酸位少的载体。而本实施方式中,使用总酸位的量a1为0.5mmol/g以上的无机氧化物载体,据此,在后述的第二加氢处理工序中重质蜡的裂化成为可能。
41.总酸位的量a1的上限没有特别限定,从进一步抑制轻质蜡的裂化的观点出发,总酸位的量a1例如可以为0.7mmol/g以下,可以为0.6mmol/g以下。
42.需要说明的是,氨程序升温脱附法(氨
‑
tpd法、ammonia temperature programmed desorption)作为表征固体催化剂的酸性的有效方法被熟知。例如,c.v.hidalgo等人、journal of catalysis、85卷、362
‑
369页(1984年)公开了,通过氨程序升温脱附法而可以测定酸位的量、酸位的酸强度的分布。
43.氨程序升温脱附法是指:同时测定通过使作为碱性探针分子的氨吸附于试样的固体并连续温度上升而发生脱附的氨的量以及温度。吸附于弱的酸位的氨在低温下发生脱附(相当于吸附热低的范围内的脱附),而吸附于强的酸位的氨在高温下发生脱附(相当于吸附热高的范围内的脱附)。在这种氨程序升温脱附法中,酸强度由温度、吸附热量表示,不利用显色反应,因此,固体酸强度和固体酸量为更准确的值。
44.需要说明的是,本实施方式中,无机氧化物载体中的酸位的量是指,根据“丹羽;沸石,10,175(1993)”等中记载的装置和测定条件,通过测定氨的吸附量的氨程序升温脱附法而求出的值。
45.在无机氧化物载体中,通过氨程序升温脱附法而测得的酸位中的在300℃以上的温度范围测定的酸位的量a2例如可以为0.2mmol/g以下,优选为0.18mmol/g以下。这种载体由于强的酸位的量少,因此,第一加氢处理工序中,轻质蜡的裂化被更显著地抑制。从后述的第二加氢处理工序中可以进一步促进重质蜡的裂化的观点出发,酸位的量a2例如可以为0.1mmol/g以上,优选0.12mmol/g以上。
46.无机氧化物载体优选为多孔性无机氧化物。无机氧化物载体例如可以为包含选自由铝、硅、锆、硼和钛组成的组中的2种以上的元素的无机氧化物。
47.向载体中导入选自由铝、硅、锆、硼和钛组成的组中的2种以上的元素的方法没有特别限定,例如可以举出如下方法:将含有多种元素的溶液等作为原料制备复合氧化物的方法;将含有各元素的溶液混合制备复合氧化物的方法;在2种以上的无机氧化物和/或复合氧化物的混合物中加入酸进行混炼为粘土状,得到捏合物,将该捏合物挤出成型、进行干燥后焙烧的方法;等。
48.含有元素的溶液例如可以为含有元素的化合物的水溶液。作为含有元素的化合物,例如,对于铝,可以举出铝、氢氧化铝、勃姆石等,对于硅,可以举出硅、水玻璃、硅溶胶等,对于锆,可以举出硫酸锆、锆的各种醇盐等,对于硼,可以举出硼酸等,对于钛,可以举出硫化钛、四氯化钛、钛的各种醇盐等。
49.包含2种以上的元素的无机氧化物由于包含不同种类的无机氧化物,因此,表面上的电荷分布会局部存在化,容易生成作为表面羟基的酸性质子,容易体现酸位。已知酸位的体现根据无机氧化物的种类、组成等而变化。因此,通过改变无机氧化物的种类、组成等,从而可以控制酸位的量、以及以氨程序升温脱附法测定酸时的氨脱附温度。从体现酸位的观点出发,无机氧化物载体优选包含3价金属的铝与价数不同的其他元素。
50.例如,无机氧化物载体由铝和硅构成的情况下(将无机氧化物载体的总量作为基准,铝和硅的总含量以氧化铝和二氧化硅换算计、为95质量%以上、优选99质量%以上的情况下),将无机氧化物载体总量作为基准,铝的含量以氧化铝换算计、优选30~90质量%、更优选40~85质量%、进一步优选50~80质量%。
51.另外,例如,无机氧化物载体由铝、硅和锆构成的情况下(将无机氧化物载体的总量作为基准,铝、硅和锆的总含量以氧化铝、二氧化硅和氧化锆换算计、为95质量%以上、优
选99质量%以上的情况下),将无机氧化物载体总量作为基准,铝的含量以氧化铝换算计、优选30~90质量%、更优选40~80质量%、进一步优选50~70质量%。
52.另外,例如,无机氧化物载体由铝、硅和钛构成的情况下(将无机氧化物载体的总量作为基准,铝、硅和钛的总含量以氧化铝、二氧化硅和二氧化钛换算计、为95质量%以上、优选99质量%以上的情况下),将无机氧化物载体总量作为基准,铝的含量以氧化铝换算计、优选30~90质量%、更优选40~80质量%、进一步优选50~70质量%。
53.在制备包含铝和铝以外的元素的无机氧化物载体的情况下,优选在焙烧载体之前的工序中添加铝以外的构成元素。例如,可以在铝水溶液中预先添加上述原料后,制备包含这些构成成分的氢氧化铝凝胶,也可以对制备好的氢氧化铝凝胶添加上述原料。另外,在氧化铝中间体或勃姆石粉中添加水或酸性水溶液并混炼的工序中,可以添加上述原料。另外,可以预先制备包含铝以外的构成元素的原料,并在其中调配勃姆石粉等氧化铝原料。铝以外的构成元素的效果体现机制未必清楚,但推测是形成了与铝复合的氧化物,认为,除酸位的体现的效果之外,产生载体表面积的增加、与活性金属的相互作用等效果,对活性产生影响。
54.无机氧化物载体可以还含有磷作为构成元素。含有磷的情况下,将无机氧化物载体总量作为基准,磷含量以氧化物换算计、优选0.1~10质量%、更优选0.5~7质量%、进一步优选2~6质量%。含有磷的情况下,可以使用磷酸、磷酸的碱金属盐等的溶液。
55.加氢处理催化剂具有选自元素周期表第6族、第8族、第9族和第10族的元素中的1种以上的金属(以下,也称为活性金属)。加氢处理催化剂中,优选具有选自钴、钼、镍和钨中的2种以上。作为活性金属的适合的组合,例如可以举出钴
‑
钼、镍
‑
钼、镍
‑
钴
‑
钼、镍
‑
钨等,更优选镍
‑
钼、镍
‑
钴
‑
钼和镍
‑
钨。这些活性金属可以在加氢处理催化剂上处于任何状态,例如可以以硫化物的状态使用。
56.对于加氢处理催化剂,按照加氢处理催化剂的总量基准、钨和钼的总含量以氧化物换算计优选12质量%以上、更优选15质量%以上。另外,对于加氢处理催化剂,按照加氢处理催化剂的总量基准、钨和钼的总含量以氧化物换算计优选35质量%以下、更优选30质量%以下。钨和钼的总含量如果为12质量%以上,则活性位点变多,有加氢活性变得更良好的倾向。另外,钨和钼的总含量如果为35质量%以下,则有金属的分散性改善,反应效率进一步改善的倾向。
57.对于加氢处理催化剂,按照加氢处理催化剂的总量基准、钴和镍的总含量以氧化物换算计优选1质量%以上、更优选1.5质量%以上。另外,对于加氢处理催化剂,按照加氢处理催化剂的总量基准、钴和镍的总含量以氧化物换算计优选15质量%以下、更优选13质量%以下。钴和镍的总含量如果为1质量%以上,则有显著发挥助催化剂的效果、活性进一步改善的倾向。另外,钴和镍的总含量如果为15质量%以下,则有金属的分散性改善、反应效率进一步改善的倾向。
58.使活性金属负载于无机氧化物载体的方法没有特别限定,可以没有特别限制地使用公知的负载方法。作为负载方法,例如可以举出:包括使包含活性金属的溶液(例如溶解有活性金属的盐的溶液)浸渗于无机氧化物载体的工序的方法等。另外,作为负载方法,也优选采用平衡吸附法、pore
‑
filling法、incipient
‑
wetness法等。例如,pore
‑
filling法是预先测定载体的孔容、使与其相同体积的金属盐溶液浸渗的方法。
70.第一加氢处理工序中的裂化率优选6.0质量%以下,更优选3.0质量%以下。第一加氢处理工序中,例如可以以裂化率成为上述范围的方式,适宜变更反应条件。
71.第一加氢处理工序中,得到第一处理油。第一处理油中的硫成分例如可以为30质量ppm以下,优选20质量ppm以下、更优选10质量ppm以下。第一加氢处理工序中,例如可以以硫成分成为上述范围的方式,适宜变更反应条件。
72.第一加氢处理工序中,通过轻质蜡的加氢裂化而可以得到气体、石脑油、灯轻油等轻质馏分,但第一处理油可以包含这些轻质馏分,也可以从加氢处理产物中去除这些轻质馏分。
73.第一处理油的15℃下的密度例如可以为0.81g/cm3以上,优选0.815g/cm3以上。另外,第一处理油的15℃下的密度例如可以低于0.835g/cm3,优选0.83g/cm3以下。
74.第一处理油中的正构烷烃的含量例如为50质量%以上、优选55质量%以上、更优选60质量%以上。
75.(第二加氢处理工序)
76.第二加氢处理工序为使重质蜡在含有加氢处理催化剂的第一反应器中流通,使加氢处理催化剂与重质蜡在温度t2下接触,得到第二处理油的工序。
77.加氢处理催化剂与重质蜡可以在氢的存在下接触。即,第二加氢处理工序可以为使重质蜡和氢在第一反应器中流通的工序。
78.重质蜡为100℃下的运动粘度为6mm2/秒以上的蜡。重质蜡的100℃下的运动粘度可以为7mm2/秒以上。另外,从容易得到适合作为润滑油基础油的馏分的观点出发,重质蜡的100℃下的运动粘度优选15mm2/秒以下、更优选12mm2/秒以下。
79.重质蜡的15℃下的密度例如可以为0.835g/cm3以上,优选0.84g/cm3以上。另外,重质蜡的15℃下的密度例如可以为0.88g/cm3以下,优选0.87g/cm3以下。
80.重质蜡中的硫成分例如可以为100质量ppm以上,可以为500质量ppm以上,可以为1000质量ppm以上。本实施方式中,在高于温度t1的温度(温度t2)下,使重质蜡与加氢处理催化剂接触,因此,即使硫成分为100质量ppm以上也可以充分脱硫。另外,重质蜡中的硫成分例如可以为5000质量ppm以下,可以为3000质量ppm以下,可以为2000质量ppm以下。通过使用这种重质蜡,从而有变得容易长时间维持催化活性的倾向。需要说明的是,本说明书中,硫成分是指,依据jis k 2541
‑
6中记载的“原油和石油制品
‑
硫成分试验方法
‑
第6部:紫外荧光法”而测得的值。
81.重质蜡中的正构烷烃的含量例如为15质量%以上、优选20质量%以上、更优选25质量%以上。
82.重质蜡中可以包含油分。重质蜡中的油分例如可以为30质量%以下,可以为20质量%以下。本说明书中,油分是指,依据jis k 2235中记载的“石油蜡”而测得的值。
83.重质蜡例如可以为石油来源的蜡,也可以为通过ft反应而合成的合成油来源的蜡,而且还可以为通过溶剂脱蜡工艺而得到的蜡。
84.第二加氢处理工序可以称为如下工序:使重质蜡在含有加氢处理催化剂的第一反应器中流通,使加氢处理催化剂与重质蜡在规定的反应条件下接触,对重质蜡进行加氢处理。
85.第二加氢处理工序中,使加氢处理催化剂与重质蜡在温度t2下接触。温度t2为高于
上述温度t1的温度。温度t2例如可以为350℃以上,优选370℃以上、更优选380℃以上。另外,温度t2例如可以为450℃以下,优选430℃以下、更优选420℃以下。温度t2如果为该范围,则效率良好地进行重质蜡的加氢裂化,变得容易得到适合于制造润滑油基础油的处理油。
86.第二加氢处理工序中,对于温度以外的反应条件没有特别限定,可以根据期望的基础油特性等而适宜变更。作为反应条件,例如可以将氢气压力设为2~20mpa、液体空间速度(lhsv)设为0.2~3h
‑1、氢油比(氢/油比)设为500~8000scfb(89~1425m3/m3)。通过增大氢气压力和氢油比,从而可以抑制焦化,而且有反应性改善的倾向。另外,氢气压力如果过大,则需要提高反应器的耐压性,氢油比如果过大,则需要内容积大的反应器,有时需要过大的设备投资。有液体空间速度越低,越有利于反应的倾向,但如果过低,则有时需要过大的反应器。
87.第二加氢处理工序中的温度以外的反应条件与第一加氢处理工序中的温度以外的反应条件可以大致相同也可以不同。使第一加氢处理工序和第二加氢处理工序中的温度以外的反应条件一致的情况下,仅凭借变更原料蜡(轻质蜡或重质蜡)和温度(t1或t2),就可以切换第一加氢处理工序和第二加氢处理工序,更有效的运转成为可能。需要说明的是,反应条件大致相同例如是指,氢气压力之差为1mpa以下,液体空间速度之差为0.3h
‑1以下,氢油比之差为500scfb以下的情况。
88.基于加氢处理的裂化率可以由原料蜡(第二加氢处理工序中为重质蜡)中的沸点为360℃以上的烃的含量w1、和加氢处理产物中的沸点为360℃以上的烃的含量w2以下述式求出。
89.裂化率(质量%)=100
×
(w1‑
w2)/w190.第二加氢处理工序中的裂化率优选15质量%以上、更优选20质量%以上。另外,第二加氢处理工序中的裂化率优选40质量%以下、更优选30质量%以下。第二加氢处理工序中,例如可以以裂化率成为上述范围的方式,适宜变更反应条件。
91.第二加氢处理工序中,得到第二处理油。第二处理油中的硫成分例如可以为30质量ppm以下,优选20质量ppm以下、更优选10质量ppm以下。第二加氢处理工序中,例如可以以硫成分成为上述范围的方式,适宜变更反应条件
92.第二加氢处理工序中,通过重质蜡的加氢裂化而得到气体、石脑油、灯轻油等轻质馏分,但第二处理油可以包含这些轻质馏分,也可以从加氢处理产物中去除这些轻质馏分。
93.第二处理油的15℃下的密度例如可以为0.82g/cm3以上,优选0.825g/cm3以上。另外,第二处理油的15℃下的密度例如可以低于0.865g/cm3,优选0.855g/cm3以下。
94.第二处理油中的正构烷烃的含量例如为10质量%以上、优选15质量%以上、更优选20质量%以上。
95.本实施方式中,实施第一加氢处理工序和第二加氢处理工序的顺序没有特别限定,可以在实施了第一加氢处理工序后、实施第二加氢处理工序,也可以在实施了第二加氢处理工序后、实施第一加氢处理工序。另外,本实施方式中,可以交替地实施第一加氢处理工序与第二加氢处理工序多次。
96.本实施方式中,可以由第一加氢处理工序中得到的第一处理油和第二加氢处理工序中得到的第二处理油制造润滑油基础油。本实施方式中,第一处理油和第二处理油可以分别单独地供于后述的基础油制造工序,也可以以混合物的形式供于后述的基础油制造工
序。
97.(基础油制造工序)
98.基础油制造工序为由含有选自由第一处理油和第二处理油组成的组中的至少一种的原料油得到润滑油基础油的工序。
99.基础油制造工序中,可以根据使用的制造装置的形态、期望的润滑油基础油的特性等对原料油进行处理,得到润滑油基础油。
100.原料油可以还含有第一处理油和第二处理油以外的其他烃油。另外,原料油可以为第一处理油、第二处理油、或第一处理油与第二处理油的混合物。
101.一方式中,基础油制造工序可以包括通过原料油的加氢异构化脱蜡而得到脱蜡油的工序(工序a
‑
1),可以还包括通过脱蜡油的加氢精制而得到加氢精制油的工序(工序a
‑
2)、和通过加氢精制油的蒸馏而得到润滑油基础油的工序(工序a
‑
3)。以下,对本方式的各工序进行详述。
102.<工序a
‑
1>
103.工序a
‑
1为通过原料油的加氢异构化脱蜡而得到脱蜡油的工序。工序a
‑
1中,加氢异构化脱蜡例如可以通过在氢的存在下、使原料油与加氢异构化催化剂接触而进行。作为加氢异构化催化剂,例如可以使用:加氢异构化中通常使用的催化剂、即、在无机载体中负载有具有加氢活性的金属的催化剂等。
104.作为加氢异构化催化剂中的具有加氢活性的金属,例如使用选自由元素周期表第6族、第8族、第9族和第10族的金属组成的组中的1种以上的金属。作为这些金属的具体例,可以举出铂、钯、铑、钌、铱、锇等贵金属、或者钴、镍、钼、钨、铁等,优选铂、钯、镍、钴、钼、钨,进一步优选铂、钯。另外,这些金属还优选组合多种而使用,作为该情况下的优选的组合,可以举出铂
‑
钯、钴
‑
钼、镍
‑
钼、镍
‑
钴
‑
钼、镍
‑
钨等。
105.作为加氢异构化催化剂中的无机载体,例如可以举出氧化铝、二氧化硅、二氧化钛、氧化锆、氧化硼等金属氧化物。这些金属氧化物可以为1种,也可以为2种以上的混合物或者二氧化硅氧化铝、二氧化硅氧化锆、氧化铝氧化锆、氧化铝氧化硼等复合金属氧化物。从有效地进行正构烷烃的加氢异构化的观点出发,上述无机载体优选二氧化硅氧化铝、二氧化硅氧化锆、氧化铝氧化锆、氧化铝氧化硼等具有固体酸性的复合金属氧化物。另外,无机载体中可以包含少量的沸石。出于改善载体的成型性和机械强度的目的,无机载体可以进而配混粘结剂。作为优选的粘结剂,可以举出氧化铝、二氧化硅、氧化镁等。
106.对于加氢异构化催化剂中的具有加氢活性的金属的含量,该金属为上述贵金属的情况下,作为金属原子,相对于无机载体100质量份,优选0.1~3质量份。另外,对于加氢异构化催化剂中的具有加氢活性的金属的含量,该金属为上述贵金属以外的金属的情况下,以金属氧化物换算计、优选2~50质量%。如果为这种含量范围,则有金属的分散性良好、得到高的催化活性的倾向。
107.加氢异构化催化剂可以为如下催化剂:在包含选自铝、硅、锆、硼、钛、镁和沸石中的至少一种的多孔性无机氧化物所构成的载体中,负载选自元素周期表第6族、第8族、第9族和第10族的金属的元素中的金属1种以上而成。
108.作为多孔性无机氧化物,可以举出氧化铝、二氧化钛、氧化锆、氧化硼、二氧化硅、沸石等,其中,优选二氧化钛、氧化锆、氧化硼、二氧化硅和沸石中的至少1种与氧化铝所构
成的无机氧化物。
109.多孔性无机氧化物的制造方法没有特别限定,可以使用对应于各元素的各种溶胶、氯化合物等状态的原料并采用任意的制备法。此外,可以暂时制备二氧化硅氧化铝、二氧化硅氧化锆、氧化铝二氧化钛、二氧化硅二氧化钛、氧化铝氧化硼等复合氢氧化物或者复合氧化物,然后以氧化铝凝胶、以及氢氧化物的状态或者适当的溶液的状态在制备工序的任意的工序中添加而制备。氧化铝与其他氧化物的比率相对于载体也可以取任意比例。氧化铝的含量以多孔性无机氧化物的总量基准计、优选90质量%以下、更优选60质量%以下、进而优选40质量%以下,且优选10质量%以上、更优选20质量%以上。
110.沸石为结晶性硅酸铝,可以举出八面沸石、pentacil、丝光沸石、ton、mtt、
*
mre、
*
bea等,可以使用:通过规定的水热处理和/或酸处理进行超稳定化而成者、或者调整沸石中的氧化铝含量而成者。优选使用八面沸石、丝光沸石、beta,特别优选使用y型、beta型。y型优选超稳定化而成者,通过水热处理而超稳定化的沸石除原本的被称为以下的微孔的孔结构之外还在超过且以下的范围形成了新的孔。水热处理条件可以使用公知的条件。
111.作为选自元素周期表第6族、第8族、第9族和第10族的元素中的1种以上的金属,优选使用选自pd、pt、rh、ir和ni中的1种以上的金属,更优选组合2种以上而使用。作为适合的组合,例如可以举出pd
‑
pt、pd
‑
ir、pd
‑
rh、pd
‑
ni、pt
‑
rh、pt
‑
ir、pt
‑
ni、rh
‑
ir、rh
‑
ni、ir
‑
ni、pd
‑
pt
‑
rh、pd
‑
pt
‑
ir、pt
‑
pd
‑
ni等。其中,更优选pd
‑
pt、pd
‑
ni、pt
‑
ni、pd
‑
ir、pt
‑
rh、pt
‑
ir、rh
‑
ir、pd
‑
pt
‑
rh、pd
‑
pt
‑
ni、pd
‑
pt
‑
ir的组合,进而更优选pd
‑
pt、pd
‑
ni、pt
‑
ni、pd
‑
ir、pt
‑
ir、pd
‑
pt
‑
ni、pd
‑
pt
‑
ir的组合。
112.选自元素周期表第6族、第8族、第9族和第10族的元素中的1种以上的金属的总含量以加氢异构化催化剂的总量基准计、作为金属原子优选0.1~2质量%、更优选0.2~1.5质量%、进一步优选0.25~1.3质量%。如果为这种含量范围,则有金属的分散性良好、可以得到高的催化活性的倾向。
113.制造加氢异构化催化剂时,使金属负载于载体的方法没有特别限定,可以采用公知的方法。通常,优选采用使溶解有金属的盐的溶液浸渗于载体的方法。另外,还优选采用平衡吸附法、pore
‑
filling法、incipient
‑
wetness法等。
114.作为加氢异构化催化剂,例如可以适合使用日本特开2017
‑
43688号公报中记载的催化剂等。
115.接着,对工序a
‑
1的反应条件进行详述。
116.工序a
‑
1中,加氢异构化脱蜡的反应温度优选200~450℃、更优选280~400℃。反应温度如果为上述范围,则可以抑制原料油的裂化,且充分进行正构烷烃的异构化。
117.加氢异构化脱蜡的反应压力优选0.1~20mpa、更优选0.5~10mpa。反应压力如果为上述范围,则焦炭生成所导致的催化剂的劣化被抑制,另外,也可以抑制装置建设成本。
118.加氢异构化脱蜡中的原料油相对于催化剂的液体空间速度优选0.01~100h
‑1、更优选0.1~50h
‑1。液体空间速度如果为上述范围,则可以抑制原料油的裂化,且充分减少/去除蜡成分。
119.加氢异构化脱蜡中的氢与原料油的供给比率(氢油比)优选100~1500nm3/m3、更优
选200~800nm3/m3。氢油比如果为上述范围,则变得容易得到充分的催化性能,另外,也可以抑制设备建设成本。
120.工序a
‑
1中得到的脱蜡油的正构烷烃浓度优选10体积%以下、更优选1体积%以下。
121.工序a
‑
1中得到的脱蜡油可以适合作为润滑油基础油原料使用。本实施方式中,例如,经过将工序a
‑
1中得到的脱蜡油加氢精制而得到加氢精制油的工序(工序a
‑
2)、和将加氢精制油蒸馏而得到润滑油基础油的工序(工序a
‑
3),可以得到润滑油基础油。
122.<工序a
‑
2>
123.工序a
‑
2为通过工序a
‑
1中得到的脱蜡油的加氢精制而得到加氢精制油的工序。通过加氢精制,例如,脱蜡油中的烯烃和芳香族化合物经加氢,可以改善润滑油基础油的氧化稳定性和色调。进而,脱蜡油中的硫化合物经加氢,从而也可以期待硫成分的减少。
124.加氢精制可以通过使脱蜡油与加氢精制催化剂在氢的存在下接触而进行。作为加氢精制催化剂,例如可以举出如下催化剂:其具备包含选自氧化铝、二氧化硅、氧化锆、二氧化钛、氧化硼、氧化镁和磷中的1种以上的无机固体酸性物质而构成的载体、以及负载于该载体上的、选自由铂、钯、镍
‑
钼、镍
‑
钨和镍
‑
钴
‑
钼组成的组中的1种以上的活性金属。
125.作为加氢精制催化剂中的适合的载体,可以举出包含至少2种以上的氧化铝、二氧化硅、氧化锆、或二氧化钛的无机固体酸性物质。作为使活性金属负载于载体的方法,可以采用浸渗、离子交换等常规方法。
126.加氢精制催化剂中的活性金属的负载量相对于载体100质量份,优选0.1~25质量份。
127.加氢精制催化剂的平均孔径优选6~60nm、更优选7~30nm。平均孔径如果为该范围,则有活性金属的分散性改善、变得容易得到良好的催化活性的倾向。
128.加氢精制催化剂的孔容优选0.2ml/g以上。孔容如果为0.2ml/g以上,则有催化剂的活性劣化被抑制的倾向。需要说明的是,加氢精制催化剂的孔容例如可以为0.5ml/g以下。另外,加氢精制催化剂的比表面积优选200m2/g以上。催化剂的比表面积如果为200m2/g以上,则有活性金属的分散性改善、催化活性改善的倾向。需要说明的是,加氢精制催化剂的比表面积例如可以为400m2/g以下。加氢精制催化剂的比表面积、孔容、平均孔径可以通过氮气吸附法而求出。比表面积通过bet法而求出,孔容和平均孔径通过bjh法而求出。
129.加氢精制的反应条件例如优选反应温度为200~300℃、氢分压为3~20mpa、lhsv为0.5~5h
‑1、氢/油比为170~850nm3/m3,更优选反应温度为200℃~300℃、氢分压为4~18mpa、lhsv为0.5~4h
‑1、氢/油比为340~850nm3/m3。
130.加氢精制的反应条件例如可以以加氢精制油中的硫成分和氮成分分别成为5质量ppm以下和1质量ppm以下的方式进行调整。需要说明的是,硫成分是基于jis k2541
‑
6中记载的“原油和石油制品
‑
硫成分试验方法
‑
第6部:紫外荧光法”而测得的值,氮成分是基于jis k2609“原油和石油制品
‑
氮成分试验方法”而测得的值。
131.<工序a
‑
3>
132.工序a
‑
3为通过工序a
‑
2中得到的加氢精制油的蒸馏而得到润滑油基础油的工序。工序a
‑
3也可以称为如下工序:将加氢精制油分馏成多种馏分,得到至少一种的润滑油基础油。
133.工序a
‑
3中的蒸馏条件只要为可以从加氢精制油分馏润滑油基础油的条件就没有特别限定。例如,工序a
‑
3优选如下进行:从加氢精制油蒸馏去除轻质馏分的常压蒸馏(或加压下的蒸馏)、和从该常压蒸馏的底油分馏润滑油基础油的减压蒸馏。
134.工序a
‑
3中,例如,通过设定多种分馏点来减压蒸馏底油,从而可以得到多种润滑油馏分。工序a
‑
3中,例如,从加氢精制油,可以分别分馏:10体积%馏出温度为280℃以上、90体积%馏出温度为390℃以下的第1润滑油馏分,10体积%馏出温度为390℃以上、90体积%馏出温度为490℃以下的第2润滑油馏分,以及10体积%馏出温度为490℃以上、90体积%馏出温度为530℃以下的第3润滑油馏分并进行回收。
135.第1润滑油馏分可以作为适于atf(自动变速器油,automatic transmission fluid)、减震器的润滑油基础油取得,该情况下,优选将100℃下的运动粘度2.7mm2/秒作为目标值。第2润滑油馏分可以作为适于满足api的组iii标准的发动机油基础油的润滑油基础油取得,该情况下,优选将100℃下的运动粘度4.0mm2/秒作为目标值,形成100℃下的运动粘度为3.5mm2/秒以上且4.5mm2/秒以下、倾点为
‑
17.5℃以下的馏分。第3润滑油馏分为满足api的组iii标准的发动机油基础油,例如可以作为适于柴油发动机等的润滑油基础油取得,该情况下,优选将40℃下的运动粘度高于32mm2/秒的值作为目标,进一步优选100℃下的运动粘度高于6.0mm2/秒的值。需要说明的是,本说明书中,40℃或100℃下的运动粘度和粘度指数是基于jis k2283“原油和石油制品
‑
运动粘度试验方法和粘度指数算出方法”而求出的值。
136.需要说明的是,第1润滑油馏分可以作为相当于70pale的润滑油基础油取得,第2润滑油馏分可以作为相当于sae
‑
10的润滑油基础油取得,第3润滑油馏分可以作为相当于sae
‑
20的润滑油基础油取得。需要说明的是,sae粘度是指,society of automotive engineers规定的标准。另外,api标准基于美国石油协会(api(american petroleum institute))的润滑油等级的分类,是指组ii(粘度指数80以上且低于120、且饱和成分90质量%以上、且硫成分含量0.03质量%以下)、组iii(粘度指数120以上、且饱和成分90质量%以上、且硫成分含量0.03质量%以下)。此外,粘度指数130以上的润滑油基础油被称为组iii+,作为api标准以上的高品质的制品要求。
137.另外,工序a
‑
2中得到的加氢精制油中,包含由于加氢异构化、加氢裂化而副产的石脑油、灯轻油等轻质馏分。工序a
‑
3中,可以作为例如90体积%馏出温度为280℃以下的馏分回收这些轻质馏分。
138.以上,对基础油制造工序的一方式进行了说明,但基础油制造工序不限定于上述方式。例如,另一方式中,基础油制造工序可以包括:通过原料油的蒸馏而得到基础油馏分的工序(工序b
‑
1)、和通过基础油馏分的加氢异构化脱蜡而得到脱蜡油的工序(工序b
‑
2),也可以还包括:通过脱蜡油的加氢精制而得到加氢精制油的工序(工序b
‑
3)、和通过加氢精制油的蒸馏而得到润滑油基础油的工序(工序b
‑
4)。以下,对该方式的各工序进行详述。
139.<工序b
‑
1>
140.工序b
‑
1中,从原料油分馏基础油馏分。另外,工序b
‑
1中,根据情况,也可以进一步分馏气体、石脑油、灯轻油等轻质馏分。另外,工序b
‑
1中,可以进一步分馏比基础油馏分还重质的重质馏分,可以将该重质馏分作为底油回收。
141.基础油馏分为经后述的工序b
‑
2(以及、根据需要的工序b
‑
3和工序b
‑
4)用于得到
润滑油基础油的馏分,其沸点范围可以根据目标制品而适宜变更。
142.基础油馏分优选为10体积%馏出温度为280℃以上、90体积%馏出温度为530℃以下的馏分。通过使基础油馏分形成沸点范围为上述范围的馏分,可以更有效地制造有用的润滑油基础油。需要说明的是,本说明书中,10体积%馏出温度和90体积%馏出温度是基于jis k2254“石油制品
‑
蒸馏试验方法
‑
气相色谱法”而测得的值。
143.根据情况,除基础油馏分以外,原料油还可以包含沸点高于基础油馏分的重质的馏分(重质馏分)、和沸点低于基础油馏分的轻质的馏分(轻质馏分)。轻质馏分是90体积%馏出温度低于基础油馏分的10体积%馏出温度的馏分,例如是具有低于280℃的90体积%馏出温度的馏分。重质馏分是10体积%馏出温度高于基础油馏分的90体积%馏出温度的馏分,例如是具有高于530℃的10体积%馏出温度的馏分。
144.工序b
‑
1中的蒸馏条件只要为可以从原料油分馏基础油馏分的条件就没有特别限定。例如工序b
‑
1可以为通过减压蒸馏从原料油分馏基础油馏分的工序,也可以为组合常压蒸馏(或加压下的蒸馏)和减压蒸馏而从原料油分馏基础油馏分的工序。
145.例如,原料油包含重质馏分和轻质馏分的情况下,工序b
‑
1可以通过从原料油蒸馏去除轻质馏分的常压蒸馏(或加压下的蒸馏)、以及从该常压蒸馏的底油分别分馏基础油馏分和重质馏分的减压蒸馏而进行。
146.工序b
‑
1中,基础油馏分可以作为单一的馏分被分馏,也可以作为根据期望的润滑油基础油的多种馏分被分馏。如此经分馏的多种润滑油馏分可以分别独立地供于后段的工序b
‑
2。另外,也可以将多种基础油馏分的一部分或全部混合而供于后段的工序b
‑
2。
147.<工序b
‑
2>
148.工序b
‑
2为将工序b
‑
1中得到的基础油馏分加氢异构化脱蜡而得到脱蜡油的工序。工序b
‑
2中的加氢异构化脱蜡例如可以通过在氢的存在下、使基础油馏分与加氢异构化催化剂接触而进行。
149.作为工序b
‑
2的加氢异构化脱蜡中的加氢异构化催化剂和反应条件,可以示例与上述工序a
‑
1同样的加氢异构化催化剂和反应条件。
150.工序b
‑
2中得到的脱蜡油的正构烷烃浓度优选10体积%以下、更优选1体积%以下。
151.工序b
‑
2中得到的脱蜡油可以适合作为润滑油基础油原料使用。本实施方式中,例如经过将工序b
‑
2中得到的脱蜡油加氢精制而得到加氢精制油的工序(工序b
‑
3)、和将加氢精制油蒸馏而得到润滑油基础油的工序(工序b
‑
4),可以得到润滑油基础油。
152.<工序b
‑
3>
153.工序b
‑
3为将工序b
‑
2中得到的脱蜡油加氢精制而得到加氢精制油的工序。通过加氢精制,例如,脱蜡油中的烯烃和芳香族化合物经加氢,可以改善润滑油基础油的氧化稳定性和色调。进而,脱蜡油中的硫化合物经加氢,从而也可以期待硫成分的减少。
154.工序b
‑
3例如可以通过在氢的存在下、使脱蜡油与加氢精制催化剂接触而进行。作为工序b
‑
3中的加氢精制催化剂和加氢精制的反应条件,可以示例与上述工序a
‑
2同样的加氢精制催化剂和反应条件。
155.加氢精制的反应条件例如可以以加氢精制油中的硫成分和氮成分分别成为5质量ppm以下和1质量ppm以下的方式进行调整。需要说明的是,硫成分为基于jis k2541
‑
6中记
载的“原油和石油制品
‑
硫成分试验方法
‑
第6部:紫外荧光法”而测得的值,氮成分为基于jis k2609中记载的“原油和石油制品
‑
氮成分试验方法”而测得的值。
156.<工序b
‑
4>
157.工序b
‑
4为通过工序b
‑
3中得到的加氢精制油的蒸馏而得到润滑油基础油的工序。工序b
‑
4也可以称为如下工序:将加氢精制油分馏为多种馏分,得到至少一种的润滑油基础油。
158.工序b
‑
4中的蒸馏条件只要为可以从加氢精制油分馏润滑油基础油的条件就没有特别限定。例如,工序b
‑
4优选通过从加氢精制油蒸馏去除轻质馏分的常压蒸馏(或加压下的蒸馏)、和从该常压蒸馏的底油分馏润滑油基础油的减压蒸馏而进行。
159.工序b
‑
4中,例如通过设定多种分馏点来减压蒸馏底油,从而可以得到多种润滑油馏分。工序b
‑
4中,例如,从加氢精制油,可以分别分馏:10体积%馏出温度为280℃以上、90体积%馏出温度为390℃以下的第1润滑油馏分,10体积%馏出温度为390℃以上、90体积%馏出温度为490℃以下的第2润滑油馏分,以及10体积%馏出温度为490℃以上、90体积%馏出温度为530℃以下的第3润滑油馏分并进行回收。
160.第1润滑油馏分可以作为适于atf、减震器的润滑油基础油取得,该情况下,优选将100℃下的运动粘度2.7mm2/秒作为目标值。第2润滑油馏分可以作为适于满足api的组iii标准的发动机油基础油的润滑油基础油取得,该情况下,优选将100℃下的运动粘度4.0mm2/秒作为目标值,形成100℃下的运动粘度为3.5mm2/秒以上且4.5mm2/秒以下、倾点为
‑
17.5℃以下的馏分。第3润滑油馏分为满足api的组iii标准的发动机油基础油,例如可以作为适于柴油发动机等的润滑油基础油取得,该情况下,将40℃下的运动粘度高于32mm2/秒的值作为目标,进一步优选100℃下的运动粘度高于6.0mm2/秒的值。
161.需要说明的是,第1润滑油馏分可以作为相当于70pale的润滑油基础油取得,第2润滑油馏分可以作为相当于sae
‑
10的润滑油基础油取得,第3润滑油馏分可以作为相当于sae
‑
20的润滑油基础油取得。需要说明的是,sae粘度是指,society of automotive engineers规定的标准。另外,api标准基于美国石油协会(api(american petroleum institute))的润滑油等级的分类,是指组ii(粘度指数80以上且低于120、且饱和成分90质量%以上、且硫成分含量0.03质量%以下)、组iii(粘度指数120以上、且饱和成分90质量%以上、且硫成分含量0.03质量%以下)。此外,粘度指数130以上的润滑油基础油被称为组iii+,作为api标准以上的高品质的制品要求。
162.另外,工序b
‑
3中得到的加氢精制油中,可以包含由于加氢异构化等而副产的石脑油、灯轻油等轻质馏分。工序b
‑
4中,例如可以作为90体积%馏出温度为280℃以下的馏分回收这些轻质馏分。
163.(其他工序)
164.本实施方式的制造方法可以还具备上述第一加氢处理工序、第二加氢处理工序和基础油制造工序以外的其他工序。
165.例如,本实施方式的制造方法可以还具备由石油系原料得到轻质蜡的工序(例如溶剂提取工序、加氢工序、脱蜡工序)、由石油系原料得到重质蜡的工序(例如脱溶剂工序、溶剂提取工序、加氢工序、脱蜡工序)等。
166.接着,参照附图,对本发明的一实施方式进行说明。图1为示出用于实施一实施方
式的润滑油基础油的制造方法的、润滑油基础油制造装置的一例的流程图。
167.图1所示的润滑油基础油制造装置100具备:对从流路l1导入的轻质蜡或重质蜡进行加氢处理的第一反应器10;将从第一反应器通过流路l2供给的加氢处理产物进行高压分离(在加压下蒸馏去除轻质馏分)的第一分隔件20;将从第一分隔件20通过流路l3供给的底油(第一处理油或第二处理油)进行加氢异构化脱蜡的第二反应器30;将从第二反应器30通过流路l7供给的脱蜡油加氢精制的第三反应器40;将从第三反应器40通过流路l8供给的加氢精制油分馏的第二分隔件50;将从第二分隔件50通过流路l9供给的底油减压蒸馏的减压蒸馏塔51,从而构成。
168.通过流路l40,向第一反应器10、第二反应器30和第三反应器40供给氢气。
169.润滑油基础油制造装置100中,设有从流路l40分支且与流路l1连接的流路l31,从流路l31供给的氢气在流路l1内与轻质蜡或重质蜡混合而导入至第一反应器10。另外,第一反应器10上连接有从流路l40分支的l32,通过来自流路l32的氢气的供给来调整第一反应器10内的氢气压力和催化剂层温度。
170.滑油基础油制造装置100中,还设有从流路l40分支且与流路l3连接的流路l33,从流路l33供给的氢气在流路l3内与第一处理油或第二处理油混合而导入至第二反应器30。另外,第二反应器30上连接有从流路l40分支的流路l34,通过来自流路l34的氢气的供给来调整第二反应器30内的氢气压力和催化剂层温度。
171.润滑油基础油制造装置100中,还设有从流路l40分支且与流路l7连接的流路l35,从流路l35供给的氢气在流路l7内与脱蜡油混合而导入至第三反应器40。另外,第三反应器40上连接有从流路l40分支的流路l36,通过来自流路l36的氢气的供给来调整第三反应器40内的氢气压力和催化剂层温度。
172.需要说明的是,从第二反应器30,通过流路l7取出与脱蜡油一起通过第二反应器30的氢气。因此,从流路l35供给的氢气的量可以根据从第二反应器30取出的氢气的量而适宜调整。
173.第一分隔件20上连接有用于将轻质馏分和氢气向体系外取出的流路l4。从流路l4取出的包含轻质馏分和氢气的混合气体供给至第一气液分离器60,分离成轻质馏分和氢气。第一气液分离器60上,连接有用于取出轻质馏分的流路l21和用于取出氢气的流路l22。
174.第二分隔件50上连接有用于将轻质馏分和氢气向体系外取出的流路l10。从流路l10取出的包含轻质馏分和氢气的混合气体供给至第二气液分离器70,分离成轻质馏分和氢气。第二气液分离器70上连接有用于取出轻质馏分的流路l23和用于取出氢气的流路l24。
175.从第一气液分离器60和第二气液分离器70取出的氢气通过流路l22和流路l24供给至酸性气体吸收塔80。从第一气液分离器60和第二气液分离器70取出的氢气中包含作为硫成分的加氢物的硫化氢等,酸性气体吸收塔80中,将该硫化氢等去除。酸性气体吸收塔80中去除了硫化氢等的氢气供给至流路l40,再次导入至各反应器。
176.减压蒸馏塔51上,设有用于将根据期望的润滑油基础油而分馏的润滑油馏分向体系外取出的流路l11、l12和l13。
177.润滑油基础油制造装置100中,第一加氢处理工序可以通过对从流路l1供给的轻质蜡在第一反应器10中进行加氢处理而实施。另外,第二加氢处理工序可以通过对从流路
l1供给的重质蜡在第一反应器10中进行加氢处理而实施。第一反应器10中,在从流路l31和流路l32供给的氢(分子氢)的存在下,使轻质蜡或重质蜡与加氢处理催化剂接触,可以进行加氢处理。
178.第一反应器10的形式没有特别限定,例如适合使用填充有加氢处理催化剂的固定床流通式反应器。需要说明的是,润滑油基础油制造装置100中,用于加氢处理的反应器仅为第一反应器10,但本实施方式中,润滑油基础油制造装置可以串联或并列地配置有用于加氢处理的多种反应器。另外,反应器内的催化床可以为单一也可以为多个。
179.润滑油基础油制造装置100中,从第一反应器取出的反应物在第一分隔件20中经高压分离后供于第二反应器。
180.第一分隔件20中,通过对从流路l2供给的加氢处理产物进行高压分离(在加压下进行分馏),从而可以将轻质馏分从流路l4取出,将底油(第一处理油或第二处理油)从流路l3取出。另外,从流路l2与加氢处理产物一起使通过第一反应器10的氢气在第一分隔件20中流通。第一分隔件20中,可以与轻质馏分一起将该氢气从流路l4取出。
181.润滑油基础油制造装置100中,在流路l3的中途可以还具备罐和送液泵。该情况下,例如事先将第一加氢处理工序中制造的第一处理油保持在该罐中,接着,将第二加氢处理工序中制造的第二处理油供给至该罐,从而在混合了第一处理油和第二处理油的状态下,可以供给至第二反应器30。另外,相反地,也可以事先将第二加氢处理工序中制造的第二处理油保持在该罐中,接着,将第一加氢处理工序中制造的第一处理油供给至该罐,从而在混合了第二处理油和第一处理油的状态下,供给至第二反应器30。
182.润滑油基础油制造装置100中,可以包括工序a
‑
1、工序a
‑
2和工序a
‑
3地实施基础油制造工序。
183.润滑油基础油制造装置100中,工序a
‑
1在第二反应器30中实施。第二反应器30中,在从流路l33和流路l34供给的氢(分子氢)的存在下,使从流路l3供给的原料油(第一处理油或第二处理油)与加氢异构化催化剂接触。由此,原料油通过加氢异构化而脱蜡。
184.第二反应器30的形式没有特别限定,例如适合使用填充有加氢异构化催化剂的固定床流通式反应器。需要说明的是,润滑油基础油制造装置100中,用于加氢异构化脱蜡的反应器仅为第二反应器30,但本实施方式中,润滑油基础油制造装置可以串联或并列地配置有用于加氢异构化脱蜡的多种反应器。另外,反应器内的催化床可以为单一也可以为多个。
185.经过第二反应器30而得到的脱蜡油与通过第二反应器30的氢气一起通过流路l7供给至第三反应器40。
186.润滑油基础油制造装置100中,工序a
‑
2在第三反应器40中实施。第三反应器40中,在从流路l7、流路l35和流路l36供给的氢(分子氢)的存在下,使从流路l7供给的脱蜡油与加氢精制催化剂接触,从而脱蜡油经加氢精制。
187.第三反应器40的形式没有特别限定,例如适合使用填充有加氢精制催化剂的固定床流通式反应器。需要说明的是,润滑油基础油制造装置100中,用于加氢精制的反应器仅为第三反应器40,但本实施方式中,润滑油基础油制造装置可以串联或并列地配置有用于加氢精制的多种反应器。另外,反应器内的催化床可以为单一也可以为多个。
188.经过第三反应器40而得到的加氢精制油与通过第三反应器40的氢气一起通过流
路l8供给至第二分隔件50。
189.润滑油基础油制造装置100中,工序a
‑
3可以由第二分隔件50和减压蒸馏塔51而实施。
190.第二分隔件50中,对通过流路l8供给的加氢精制油进行高压分离(在加压下进行分馏),从而从作为润滑油基础油有用的馏分自流路l10取出轻质的馏分(例如石脑油和燃料油馏分),可以自流路l9取出底油。另外,从流路l8使通过第三反应器40的氢气与加氢精制油一起流通,但第二分隔件50中,可以将该氢气与轻质馏分一起从流路l10取出。
191.减压蒸馏塔51中,将从流路l9供给的底油进行减压蒸馏,从而可以从流路l11、流路l12和流路l13取出润滑油馏分,从各流路取出的润滑油馏分可以分别适合作为润滑油基础油使用。另外,减压蒸馏塔51中,可以将比润滑油馏分还轻质的馏分从流路l10’提取,在流路l10中合流。
192.需要说明的是,润滑油基础油制造装置100中,工序a
‑
3由第二分隔件50和减压蒸馏塔51进行,但工序a
‑
3例如也可以由3个以上的蒸馏塔实施。另外,减压蒸馏塔51中,将作为润滑油馏分的3个馏分分馏并取出,但本实施方式的制造方法中,可以将作为润滑油馏分的单一的馏分取出,也可以将作为润滑油馏分的2个馏分或4个以上的馏分分馏而取出。
193.润滑油基础油制造装置100中,第一反应器10中,轻质蜡或重质蜡经加氢处理。此时,轻质蜡或重质蜡中所含的硫成分经加氢,有时产生硫化氢。即,通过第一反应器10的氢气有时包含硫化氢。
194.将通过第一反应器10且包含硫化氢的氢气直接返回至流路l40并再利用时,向第二反应器30供给包含硫化氢的氢气,第二反应器30的催化活性有时降低。因此,润滑油基础油制造装置100中,通过第一反应器10的氢气经过流路l2、第一分隔件20、流路l4、第一气液分离器60和流路l22供给至酸性气体吸收塔80,在该酸性气体吸收塔80中将硫化氢去除后,返回至流路l40。
195.另外,润滑油基础油制造装置100中,通过第二反应器30和第三反应器40的氢气有时也含有由基础油馏分中微量包含的硫成分而产生的硫化氢,因此,通过流路l24供给至酸性气体吸收塔80后,返回至流路l40。
196.润滑油基础油制造装置100中,如上述那样借助酸性气体吸收塔80使氢气循环,但本实施方式中,未必需要使氢气循环,可以向各反应器分别独立地供给氢气。
197.另外,润滑油基础油制造装置100中,在酸性气体吸收塔80的前段或后段可以具备用于去除由氮成分的加氢而产生的氨等的、排水处理设备。氨与汽提蒸汽等混合而在排水处理设备中经处理,以硫回收与硫一起成为nox,之后在脱硝反应中恢复成氮。
198.以上,对润滑油基础油制造装置的一例进行了说明,但用于实施本实施方式的润滑油基础油的制造方法的润滑油基础油制造装置不限定于上述制造装置。
199.例如,润滑油基础油制造装置可以在第一分隔件20与第二反应器30之间还具备通过流路l3将自第一分隔件20供给的底油进行减压蒸馏的减压蒸馏塔。这种润滑油基础油制造装置中,减压蒸馏塔中经分馏的基础油馏分供给至第二反应器30。
200.根据这种润滑油基础油制造装置,可以包括工序b
‑
1、工序b
‑
2、工序b
‑
3和工序b
‑
4,实施基础油制造工序。
201.以上,对本发明的适合的实施方式进行了说明,但本发明不限定于上述实施方式。
202.实施例
203.以下,根据实施例,对本发明更具体地进行说明,但本发明不限定于实施例。需要说明的是,以下,将实施属于第一加氢处理工序或第二加氢处理工序的加氢处理的情况作为实施例,将实施不属于第一加氢处理工序和第二加氢处理工序中的任一者的加氢处理的情况作为比较例。
204.(制造例1:加氢处理催化剂(a
‑
1)的制备)
205.在二氧化硅氧化锆40质量%与氧化铝60质量%的混合物中加入稀硝酸,进行混炼成粘土状,制备捏合物。将该捏合物进行挤出成型、干燥、焙烧,制备载体。利用浸渗法,在该载体中负载镍氧化物4质量%、钼氧化物23质量%、磷氧化物3质量%,得到加氢裂化催化剂(a
‑
1)。
206.(制造例2:加氢处理催化剂(a
‑
2)的制备)
207.在二氧化硅氧化锆70质量%与氧化铝30质量%的混合物中加入稀硝酸,进行混炼成粘土状,制备捏合物。将该捏合物进行挤出成型、干燥、焙烧,制备载体。利用浸渗法,在该载体中负载镍氧化物11质量%、钨氧化物20质量%,得到加氢裂化催化剂(a
‑
2)。
208.(制造例3:加氢处理催化剂(x
‑
1)的制备)
209.在二氧化硅二氧化钛8质量%与氧化铝92质量%的混合物中加入稀硝酸,进行混炼成粘土状,制备捏合物。将该捏合物进行挤出成型、干燥、焙烧,制备载体。利用浸渗法,在该载体中负载镍氧化物3质量%、钼氧化物22质量%、磷氧化物3质量%,得到加氢裂化催化剂(x
‑
1)。
210.对于制造例1~3的加氢处理催化剂,通过氨程序升温脱附法测定载体的酸位,结果成为表1所示的结果。需要说明的是,测定装置使用的是microtrac bel inc.制的belcat。
211.[表1]
[0212][0213]
(实施例1
‑
1)
[0214]
作为轻质蜡,准备下述表2所示的性状的轻质蜡。使轻质蜡在填充有加氢处理催化剂(a
‑
1)的反应器中流通,在下述表3所示的条件下进行加氢处理。对于加氢处理产物,以下述所示的方法求出裂化率和硫成分,结果成为表3所示的结果。
[0215]
[表2]
[0216] 轻质蜡密度(15℃,g/cm3)o.8240运动粘度(100℃,mm2/s)3.70硫成分(质量ppm)300
油分(质量%)13.0正构烷烃含量(质量%)61.2沸点为360℃以上的烃的含量w1(质量%)98.5
[0217]
裂化率由原料蜡中的沸点为360℃以上的烃的含量w1、和加氢处理产物中的沸点为360℃以上的烃的含量w2以下述式求出。
[0218]
裂化率(质量%)=100
×
(w1‑
w2)/w1[0219]
硫成分依据jis k 2541
‑
6中记载的“原油和石油制品
‑
硫成分试验方法
‑
第6部:紫外荧光法”而测定。
[0220]
(实施例1
‑
2~1
‑
4)
[0221]
将加氢处理的条件变更为表3所示的条件,除此之外,与实施例1
‑
1同样地进行加氢处理,评价加氢处理产物。将结果示于表3。
[0222]
[表3]
[0223][0224]
(实施例2
‑
1)
[0225]
作为重质蜡,准备下述表4所示的性状的重质蜡。使重质蜡在填充有加氢处理催化剂(a
‑
1)的反应器中流通,在下述表5所示的条件下进行加氢处理。对于加氢处理产物,求出裂化率和硫成分,结果成为表5所示的结果。
[0226]
[表4]
[0227] 重质蜡密度(15℃,g/cm3)0.8540运动粘度(100℃,mm2/s)7.94硫成分(质量ppm)1576油分(质量%)20.1正构烷烃含量(质量%)21.6沸点为360℃以上的烃的含量w1(质量%)100.0
[0228]
(实施例2
‑
2~2
‑
8)
[0229]
将加氢处理的条件变更为表5或表6所示的条件,除此之外,与实施例2
‑
1同样地进行加氢处理,评价加氢处理产物。将结果示于表5或表6。
[0230]
[表5]
[0231][0232]
[表6]
[0233][0234]
(实施例3)
[0235]
作为轻质蜡,准备表2所示的性状的轻质蜡。使轻质蜡在填充有加氢处理催化剂(a
‑
2)的反应器中流通,在下述表7所示的条件下进行加氢处理。
[0236]
对于加氢处理产物,求出裂化率和硫成分,结果成为表7所示的结果。
[0237]
[表7]
[0238][0239]
(比较例1)
[0240]
作为重质蜡,准备表4所示的性状的重质蜡。使重质蜡在填充有加氢处理催化剂(x
‑
1)的反应器中流通,在下述表8所示的条件下进行加氢处理。对于加氢处理产物,求出裂化率和硫成分,结果成为表8所示的结果。
[0241]
[表8]
[0242][0243]
如实施例所示,根据本发明,对于轻质蜡,可以充分地抑制裂化且进行脱硫,对于重质蜡,可以通过加氢裂化进行轻质化。由该结果表明,根据本发明的制造方法,可以效率良好地由轻质蜡和重质蜡这两者制造润滑油基础油。
[0244]
使用了加氢处理催化剂(x
‑
1)的比较例1中,与同一条件的实施例2
‑
7相比,加氢裂化的效率降低。
[0245]
附图标记说明
[0246]
10
…
第一反应器、20
…
第一分隔件、30
…
第二反应器、40
…
第三反应器、50
…
第二分隔件、51
…
减压蒸馏塔、60
…
第一气液分离器、70
…
第二气液分离器、80
…
酸性气体吸收塔、l1、l2、l3、l4、l7、l8、l9、l10、l10’、l11、l12、l13、l21、l22、l23、l24、l31、l32、l33、l34、l35、l36、l40
…
流路、100
…
润滑油基础油制造装置。